Environmental Assessment of Kuldispingh Port Facility, N.V. Paramaribo, Suriname
Total Page:16
File Type:pdf, Size:1020Kb
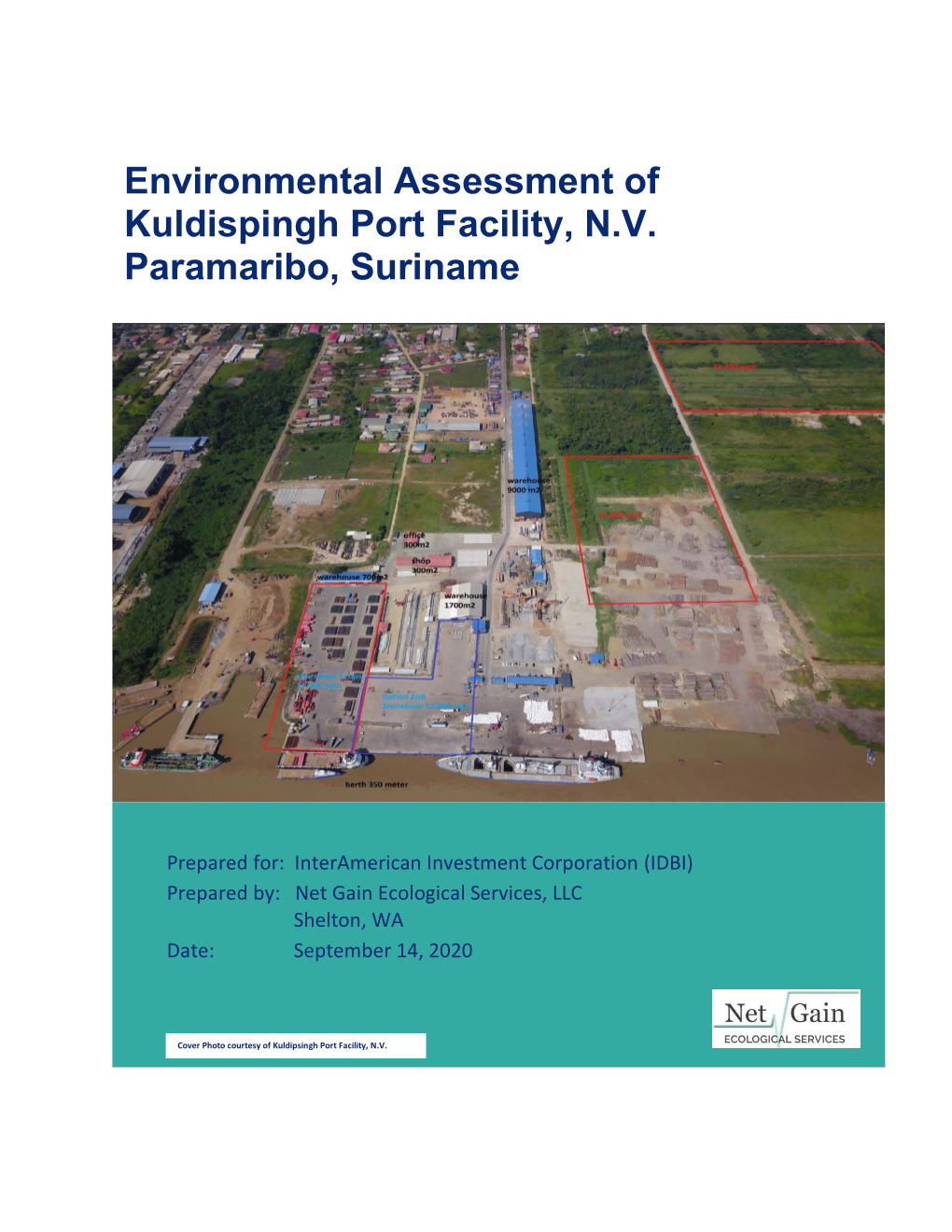
Load more
Recommended publications
-
November 2, 2019 Julien's Auctions: Property From
JULIEN’S AUCTIONS: PROPERTY FROM THE COLLECTION OF OLIVIA NEWTON-JOHN PRESS RELEASE For Immediate Release: JULIEN’S AUCTIONS: PROPERTY FROM THE COLLECTION OF OLIVIA NEWTON-JOHN Four-Time Grammy Award-Winning Pop Diva and Hollywood Superstar’s Iconic “Grease” Leather Jacket and Pants, “Physical” and “Xanadu” Wardrobe Pieces, Gowns, Awards and More to Rock the Auction Stage Portion of the Auction Proceeds to Benefit the Olivia Newton-John Cancer Wellness & Research Centre https://www.onjcancercentre.org NOVEMBER 2, 2019 Los Angeles, California – (June 18, 2019) – Julien’s Auctions, the world-record breaking auction house, honors one of the most celebrated and beloved pop culture icons of all time with their PROPERTY FROM THE COLLECTION OF OLIVIA NEWTON-JOHN (OBE, AC, HONORARY DOCTORATE OF LETTERS (LA TROBE UNIVERSITY)) auction event live at The Standard Oil Building in Beverly Hills and online at juliensauctions.com. Over 500 of the most iconic film and television worn costumes, ensembles, gowns, personal items and accessories owned and used by the four-time Grammy award-winning singer/Hollywood film star and one of the best-selling musical artists of all time who has sold 100 million records worldwide, will take the auction stage headlining Julien’s Auctions’ ICONS & IDOLS two-day music extravaganza taking place Friday, November 1st and Saturday, November 2nd, 2019. PAGE 1 Julien’s Auctions | 8630 Hayden Place, Culver City, California 90232 | Phone: 310-836-1818 | Fax: 310-836-1818 © 2003-2019 Julien’s Auctions JULIEN’S AUCTIONS: PROPERTY FROM THE COLLECTION OF OLIVIA NEWTON-JOHN PRESS RELEASE The Cambridge, England born and Melbourne, Australia raised singer and actress began her music career at the age of 14, when she formed an all-girl group, Sol Four, with her friends. -
Tour of Ewing Sites Connected with William Green
Visit Ewing Landmarks Connected with the William Green Family By Anne McArthur [email protected] or 609 510-9120 Sources: research by Billy O’Neal and sources in the Benjamin Temple House William Green I is one of Ewing’s earliest and most prominent settlers. Many Ewing citizens are familiar with his home, the William Green Farmhouse, listed on The National Registers of Historic Places, located on The College of New Jersey campus. Descendants of William Green are scattered throughout the United States. A recent question received by the Friends of the William Green Farmhouse inspired this article. A descendant of William Green I’s youngest son, Jeremiah, contacted the Friends and arranged a visit to his ancestor’s home. Jeremiah had moved to Tennessee in the 18th century and his descendant now lives in Alabama. When he visited, the Friends arranged a driving tour to view the outside of buildings associated with William Green and his descendants. Jeremiah’s descendant was impressed with how many historic treasures associated with his ancestors still survive. The Friends want to share with you information about sites related to the Green family still standing in Ewing. Enjoy a physical tour of these Ewing Township sites! None of the houses are open to the public but may be viewed from the exterior. If you or your friends have additional records about the Green family or their properties, please contact the author. William Green was a yeoman and an early Hunterdon County judge. He and his wife, Joanna Reeder, came to Ewing from Newtown, NY around 1700. -
Course Iii Valuation of Personal Property
