Preparation of Nanoparticles of Barium Ferrite from Precipitation in Microemulsions
Total Page:16
File Type:pdf, Size:1020Kb
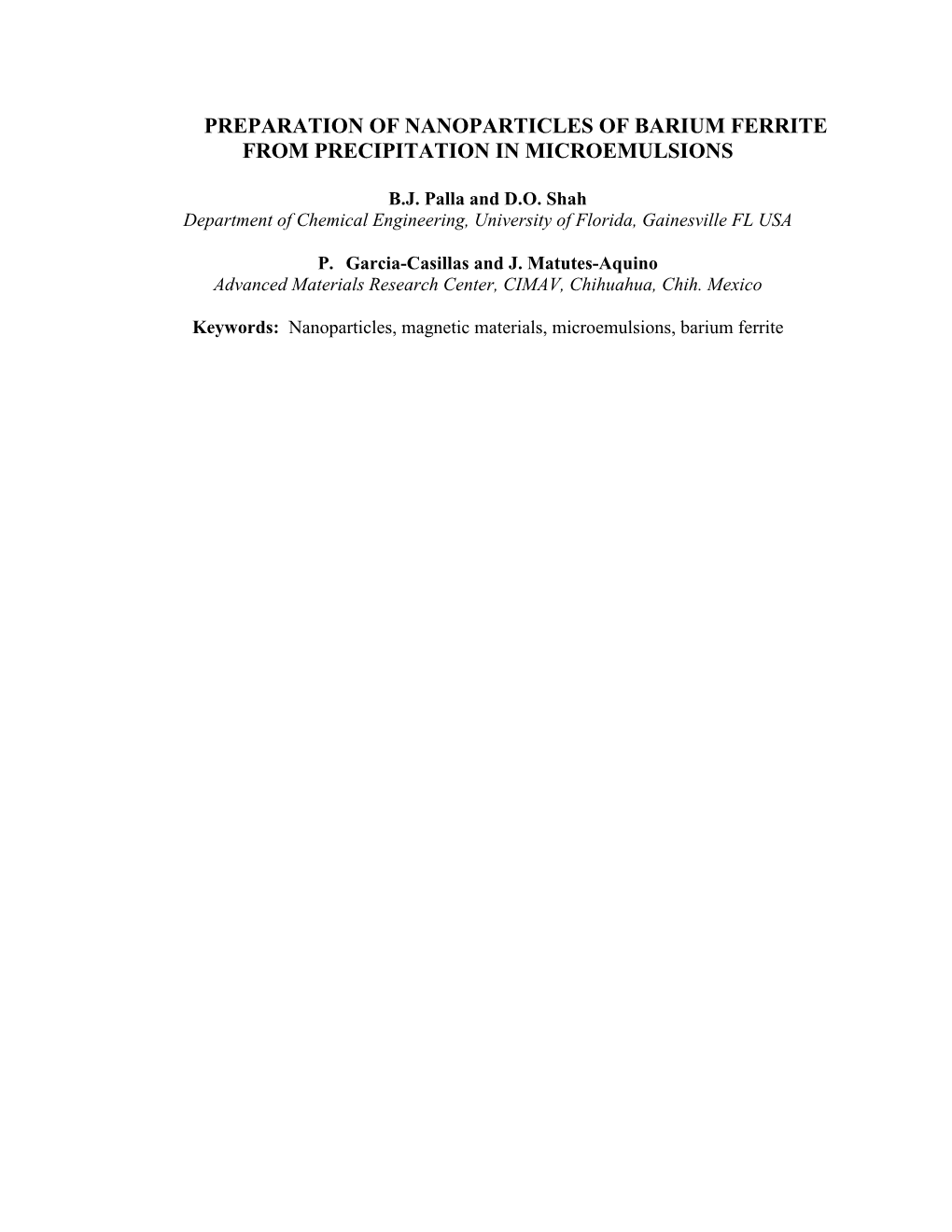
Load more
Recommended publications
-
Epitaxially Grown Bam Hexaferrite Films Having Uniaxial Axis in the Film
www.nature.com/scientificreports OPEN Epitaxially grown BaM hexaferrite films having uniaxial axis in the film plane for self-biased devices Received: 16 November 2016 Xiaozhi Zhang1, Siqin Meng1, Dongsheng Song2, Yao Zhang1, Zhenxing Yue1 & Accepted: 03 February 2017 Vincent G. Harris3 Published: 09 March 2017 Barium hexaferrite (BaM) films with in-planec -axis orientation are promising and technically important materials for self-biased magnetic microwave devices. In this work, highly oriented BaM films with different thickness and an in-plane easy axis (c-axis) of magnetization were grown on a-plane (1120) single-crystal sapphire substrates by direct current magnetron sputtering. A procedure involving seed layers, layer-by-layer annealing was adopted to reduce the substrate-induced strains and allow for the growth of thick (~3.44 μm) films. The epitaxial growth of the BaM film on sapphire was revealed by high- resolution transmission electron microscopy with dislocations being observed at the film-substrate interface. The orientation was also verified by X-ray diffraction and more notably, polarized Raman scattering. The magnetic properties and ferromagnetic resonant frequencies were experimentally characterized by a vibrating sample magnetometry and a frequency-swept ferromagnetic resonant flip- chip technique, respectively. The micron-thick BaM films exhibited a large remanence ratio of 0.92 along in-plane easy axis and a small one of 0.09 for the in-plane hard axis loop measurement. The FMR frequency was 50.3 GHz at zero field and reached 57.9 GHz under a magnetic field of 3 kOe, indicating that the epitaxial BaM films with strong self-biased behaviors have good electromagnetic properties in millimeter-wave range. -
Investigation of Structural, Thermal and Magnetic Properties of Strontium Substituted Barium Hexaferrite Synthesized Via Co-Precipitation Method
International Journal of ChemTech Research CODEN (USA): IJCRGG ISSN: 0974-4290 Vol.8, No.12 pp 404-410, 2015 Investigation of Structural, Thermal and Magnetic properties of Strontium substituted Barium Hexaferrite Synthesized via co-precipitation Method S.Vadivelan*, N.VictorJaya Department of physics, Anna University, Chennai-25, India Abstract: In this paper, the strontium doped barium hexaferrite (BaSrxFe12-xO19) is synthesized by co-precipitated technique and involved the sintering process (1000°C up to 5hrs). After that the properties of these prepared samples are analyzed using various characterizations. The barium hexaferrite is mostly used in recording devices as well as permanent magnetic materials, because it exhibits perfect magnetic properties. The pure and strontium doped (X=1%, 3%, 5% and 7%) barium hexaferrite were obtained from the technique. The x-rd peaks were indexed as a primitive hexagonal cell with the refined lattice parameter values of a=b=5.865 Å, and c=23.099 Å. From the lattice parameter