401 the Development of the Sullivan Mine and Processes for the Treatment of Its Ores
Total Page:16
File Type:pdf, Size:1020Kb
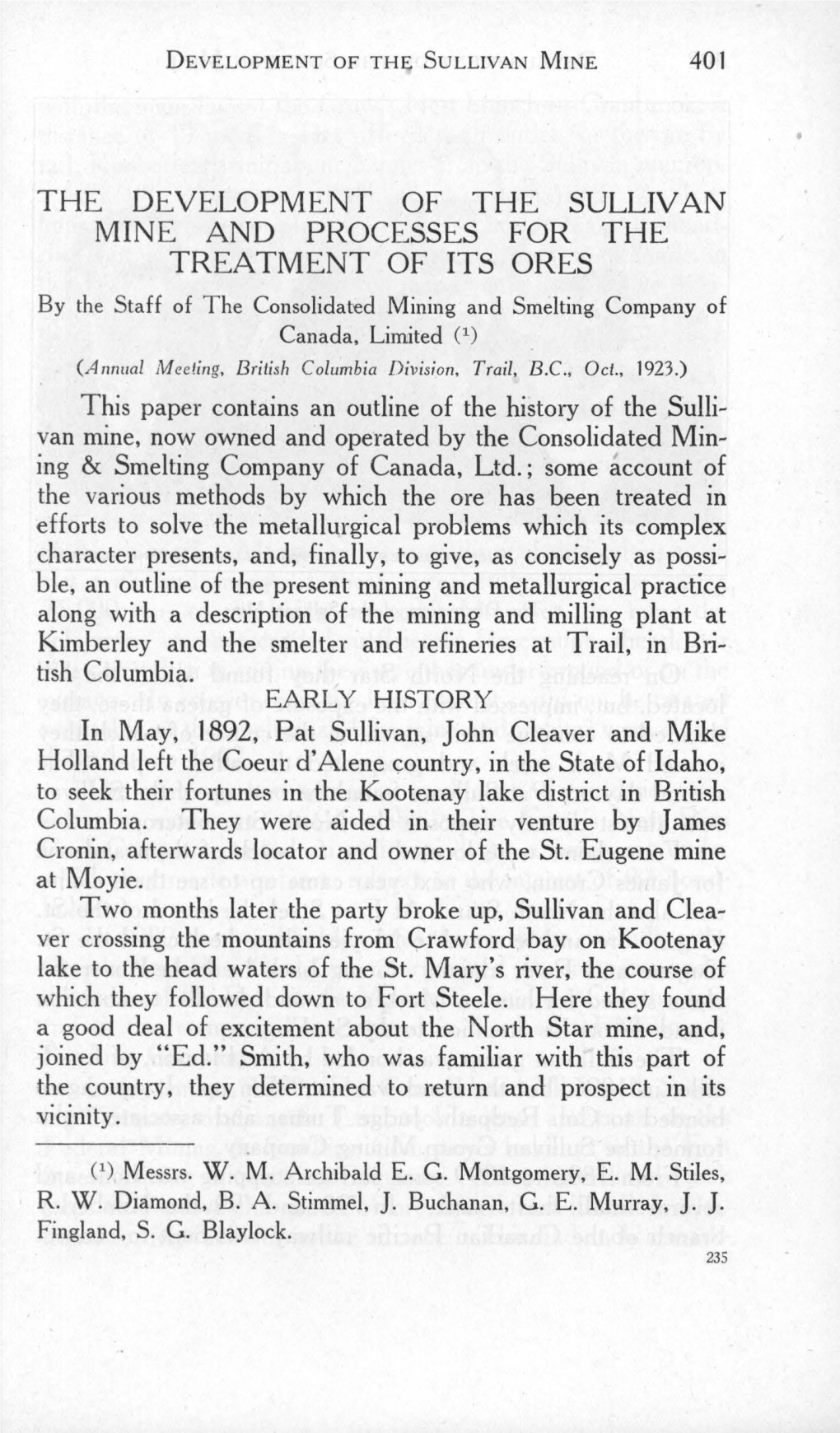
Load more
Recommended publications
-
BOOM DAYS in HANCOCK COUNTY Or a History of Mining in the Towns of Hancock and Sullivan, Maine
BOOM DAYS IN HANCOCK COUNTY or A History of Mining in the Towns of Hancock and Sullivan, Maine By Henry B. Gallison U. of M. '35 As partial, fulfillment of the requirements of Ed 52 - History of Education in Maine. 2 . Foreword I must confess that in choosing this subject I did not expect to find so much material as I have succeeded in doing. I am not sorry; I am glad. I knew from hearsay and from the older folk of the region that there had been a great deal of excitement at one time, but I did known when the boom had taken place when I started my research. I had never heard of any report being published on the subject, and as a matter of fact, no comprehensive report has ever been written. Scattered reports on different phases of the work are here brought together for what I take to be the first time. All material used is source material, and I am only sorry that time will not allow me to go further than I have. The Library at Harvard College and the Library at Bowdoin both, contain reports which I should have like to read and incorporate into this report; and the Ellsworth American, a newspaper that was published weekly in Hancock County during those hectic days as well as at the present time, must have contained some truly classic stories about the boom. This narrative, then, must remain embellished by the personal incidents which would so liven it, and be only a statement of facts. -
Zinc Information Circular
The British Columbia Ministry of Energy and Mines MINFILE database contains 4510 zinc occurrences; of these occurrences, 589 list zinc as the primary commodity. There are 569 past producers, and one recent producer, Myra Falls Zinc in British Columbia (092F 330). B.C.’s largest producer was the Sullivan Mine (082FNE052), which yielded nearly 8 million tonnes of zinc British Columbia Geological Survey over 100 years of production. Information Circular 2015-12 Global production of zinc in 2014 was approximately 12 million tonnes. Most (60%) is used for galvanizing steel, 15% Akie for zinc based alloys used in die casting, 14% for brass and Owned and operated by Canada Zinc Metals Corp. bronze, 8% for compounds containing zinc oxide or zinc SEDEX Zn-Pb-Ag in Paleozoic basin (Kechika Trough) sulphate, and most of the remainder is used in other alloys Advanced exploration project with drill indicated resources (source: International Zinc Association). (see table). Resources are open to expansion Zinc Resources Deposit Category Grades Au Ag Year t (x106) %Zn %Cu %Pb (g/t) (g/t) Cirque Hist 38.5 8 2.2 47.2 1991 North Cirque Hist 15.5 6.9 1.4 32 South Akie Ind 12.7 8.4 1.7 13.7 2012 Inf 16.3 7.4 1.3 11.6 Myra Falls M+I 7.36 6.41 1 0.66 1.72 66.31 2014 Inf 2.08 6.13 0.54 0.71 2.22 109.53 Cirque Ruddock M+I 6.2 6.5 1.3 2013 Creek5 Inf 6.7 6.33 1.2 Joint venture between Teck Resources Limited (50%), 2 Tulsequah3 Ind 6.8 5.9 1.2 1.1 2.4 85 2012 and Korea Zinc Co., Ltd. -
00Sullivangac-Mdd.Pdf
