Acoustic and Strength Characterization of Concrete and Wood- Based Composites Comprised of Micronized Rubber Powder
Total Page:16
File Type:pdf, Size:1020Kb
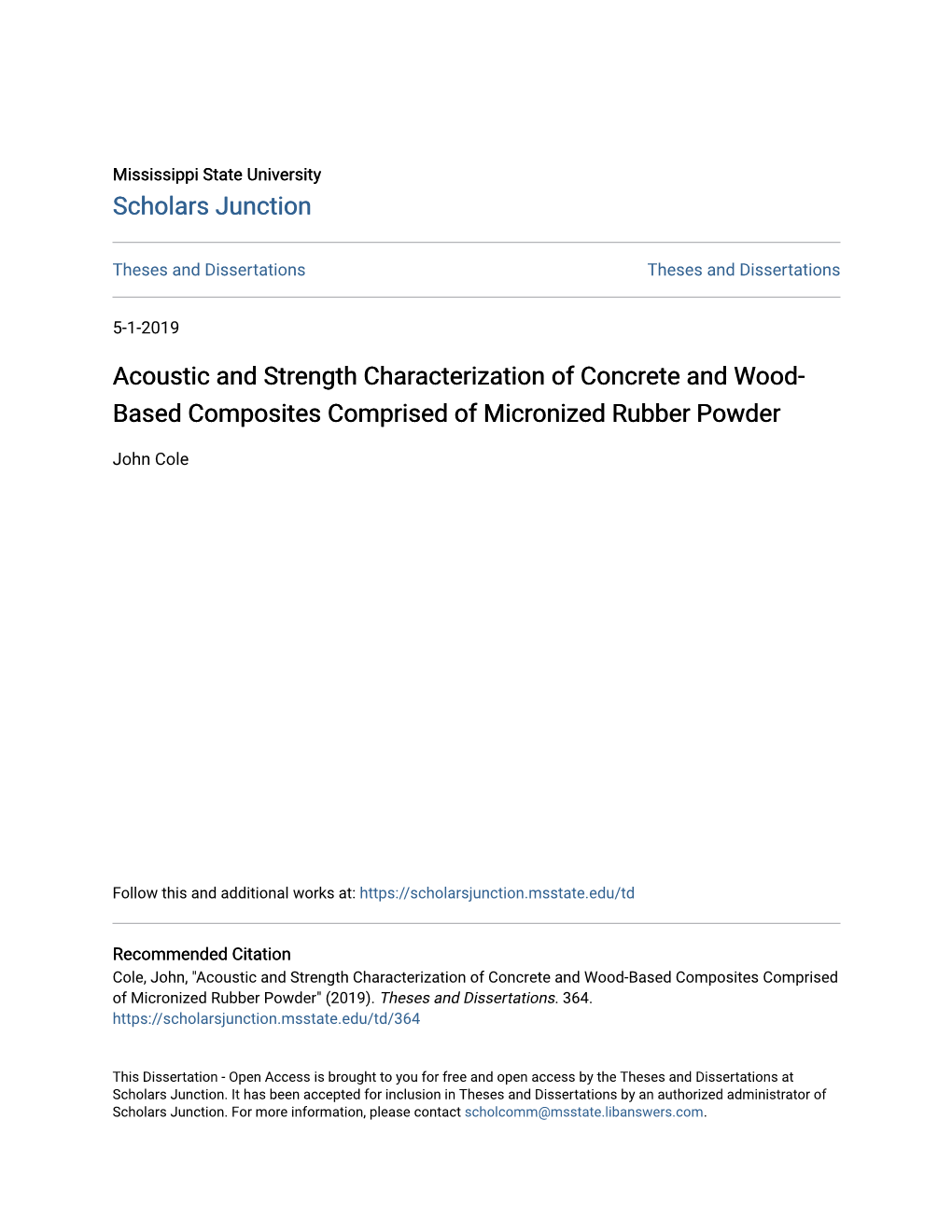
Load more
Recommended publications
-
Act Global Crumb Rubber Safety Study
ACT GLOBAL CRUMB RUBBER SAFETY STUDY Prepared for Act Global By R. William Tilford, PhD. Published February 11, 2015 Act Global initiated crumb rubber testing from three independent laboratories. To validate and triangulate the results, Dr. R. William Tilford was engaged by Act Global for objective and professional oversight and review. Dr. Tilford has a doctorate in organic chemistry and fourteen years of experience as a research chemist, with a thorough understanding of how organic molecules react with each other and their environments. 1 Introduction Artificial turf has been used in sports fields since invented in 1962. Despite their many benefits, for years these fields suffered from one key drawback. The relatively thin layer of turf, normally installed over a hard durable surface such as concrete, did not provide sufficient shock absorption to accommodate the rigors of athletic competition. To address this issue, an intermediate cushioning layer of elastic material was implemented into the design in the 1990s. An ideal material with which to create this shock-absorbing interlayer was styrene butadiene rubber (SBR), which is often utilized for applications where it is necessary to protect bodies against repeated exposure to mechanical stress. The most notable example is in automobile tires which provide a constant elastic buffer between the road and automobile. Developments in recycling technologies enabled used automobile tires destined for landfills to instead be processed and repurposed as SBR crumb rubber infill. This source of SBR provides an efficient means of improving both the performance and safety of artificial turf systems. Act Global initiated a review of a crumb rubber supply used in their synthetic turf systems to examine the potential presence of any chemical species that would cause concern over its use as a raw material. -
A Review of the Potential Health and Safety Risks from Synthetic Turf Fields Containing Crumb Rubber Infill
A REVIEW OF THE POTENTIAL HEALTH AND SAFETY RISKS FROM SYNTHETIC TURF FIELDS CONTAINING CRUMB RUBBER INFILL Prepared for New York City Department of Health and Mental Hygiene New York, NY Prepared by TRC Windsor, Connecticut May 2008 A REVIEW OF THE POTENTIAL HEALTH AND SAFETY RISKS FROM SYNTHETIC TURF FIELDS CONTAINING CRUMB RUBBER INFILL Prepared for New York City Department of Health and Mental Hygiene New York, NY Prepared by TRC Windsor, Connecticut Report Authors: Elizabeth Denly Katarina Rutkowski Karen M. Vetrano, Ph.D. NYC DOHMH Reviewers: Andriana Azarias, Nancy Clark, Nathan Graber, Paromita Hore, Maureen Little TRC Project No. 153896 May 2008 TRC 21 Griffin Road North Windsor, Connecticut 06095 Telephone 860-298-9692 Facsimile 860-298-6399 TABLE OF CONTENTS SECTION PAGE LIST OF ACRONYMS .................................................................................................................... iv EXECUTIVE SUMMARY .........................................................................................................ES–1 1.0 INTRODUCTION .............................................................................................................. 1-1 1.1 Background and Purpose of Review............................................................................... 1-1 1.2 Scope of Work................................................................................................................ 1-3 1.2.1 Literature Search.................................................................................................... -
Synthetic Turf Wars 1
