LOE Ultrasonic Level Sensors User Manual
Total Page:16
File Type:pdf, Size:1020Kb
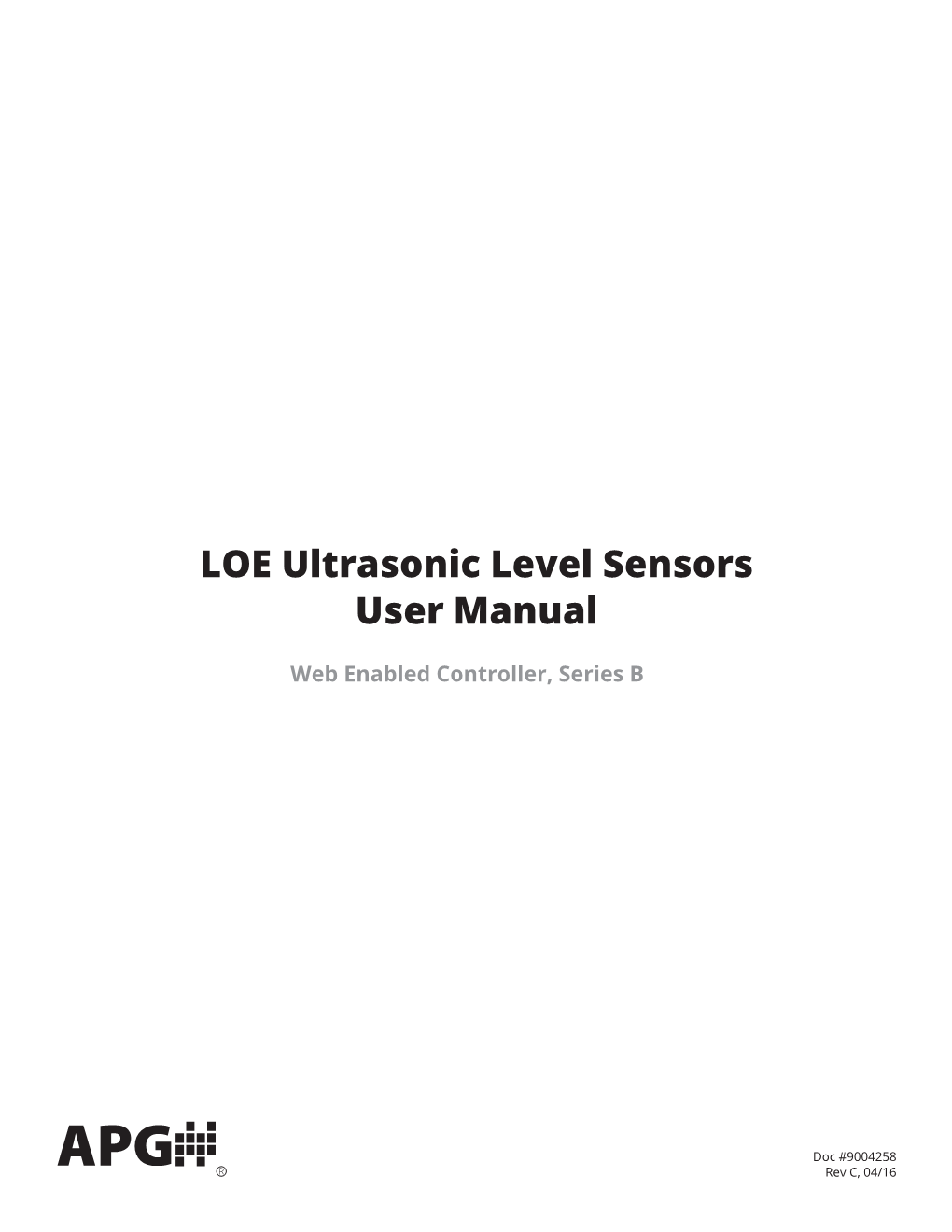
Load more
Recommended publications
-
Microwave Sensing of Water Quality
SPECIAL SECTION ON ADVANCED SENSOR TECHNOLOGIES ON WATER MONITORING AND MODELING Received April 22, 2019, accepted May 19, 2019, date of publication May 27, 2019, date of current version June 10, 2019. Digital Object Identifier 10.1109/ACCESS.2019.2918996 Microwave Sensing of Water Quality KUNYI ZHANG1, (Student Member, IEEE), REZA K. AMINEH 1, (Senior Member, IEEE), ZIQIAN DONG 1, (Senior Member, IEEE), AND DAVID NADLER2 1Department of Electrical and Computer Engineering, New York Institute of Technology, New York, NY 10023, USA 2Department of Environmental Technology and Sustainability, New York Institute of Technology, Old Westbury, NY 11568, USA Corresponding author: Reza K. Amineh ([email protected]) This work was partially supported by the U.S. National Science Foundation under Grant 1841558. ABSTRACT Fine-grained water quality data can facilitate the optimized management of water resources, which have become increasingly scarce due to population growth, increased demand for safe sources of water, and environmental pollutions. There is a pressing need for cost-effective, reliable, re-usable, and autonomous water sensing technologies that can provide accurate real-time water quality measurements. In this paper, we present a microwave sensor array with sensing elements operating at different frequencies in the wide frequency band of 1 GHz to 10 GHz. The use of array allows for collecting more information compared with a single sensor system. The sensor array can be fabricated in a cost-effective way through standard printed circuit board (PCB) technology. Here, it is tested with water solutions of various contam- inants and parameter values. The dielectric properties of the water sample with different contaminants and parameter values are measured and provided as well. -
Level Sensors
1-800-633-0405 For the latest prices, please check AutomationDirect.com EchoPod/EchoTouch® Reflective Technology™ Ultrasonic Liquid Level Sensors Overview The innovative EchoPod/EchoTouch Reflective Techonolgy ultrasonic liquid level sensors replace other ultrasonic level sensors in condensation applications, as well as float, conductance and pressure sensors that fail due to contact with dirty, sticky and scaling media in small, medium and large capacity tanks. Applied in chemical, water and wastewater applications, these general purpose or intrinsically safe non-contact sensors are available with single and multi-function capabilities, including continuous level measurement, switching and control. The standard 4-20 mA output is easily monitored by a PLC or other controller. Models with four relays can be configured for level alarms and/or stand- alone level control such as automatic fill or empty functions using the embedded level controller. PC configuration of all models is simple with WebCal™ software, while the UG06, UG12 and US06 models also offer limited configuration via their pushbuttons and integral display. What is Reflective Technology™? Condensation is the most commonly encountered variable in liquid level applications. Condensation attenuates the acoustic signal of ultrasonic sensors that have a flat horizontal transducer face, weakening their signal strength and signal-to-noise ratio by up to 50%, and substantially reducing their measurement reliability. At the core of Reflective Technology™ is a simple fact: unlike flat horizontal surfaces, significant water droplets cannot adhere to smooth vertical surfaces. By orienting the internal ultrasonic transducer vertically, condensation runs off the transducer face and does not affect sensor performance. The unimpeded transmit and receive signals are redirected to and from the liquid off a 45º reflector, delivering reliable level measurement. -