values the structure of this compound is hexagonal. TGA/DTA is the studies to analysis the degradation mechanisms, reaction kinetics, determination of organic content and determination of inorganic (e.g. ash) content in a sample around 850°C and transformation of residuals at the around temperature 585°C. From the FT-IR, the functional groups and vibration modes are identified. SEM image is confirmed the size of the particles of the sample. From VSM characterization, the magnetic saturation (Ms) Value is increasing from 10.9-33.9emu/g with increasing doped percentage of strontium and magnetic remanenc (Mr) increased from 3.98- 24.95 emu/g with increasing doped percentage of strontium. -
Innovative Ironless Loudspeaker Motor Adapted to Automotive Audio Mathias Rémy
Innovative Ironless Loudspeaker Motor Adapted to Automotive Audio Mathias Rémy To cite this version: Mathias Rémy. Innovative Ironless Loudspeaker Motor Adapted to Automotive Audio. Acoustics [physics.class-ph]. Université du Maine, 2011. English. <NNT : 2011LEMA1026>. <tel-01279478> HAL Id: tel-01279478 https://tel.archives-ouvertes.fr/tel-01279478 Submitted on 26 Feb 2016 HAL is a multi-disciplinary open access L’archive ouverte pluridisciplinaire HAL, est archive for the deposit and dissemination of sci- destinée au dépôt et à la diffusion de documents entific research documents, whether they are pub- scientifiques de niveau recherche, publiés ou non, lished or not. The documents may come from émanant des établissements d’enseignement et de teaching and research institutions in France or recherche français ou étrangers, des laboratoires abroad, or from public or private research centers. publics ou privés. Acad´emie de Nantes E´COLE DOCTORALE SCIENCES POUR L’INGENIEUR,´ GEOSCIENCES,´ ARCHITECTURE UNIVERSITE´ DU MAINE, LE MANS, FRANCE THESE` DE DOCTORAT Sp´ecialit´e: ACOUSTIQUE pr´esent´ee par Mathias REMY pour obtenir le titre de Docteur d’Universit´e Innovative Ironless Loudspeaker Motor Adapted to Automotive Audio Moteur de Haut-parleur Sans Fer Innovant Adapt´e`al’Audio Automobile Th`ese pr´epar´ee au Laboratoire d’Acoustique de l’Universit´edu Maine soutenue le 9 septembre 2011 devant le jury compos´ede : A. DOBRUCKI Professeur, Wroclaw University of Technology Rapporteur B. MULTON Professeur,ENSCachan,Bruz Rapporteur N. DAUCHEZ Professeur, SUPMECA, Saint-Ouen Examinateur C. HENAUX Maˆıtre de Conf´erence, INP Toulouse Examinateur Y. AUREGAN Professeur, LAUM, Universit´edu Maine Examinateur B. -
Plastiform 1037
PLASTIFORM® 1037 Permanent Magnet Material Energy product 1.0 MGOe flexible permanent magnet product • Machinability permits simple and inexpensive shaping and assembly processing • Resilience prevents chipping, cracking or shattering • Close dimensional and magnetic tolerances allow substantial cost reductions Description Cost reductions—Greater design Moveable partition supports PLASTIFORM® Permanent Magnet latitude and more efficient production Metal storage bin identification label Materials are rubber barium ferrite methods made possible by its unique holders composites manufactured in sheets, strips properties contribute to reduced costs in Magnetic jigs and