Development of New 3D Printed Plug Flow Reactors – Using Oscillatory
Total Page:16
File Type:pdf, Size:1020Kb
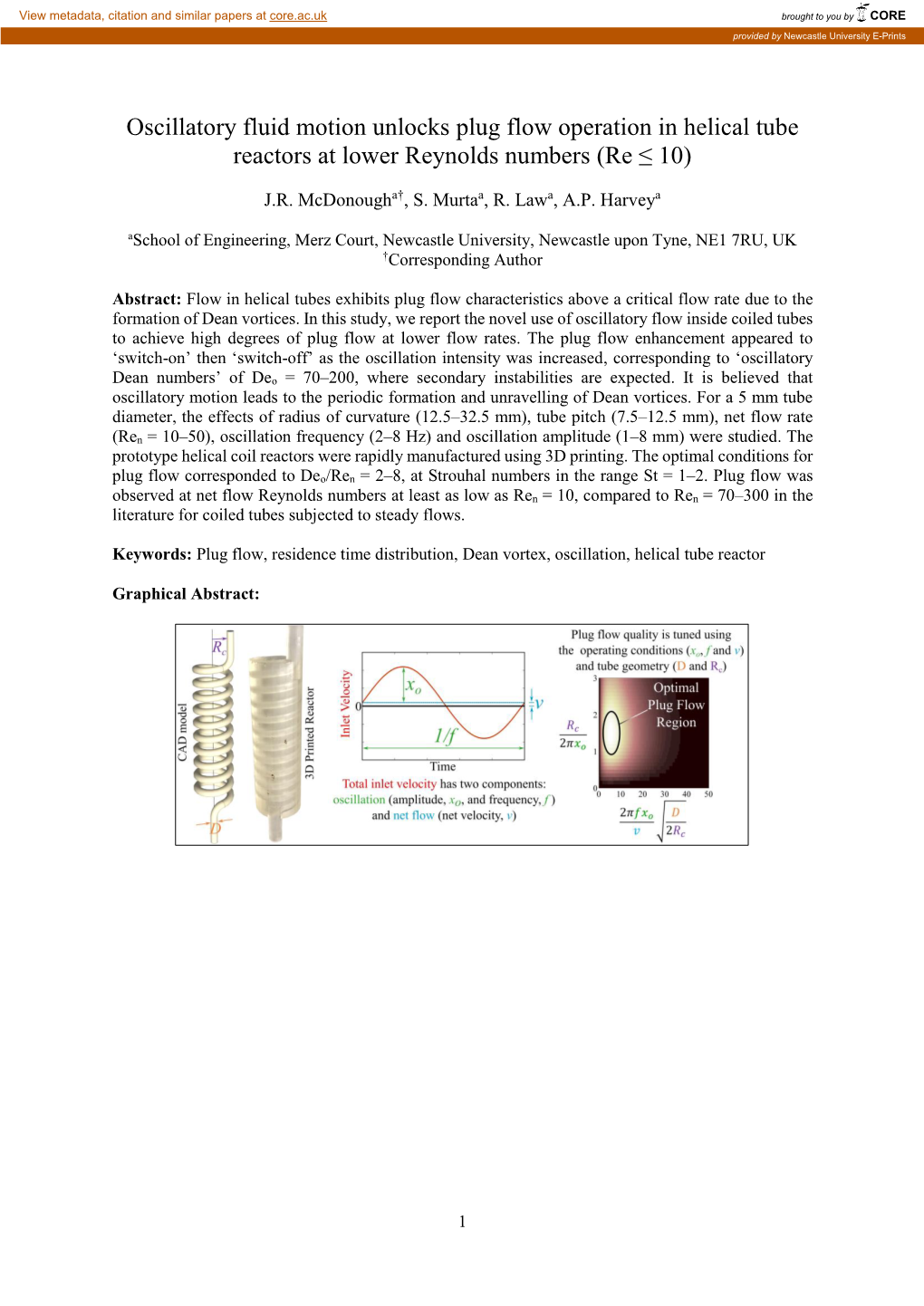
Load more
Recommended publications
-
Effect of Dean Number on Heating Transfer Coefficients in an Flat Bottom Agitated Vessel
IOSR Journal of Engineering May. 2012, Vol. 2(5) pp: 945-951 Effect of Dean Number on Heating Transfer Coefficients in an Flat Bottom Agitated Vessel 1*Ashok Reddy K 2 Bhagvanth Rao M 3 Ram Reddy P 1*..Professor Dept. of Mechanical Engineering ,Prof Rama Reddy College of Engineering & Technology Nandigoan(V) Pantacheru(M) Greater Hyderabad A P 2. Director CVSR College of Engineering Ghatkesar(M) R R Dist A P 3 .Director Malla Reddy College of Engineering Hyderbad A P ABSTRACT Experimental work has been reviewed using non- Newtonian and Newtonian fluids like Sodium Carboxymethal Cellulose with varying concentrations 0.05%,0.1%,0.15% and 0.2% with two different lengths (L=2.82m,L=2.362m) and outer diameter do=6.4mm,inner diameter di=4.0mm in an mixing vessel completely submerged helical coil. In our present study, the effect impeller speed, discharge ,flow behavior index(n) and consistency index (K) of test fluids with dimensionless curvature of the helical coil based on characteristic diameter were presented.. Keywords: Dean Number, Curvature, Heating Rates, Agitated Vessel I. Introduction To improve the performance of heat transfer rates, the fundamental aspect of flow patterns is an essential and important criteria in the helical coil design theory. The helical coil silent features consists of a inner diameter di and mean coil diameter Dm which is also known as pitch circle diameter of the coil. The ratio of coil pipe diameter to the mean coil diameter is known as dimensionless curvature .The ratio of pitch of the helical coil to the developed length of one turn is called non dimensional pitch .The angle which makes with plane geometry perpendicular to the axis of the one turn of the coil dimensions ic defined as helix angle. -
Introduction to Biofluid Mechanics Portonovo S
To protect the rights of the author(s) and publisher we inform you that this PDF is an uncorrected proof for internal business use only by the author(s), editor(s), reviewer(s), Elsevier and typesetter TNQ Books and Journals Pvt Ltd. It is not allowed to publish this proof online or in print. This proof copy is the copyright property of the publisher and is confidential until formal publication. CHAPTER 16 Introduction to Biofluid Mechanics Portonovo S. Ayyaswamy OUTLINE 16.1 Introduction e2 Exercises e71 16.2 The Circulatory System in the Acknowledgments e72 Human Body e2 Literature Cited e72 16.3 Modeling of Flow in Blood Vessels e18 Supplemental Reading e73 16.4 Introduction to the Fluid Mechanics of Plants e65 CHAPTER OBJECTIVES • To properly introduce the subject of biofluid • To review the parametric impact of the prop- mechanics including the necessary language erties of rigid, flexible, branched, and curved fl • To describe the components of the human cir- tubes on blood ow culation system and document their nominal • To provide an overview of fluid transport in characteristics plants • To present analytical results of relevant models of steady and pulsatile blood flow Fluid Mechanics http://dx.doi.org/10.1016/B978-0-12-405935-1.00016-2 e1 Copyright © 2016 Elsevier Inc. All rights reserved. To protect the rights of the author(s) and publisher we inform you that this PDF is an uncorrected proof for internal business use only by the author(s), editor(s), reviewer(s), Elsevier and typesetter TNQ Books and Journals Pvt Ltd. It is not allowed to publish this proof online or in print. -
