SAMPLE Contract Completion Time NOT for BIDDING PURPOSES 120 Working Days This Contract Is Exempt from Federal Oversight
Total Page:16
File Type:pdf, Size:1020Kb
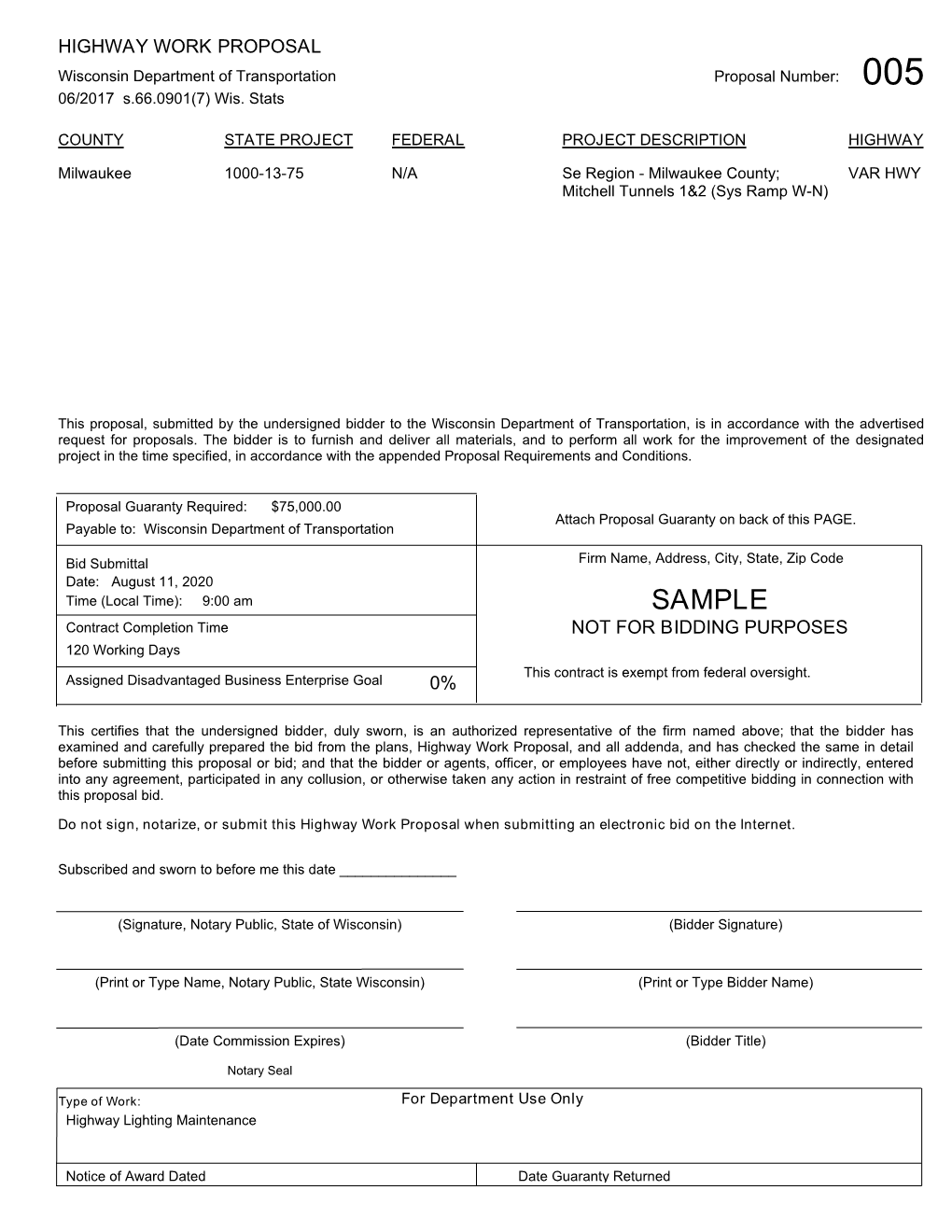
Load more
Recommended publications
-
A2LA Cert. No. 0859.03) 10/29/2020 Page 1 of 5 Accelerated Weathering Tests (Continued) Test Method(S)
SCOPE OF ACCREDITATION TO ISO/IEC 17025:2017 Q-LAB DEUTSCHLAND GMBH In den Hallen 30 66115 Saarbrücken, Germany Axel Koerper Phone: +49 681 8574735 Email: [email protected] Website: www.q-lab.com MECHANICAL Valid To: September 30, 2022 Certificate Number: 0859.03 In recognition of the successful completion of the A2LA evaluation process, accreditation is granted to this laboratory to perform the following weathering and corrosion tests: Testing to determine material durability using laboratory accelerated methods, visual and instrumental evaluations to measure degradation effects, including gloss and color, mechanical measurements of physical properties before and after exposure. On the following materials: Automotive Components, Plastics, Paints, Textiles, Roofing, Sealants, Glass, Photovoltaic, and Solar Heating materials Using the following test methods: Accelerated Weathering Tests Test Method(s) Salt Spray (Fog) Testing ASTM B117 Water Resistance of Coatings Using Water for Apparatus ASTM D1735 Water Resistance to 100% Relative Humidity ASTM D2247 Lightfastness and Weatherability of Printed Matter ASTM D3424 Methods 3 & 4 Lightfastness of Colorants Used in Artists’ Materials ASTM D4303 Methods C & D Testing Water Resistance of Coatings Using Controlled Condensation ASTM D4585 Fluorescent UV Condensation Exposure of Paint and Related Coatings ASTM D4587 Accelerated Testing Color Stability of Indoor Plastics ASTM D4674 Methods III & IV Cyclic Salt Fog / UV Exposure of Painted Metal ASTM D5894 Specification for Polyolefin Based Plastic Lumber Decking Boards ASTM D6662 Accelerated Acid Etch Weathering of Automotive Clearcoats Using a ASTM D7356 Xenon Arc Exposure Device Xenon Arc Exposure Test with Enhanced Light and Water Exposure for ASTM D7869 Transportation Coating Modified Salt Spray (Fog) Testing ASTM G85 (A2LA Cert. -
Annual Report 2015 2015 Annual Report Annual
www.fhs.ch Annual Report 2015 2015 Annual Report 1 FH Annual Report 2015 2 ISSN 1421-7384 The annual report is also available in French and German in paper or electronic format, upon request. © Fédération de l’industrie horlogère suisse FH, 2016 3 Table of contents The word of the President 4 Highlights of 2015 6 Swissness - Swiss made – Final step before entry into force 8 Hong Kong Watch & Clock Fair – Intensive surveillance 10 Counterfeiting on the Internet – Social networks in force 11 ISO/TC 114 - Watchmaking Conference – In Lucerne in May 12 Panorama of the 2015 activities 14 Improvement of framework conditions 16 Information and public relations 22 The fight against counterfeiting 26 Standardisation 33 Legal, economic and commercial services 34 Relations with the authorities and economic circles 35 FH centres abroad 37 The Swiss watch industry in 2015 38 Watch industry statistics 40 Structure of the FH in 2015 44 The FH in 2015 46 The General Meeting 47 The Board 48 The Bureau and Commissions 49 The Departments and the Services 50 The network of partners 51 The word of 5 the President In 2015 the watch industry Council will take its decision in 2016 according to the results experienced its first nega- of the consultation, the revised OSM is also expected to enter tive year since 2009, with into force in 2017. a fall in exports of 3.3%. This is due to the down- Defending the Swiss made label abroad, the FH took action turn in trade in Hong Kong, against a Chinese participant at the Hong Kong Watch and China and Russia. -
