University of Cincinnati
Total Page:16
File Type:pdf, Size:1020Kb
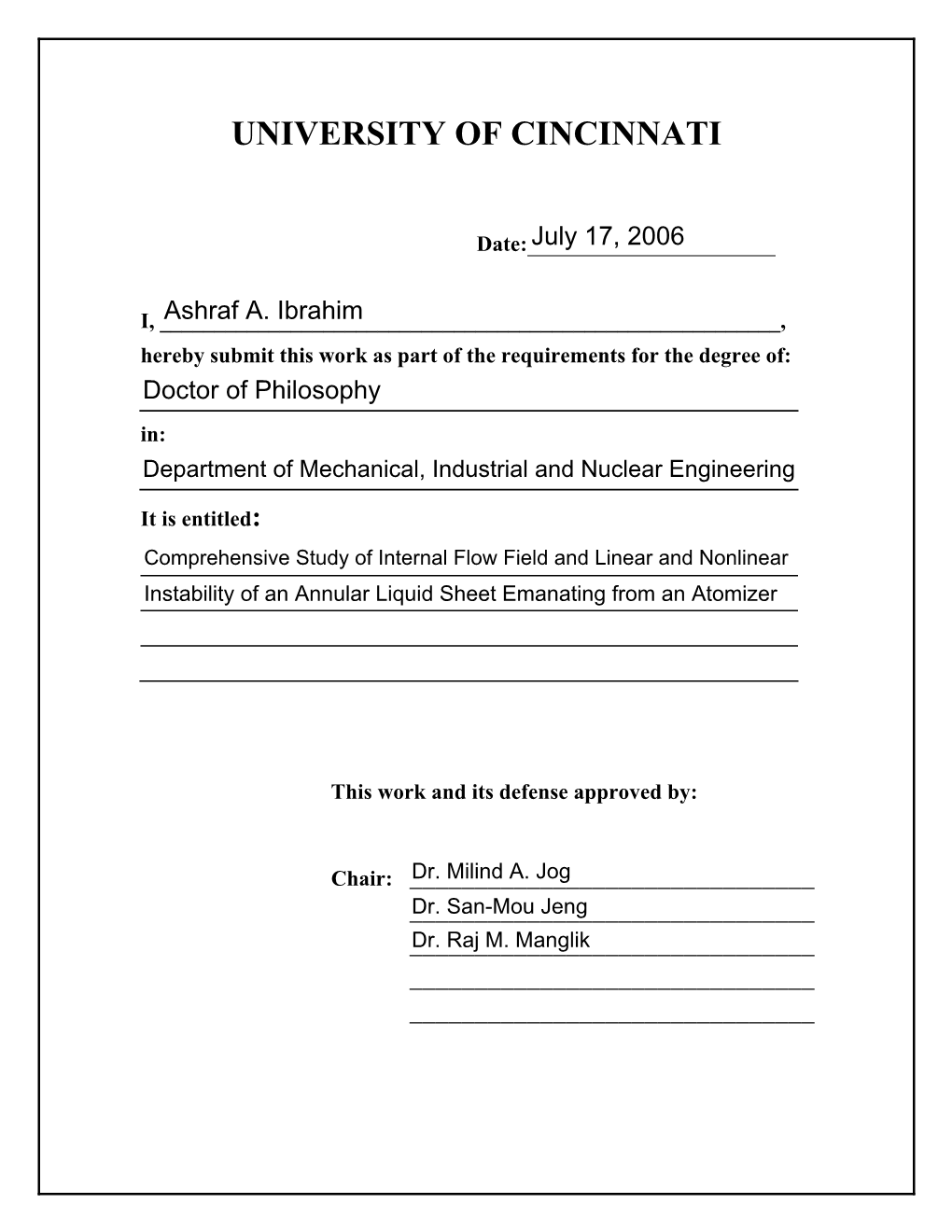
Load more
Recommended publications
-
Atomization of Viscous Fluids Using Counterflow Nozzle
Atomization of Viscous Fluids using Counterflow Nozzle A THESIS SUBMITTED TO THE FACULTY OF THE GRADUATE SCHOOL OF THE UNIVERSITY OF MINNESOTA BY Roshan Rangarajan IN PARTIAL FULFILLMENT OF THE REQUIREMENTS FOR THE DEGREE OF MASTER OF SCIENCE Prof.Vinod Srinivasan August, 2020 c Roshan Rangarajan 2020 ALL RIGHTS RESERVED Acknowledgements I would like to express my sincere gratitude to my academic advisor, Prof.V.Srinivasan for his continuous support throughout this pursuit. His consistent motivation guided me during the course of this rigorous experimental effort. He helped instill a deep sense of work ethic and discipline towards academic research. In addition, I would like to thank Prof.Strykowski (ME Dept, University of Minnesota- Twin Cities) and Prof.Hoxie (ME Dept, University of Minnesota-Duluth) for their en- gaging technical insights into my present work. In particular, I was able to develop a sound understanding of techniques used in Image processing through my interactions with Eric and Prof.Hoxie at UMN-Duluth. I would like to thank my fellow lab mates Akash, Ian, Chinmayi, Manish, Sankar, Ankit, Peter and Amber for simulating discussions and sleepless nights before important deadlines. Research becomes not just interesting but also fun when you have the right minds around. Besides my advisor, I would like to thank Prof.Hogan and Prof.Ramaswamy for their time and encouragement in this work. i Dedication Parents and my sister for always believing in me. ii Abstract In the present work, we study the enhanced atomization of viscous liquids by using a novel twin-fluid atomizer. A two-phase mixing region is developed within the nozzle us- ing counterflow configuration by supplying air and liquid streams in opposite directions. -
Laboratory Experiments on Rain-Driven Convection: Implications for Planetary Dynamos Peter Olson, Maylis Landeau, Benjamin Hirsh
Laboratory experiments on rain-driven convection: Implications for planetary dynamos Peter Olson, Maylis Landeau, Benjamin Hirsh To cite this version: Peter Olson, Maylis Landeau, Benjamin Hirsh. Laboratory experiments on rain-driven convection: Implications for planetary dynamos. Earth and Planetary Science Letters, Elsevier, 2017, 457, pp.403- 411. 10.1016/j.epsl.2016.10.015. hal-03271246 HAL Id: hal-03271246 https://hal.archives-ouvertes.fr/hal-03271246 Submitted on 25 Jun 2021 HAL is a multi-disciplinary open access L’archive ouverte pluridisciplinaire HAL, est archive for the deposit and dissemination of sci- destinée au dépôt et à la diffusion de documents entific research documents, whether they are pub- scientifiques de niveau recherche, publiés ou non, lished or not. The documents may come from émanant des établissements d’enseignement et de teaching and research institutions in France or recherche français ou étrangers, des laboratoires abroad, or from public or private research centers. publics ou privés. 1 Laboratory experiments on rain-driven convection: 2 implications for planetary dynamos 3 Peter Olson*, Maylis Landeau, & Benjamin H. Hirsh Department of Earth & Planetary Sciences Johns Hopkins University, Baltimore, MD 21218 4 August 22, 2016 5 Abstract 6 Compositional convection driven by precipitating solids or immiscible liquids has been 7 invoked as a dynamo mechanism in planets and satellites throughout the solar system, 8 including Mercury, Ganymede, and the Earth. Here we report laboratory experiments 9 on turbulent rain-driven convection, analogs for the flows generated by precipitation 10 within planetary fluid interiors. We subject a two-layer fluid to a uniform intensity 11 rainfall, in which the rain is immiscible in the upper layer and miscible in the lower 12 layer. -
