In-Situ Formation of 2D-Ticx in Cu-Ti2alc Composites: an Interface Reaction Study
Total Page:16
File Type:pdf, Size:1020Kb
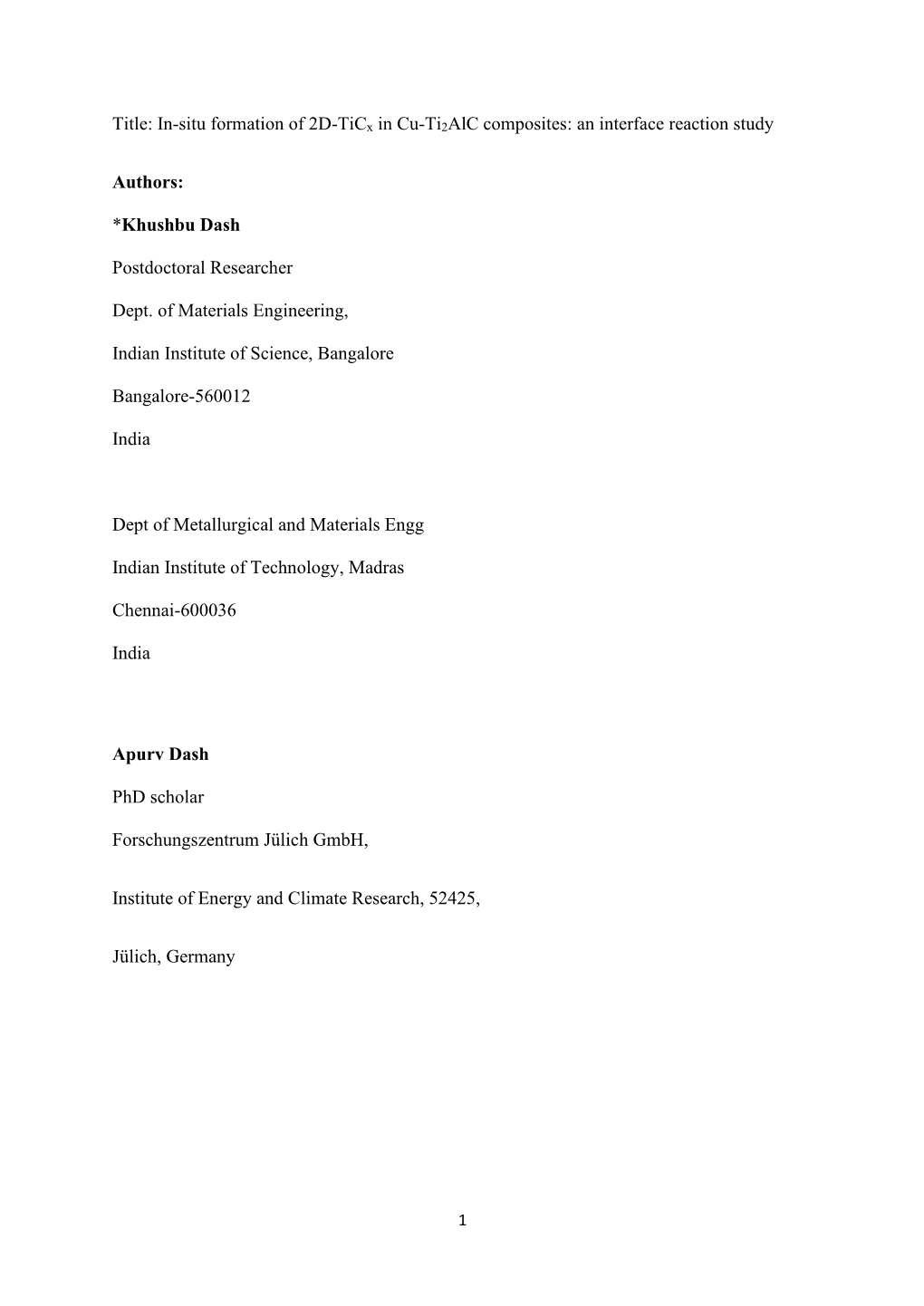
Load more
Recommended publications
-
Technical Annex
TECHNICAL ANNEX TO THE DOCUMENT MATERIALS FOR SUSTAINABLE NUCLEAR ENERGY The Strategic Research Agenda (SRA) of the Joint Programme on Nuclear Materials (JPNM) of the European Energy Research Alliance (EERA) TA.1 Detailed nuclear materials research agenda TA.1.1 Structural materials TA.1.1.1 Pre-normative research: qualification, test procedures, design rules This section concerns the development of the assessment tools and the collection of the materials data in support of the design, licensing, and construction of the ESNII demonstrators, with a view also towards the FOAK prototypes and commercial reactors to be deployed later. 1 An especially delicate issue in this context is the extension of the operational life of non-replaceable components from 40 to at least 60 years as a general Gen IV requirement .2 All relevant slow long- term degradation processes need to be accounted for, especially high-temperature processes (creep, fatigue, thermal ageing), but also corrosion and low-dose-rate long-term irradiation effects. A fundamental issue is how to measure material properties representative for long-term operation . This is a tremendous challenge shared by all Gen IV concepts, for which design and assessment methodologies need to be developed and translated into codes and standards. For instance, for creep extrapolation by a factor 3 is considered feasible, but this would require tests of 20 years duration for reliable 60 years design data. In a future low-carbon energy mix, the nuclear contribution will also need to operate in a load-following mode, whereby the reactor components will accumulate more load cycles, which should also be taken into account in a long-term operation perspective. -
Multielemental Single-Atom-Thick a Layers in Nanolaminated V2
Multielemental single-atom-thick A layers in nanolaminated V2(Sn, A)C (A=Fe, Co, Ni, Mn) for tailoring magnetic properties Youbing Li 1, 2†, Jun Lu 3†, Mian Li 1, Keke Chang 1, Xianhu Zha 1, 4, Yiming Zhang 1, Ke Chen 1, Per O. Å. Persson 3, Lars Hultman 3, Per Eklund 3, Shiyu Du 1, Zhifang Chai 1, Zhengren Huang 1, Qing Huang 1* 1Engineering Laboratory of Advanced Energy Materials, Ningbo Institute of Materials Technology and Engineering, Chinese Academy of Sciences, Ningbo, Zhejiang 315201, China 2University of Chinese Academy of Sciences, 19 A Yuquan Rd, Shijingshan District, Beijing 100049, China 3Thin Film Physics Division, Department of Physics, Chemistry, and Biology (IFM), Linköping University, SE-581 83 Linköping, Sweden 4 Center for Quantum Computing, Peng Cheng Laboratory, Shenzhen 518055, China Abstract Tailoring of individual single-atom-thick layers in nanolaminated materials offers atomic-level control over material properties. Nonetheless, multielement alloying in individual atomic layers in nanolaminates is largely unexplored. Here, we report a series of inherently nanolaminated V2(AxSn1-x)C (A=Fe, Co, Ni and Mn, and combinations thereof, with x≈1/3) synthesized by an alloy-guided reaction. The simultaneous occupancy of the four magnetic elements and Sn, the individual single-atom-thick A layers in the compound constitute high-entropy-alloy analogues, two-dimensional in the sense that the alloying exclusively occurs in the A layers. V2(AxSn1-x)C exhibit distinct ferromagnetic behavior that can be compositionally tailored from the multielement A-layer alloying. This two-dimensional alloying provides a structural-design route with expanded chemical space for discovering materials and exploit properties. -