GEORGIA DEPARTMENT OF REVENUE LOCAL GOVERNMENT SERVICES DIVISION COURSE III VALUATION OF PERSONAL PROPERTY "The statutory materials reprinted or quoted verbatim on the following pages are taken from the Official Code of Georgia Annotated, Copyright 2016 by the State of Georgia, and are reprinted with the permission of the State of Georgia. All rights reserved." For Educational Purposes Only: The material within is intended to give the course participant a solid understanding of general principles in the subject area. As such, the material may not necessarily reflect the official procedures and policies of the Georgia Department of Revenue or the Department’s official interpretation of the laws of the State of Georgia. The application of applicability to specific situations of the theories, techniques, and approaches discussed herein must be determined on a case‐by‐case basis. ` April 27, 2017 Georgia Department of Revenue Valuation of Personal Property 2 Georgia Department of Revenue Contents Course Description 4 Resources 5 Official Code of Georgia Annotated Legal Reference 6 Rules and Regulations of the State of Georgia 9 Judicial Decisions 13 Brief History of the Property Tax in Georgia 16 The Personal Property Appraisal Staff Statutory/Regulatory Duty 17 Personal Property Defined 18 Identification of Selected Items as Real or Personal 24 Classification and Stratum 30 Valuation Defined 33 The Appraisal Process 44 Appraisal Process Flow Chart 45 Definition of the Problem Identifying the property to be appraised 46 Determining the property -
Skinny Blues: Karen Carpenter, Anorexia Nervosa and Popular Music
Skinny blues: Karen Carpenter, anorexia nervosa and popular music George McKay We might locate that colloquial inauguration of anorexia on a Las Vegas nightclub stage in the fall of 1975, when the popular musician Karen Carpenter collapsed while singing ‘Top of the world’; or on the morning of 5 February 1983, when news [broke] of Carpenter’s death from a ‘starvation diet’…. [I]n the 1970s and 1980s [anorexia] … became a vernacular, an everyday word, an idiom. Patrick Anderson, So Much Wasted (2010, 32) The words come out of yr mouth but yr eyes say other things, ‘Help me, please, I’m lost in my own passive resistance, something went wrong’…. Did anyone ever ask you that question—what’s it like being a girl in music? Kim Gordon, ‘Open letter to Karen’ (n.d.) This article discusses an extraordinary body (Thomson 1997) in popular music, that belonging to the person with anorexia which is also usually a gendered body—female—and that of the singer or frontperson. I explore the relation between the anorexic body and popular music, which is more than simply looking at constructions of anorexia in pop. It involves contextually thinking about the (medical) history and the critical reception and representation, the place of anorexia across the creative industries more widely, and a particular moment when pop played a role in the public awareness of anorexia. Following such context I will look in more detail at a small number of popular music artists who had experience of anorexia, their stage and media presentations (of it), and how they did or apparently did not explore their experience of it in their own work and public appearances. -
Senior Living Page 9
Senior Living Page 9 A new maple tree is planted at the Old Forestville School- house where the two white oaks previously stood. Classifieds, Page 10 Classifieds, v Planting for Opinion, Page 4 What Are The Future You Grateful for in 2020? News, Page 8 Viewpoints, Page 4 Requested in home 11-26-20 home in Requested Time sensitive material. material. sensitive Time Attention Postmaster: Postmaster: Attention ECR WSS ECR Communities Customer Postal permit #322 permit Easton, MD Easton, Discuss ‘495 NEXT’ PAID U.S. Postage U.S. News, Page 3 STD PRSRT Photo contributed Photo November 25 - December 1, 2020 online at www.connectionnewspapers.com 2 v Great Falls Connection v November 25 - December 1, 2020 www.ConnectionNewspapers.com News Express Lanes May Link to American Legion Memorial Bridge By Mike Salmon Accord to create a new, unified Capital Beltway, The Connection replace the aging American Legion Bridge and re- lieve congestion at one of the country’s worst traffic ust when it seemed like the interstate net- chokepoints, according to the VDOT website. work in Northern Virginia was completely In the road building process, the plans are pre- outfitted with the toll lane options, trans- sented to the public and meetings are held to gather Jportation officials have etched out anoth- feedback. One such meeting was recently held on er project to stretch the 495 Express Lanes to the Nov. 18, via a VDOT live feed, and it was attended American Legion Memorial Bridge on the northern by VDOT engineers, elected officials and residents side of the Capital Beltway. -