TEMPERATURE and LIQUID-LEVEL SENSOR for LIQUID-HYDROGEN PRESSURIZATION and EXPULSION STUDIES by Robert J
NASA TECHNICAL NOTE ---NASA TN D-4339 c./ o* m m d I m L TEMPERATURE AND LIQUID-LEVEL SENSOR FOR LIQUID-HYDROGEN PRESSURIZATION AND EXPULSION STUDIES by Robert J. Stochl und Richard L. DeWitt Lewis Reseurch Center CZeveZund, Ohio NATIONAL AERONAUTICS AND SPACE ADMINISTRATION WASHINGTON, D. C. FEBRUARY 1968 TECH LIBRARY KAFB, NM __ . 0333238 TEMPERATURE AND LIQUID-LEVEL SENSOR FOR LIQUID- HYDROGEN PRESSURIZATION AND EXPULSION STUDIES By Robert J. Stochl and Richard L. DeWitt Lewis Research Center Cleveland, Ohio NATIONAL AERONAUTICS AND SPACE ADMINISTRATION ~~ For sale by the Clearinghouse for Federal Scientific and Technical Information Springfield, Virginia 22151 - CFSTI price $3.00 TEMPERATURE AND LIQU I D-LEVEL SENSOR FOR LlQU ID-HY D ROGEN PRESSURIZATION AND EXPULSION STUDIES by Robert J. Stochl and Richard L. DeWitt Lewis Research Center SUMMARY In experimental studies of the pressurization and expulsion of liquid hydrogen, temperature-measuring systems are needed to understand the effectiveness of a parti- cular pressurization system. Existing state-of -the-art temperature-measuring systems are considered inadequate to meet the rather stringent design requirements necessary for accuracy and precision in the measurement of ullage gas temperatures. A temperature-measurement technique that uses thermopiles (i. e. , thermocouples in series) as sensors was therefore developed. The results of this development indicate (1) that an instrument rake using measurement stations constructed of thermopiles can measure temperatures to within *l.65' K (for gas temperatures between 20' and 300' K) and (2) that, in addition to their use as temperature sensors, thermopile units can be used as point liquid-level sensors for subcooled liquid during liquid outflow. -
Liquid Metal Diagnostics
Fusion Science and Technology ISSN: 1536-1055 (Print) 1943-7641 (Online) Journal homepage: https://www.tandfonline.com/loi/ufst20 Liquid Metal Diagnostics M. G. Hvasta, G. Bruhaug, A. E. Fisher, D. Dudt & E. Kolemen To cite this article: M. G. Hvasta, G. Bruhaug, A. E. Fisher, D. Dudt & E. Kolemen (2019): Liquid Metal Diagnostics, Fusion Science and Technology, DOI: 10.1080/15361055.2019.1661719 To link to this article: https://doi.org/10.1080/15361055.2019.1661719 Published online: 18 Nov 2019. Submit your article to this journal View related articles View Crossmark data Full Terms & Conditions of access and use can be found at https://www.tandfonline.com/action/journalInformation?journalCode=ufst20 FUSION SCIENCE AND TECHNOLOGY © 2019 American Nuclear Society DOI: https://doi.org/10.1080/15361055.2019.1661719 Liquid Metal Diagnostics M. G. Hvasta, a G. Bruhaug, b A. E. Fisher, c D. Dudt, c and E. Kolemen c* aAlkali Consulting LLC, Lawrenceville, New Jersey bUniversity of Rochester, Rochester, New York cPrinceton University, Princeton, New Jersey Received June 16, 2018 Accepted for Publication August 16, 2019 Abstract — Liquid metal (LM) plasma-facing components (PFCs) (LM-PFCs) within next-generation fusion reactors are expected to enhance plasma confinement, facilitate tritium breeding, improve reactor thermal efficiency, and withstand large heat and particle fluxes better than solid components made from tungsten, molybdenum, or graphite. Some LM divertor concepts intended for long-pulse operation at >20 MW/m2 incorporate thin (~1 cm), fast-moving (~5 to 10 m/s), free-surface flows. Such systems will require a range of diagnostics to monitor and control the velocity, flow depth, temperature, and impurity concentration of the LM. -