Running head: SYNTHETIC TURF WARS 1 Synthetic Turf Wars: A Crumb Rubber Human Health Risk Assessment Submitted by Jacob Kromberg Health Sciences – Pre-Health Professional, Exercise Science To The Honors College Oakland University In partial fulfillment of the requirement to graduate from The Honors College Mentor: Richard Olawoyin PhD, Associate Professor of Industrial and Systems Engineering Oakland University (04/12/2020) SYNTHETIC TURF WARS 2 Abstract Background: Crumb rubber (CR) is a recycled product generated from automotive and truck scrap tires and produced with a granulated consistency, often treated with several chemicals before being spread into the environment. It is often found on athletic artificial/synthetic turf fields and children’s playgrounds. Current studies have established that there is no correlation between CR exposure and non-carcinogenic and carcinogenic health effects. However, other research has found hazardous substances within CR. No matter the case, concerns among the general public continue to grow about the health risks of CR, most notably regarding soccer player, specifically goalkeeper, populations. Objective: The purpose of this study was to investigate the level of health risk CR poses to exposed human populations, particularly individuals 6-21 years old. Methods: A human health risk assessment (HHRA) was conducted in four phases with an initial planning phase: 1) hazard identification, 2) dose-response assessment, 3) exposure assessment, and 4) risk characterization. Results: This study examined 115 chemicals of potential concern (COPCs). Intake dose (ID), lifetime average daily dose (LADD), reference dose (RfD), reference concentration (RfC), oral slope factor (OSF), inhalation unit risk (IUR), hazard quotient (HQ), excess lifetime cancer risk (ELCR), hazard index (HI), and total cancer risk (TCR) were analyzed. -
Devulcanization Technologies for Recycling of Tire-Derived Rubber: a Review
materials Review Devulcanization Technologies for Recycling of Tire-Derived Rubber: A Review Erich Markl and Maximilian Lackner * University of Applied Sciences FH Technikum Wien, A-1200 Vienna, Austria; [email protected] * Correspondence: [email protected] Received: 20 January 2020; Accepted: 2 March 2020; Published: 10 March 2020 Abstract: In general, composite materials are difficult to recycle. Tires belong to this class of materials. On top, one of their main constitutents, vulcanized rubber, is as elastomer, which cannot be remolten and hence is particularly challenging to put to a new use. Today, the main end-of-life routes of tires and other rubber products are landfilling, incineration in e.g., cement plants, and grinding to a fine powder, generating huge quantities and indicating a lack of sustainable recycling of this valuable material. True feedstock recycling is not feasible for complex mixtures such as tires, but devulcanization can be done to reactivate the cross-linked polymer for material recycling in novel rubber products. Devulcanization, i.e., the breaking up of sulfur bonds by chemical, thermophysical, or biological means, is a promising route that has been investigated for more than 50 years. This review article presents an update on the state-of-the art in rubber devulcanization. The article addresses established devulcanization technologies and novel processes described in the scientific and patent literatures. On the one hand, tires have become high-tech products, where the simultaneous improvement of wet traction, rolling resistance, and abrasion resistance (the so-called “magic triangle”) is hard to achieve. On the other hand, recycling and sustainable end-of-life uses are becoming more and more important. -
Fatigue Properties and Fracture Morphology of Micronised Rubber Powder (MRP) from Waste Tyres in Unfilled Elastomers
