EXPERIMENTAL INVESTIGATION of an INTEGRATED SOLAR DRIVEN WASTEWATER TREATMENT SYSTEM for TRIGENERATION APPLICATIONS by MURAT
Total Page:16
File Type:pdf, Size:1020Kb
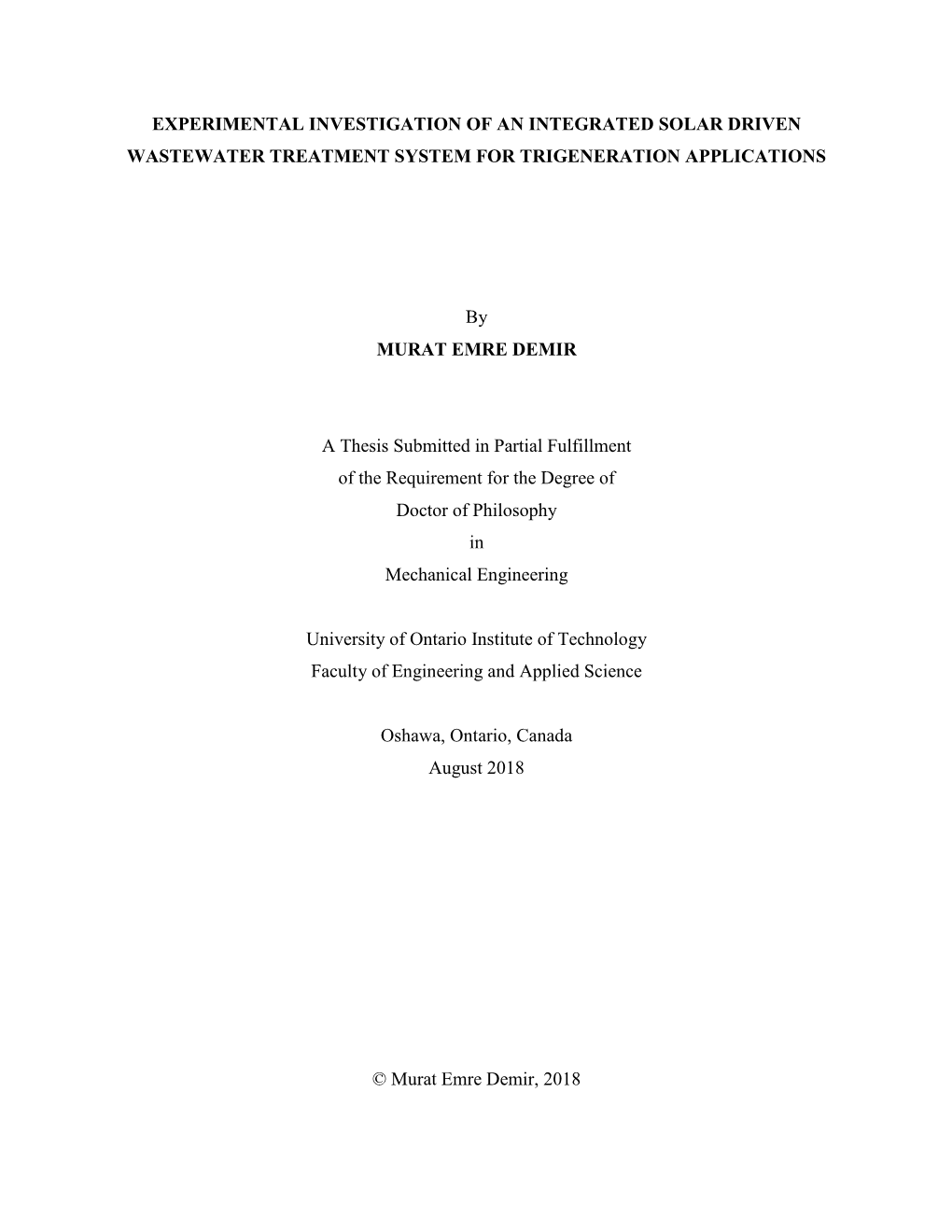
Load more
Recommended publications
-
A Mini-Review: Emerging All-Solid-State Energy Storage Electrode Materials for Flexible Devices
Nanoscale A mini-review: Emerging All-Solid-State Energy Storage Electrode Materials for Flexible Devices Journal: Nanoscale Manuscript ID NR-MRV-10-2019-008722.R1 Article Type: Minireview Date Submitted by the 25-Dec-2019 Author: Complete List of Authors: Yang, Yang; University of Central Florida, NanoScience Technology Center Page 1 of 31 Nanoscale A mini-review: Emerging All-Solid-State Energy Storage Electrode Materials for Flexible Devices Yang Yang* NanoScience Technology Center, Department of Materials Science and Engineering, Energy Conversion and Propulsion Cluster, University of Central Florida, 12424 Research Parkway Suite 423, Orlando, Florida 32826, United States *E-mail: [email protected] Abstract: New technologies for future electronics such as personal healthcare devices and foldable smartphones require emerging developments in flexible energy storage devices as power sources. Besides the energy and power densities of the energy device, more attention should be paid to safety, reliability, and compatibility within the highly integrated systems because they are almost in 24-hour real-time operation close to the human body. Thereupon, all-solid-state energy devices become the most promising candidates to meet these requirements. In this mini-review, the most recent research progress in the all-solid-state flexible supercapacitors and batteries will be covered. The main focus of this mini-review is to summarize new materials development for all-solid-state flexible energy devices. The potential issues and perspectives regarding -
University of Southampton Research Repository Eprints Soton
University of Southampton Research Repository ePrints Soton Copyright © and Moral Rights for this thesis are retained by the author and/or other copyright owners. A copy can be downloaded for personal non-commercial research or study, without prior permission or charge. This thesis cannot be reproduced or quoted extensively from without first obtaining permission in writing from the copyright holder/s. The content must not be changed in any way or sold commercially in any format or medium without the formal permission of the copyright holders. When referring to this work, full bibliographic details including the author, title, awarding institution and date of the thesis must be given e.g. AUTHOR (year of submission) "Full thesis title", University of Southampton, name of the University School or Department, PhD Thesis, pagination http://eprints.soton.ac.uk University of Southampton Printable Thermoelectric Devices for Energy Harvesting By Zhuo Cao A thesis submitted in partial fulfilment for the degree of Doctor of Philosophy In the Faculty of Physical Science and Engineering Electronics and Computer Science October, 2014 Abstract This thesis describes the approaches of fabricating and testing thermoelectric generators (TEG) using screen printing. It includes the formation of the pastes, optimizing of the manufacture processes and the measurement of the thermoelectric properties. A nickel/copper based high temperature TEG was made to demonstrating the screen printing can be applied to fabricate thermoelectric materials. A bismuth/antimony based low temperature TEG was fabricated to identify the proper polymer binder for low temperature TEG application. A flexible bismuth tellurium/antimony tellurium low temperature TEG with 4 thermocouples was presented with a generated voltage of 23 mV and an output power of 194 nW when ∆T=20°C . -