LEVEL MEASUREMENT TECHNOLOGIES How To
Q1 2016 Your Top 10 LEVEL Customers of 2015 MEASUREMENT Will Not be Your TECHNOLOGIES In The Process Top 10 of 2016 Control Industry þ What You Should Do How to Two Birds with MEASURE One Stone FLOW RATE Level Indication with Level & Pump Control Sensors NEWPREDIG.COM Redesigned. Responsive. Resourceful. www.predig.com Not a subscriber? Subscribe to ON DISPLAY subscribe.predig.com Table of Contents The Eclectic Engineer: How to Measure Flow Rate with Level Sensors 5 Two Birds with One Stone: Reader’s Level Indication and Pump Control with Brief The PROVU® Series 6 Your Top 10 Customers of 2015 Will Our first issue of 2016 is entirely dedicated to level measurement. Learn about various Not be Your Top 10 of 2016. What You topics on the subject including how to measure Should Do About It. flow rate using level sensors, level indication 9 and pump control using one device, and an introduction to level measurement technologies to guide you in selecting level instrumentation. Make sure to visit our brand new website. The completely redesigned site, now mobile friendly, offers great new features including easy product configurator, lead times checker, and more. Visit www.predig.com. We'd like to hear from you, our readers! Level Measurement Technologies Tell us how we are doing or recommend topics In The Process Control Industry for future articles. Send your feedback to 10 [email protected]. - Precision Digital contact us U.S. & Canada Tech Support 1-800-343-1001 [email protected] International Sales 1-508-655-7300 [email protected] Corporate Office 233 South St • Hopkinton, MA 01748 USA 2 Redesigned. -
Float Type Level Switches Contents Page Start Single Point Small Size Engineered Plastic
INTRODUCTION Float Type Level Switches Contents Page Start Single Point Small Size Engineered Plastic ........................................... A-2 GEMS Level Switches operate on a direct, Alloy ........................................................................ A-8 simple principle. In most models, a float encircling a stationary stem is equipped Large Size PERMANENT with powerful, permanent magnets. As MAGNET Engineered Plastic .........................................A-12 the float rises or lowers with liquid level, Alloy ......................................................................A-13 the magnetic field generated from within FLOAT the float actuates a hermetically sealed, Specialty Switches ...............................................A-20 magnetic reed switch mounted within the HERMETICALLY stem. The stem is made of non-magnetic SEALED MAGNETIC REED SWITCH Leak Detection .......................................................A-22 metals or rugged, engineered plastics. When mounted vertically, this basic design provides a consistent accuracy of ±1/8 inch. Multi-station versions use a separate reed switch for each level point being monitored. Side-mounted units use different actuation methods because of their horizontal attitude. The basic principle, however, is the same: as a direct result of rising or falling liquid, a magnetic field is moved into the proximity of a reed switch, causing its actuation. N Reed Switch Reliability – SINGLE POINT LEVEL SWITCHES GLASS The durable construction of these reed switch designs ensures long, trouble- REED SWITCH ENVELOPE free service. Because the effects of shock, wear and vibration are minimized, these hermetically sealed switches provide precise S repeatability with no more than 1% deviation. The switch actuation points N S remain constant over the life of the unit. See “Reed Switch Protection” in MAGNET Appendix X for information on extending the life of GEMS Level Switches. -
