Applicability and Limitations of 3D Printing for Civil Structures Mostafa Yossef Iowa State University, [email protected]
Total Page:16
File Type:pdf, Size:1020Kb
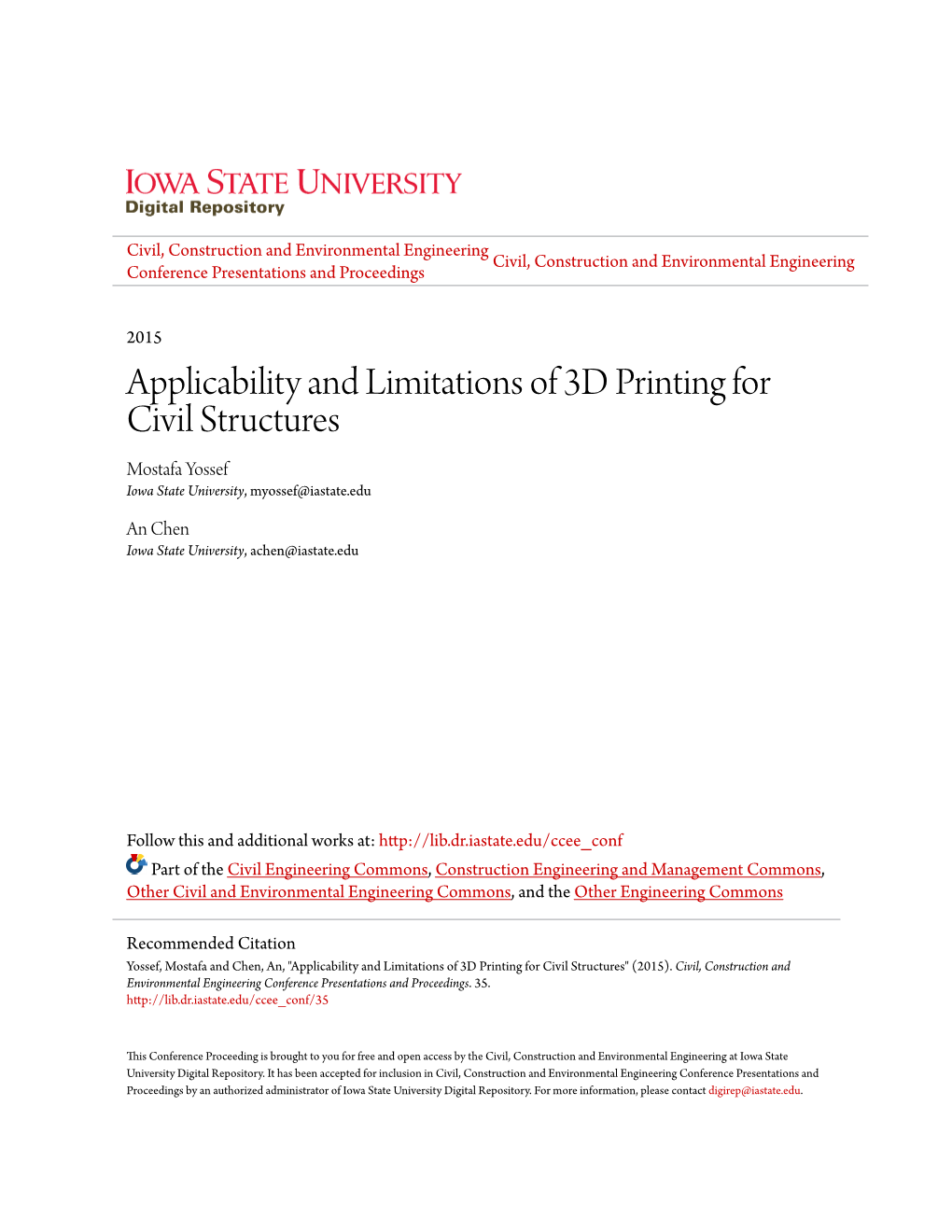
Load more
Recommended publications
-
3D Printing of Concrete Structures
Eindhoven University of Technology MASTER 3D printing of concrete structures Wolfs, Rob Award date: 2015 Link to publication Disclaimer This document contains a student thesis (bachelor's or master's), as authored by a student at Eindhoven University of Technology. Student theses are made available in the TU/e repository upon obtaining the required degree. The grade received is not published on the document as presented in the repository. The required complexity or quality of research of student theses may vary by program, and the required minimum study period may vary in duration. General rights Copyright and moral rights for the publications made accessible in the public portal are retained by the authors and/or other copyright owners and it is a condition of accessing publications that users recognise and abide by the legal requirements associated with these rights. • Users may download and print one copy of any publication from the public portal for the purpose of private study or research. • You may not further distribute the material or use it for any profit-making activity or commercial gain 3D PRINTING OF CONCRETE STRUCTURES GRADUATION THESIS R.J.M. Wolfs Eindhoven University of Technology Department of the Built Environment Master Architecture, Building and Planning Specialization Structural Design Title: 3D PRINTING OF CONCRETE STRUCTURES Report number: A-2015.85 Version: 1.0 Date: February 2015 Student: R.J.M. (Rob) Wolfs ID-number: 0675429 Email: [email protected] [email protected] Graduation committee: Prof. Dr. Ir. T.A.M. Salet 1 (Chairman) Dr. Dipl.–Ing. J. Beetz 1 Dr.-Ing. -
Paste Deposition Modelling, Deconstructing the Additive Manufacturing Process: Development of Novel Multi- Material Tools and Techniques for Craft Practitioners
PASTE DEPOSITION MODELLING, DECONSTRUCTING THE ADDITIVE MANUFACTURING PROCESS: DEVELOPMENT OF NOVEL MULTI- MATERIAL TOOLS AND TECHNIQUES FOR CRAFT PRACTITIONERS A thesis submitted for the degree of Doctor of Philosophy by Esteban Schunemann Department of Engineering and Design, Brunel University London 2015 ii I. Abstract A novel paste deposition process was developed to widen the range of possible materials and applications. This experimental process developed an increasingly complex series of additive manufacturing machines, resulting in new combinations of novel materials and deposition paths without sacrificing many of the design freedoms inherit in the craft process. The investigation made use of open-source software together with an approach to programming user originated infill geometries to form structural parts, differing from the somewhat automated processing by 'closed' commercial RP systems. A series of experimental trials were conducted to test a range of candidate materials and machines which might be suitable for the PDM process. The combination of process and materials were trailed and validated using a series of themed case studies including medical, food industry and jewellery. Some of the object created great interest and even, in the case of the jewellery items, won awards. Further evidence of the commercial validity was evidenced through a collaborative partnership resulting in the development of a commercial version of the experimental system called Newton3D. A number of exciting potential future directions having been opened up by this project including silicone fabrics, bio material deposition and inclusive software development for user originated infills and structures. iii II. Acknowledgments First and foremost I would like to extend my deepest gratitude to both my supervisors, Dr. -