Inkjet-Printed Light-Emitting Devices: Applying Inkjet Microfabrication to Multilayer Electronics
Inkjet-Printed Light-Emitting Devices: Applying Inkjet Microfabrication to Multilayer Electronics by Peter D. Angelo A thesis submitted in conformity with the requirements for the degree of Doctor of Philosophy Department of Chemical Engineering & Applied Chemistry University of Toronto Copyright by Peter David Angelo 2013 Inkjet-Printed Light-Emitting Devices: Applying Inkjet Microfabrication to Multilayer Electronics Peter D. Angelo Doctor of Philosophy Department of Chemical Engineering & Applied Chemistry University of Toronto 2013 Abstract This work presents a novel means of producing thin-film light-emitting devices, functioning according to the principle of electroluminescence, using an inkjet printing technique. This study represents the first report of a light-emitting device deposited completely by inkjet printing. An electroluminescent species, doped zinc sulfide, was incorporated into a polymeric matrix and deposited by piezoelectric inkjet printing. The layer was printed over other printed layers including electrodes composed of the conductive polymer poly(3,4-ethylenedioxythiophene), doped with poly(styrenesulfonate) (PEDOT:PSS) and single-walled carbon nanotubes, and in certain device structures, an insulating species, barium titanate, in an insulating polymer binder. The materials used were all suitable for deposition and curing at low to moderate (<150°C) temperatures and atmospheric pressure, allowing for the use of polymers or paper as supportive substrates for the devices, and greatly facilitating the fabrication process. ii The deposition of a completely inkjet-printed light-emitting device has hitherto been unreported. When ZnS has been used as the emitter, solution-processed layers have been prepared by spin- coating, and never by inkjet printing. Furthermore, the utilization of the low-temperature- processed PEDOT:PSS/nanotube composite for both electrodes has not yet been reported. -
Scenarios of Drop Deformation and Breakup in Sprays T´Imea Kékesi
Scenarios of drop deformation and breakup in sprays by T´ımeaK´ekesi September 2017 Technical Report Royal Institute of Technology Department of Mechanics SE-100 44 Stockholm, Sweden Akademisk avhandling som med tillst˚andav Kungliga Tekniska H¨ogskolan i Stockholm framl¨aggestill offentlig granskning f¨oravl¨aggandeav teknologie dok- torsexamen fredagen den 15 september 2017 kl 10.15 i D3, Lindstedtsv¨agen5, Kungliga Tekniska H¨ogskolan, Stockholm. TRITA-MEK Technical report 2017:10 ISSN 0348-467X ISRN KTH/MEK/TR-2017/10-SE ISBN 978-91-7729-500-6 c T. K´ekesi 2017 Tryckt av Universitetsservice US-AB, Stockholm 2017 Scenarios of drop deformation and breakup in sprays T´ımeaK´ekesi Linn´eFLOW Centre, KTH Mechanics, The Royal Institute of Technology SE-100 44 Stockholm, Sweden Abstract Sprays are used in a wide range of engineering applications, in the food and pharmaceutical industry in order to produce certain materials in the desired powder-form, or in internal combustion engines where liquid fuel is injected and atomized in order to obtain the required air/fuel mixture for ideal combustion. The optimization of such processes requires the detailed understanding of the breakup of liquid structures. In this work, we focus on the secondary breakup of medium size liquid drops that are the result of primary breakup at earlier stages of the breakup process, and that are subject to further breakup. The fragmentation of such drops is determined by the competing disruptive (pressure and viscous) and cohesive (surface tension) forces. In order to gain a deeper understanding on the dynamics of the deformation and breakup of such drops, numerical simulations on single drops in uniform and shear flows, and on dual drops in uniform flows have been performed employing a Volume of Fluid (VOF) method. -