Radar Level Sensor
RADAR LEVEL SENSOR LVRD501 Series U Non-Contact Measurement U Continuous Level Measurement U Pulse Radar Measurement Range: 0.254 to 15 m (10" to 50') U Simple Pushbutton Calibration U Communications Standard The LVRD500 Series a logical extension to the ultrasonic sensor LVRD501-RS232 series, is designed for applications shown smaller requiring non-contact liquid level than actual size. measurement, in which ultrasonic level measurement is not acceptable. The LVRD500 Series radar technology can be adjusted for variables such as materials to be measured, vessel configuration, and system interface. These sensors are ideal when vapor, dust, or a foaming surface prevents ultrasonic-wave measurements. LVRD500 Series radar sensors can detect the level under a layer of light dust or airy foam, but if the dust particle size increases, or if the foam or dust gets thick, they will no longer detect the liquid level. Instead, the level of the dust or foam will be measured. Internal piping, deposits on the antenna, multiple reflections, or reflections from the wall can interfere with of the target from the antenna the proper operation of the and the dielectric constant of radar sensor. Other sources of the reflecting material. interference are rat-holing and LVRD500 sensors feature bridging of solids, as well as angled The antenna comes in polypropylene process material surfaces that can “echo marker” signal process- ing, making them among the most or an optional high resistance PTFE reflect the radar beam away from that can help protect against material the receiver. technologically advanced pulse radar systems on the market. This buildup. -
Water Level Sensor Testing ITRC Report No
Water Level Sensor Testing http://www.itrc.org/reports/pdf/testing.pdf ITRC Report No. 04-005 IRRIGATION TRAINING AND RESEARCH CENTER Water Level Sensor Testing November 2002/ December 2003 Water Level Sensor Testing http://www.itrc.org/reports/pdf/testing.pdf ITRC Report No. 04-005 IRRIGATION TRAINING AND RESEARCH CENTER Prepared by Dr. Stuart Styles Sarah Herman Marcus Yasutake Chuck Keezer Irrigation Training and Research Center (ITRC) California Polytechnic State University San Luis Obispo, CA 93407-0730 805-756-2429 www.itrc.org Prepared for Bryce White Water Conservation Office Mid-Pacific Region United States Bureau of Reclamation Sacramento, California Disclaimer: Reference to any specific process, product or service by manufacturer, trade name, trademark or otherwise does not necessarily imply endorsement or recommendation of use by either California Polytechnic State University, the Irrigation Training and Research Center, or any other party mentioned in this document. No party makes any warranty, express or implied and assumes no legal liability or responsibility for the accuracy or completeness of any apparatus, product, process or data described previously. This report was prepared by ITRC as an account of work done to date. All designs and cost estimates are subject to final confirmation. Irrigation Training and Research Center December 2003 Water Level Sensor Testing http://www.itrc.org/reports/pdf/testing.pdf ITRC Report No. 04-005 EXECUTIVE SUMMARY The findings presented here are the continuation of a series of studies begun in 1998 by the Irrigation Training and Research Center (ITRC) at California Polytechnic State University (Cal Poly), San Luis Obispo, California, on behalf of the Mid-Pacific Region of the United States Bureau of Reclamation (USBR) to test water level sensors under a variety of hydraulic conditions. -