15. THERMOBAROMETRIC CALCULATION OF PEAK METAMORPHIC CONDITIONS OF THE SULLIVAN DEPOSIT Glen R. De Paoli1 and David R.M. Pattison2 1 2739 4th Ave N.W., Calgary, Alberta T2N 0P9 2 Department of Geology and Geophysics, The University of Calgary, 2500 University Drive N.W., Calgary, Alberta T2N 1N4 ABSTRACT The Sullivan Zn-Pb-Ag mine in southeastern British Columbia is a mid-Proterozoic sedimentary exhalative deposit that has been metamorphosed to transitional greenschist-amphibolite grade. The mineral textures are predominantly of metamorphic origin. There are no significant differences in silicate mineral compositions between sulphide-rich litholo- gies and silicate-rich lithologies. High modal abundance of Mn-rich garnet in some rocks indicates a Mn-rich phase was likely part of the pre-metamorphic mineral assemblage. Metamorphic conditions were estimated using multi-equi- librium thermobarometric techniques involving silicate-carbonate equilibria. Peak metamorphic temperature estimated by the garnet-biotite Fe-Mg exchange equilibrium is 450oC ± 50oC. Lower temperature estimates from some samples are interpreted to record the temperature of cessation of garnet growth prior to the attainment of peak metamorphic tem- perature. Peak metamorphic pressure determined from equilibria applicable to the assemblage garnet-biotite-mus- covite-chlorite-calcite-quartz-fluid is 380 MPa ± 100 MPa (equivalent to approximately 14 km of burial). The fluid composition accompanying this pressure estimate is XH2O = 0.38, XCO2 = 0.62 ± 0.07. The P-T estimates are con- sistent with burial metamorphism during Proterozoic times. INTRODUCTION PETROGRAPHY The Sullivan mine, in southeastern British Columbia, is a Samples were classified into three rock types on the basis of sedimentary exhalative Zn-Pb-Ag orebody which was bulk mineralogy: silicate matrix rocks, sulphide matrix deposited in mid-Proterozoic times. -
Mining and the Public
Proceedings of the 17th Annual British Columbia Mine Reclamation Symposium in Port Hardy, BC, 1993. The Technical and Research Committee on Reclamation MINING AND THE PUBLIC 'THE SULLIVAN EXPERIENCE' by Andrew Whale B.C. Energy Mines and Petroleum Resources Fernie, B.C. Ron Simkus Cominco Ltd, Sullivan Mine Kimberley, B.C. Laura Duncan East Kootenay Environmental Society Kimberley, B.C. ABSTRACT In 1990, Cominco Ltd announced the indefinite closure of the Sullivan Mine, stimulating concerns from the community of Kimberley, regarding environmental protection and mine reclamation. The B.C. Ministry of Energy Mines and Petroleum Resources (MEMPR) established a Public Liaison Committee (SPLC) to review the Sullivan Mine Decommissioning and Closure Plan. This committee, open to participation by all interested parties, was formed to provide local public input to the Reclamation Advisory Committee on the terms and conditions of the Mines Act Reclamation Permit. The East Kootenay Environmental Society, through the commitment of two of its members, has participated very extensively in the public review process. Through an open exchange between the committee's constituent groups and through Cominco's active support, understanding of diverse needs and concerns was achieved without wasteful confrontation. The paper describes the success of this process, the evolution of the committee and the unique format of the process. 45 Proceedings of the 17th Annual British Columbia Mine Reclamation Symposium in Port Hardy, BC, 1993. The Technical and Research Committee on Reclamation INTRODUCTION The Sullivan Public Liaison Committee (SPLC) was formed in 1991 to review the contents of and provide recommendations on the decommissioning and closure plan for the Sullivan Mine in Kimberley, British Columbia. -
Tourmaline - a Prospecting Guide for Massive Base-Metal Sulfide Deposits in the Penobscot Bay Area, Maine