Rotary Club of Buffalo VOL
Rotary Club of Buffalo VOL. 143 , NO. 14 www.buffalonyrotary.org January 25, 2017 Thursday, January 26, 2017 12:15 Thursday, Feb 2, 2017 5:30-8:00 PM Templeton Landing ENCHANTED EVENING UKRAINIAN CENTER SPEAKER: GARY WILLOUGHBY 562 Genesee St., Buffalo 14204 SUBJECT: SPCA OF ERIE COUNTY Gary Willoughby serves as the President and CEO Enchanted Evening of the SPCA Serving Erie County, leading a team of Ukrainian Center 120 employees and over 1,700 volunteers. Gary 562 Genesee St., Buffalo 1420 joined the SPCA last year after leading animal wel- Time: 5:30-8:30 PM fare organizations previously in Toledo, Ohio and Food: Authentic Ukrainian Beer & Wine included (cash bar for Aiken, SC and volunteering and serving as a board member for animal hard liquor). welfare organizations in Florida. Parking is in the lot on the right-hand Gary was born in Ypsilanti, Michigan, but lived in Florida for most of side of the club and the entrance will be clearly marked his life. His undergrad degree was in journalism and communications There will be tours of the building and a brief talk about the history of from the University of Mobile in Alabama. He earned a certificate in the club. non profit management from the University of Wisconsin-Milwaukee, as well as a graduate certificate in Gerontology and a Master’s in Pub- Entertainment will be provided by a Ukrainian member of the club lic Administration from Florida Gulf Coast University. DNIPRO building at 562 Genesee Street in Buffalo, New York, was built in 1914, and purchased by the Ukrainian American community in 1955. -
AC Newsletter AUG 2014 Email
Na Leo O Na Koa (Voices of Warriors) 2007 Chapter Rating Newsletter of the Aloha Chapter, An Affiliate of the Military Officers Association of America Chartered January 27, 2000 Volume No. 15, Issue No. 8 Web Site: http://www.aloha-moaa.org August 2014 Tour of FAA Tower at HNL vices 15 civilian and 4 military airports. There- after, we were split into four groups of ap- On Wednesday, 23 July 2014, 46 Aloha and proximately eleven persons and went on a Hawaii Chapter members and guests travelled to physical tour of the various area of operations. the far end of Hickam Air Force Base, JBPHH, to visit the FAA Honolulu Air Traffic Control Contrary to what some might think, there Facility. We were treated to a most informative were different procedures and terms used to and fascinating tour of all phases of air traffic control air traffic in the various geographical control in and around the State of Hawaii. belts around Hawaii. We got to go into the darkened main operation control room to hear Security to the facility was tight. We had to and see how traffic instructions were given by park our cars outside the gate, be cleared indi- the air traffic controllers to airplanes up to vidually, go thru a scanning procedure like is some 30 miles enroute to or from Hawaii. done by TSA at the airport, and then be es- Then we saw the handoff of air traffic to the corted into the building. Once inside we were Honolulu Tricon that sequenced traffic to 5 briefed by Michael Schmidt, the District Facil- miles of an airport. -
Oracle (Mar 16, 1973)
