Gauge Repeatability and Reproducibility Study for a Bulge Test Fixture for Corrugated Boxes
Total Page:16
File Type:pdf, Size:1020Kb
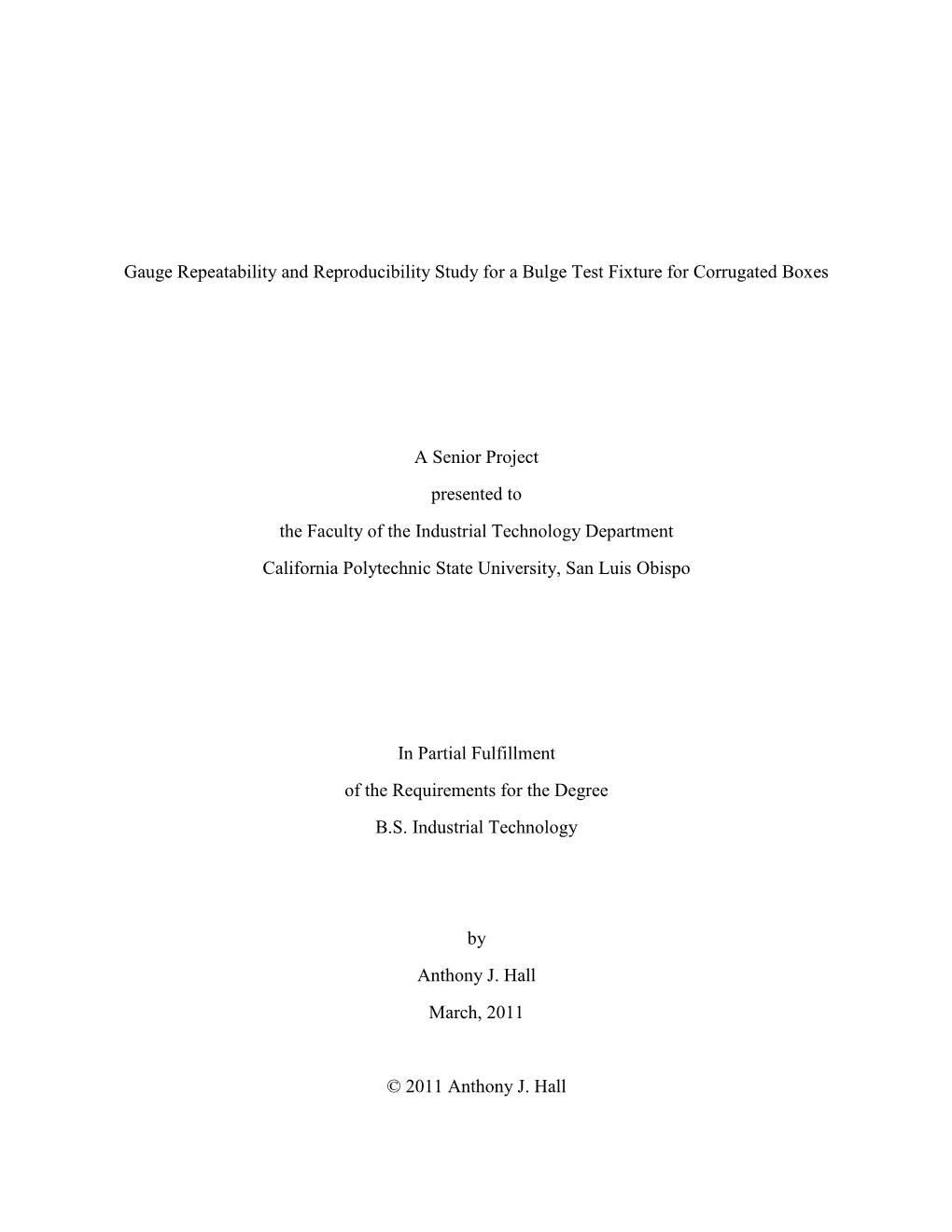
Load more
Recommended publications
-
Learn the Six Methods for Determining Moisture
SCIENCE OF SENSING Learn the Six Methods For Determining Moisture ADVANTAGES, DEFICIENCIES AND WHO USES EACH METHOD CONTENTS 1. Introduction 3 2. Primary versus Secondary Test Methods 4 3. Primary Methods 5 a. Karl Fisher 6 b. Loss On Drying 8 4. Secondary Methods 10 a. Electrical Methods 11 b. Microwave 13 c. Nuclear 15 d. Near-Infrared 17 5. Conclusion 19 6. About the Author 20 7. About Kett 20 8. Next Steps 21 Learn the Six Methods For Determining Moisture | www.kett.com 2 1. INTRODUCTION With three-quarters of the earth covered with water, almost everything we touch or eat has some water content. The accurate measurement of water content is very important, as it affects all aspects of a business and it’s supply chain. As discussed in our previous ebook “A Guide To Accurate and Reliable Moisture Measurement”, the proper (or improper) utilization of moisture meters to optimize water can be the difference between profitability and failure for a business. This ebook, the 6 Methods For Determining Moisture is for anyone interested in pursuing the goal of accurate moisture measurement, including: quality control, quality assurance, production management, design/build engineers, executive management and of course anyone wanting to learn more about this far reaching topic. The purpose of this ebook is to provide insight into the various major moisture measurement technologies and to help you identify which is the right type of instrument for your needs. Expect to learn the six major methods of moisture measurement, the positive aspects of each, as well as the drawbacks. -
Variation Factors in the Design and Analysis of Replicated Controlled Experiments - Three (Dis)Similar Studies on Inspections Versus Unit Testing
Variation Factors in the Design and Analysis of Replicated Controlled Experiments - Three (Dis)similar Studies on Inspections versus Unit Testing Runeson, Per; Stefik, Andreas; Andrews, Anneliese Published in: Empirical Software Engineering DOI: 10.1007/s10664-013-9262-z 2014 Link to publication Citation for published version (APA): Runeson, P., Stefik, A., & Andrews, A. (2014). Variation Factors in the Design and Analysis of Replicated Controlled Experiments - Three (Dis)similar Studies on Inspections versus Unit Testing. Empirical Software Engineering, 19(6), 1781-1808. https://doi.org/10.1007/s10664-013-9262-z Total number of authors: 3 General rights Unless other specific re-use rights are stated the following general rights apply: Copyright and moral rights for the publications made accessible in the public portal are retained by the authors and/or other copyright owners and it is a condition of accessing publications that users recognise and abide by the legal requirements associated with these rights. • Users may download and print one copy of any publication from the public portal for the purpose of private study or research. • You may not further distribute the material or use it for any profit-making activity or commercial gain • You may freely distribute the URL identifying the publication in the public portal Read more about Creative commons licenses: https://creativecommons.org/licenses/ Take down policy If you believe that this document breaches copyright please contact us providing details, and we will remove access to the work immediately and investigate your claim. LUND UNIVERSITY PO Box 117 221 00 Lund +46 46-222 00 00 Variation Factors in the Design and Analysis of Replicated Controlled Experiments { Three (Dis)similar Studies on Inspections versus Unit Testing Per Runeson, Andreas Stefik and Anneliese Andrews Lund University, Sweden, [email protected] University of Nevada, NV, USA, stefi[email protected] University of Denver, CO, USA, [email protected] Empirical Software Engineering, DOI: 10.1007/s10664-013-9262-z Self archiving version. -
Methods, Method Verification and Validation Volume 2