University of Southern Maine USM Digital Commons Maine Collection 6-1980 Tourmaline - A Prospecting Guide for Massive Base-Metal Sulfide Deposits in the Penobscot Bay Area, Maine John F. Slack Follow this and additional works at: https://digitalcommons.usm.maine.edu/me_collection Part of the Geochemistry Commons, Geology Commons, Geomorphology Commons, Mineral Physics Commons, Other Earth Sciences Commons, Sedimentology Commons, Stratigraphy Commons, Tectonics and Structure Commons, and the Volcanology Commons Recommended Citation Slack, John F., "Tourmaline - A Prospecting Guide for Massive Base-Metal Sulfide Deposits in the Penobscot Bay Area, Maine" (1980). Maine Collection. 124. https://digitalcommons.usm.maine.edu/me_collection/124 This Book is brought to you for free and open access by USM Digital Commons. It has been accepted for inclusion in Maine Collection by an authorized administrator of USM Digital Commons. For more information, please contact [email protected]. Maine Geological Survey DEPARTMENT OF CONSERVATION Augusta, Maine 04333 TOURMALINE--A PROSPECTING GUIDE for MASSIVE BASE-METAL SULFIDE DEPOSITS in the PENOBSCOT BAY AREA, MAINE by John F. Slack U.S. Geological Survey Reston, Virginia 22092 Special Economic Studies Series No. 8 June, 1980 Walter A. Anderson, State Geologist TABLE OF CONTENTS Page ABSTRACT-------------------------------------------------------- 1 INTRODUCTION---------------------------------------------------- 2 GEOLOGIC SETTING------------------------------------------------ 2 MASSIVE SULFIDE -
Earth & Space Sciences 345: Economic Geology
Earth & Space Sciences 345: Economic Geology Introductory example – the Broken Hill Ag-Pb-Zn deposit: To introduce the class with some basic ideas, unusual geology, and strange words, here’s a brief history of the Broken Hill deposit (see also: http://en.wikipedia.org/wiki/Broken_Hill_ore_deposit and http://en.wikipedia.org/wiki/BHP_Billiton (section on the history of Broken Hill Proprietary Co): Remote location in far western New Nondescript black hill first staked by South Wales, Australia Charles Rasp (a boundary rider on a sheep station). Originally prospected as a tin deposit (though interest in silver had been aroused by earlier finds and mining at Silverton nearby). What Rasp found was a gossan, a surficial mass of iron-oxide that can form when reactive sulfide minerals are exposed to oxygen and water. Some gossans conceal underlying metal sulfide deposits. Others are uninteresting (e.g. formed at the expense of pyrite, or mafic silicate minerals). Initial assay revealed no tin, some Pb, and a trace of Ag. Rasp and his partners persisted, staked the whole of the exposed hill, and eventually reached rich deposits of Ag, Pb and Zn which turned out to be wildly profitable. The mineralogy of the upper oxidized zone of the deposit is interesting. Silver occurred as the native metal, various metal alloys (e.g. dyscrasite Ag Sb) and in 3 halides such as chlorargyrite AgCl and bromargyrite AgBr. Lead and zinc occurred in a variety of oxide, carbonate, sulfate and phosphate minerals. The deposit was enriched in other unusual elements such as Mn and Ba, which we now recognize as a clue to its origin. -
Sullivan Mine: Water Collection Closure Plan Vs. 10 Yrs Post-Closure Experience Authors: Michelle Unger, Bsc