Extended Stokes Series for Dean Flow in Weakly Curved Pipes
EXTENDED STOKES SERIES FOR DEAN FLOW IN WEAKLY CURVED PIPES A thesis presented for the degree of Doctor of Philosophy of Imperial College by Florencia Amalia Tettamanti Department of Mathematics Imperial College 180 Queen’s Gate, London SW7 2BZ June 24, 2012 2 I certify that this thesis, and the research to which it refers, are the product of my own work, and that any ideas or quotations from the work of other people, published or otherwise, are fully acknowledged in accordance with the standard referencing practices of the discipline. Signed: 3 Copyright Copyright in text of this thesis rests with the Author. Copies (by any process) either in full, or of extracts, may be made only in accordance with instructions given by the Author and lodged in the doctorate thesis archive of the college central library. Details may be obtained from the Librarian. This page must form part of any such copies made. Further copies (by any process) of copies made in accordance with such instructions may not be made without the permission (in writing) of the Author. The ownership of any intellectual property rights which may be described in this thesis is vested in Imperial College, subject to any prior agreement to the contrary, and may not be made available for use by third parties without the written permission of the University, which will prescribe the terms and conditions of any such agreement. Further information on the conditions under which disclosures and exploitation may take place is available from the Imperial College registry. 4 5 Abstract This thesis considers steady, fully-developed flows through weakly curved pipes using the extended Stokes series method. -
(English Edition) a Review on the Flow Instability of Nanofluids
Appl. Math. Mech. -Engl. Ed., 40(9), 1227–1238 (2019) Applied Mathematics and Mechanics (English Edition) https://doi.org/10.1007/s10483-019-2521-9 A review on the flow instability of nanofluids∗ Jianzhong LIN†, Hailin YANG Department of Mechanics, State Key Laboratory of Fluid Power and Mechatronic Systems, Zhejiang University, Hangzhou 310027, China (Received Mar. 22, 2019 / Revised May 6, 2019) Abstract Nanofluid flow occurs in extensive applications, and hence has received widespread attention. The transition of nanofluids from laminar to turbulent flow is an important issue because of the differences in pressure drop and heat transfer between laminar and turbulent flow. Nanofluids will become unstable when they depart from the thermal equilibrium or dynamic equilibrium state. This paper conducts a brief review of research on the flow instability of nanofluids, including hydrodynamic instability and thermal instability. Some open questions on the subject are also identified. Key words nanofluid, thermal instability, hydrodynamic instability, review Chinese Library Classification O358, O359 2010 Mathematics Subject Classification 76E09, 76T20 1 Introduction Nanofluids have aroused significant interest over the past few decades for their wide applica- tions in energy, machinery, transportation, and healthcare. For example, low concentration of particles causes viscosity changes[1–2], decreases viscosity with increasing shear rate[3], changes friction factors and pressure drops[4–6], and improves heat transfer[7–9]. Moreover, the unique flow properties of nanofluids are determined by the flow pattern. Heat transfer[10] and pressure drop[11] are also much lower and higher, respectively, in laminar flow than in turbulent flow. By adding particles to the fluid, the thermal entropy generation and friction are of the same order of magnitude as in turbulent flow, while the effect of heat transfer entropy generation strongly outweighs that of the friction entropy generation in laminar flow. -