OOD AND RUG DMINISTRATION Revision #: 02 F D A Document Number: OFFICE OF REGULATORY AFFAIRS Revision Date: ORA-LAB.5.4.5 ORA Laboratory Manual Volume II 06/30/2020 Title: Page 1 of 32 Methods, Method Verification and Validation Sections in This Document 1. Purpose ....................................................................................................................................2 2. Scope .......................................................................................................................................2 3. Responsibility............................................................................................................................2 4. Background...............................................................................................................................3 5. References ...............................................................................................................................4 6. Procedure .................................................................................................................................5 6.1. Method Selection ...........................................................................................................5 6.2. Method Evaluation & Record .........................................................................................5 6.3. Standard Method Verification .........................................................................................5 6.3.1. Chemistry........................................................................................................ -
ETA Visible Emissions Observer Training Manual
Eastern Technical Associates Visible Emissions Observer Training Manual June 2013 Copyright © 1997-2013 by ETA i Eastern Technical Associates © Welcome Visible Emissions Observer Trainee: During the next few days you will be trained in one of the oldest and most common source measurement techniques – visible emissions observations. There are more people measuring visible emissions today than at any time in the 100-plus-year history of emissions observations. We have prepared this manual to assist you in your training, certification, and most important, field observations. It is impossible to give proper credit to all who developed and supported the technology that contributed to this manual. The list would probably be longer than the manual itself. We have been working in this field since 1970 and stand in the footprints of many innovators. Much of the material in this manual comes from the contributions of the many visible emissions instructors we have been privileged to work with as well as U.S. EPA documents and the contributions of our staff for more than 30 years. The purpose of this manual is to give you a hands-on, readable reference for the topics addressed in the classroom portion of our training. It should also be useful as a reference document in the future when you are a certified observer performing measurements in the field. Unfortunately, we cannot cover all of the possible situations you might encounter, but the guidance in this document combined with the training you receive in ETA’s classroom and field programs should enable you to make valid observations for more than 90% of the sources you observe. -
Description of Aoac Statistics Committee Generated Documents
DESCRIPTION OF AOAC STATISTICS COMMITTEE GENERATED DOCUMENTS ALTERNATIVE APROACHES FOR MULTI‐LAB STUDY DOCUMNTS. Alternative approaches approved by Committee on Statistics and by OMB. 1. *tr322‐SAIS‐XXXV‐Reproducibility‐from‐PT‐data.pdf: Discussion on how to obtain reproducibility from proficiency test data, and the issues involved. ……………………………… 2 2. tr333‐SAIS‐XLII‐guidelines‐for‐use‐of‐PT‐data.pdf: Recommended use of proficiency test data for estimating repeatability and reproducibility. ……………………………… 8 3. *tr324‐SAIS‐XXXVII‐Incremental‐collaborative‐studies.pdf: Proposed incremental collaborative studies to find repeatability and reproducibility via a sequential series of experiments. ……………………………... 11 4. tr326‐SAIS‐XXXIX‐Min‐degr‐freed‐for‐random‐factor‐estimation.pdf: The relationship of number of replicates or number of collaborators to precision of standard deviation for repeatability or reproducibility. ……………………………… 19 5. tr323‐SAIS‐XXXVI‐When‐robust‐statistics‐make‐sense.pdf: Caveats and recommendations on the use of so‐called ‘robust’ statistics in accreditation studies. ……………………………… 21 TRADITIONAL PATHWAY MULTI‐LAB STUDY DOCUMENTS AND INSTRUMENTS. Traditional study approach spreadsheet remaining as part of acceptable approaches. 6. JAOAC 2006 89.3.797_Foster_Lee1.pdf: Journal article by Foster and Lee on the number of collaborators needed to estimate accurately a relative standard deviation for reproducibility. ……………………………… 29 7. LCFMPNCalculator.exe: This program analyzes serial dilution assay data to obtain a most probable -