Sullivan Mine: Water Collection Closure Plan vs. 10 yrs Post-Closure experience Authors: Michelle Unger, BSc. & Dave van Dieren, P.Eng Introduction Description of Site Reclamation and Seepage Collection Systems Post Closure Projections and Current Experience: - Underground Mine filling, dewatering flows, water quality and metal loading - Mine Area Seepage flows, water quality and metal loading - Tailings Area Seepage flows, water quality and metal loading Summary of Results Sullivan Mine Location Sullivan Mine History and Layout Mine and Mill areas Subsidence Area Mine Site and Lead, Zinc and Silver Waste Dumps Operated 1909 –2001 City of Primarily underground, some open pit Kimberley 150 million tonnes ore Mill Site and Production (tonnes): Tailings Concentrate: 25.8 million Waste rock: 9.8 million Mark Creek Tailings: 122 million Total area of disturbance: 1100 ha Environmental Concerns: Acid Rock Drainage (ARD) Sulphide oxidation: Historic Photo of Pyrrhotite and pyrite No. 1 Shaft Waste Dump Principal Ore: • Galena and sphalerite ARD impacts to surface water and groundwater : • mine workings; • waste dumps; Historic Photo of North and South Waste Dumps adjacent to Mark Creek Environmental Concerns: Acid Rock Drainage (ARD) Sulphide oxidation: Pyrrhotite and pyrite Principal Ore: • Galena and sphalerite ARD impacts to surface water and groundwater: • mine workings; • waste dumps; and • tailings impoundments Historic Photo of Tailings produced by Concentrator Review Reclamation Plan Revised Decommissioning and Closure Plan 2000 Main Objectives: Wildlife habitat ARD collection and treatment for perpetuity Reclamation progressive from 1990 to 2010 Review Reclamation Plan: Mine Site . Source Control: . Rock from the Open Pit Waste Dump was placed in the Open Pit. -
The Consolidated Mining and Smelting Company of Canada Limited
Report of the Directors of The Consolidated Mining and Smelting Company of Canada Limited 11 For twelve months ending December 31, 1927 BOARD OF DIRECTORS JAMES J. WARREN, Montreal - - President E. W. BEATTY. K.C. Montreal W. A. BLACK Montreal S. G. BLAYLOCK - Trail, B.C. J. C. HODGSON - Montreal SIR HERBERT HOLT - Montreal HENRY JOSEPH - Montreal W. L. MATTHEWS - - Toronto SIR VINCENT MEREDITH. BART Montreal F. GORDON OSLER Toronto J. K. L. ROSS Montreal J. E. RILEY, Secretary THE TORONTO GENERAL TRUSTS CORPORATION, TORONTO THE ROYAL TRUST COMPANY - - MOXTREAL The Consolidated Mining and Smelting Company of Canada, Limited DIRECTORS REPORT To the Shareholders of The Consolidated Mining and Smelting Company of Canada, Limited: Gentlemen :- Your Directors submit the twenty-second Financial State- ment along with the reports of the General Manager, the Manager of Mines, the Comptroller, and the Manager of Sales. As usual the report of thc West Kootenay Power and Light Company, Limited, is included. After providing for current development, depreciation of plant, depletion of property and adding $62,993.74 to the Fire Insurance Reserve, the net profits were $13,139,957.92, as compared with $13,915,262.44 in 1926. Capital Expenditure during the year amounting to $3,590,506.77 was added to the reserve for Additions to Property through Profitand Loss, ascompared with $2,274,771.66 in 1926. Your Directors think it wise to add another $1,000,000.00 to the Contingent Reserve. After deducting these sums and Federal and Provincial Taxes (amonnting to $1,388,089.30) aud providing for Dividends Numbers 46 and 47, the remainder, $801,586.85, was added to the Profit and Loss Account. -
Sullivan Mine Fatalities and the Role of Air Quality in Mine-Related Incidents
