Task Analysis and Synthesis As Well As Work Structuring
Total Page:16
File Type:pdf, Size:1020Kb
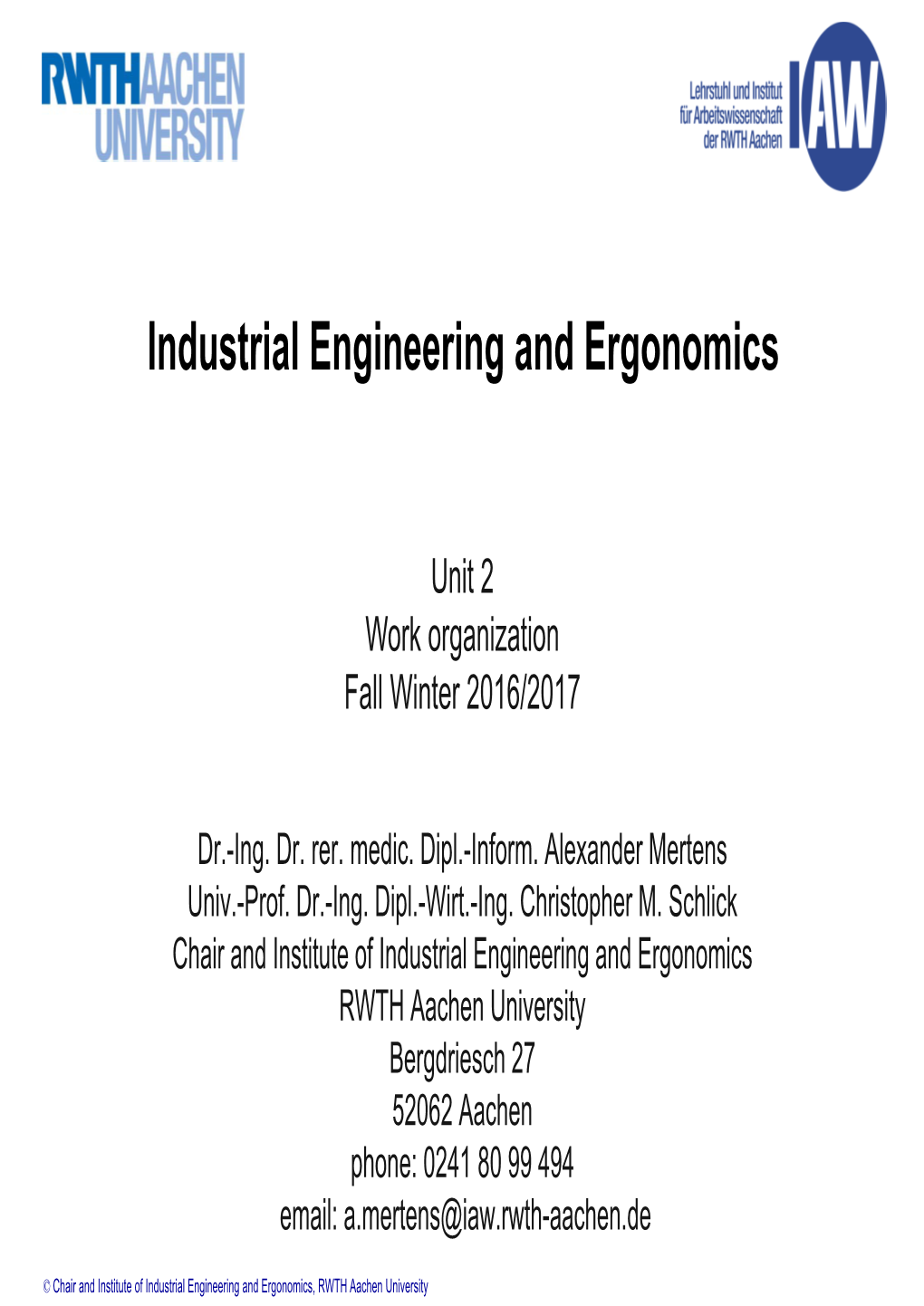
Load more
Recommended publications
-
Workplace Ergonomics Control Work Processes to Avoid Strains and Sprains
Ergonomics Workplace ergonomics Control work processes to avoid strains and sprains Ergonomics is about fitting the task to the • Provide adjustable workstations, anti-fatigue Ergonomics risk individual. It’s an important part of employee mats, and footrests. factors: safety and health, whether you work in an • Use and promote proper body mechanics. office, on a factory floor, or other environment. Posture: Can you • Maintain neutral postures; redistribute maintain a neutral Good ergonomics can improve efficiency posture while and productivity as well as reduce the risk of loads to larger muscle groups. performing the task? strains and sprains. • Adjust lighting higher or lower to suit the task. (Neutral posture supports the natural If you observe risk factors in your • Minimize exposure to heat and cold. curve of the spine and workplace, look for ways to modify the task to body alignment, and minimize the impact on employees. Here are Match the tool to the task. can be sustained with some guidelines: • Avoid pinch grip or repetitive gripping; allow minimal effort.) Do you avoid awkward and Optimize the process. power grip for forceful tasks. static postures? • Place frequently used items within arm’s • Spread contact over several fingers. Frequency and reach; provide easy access to the load. • Consider how tool design (shape, contour duration: How often do texture) makes it harder or easier to grip. you repeat the same • Mechanize operations; use gravity, carts, motion or motions? and conveyors when possible. • Reduce or isolate equipment vibration. How much time do you spend performing the • Break down the load. Lift fewer items at • Consider inline vs. -
Empowerment Job Design and Satisfaction of the Blue-Collars’ Motivational Needs
Empowerment job design and satisfaction of the blue-collars’ motivational needs A case study of Étoile du Rhône and Rastatt Mercedes- Benz factories Authors: Hong Nguyen Edouard de Willermin Supervisor: Karl Johan Bonnedahl Student Umeå School of Business and Economics Spring semester 2015 Master thesis, one-year, 15 hp Nguyen & de Willermin, 2015 ABSTRACT The main purpose of this research is to study the impact of the empowerment Job Design (JD) techniques on the satisfaction of the blue-collars’ motivational needs in the context of assembly line system in the automotive industry. We have developed this purpose aiming to make a theoretical contribution due to the fact that only a few studies were developed and were linked to the empowerment model developed by Conger and Kanungo (1988) which is a JD model relevant for the context of assembly line work which is qualified as repetitive and monotone. To fulfil this gap, we have established a conceptual model based on the empowerment model developed by Conger and Kanungo (1988) and theories of motivational needs. We conducted our thesis with the following research question as guideline: What are the effects of the empowerment job design on the satisfaction of the blue- collars’ motivational needs in an automotive assembly line system context? Our objective of this research question was: to study the impact of the empowerment Job Design techniques on the blue-collars’ motivational needs thanks to a case study as research design. This research is made independently to the effects of the context on the blue-collar’s motivation. We have conducted a quantitative study from a positivist and objectivist perspective in two MB (Mercedes-Benz) factories: ELC Étoile du Rhône in France (sample part factory) and Rastatt MB (engine factory) in Germany. -
Effect of Job Enlargement on Employee Performance at the Rift Valley Railways (K) Ltd