International Journal of Materials, Mechanics and Manufacturing, Vol. 6, No. 4, August 2018 Fatigue Properties and Fracture Morphology of Micronised Rubber Powder (MRP) from Waste Tyres in Unfilled Elastomers Dayang Habibah A. I. H, Frank Abraham, John Summerscales, and Paul Brown economic and environmental benefits. The emergence of Abstract—Ground rubber from waste tyres may be added to smaller sizes of recycled rubber powder in micronised form elastomers with economic and environmental benefits. The certainly has great potential in many applications. Ayyer and untreated or treated fillers have been investigated in different co-authors [5] investigated the effects of particle size of types of virgin rubber matrix. A principal concern is their crosslinked structure and large particle sizes. These additives cryogenically-ground micronised rubber powder (MRP) on introduce flaws leading to micro-crack initiation especially the properties of polypropylene-MRP compounds. They under dynamic loading. The incorporation of smaller particles reported that the cryogenic particles had higher surface area at a suitable concentration may avoid deterioration in the key due to higher content of finer particles compared to ambient properties. particles at all the nominal particle sizes. Ambient particles The present work studies the effect of commercial cryogenic are claimed to provide better mechanical properties compared micronised rubber particle (MRP) (apparent particle size to cryogenic filled particle compound due to the convoluted diameter less than 100 µm) as filler at either 10 or 30 parts per hundred rubber (pphr) on the fatigue properties of natural structure. Nonetheless, the commercial scale process for rubber (NR), butadiene rubber (BR) or NR/BR blends (without ambient ground rubber is only able to produce ≥ 400 µm carbon black in the host matrix). -
Crumb Rubber Use in Artificial Athletic Turf
Crumb Rubber Use in Artificial Athletic Turf Prepared by Sheena Ahrar In partial fulfillment of the requirements for a master of public health degree in Environmental Health Advisor: Dr. Elizabeth Wattenberg Prepared on Behalf of City of Brooklyn Park Recreation and Parks Department Spring 2017 The project on which this report is based was completed in collaboration with the City of Brooklyn Park as part of the 2016–2017 Resilient Communities Project (RCP) partnership. RCP is a program at the University of Minnesota’s Center for Urban and Regional Affairs (CURA) that connects University faculty and students with Minnesota communities to address strategic projects that advance local resilience and sustainability. The contents of this report represent the views of the authors, and do not reflect those of RCP, CURA, the Regents of the University of Minnesota, or the City of Brooklyn Park. This work is licensed under a Creative Commons Attribution- NonCommercial 3.0 Unported License. To view a copy of this license, visit www.creativecommons.org/licenses/by-nc/3.0/ or send a letter to Creative Commons, 444 Castro Street, Suite 900, Mountain View, California, 94041, USA. Any reproduction, distribution, or derivative use of this work under this license must be accompanied by the following attribution: “Produced by the Resilient Communities Project (www.rcp.umn.edu) at the University of Minnesota. Reproduced under a Creative Commons Attribution- NonCommercial 3.0 Unported License.” This publication may be available in alternate formats upon request. Resilient Communities Project University of Minnesota 330 HHHSPA 301—19th Avenue South Minneapolis, Minnesota 55455 Phone: (612) 625-7501 E-mail: [email protected] Web site: http://www.rcp.umn.edu The University of Minnesota is committed to the policy that all persons shall have equal access to its programs, facilities, and employment without regard to race, color, creed, religion, national origin, sex, age, marital status, disability, public assistance status, veteran status, or sexual orientation. -