Battery Charging Considerations in Small Scale Electricity Generation from a Thermoelectric Module
Battery Charging Considerations in Small Scale Electricity Generation from a Thermoelectric Module C. E. Kinsella1, S. M. O’Shaughnessy1, M.J. Deasy1, M. Duffy2, A.J. Robinson*1 1Department of Mechanical & Manufacturing Engineering, Parsons Building, Trinity College Dublin, Ireland. 2 Electrical and Electronic Engineering, NUI Galway, Ireland *Email: [email protected] *Tel: +353 1 896 3919 Abstract This project involves the development of a prototype electrical generator for delivering and storing small amounts of electricity. Power is generated using the thermoelectric effect. A single thermoelectric generator (TEG) is utilised to convert a small portion of the heat flowing through it to electricity. The electricity produced is used to charge a single rechargeable 3.3 Volt lithium-iron phosphate battery. This study investigates methods of delivering maximum power to the battery for a range of temperature gradients across the thermoelectric module. The paper explores load matching and maximum power point tracking techniques. It was found that, for the TEG tested, a SEPIC DC-DC converter was only beneficial for temperature gradients less than 100 ⁰C across the TEG. At a temperature gradient of 150 ⁰C, the effective resistance of the battery was close to the internal resistance of the TEG. For temperature gradients in excess of 100°C a DC-DC converter is not suggested and a simple charge protection circuit is sufficient. Keywords Thermoelectricity, Electricity Generation, Load Matching, Maximum Power Point Tracking 1. Introduction Thermoelectric generators (TEGs) are solid state devices that convert heat directly to electricity. Although TEGs are commercially available, they are low in efficiency, typically of the order of 3-5%. -
Perspectives in Using of the 3D Textile Composites to Produce Rechargeable Batteries
PERSPECTIVES IN USING OF THE 3D TEXTILE COMPOSITES TO PRODUCE RECHARGEABLE BATTERIES CS III Dr. Eng. Raluca Maria AILENI1, CS Eng. Laura CHIRIAC1 1 INCDTP, Bucharest, Romania REZUMAT. Această lucrare prezintă câteva aspecte privind compozitele 3D textile cu funcţionalizare controlată a suprafeţei la nivel micro/nano pentru a obţine compozitul adecvat cu capacitate de a stoca energia. Bateriile clasice nu sunt flexibile, nu sunt uşoare, şi generează probleme la integrarea în produsele textile. Recent bateriile pe bază de textile utilizează acoperiri metalice (de exemplu: argint, nichel, cupru, zinc) sau materiale pe bază de carbon pentru realizarea supercapacitorilor (SCs). În plus, prin intermediul tehnologiei Polymer-Assisted Metal Deposition (PAMD), metalele cu conductivitate mare cum ar fi cuprul (Cu) şi nichelul (Ni) pot fi depuse uniform, pe materialele textile pretratate pentru a realiza baterii pe suport textil flexibil pe bază de litiu. Interesul crescut în realizarea bateriilor flexibile cu consum redus de energie pentru sisteme de monitorizare purtabile este datorat faptului că bateriile clasice sunt rigide şi produc disconfort la purtare. O alternativă o reprezintă dezvoltarea bateriilor flexibile, a capacitorilor utilizând acoperiri prin peliculizare, impregnare, printare directă, printare 3D pe bază de soluţii polimerice conţinut de micro/nanoparticule. În literatura ştiinţifică, câteva abordări constau în electrozilor din argint, cupru, argint/nichel, nichel/cupru, cupru/argint, oxizi de grafen şi nanotuburi de carbon (CNTs) combinate cu materialele pentru electroliţi cum ar fi sulfonat de polistiren (3,4-etilen-dioxitiofen) (PEDOT: PSS) sau triiodura de potasiu (KI3). Câteva grupuri de cercetare au raportat SCs flexibili pe bază de electrozi flexibili 1D integraţi prin procedee mecanice şi electrozi capacitivi integraţi într-o singură fibră sau fir. -