Carbide and MAX-Phase Engineering by Thin Film Synthesis
Comprehensive Summaries of Uppsala Dissertations from the Faculty of Science and Technology 930 Carbide and MAX-Phase Engineering by Thin Film Synthesis JENS-PETTER PALMQUIST ACTA UNIVERSITATIS UPSALIENSIS UPPSALA 2004 ! ""# $%&$' ( ( ( ) * + , ) - ./) ""#) 0 123/ , * 4 ) 56 123/( ( 7) 2 ) 8%") !" ) ) 94:; 8$/''#/'<'</" * ( +/ ( 123/ ( + ) 1 ( ( - ( ( ) ( = = 0 >/=0$/ ( + ( + =- 0 + $"" 0) = ( + " ? 0 / (( + ( %' @ ) ( ( *$/A0 ( ( / /( ( + ( () 1 + 5;1 70 5*=70 () * ( 40 / + ) 2 ( ( ( 123/ ) * ( ( + 1 B$23 C$ % + 1 2 $%/$# 30 ;) * + ( ( - ( ) 4 ( 123/ / D ( ) E + ( ( 123/ ( + !'" 0) ( / ( ( *%40 *%20 * 20 + ) * + 123/ *#40%) 9 + + 123/ *'4 0% *!4 0') 0 + ( + + D ) ( 123/ ( + ( ( ( +/( + ) * ( =0 123/ *%40 0 A F 4 1 F41 !" "# $ % $ &' ()*$ $ +!,(-.- $ G . / - ""# 944; $$"#/ % 3 94:; 8$/''#/'<'</" & &&& /%8! 5 &HH )D)H I C & &&& /%8! 7 Printed in Sweden by Universitetstryckeriet, Uppsala 2004 Till Professor Baltazar Carbide and MAX-Phase -
Introduction to Nanomaterials and Nanotechnology Pdf
Introduction to nanomaterials and nanotechnology pdf Continue Materials whoseular size lies between 1 to 100 nm part of the series of articles onNanomaterials Carbon nanotubes Synthesis Chemistry Mechanical properties Opt ical Properties Apps Timeline Fullerenes Buckminsterfullerene C70 fullerene Chemistry Health impact Carbon allotropes Other nanoparticles Quantum dots Aluminium oxide Cellulose Ceramic Cobalt oxide Copper Gold Iron Iron Oxide Iron–Platinum Lipid Platinum Silver Titanium Dioxide Nanostructured Materials Nanocomposite Nanofoam Nanoporous materials Nanocrystalline material science portal portal partvte of series of articles onNanotechnology Organizations Popular Cultureline Impactline and Science portal application Nanomedicine Nanooxicology Green Nanotechnology Hazards Regulation Nanomaterials Fullerenes Carbon Nanoparticles Nanoparticles Molecular self-assembly Self-assembled monolayer Supramolecular assembly DNA nanotechnology Nanoelectronics Molecular scale electronics Nanolithography Moore's law Semiconductor device fabrication Semiconductor scale examples Nanometrology Atomic Force microscopy Scanning tunneling microscope Electron microscope Super resolution microscopy Nanotribology Molecular nanotechnology Molecular assembler Nanorobotics Mechanosynthesis Molecular engineering science portal technology portalvte Nanomaterials describes , in principle, material in which a single size unit is small (at least one dimension) between 1 and 100 nm (the usual definition of nanoscale[1]). Nanomaterials research takes a science-based -
MAX Phases: Bridging the Gap Between Metals and Ceramics Figure 1
MAX phases: Bridging the gap between metals and ceramics Figure 1. Scanning electron microscopy of the fractured surface –1 in Ti2AlC after dynamic testing of at a strain rate of 2400 s showing typical laminated nature and deformation of individu- al grains by kinking. bulletin cover story MAX phases: Bridging the gap between metals and ceramics By Miladin Radovic and Michel W. Barsoum he term “MAX phases” was coined T in the late 1990s and applies to a family of 60+ ternary carbides and nitrides that share a layered structure as illustrated in Figures 1 and 2. They are so called because of their chemical formula: Mn+1AXn —where n = 1, 2, or 3, where M is an early transition metal, A is an A-group element (specifi- cally, the