Global Risks Report 2017 12Th Edition
Strategic Partner of the Report The Global Risks Report 2017 12th Edition Strategic Partners Marsh & McLennan Companies Zurich Insurance Group Academic Advisers National University of Singapore Oxford Martin School, University of Oxford Wharton Risk Management and Decision Processes Center, University of Pennsylvania Contents 4 Preface By Klaus Schwab 5 Foreword 6 Executive Summary 8 Introduction 10 Part 1: Global Risks 2017 – Economy: Growth and Reform – Society: Rebuilding Communities – Technology: Managing Disruption – Geopolitics: Strengthening Cooperation – Environment: Accelerating Action 22 Part 2: Social and Political Challenges 23 2.1 Western Democracy in Crisis? 29 2.2 Fraying Rule of Law and Declining Civic Freedoms: Citizens and Civic Space at Risk 35 2.3 The Future of Social Protection Systems 42 Part 3: Emerging Technologies 43 3.1 Understanding the Technology Risk Landscape 48 3.2 Assessing the Risk of Artificial Intelligence 53 3.3 Physical Infrastructure Networks and the Fourth Industrial Revolution 58 Conclusion 60 Appendices Appendix A: Description of Global Risks, Trends and Emerging Technologies 2017 Appendix B: Global Risks Perception Survey 2016 and Methodology 68 Acknowledgements As in previous years, the analysis contained in this Report builds on the Preface annual Global Risks Perception Survey, completed by almost 750 members of the World Economic Forum’s global multistakeholder community. The year 2017 will present a pivotal moment for the global community. The threat of a less cooperative, more inward-looking world also creates the opportunity to address global risks and the trends that drive them. This will require responsive and responsible leadership with a deeper commitment to inclusive development and equitable growth, both nationally and globally. -
A Study on 3D Printing and Its Effects on the Future of Transportation
CAIT-UTC-NC19 A Study on 3D Printing and its Effects on the Future of Transportation September 2018 Submitted by: Omar Jumaah, Doctoral Candidate Department of Mechanical and Aerospace Engineering Rutgers, The State University of New Jersey 98 Brett Road Piscataway, NJ 08854-8058 [email protected] External Project Manager Patrick Szary, PhD Associate Director, CAIT Central Administration Rutgers, The State University of New Jersey 100 Brett Road Piscataway, NJ 08854-8058 [email protected] In cooperation with Rutgers, The State University of New Jersey & State of Department of Transportation & U.S. Department of Transportation Federal Highway Administration i Disclaimer Statement The contents of this report reflect the views of the authors, who are responsible for the facts and the accuracy of the information presented herein. This document is disseminated under the sponsorship of the Department of Transportation, University Transportation Centers Program, in the interest of information exchange. The U.S. Government assumes no liability for the contents or use thereof. The Center for Advanced Infrastructure and Transportation (CAIT) is a National UTC Consortium led by Rutgers, The State University. Members of the consortium are the University of Delaware, Utah State University, Columbia University, New Jersey Institute of Technology, Princeton University, University of Texas at El Paso, Virginia Polytechnic Institute, and University of South Florida. The Center is funded by the U.S. Department of Transportation. ii CAIT-UTC-NC19 1. Report No. 2. Government Accession No. 3. Recipient’s Catalog No. CAIT-UTC-NC19 4. Title and Subtitle 5. Report Date A Study on 3D Printing and its Effects on the Future of Transportation September 2018 6. -