Blood Flow in Arteries
November 8, 1996 13:58 Annual Reviews KUTEXT.DOC AR23-12 Annu. Rev. Fluid Mech. 1997. 29:399–434 Copyright c 1997 by Annual Reviews Inc. All rights reserved BLOOD FLOW IN ARTERIES David N. Ku G. W. Woodruff School of Mechanical Engineering, Georgia Institute of Technology, Atlanta, Georgia 30332-0405 ABSTRACT Blood flow in arteries is dominated by unsteady flow phenomena. The cardiovas- cular system is an internal flow loop with multiple branches in which a complex liquid circulates. A nondimensional frequency parameter, the Womersley num- ber, governs the relationship between the unsteady and viscous forces. Normal arterial flow is laminar with secondary flows generated at curves and branches. The arteries are living organs that can adapt to and change with the varying hemo- dynamic conditions. In certain circumstances, unusual hemodynamic conditions create an abnormal biological response. Velocity profile skewing can create pock- ets in which the direction of the wall shear stress oscillates. Atherosclerotic dis- ease tends to be localized in these sites and results in a narrowing of the artery lumen—a stenosis. The stenosis can cause turbulence and reduce flow by means of viscous head losses and flow choking. Very high shear stresses near the throat of the stenosis can activate platelets and thereby induce thrombosis, which can totally block blood flow to the heart or brain. Detection and quantification of by CAPES on 04/01/09. For personal use only. stenosis serve as the basis for surgical intervention. In the future, the study of arterial blood flow will lead to the prediction of individual hemodynamic flows in any patient, the development of diagnostic tools to quantify disease, and the design of devices that mimic or alter blood flow. -
Secondary Flow Structures Under Stent-Induced Perturbations for Cardiovascular Flow in a Curved Artery Model
SECONDARY FLOW STRUCTURES UNDER STENT-INDUCED PERTURBATIONS FOR CARDIOVASCULAR FLOW IN A CURVED ARTERY MODEL Autumn L. Glenn, Kartik V. Bulusu, and Michael W. Plesniak Department of Mechanical and Aerospace Engineering The George Washington University 801 22 nd Street, N.W, Washington, D.C. 20052 [email protected] Fangjun Shu Department of Mechanical and Aerospace Engineering New Mexico State University MSC 3450, P.O. Box 30001, Las Cruces, NM 88003-8001 [email protected] ABSTRACT by the complex geometry and inherent forcing functions, as Secondary flows within curved arteries with unsteady well as changes due to disease. Strong evidence linking forcing are well understood to result from amplified cellular biochemical response to mechanical factors such as centrifugal instabilities under steady-flow conditions and are shear stress on the endothelial cells lining the arterial wall has expected to be driven by the rapid accelerations and received considerable interest (Berger and Jou, 2000; Barakat decelerations inherent in such waveforms. They may also and Lieu, 2003; White and Frangos, 2007; Melchior and affect the function of curved arteries through pro-atherogenic Frangos, 2010). Secondary flow structures may affect the wall shear stresses, platelet residence time and other vascular wall shear stress in arteries, which is known to be closely response mechanisms. related to atherogenesis (Mallubhotla et al., 2001; Evegren et Planar PIV measurements were made under multi-harmonic al., 2010). non-zero-mean and physiological carotid artery waveforms at In curved tubes, secondary flow structures characterized various locations in a rigid bent-pipe curved artery model. by counter-rotating vortex pairs (Dean vortices) are well- Results revealed symmetric counter-rotating vortex pairs that understood to result from amplified centrifugal instabilities developed during the acceleration phases of both multi- under steady flow conditions. -