SULLIVAN MINE FATALITIES AND THE ROLE OF AIR QUALITY IN MINE-RELATED INCIDENTS M. PhillipA, D. HockleyB, B. DawsonC AO’Kane Consultants USA, 3510 Hwy 1 West, Anaconda, MT, USA 59711 BSRK Consulting Inc, Suite 2200, 1066 W Hastings Street, Vancouver, BC, Canada V6E 3X2 CTeck Cominco Metals Ltd, 601 Knighton Rd, Kimberley, BC, Canada V1A 1C7 ABSTRACT During May 15 – 17, 2006, four fatalities occurred at a partially reclaimed waste rock dump at the closed Teck Cominco Sullivan Mine near Kimberley, British Columbia, Canada. The fatalities occurred at the toe of the dump in a seepage monitoring station that is connected hydraulically, via a pipe and dump toe drain, to the covered acid generating waste rock. Since August 2006, the dump has been heavily instrumented and studied in stages. Results have shown that atmospheric air temperature, not barometric pressure, is the dominant control on air movement between the waste dump and the atmosphere. This air movement, which changes direction seasonally, results in a gas containing elevated carbon dioxide and depressed oxygen exiting the dump. Air quality has been a historic mining issue that is now managed with testing methods and modern ventilation. Advancements aside, air quality remains an issue for current operations and legacy sites. This paper presents recent results of the Sullivan Mine fatalities technical investigations and reviews historic and recent incidents involving poor air quality at mine sites. INTRODUCTION During May 15 – 17, 2006, four fatalities occurred at the partially reclaimed No. 1 Shaft Waste Dump at the closed Teck Cominco Sullivan Mine near Kimberley, British Columbia, Canada (see Figure 1). -
Sedimentary Exhalative (Sedex) Zinc-Lead-Silver Deposit Model
Sedimentary Exhalative (Sedex) Zinc-Lead-Silver Deposit Model Chapter N of Mineral Deposit Models for Resource Assessment Scientific Investigations Report 2010–5070–N U.S. Department of the Interior U.S. Geological Survey Zn Pb Fe 7 MILLIMETERS Cover. Polymictic sedimentary conglomerate overlying rhythmically laminated high-grade sphalerite and galena ore from the I 3/4 horizon in McArthur River (HYC) deposit, Australia. Inset shows scanning micro x-ray fluorescence (XRF) map of zinc (Zn), lead (Pb), and iron (Fe) concentrations. Deformation and partial truncation of fine, chemically graded laminae at contact with conglomeratic base of the overlying turbidite and intralaminar deformation together indicate deposition and modification through sea-floor processes, suggesting ore was deposited syndepositionally as a chemical sediment on the sea floor. Sedimentary Exhalative (Sedex) Zinc-Lead-Silver Deposit Model By Poul Emsbo, Robert R. Seal, George N. Breit, Sharon F. Diehl, and Anjana K. Shah Chapter N of Mineral Deposit Models for Resource Assessment Scientific Investigations Report 2010–5070–N U.S. Department of the Interior U.S. Geological Survey U.S. Department of the Interior SALLY JEWELL, Secretary U.S. Geological Survey Suzette M. Kimball, Director U.S. Geological Survey, Reston, Virginia: 2016 For more information on the USGS—the Federal source for science about the Earth, its natural and living resources, natural hazards, and the environment—visit http://www.usgs.gov or call 1–888–ASK–USGS. For an overview of USGS information products, including maps, imagery, and publications, visit http://store.usgs.gov. Any use of trade, firm, or product names is for descriptive purposes only and does not imply endorsement by the U.S. -
Origin of the Mineral Deposits