Strategies for Adopting Additive Manufacturing Technology Into Business Models Robert Martens Walden University
Walden University ScholarWorks Walden Dissertations and Doctoral Studies Walden Dissertations and Doctoral Studies Collection 2018 Strategies for Adopting Additive Manufacturing Technology Into Business Models Robert Martens Walden University Follow this and additional works at: https://scholarworks.waldenu.edu/dissertations Part of the Business Commons This Dissertation is brought to you for free and open access by the Walden Dissertations and Doctoral Studies Collection at ScholarWorks. It has been accepted for inclusion in Walden Dissertations and Doctoral Studies by an authorized administrator of ScholarWorks. For more information, please contact [email protected]. Walden University College of Management and Technology This is to certify that the doctoral study by Robert Martens has been found to be complete and satisfactory in all respects, and that any and all revisions required by the review committee have been made. Review Committee Dr. Susan Fan, Committee Chairperson, Doctor of Business Administration Faculty Dr. Charles Needham, Committee Member, Doctor of Business Administration Faculty Dr. Lisa Kangas, University Reviewer, Doctor of Business Administration Faculty Chief Academic Officer Eric Riedel, Ph.D. Walden University 2018 Abstract Strategies for Adopting Additive Manufacturing Technology Into Business Models by Robert Martens MS, University of Glamorgan, 2007 MBA, Keele University, 2006 Doctoral Study Submitted in Partial Fulfillment of the Requirements for the Degree of Doctor of Business Administration Walden University August 2018 Abstract Additive manufacturing (AM), also called 3-dimensional printing (3DP), emerged as a disruptive technology affecting multiple organizations’ business models and supply chains and endangering incumbents’ financial health, or even rendering them obsolete. The world market for products created by AM has increased more than 25% year over year. -
MMM 272 February2014
MMM #272 Since December 1986 FEBRUARY 2014 p 1 Soon many people will be able to fly to the edge of space. As prices drop, this will be but the beginning. Day flights and night flights, aurora flights, full moon flights; milky way flights. Further down the road are flights via the edge of space to especially attractive intercontinental destinations: Hong Kong, CapeTown, Rio de Janeiro, Dubai etc. Feature Articles 1 In Focus: Creating a Manufacturing “Beachhead” on the Moon, Peter Kokh 5 Growing “Start-up” Industries on the Moon, Dave Dietzler 6 “Backing up” our Civilization, Peter Kokh Left: Station at L1 -------- Right: archives of human civilization in a lunar lavatube For past articles, Visit http://www.moonsociety.org/publications/mmm_classics/ or /mmm_themes/ MMM #272 Since December 1986 FEBRUARY 2014 p 2 About Moon Miners’ Manifesto - “The Moon - it’s not Earth, but it’s Earth’s!” • MMM’s VISION: “expanding the human economy through of-planet resources”; early heavy reliance on Lunar materials; early use of Mars system and asteroid resources; and permanent settlements supporting this economy. • MMM’s MISSION: to encourage “spin-up” entrepreneurial development of the novel technologies needed and promote the economic-environmental rationale of space and lunar settlement. • Moon Miners’ Manifesto CLASSICS: The non-time-sensitive articles and editorials of MMM’s first twenty years plus have been re-edited, reillustrated, and republished in 23 PDF format volumes, for free downloading from this location: http://www.MoonSociety.org/publications/mmm_classics/ • MMM THEME Issues: 14 collections of articles according to themes: ..../publications/mmm_themes/ • MMM Glossary: new terms, old terms/new meanings: www.moonsociety.org/publications/m3glossary.html • MMM retains its editorial independence and serves many groups, each with its own philosophy, agenda, and programs. -