Salt Spray Test by W
RWB:WHM:PWCS:CAR U. S. DEPARTMENT OF COBilMSRCE Letter VIII-1 & V-6 NATIONAL BUREAU OF STANDARDS Circular No. 530 July 1, 19 RS Salt Spray Test by W. H. Mutchler, R. W. Buzzard, and P. W. C. Strausser I. Introduction II. Historical conditions ^ III. Operating .... , 1. The spray ^ a. Formation and distribution b. Atomizers and operating pressures c. Density of the fog 2. The solution a. Purity b. Concentration ^ J. Temperature a. The need for control b. Results of non-control IV. Salt spray cabinets 1. T 3'’pical system 2. Details of construction a. Army-Navy specifications b. Bureau of Standards 'Equipment c. High temperature equipment V. Procedure in testinp: 1. Cleaning 2. TjRe speciraeiis R. Methods of suspension 4. Movement of specimens 5 . Starting the tests 6. Inspection 7. Temperature control VI. Typical_ applications VII. Methods of measuring and expressing results VIII. Interpretation of results IX. Bibliography I. Introduction The corrosion of metals has been an absorbing study of countlovcs investigators for many years. In order to acquire more rapidly knowledge of the fundamentril causes and pro- cesses of corrosion, and to obtain facts indicative of the probable behavior of metals under various conditions of ser- vice, numerous laboratory methods for accelerating attack have been devised. One of these, the subject matter of the present paper and popularly known as the "salt spraj'' test", has enjoyed increasins’ly widespread use in this country. At the present 'writing t.he procedures employed -in salt spray testing differ appreciably in different laboratories. , " - 2 - Ov\ring to this lack of uniformity, and to the failure to con- trol essential variables associated with the method, the test itself has been subjected to some unjust criticisms. -
Green Surface in Avariety of Fields
i cc 99 for Go .I. G n for the Env!i ron ment- A Positive Outlook for the Year 2000 and Beyond By J.H. Lindsay Organizers The Past is Prologue- tal equipment, including automaticcon- Session E Setting the Perspective trols and laboratory instrumentation for 1 SUR/FINa ’92-Atlanta For the Year 2000 new process development. Very often, we forget that the key to the In the year 2000 and beyond, Pfaff future lies in reviewing the past. It fell to sees the industry consolidating, but Michael A. Pfaff, vice president-ln- continuing to survive and continuing to dustrial Products Group, MacDermid, meet the challenges of our world. Ac- Inc. and president of the Metal Finish- tivities will be influenced by world stan- ing Suppliers’ Association, to do just dards on specifications and the envi- that. He set the perspective for the coming century and noted that the sur- face finishing industry is driven by tech- Will the Year Zoo0 nology, is environmentally safer and is worldwide in scope. see the supplanting of The surface finishing community was It got that way through a long and “surface finishing” by heartened by the outlook for the indus- eventful history. He reviewed the early “surfaceengineering?” try as envisioned by the participants in days of sacrificial Dr. David R. Gabe a unique and special session on the coating applications conference program at SUR/FlN@’92in (such as cadmium Atlanta. SURFACE FINISHING-THE on piano wire), the YEAR 2000 AND BEYOND took an functional military ronment, computerized instrumenta- expert look at what opportunities, chal- applications of World tion, more specialized finishes and coat- lenges and advances are likely to exist War II and the glory ings. -