fixtures and individually cut pieces. Magnetic many stages of product development. Novelties properties are generated by preferentially orienting ferromagnetic barium ferrite in Applications Availability a stable binder. It is highly anisotropic and Uses for this magnet product range from PLASTIFORM® permanent magnets are possesses an unusually strong resistance novelties to industrial applications, such fabricated in accordance with customer to demagnetization. as magnetic separator equipment and specification. The material can be freezer door latches. Many of these uses produced in virtually any size and shape. 1037 material is a specially formulated require specialized fabrication of the The material is available in either magne- magnet product designed for use in latch magnet material, a demand which 1037 tized or nonmagnetized condition. It can and similar applications. The high degree is eminently well suited to meet. be magnetized with one or more poles of conformability exhibited by this Because PLASTIFORM® magnet material on each surface and in a pattern that material allows it to match various pole meets with the application needs. piece configurations and yields optimum successfully combines high coercive force performance when sandwiched between and residual induction with flexibility and PLASTIFORM® Quality ease of fabrication, it is currently being pole pieces. -
SAFETY DATA SHEET Revision Date 24.06.2020 According to Regulation (EC) No
Version 6.2 SAFETY DATA SHEET Revision Date 24.06.2020 according to Regulation (EC) No. 1907/2006 Print Date 02.10.2021 GENERIC EU MSDS - NO COUNTRY SPECIFIC DATA - NO OEL DATA SECTION 1: Identification of the substance/mixture and of the company/undertaking 1.1 Product identifiers Product name : Barium ferrite Product Number : 383295 Brand : Aldrich REACH No. : A registration number is not available for this substance as the substance or its uses are exempted from registration, the annual tonnage does not require a registration or the registration is envisaged for a later registration deadline. CAS-No. : 12047-11-9 1.2 Relevant identified uses of the substance or mixture and uses advised against Identified uses : Laboratory chemicals, Manufacture of substances 1.3 Details of the supplier of the safety data sheet Company : Sigma-Aldrich Inc. 3050 SPRUCE ST ST. LOUIS MO 63103 UNITED STATES Telephone : +1 314 771-5765 Fax : +1 800 325-5052 1.4 Emergency telephone Emergency Phone # : 800-424-9300 CHEMTREC (USA) +1-703- 527-3887 CHEMTREC (International) 24 Hours/day; 7 Days/week SECTION 2: Hazards identification 2.1 Classification of the substance or mixture Classification according to Regulation (EC) No 1272/2008 Acute toxicity, Oral (Category 4), H302 Acute toxicity, Inhalation (Category 4), H332 Specific target organ toxicity - single exposure (Category 2), H371 Specific target organ toxicity - repeated exposure (Category 2), H373 For the full text of the H-Statements mentioned in this Section, see Section 16. 2.2 Label elements Labelling according Regulation (EC) No 1272/2008 Aldrich- 383295 Page 1 of 8 The life science business of Merck operates as MilliporeSigma in the US and Canada Pictogram Signal word Warning Hazard statement(s) H302 + H332 Harmful if swallowed or if inhaled. -