Wef 2019-20 Admitted Batch
REGULATIONS AND SYLLABUS of B.Tech (Mechanical Engineering) (w.e.f 2019-20 admitted batch) VISAKAPATNAM-530 045 www.gitam.edu A University Committed to Excellence B. Tech. in Mechanical Engineering REGULATIONS (w.e.f. 2019-20 admitted batches) 1. ADMISSION 1.1 Admission into B. Tech. in Mechanical Engineering program of GITAM (Deemed to be University) is governed by GITAM admission regulations. 2. ELIGIBILITY CRITERIA 2.1 A first class in 10+2 or equivalent examination approved by GITAM (Deemed to be University) with subjects Physics, Chemistry and Mathematics. 2.2 Admission into B.Tech. will be based on an All India Entrance Test (GITAM Admission Test - GAT) conducted by GITAM/Specified rank holders of JEE mains/EAMCET(AP & TS) and the rules of reservation of statutory bodies, wherever applicable, will be followed. 3. CHOICE BASED CREDIT SYSTEM 3.1 Choice Based Credit System (CBCS) was introduced with effect from the academic year of 2015-16 admitted batch and revised in 2019-2020 academic year, based on guidelines of the statutory bodies in order to promote: o Activity based learning o Student centered learning o Cafeteria approach o Students to choose courses of their choice o Learning at their own pace o Interdisciplinary learning 3.2 Course Objectives, Learning Outcomes and Course Outcomes are specified, focusing on what a student should be able to do at the end of the course and program. 4. STRUCTURE OF THE PROGRAM 4.1 The Program consists of humanities and social sciences, basic sciences, basic engineering, program core, program electives, open electives, interdisciplinary electives, industry internship, laboratory, mandatory courses and project work. -
Challenges Ahead! a Manufacturer’S Perspective Dr
Challenges Ahead! A Manufacturer’s Perspective Dr. Ziya Haktan Karadeniz Dr. Macit Toksoy, General Coordinator Assistant Professor ENECO A.Ş İzmir Katip Çelebi University Çiğli / İzmir, Turkey Çiğli / İzmir, Turkey HVAC sector challenges ahead us REHVA Seminar – REHVA Annual Meeting 2017, 2-4 April 2017, London, UK 3D printingc of c HVAC Components, c Units c & c Systems c CONTENT • Integrated Building Design in the Greco-Roman World • Trends, Innovations, Research & Development That Will Change HVAC future • Additive Manufacturing (3D Printing) Technology and HVAC: • 3D Components Manufacturing • 3D Equipments Manufacturing • Integrated Design and 3D Building Construction 3D CM - 3D EM - 3D BC Fully Integrated Solutions: Hypocaust – Hypocaustum Roman Bath and Sanitary System Ondol Korean Cooking and Underfloor Heating Systems Arcadian Street, Ephesus EPHESUS Library of Celcius (Celsus) Ephesus Latrines (Public Toilets) A hypocaust (Latin hypocaustum) Roman villa (Caen, France) A Futuristic Surf // 21 SOURCES (2014 – 2016) (web sources on Innovations and trends That Will Change HVAC future DOE BTO Reports - ORNL Report – NERL Report – Papers) NON - VAPOUR- 1 ADV.VAPOUR COMP. TECH. UD 10 EDUCATION 19 COMPRESSION 2 AIR FILTRATION 11 ENERGY RECOVERY 20 RECYCLING OF MATERIAL 3 ALTERNATIVE ENERGY 12 ENERGY STORAGE 21 REGULATIONS 4 BIM 13 INSULATION 22 SIMULATION TOOLS SMART EQUIPMENT and 5 BUSINESS MODEL 14 INT. DES. - BUILDING ENVELOPE 23 SYSTEMS SMART SALES and 6 CLIMATE SPESIFIC HVAC 15 INTEGRATED A/C TECH. 24 MAINTENANCE 7 CONTROL 16 INTEGRATED BUILDING DESIGN 25 SYSTEM MIX SYSTEM (COMP and NON- 8 DESIGN MODELING 17 COMP) 9 MULTIPLE ENERGY SOURCES 18 MOBILE PERSONEL SYSTEM 1 ADV.VAPOUR COMP. TECH. -
Additive Manufacturing Applications for Industry 4.0: a Systematic Critical Review