EFFECT OF JOB ENLARGEMENT ON EMPLOYEE PERFORMANCE AT THE RIFT VALLEY RAILWAYS (K) LTD GICHUKI MARY MWIHAKI D61/74359/2014 A RESEARCH PROJECT SUBMITTED IN PARTIAL FULFILMENT OF REQUIREMENTS FOR THE AWARD OF THE DEGREE OF MASTER OF BUSINESS ADMINISTRATION, SCHOOL OF BUSINESS, UNIVERSITY OF NAIROBI DECEMBER 2017 DECLARATION This research project is my original work and has never been submitted for examination to any other University. Signature…………………………….. Date……………………………… GICHUKI MARY MWIHAKI D61/74359/2014 This research project has been submitted with my authority as the university supervisor. Signature……………………………………. Date.................................................... DR. MERCY MUNJURI LECTURER, SCHOOL OF BUSINESS, UNIVERSITY OF NAIROBI. ii ACKNOWLEDGEMENT I want to I wish to thank a few individuals and groups that supported me to complete this research project. My sincere appreciation goes to my supervisor, Dr. Mercy Munjuri for her guidance and advice when I was writing this project. Rift Valley Railways (K) LTD, for accepting my request to collect data and to my family and friends, for their encouragement to finish this project. Lastly, I thank God for giving me good health throughout my studies. iii DEDICATION This project is devoted to my parents, Mr. and Mrs. Gichuki for instilling in me virtues of discipline and hard work. iv TABLE OF CONTENTS DECLARATION.......................................................................................................... ii ACKNOWLEDGEMENT ........................................................................................ -
Opportunities, More Concerns: a Look at the Reactionary Nature of Whistleblower Protections in a Growing Global Economy
MORE OPPORTUNITIES, MORE CONCERNS: A LOOK AT THE REACTIONARY NATURE OF WHISTLEBLOWER PROTECTIONS IN A GROWING GLOBAL ECONOMY Jake Smith TABLE OF CONTENTS I. INTRODUCTION ........................................................................................... 381 II. WHISTLEBLOWER PROTECTION LAWS IN THE UNITED STATES .... 383 A. History of Whistleblower Protections in the United States ....................... 384 1. Public Sector Whistleblower Protections ............................................... 384 2. Private Sector Whistleblower Protections .............................................. 385 B. The Sarbanes-Oxley Act ............................................................................ 387 C. The Dodd-Frank Wall Street Reform and Consumer Protection Act ........ 390 D. Edward Snowden, Public Sector Whistleblower Protections in US Today ........................................................................................................................ 393 III. GERMAN WHISTLEBLOWER PROTECTION LAWS ............................. 396 A. German Whistleblower Protections of the Past ......................................... 396 1. Germans Whistleblowing in Germany ................................................... 398 2. Siemens Scandals and International Whistleblowing ............................. 399 B. German Whistleblower Protections in 2020 .............................................. 400 IV. AUSTRALIAN WHISTLEBLOWER PROTECTION LAWS ..................... 402 A. Australian Whistleblower Protections of the Past .................................... -
Role of Job Enrichment and Job Enlargement in Work Life Balance
Global Journal of Finance and Management. ISSN 0975-6477 Volume 6, Number 3 (2014), pp. 239-244 © Research India Publications http://www.ripublication.com Role of Job Enrichment and Job Enlargement in Work Life Balance Sarika Sushil Department of Commerce & Business Administration, University of Allahabad, Abstract There has been a tremendous change in the business environment in the past few years. The organizations in the world are competing globally and giving birth to a very tough competition. The rising of intense competition have made three words echo in the mind of every employee that is targets, deadlines and performance which in turn has created stress in their minds and imbalance in work and family life. This has affected the efficiency and effectiveness of the organization as well as the growth and development of employees. Work-Life Balance is an essential requirement for sustainability of business as it improves the quality of life for everyone. It is believed that this creates a win – win situation as employees become more productive if they are satisfied and happy in their jobs. Not only this, balance is created between work commitments and family life. Job Enrichment and Job Enlargement are the two important techniques of job design which increase the motivational level of employees and job satisfaction which is essential for achieving work life balance and ultimately sustainability in business. The paper is an attempt to focus the significance of work life balance in attaining business sustainability, role of job enrichment and job enlargement in work life balance and identifying practices to rectify the imbalance in work and family life. -