On Dimensionless Numbers
chemical engineering research and design 8 6 (2008) 835–868 Contents lists available at ScienceDirect Chemical Engineering Research and Design journal homepage: www.elsevier.com/locate/cherd Review On dimensionless numbers M.C. Ruzicka ∗ Department of Multiphase Reactors, Institute of Chemical Process Fundamentals, Czech Academy of Sciences, Rozvojova 135, 16502 Prague, Czech Republic This contribution is dedicated to Kamil Admiral´ Wichterle, a professor of chemical engineering, who admitted to feel a bit lost in the jungle of the dimensionless numbers, in our seminar at “Za Plıhalovic´ ohradou” abstract The goal is to provide a little review on dimensionless numbers, commonly encountered in chemical engineering. Both their sources are considered: dimensional analysis and scaling of governing equations with boundary con- ditions. The numbers produced by scaling of equation are presented for transport of momentum, heat and mass. Momentum transport is considered in both single-phase and multi-phase flows. The numbers obtained are assigned the physical meaning, and their mutual relations are highlighted. Certain drawbacks of building correlations based on dimensionless numbers are pointed out. © 2008 The Institution of Chemical Engineers. Published by Elsevier B.V. All rights reserved. Keywords: Dimensionless numbers; Dimensional analysis; Scaling of equations; Scaling of boundary conditions; Single-phase flow; Multi-phase flow; Correlations Contents 1. Introduction ................................................................................................................. -
Numerical Investigation of the Effect of Curvature and Reynold's Number
mp Co uta & tio d n e a li Mwangi et al., J Appl Computat Math 2017, 6:3 l p M p a Journal of A t h DOI: 10.4172/2168-9679.1000363 f e o m l a a n t r ISSN: 2168-9679i c u s o J Applied & Computational Mathematics Research Article Open Access Numerical Investigation of the Effect of Curvature and Reynold’s Number to Radial Velocity in a Curved Porous Pipe Mwangi DM1* Karanja S1 and Kimathi M2 1Meru University of Science and Technology, Meru, Kenya 2Technical University of Kenya, Nairobi Kenya, Nairobi, Kenya Abstract Different irrigation methods are being used in agriculture. However, due to scarcity of water, irrigation methods that use water efficiently are needed. The Motivation of this study is the increasing use of porous pipes to meet this requirement. The objective of this study is to investigate the effect of curvature and Reynold’s number on radial velocity profile of water across a porous wall of a curved pipe with circular cross-section, constant permeability, k and porosity, φ. The momentum equations of the two dimensional flow are written in toroidal coordinates. The main flow in the pipe is only characterized by δ and Re as the only non-dimensional groups of numbers. We also considered the flow to be fully developed, unsteady, laminar and irrotational. Darcy law is used to analyse the flow across the porous membrane. The main flow was coupled with the flow through the porous wall of the pipe. The equations were solved using finite difference method. -
