Review on Defects in Hot Forging Process- Investigation
Total Page:16
File Type:pdf, Size:1020Kb
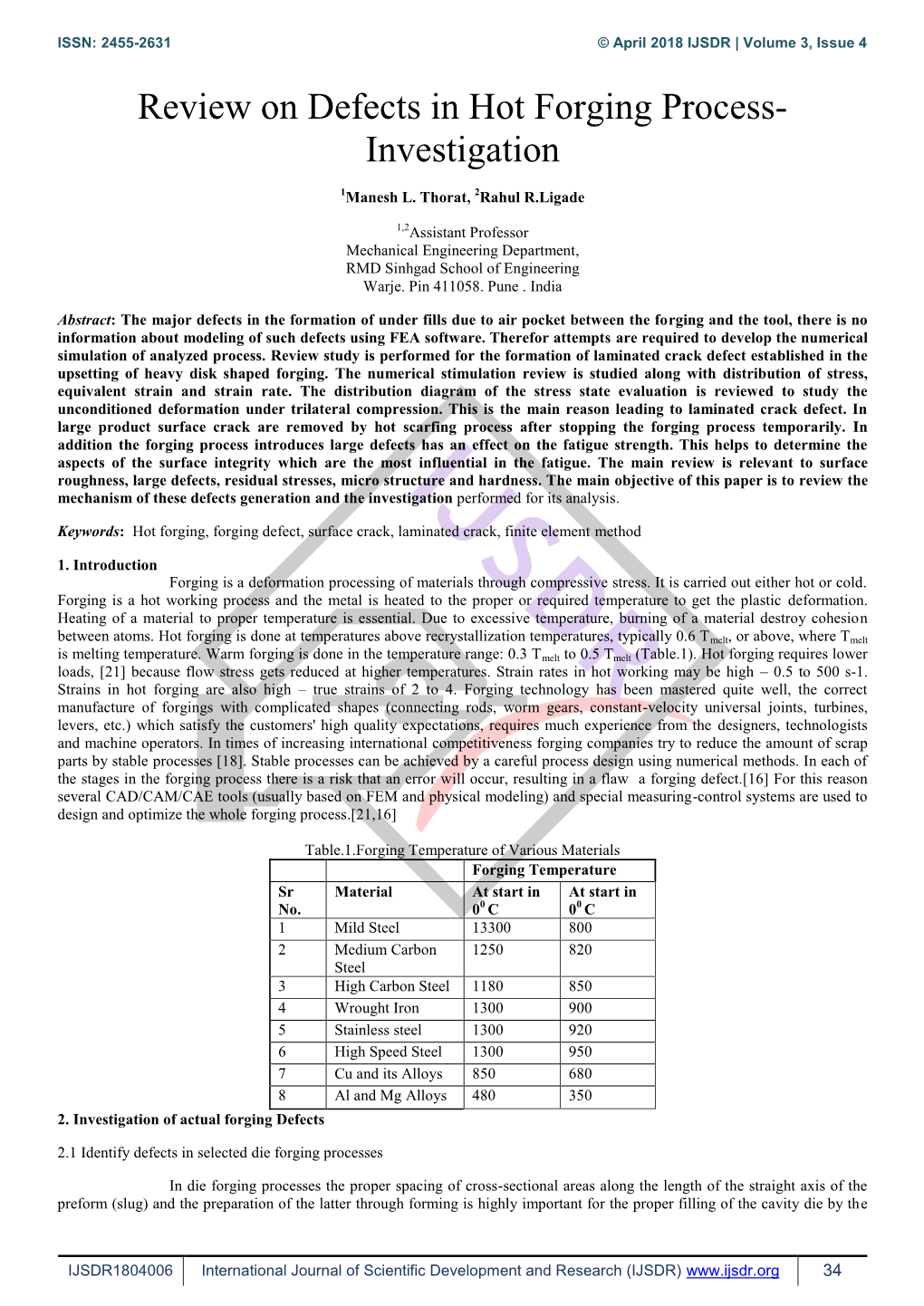
Load more
Recommended publications
-
January 2016“Azbil”
2016 Vol.1 azbil Group PR magazine Moving Ahead To Expand Business Overseas Amari Watergate Bangkok Focusing on Safe, Reliable, Proven, and Durable Technologies - Special Feature Cognicise the aging of population is accelerating. The most advanced medical care and Particularly important is to gain A coined term combining "cognition" and "exercise." This exercise program is designed to simulate the brain function by promoting thinking while exercising. Needless to say, healthy understanding of the aging process. lifestyle with proper daily diet, ample sleep, and adequate exercise is also very important. research taking on the challenge of Spearheading those efforts is the National Institute for Longevity Sciences-Longitudi- Stamping Multi-stepping ever-increasing dementia nal Study of Aging (NILS-LSA) conducted by NCGG. The main objectives of NILS-LSA are to The discover the causes of aging and genera- Estimated number of people number of dementia patients tion of geriatric diseases such as demen- with dementia in Japan is forecast to exceed seven tia, osteoporosis, and presbycusis and to ? million in 2025. This means one out of every develop methods to prevent them. To five people aged 65 and over will suffer from those ends, not only medical profession- dementia. The National Center for Geriatrics and 1 Stamp rhythmically. 1 Stamp by moving the stamping foot in the als but also specialists in a broad range following order: right foot forward, left foot Gerontology (NCGG) is a leader in the research and ? of fields including psychology, kinematics, 2 Clap hands once forward, right foot to right, and left foot to left. treatment of dementia in Japan. -
Forging Casting Metal-Cutting Machines the Lathe
ГБПОУ КК НКРП Forging Основные процессы литейного производства, изготовление отливок; важность процесса ковки. Основные операции, выполняемые на металлорежущих станках Casting Основы технологии резания металлов Metal-Cutting Machines The Lathe УЧЕБНОЕ ПОСОБИЕ по дисциплине «Иностранный язык» (английский язык) для студентов 4 курса специальности 220703 Автоматизация технологических процессов и производств НОВОРОССИЙСК, 2015 ~ 1 ~ МИНИСТЕРСТВО ОБРАЗОВАНИЯ И НАУКИ КРАСНОДАРСКОГО КРАЯ ГОСУДАРСТВЕННОЕ БЮДЖЕТНОЕ ПРОФЕССИОНАЛЬНОЕ ОБРАЗОВАТЕЛЬНОЕ УЧРЕЖДЕНИЕ КРАСНОДАРСКОГО КРАЯ «НОВОРОССИЙСКИЙ КОЛЛЕДЖ РАДИОЭЛЕКТРОННОГО ПРИБОРОСТРОЕНИЯ» Учебное пособие по дисциплине «Иностранный язык» (английский) по теме «Основы технологических процессов: основные процессы литейного производства, изготовление отливок; важность процесса ковки. Основные операции, выполняемые на металлорежущих станках. Основы технологии резания металлов» для студентов 4 курса специальности 220703 Автоматизация технологических процессов и производств Н о в о р о с с и й с к 2 0 15 ~ 2 ~ ~ 3 ~ ~ 4 ~ ~ 5 ~ ~ 6 ~ ОГЛАВЛЕНИЕ Стр. ВВЕДЕНИЕ 8 UNIT 1 CASTING 9 THEORY - PRACTICAL TASKS 16 UNIT 2 FORGING 24 THEORY - PRACTICAL TASKS 32 UNIT 3 METAL-CUTTING MACHINES 35 THEORY - PRACTICAL TASKS 38 СПИСОК ЛИТЕРАТУРЫ 43 ~ 7 ~ ВВЕДЕНИЕ Данное учебное пособие «Основы технологических процессов: основные процессы литейного производства, изготовление отливок; важность процесса ковки. Основные операции, выполняемые на металлорежущих станках. Основы технологии резания металлов» предназначено для базового -
Unit 22: Fabrication Processes and Technology