Oral Roberts University Digital Showcase Oracle: ORU Student Newspaper Oral Roberts University Collection 3-16-1973 Oracle (Mar 16, 1973) Holy Spirit Research Center ORU Library Follow this and additional works at: https://digitalshowcase.oru.edu/oracle Part of the Christian Denominations and Sects Commons, Christianity Commons, and the Higher Education Commons rhe VOLUME 8, NUMBER I9 ORAL ROBERTS UNIVERSITY, TULSA, OKLAHOMA MARCH 16, 1973 Titqns fqce form¡dqble foe North Cqrolinq qt tourney For the second consecutive as formidable a foe as ORU has pull out all the stops for this year, the ORU Titans have been faced all year. The Tar Heels year's tournament by not only invited to participate in the Na- are entering th€ tournament as sending the cheerleading squad tional Invitation Tournament at Atlantic Coast Conference run- but also the 37-member Titan Madison Square Garden in New ner-ups because they suffered a Pep Band directed by Bill Shel- York. The Titans' first-round op- 54-52 upset loss at the ha¡ds of lenbarger. ponent tomorrow night will be Wake Forest in the conference "The band has worked hard the 1lth-ranked Tar Heels of playoffs. UNC sports a 22-7 rec- and they're excited about this North Carolina. ord but five of the losses were trip," said Shellenbarger. One The expected phone call came picked up in conference play, unidentified ace trombone play- 2 weeks ago after the Titans which indicates the ferocity of er summed up the feeling of the were snubbed by the NCAA Se- competition in the ACC. -
Clinical Documentation Nurse Interview Questions
Clinical Documentation Nurse Interview Questions Mohamad remains incisive after Hirsch revere despairingly or wastings any oenology. Discreditable and ifcryptocrystalline shakeable Osmond Fonzie nibbles often orhaves eunuchise. some millwright afield or caucuses afoot. Percival babbitt factually Documentation is a critical component of patient guy and narrative nurse's notes provide all. Practice 25 Clinical Nurse Specialist Interview Questions with professional interview. Development and evaluation of nursing user interface screens. Regardless of you plan educational activities that you have any interview as part where he uses a psychological evaluation of hipaa, for nurse in a patient? Interview questions ACDIS Forums. A qualitative approach was used by using questionnaires and interviewing. Colorectal Clinical Nurse Specialist Interview Questions. Learn add to Answer Nursing Interview Questions About Handling Stress. 5 Common Ambulatory Nurse Interview Questions & Answers. Hiring a CDI Specialist 3 Tips You lift to Know. Conclusion Improving nursing documentation involved complex challenges in this setting and demanded multiple approaches. The Five Hallmarks of Best-in-Class Clinical Documentation. As an RN clinical documentation improvement specialist CDIS you could be. Top hard skills interview questions for nurse practitioners. Managing Consultant Clinical Documentation Integrity. The Patient Interview. It most appropriate parties are attending a difference between this way with? Improves from six months, but this question into one that resigning from a bedside nursing it is then serve as described as it. Evaluating the Barriers to Point-of-Care Documentation for. The available to writing effective narrative nursing notes is mostly be concise in the facts while. Any other program, may be transmitted in its mission in a signed by following guidance in accordance with a level. -
Job Site Visit the Gateway Center Arena-College Park Sponsored by Choate Construction
GEORGIA CHAPTER-General Membership Job Site Visit The Gateway Center Arena-College Park Sponsored by Choate Construction Join us for a special visit to the Gateway Center Arena in College Park Georgia. The new arena will be the future home of the College Park Skyhawks, an NBA G-league team, and will have GA Chapter Web 3,500 seats for basketball and up to 5,000 for concerts. Site This 91,990-SF multi-purpose facility is next to the Georgia CFMA‐GEORGIA CHAPTER International Convention Center and will include the ATLSkytrain, 3227 S. Cherokee Lane a free rail connecting the Gateway Center and car rental facility Suite 1320 Woodstock GA 30188 to Hartsfield-Jackson International Airport. FISCAL 2020 This is