Direct Numerical Simulation of Fragmentation of Droplets
Direct Numerical Simulation of Fragmentation of Droplets by Maziyar Jalaal B.Sc., University of Tabriz, 2009 A THESIS SUBMITTED IN PARTIAL FULFILLMENT OF THE REQUIRMENTS FOR THE DEEGREE OF Master of Applied Science in The College of Graduate Studies (Mechanical Engineering) THE UNIVERSITY OF BRITISH COLUMBIA (Okanagan) May 2012 © Maziyar Jalaal, 2012 Abstract The work described in the present thesis is related to a series of projects that I worked on toward the better understanding of fragmentation phenomena. In the past decades, the science of fragmentation has attracted many attentions within the researchers due to its wide range of applications. However, because of the complexity of the subject, even its basic concepts need more investigations. This thesis starts with an introduction to fragmentation of droplets using experimental or numerical approaches. It is discussed that the current mathematical and experimental tools are not able to describe all the details. Thus, high performance numerical simulations are the best alternatives to study the breakup of droplets. The introduction is followed by a discussion on the numerical method and the ranges of the non-dimensional groups. It is described that an adaptive, volume of fluid (VOF) method based on octree meshing is used, providing a notable reduction of computational cost. The rest of the thesis basically discusses the obtained results using direct numerical simulations. Two main geometries are investigated: falling droplets and droplets in a stream. For the case of falling droplets, three simulations with different Eötvös numbers are performed. For the case of droplets in a stream, two-dimensional and three-dimensional simulations are performed for a range of Weber number. -
Droplet Impact on Deep Liquid Pools: Secondary Droplets Formation from Rayleigh Jet Break-Up and Crown Splash
DROPLET IMPACT ON DEEP LIQUID POOLS: SECONDARY DROPLETS FORMATION FROM RAYLEIGH JET BREAK-UP AND CROWN SPLASH by EDUARDO A. CASTILLO OROZCO B.S. Escuela Superior Politécnica del Litoral, 2012 A dissertation submitted in partial fulfillment of the requirements for the degree of Master of Science in Mechanical Engineering in the Department of Mechanical and Aerospace Engineering in the College of Engineering and Computer Science at the University of Central Florida Orlando, Florida Fall-Term 2015 Major Professor: Ranganathan Kumar © 2015 Eduardo A. Castillo Orozco ii ABSTRACT This work aims to study the impact of a droplet on liquid pools of the same fluid to understand the formation of secondary drops from the central jet and crown splash that occur after the impact. The impact of droplets on a deep pool has applications in cleaning up oil spill, spray cooling, painting, inkjet printing and forensic analysis, relying on the changes in properties such as viscosity, interfacial tension and density. Despite the exhaustive research on different aspects of droplet impact, it is not clear how liquid properties can affect the instabilities leading to the Rayleigh jet breakup and the number of secondary drops formed after it pinches off. In this work, through systematic experiments, the droplet impact phenomena is investigated by varying viscosity and surface tension of liquids as well as impact speeds. Further, using a Volume-of-Fluid (VOF) method, it is shown that Rayleigh-Plateau instability is influenced by these parameters, and capillary timescale is the appropriate scale to normalize the breakup time. Increase in impact velocity increases the height of the thin column of fluid that emerges from the liquid pool. -