United Nations ST/SG/AC.10/C.3/2018/105
United Nations ST/SG/AC.10/C.3/2018/105 Secretariat Distr.: General 5 September 2018 Original: English Committee of Experts on the Transport of Dangerous Goods and on the Globally Harmonized System of Classification and Labelling of Chemicals Sub-Committee of Experts on the Transport of Dangerous Goods Fifty-fourth session Geneva, 26 November-4 December 2018 Item 2 (c) of the provisional agenda Recommendations made by the Sub-Committee on its fifty-first, fifty-second and fifty-third sessions and pending issues: Listing, classification and packing Transport of barium carbonate as non-dangerous good Submitted by the expert from Spain* Introduction 1. Barium carbonate is a barium compound, and therefore by defect classified as UN 1564, BARIUM COMPOUND, N.O.S, in Division class 6.1. 2. Nevertheless, according to the information available, barium carbonate may not be toxic as can be shown by the information and tests provided. 3. To facilitate international trade and to avoid different interpretation of the applicable prescriptions for the transport of dangerous goods, it would be interesting to clearly exempt barium carbonates from the scope of the Model Regulations, as has already been done for Barium sulphate by special provision (SP) 177: “177 Barium sulphate is not subject to these Regulations.” 4. During the fifty-third session of the Sub-Committee, Spain submitted informal document INF.32, which included this proposal, justified by some test results for Barium Carbonate. Spain was asked to submit a formal document, taking into account the comments provided by the Sub-Committee experts (refer to ST/SG/AC.10/C.3/106 paragraphs 60-62), including additional test results for the barium carbonate from other sources of information. -
Magnetic and Physical Properties Modification Using Sintering Temperature Variations in the Process of Making Barium Hexaferrite Permanent Magnet
Magnetic and Physical Properties Modification using Sintering Temperature Variations in the Process of Making Barium Hexaferrite Permanent Magnet Wibowo, R Lullus L. G. Hidajat, Sony Wijaya, Eko Surojo Mechanical Engineering Department, Sebelas Maret University, Surakarta 57128, Indonesia Keywords: Hard-Magnetic, Barium Hexaferrite, Magnetic Properties, Mechanical Alloying, Sintering. Abstract: This paper discusses the modification of magnetic hysteresis and particle size of barium hexaferrite permanent magnet using sintering temperature variatons. The materials used were Barium Carbonate (BaCO3) and Hematite (Fe2O3) with a stochiometric ratio of (1: 6), obtained by the dry miling mixing process for 6 hours. Then this material was calcined at 1100°Celsius for 30 minutes and sieved to pass through the 200 mesh filter. The sample is compacted by 3wt% additive shellac and 5 Ton pressing to form a pellet with diameter of 5 mm. The next process is samples were sintered at temperatures of 900°C, 1000°C and 1100°C for 30 minutes. The magnetic hysteresis of this sample were then determined using VSM and microstructure analysis was determined using SEM. The