Unit 22: Fabrication Processes and Technology Unit code: L/600/0273 QCF Level 3: BTEC Nationals Credit value: 10 Guided learning hours: 60 Aim and purpose This unit aims to give learners a knowledge of the processes used to safely measure, mark out, cut, form and assemble fabricated structures using sheet metal. Unit introduction Fabrication processes and technology are used in the production of metal structures in a wide range of manufacturing industries. The fabrication of metal structures involves four essential stages: measuring and marking out, preparation of the material for fabrication, forming processes and the assembly of the materials. This unit gives learners with no previous fabrication experience an understanding of the processes and technologies used throughout the fabrication industry, whilst learning to work in a safe environment. The unit is appropriate for work-based learners or for those who are being prepared for employment in an industrial environment where fabrication is an integral part of the manufacturing process. Learners will work with ferrous or non-ferrous metals in the form of sheet, plate and sectional materials to construct a fabricated structure. They will learn how to use a range of industrial hand tools and machinery to complete fabrication tasks. The unit will give learners the ability to identify the correct processes and equipment to use, and the tools and equipment appropriate to each stage of the fabrication process. Learning outcomes On completion of this unit a learner should: 1 Know about health and safety legislation, regulations and safe working practices in the fabrication industry 2 Know the processes used to mark out and prepare materials to produce fabricated structures 3 Know how materials are formed and assembled to produce fabricated structures 4 Be able to interpret the specification of a fabricated structure and plan and carry out its manufacture. -
A Novel NDT Method for Measuring Thickness of Brush-Electroplated
17th World Conference on Nondestructive Testing, 25-28 Oct 2008, Shanghai, China A Novel NDT Method for Measuring Thickness of Brush-Electroplated Nickel Coating on Ferrous Metal Sueface Shiyun DONG 1, * , Binshi XU 1 , Junming LIN 2 1 National Key Laboratory for Remanufacturing, Beijing 100072, China 2 Eddysun (Xiamen) Electronic Co., LTD., Xiamen, Fujian, 361004, China * Tel: +86-10-66718541, Email: [email protected] Abstract Brush-electroplated nickel coating has been widely applied to repair and remanufacture ferrous metal component. Generally, the nickel coating has thickness from 0.05 mm to 0.2 mm, and it is also ferromagnetic like iorn metals. Therefore, the traditional supersonic thickness tester and eddy current thickness tester are not competent to measure the nickel coating thickness on iron or steel metal surface, and the brush-electropalted nickel coatings are still lack of NDT method to measure its thickness. In this paper, a novel NDT method for the brush-electroplated nickel coating thickness measuring was investigated on eddy current mechanism. A series of brush-electroplated nickel coatings with various thickness were prepared on SUS1045 steel, whose thickness was confirmed on cross-section with SEM or optical microscope. Then Eddy signals of the coatings was tested, and a fitted relationship between the eddy signal phase and the thickness was found for the nickel coatings. Based on this results, a novel NDT method to measure the nickel coating thickness was set up, which could give precise resuts and be operated simply. Therefore, the method shows wide application in engineering. Key words :eddy current, brush-electroplated nickel coating, coating thickness, NDT 1. -