Level Measuring Instruments Part of Your Business
Product review Level measuring instruments Part of your business Contents WIKA product lines 3 Measurement via communicating chambers 4 Continuous in-tank measurement 10 Measurement of switch points in the tank 12 Submersible pressure transmitters 16 Customer-specific versions 17 Accessories 18 Technical information 19 WIKA worldwide 20 Ability to meet any challenge As a family-run business acting globally, with over 7,900 With manufacturing locations around the globe, WIKA highly qualified employees, the WIKA group of companies ensures flexibility and the highest delivery performance. is a worldwide leader in pressure and temperature Every year, over 50 million quality products, both standard measurement. The company also sets the standard in and customer-specific solutions, are delivered in batches the measurement of level and flow, and in calibration of 1 to over 10,000 units. With numerous wholly-owned technology. Founded in 1946, WIKA is today a strong subsidiaries and partners, WIKA competently and reliably and reliable partner for all the requirements of industrial supports its customers worldwide. Our experienced measurement technology, thanks to a broad portfolio of engineers and sales experts are your competent and high-precision instruments and comprehensive services. dependable contacts locally. Efficient logistics Fully automatic Certified calibration production laboratories 2 WIKA product lines WIKA product lines The WIKA programme covers the following product lines for various fields of application. Electronic pressure measurement Electrical temperature measurement WIKA offers a complete range of electronic pressure Our range of products includes thermocouples, resistance measuring instruments: pressure sensors, pressure switches, thermometers (also with on-site display), temperature pressure transmitters and process transmitters for the switches as well as analogue and digital temperature measurement of gauge, absolute and differential pressure. -
Metamaterials
International Journal of Antennas and Propagation Metamaterials Guest Editors: Alejandro Lucas Borja, James R. Kelly, Fuli Zhang, and Eric Lheurette Metamaterials International Journal of Antennas and Propagation Metamaterials Guest Editors: Alejandro Lucas Borja, James R. Kelly, Fuli Zhang, and Eric Lheurette Copyright © 2013 Hindawi Publishing Corporation. All rights reserved. This is a special issue published in “International Journal of Antennas and Propagation.” All articles are open access articles distributed under the Creative Commons Attribution License, which permits unrestricted use, distribution, and reproduction in any medium, pro- vided the original work is properly cited. Editorial Board M. Ali, USA Se-Yun Kim, Republic of Korea S. M. Rao, USA C. Bunting, USA Ahmed A. Kishk, Canada S. R. Rengarajan, USA F. Catedra,´ Spain T. Kundu, USA Ahmad Safaai-Jazi, USA Dau-Chyrh Chang, Taiwan Ju-Hong Lee, Taiwan S. Safavi-Naeini, Canada Deb Chatterjee, USA B. Lee, Republic of Korea M. Salazar-Palma, Spain Z. N. Chen, Singapore L. Li, Singapore S. Selleri, Italy M. Y. W. Chia, Singapore Y. Lu, Singapore K. T. Selvan, India C. Christodoulou, USA Atsushi Mase, Japan Z. Q. Shen, Singapore Shyh-Jong Chung, Taiwan Andrea Massa, Italy John J. Shynk, USA L. Crocco, Italy G. Mazzarella, Italy M. S. J. Singh, Malaysia T. A. Denidni, Canada Derek McNamara, Canada Seong-Youp Suh, USA A. R. Djordjevic, Serbia C. Mecklenbrauker,¨ Austria P. Wahid, USA K. P. Esselle, Australia M. Midrio, Italy Y. Ethan Wang, USA F. Falcone, Spain Mark Mirotznik, USA D. S. Weile, USA Miguel Ferrando, Spain A. S. Mohan, Australia Quan Xue, Hong Kong V. -