results showed that the average Hmax and particle size increase for temperatur of 900°Cto 1000°C and decrease from 1000°C to 1100°C. At sintering temperature of 1000° C a granullar fusion was formed while new phase had not been formed, whereas at a sintering temperature of 1100°C a new phase had been formed which causes coercivity decreased. It was concluded that the optimal modification of magnetic properties and particle size was obtained at sintering temperature of 1000°C. 1 INTRODUCTION used as permanent magnets in electric motors, generators and speakers (S. -
Environmental Stability Study and Life Expectancies of Magnetic Media for Use with Ibm 3590 and Quantum Digital Linear Tape Systems
ARKIVAL TECHNOLOGY CORPORATION ENVIRONMENTAL STABILITY STUDY AND LIFE EXPECTANCIES OF MAGNETIC MEDIA FOR USE WITH IBM 3590 AND QUANTUM DIGITAL LINEAR TAPE SYSTEMS Ronald D. Weiss Arkival Technology Corporation 427 Amherst St. Nashua, NH 03063 Phone: (603) 881-3322 www.ARKIVAL.com 1 ARKIVAL TECHNOLOGY CORPORATION ENVIRONMENTAL STABILITY STUDY AND LIFE EXPECTANCIES OF MAGNETIC MEDIA FOR USE WITH IBM 3590 AND QUANTUM DIGITAL LINEAR TAPE SYSTEMS National Archives and Records Administration #NAMA-01-F-0061 FINAL REPORT PERIOD of WORK: October 2001- June 2002 Federal Supply Service Contract Number: GS 35F 0611L Arkival Technology Corporation 427 Amherst St. Nashua, NH 03063 Phone: (603) 881-3322 www.ARKIVAL.com 2 TABLE of CONTENTS Executive Summary………………………………………………………… 5 1.0 STUDY OVERVIEW…………………………………………………… 7 1.1 Technical Areas of Study 1.2 Study Duration 1.3 Tape Drive Recording Features 1.4 Test Environments 1.5 Data Collection and Analysis 2.0 TECHNICAL STUDIES 2.1 Magnetic & Microstructure Analyses of the Recording Media….. 9 2.1.1 Transmission Electron Microscopy (TEM) Analysis 2.1.2 Vibrating Sample Magnetometer (VSM) Analysis 2.2 VSM/Aging Study…………………………………………………. 14 2.3 Binder Hydrolysis ………………………………………………... 17 2.4 Physical Properties ……………………………………………….. 24 2.4.1 Resistivity 2.4.2 Friction 2.5 RF Amplitude response …………………………………………….28 2.6 Error Study ……………………………………………………….. 31 2.6.1 Catastrophic Tape and Drive Failures 2.7 Life Expectancies (LE) …………………………………………… 38 2.7.1 Magnetic Saturation LE 2.7.2 Error Rate (B*ER) LE Conclusions -
Factors Affecting the Synthesis and Formation of Single-Phase Barium Hexaferrite by a Technique of Oxalate Precursor
View metadata, citation and similar papers at core.ac.uk brought to you by CORE provided by Directory of Open Access Journals American Journal of Applied Sciences 7 (7): 914-921, 2010 ISSN 1546-9239 © 2010 Science Publications Factors Affecting the Synthesis and Formation of Single-Phase Barium Hexaferrite by a Technique of Oxalate Precursor Q. Mohsen Materials and Corrosion Lab (MCL), Faculty of Science, Taif University, Saudi Arabia Abstract: Problem statement: Barium hexaferrite (BaFe 12 O19 ), is of great importance as permanent magnets, particularly for magnetic recording as well as in microwave devices. Approach: The aim of this study was to synthesize Stoichiometric and single-phase barium hexaferrite through a technique of oxalate precursor. Effects of different Fe 3+ /Ba 2+ mole ratio and