subset of elements 13–16), and X is 1 (Credit: Credit: Radovic and Benitez; TAMU.) carbon and/or nitrogen, Figure 2. Nowotny and coworkers2, 3 discovered most of these phases in powder form roughly 40 years ago. However, Barsoum and El-Raghy’s4 report The MAX phases are a new and exciting class of carbides in 1996 on the synthesis of phase-pure bulk and nitrides that bridge the gap between properties typical of metals and ceramics, while offering fundamentally new Ti3SiC2 samples and their unusual combina- directions in tuning the structure and properties of ceramics tion of properties catalyzed renewed interest for emerging applications. in them. Since then, research on the MAX phases has exploded. According to ISI, to date around 1,200 papers have been published on one MAX phase alone, Ti3SiC2, with roughly half of those published in the past six years. -
Chemical Bonding and Electronic-Structure in MAX Phases As Viewed by X-Ray Spectroscopy and Density Functional Theory
Chemical bonding and electronic-structure in MAX phases as viewed by X-ray spectroscopy and density functional theory Martin Magnuson and Maurizio Mattesini Journal Article N.B.: When citing this work, cite the original article. Original Publication: Martin Magnuson and Maurizio Mattesini, Chemical bonding and electronic-structure in MAX phases as viewed by X-ray spectroscopy and density functional theory, Thin Solid Films, 2017. 621(), pp.108-130. http://dx.doi.org/10.1016/j.tsf.2016.11.005 Copyright: Elsevier http://www.elsevier.com/ Postprint available at: Linköping University Electronic Press http://urn.kb.se/resolve?urn=urn:nbn:se:liu:diva-132966 Thin Solid Films 621, 108-130 (2017) Chemical bonding and electronic-structure in MAX phases as viewed by X- ray spectroscopy and density functional theory Martin Magnuson1 and Maurizio Mattesini2,3 1Thin Film Physics Division, Department of Physics, Chemistry and Biology, IFM, Linköping University, SE-58183 Linköping, Sweden. 2Departamento de Física de la Tierra, Astronomía y Astrofísica I, Universidad Complutense de Madrid, Madrid, E-28040, Spain. 3Instituto de Geociencias (CSIC-UCM), Facultad de CC. Físicas, E-28040 Madrid, Spain. Abstract This is a critical review of MAX-phase carbides and nitrides from an electronic-structure and chemical bonding perspective. This large group of nanolaminated materials is of great scientific and technological interest and exhibit a combination of metallic and ceramic features. These properties are related to the special crystal structure and bonding characteristics with alternating strong M-C bonds in high-density MC slabs, and relatively weak M-A bonds between the slabs. Here, we review the trend and relationship between the chemical bonding, conductivity, elastic and magnetic properties of the MAX phases in comparison to the parent binary MX compounds with the underlying electronic structure probed by polarized X-ray spectroscopy. -
Current Trends in Mxene-Based Nanomaterials for Energy Storage and Conversion System: a Mini Review
catalysts Review Current Trends in MXene-Based Nanomaterials for Energy Storage and Conversion System: A Mini Review Karthik Kannan 1, Kishor Kumar Sadasivuni 1,*, Aboubakr M. Abdullah 1 and Bijandra Kumar 2,* 1 Center for Advanced Materials, Qatar University, P.O. Box 2713, Doha, Qatar; [email protected] (K.K.); [email protected] (A.M.A.) 2 Department of Technology, Elizabeth City State University, Elizabeth City, NC 27909, USA * Correspondence: [email protected] (K.K.S.); [email protected] (B.K.) Received: 9 March 2020; Accepted: 14 April 2020; Published: 