Iso17025-Dsm-Scope-Tuv-Sud.Pdf
Schedule Issue date: 1 February 2019 Valid until: 12 January 2022 NO: SAMM 755 MS ISO/IEC 17025 Page: 1 of 5 LABORATORY LOCATION: TUV SUD (M) SDN. BHD. (PERMANENT LABORATORY) NO. 18, JALAN ASTAKA U8/82, BUKIT JELUTONG, 40150 SHAH ALAM, SELANGOR, MALAYSIA FIELD OF TESTING: MECHANICAL This laboratory has demonstrated its technical competence to operate in accordance with MS ISO/IEC 17025:2005 (ISO/IEC 17025:2005). This laboratory’s fulfillment of the requirements of ISO/IEC 17025 means the laboratory meets both the technical competence requirements and management system requirements that are necessary for it to consistently deliver technically valid test results and calibrations. The management system requirements in ISO/IEC 17025 are written in language relevant to laboratory operations and operate generally in accordance with the principles of ISO 9001 (see Joint ISO-ILAC-IAF Communiqué dated April 2017). SCOPE OF TESTING: MECHANICAL he current scope accreditation of for t Materials/ Type of Test/ Standard Test Methods/ Products Tested Properties Measured/ Equipment/Techniques Range of Measurement directories - Electrical and Electronic Low Temperature Tests IEC 60068-2-1: Ed 6.0 (2007) : Test A Equipment and Automotive (down to -60°C) Parts/Materials/component ISO 16750-4: 2010 Clause 5.1.1 High Temperature Tests IEC 60068-2-2: Ed 5.0 (2007) : Test B (up to +200°C) www.jsm.gov.my/cab ISO 16750-4: 2010 Clause 5.1.2 Rapid Change of Temperature IEC 60068-2-14: Ed 6.0 (2009) Test Na with prescribe time (-60°C to 200°C) ISO 16750-4: 2010 -
1. Technology 2. Salt Spray Test Results 3. Benefits 4. Assembly Instructions 5. Production and Transition Phase
INDEX 1. TECHNOLOGY 2. SALT SPRAY TEST RESULTS 3. BENEFITS 4. ASSEMBLY INSTRUCTIONS 5. PRODUCTION AND TRANSITION PHASE 1 1. TECHNOLOGY The innovative Larga Zn/Ni plating exceeds the requirements of European laws, combining top corrosion resistance and environment safety. Here below is the comparison of the coating structure in the evolution from yellow CrVI (A3C) to white CrIII and to the new Zinc/Nickel. Sealing layer Passivation Sealing layer Zn/Ni Chromate coating CrIII Zinc Steel Chromate coating CrVI Zinc Steel Steel A3C YELLOW CrVI CHROMATION WHITE CrIII CHROMATION LARGA Zn/Ni 2 2. SALT SPRAY TEST RESULTS The special coating with a total layer thickness of 6-10 mm and a nickel content of 12%-15% offers the best corrosion resistance. Here below are examples of salt spray tests: EN ISO9227, runned in house showing the major benefits of Zn/Ni coating versus actual CrIII passivation technology.  PICTURE SEQUENCE 1 It shows the evolution in time, before red rust occurrence, of non-stressed parts. 200 HOURS 450 HOURS 800 HOURS 1000 HOURS CrIII Zn/Ni CrIII Zn/Ni Zn/Ni Zn/Ni  PICTURE SEQUENCE 2 It shows the evolution in time, before red rust occurrence, of non-swaged ferrules. 200 HOURS 450 HOURS 600 HOURS 1000 HOURS CrIII Zn/Ni CrIII Zn/Ni Zn/Ni Zn/Ni 3  PICTURE SEQUENCE 3 It shows the evolution in time, before red rust occurrence, of swaged ferrules. The sequence shows the benefit of the top coating on stressed parts. 120 HOURS 350 HOURS 600 HOURS CrIII Zn/Ni CrIII Zn/Ni Zn/Ni 4 3. -