buildings Review Additive Manufacturing Applications for Industry 4.0: A Systematic Critical Review Samad M. E. Sepasgozar 1,* , Anqi Shi 1, Liming Yang 1 , Sara Shirowzhan 1 and David J. Edwards 2 1 Faculty of Built Environment, University of New South Wales, Sydney, NSW 2052, Australia; [email protected] (A.S.); [email protected] (L.Y.); [email protected] (S.S.) 2 School of Engineering and the Built Environment, Birmingham City University, Birmingham B5 5JU, UK; [email protected] * Correspondence: [email protected] Received: 29 October 2020; Accepted: 24 November 2020; Published: 6 December 2020 Abstract: Additive manufacturing, including 3D printing (3DP), is one of the critical pillars of Industry 4.0 and the next construction revolution. Several countries, including China, have utilized 3DP on larger scales or real projects. However, reviews of the lessons learned from previous large-sized practices of 3DP utilization are scarce. This paper presents a few practical applications of implementing 3DP over the past decade and suggests a direction for future research work. Recent publications on 3DP practices are systematically reviewed using an interpretivist philosophical lens, and more specifically, the nozzle characteristics are focused upon. The Scopus and China National Knowledge Infrastructure (CNKI) journal databases are utilized, resulting in the examination of 54 English and 62 Chinese papers. The selected practices from Mainland China, Hong Kong, Taiwan and Macao are considered for this review. A content critical review approach is adopted, and the identified papers are critically reviewed. These papers reported key challenges and advantages from their reported practices, such as limitations in aggregate sizes, nozzle sizes, standards, post-occupancy satisfaction, final product quality, productivity challenges and other associated risks. -
Accepted Manuscript
ACCEPTED MANUSCRIPT Title: APPLICATION OF 3D PRINTING TECHNOLOGY FOR MECHANICAL PROPERTIES STUDY OF THE PHOTOPOLYMER RESIN USED TO PRINT POROUS STRUCTURES Authors: Ewelina Małek, Danuta Miedzińska, Arkadiusz Popławski, Wiesław Szymczyk To appear in: Technical Sciences Received 10 June 2018; Accepted 11 June 2019; Available online 14 June 2019. This is a PDF file of an unedited manuscript that has been accepted for publication. As a service to our customers we are providing this early version of the manuscript. The manuscript will undergo copyediting, typesetting, and review of the resulting proof before it is published in its final form. Please note that during the production process errors may be discovered which could affect the content, and all legal disclaimers that apply to the journal pertain. APPLICATION OF 3D PRINTING TECHNOLOGY FOR MECHANICAL PROPERTIES STUDY OF THE PHOTOPOLYMER RESIN USED TO PRINT POROUS STRUCTURES Ewelina Małek1*, Danuta Miedzińska1, Arkadiusz Popławski1, Wiesław Szymczyk1 1Military University of Technology, Faculty of Mechanical Engineering, Kaliskiego 2 St, 00-908 Warsaw, Poland *corresponding author: [email protected] Abstract In the field of numerical research there are various approaches and methods for structures of porous materials modeling. The solution is the use of fractal models to develop the porous structure. In the case of modeling the geometry of natural (random) materials, there is a problem of compatibility of the FE model geometry and real one. This is a source of differences between the results of calculations and experimental ones. Application of 3D printing technology will allow to receive a real structure in a controlled manner, which exactly reflects the designed structure and is consistent with the geometry of the numerical model. -
Automated Additive Construction (AAC) for Earth and Space Using In-Situ Resources