Basic Statistical Concepts for Sensory Evaluation
BASIC STATISTICAL CONCEPTS FOR SENSORY EVALUATION It is important when taking a sample or designing an experiment to remember that no matter how powerful the statistics used, the infer ences made from a sample are only as good as the data in that sample. No amount of sophisticated statistical analysis will make good data out of bad data. There are many scientists who try to disguise badly constructed experiments by blinding their readers with a com plex statistical analysis."-O'Mahony (1986, pp. 6, 8) INTRODUCTION The main body of this book has been concerned with using good sensory test methods that can generate quality data in well-designed and well-exe cuted studies. Now we turn to summarize the applications of statistics to sensory data analysis. Although statistics are a necessary part of sensory research, the sensory scientist would do well to keep in mind O'Mahony's admonishment: Statistical anlaysis, no matter how clever, cannot be used to save a poor experiment. The techniques of statistical analysis do, how ever, serve several useful purposes, mainly in the efficient summarization of data and in allowing the sensory scientist to make reasonable conclu- 647 648 SENSORY EVALUATION OF FOOD: PRINCIPLES AND PRACTICES sions from the information gained in an experiment One of the most im portant conclusions is to help rule out the effects of chance variation in producing our results. "Most people, including scientists, are more likely to be convinced by phenomena that cannot readily be explained by a chance hypothesis" (Carver, 1978, p. 587). Statistics function in three important ways in the analysis and interpre tation of sensory data. -
Understanding Cmm Specifications and Calibration Methods a Technical Presentation from the Leading Manufacturer of Metrology Instruments Education
UNDERSTANDING CMM SPECIFICATIONS AND CALIBRATION METHODS A TECHNICAL PRESENTATION FROM THE LEADING MANUFACTURER OF METROLOGY INSTRUMENTS EDUCATION Bulletin No. 2183 EDU-14003A-H Mitutoyo Institute of Metrology The Mitutoyo Institute of Metrology provides educational courses and on-demand resources across a wide variety of measurement related topics including basic inspection techniques, principles of dimensional metrology, calibration methods, and GD&T. Visit www.mitutoyo.com/education for details on the educational opportunities available from Mitutoyo America Corporation. About this Technical Presentation This technical presentation provides an overview of the specifications used to describe the accuracy of coordinate measuring machines (CMMs) along with the methods and tools used to calibrate CMMs in the field. The national and international standards used by all CMM manufacturers, including the ISO 10360 series, will be discussed. The history and purpose of standardized testing will also be briefly reviewed to provide understanding on how the calibration of CMMs © 2016 Mitutoyo America Corporation differs from other measuring equipment. This presentation will also discuss the role of CMM calibration in traceability and show how Mitutoyo America provides traceability to CMM calibrations. Coordinate Measuring Machines Vision Measuring Systems Form Measurement Optical Measuring Whatever your challenges are, Mitutoyo supports you from start to finish. Mitutoyo is not only a manufacturer of top-quality measuring products but one that also offers qualified support for the lifetime of the equipment, backed by comprehensive services that ensure your staff can make the very best use of the investment. Test Equipment Small Tool Instruments Sensor Systems Digital Scale and DRO Systems and Seismometers and Data Management Apart from the basics of calibration and repair, Mitutoyo offers product and metrology training, as well as IT support for the sophisticated software used in modern measuring technology. -
Guidance for the Validation of Analytical Methodology and Calibration of Equipment Used for Testing of Illicit Drugs in Seized Materials and Biological Specimens