On the Codingdemise of Job Enrichment. Technical Yale
e ,DOCUMENT RESUME -ED 109 350 ,'_GE 004 133 AUTHOR; j-7!4Hackman, J. Richard TITLE ---On the CodingDemise of Job Enrichment. Technical Report No. 9. INSTITUTION Yale Univ., New Haven; Conn: Dept. of Administrative - Sciences. SPONS AGENCY Manpower Administration (DOL), .Washington, D.C.; Office-of Naval Research, Washington, D.C. _Organizational EffeCtiveness Research Program. REPORT. NO bLHA-21-09-74-14-5 - PUB DATE Dec 74 NOTE , 33p. EDRS _PRICE ° MF-$0.76 HC-$1.95-PLUS POSTAGE DESCRIPTORS Attitudes; Automation; Evaluation;-Failure_Factors; *Job Development; *Job Satisfaction; 'Motivation;. *Organizational Change; *Personnel Management; Productivity; Program Effectivenes; Success Factors ,' IDENTIFIERS *Job Enrichment ABSTRACT T Job` enrichment rapidly is becoming- one of the' most Widely used behavioral science strategies for organizational change. And there is scattered but compelling evidence that, undercertain conditions, the technique can lead simultaneously to both improved productivity and an increase in the quality of employee work experiences. Yet obsetvations of on-going lob enrichment projects in a number of organizaHons suggest that theapproach. is failing in practice at least as often as it is succeedint -and that its future as a strategy fOr personal and organizational change may bebleak. The report (1) explores a,, number of frequently-observed errors in .implemediing job enrichment that _can lead ,to "failures" of the technique, and (21 ideitifieg-a number of ingredients found to be common to most of the:nsuccessfuln-job enrichment projects that were observed. (Author) J. ***********,#*o******************************************************** . * Documents acquired by ERIC. include many-informal unpublished * materials not available from other sources: ERIC makes every'effort * * to obtain the best copy available. -
A Look at the Reactionary Nature of Whistleblower Protections in a Growing Global Economy [Note]
More Opportunities, More Concerns: A Look at the Reactionary Nature of Whistleblower Protections in a Growing Global Economy [Note] Item Type Article; text Authors Smith, Jake Citation 37 Ariz. J. Int'l & Comp. L. 381 (2020) Publisher The University of Arizona James E. Rogers College of Law (Tucson, AZ) Journal Arizona Journal of International and Comparative Law Rights Copyright © The Author(s) Download date 27/09/2021 14:02:34 Item License http://rightsstatements.org/vocab/InC/1.0/ Version Final published version Link to Item http://hdl.handle.net/10150/658745 MORE OPPORTUNITIES, MORE CONCERNS: A LOOK AT THE REACTIONARY NATURE OF WHISTLEBLOWER PROTECTIONS IN A GROWING GLOBAL ECONOMY Jake Smith TABLE OF CONTENTS I. INTRODUCTION ........................................................................................... 381 II. WHISTLEBLOWER PROTECTION LAWS IN THE UNITED STATES .... 383 A. History of Whistleblower Protections in the United States ....................... 384 1. Public Sector Whistleblower Protections ............................................... 384 2. Private Sector Whistleblower Protections .............................................. 385 B. The Sarbanes-Oxley Act............................................................................387 C. The Dodd-Frank Wall Street Reform and Consumer Protection Act ........ 390 D. Edward Snowden, Public Sector Whistleblower Protections in US Today ........................................................................................................................ 393 III. -
Analyzing Work and Designing Jobs