UNIT 3 PRESS and PRESS TOOLS Press and Press Tools
UNIT 3 PRESS AND PRESS TOOLS Press and Press Tools Structure 3.1 Introduction Objectives 3.2 Press 3.3 Types of Presses 3.4 Main Parts of Typical Power Press 3.5 Specifications of a Press 3.6 Press Tool 3.7 Die Set and its Details 3.8 Methods of Die Supporting 3.9 Classification of Dies 3.10 Important Consideration for Design of a Die Set 3.11 Summary 3.12 Answers to SAQs 3.1 INTRODUCTION Metal forming is one of the manufacturing processes which are almost chipless. These operations are mainly carried out by the help of presses and press tools. These operations include deformation of metal work pieces to the desired size and size by applying pressure or force. Presses and press tools facilitate mass production work. These are considered fastest and most efficient way to form a sheet metal into finished products. Objectives After studying this unit, you should be able to understand introduction of press tool, major components of press working system, different criteria of classification of presses, different types of presses, description of important parts of a press, specifications of a press, other press working tools, like punch and die, components of press working system, different types of die sets, and design considerations for die set design. 3.2 PRESS A press is a sheet metal working tool with a stationary bed and a powered ram can be driven towards the bed or away from the bed to apply force or required pressure for various metal forming operations. A line diagram of a typical pres is explained in the Figure 2.1 hydraulic system. -
Design of Special Purpose Hydraulic Press Machine
Vol-4 Issue-3 2018 IJARIIE-ISSN(O)-2395-4396 DESIGN OF SPECIAL PURPOSE HYDRAULIC PRESS MACHINE Joshi Ameya1, Kamble Sanket2, Parvatikar Darshan3 1Student, Mechanical Engineering, LGNS College Of Engg, Maharashtra, India 2Student, Mechanical Engineering, LGNS College Of Engg, Maharashtra, India 3Student, Mechanical Engineering, LGNS College Of Engg, Maharashtra, India ABSTRACT A hydraulic press is a device using a hydraulic cylinder to generate a compressive force. Hydraulic presses are commonly used for forging, clinching, molding, blanking, punching, deep drawing, and metal forming operations. A special purpose hydraulic press is suggested for press fitting two child parts of muffler used in silencers of automobile and marine industry. After observing the drawbacks in manual process of press fitting, hydraulic press needs to be designed. Thus the project is to design, analysis and fabrication of special purpose hydraulic press machine of required tonnage. Keywords- Hydraulic press, special purpose machine, press fitting, muffler, silencer 1. INTROCUCTION A muffler is a device for decreasing the amount of noise emitted by the exhaust of an internal combustion engine. Mufflers are installed within the exhaust system of most internal combustion engines, although the muffler is not designed to serve any primary exhaust function. The muffler is engineered as an acoustic soundproofing device designed to reduce the loudness of the sound pressure created by the engine by way of acoustic quieting. The majority of the sound pressure produced by the engine is emanated out of the vehicle via the same piping used by the silent exhaust gases. The emitted noise is abated by a series of passages and chambers lined with insulation and/or resonating chambers harmonically tuned to cause destructive interference, wherein opposite sound waves cancel each other out. -