1 May 2020 Abstract: MXene is deemed to be one of the best attentive materials in an extensive range of applications due to its stupendous optical, electronic, thermal, and mechanical properties. Several MXene-based nanomaterials with extraordinary characteristics have been proposed, prepared, and practiced as a catalyst due to its two-dimensional (2D) structure, large specific surface area, facile decoration, and high adsorption capacity. This review summarizes the synthesis and characterization studies, and the appropriate applications in the catalysis field, exclusively in the energy storage systems. Ultimately, we also discussed the encounters and prospects for the future growth of MXene-based nanomaterials as an efficient candidate in developing efficient energy storage systems. This review delivers crucial knowledge within the scientific community intending to design efficient energy storage systems. Keywords: MXene; 2D materials; Li-ion batteries; supercapacitors; Proton reduction; CO2 conversion and oxygen reduction 1. Introduction Two-dimensional layered materials have substantial research due to their amazing structural [1–3], mechanical [4], electronic [5,6], and optical properties [7]. -
Processing of MAX Phases: from Synthesis to Applications
Received: 5 June 2020 | Revised: 7 September 2020 | Accepted: 30 September 2020 DOI: 10.1111/jace.17544 INVITED FEATURE ARTICLE Processing of MAX phases: From synthesis to applications Jesus Gonzalez-Julian Forschungszentrum Jülich GmbH, Institute of Energy and Climate Research, Materials Abstract Synthesis and Processing (IEK-1), Jülich, MAX phases are a large family of materials with more than 150 different composi- Germany tions that have been extensively investigated during the last 25 years. They present a Correspondence layered structure and a unique combination of properties, bridging the gap between Jesus Gonzalez-Julian, Forschungszentrum metallic and ceramic properties. However, despite their excellent response of some Jülich GmbH, Institute of Energy and compositions at high temperature—excellent oxidation resistance up to 1400°C Climate Research, Materials Synthesis and Processing (IEK-1), 52425 Jülich, Germany. under corrosive environment, good damage and radiation tolerance, thermal shock Email: [email protected] resistance, and self-crack healing—their transfer to applications has been limited by three main factors: i) complexity of this large family of materials, ii) unavailability of Funding information Bundesministerium für Bildung und highly pure commercial powders, and iii) extensive time to license products in strate- Forschung, Grant/Award Number: gic fields such as nuclear or aviation. In this article, the main properties and synthesis MAXCOM 03SF0534 routes are reviewed, including solid state reaction methods, physical vapor deposi- tion (PVD) techniques and molten salt processes. Emphasis is given to processing routes for developing different structures such as dense bulk samples, ceramic ma- trix composites, foams with different porosity, coatings by PVD and thermal spray technologies, and near net shaping by slip casting, injection molding, and additive manufacturing. -
Synthesis and Tribological