Resource Responsible Use of Recycled Tire Rubber in Asphalt Pavements
Resource Responsible Use of Recycled Tire Rubber in Asphalt Pavements PUBLICATION NO. FHWA-HIF-20-043 April 2020 FOREWORD Pneumatic tires are designed to fulfill fundamental functions throughout their useful lives like cushioning, damping, transmitting of torque (driving and braking), dimensional stability, abrasion resistance, efficient rolling resistance, and durability. Lacking the ability to recycle old tires into new tires, there are several common repurposing methods to effectively reuse rubber. Recycling of rubber from old tires may include but is not limited to: tire-derived fuel, ground tire rubber, and civil engineering applications. GTR is the second highest consumer of recycled tire rubber. This informational brief provides a review and update on the various GTR processes used in production of asphalt pavements. It presents the most recent waste tire data along with a historical perspective of GTR use as a modifier for asphalt binders and as an additive in asphalt mixtures. Consideration for responsible use of GTR is given to promote sustainable use of GTR in asphalt pavements. Additional detailed information can be obtained from Federal Highway Administration (FHWA) publication FHWA-HIF-14-015 on The Use of Recycled Tire Rubber to Modify Asphalt Binder and Mixtures. The FHWA has an ongoing Accelerated Implementation and Deployment of Pavement Technologies (AIDPT) Program, which includes the deployment of innovative technologies to improve pavement performance and reduce agency risk. This report was prepared under Development and Deployment of Innovative Asphalt Pavement Technologies Cooperative Agreement with the University of Nevada, Reno. Notice This document is disseminated under the sponsorship of the U.S. Department of Transportation (USDOT) in the interest of information exchange. -
Crumb Rubber As a Secondary Raw Material from Waste Rubber: a Short Review of End-Of-Life Mechanical Processing Methods
recycling Review Crumb Rubber as a Secondary Raw Material from Waste Rubber: A Short Review of End-Of-Life Mechanical Processing Methods Vjaceslavs Lapkovskis 1,* , Viktors Mironovs 1, Andrei Kasperovich 2, Vadim Myadelets 2 and Dmitri Goljandin 3 1 Scientific Laboratory of Powder Materials, Riga Technical University, 6B Kipsalas Str., Lab. 110, LV-1048 Riga, Latvia; [email protected] 2 Department of Technology of Petrochemical Synthesis and Polymer Materials Processing, Belarussian State Technological University, Sverdlova Str. 13a, 220006 Minsk, Belarus; [email protected] (A.K.); [email protected] (V.M.) 3 Department of Mechanical and Industrial Engineering, Tallinn University of Technology (TalTech), Ehitajate Tee 5, 19086 Tallinn, Estonia; [email protected] * Correspondence: [email protected]; Tel.: +371-2953-6301 Received: 11 September 2020; Accepted: 26 November 2020; Published: 1 December 2020 Abstract: Despite technological developments, modern methods for the disposal of end-of-life tires most often involve either their incineration in cement kilns or the destruction of tires in special landfills, demonstrating a lack of sustainable recycling of this valuable material. The fundamental role of recycling is evident, and the development of high-efficiency processes represents a crucial priority for the European market. Therefore, the investigation of end-of-life rubber processing methods is of high importance for both manufacturers and recyclers of rubber materials. In this paper, we review existing methods for processing of end-of-life tires, in order to obtain rubber crumb, which can later be used in the production of new industrial rubber goods and composites. We consider processes for separating end-of-life tires into fractions (in terms of types of materials) using chemical, mechanochemical, and mechanical methods to process the materials of used tires, in order to obtain crumb rubber of various fractions and chemical reactivities. -