Steel Characteristics and Their Link to Chip Breaking and Tool Wear in Metal Cutting
Steel characteristics and their link to chip breaking and tool wear in metal cutting Niclas Ånmark Doctoral Thesis in Materials Science and Engineering Stockholm 2016 i Akademisk avhandling som med tillstånd av Kungliga Tekniska Högskolan i Stockholm, framlägges för offentlig granskning för avläggande av teknologie doktorsexamen, onsdagen den 8 juni 2016, kl. 10.00 i hörsal B3, Brinellvägen 23, Kungliga Tekniska Högskolan, Stockholm KTH Royal Institute of Technology School of Industrial Engineering and Management Department of Materials Science and Engineering Division of Applied Process Metallurgy SE-100 44 Stockholm, Sweden ISBN 978-91-7595-949-8 Cover: Reprinted with permission of Sandvik Coromant Copyright © Niclas Ånmark, 2016 This thesis is available in electronic version at kth.diva-portal.org Printed by US-AB, Stockholm, Sweden ii Abstract The vision of this thesis is to study how it is possible to obtain optimised workpieces during metal cutting processes in industry. Specifically, the work is aimed to increase the understanding between the steel characteristics and their link to the chip breaking and tool wear during metal cutting. The emphasis is on the influence of the cleanliness and the characteristics of non-metallic inclusions in the workpiece on the machinability of carburising steel grades. The machinability of a case hardening steel is improved by a M-treatment (additions of Ca). Also, the improved machinability of the M-steels offers an attractive potential to save money which makes it possible to reduce the tooling costs with up to 50%. The improved machinability of Ca-treated steels is correlated to the formation of lubricating slag layers consisting of Ca-enriched sulfide inclusions and oxy-sulfide inclusions, which are formed on the rake face during the machining operation. -
Investigation of Rheo-Diecasting Mold Filling of Semi-Solid A380 Aluminum Alloy Slurry
International Journal of Minerals, Metallurgy and Materials Volume 24, Number 6, June 2017, Page 691 DOI: 10.1007/s12613-017-1452-z Investigation of rheo-diecasting mold filling of semi-solid A380 aluminum alloy slurry Zhi-yong Liu1), Wei-min Mao2), Wei-pan Wang3), Zhi-kai Zheng2), and Rui Yue4) 1) School of Materials Science and Engineering, Tsinghua University, Beijing 100084, China 2) School of Materials Science and Engineering, University of Science and Technology Beijing, Beijing 100083, China 3) Beijing Nanshan Institute of Aeronautical Materials, Beijing 100048, China 4) National Engineering Research Center of Light Alloy Net Forming, Shanghai Jiao Tong University, Shanghai 200240, China (Received: 30 August 2016; revised: 9 January 2017; accepted: 12 January 2017) Abstract: The rheo-diecasting mold filling capacity and the microstructure of the semi-solid A380 aluminum alloy slurry were investigated. The results show that the mold filling capacity was strengthened with increasing pouring temperature or increasing injection pressure. Under certain process parameters, the mold cavity was fully filled. However, the mold filling capacity decreased with increasing holding time. The mold filling capacity was improved with increasing shape factor of primary α(Al) grains; however, the solid fraction and the grain size sig- nificantly increased at the same time. In addition, the microstructures along the route of the spiral samples obviously differed. The grain size decreased gradually from the near-end to the far-end, whereas the shape factor increased gradually. Keywords: aluminum alloys; semi-solid slurry; rheo-diecasting; mold filling; microstructure 1. Introduction increasing the size of the inner gate facilitates mold fill- ing [11]. -