CHARACTERIZATION of SECONDARY ATOMIZATION at HIGH OHNESORGE NUMBERS by Vishnu Radhakrishna
CHARACTERIZATION OF SECONDARY ATOMIZATION AT HIGH OHNESORGE NUMBERS by Vishnu Radhakrishna A Thesis Submitted to the Faculty of Purdue University In Partial Fulfillment of the Requirements for the degree of Master of Science in Aeronautics and Astronautics School of Aeronautics & Astronautics West Lafayette, Indiana December 2018 2 THE PURDUE UNIVERSITY GRADUATE SCHOOL STATEMENT OF COMMITTEE APPROVAL Dr. Paul E. Sojka, Co-Chair Department of Mechanical Engineering Dr. Timothée Pourpoint, Co-Chair Department of Aeronautics and Astronautics Dr. Guillermo Paniagua Perez Department of Mechanical Engineering Approved by: Dr. Weinong Chen Head of the Graduate Program 3 To my family 4 ACKNOWLEDGMENTS I would like to extend my deepest sense of gratitude to those who have been instrumental in making this thesis possible. Words cannot describe my gratefulness to Professor Paul E. Sojka, for first trusting me with this opportunity, and for being a great advisor. The kind of support and understanding he extended made my life much easier at Purdue. Coming into Purdue as a master’s student, it was my dream to work with him. Presenting this thesis under his guidance is the surely the proudest moment in my life. He always appreciated individual thinking and challenged me with thought provoking questions. The knowledge I have gained from him, not just as a student but also a human being is priceless. I thank him for making me realize that dreams come true indeed. I would like to thank my committee members, Dr. Guillermo Paniagua Perez and Dr. Timothée Pourpoint, for their valuable time, and especially Prof. Paniagua for being my well-wisher throughout the course of my masters. -
1 Introductory Remarks Ian M
1 1 Introductory Remarks Ian M. Hutchings, Graham D. Martin, and Stephen D. Hoath 1.1 Introduction From newspapers to food packaging, from magazines to junk mail and roadside advertising,weliveinaworldofprintedmaterials.Theprocessofprintinginvolves the reproduction of a pattern on a substrate, usually in order to represent text or images or, in many cases, both. Conventional printing methods, including, for example, lithography, flexography, gravure, and screen printing, have evolved over several centuries and can now achieve remarkable levels of quality at very low cost. All these processes share a common feature: the pattern to be printed is embod- ied in a physical form such as on a roll, plate, or screen and transferred from this template during the act of printing through direct or indirect contact with the substrate. The pattern of ink that forms the printed text or image on the substrate thus originates in a pattern that is defined before the printing machine starts to run. Changes to the printed product can be achieved only by changing the mas- ter pattern, which involves making physical changes to the template within the printing machine. Inkjet printing, in contrast, employs a fundamentally different principle. Rather than the printed pattern being created by transfer of ink from a pre-existing master pattern, it is progressively built up directly on to the substrate by the deposition of a large number of individual, tiny drops of ink. Each small droplet, typically 10–100 μm in diameter, is created and deposited under digital control, so that each pattern printed in a sequence by the same machine can just as readily be different from all the others as it can be the same. -