annealing temperature on the particle size, microstructure and magnetic properties of the resulting barium hexaferrite powders has been studied and reported in the presented research. The annealing temperature was controlled from 900- 1200°C, while the Fe 3+ /Ba 2+ was controlled from 12-8.57. Results: The resultant powders were investigated by Differential Thermal Analyzer (DTA), X-Ray Diffractometer (XRD), Scanning Electron Microscopy (SEM) and Vibrating Sample Magnetometer (VSM). Single phase of well 3+ 2+ crystalline BaFe 12 O19 was first obtained at Fe /Ba mole ratio of 9.23 and 8.57 at annealing temperature 1100°C. Moreover, at annealing temperature 1200°C the single phase BaFe 12 O19 appeared at all different Fe 3+ /Ba 2+ mole ratio. The SEM results showed that the grains were regular hexagonal − platelets. In addition, maximum saturation magnetization (70.25 emu g 1) was observed at mole ratio 10 and annealing temperature 1200°C. -
Barium Ferrite Nanoparticles Prepared by Self-Propagating Low-Temperature Combustion Method and Its Characterization
Bull. Mater. Sci., Vol. 34, No. 7, December 2011, pp. 1319–1323. © Indian Academy of Sciences. Barium ferrite nanoparticles prepared by self-propagating low-temperature combustion method and its characterization P M PRITHVIRAJ SWAMY, S BASAVARAJA†, VIJAYANAND HAVANOOR, N V SRINIVAS RAO††, R NIJAGUNAPPA††† and A VENKATARAMAN* Materials Chemistry Laboratory, Department of Materials Science, Gulbarga University, Gulbarga 585 106, India †Present address: Veeco-India Nanotechnology Laboratory, Jawaharlal Nehru Centre for Advanced Scientific Research, Jakkur, Bangalore 560 064, India ††R&D Centre Premier Explosives Pvt. Ltd., Hyderabad 500 015, India †††Department of Environmental Sciences, Gulbarga University, Gulbarga 585 106, India MS received 14 April 2010 Abstract. The barium ferrite particles were prepared using a self-propagating low-temperature combustion method using polyethylene glycol (PEG) as a fuel. The process was investigated with simultaneous thermo- gravimetric-differential thermal analysis (TG–DTA). The crystalline structure, morphology and the magnetic properties of the barium ferrite particles were studied by means of X-ray diffraction (XRD), scanning electron microscopy (SEM), transmission electron microscopy (TEM) and SQUID susceptometer. The results show that the ignition temperature of PEG is lower compared with other combustion methods and gives nanocrys- talline barium ferrite. Keywords. Barium ferrite; self-propagating combustion method; magnetic property; X-ray diffraction; morphology. 1. Introduction other words, -
Chapter One Introduction 1.1 Prelude Ferrite Is a Polycrystalline, Sintered
Chapter One Introduction 1.1 Prelude Ferrite is a polycrystalline, sintered material with high electrical resistivity. The high resistance of ferrite makes eddy current losses extremely low at high frequencies. Therefore, unlike other magnetic components, ferrite can be used at considerably high frequencies. Manganese-zinc (Mn-Zn) ferrites can be used at frequencies up to several megahertz. The basic ferrite materials are obtained in an extremely high purity. These materials are