Status Quo and Development Trend of Lost Foam Casting Technology
Special Report Celebrating the th Anniversray 2004-2014 CHINA FOUNDRY Vol.11 No.4 July 2014 10 Status quo and development trend of lost foam casting technology *Fan Zitian1, Jiang Wenming1,2, Liu Fuchu1, and Xiao Botao1 1. State Key Laboratory of Material Processing and Die & Mould Technology, Huazhong University of Science and Technology, Wuhan 430074, China; 2. School of Mechanical & Electrical Engineering, Wuhan Institute of Technology, Wuhan 430073, China Abstract: Lost foam casting (LFC) technology has been widely applied to cast iron and cast steel. However, the development of LFC for Al and Mg alloys was relatively slower than that for cast iron and cast steel. The application of LFC to Al and Mg alloys needs more effort, especially in China. In this paper, the development history of LFC is reviewed, and the application situations of LFC to Al and Mg alloys are mainly discussed. Meanwhile, the key problems of LFC for Al and Mg alloys are also pointed out. Finally, the prospects for LFC technology are discussed, and some special new LFC technologies are introduced for casting Al and Mg alloys. In future, the development trends of green LFC technology mainly focus on the special new LFC methods, metal material, coating, heat treatment, new foam materials as well as purification technology of tail gas, etc. Key words: lost foam casting (LFC); technology actuality; development trend; aluminum alloy; magnesium alloy CLC numbers: TG249.5 *Fan Zitian Document code: A Born in 1962 Ph.D, Professor. Article ID: 1672-6421(2014)04-296-12 He has been mainly concentrating on education, research and application of casting materials; process theory and equipment. -
Metalworking Dust Collection Stand Model JDCS-505
Operating Instructions and Parts Manual Metalworking Dust Collection Stand Model JDCS-505 JET 427 New Sanford Road LaVergne, Tennessee 37086 Part No. M-414800 Ph.: 800-274-6848 Edition 7 12/2020 www.jettools.com Copyright © 2016 JET 13. Remove adjusting keys and wrenches. Form a habit of checking to see that keys and adjusting wrenches are removed from the machine before turning it on. 14. Keep safety guards in place at all times when 1.0 IMPORTANT SAFETY the machine is in use. If removed for INSTRUCTIONS maintenance purposes, use extreme caution and replace the guards immediately after When using an electrical appliance, basic maintenance is complete. precautions should always be followed, including the following: 15. Check damaged parts. Before further use of the machine, a guard or other part that is damaged READ ALL INSTRUCTIONS BEFORE USING THIS should be carefully checked to determine that it DUST COLLECTOR. will operate properly and perform its intended function. Check for alignment of moving parts, WARNING – To reduce the risk of fire, binding of moving parts, breakage of parts, electric shock, or injury: mounting and any other conditions that may affect its operation. A guard or other part that is 1. Read and understand entire owner’s manual damaged should be properly repaired or before attempting assembly or operation of this replaced. dust collector. 16. Provide for adequate space surrounding work 2. Read and understand the warnings posted on area and non-glare, overhead lighting. the machine and in this manual. 17. Keep the floor around the machine clean and 3. -