Workshop on Thin Films and Fluid Interfaces January 30Th – February 2Th, 2006
Workshop on Thin Films and Fluid Interfaces January 30th { February 2th, 2006 supported by NSF #0244498 FRG-Collaborative Research Grant: New Challenges in the Dynamics of Thin Films and Fluid Interfaces Held at the Institute for Pure and Applied Mathematics, UCLA This workshop brings together an international group of researchers working on experimental, analytical, and computational problems related to thin films and fluid interfaces. Problems of current interest include solid-liquid- vapor interfaces, moving contact lines, and surface tension effects. Conference organizers • Robert Behringer, Duke University • Andrea Bertozzi, UCLA • Michael Shearer, NCSU • Dejan Slepcev, UCLA • Thomas Witelski, Duke University Monday, January 30, 2006 8:45 am-9:00 am Bertozzi Welcome and opening remarks 9:00 am-9:30 am Craster Flow down a vertical fibre 9:30 am-10:00 am Matar Dynamics, stability and pattern formation in surfactant-driven thin liquid films 10:00 am-10:30 am Coffee break 10:30 am-11:30 am Cazabat A short story of drops 11:30 am-1:30 pm Lunch 1:30 pm-2:00 pm Ben Amar Darcy versus Stokes: the case of suction 2:00 pm-2:30 pm Shen Evaporation and rheological effects on Sol-gel coating 2:30 pm-3:00 pm Witelski Fingering flows of Marangoni-driven thin films 3:00 pm-3:30 pm Coffee break 3:30 pm-4:00 pm Grun¨ Thin-Film Flow Influenced by Thermal Fluctuations 4:00 pm-4:30 pm Giacomelli Microscopic and effective spreading rates for shear-thinning droplets 4:30 pm-5:00 pm Slepˇcev Coarsening in thin liquid films 5:00 pm-7:00 pm Conference reception Tuesday, -
Fls
BREAKDOWN OF A LIQUID FILAMENT INTO DROPS UNDER THE ACTION OF ACOUSTIC DISTURBANCES BY Robert Henry Wickemeyer A. K. Oppenheim Faculty Investigator d - fi3c 7 (THRU) / > (PAGES) (CODE) i fls -3 GPO PRICE i - < /?k'"- p-p-3Lr- (CATEGORY) (,$&*>R OKTMX- OR AD NUMBER' CFSTI PRICE(S) $ Technical Note No. 1-67 Hard copy (HC) 2 2-29 NASA Grant NsG -702 /- Report No. As-67-6 Microfiche (MF) /L3 ff 653 July 65 June 1967 COLLEGE OF ENGINEERING UNIVERSITY OF CALIFORNIA, Berkeley -* 'T OFFICE OF RESEARCH SERVICES University of California Berkeley, California 94720 BREAKDOWN OF A LIQUID FILAMENT INTO DROPS UNDER THE ACTION OF ACOUSTIC DISTURBANCES BY Robert Henry Wickemeyer and c A. K. Oppenheim Technical Note No. 1-67 NASA Grant NsG-702 Report No. AS-67-6 1 ABSTRACT For the purpose of producing small uniform drops for spray combustion experimentation, the theoretical and experi- mental aspects of the breakdown of a liquid filament into drops under the action of acoustic disturbances are studied. The theory expands the Rayleigh criterion for capillary instability of jets by introducing additional terms to account for aero- dynamic forces and fluid viscosity. Experimental results in- dicate that there exists, at each flow rate, a spread of fre- quencies capable of producing uniform drops, rather than unique frequency as predicted by the theory and that, for Reynolds numbers in excess of 600, the size of drops is in- dependent of the filament velocity. 2 TABLE OF CONTENTS Abstract 1 Table of Contents 2 Acknowledgments 3 Nomenclature 4 Introduction 6 Capillary Instability 6 Formulation of the Problem 7 Non-Dimensional Formulation 10 General Solution 12 Surface Tension Pressure 15 Aerodynamic Pressure 16 Specific Solution 17 First Order Solution 18 c Instability Criterion 19 b Experimental Results of Mechanical Generation of Drops 21 Ultrasonic Drop Generation 26 Summary and Conclusions 27 References 28 Tables 31 Figure Captions 32 Figures 33 3 ACKNOWLEDGMENT The experimental work reported here was initiated by Dr. -
Role of All Jet Drops in Mass Transfer from Bursting Bubbles Alexis Berny, Luc Deike, Thomas Séon, Stéphane Popinet