Vienna International Centre, PO Box 500, 1400 Vienna, Austria Tel.: (+43-1) 26060-0, Fax: (+43-1) 26060-5866, www.unodc.org Guidance for the Validation of Analytical Methodology and Calibration of Equipment used for Testing of Illicit Drugs in Seized Materials and Biological Specimens FOR UNITED NATIONS USE ONLY United Nations publication ISBN 978-92-1-148243-0 Sales No. E.09.XI.16 *0984578*Printed in Austria ST/NAR/41 V.09-84578—October 2009—200 A commitment to quality and continuous improvement Photo credits: UNODC Photo Library Laboratory and Scientific Section UNITED NATIONS OFFICE ON DRUGS AND CRIME Vienna Guidance for the Validation of Analytical Methodology and Calibration of Equipment used for Testing of Illicit Drugs in Seized Materials and Biological Specimens A commitment to quality and continuous improvement UNITED NATIONS New York, 2009 Acknowledgements This manual was produced by the Laboratory and Scientific Section (LSS) of the United Nations Office on Drugs and Crime (UNODC) and its preparation was coor- dinated by Iphigenia Naidis and Satu Turpeinen, staff of UNODC LSS (headed by Justice Tettey). LSS wishes to express its appreciation and thanks to the members of the Standing Panel of the UNODC’s International Quality Assurance Programme, Dr. Robert Anderson, Dr. Robert Bramley, Dr. David Clarke, and Dr. Pirjo Lillsunde, for the conceptualization of this manual, their valuable contributions, the review and finali- zation of the document.* *Contact details of named individuals can be requested from the UNODC Laboratory and Scientific Section (P.O. Box 500, 1400 Vienna, Austria). ST/NAR/41 UNITED NATIONS PUBLICATION Sales No. -
Guidelines for Selecting and Using ISTA® Test Procedures and Projects
® GUIDELINES FOR SELECTING AND USING ISTA TEST PROCEDURES & PROJECTS Getting Started 2 Testing Rationale 2 Testing Expectations and Objectives 2-3 Testing as a Demonstration of Minimum Use of Packaging 3 Laboratory Tests and Distribution Hazards 3 Guidelines for Selecting and ® Types of ISTA Tests 4 Using ISTA Test Procedures Use of the ISTA Certification Mark After Testing 5 and Projects ISTA 7E Program and Using the ISTA Thermal 5 Certification Mark These Guidelines are intended to provide the user of ISTA® Test Procedures and Projects and other ISTA ISTA Responsible Packaging by Design Program 6 documents with insight and information on the protocols, and what factors to consider in selection, Specialized Test Protocols Developed by ISTA 6 use, and results interpretation. Member Performance Tests 6 Special Considerations for ISTA Procedures & Projects 6-7 PREFACE The International Safe Transit Association (ISTA) is a global Know Your Distribution Environment 7 alliance of shippers, carriers, suppliers, testing laboratories, and educational and research institutions focused on the Product Damage Tolerance and Package 7 Degradation Allowance specific concerns of transport packaging. We help our members control costs, damage, and resources during the Face, Edge and Corner Identification 7-8 distribution of packaged-products by: Samples and Replicate Testing 8 1. Creating and publishing laboratory preshipment Testing Retesting 8 Procedures Retesting Based on Changes in Corrugated Board 8-9 2. Certifying Packaging Laboratories Return Distribution -
TAPPI Standards: Regulations and Style Guidelines
TAPPI Standards: Regulations and Style Guidelines REVISED January 2018 1 Preface This manual contains the TAPPI regulations and style guidelines for TAPPI Standards. The regulations and guidelines are developed and approved by the Quality and Standards Management Committee with the advice and consent of the TAPPI Board of Directors. NOTE: Throughout this manual, “Standards” used alone as a noun refers to ALL categories of Standards. For specific types, the word “Standard” is used as an adjective, e.g., “Standard Test Method,” “Standard Specification,” “Standard Glossary,” or “Standard Guideline.” If you are a Working Group Chairman preparing a Standard or reviewing an existing Standard, you will find the following important information in this manual: • How to write a Standard Test Method using proper terminology and format (Section 7) • How to write TAPPI Standard Specifications, Glossaries, and Guidelines using proper terminology and format (Section 8) • What