SYNTHESIS AND TRIBOLOGICAL CHARACTERIZATION OF IN-SITU SPARK PLASMA SINTERED Ti3SiC2 AND Ti3SIC2-TiC COMPOSITES. By NIDUL CHANDRA GHOSH Bachelor of Science in Mechanical Engineering Bangladesh University of Engineering and Technology Dhaka, Bangladesh October 2009 Submitted to the Faculty of the Graduate College of the Oklahoma State University in partial fulfillment of the requirements for the Degree of MASTER OF SCIENCE December, 2012 SYNTHESIS AND TRIBOLOGICAL CHARACTERIZATION OF IN-SITU SPARK PLASMA SINTERED Ti3SiC2 AND Ti3SIC2-TiC COMPOSITES. Thesis Approved: Dr. Sandip P. Harimkar Thesis Adviser Dr. Kaan Kalkan Dr. Raman Singh Dr. Sheryl A. Tucker Dean of the Graduate College ii TABLE OF CONTENTS Chapter Page I. INTRODUCTION ......................................................................................................1 1.1 Introduction ........................................................................................................1 1.2 MAX Phase Materials ........................................................................................1 1.3 Titanium Silicon Carbide, Ti3SiC2 .....................................................................3 1.3.1 Crystal structure & properties of Ti3SiC2 ...............................................4 1.3.2 Application of Ti3SiC2 ............................................................................9 1.4 Synthesis of Ti3SiC2 .........................................................................................11 1.5 Spark Plasma Sintering ....................................................................................12 -
Development of Novel Max Phase Composites Thomas Jacob Hammann
University of North Dakota UND Scholarly Commons Theses and Dissertations Theses, Dissertations, and Senior Projects January 2014 Development Of Novel Max Phase Composites Thomas Jacob Hammann Follow this and additional works at: https://commons.und.edu/theses Recommended Citation Hammann, Thomas Jacob, "Development Of Novel Max Phase Composites" (2014). Theses and Dissertations. 1658. https://commons.und.edu/theses/1658 This Thesis is brought to you for free and open access by the Theses, Dissertations, and Senior Projects at UND Scholarly Commons. It has been accepted for inclusion in Theses and Dissertations by an authorized administrator of UND Scholarly Commons. For more information, please contact [email protected]. DEVELOPMENT OF NOVEL MAX PHASE COMPOSITES by Thomas Jacob Hammann Bachelor of Science, University of North Dakota, 2013 A Thesis Submitted to the Graduate Faculty of the University of North Dakota In partial fulfillment of the requirements for the degree of Master of Science Grand Forks, North Dakota December 2014 Copyright 2014 Thomas J. Hammann ii PERMISSION Title DEVELOPMENT OF NOVEL MAX PHASE COMPOSITES Department Mechanical Engineering Degree Masters of Science In presenting this thesis in partial fulfillment of the requirements for a graduate degree from the University of North Dakota, I agree that the library of this University shall make it freely available for inspection. I further agree that permission for extensive copying for scholarly purposes may be granted by the professor who supervised my thesis work or, in his absence, by the Chairperson of the department or the Dean of the Graduate School. It is understood that any copying or publication or other use of this thesis or part thereof for financial gain shall not be allowed without my written permission. -
Computational Prediction of Boron-Based MAX Phases and Mxene Derivatives Nanxi Miao, Junjie Wang,* Yutong Gong, Jiazhen Wu, Haiyang Niu, Shiyao Wang, Kun Li, Artem R