EVALUATION of PRACTICABILITY of a RADIOISOTOPE THERMAL CONVERTER for an ARTIFICIAL HEART DEVICE Phase 1 Final Report
4. ^^I_ SAN-857-1 EVALUATION OF PRACTICABILITY OF A RADIOISOTOPE THERMAL CONVERTER FOR AN ARTIFICIAL HEART DEVICE Phase 1 Final Report April 1972 TRWSystems Group Redondo Beach, California DISTRIBUTION OF THIS DOCUMENT IS UNLIMITED* UNITED STATES ATOMIC ENERGY COMMISSION • TECHNICAL INFORMATION CENTER DISCLAIMER This report was prepared as an account of work sponsored by an agency of the United States Government. Neither the United States Government nor any agency Thereof, nor any of their employees, makes any warranty, express or implied, or assumes any legal liability or responsibility for the accuracy, completeness, or usefulness of any information, apparatus, product, or process disclosed, or represents that its use would not infringe privately owned rights. Reference herein to any specific commercial product, process, or service by trade name, trademark, manufacturer, or otherwise does not necessarily constitute or imply its endorsement, recommendation, or favoring by the United States Government or any agency thereof. The views and opinions of authors expressed herein do not necessarily state or reflect those of the United States Government or any agency thereof. DISCLAIMER Portions of this document may be illegible in electronic image products. Images are produced from the best available original document. NOTICE This report was prepared as an account of work sponsored by the United States Government Neither the United States nor the United States Atomic Energy Commission, nor any of their employees, nor any of their contractors, subcontractors, or their employees, makes any warranty, express or implied, or assumes any legal liability or responsibility for the accuracy, completeness or usefulness of any information, apparatus, product or process disclosed, or represents that its use would not infringe privately owned rights rhis report has been reproduced directly from the best available copy. -
Design and Construction of High Temperature Thermoelectric Power Generator Module Characterisation System
University of Wollongong Research Online University of Wollongong Thesis Collection 1954-2016 University of Wollongong Thesis Collections 2015 Design and construction of high temperature thermoelectric power generator module characterisation system Tomas Katkus University of Wollongong Follow this and additional works at: https://ro.uow.edu.au/theses University of Wollongong Copyright Warning You may print or download ONE copy of this document for the purpose of your own research or study. The University does not authorise you to copy, communicate or otherwise make available electronically to any other person any copyright material contained on this site. You are reminded of the following: This work is copyright. Apart from any use permitted under the Copyright Act 1968, no part of this work may be reproduced by any process, nor may any other exclusive right be exercised, without the permission of the author. Copyright owners are entitled to take legal action against persons who infringe their copyright. A reproduction of material that is protected by copyright may be a copyright infringement. A court may impose penalties and award damages in relation to offences and infringements relating to copyright material. Higher penalties may apply, and higher damages may be awarded, for offences and infringements involving the conversion of material into digital or electronic form. Unless otherwise indicated, the views expressed in this thesis are those of the author and do not necessarily represent the views of the University of Wollongong. Recommended Citation Katkus, Tomas, Design and construction of high temperature thermoelectric power generator module characterisation system, thesis, Institute for Superconducting and Electronic Materials, University of Wollongong, 2015. -