Ultrasonic Liquid Level Sensors & Switches Sensors & Switches
Prices as of April 27, 2016. Check Web site for most current prices. Company Information Drives Soft Starters Level Sensors Motors Power Transmission Motion: Servos and Steppers Motor Controls Sensors: Proximity Up-to-date price list: Sensors: Photoelectric www.automationdirect.com/pricelist Sensors: FREE Technical Support: Encoders www.automationdirect.com/support Sensors: Limit Switches FREE Videos: Sensors: www.automationdirect.com/videos Current Sensors: In this interactive PDF you can: FREE Documentation: Pressure • Use bookmarks to navigate www.automationdirect.com/documentation Sensors: by product category Temperature FREE CAD drawings: Sensors: • Use bookmarks to save, www.automationdirect.com/cad Level search, print or e-mail the Sensors: catalog section Flow Pushbuttons • Click on part #s to link and Lights directly to our online store for current pricing, specs, Stacklights stocking information and Signal more Devices Process Relays and Timers Pneumatics: Air Prep Pneumatics: Directional Control Valves Pneumatics: Cylinders Pneumatics: Tubing Pneumatics: Air Fittings Appendix Book 2 Terms and Conditions Book 2 (14.3) www.automationdirect.com/ultrasonic-level-sensors Level Sensors eLE-1 Prices as of April 27, 2016. Check Web site for most current prices. Liquid Level Sensors and Switches Flowline® Ultrasonic Level Sensors and Switches (Non-contact) The Flowline EchoPod®, EchoSonic® II, Echotouch™, EchoSpan® and EchoSwitch® are innovative ultrasonic liquid level sensor families that replace float, conductance and pressure sensors that fail due to contact with dirty, sticky and scaling liquids in small, medium and large capacity tanks. These liquid level sensors can be used in either open or enclosed tanks (not suitable for pressurized tanks). PC software configured or pushbutton config- ured models are available. -
Ultrasonic Point Level Sensor
Product Overview Ultrasonic Point Level Sensor Product Overview The Fluid-Trac® PLS (Point Level Sensor) is a durable, economical control module for reliable limit level control OEM applications. The Fluid-Trac® PLS comes in a compact package that combines a smart point level ultrasonic level sensor, internal temperature compensation, embedded software and three low side output circuit drivers. The Fluid-Trac® PLS control module was designed for versatile external control capability. It can be interfaced to Relays, Switches, Pumps, Valves, Audible Alarms/Buzzers and Flashing Alarms. Listed below are a few of the typical OEM applications: • Single Point Control – Fluid-Trac® PLS can keep a tank from running dry or overflowing. The PLS can be factory programmed with a critical level set point so that whenever the set point is reached, the low side driver will close the circuit to allow a pump to turn on or open a valve. • Multiple Point Control – Fluid-Trac® PLS can be used for liquid level regulation to either keep a tank between two or three critical level set points or to activate two or three different external operations at each critical set point. Monitoring liquid levels to the factory programmable limit level set points allows for activation of pumps, valves and external alarms (audible, flasher, LED). For original equipment manufacturers, SSI engineering can customize the Fluid-Trac® PLS embedded software to provide the best solution for your unique application needs. Some custom options include the following: • Latching of Output Driver Circuit • Time Delays – When the level limit is tripped, the timer is started and the output is energized.