Identification and Laboratory Assessment of Best Practices to Protect DOT Equipment from the Corrosive Effect of Chemical Deicers
Identification and Laboratory Assessment of Best Practices to Protect DOT Equipment from the Corrosive Effect of Chemical Deicers Item Type Report Authors Shi, Xianming; Li, Yongxin; Jungwirth, Scott; Fang, Yida; Seeley, Nicholas; Jackson, Emily Publisher Alaska University Transportation Center Download date 05/10/2021 16:29:36 Link to Item http://hdl.handle.net/11122/7506 Identification and Laboratory Assessment of Best Practices to Protect DOT Equipment Alaska University Transportation Center Transportation Alaska University from the Corrosive Effect of Chemical Deicers Prepared By: Xianming Shi, Yongxin Li, Scott Jungwirth, Yida Fang, Nicholas Seeley, Emily Jackson March 2013 Prepared For: Alaska University Transportation Center Duckering Building Room 245 P.O. Box 755900 Fairbanks, AK 99775-5900 INE/AUTC 12.35 Form approved OMB No. REPORT DOCUMENTATION PAGE Public reporting for this collection of information is estimated to average 1 hour per response, including the time for reviewing instructions, searching existing data sources, gathering and maintaining the data needed, and completing and reviewing the collection of information. Send comments regarding this burden estimate or any other aspect of this collection of information, including suggestion for reducing this burden to Washington Headquarters Services, Directorate for Information Operations and Reports, 1215 Jefferson Davis Highway, Suite 1204, Arlington, VA 22202-4302, and to the Office of Management and Budget, Paperwork Reduction Project (0704-1833), Washington, DC 20503 1. AGENCY USE ONLY (LEAVE BLANK) 2. REPORT DATE 3. REPORT TYPE AND DATES COVERED FHWA-WA-RD 796.1 December 2012 Final Report (01/11/2011-12/31/2012) 4. TITLE AND SUBTITLE 5. FUNDING NUMBERS Identification and Laboratory Assessment of Best Practices to Protect AUTC# 410005 DOT Equipment from the Corrosive Effect of Chemical Deicers DTRT06-G-0011 6. -
SCHNORR® Product Range
SCHNORR® Product range Disc springs Bolt locking systems DISC SPRING ENGINEERING Grown competence DISC SPRING ENGINEERING for highest precision. Adolf Schnorr, who founded our business in 1908, showed true pioneering spirit and his inventiveness laid the foundation for our success. Today, SCHNORR® has grown to be- come an internationally leading company in the field of disc springs and bolt locking systems. The constructive and economic solutions offered by SCHNORR® accrue from long- term experience, reliability and high de- mands on perfection and quality. SCHNORR® is a proven partner for renowned industrial companies, whether it be the automotive industry, machine construction and plant engineering, or for the aerospace industry. Certified acc. to ISO/TS 16949-2002 Original SCHNORR® disc springs SCHNORR® disc springs Page 4 Disc spring dimension tables Standard materials (spring steel) Page 11 Page 16 ® disc springs Material grade 1.4310 (X10 CrNi 18-8); rust-resistant Content SCHNORR® bearing preload springs Page 20 CHNORR Bearing preload springs “K“ dimension tables Bearing preload springs “K“ (non-slotted springs) Page 21 riginal S O Bearing preload springs “K“ (slotted springs) Page 23 SCHNORR® Engineering Page 24 Customized solutions Original SCHNORR® bolt locking systems SCHNORR® safety washers Page 26 Safety washers dimension tables Standard safety washers type “S“ Page 29 Extra strong safety washers type “VS“ Page 31 Captive safety washers type “UV“ Page 32 ® bolt locking systems SCHNORR® load washers Page 33 CHNORR Load washer dimension tables Load washers according to DIN 6796 Page 34 riginal S O High-stress load washers type “HS” Page 35 Material types and surface protection Material types Page 36 Materials overview table Page 38 Surface protection Page 40 Material types and surfaceMaterial protection 2 • 3 2 - 3 . -