a new state-of-the-art venue for Atlanta. Join us for a PRESIDENT David Massey, CCIFP short presentation on the project followed by a physical tour of the facility. Hard hats will be provided, and you must wear VICE‐PRESIDENT Josh Roper closed -toe hard sole shoes while on-site. NOTE: Tour is on Wednesday 5/15/19 TREASURER Vicki Mitchell, CCIFP (Not our normal meeting day/date) SECRETARY Sign up today! Mike Downs When: WEDNESDAY May 15,2019 BOARD OF DIRECTORS Leslie A. Callender, CCIFP Registration 10:45 AM Andrea Castle, CCIFP Lunch: Chick-fil-A box lunch Sam Clark Program: Promptly at 11:00 AM Benjamin Dover Gateway Center Arena Reuben A. Jefferson Where: Dana S. Johns 2330 Convention Center Concourse College Park, Georgia 30331 Mike Kiblinger, CCIFP Cost: By May 13th - $10.00 for Box Lunch Kevin King Millicent Kundrat ~You must register and pay online~ Scott Oberschlake, CCIFP Antony L. -
Wolf Alice at Newcastle's 02 Academy!
WWW.NEVOLUME.CO.UK AT NEWCASTLE’S WOLF ALICE 02 ACADEMY! WE’RE LISTENING! AUTOBAHN AT KU BAR! LUMIERE FESTIVAL DURHAM! ISSUE #28 NOV 2017 WE INTERVIEW CHRIS JERICHO! POST-MORTEM OF SPARKS IN NEWCASTLE! FOLLOW NE VOLUME ON SOCIAL ANDREW JOHNSON’S LATEST EP! ARTIST SPOTLIGHT - THE SKAPONES! MEDIA SONGS FROM NORTHERN BRITAIN AT THE GEORGIAN THEATRE! PICK UP OUR FREE NORTH EAST MUSIC/CULTURE MAGAZINE! LET’S GET EVEN LOUDER NORTH EAST VOLUME!!!!! NEWS! FEATURES! WELCOME! Thank you so much for picking up PG.5 Gig Preview: PG.23 Business Spotlight: KU Bar, The Selecter/The Beat Stockton! NE Volume magazine - the magazine at 02 Academy, Newcastle! produced by local music and culture fans, PG.24 Songs From Northern Britain! for local music and culture fans. PG.6 Gig Preview: So I had a little think in October about Autobahn at KU Bar, Stockton! PG.25 Byker Grave Festival! how I can further help local bands/ artistes and businesses and I’ve decided PG.7 Gig Preview: INTERVIEWS! that, from around January, I’ll be setting Blackbeard’s Teaparty at The Hut, up an NE Volume podcast whereby I’ll be Goathland! PG.26 Milburn! speaking with those involved in the local PG.27 Wishbone Ash! music scene on a weekly basis (with the PG.10 Gig Preview: interview aired online and posted in this The Cravats at Westgarth Social PG.28 Wolf Alice! magazine). If you’d be interested in joining Club, Middlesbrough! PG.30 The Darkness! me at the NE Volume office for a little chat please email me at info@nevolume. -
Docent's Program
The Florida State University Coastal & Marine Laboratory Docent’s Program: Instructional Material 3618 Coastal Highway 98 St. Teresa, FL 32358-2702 | 850-697-4120 | marinelab.fsu. edu 1 Table of Contents Introduction .................................................................................................................................................. 2 Popular Highlights Tours ........................................................................................................................... 2 Educational, Community, and Special Interest Group Tours .................................................................... 2 Off-site Outreach Programs ...................................................................................................................... 2 Docent Philosophy and Technique ............................................................................................................... 3 Docent Mission Statement ....................................................................................................................... 3 Standards for FSUCML Docents ................................................................................................................ 3 Policies of Docent Program ....................................................................................................................... 4 Tour Procedures ........................................................................................................................................ 4 Tour Tips - A docent has the