Battery Life and How to Improve It
Battery Life and How To Improve It Battery and Energy Technologies Technologies Battery Life (and Death) Low Power Cells High Power Cells For product designers, an understanding of the factors affecting battery life is vitally important for managing both product Chargers & Charging performance and warranty liabilities particularly with high cost, high power batteries. Offer too low a warranty period and you won't Battery Management sell any batteries/products. Overestimate the battery lifetime and you could lose a fortune. Battery Testing Cell Chemistries FAQ That batteries have a finite life is due to occurrence of the unwanted chemical or physical changes to, or the loss of, the active materials of which Free Report they are made. Otherwise they would last indefinitely. These changes are usually irreversible and they affect the electrical performance of the cell. Buying Batteries in China Battery life can usually only be extended by preventing or reducing the cause of the unwanted parasitic chemical effects which occur in the cells. Choosing a Battery Some ways of improving battery life and hence reliability are considered below. How to Specify Batteries Battery cycle life is defined as the number of complete charge - discharge cycles a battery can perform before its nominal capacity falls below Sponsors 80% of its initial rated capacity. Lifetimes of 500 to 1200 cycles are typical. The actual ageing process results in a gradual reduction in capacity over time. When a cell reaches its specified lifetime it does not stop working suddenly. The ageing process continues at the same rate as before so that a cell whose capacity had fallen to 80% after 1000 cycles will probably continue working to perhaps 2000 cycles when its effective capacity will have fallen to 60% of its original capacity. -
Sept. 25, 1962 I
Sept. 25, 1962 I. D. YAOM ET AL 3,055,960 THERMOELECTRIC BATTERY Filed Jan. 6, 1956 ”Z’DIA ×zzzzzzzzzzzzzzzzzzZzZzZzZzZ 3%% INVENTORS I. D. YALOM J. C. JEROME ?/2 ATTORNES United States Patent Office 3,055,960 Patented Sept. 25, 1962 2 3,055,960 ing the tab to the cell casing. Deposited on the under Isador D.Yalon,THERMOELECTRIC Silver Spring, and BATTERY Joseph C. Jerome, side of enlarged portion 7 of the linking tab 6 is a coating Hyattsville, Md., assignors to the United States of of calcium 9. America as represented by the Secretary of the Navy As shown on FIG. 2 after the casing 1 has been bent Filed Jan. 6, 1956, Ser. No. 557,814 into the desired "cup" shape, a rectangular pad, or layer, 4 Claims. (Cl. 136-4) of electrolyte material 11 is placed therein in contact (Granted under Title 35, U.S. Code (1952), sec. 266) relationship with bottom wall 2. The electrolyte is of a eutectic mixture, or composition, such as lithium, and The invention described herein may be manufactured potassium chlorides, adapted to be converted from a solid and used by or for the Government of the United States 0. nonconductive state to a liquid conductive state upon of America for governmental purposes without the ??? application of a predetermined quantity of heat energy. ment of any royalties thereon or therefor. Superposed on the electrolyte pad is a rectangular metallic This invention relates to thermoelectric generators of plate, such as the enlarged portion 7 of interlinking tab the cell type having a source of heat energy and an as 6 having its calcium coated underside 9 in contiguous sociated electrical energy generating unit. -