Confirming Pages chapter 4 Analyzing Work and Designing Jobs What Do I Need to Know? Introduction After reading this chapter, you should When brothers Michael and Jack Kennedy be able to: started Railroad Associates Corporation, a con- LO1 Summarize the elements of work flow tracting firm that repairs railways, they wanted analysis. an organization that would be both flexible LO2 Describe how work flow is related to an and efficient. So the two owners decided that organization’s structure. decision making wouldn’t be a managers-only LO3 Define the elements of a job analysis, and discuss their significance for human resource responsibility. In fact, they skipped middle man- management. agement altogether. Workers at job sites are LO4 Tell how to obtain information for a job expected to make their own decisions when analysis. questions and problems arise. That means Rail- LO5 Summarize recent trends in job road Associates has to hire workers who are analysis. willing and able to take responsibility, and the LO6 Describe methods for designing a job so that it company has to provide plenty of training. The can be done efficiently. company also gives employees access to its LO7 Identify approaches to designing a job to make it intranet, where they can look up budgets and motivating. schedules for the jobs they’re working on. But LO8 Explain how organizations apply ergonomics to the company doesn’t just expect flexibility from design safe jobs. its employees; it also offers flexibility to them LO9 Discuss how organizations can plan for the mental demands of a job. -
Job Design and Employee Performance: the Moderating Role of Employee Psychological Perception
View metadata, citation and similar papers at core.ac.uk brought to you by CORE provided by International Institute for Science, Technology and Education (IISTE): E-Journals European Journal of Business and Management www.iiste.org ISSN 2222-1905 (Paper) ISSN 2222-2839 (Online) Vol.5, No.5, 2013 Job Design and Employee Performance: the Moderating Role of Employee Psychological Perception Memoona Zareen 1* Kiran Razzaq 1 Bahaudin G. Mujtaba 2 1. Superior University Department of Business Administration, Lahore, Pakistan. 2. H. Wayne Huizenga School of Business and Entrepreneurship, Nova Southeastern University, Florida. * E-mail of the corresponding author: [email protected] Abstract Job design plays a vital role in the performance maximization. A well designed job brings involvement and satisfaction to the employees and they perform well by employing all their energies in the work. Job design remains a valued issue among the researchers for its importance and effectiveness. A well designed job, according to psychological perception and attitude of employees, motivate workers towards task performance, and such employees become highly productive and loyal to the organization. This study is based on a review of the published literature and personal observation in the workplace to analyze the impact of job design on employee performance. Furthermore, this study proposes a new variable known as “psychological perception” of employee to highlight how employees behave towards a job design. A conceptual framework has been proposed to show the construct of job design by job rotation, job enrichment and job enlargement and relationship of job design with employee performance. It has been found that the psychological perception of an employee has a significant positive impact on the relationship of job design and employee performance. -
JOB ENRICHMENT Job Enrichment Is a Management Concept That Involves Redesigning Jobs So That They Are More Challenging to the Employee and Have Less Repetitive Work
JOB ENRICHMENT Job enrichment is a management concept that involves redesigning jobs so that they are more challenging to the employee and have less repetitive work. The concept is based on a 1968 Harvard Business Review article by psychologist Frederick Herzberg titled 'One More Time: How Do You Motivate Employees?' In the article, Herzberg stated that the greatest employee motivators, based on several investigations, are (in descending order): achievements, recognition, work itself, responsibility, advancement, and growth. To improve employee motivation and productivity, jobs should be modified to increase the motivators present for the employee. To make this concept more usable, let's imagine you are a company manager and want to increase the satisfaction of your staff. As you walk through the process of job enrichment, you'll need to keep in mind these goals: Reduce repetitive work. Increase the employee's feelings of recognition and achievement. Provide opportunities for employee advancement (i.e. promotions into jobs requiring more skills). Provide opportunities for employee growth (i.e. an increase in skills and knowledge without a job promotion). Why Enrich Jobs? The purpose of job enrichment is to make the position more satisfying to the employee. Overall goals for the company often include increasing employee job satisfaction, reducing turnover, and improving productivity of employees. To rephrase this: we want to enrich our staff's positions so that they will be happier, more productive, and less likely to seek a job elsewhere. PRINCIPLES OF JOB ENRICHMENT Vertical job loading is the terminology used by Herzberg to describe his principles for enriching positions and giving employees more challenging work. -