ORIGIN OF THE MINERAL DEPOSITS VOLCANIC EXHALATIVE PROCESS Group No 03 Ore is solid naturally occurring body metallic ferrous mineral or aggregate with metallic ferrous mineral more or less mixed with gangue mineral and it should mine economically extract. When concerning the processes of formation of ore bodies, it can be subdivided into two main processes as 1. Primary Processes 2. Secondary Processes So these processes can be subdivided further more as follows. Theories of ore formation Primary Processes Secondary Processes INTERNAL PROCESSES EXTERNAL PROCESSES Magmatic Crystallization Mechanical Accumulation Magmatic segregation Sedimentary Precipitation Lateral Segregation Residual Process Hydrothermal Process Secondary ore supergene Metamorphic Process Enrichment Volcanic Exhalative process More than one above processes is responsible in forming of an ore body. Today we have to discuss about the Volcanic Exhalative (Sedimentary Exhalative) Process. VOLCANIC EXHALATIVE PROCESS(SEDIMENTARY EXHALATIVE PROCESS This is exhalations of sulfide rich magmas at the surface, usually under marine conditions. The deposits form from this process can be known as volcanic exhalative Deposits. These are group of deposits which are known as exhalities including massive sulfide ores. These ores frequently shows a spatial relationship to volcanic rocks. These Volcanic associated types principle constituent is Pyrite with varying amount of copper, Lead, Zinc & Barite together with other minerals may be present. For many decades they were concern as epigenetic replacement hydrothermal ore bodies which, a deposit introduced into the host rocks at some time after they were deposited .But later they were concern as syngenetic which A deposit formed at the same time as the rocks in which it occurs. -
SEDIMENTARY EXHALATIVE ZN-PB-AG DEPOSITS (MODEL 31A; Briskey, 1986)
SEDIMENTARY EXHALATIVE ZN-PB-AG DEPOSITS (MODEL 31a; Briskey, 1986) by Karen D. Kelley, Robert R. Seal, II, Jeanine M. Schmidt, Donald B. Hoover, and Douglas P. Klein SUMMARY OF RELEVANT GEOLOGIC, GEOENVIRONMENTAL, AND GEOPHYSICAL INFORMATION Deposit geology Lens-like bodies of stratiform sulfide minerals (lead, zinc, ± iron) as much as a few tens of meters in thickness are interbedded with fine-grained dark clastic and chemical sedimentary rocks. These deposits may have large lateral extent (hundreds of meters to kilometers). Mineralized rock varies from a single layer to numerous bodies that may be vertically stacked or lateral equivalents. The most common associated sulfate mineral is barite which may be peripheral to or stratigraphically above the deposit (Rammelsberg and Meggen, Germany; Tom, Yukon Territory; Lady Loretta, Australia; and Red Dog, Alaska), or it may form crudely segregated mixtures with sulfide minerals (Cirque, British Columbia). Many deposits have no associated barite (HYC, Australia; Sullivan, British Columbia; and Howard's Pass, Yukon Territory). Stockwork, disseminated, or vein-type ore, interpreted as feeder zones to stratiform mineralized rock, are sometimes found underlying or adjacent to stratiform ore and are sometimes accompanied by alteration of footwall rocks (fig. 1). U.S. Bureau of Mines (1993) statistics show that in 1993 the two mines in the United States with greatest zinc output were Red Dog, Alaska and Balmat, N.Y. In 1994, the Red Dog mine produced 533,500 t of zinc concentrate with an average grade of 55.8 weight percent zinc (Mining Journal, 1995). Mines in the Balmat district produced 499,000 t in 1993.