The Effect of Entrance Flow Development on Vortex Formation
The effect of entrance flow development on vortex formation and wall shear stress in a curved artery model Christopher Coxa) and Michael W. Plesniakb) Department of Mechanical and Aerospace Engineering, The George Washington University, Washington, DC 20052, USA We numerically investigate the effect of entrance condition on the spatial and temporal evolution of multiple three- dimensional vortex pairs and wall shear stress distribution in a curved artery model. We perform this study using a Newtonian blood-analog fluid subjected to a pulsatile flow with two inflow conditions. The first flow condition is fully developed while the second condition is undeveloped (i.e. uniform). We discuss the connection along the axial direction between regions of organized vorticity observed at various cross-sections of the model and compare results between the different entrance conditions. We model a human artery with a simple, rigid 180◦ curved pipe with circular cross-section and constant curvature, neglecting effects of taper, torsion and elasticity. Numerical results are computed from a discontinuous high-order spectral element flow solver. The flow rate used in this study is physiological. We observe differences in secondary flow patterns, especially during the deceleration phase of the physiological waveform where multiple vortical structures of both Dean-type and Lyne-type coexist. We highlight the effect of the entrance condition on the formation of these structures and subsequent appearance of abnormal inner wall shear stresses—a potentially significant correlation since cardiovascular disease is known to progress along the inner wall of curved arteries under varying degrees of flow development. Keywords: cardiovascular flows, wall shear stress, vortex dynamics, computational fluid dynamics, discontinuous spectral element I. -
Steady Laminar Flow in a 90° Bend DOI: 10.1177/1687814016669472 Aime.Sagepub.Com
Research Article Advances in Mechanical Engineering 2016, Vol. 8(9) 1–9 Ó The Author(s) 2016 Steady laminar flow in a 90° bend DOI: 10.1177/1687814016669472 aime.sagepub.com Asterios Pantokratoras Abstract This research undertook an assessment of the characteristics of laminar flow in a 90° bend. The research utilised the computational fluid dynamics software tool ANSYS Fluent, adopting a finite volume method. The study focused on pres- sure decreases, velocity profiles, Dean vortices and Dean cells present in the bend. The results indicated that the Dean vortices first appear slightly at the bend, take a clear form at the exit pipe and disappear further downstream. This article contains also an original chart for determining the Darcy–Weisbach friction factor, while the areas of pipe where Dean vortices and Dean cells formed are presented in a bifurcation diagram. Keywords Curved pipe, bend, laminar, friction factor, Dean vortices Date received: 11 May 2016; accepted: 18 August 2016 Academic Editor: Ishak Hashim Introduction analysis of data concerning declining pressure during turbulent flow in smooth-pipe curves. Pipe bends of An investigation of flow through bends has consider- varying angle were attached to linear piping, to form a able relevance and application to a vast array of situa- consistent entrance and exit flow. Laser-Doppler data tions, given their presence in almost all pipelines. were acquired by Enayet et al.,5 by assessing a 90° pipe Interest has arisen, for instance, concerning the charac- curve’s laminar flow characteristics, where the pipe’s teristics of falls in pressure in the emerging and com- cross-sectional profile had a curvature of d = 0.18. -