A Dissertation
A RESOURCE RESEARCH IN ELECTRICITY For American Industrial Arts Education with Implications for Teacher Education A DISSERTATION Presented in Partial Fulfil latent of the Requirements for the Degree Doctor of Philosophy In the Graduate School of The Ohio Stete University by WILLIAM L J I H M DECK, D.S., M.A. Southwest Texas State Teachers College San Marcos, Texas THE OHIO STATa UNIVERSITY 1955 Approved by: Adviser Department of Educntion rtidf/ci; The commercialisation of the phenomenon of electricity haa assumed amaBing proportions. The original presentation of lighting and telephone displays occurred only sixty yearn ago at the Columbian imposition in Chicago in 1893* Teas than 50 million dollars was spent for electrical equipment and service of all types during the year of 1900. This mushroomed to two billion dollars by 19^0 and the current figure i» approximately twenty billion doilrre annually. Such data oannot be ignored by those engaged in American public education, and especially by those in industrial arts education. The question of whet to do about this problem has been accepted by this dissertation. Its organization and development have been designed especially to answer most of the questions thnt should be resolved by the industrial arts profession. The names of many students of this subject should be acknowl edged because the writer has been engrossed with t.h ' problem for some twenty years and has had the very real privilege of working directly with those in industry. Chief among the above is f’rofeusor Lawrence C. Scorest of the Industrial Arts electrical Laboratory in the State Teachers College at LeKalb, Illinois. -
Real-Time Estimation of Battery Internal Temperature Based on a Simplified Thermoelectric Model
Real-time Estimation of Battery Internal Temperature Based on a Simplified Thermoelectric Model Cheng Zhanga, Kang Lia,∗, Jing Denga aSchool of Electronics, Electrical Engineering and Computer Science, Queen's University Belfast, 125 Stramillis Road, Ashby Building, Belfast, BT9 5AH, UK Abstract Li-ion batteries have been widely used in the EVs, and the battery thermal management is a key but challenging part of the battery management system. For EV batteries, only the battery surface temperature can be measured in real- time. However, it is the battery internal temperature that directly affects the battery performance, and large temperature difference may exist between sur- face and internal temperatures, especially in high power demand applications. In this paper, an online battery internal temperature estimation method is pro- posed based on a novel simplified thermoelectric model. The battery thermal behaviour is first described by a simplified thermal model, and battery electri- cal behaviour by an electric model. Then, these two models are interrelated to capture the interactions between battery thermal and electrical behaviours, thus offer a comprehensive description of the battery behaviour that is useful for battery management. Finally, based on the developed model, the battery internal temperature is estimated using an extended Kalman filter. The exper- imental results confirm the efficacy of the proposed method, and it can be used for online internal temperature estimation which is a key indicator for better real-time battery thermal management. Keywords: LiFePO4/C battery, internal temperature estimation, simplified thermoelectric model, extended Kalman Filter ∗Corresponding author: [email protected] (K. Li) Preprint submitted to Journal of Power Source September 24, 2015 1. -