Automated Additive Construction (AAC) for Earth and Space Using In-situ Resources Robert P. Mueller1, Scott Howe2*, Dennis Kochmann3, Hisham Ali4, Christian Andersen5, Hayden Burgoyne6, Wesley Chambers7, Raymond Clinton8, Xavier De Kestellier9, Keye Ebelt10, Shai Gerner11, Douglas Hofmann12, Kristina Hogstrom13, Erika Ilves14, Alex Jerves15, Ryan Keenan16, Jim Keravala17, Behrokh Khoshnevis18, Sungwoo Lim19, Philip Metzger20, Lucas Meza21, Takashi Nakamura22, Andrew Nelson23, Harry Partridge24, Donald Pettit25, Rod Pyle26, Eric Reiners27, Andrew Shapiro28, Russell Singer29, Wei-Lin Tan30, Noel Vazquez31, Brian Wilcox32, Alex Zelhofer33 1 Team Lead, NASA Kennedy Space Center; 2 Team Lead, Jet Propulsion Laboratory; 3 Team Lead, California Institute of Technology; 4 Georgia Institute of Technology; 5 Pacific International Space Center for Exploration Systems (PISCES); 6 California Institute of Technology ; 7 University of Central Florida; 8 NASA Marshall Space Flight Center; 9 Foster + Partners; 10 National Science Foundation; 11 University of Pennsylvania; 12 Jet Propulsion Laboratory; 13 California Institute of Technology; 14 Shackleton Energy Company; 15 California Institute of Technology; 16 California Polytechnic University Pomona; 17 Shackleton Energy Company; 18 University of Southern California; 19 The Open University; 20 University of Central Florida; 21 California Institute of Technology; 22 Physical Sciences Inc; 23 US Army Corps of Engineers; 24 NASA Ames Research Center; 25 NASA Johnson Space Center; 26 California Institute of Technology; 27 Caterpillar, Inc; 28 Jet Propulsion Laboratory; 29 Pasadena Art Center; 30 California Institute of Technology; 31 California Polytechnic University Pomona; 32 Jet Propulsion Laboratory; 33 California Institute of Technology. * Correspondence should be addressed to E-mail: [email protected] Team leads are listed first, then all authors are listed in alphabetical order, contributing to the work equally. -
Application and Research on Building 3D Printing
Journal of Critical Reviews ISSN- 2394-5125 Vol 7, Issue 12, 2020 APPLICATION AND RESEARCH ON BUILDING 3D PRINTING WENJIE LUO1*, XINCHEN MA1 ,JIAN YIN2 1 Department of Architecture and Civil Engineering, City University of Hong Kong, Hong Kong, 999077, China 2 School of Civil Engineering, Henan Polytechnic University, Henan, 454003, China Corresponding author’s e-mail: [email protected] Received: 11.03.2020 Revised: 12.04.2020 Accepted: 13.05.2020 Abstract As a novel category of green construction method, Building 3D Printing has the advantages of material saving, energy-saving, time-saving and customization. Nevertheless, this technology still cannot suffice the practical requirements of large-scale production in the construction industry, and it requires further exploration and research in printing equipment and materials, supportive software, evaluation standards and other aspects. Hence, this paper starts with the introduction of 3D Printing in industrial manufacturing, expounds the classification of 3D Printing in the construction field and the research status, introduces the technical process of Concrete Printing within the Building 3D Printing, printing equipment and software concerned, eventually analyze the existing problems and look forward to the prospective development. Keywords: Additive Manufacturing; 3D Printing; green construction; Concrete Printing; research status © 2020 by Advance Scientific Research. This is an open-access article under the CC BY license (http://creativecommons.org/licenses/by/4.0/) DOI: http://dx.doi.org/10.31838/jcr.07.12.103 INTRODUCTION German Photonics Research Plan, which included financial The manufacturing technology employing Computer support for the research and development of 3D Printing Numerical Control (CNC) is also known as Subtractive technology [3].