Scanned by Camscanner
Scanned by CamScanner Scanned by CamScanner Scanned by CamScanner Scanned by CamScanner Scanned by CamScanner Scanned by CamScanner Scanned by CamScanner Scanned by CamScanner Scanned by CamScanner Scanned by CamScanner EXPERIMENTAL ANALYSIS ON FAILURE OF STEERING WHEELS CHAPTER 1: INTRODUCTION A controlling wheel is additionally called as a driving wheel or hand haggle is a kind of directing control in all vehicles and vessels ships and pontoons. Directing wheels are utilized in nearly of all the cutting edge vehicles, including all the large scale manufacturing autos and transports, light and substantial trucks and tractors. The controlling wheels is the piece of the directing framework, which is controlled by the driver to the remainder of the guiding framework reacts to such driver inputs. This can be through the direct mechanical contact as a recycling ball or rack and pinion guiding apparatus, with or without the help of the water driven power guiding, HPS or in a portion of the cutting edge generation autos with help of PC controlled engines which are known as Electric Power Steering. Close to the beginning of the eighteenth century, an enormous number of ocean vessels showed up as the ship's wheel structure, yet students of history are misty that the way to deal with guiding wheel was first utilized. The main vehicles were controlled with a tiller, yet in 1894 Alfred Vacheron partook in the Paris–Rouen race with a Panhard 4 hp model which he had fitted with a guiding wheel. That is accepted to be one of the most punctual jobs of guideline. -
(A2LA Cert. No. 0098.11 (Formerly 0038.01)) 03/04/2021 Page 1 of 18 Test Technology Range Reference Standard
SCOPE OF ACCREDITATION TO ISO/IEC 17025:2017 ELEMENT MATERIALS TECHNOLOGY DETROIT - WARREN 11 MILE 27485 George Merrelli Drive Warren, MI 48092 Stephen Karrer Phone: 586 754 9000 ext. 32900 Email: [email protected] MECHANICAL Valid To: December 31, 2022 Certificate Number: 0098.11 In recognition of the successful completion of the A2LA evaluation process, accreditation is granted to this laboratory at the location above as well as the two satellite laboratory locations listed below to perform the following tests: Mechanical Tests: Tensile/Elongation; Hardness (Durometer and Rockwell); Compression; Impact (Izod, Charpy, and GM9300P); Strength at Room and High Temperatures; Shear Strength; Physical Properties Following Fluid Exposure; Hoses and Tubing; Tear Strength Using Tongue, and Trapezoid Methods; Filler, Glass, Carbon Black Content; Volume Change; Specific Gravity and Density; Cleanability; Dimensional Stability; Water Absorption; Melt Flow/Index; Migration and Contact Staining; Flammability; Compression Set; Low-Temperature Brittleness; Deflection Temperature; On Plastics, Rubber, Elastomer, Composite, Paper/Paperboard, Construction Elements, and Textile Products. Environmental Simulation Tests: Weatherometer (Xenon); Sunlamp and QUV Exposure; Fadometer; Ozone Resistance; Fogging; Salt Spray; CASS; Humidity; Condensing; Crocking; Water Immersion; Taber Abrasion; Gravelometer; Specular Gloss; Luminous Transmittance; Chromaticity; Color Reading; Corrodokote; Oil/Gas Immersion Solvent and Detergent Resistance; Thermal Shock; -