Thermal Modelling and Cost Analysis for Large-Scale Battery Energy Storage System (BESS) in Grid-Connected PV Plant
Thermal Modelling and Cost Analysis for Large-Scale Battery Energy Storage System (BESS) in Grid-Connected PV Plant Md Mehedi Hasan Bachelor of Engineering (Electrical and Electronic Engineering) A thesis submitted for the degree of Master of Philosophy at The University of Queensland in 2019 School of Information Technology and Electrical Engineering Abstract With the growing renewable energy capacity at an exponential rate every year, energy storage system has become popular. Among available energy storage systems, battery energy storage system (BESS) is widely used technology for its high-power density and fast response in renewable plants such as photovoltaic (PV) farm. The indispensable operation of battery system is to store excess PV generation and utilise it effectively. Fluctuation in PV generation output is a usual incident due to the unpredictable nature of PV generation. Therefore, a storage system is required to smooth its output generation prior to export it to the grid. Despite a lot of advancement in electrochemical storage technology and cost reduction, battery degradation remains a big obstacle for its wider acceptance in large-scale PV plant. Battery degrades because of charging/discharging operation as well as during idle condition. Elevated temperature of battery cell accelerates battery degradation, which indicates an imminent loss of expensive investment on BESS. In addition, elevated temperature is responsible for adding to the cost of battery system operation in the plant by accelerating cooling system operation. A number of research studies have been carried out to model thermal characteristics and be- haviour of battery. However, the majority of studies reported in the literature are conducted on the small-scale battery thermal management where thermal behaviour is investigated using complicated thermo-dynamical models. -
An Advanced Lithium-Ion Battery Optimal Charging Strategy Based on a Coupled Thermoelectric Model
This is a repository copy of An advanced Lithium-ion battery optimal charging strategy based on a coupled thermoelectric model. White Rose Research Online URL for this paper: http://eprints.whiterose.ac.uk/132841/ Version: Accepted Version Article: Liu, K, Li, K, Yang, Z et al. (2 more authors) (2017) An advanced Lithium-ion battery optimal charging strategy based on a coupled thermoelectric model. Electrochimica Acta, 225. pp. 330-344. ISSN 0013-4686 https://doi.org/10.1016/j.electacta.2016.12.129 © 2016 Published by Elsevier Ltd. This manuscript version is made available under the CC-BY-NC-ND 4.0 license http://creativecommons.org/licenses/by-nc-nd/4.0/ Reuse Items deposited in White Rose Research Online are protected by copyright, with all rights reserved unless indicated otherwise. They may be downloaded and/or printed for private study, or other acts as permitted by national copyright laws. The publisher or other rights holders may allow further reproduction and re-use of the full text version. This is indicated by the licence information on the White Rose Research Online record for the item. Takedown If you consider content in White Rose Research Online to be in breach of UK law, please notify us by emailing [email protected] including the URL of the record and the reason for the withdrawal request. [email protected] https://eprints.whiterose.ac.uk/ An advanced Lithium-ion battery optimal charging strategy based on a coupled thermoelectric model Kailong Liua, Kang Lia, Zhile Yanga, Cheng Zhanga, Jing Denga a S E E E C S Q U B Belfast, BT9 5AH, United Kingdom (Email:{kliu02,k.li,zyang07,czhang07,j.deng}@qub.ac.uk).