pubs.acs.org/cm Article Computational Prediction of Boron-Based MAX Phases and MXene Derivatives Nanxi Miao, Junjie Wang,* Yutong Gong, Jiazhen Wu, Haiyang Niu, Shiyao Wang, Kun Li, Artem R. Oganov,* Tomofumi Tada, and Hideo Hosono Cite This: Chem. Mater. 2020, 32, 6947−6957 Read Online ACCESS Metrics & More Article Recommendations *sı Supporting Information ABSTRACT: Conventional MAX phases (M is an early transition metal, A represents a p-block element or Cd, and X is carbon or nitrogen) have so far been limited to carbides and/or nitrides. In the present work, a series of stable layered ternary borides were predicted by combining variable-composition evolutionary struc- fi ture search and rst-principles calculations. The predicted Hf2InB2, Hf2SnB2,Zr2TlB2,Zr2PbB2, and Zr2InB2 show a Ti2InB2 type of structure (space group P6̅m2, No. 187, Nat. Commun. 2019, 10, 2284), and the structures of Hf3PB4 and Zr3CdB4 share the same space group with Ti2InB2 but belong to a new structure type. These two structural prototypes, M2AB2 and M3AB4 (M is Zr or Hf), have the composition and local structures of MAB phases, but inherit a hexagonal symmetry of MAX phases. Moreover, Hf2BiB and fi Hf2PbB exhibit a typical structure of conventional MAX phases (Mn+1AXn, space group P63/mmc, No. 194). These ndings suggest that boron-based ternary compounds may be a new platform of MAX phases. The functionalized two-dimensional (2D) borides derived from the predicted ternary phases are calculated to be with improved mechanical flexibility and adjustable electronic properties relative to the parent ones. In particular, the 2D Hf2B2T2 and Zr2B2T2 (T = F, Cl) can transform from metal to semiconductor or semimetal under appropriate compressive biaxial strains. -
Double Transition-Metal Mxenes: Atomistic Design of Two-Dimensional Carbides and Nitrides Weichen Hong†, Brian C
Double transition-metal MXenes: Atomistic design of two-dimensional carbides and nitrides Weichen Hong†, Brian C. Wyatt†, Srinivasa Kartik Nemani†, and Babak Anasori MXenes are a large family of two-dimensional (2D) transition-metal carbides, nitrides, and carbonitrides. The MXene family has expanded since their original discovery in 2011, and has grown larger with the discovery of ordered double transition-metal (DTM) MXenes. These DTM MXenes differ from their counterpart mono-transition-metal (mono-M) MXenes, where two transition metals can occupy the metal sites. Ordered DTM MXenes are comprised of transition metals in either an in-plane or out-of-plane ordered structure. Additionally, some DTM MXenes are in the form of random solid solutions, which are defined by two randomly distributed transition metals throughout the 2D structure. Their different structures and array of transition-metal pairs provide the ability to tune DTM MXenes for specific optical, magnetic, electrochemical, thermoelectric, catalytic, or mechanical behavior. This degree of control over their composition and structure is unique in the field of 2D materials and offers a new avenue for application- driven design of functional nanomaterials. In this article, we review the synthesis, structure, and properties † of DTM MXenes and provide an outlook for future research in this field. ( : Authors contributed equally.) Introduction There has been significant interest in the design of two-dimensional (2D) materials since the characterization of single layer graphene in 20041 to meet rapidly evolving demands for advanced materials in technological applications, including energy storage,2-4 electronics,5 membranes,6,7 catalysts,8 and sensors.9,10 MXenes are a large family of 2D materials, discovered in 2011,11,12 which offer a unique combination of electronic,13-15 optical,16-18 mechanical,19-21 and colloidal properties.22,23 MXenes are few-atoms-thick 2D sheets with a general formula of Mn+1XnTx.