mixed, calcined, milled, granulated, formed by pressing, and sintered at a temperature of 1000°C to 1400°C, and then machined. The electrical and mechanical properties of a particular ferrite material are obtained by the material formulation and the processing applied. Extraordinary exacting process controls are required to assure the high uniformity of product for which TDK (Japanese multinational electronics company) ferrites are well known. Through the above processes, ferrite materials can be optimized for specific applications. 1.2 Research Problem Magnets and its general properties. Types of magnetic materials and the difference in structure. Components of the ferrite and its most important general characteristics. Uses of ferrite magnet. 1.3 Literature Review *Physical and Magnetic Properties of Manganese Ferrite Nanoparticles In this paper, manganese ferrite (MnFe2O4) nanoparticles were synthesized using chemical bath deposition (CBD) method and characterized by XRD and TEM to determine different properties of nanoparticles. The results obtained showed the formation of manganese ferrite nanoparticles with an average particle size are in good agreement with previous reported experimental results and displayed good magnetic properties. Magnetic properties were determined using Vibrating Sample Magnetometer (VSM). Due to simplicity and low cost of this process, it could be used for synthesis of ferrites nanoparticles. -
2 Preparation of Barium Ferrite Bafe12o19 and the Study
College of Basic Education Researchers Journal Vol.11 No.1 Preparation of barium ferrite BaFe12O19 and the study of the effect of fast neutrons on its magnetic and dielectrical properties. Dr. Jassim Mohammed Yaseen University of Mosul / College of Basic Education Received: 7/3/2011 ; Accepted: 2/6/2011 Abstract: Hard hexagonal barium ferrite BaFe12O19 was prepared by solid state reaction method using a precursor (BaO- 6 Fe2O3) mixture at calcinations temperature 1100 C for 2 hr. The XRD patterns of the calcined samples show the formation of BaFe12O19 at this temperature .In this work, some of the samples were irradiated by fast neutron (241Am-Be ) in average energy 5 MeV with flux ( 1.5 ×106 n/cm2.s ). The fast neutron irradiation did not affect the magnetic properties of prepared samples obviously, but it affected the electrical resistivity in direct relation in which the increasing of irradiation dosages lead to increasing of electrical resistivity obviously . BaFe12O19 ﺘﻡ ﺘﺤﻀﻴﺭ ﻤﺎﺩﺓ ﺍﻟﺒﺎﺭﻴﻭﻡ ﻓﺭﺍﻴﺕ BaFe12O19 ﺒﻁﺭﻴﻘﺔ ﺍﻟﺘﻔﺎﻋل ﺍﻟﺼﻠﺏ ﻋﻥ ﻁﺭﻴﻕ ﺨﻠـﻁ ﺍﻟﻤـﺭﻜﺒﻴﻥ BaO ﻭFe2O3 ﺒﺎﻟﻨﺴﺒﺔ ﺍﻟﻤﻭﻟﻴﺔ (BaO- 6 Fe2O3) . ﺒﻌﺩ ﺍﺠﺭﺍﺀ ﻋﻤﻠﻴﺎﺕ ﺍﻟﺨﻠﻁ ﺍﻟﺭﻁﺏ ﻭﺍﻟﺘﺠﻔﻴﻑ ﺘﻡ ﺤـﺭﻕ ﺍﻟﺨﻠﻴﻁ ﺒﺩﺭﺠﺔ ﺤﺭﺍﺭﺓ C 1100 ﻭﻟﻤﺩﺓ ﺴﺎﻋﺘﻴﻥ . ﺒﺎﺴﺘﺨﺩﺍﻡ ﺘﻘﻨﻴﺔ ﺍﻟﺤﻴﻭﺩ ﻟﻼﺸﻌﺔ ﺍﻟﺴﻴﻨﻴﺔ ﺘـﻡ ﺍﻟﺤﺼـﻭل ﻋﻠـﻰ ﻨﻤﻭﺫﺝ ﺍﻟﺤﻴﻭﺩ ﺍﻟﺴﻴﻨﻲ ﻟﻁﻭﺭ ﺍﻟﺒﺎﺭﻴﻭﻡ ﻓﺭﺍﻴﺕ BaFe12O19 ﺍﻟﻤﺤﻀﺭ ﻭﻓﻕ ﺍﻟﻅﺭﻭﻑ ﺃﻋﻼﻩ. ﻓﻲ ﻫﺫﺍ ﺍﻟﻌﻤل ﺘـﻡ 241 ﺘﺸﻌﻴﻊ ﺒﻌﺽ ﺍﻟﻨﻤﺎﺫﺝ ﺒﺎﻟﻨﻴﻭﺘﺭﻭﻨﺎﺕ ﺍﻟﺴﺭﻴﻌﺔ (Am-Be ) ﻭﺒﻤﻌﺩل ﻁﺎﻓﻲ ﻗﺩﺭﻩMeV 5 ﻭﺒﻔﻴﺽ ﻨﻴـﻭﺘﺭﻭﻨﻲ 6 2 ﻗﺩﺭﻩ ( n/cm .s 10× 1.5 ) ﻨﺘﺎﺌﺞ ﺍﻟﺘﺸﻌﻴﻊ ﺃﻅﻬﺭﺕ ﺃﻥ ﺍﻟﺘﺸﻌﻴﻊ ﺍﻟﻨﻴﻭﺘﺭﻭﻨﻲ ﻭﻓﻕ ﺍﻟﻅﺭﻭﻑ ﺍﻋﻼﻩ ﻟﻡ ﻴـﺅﺜﺭ ﻋﻠﻰ ﺍﻟﺨﻭﺍﺹ ﺍﻟﻤﻐﻨﺎﻁﻴﺴﻴﺔ ﻟﻠﺒﺎﺭﻴﻭﻡ ﻓﺭﺍﻴﺕ ﺒﺸﻜل ﻭﺍﻀﺢ ، ﻓﻲ ﺤﻴﻥ ﺃﺜﺭﺕ ﺒﺸـﻜل ﻜﺒﻴـﺭ ﻋﻠـﻰ ﺍﻟﻤﻘﺎﻭﻤﻴـﺔ ﺍﻟﻜﻬﺭﺒﺎﺌﻴﺔ ﻟﻠﻤﺎﺩﺓ ، ﺤﻴﺙ ﺃﻥ ﺍﻟﻤﻘﺎﻭﻤﻴﺔ ﺍﻟﻜﻬﺭﺒﺎﺌﻴﺔ ﺘﺯﺩﺍﺩ ﺒﺯﻴﺎﺩﺓ ﺍﻟﺠﺭﻋﺔ ﺍﻹﺸﻌﺎﻋﻴﺔ .