Role of all jet drops in mass transfer from bursting bubbles Alexis Berny, Luc Deike, Thomas Séon, Stéphane Popinet To cite this version: Alexis Berny, Luc Deike, Thomas Séon, Stéphane Popinet. Role of all jet drops in mass transfer from bursting bubbles. Physical Review Fluids, American Physical Society, 2020, 5 (3), pp.033605. 10.1103/PhysRevFluids.5.033605. hal-02481349v2 HAL Id: hal-02481349 https://hal.archives-ouvertes.fr/hal-02481349v2 Submitted on 17 Mar 2020 HAL is a multi-disciplinary open access L’archive ouverte pluridisciplinaire HAL, est archive for the deposit and dissemination of sci- destinée au dépôt et à la diffusion de documents entific research documents, whether they are pub- scientifiques de niveau recherche, publiés ou non, lished or not. The documents may come from émanant des établissements d’enseignement et de teaching and research institutions in France or recherche français ou étrangers, des laboratoires abroad, or from public or private research centers. publics ou privés. Role of all jet drops in mass transfer from bursting bubbles Alexis Berny 1;2, Luc Deike 2;3, Thomas Seon´ 1, and Stephane´ Popinet 1 1 Sorbonne Universite,´ CNRS, UMR 7190, Institut Jean le Rond @’Alembert, F-75005 Paris, France 2 Department of Mechanical and Aerospace Engineering, Princeton University, Princeton, New Jersey 08544 USA 3 Princeton Environmental Institute, Princeton University, Princeton, New Jersey 08544, USA When a bubble bursts at the surface of a liquid, it creates a jet that may break up and produce jet droplets. This phenomenon has motivated numerous studies due to its multiple applications, from bubbles in a glass of champagne to ocean/atmosphere interactions. -
SASO-ISO-80000-11-2020-E.Pdf
SASO ISO 80000-11:2020 ISO 80000-11:2019 Quantities and units - Part 11: Characteristic numbers ICS 01.060 Saudi Standards, Metrology and Quality Org (SASO) ----------------------------------------------------------------------------------------------------------- this document is a draft saudi standard circulated for comment. it is, therefore subject to change and may not be referred to as a saudi standard until approved by the boardDRAFT of directors. Foreword The Saudi Standards ,Metrology and Quality Organization (SASO)has adopted the International standard No. ISO 80000-11:2019 “Quantities and units — Part 11: Characteristic numbers” issued by (ISO). The text of this international standard has been translated into Arabic so as to be approved as a Saudi standard. DRAFT DRAFT SAUDI STANDADR SASO ISO 80000-11: 2020 Introduction Characteristic numbers are physical quantities of unit one, although commonly and erroneously called “dimensionless” quantities. They are used in the studies of natural and technical processes, and (can) present information about the behaviour of the process, or reveal similarities between different processes. Characteristic numbers often are described as ratios of forces in equilibrium; in some cases, however, they are ratios of energy or work, although noted as forces in the literature; sometimes they are the ratio of characteristic times. Characteristic numbers can be defined by the same equation but carry different names if they are concerned with different kinds of processes. Characteristic numbers can be expressed as products or fractions of other characteristic numbers if these are valid for the same kind of process. So, the clauses in this document are arranged according to some groups of processes. As the amount of characteristic numbers is tremendous, and their use in technology and science is not uniform, only a small amount of them is given in this document, where their inclusion depends on their common use.