requirements exist for precision statements in Official and Provisional Test Methods (Sections 4.1.1.1, 4.1.1.2, 6.4.5, 7.4.17). • Use of a checklist to make sure that all required sections have been included in a Standard draft (Appendix 4). • How Working Group Chairman, Working Groups, and Standard-Specific Interest Groups fit into the process of preparing a Standard (Section 6.3, 6.4.1, 6.4.2, 6.4.3, 6.4.4, 6.4.6, 6.4.7). • How the balloting process works (Sections 6.4.6, 6.4.7, 6.4.8, 6.4.9) • How to resolve comments and negative votes (Sections 9.5, 9.6, 9.7) NOTE: This document covers only the regulations for TAPPI Standards, which may include Test Methods or other types of Standards as defined in these regulations. -
Form and Style for ASTM Standards
ASTM INTERNATIONAL Helping our world work better Form and Style for ASTM Standards OctoberJanuary 2015 2016 Copyright ©2016 ASTM International, West Conshohocken, PA. Prior editions copyrighted 2015 and earlier, by the American Society for Testing and Materials. All rights reserved. This material may not be reproduced or copied, in whole or in part, in any printed, mechanical, electronic, film, or other distribution and storage media, without the written consent of the publisher. Contents Preface ii Introduction iii Definitions iv Part A. Form of ASTM Test Methods A-1 Part B. Form of ASTM Specifications B-1 Part C. Form of Other Types of ASTM Standards C-1 Part D. Use of the Modified Decimal Numbering System D-1 Part E. Terminology in ASTM Standards E-1 Part F. Caveats and Other Legal Aspects in Standards—Special Instructions F-1 Part G. Standards Style Manual G-1 Part H. Use of SI Units in ASTM Standards H-1 Annex A. SI Quick Reference Guide Annex-1 Summary of Changes Changes-1 Index Index-1 Form and Style for ASTM Standards www.astm.org i Preface ASTM International (hereafter referred to as ASTM International or ASTM), founded in 1898, is a scientific and technical organization formed for “the development of standards on characteristics and performance of materials, products, systems, and services; and the promotion of related knowledge.” It is the world’s largest source of vol- untary consensus standards. The purpose of this manual is to promote uniformity of form and style in ASTM standards. Such uniformity is desir- able because it helps the user to find what is needed more easily and to understand what is read more quickly. -
ASTM International/Definitions and Sample Standards
ASTM International/Definitions and Sample Standards standard, n—as used in ASTM International, a document that has been developed and established within the consensus principles of the Society and that meets the approval requirements of ASTM procedures and regulations. DISCUSSION—The term “standard” serves in ASTM International as a nominative adjective in the title of documents, such as test methods or specifications, to connote specified consensus and approval. The various types of standard documents are based on the needs and usages as prescribed by the technical committees of the Society. Definitions for the types of ASTM International standards (classification, guide, practice, specification, terminology, and test method) are quoted below from the current Regulations Governing ASTM Technical Committees. Select the link identifying each type of standard to view a sample. NOTE: These documents may only be used by student members for study purposes only, and not for any other distribution, republication, or resale. No further reproduction of these documents, in full or part, without the expressed written permission of ASTM, is authorized. classification, n—a systematic arrangement or division of materials, products, systems, or services into groups based on similar characteristics such as origin, composition, properties, or use. guide, n—a compendium of information or series of options that does not recommend a specific course of action. DISCUSSION—A guide increases the awareness of information and approaches in a given subject area. practice, n—a definitive set of instructions for performing one or more specific operations that does not produce a test result. DISCUSSION—Examples of practices include, but are not limited to: application, assessment, cleaning, collection, decontamination, inspection, installation, preparation, sampling, screening, and training.