The Relationship Between and Among Job Satisfaction, Training and Organizational
The Relationship between and among Job Satisfaction, Training and Organizational Culture in South Korea’s Manufacturing Industry Dissertation Presented in Partial Fulfillment of the Requirements for the Degree Doctor of Philosophy in the Graduate School of The Ohio State University By Hae Na Kim, M.P.A., M.A. College of Education and Human Ecology The Ohio State University 2016 Dissertation Committee: David Stein, Advisor Joshua Hawley Chris Zirkle Copyright by Hae Na Kim 2016 Abstract This dissertation explored the impact of training in organizational cultures and the influence on job satisfaction in South Korea’s manufacturing industry. To address the relationship between and among training, organizational culture and job satisfaction, principal component analysis and multiple regression analysis were applied using the 2013 Korean Human Capital Corporate Dataset. In spite of the significant relationship between job satisfaction and organizational culture, previous research has not fully focused on these relations outside Western countries (Dirani & Kuchinke, 2011). Especially, data on how to promote the organizational culture of the South Korean manufacturing industry is still empirically insufficient. The results of this analysis showed significant relationships between training and job satisfaction, and between organizational culture and job satisfaction, and among training, organizational culture and job satisfaction. Also, this dissertation showed position is statistically significant in all regressions but gender is not statistically significant with current salary. In addition, job satisfaction with work itself is not correlated to gender after inserting the interaction term of gender and position. This study indicates no clear distinction between Adhocracy Culture and Market Culture in South Korea’s manufacturing industry. -
AUTHOR Quinn, Robert P.; and Others TITLE Job Satisfaction: Is There a Trend? Manpower Research Monograph No
DOCUMENT RESUME ED 090 374 CE 001 212 AUTHOR Quinn, Robert P.; And Others TITLE Job Satisfaction: Is There a Trend? Manpower Research Monograph No. 30. INSTITUTION Manpower Administration (DOL), Washington, D.C. PUB DATE 74 NOTE 60p. AVAILABLE FROM Superintendent of Documents, U.S. Government Printing Office, Washington, D. C. 20402 (Stock Number 2900-00195, $0.95) EDRS PRICE MF-$0.75 HC-$3.15 PLUS POSTAGE DESCRIPTORS Employee Attitudes; Employer Attitudes; Employer Employee Relationship; *Job Satisfaction; *Literature Reviews; *National Surveys; Social Factors; Vocational Adjustment; Work Attitudes ABSTRACT A detailed review is presented of some of the major research on job satisfaction conducted in the past 40 years. The information is discussed in five major sections, each introduced by a series of related queStions, under the following headings: national trends in job satisfaction, 1958-73; distribution of job satisfaction in the work force (by occupation, sex, education, and age); what Americans want from their jobs (national sample, white collar, blue collar, and women worker's preferences); the importance of job satisfaction (from the perspective of the employer, the employee, and society); and new approad es, strategies, and findings (goals to be achieved or ignored, necessary assumptions, matching workers and jobs, training, changing the job--hours, bases of compensation, supervision, and work performed, and evaluating the change). Pour pages of references are included, together with appendixes covering: characteristics .of national surveys cited; problems with single-question measures of overall job satisfaction; sampling errors at the 95 percent confi'-nce level; percentage of usatisfiedu workers, 1958-73 by race, education, age, and sex; and mean job satisfactiOn in 1973 by selected demographic and occupational characteristics.