Bifurcations in Curved Duct Flow Based on a Simplified Dean Model
Rigo, Biau & Gloerfelt Bifurcations in curved duct flow based on a simplified Dean model Leonardo Rigo, Damien Biau,a) and Xavier Gloerfelt Dynfluid Laboratory, Ecole´ Nationale Superieure d’Arts et M´etiers. 151 Boulevard de l’Hˆopital, 75013 Paris, France (Dated: 10 April 2020) We present a minimal model of an incompressible flow in square duct subject to a slight curvature. Using a Poincar´e-like section we identify stationary, periodic, aperiodic and chaotic regimes, depending on the unique control parameter of the problem: the Dean number (De). Aside from representing a simple, yet rich, dynamical system the present simplified model is also representative of the full problem, reproducing quite accurately the bifurcation points observed in the literature. We analyse the bifurcation diagram from De = 0 (no curvature) to De = 500, observing a periodic segment followed by two separate chaotic regions. The phase diagram of the flow in the periodic regime shows the presence of two symmetric steady states, the system oscillates around these solutions following a heteroclinic cycle. In the appendix some quantitative results are provided for validation purposes, as well as the python code used for the numerical solution of the Navier-Stokes equations. PACS numbers: Valid PACS appear here Keywords: Navier-Stokes equations, deterministic chaos, curved flow, Dean vortices The flow in a curved square duct is governed by for the flow in a pipe or square duct subject to a slight the Navier-Stokes (NS) equations in polar coor- curvature, based on a truncation of the Navier-Stokes dinates. The dynamics of this kind of flow can (NS) equations written in polar coordinates. -
Steady Streaming Motion in Entrance Region of Curved Tubes During Oscillatory Flow
Avestia Publishing Journal of Fluid Flow, Heat and Mass Transfer Volume 4, Year 2017 ISSN: 2368-6111 DOI: 10.11159/jffhmt.2017.005 Steady Streaming Motion in Entrance Region of Curved Tubes during Oscillatory Flow Masaru Sumida Kindai University, Faculty of Engineering 1 Takaya Umenobe, Higashi-Hiroshima, 739-2116, Japan [email protected] Abstract - An experimental investigation was carried out on Nomenclature the development of oscillatory laminar flow in curved tubes a radius of tube, ad2 (d: tube diameter) with a turn angle of 180 (i.e., U-shaped tubes) and curvature D Dean number, D =Re Rc-1/2 radius ratios Rc of 4 and 10. Experiments were conducted Q Flow rate under Womersley numbers of 18 to 30 and Dean numbers D R curvature radius of tube axis of 150 and 300, giving (2/D) above 0.655, for which the characteristics of the oscillatory flow in the fully developed Rc curvature radius ratio, Rc=R/a region of the curved tubes are roughly divisible into two. The Re Reynolds number, Re =2awm,o / secondary flow induced in the cross section was visualized by a S secondary flow velocity solid tracer method with a stroboscopic light and was recorded T oscillation period, T 2 ( : angular photographically at several stations upstream and frequency) downstream from the entrance of the curved tube. The u,v, w velocities in x, y and z directions, respecttively development of the secondary flow and transitions between the wm axial velocity averaged over cross section straight-tube and curved-tube oscillatory flows were x, y, z coordinate system, see Figure 3 systematically investigated in detail.