NCHRP Report 577 – Guidelines for the Selection of Snow and Ice
NATIONAL COOPERATIVE HIGHWAY RESEARCH NCHRP PROGRAM REPORT 577 Guidelines for the Selection of Snow and Ice Control Materials to Mitigate Environmental Impacts TRANSPORTATION RESEARCH BOARD 2007 EXECUTIVE COMMITTEE* OFFICERS CHAIR: Linda S. Watson, CEO, LYNX–Central Florida Regional Transportation Authority, Orlando VICE CHAIR: Carol A. Murray, Commissioner, New Hampshire DOT, Concord EXECUTIVE DIRECTOR: Robert E. Skinner, Jr., Transportation Research Board MEMBERS J. Barry Barker, Executive Director, Transit Authority of River City, Louisville, KY Michael W. Behrens, Executive Director, Texas DOT, Austin Allen D. Biehler, Secretary, Pennsylvania DOT, Harrisburg John D. Bowe, President, Americas Region, APL Limited, Oakland, CA Larry L. Brown, Sr., Executive Director, Mississippi DOT, Jackson Deborah H. Butler, Vice President, Customer Service, Norfolk Southern Corporation and Subsidiaries, Atlanta, GA Anne P. Canby, President, Surface Transportation Policy Partnership, Washington, DC Nicholas J. Garber, Henry L. Kinnier Professor, Department of Civil Engineering, University of Virginia, Charlottesville Angela Gittens, Vice President, Airport Business Services, HNTB Corporation, Miami, FL Susan Hanson, Landry University Professor of Geography, Graduate School of Geography, Clark University, Worcester, MA Adib K. Kanafani, Cahill Professor of Civil Engineering, University of California, Berkeley Harold E. Linnenkohl, Commissioner, Georgia DOT, Atlanta Michael D. Meyer, Professor, School of Civil and Environmental Engineering, Georgia Institute -
The Role of Coatings in the Prevention of Mechanical Failures
NATL INST OF ||||||| ^ A1 11 03088706 Mechanical Failures/The role of coat^^^^^ NBS-PUB-l^ 1» QC100 .U57 N0.452, 1976 C.2 Q NBS SPECIAL PUBLICATION 452 U.S. DEPARTMENT OF COMMERCE / National Bureau of Standards The Role of Coatings in the Prevention of Mechanical Failures MFPG 23rd Meeting NATIONAL BUREAU OF STANDARDS The National Bureau of Standards' was established by an act of Congress March 3, 1901. The Bureau's overall goal is to strengthen and advance the Nation's science and technology and facilitate their efTective application for public benefit. To this end, the Bureau conducts research and provides: {!) a basis for the Nation's physical measurement system, (2) scientific and technological services for industry and government, O) a technical basis for equity in trade, and (4) technical services to promote public safety. The Bureau consists of the Institute for Basic Standards, the Institute for Materials Research, the Institute for Applied Technology, the Institute for Computer Sciences and Technology, and the Office for Information Programs. THE INSTITUTE FOR BASIC STANDARDS provides the central basis within the United States of a complete and consistent system of physical measurement; coordinates that system with measurement systems of other nations; and furnishes essential services leading to accurate and uniform physical measurements throughout the Nation's scientific community, industry, and commerce. The Institute consists of the Office of Measurement Services, the Office of Radiation Measurement and the following Center