The Effects of Crumb Rubber on Water Quality September, 2008
The Coastal Marine Resource Center Policy Project 334 Furman St., Brooklyn, NY 11201 The Effects of Crumb Rubber on Water Quality September, 2008 Abstract This paper will present the arguments both for and against the use of crumb focusing on the implications for water quality and advance certain precautions and guidelines that may be taken to safeguard against potential hazards (Table 1, Recommendations for Containing and Managing Crumb Rubber). These are recommendations to prevent the release of crumb rubber into the surrounding environment and minimize the flow of water from fields to water sources and water bodies. The potential hazards to water quality from crumb rubber may not justify a moratorium on the construction of synthetic fields, however officials involved in building these fields must be circumspect in their designs and take full account of the effects that crumb rubber may have on the surrounding environment and the water supply, aside from possible health effects. Additionally, with numerous sources citing the potential danger of crumb rubber, officials have the responsibility to search out alternatives and to further justify their use of crumb rubber with more research, a detailed site assessment, and benefit-cost analysis for large scale projects. Introduction The United States generates just under 300 resiliency of synthetic turf found on million waste tires each year. Waste tire playgrounds and recreational areas. According generation has become a growing concern to the New York City Parks Department, as of amongst the public both for the congestion they the end of 2007 there were 63 of these fields create in our landfills and for the possible health across New York City and another 16 are and environmental effects that may be associated currently under construction.2 In processing the with the disposal of used tires. -
Sodium Hydroxide Treatment of Waste Rubber Crumb and Its Effects On
applied sciences Article Sodium Hydroxide Treatment of Waste Rubber Crumb and Its Effects on Properties of Unsaturated Polyester Composites M. Nuzaimah 1,2 , S.M. Sapuan 1,3,*, R. Nadlene 4 and M. Jawaid 3 1 Advanced Engineering Materials and Composites Research Centre, Department of Mechanical and Manufacturing Engineering, Universiti Putra Malaysia, Selangor, Serdang 43400, Malaysia; [email protected] 2 Fakulti Teknologi Kejuruteraan Mekanikal dan Pembuatan, Universiti Teknikal Malaysia Melaka, Jalan Hang Tuah Jaya, Melaka, Durian Tunggal 76100, Malaysia 3 Laboratory of Biocomposite Technology, Institute of Tropical Forestry and Forest Products (INTROP), Universiti Putra Malaysia, Selangor, Serdang 43400, Malaysia; [email protected] 4 Fakulti Kejuruteraan Mekanikal, Universiti Teknikal Malaysia Melaka, Jalan Hang Tuah Jaya, Melaka, Durian Tunggal 76100, Malaysia; [email protected] * Correspondence: [email protected] Received: 14 March 2020; Accepted: 28 April 2020; Published: 5 June 2020 Abstract: This study investigated the optimum NaOH concentration treatment for rubber crumbs that improves adhesion between the polymer matrix and rubber filler in rubber polyester composites. The composite was prepared by mixing rubber crumbs from waste rubber gloves with unsaturated polyester matrix. Rubber crumbs were cryogenically ground from waste gloves and treated with 1%, 4%, 7%, and 10% NaOH (by volume). Treatment with 7% and 10% NaOH provides better wettability and hydrophilicity for rubber as it decreases the surface contact angle by approximately 27%. Higher concentration of NaOH intensively etched the rubber and made the surface rougher with more microcracks, providing a larger surface area for greater polyester coverage and holding the rubber firmly. It also induced more functional groups that increased the rubber surface energy and removed the hydrophobic layer on the rubber. -