Operation and Maintenance Manual for the Pemserter 3000™ Fastener Installation Press Operation and Maintenance Manual
OPERATION AND MAINTENANCE MANUAL FOR THE PEMSERTER 3000™ FASTENER INSTALLATION PRESS OPERATION AND MAINTENANCE MANUAL PEMSERTER 3000 ™ PRESS MODEL FASTENER INSTALLATION PRESS SERIAL NUMBER _____________ ® PennEngineering 5190 Old Easton Road DANBORO, PENNSYLVANIA 18916 1-800-523-5321 • 1-215-766-8853 Document Part Number 8019287 Rev. B Revision Dec, 2015 Copyright 2015 by PennEngineering ®, Inc. All rights reserved. No part of this documentation may be reproduced, copied or transmitted in any form, or by any electronic, digital or other means, without permission in writing from PennEngineering ®, Inc. (referred to herein as the “Company”). This includes photocopying and information storage and retrieval systems. The material in this documentation is subject to change without notice. PLEASE READ THESE TERMS AND CONDITIONS CAREFULLY BEFORE USING THE SOFTWARE INCLUDED WITH THE EQUIPMENT. BY USING THE SOFTWARE ACCOMPANYING THE EQUIPMENT YOU AGREE TO BE BOUND BY THE TERMS AND CONDITIONS OF THIS LICENSE. All software furnished with the equipment is on a licensed basis. The Company grants to the user a non-transferable and non-exclusive license to use such software in object code only and solely in connection with the use of the equipment. Such license may not be assigned, sublicensed, or otherwise transferred by the user apart from the equipment. No right to copy a licensed program in whole or in part is granted. Title to the software and documentation shall remain with the Company. The user shall not modify, merge, or incorporate any form or portion of a licensed program with other program material, create a derivative work from a licensed program, or use a licensed program in a network. -
Strada Ep Electronically Controlled Gear Pumps Provide Precise, Direct Pressure Control
manual strada ep Electronically controlled gear pumps provide precise, direct pressure control. Motor speed control with La Marzocco‘s classic paddle interface. Absolute and direct control of pressure at any point during the extraction. Manuallt operated by the Barista. Record feature to program and reproduce pressure profiles. strada ep Operating Manual V2.1 - 11/2014 Chapters 1. General Warnings and Safety Specifications page 3 La Marzocco S.r.l. 2. Definition of Available Models page 5 Via La Torre 14/H Località La Torre 3. Installation page 8 50038 Scarperia e San Piero (Firenze) - ITALIA 4. Machine Operation and Coffee Preparation page 15 www.lamarzocco.com [email protected] 5. Dispensing Steam and Hot Water page 18 T: +39 055 849 191 6. Maintenance and Periodic Cleaning Operations page 19 F: +39 055 849 1990 7. De-commissioning and Demolition page 21 8. Mandatory Maintenance and Check-up Operations page 22 9. Software Programming Guide page 23 certifications available: EN 1. General Warnings and Safety Specifications WARNING 4) Packaging (boxes, plastic bags, foam 9) Furthermore, you must ensure that THIS MACHINE IS FOR PROFESSIONAL parts and whatever else) must not be left the capacity of the available electrical USE ONLY AND SHOULD BE INSTALLED around within easy reach of children, due system is suitable for the maximum power IN LOCATIONS WHERE ITS USE AND MAINTENANCE IS RESTRICED to the potential danger it represents, nor consumption indicated on the espresso TO TRAINED PERSONNEL. be discarded in the environment. machine. CHILDREN ARE FORBIDDEN TO OPERATE OR 5) Check to see that data on the rating plate 10) We do not recommend using adapters, PLAY WITH THE MACHINE.