Recycling Waste Tires Into Ground Tire Rubber (GTR)/Rubber Compounds: a Review
Review Recycling Waste Tires into Ground Tire Rubber (GTR)/Rubber Compounds: A Review Ali Fazli and Denis Rodrigue * Department of Department of Chemical Engineering, Université Laval, Quebec, QC G1V 0A6, Canada; [email protected] * Correspondence: [email protected]; Tel.: +1-418-656-2903 Received: 13 July 2020; Accepted: 29 July 2020; Published: 31 July 2020 Abstract: Recycling and recovery of waste tires is a serious environmental problem since vulcanized rubbers require several years to degrade naturally and remain for long periods of time in the environment. This is associated to a complex three dimensional (3D) crosslinked structure and the presence of a high number of different additives inside a tire formulation. Most end-of-life tires are discarded as waste in landfills taking space or incinerated for energy recovery, especially for highly degraded rubber wastes. All these options are no longer acceptable for the environment and circular economy. However, a great deal of progress has been made on the sustainability of waste tires via recycling as this material has high potential being a source of valuable raw materials. Extensive researches were performed on using these end-of-life tires as fillers in civil engineering applications (concrete and asphalt), as well as blending with polymeric matrices (thermoplastics, thermosets or virgin rubber). Several grinding technologies, such as ambient, wet or cryogenic processes, are widely used for downsizing waste tires and converting them into ground tire rubber (GTR) with a larger specific surface area. Here, a focus is made on the use of GTR as a partial replacement in virgin rubber compounds. -
Water Use Impacts of Artificial Turf
Field, Pilot, and Laboratory Studies for the Assessment of Water Quality Impacts of Artificial Turf JUNE 2010 Prepared For Santa Clara Valley Water District 5750 Almaden Expressway San Jose, CA 95118-3614 Prepared By Hefa Cheng and Martin Reinhard Department of Civil and Environmental Engineering Stanford University Stanford, CA 94305 (Blank page) ii Legal Notice This report was prepared as a result of work sponsored by the Santa Clara Valley Water District. Content and opinions expressed in this report do not necessarily represent the views of this agency or its employees. The Santa Clara Valley Water District, its employees, contractors, and subcontractors make no warranty, express or implied, and assume no legal liability for the information in this report; nor does any party represent that the use of this information will not infringe upon privately owned rights. iii Disclaimer The information contained in this report was developed by Stanford University for the Santa Clara Valley Water District; no warranty as to the accuracy, usefulness, or completeness is expressed or implied. Information contained in this report regarding commercial products or firms was supplied by those firms. It may not be used for advertising or promotional purposes and is not to be construed as an endorsement of any product or firm by Stanford University. iv ACKNOWLEDGEMENT The authors thank Jeannine Larabee, SCVWD, and Drs. Eric Litwiller and Alexander Robertson, Stanford University, for valuable input. v TABLE OF CONTENT Legal Notice..........................................................................................................