Pultrusion Exotherm Study Gauge Sensitivity and Application To
Total Page:16
File Type:pdf, Size:1020Kb
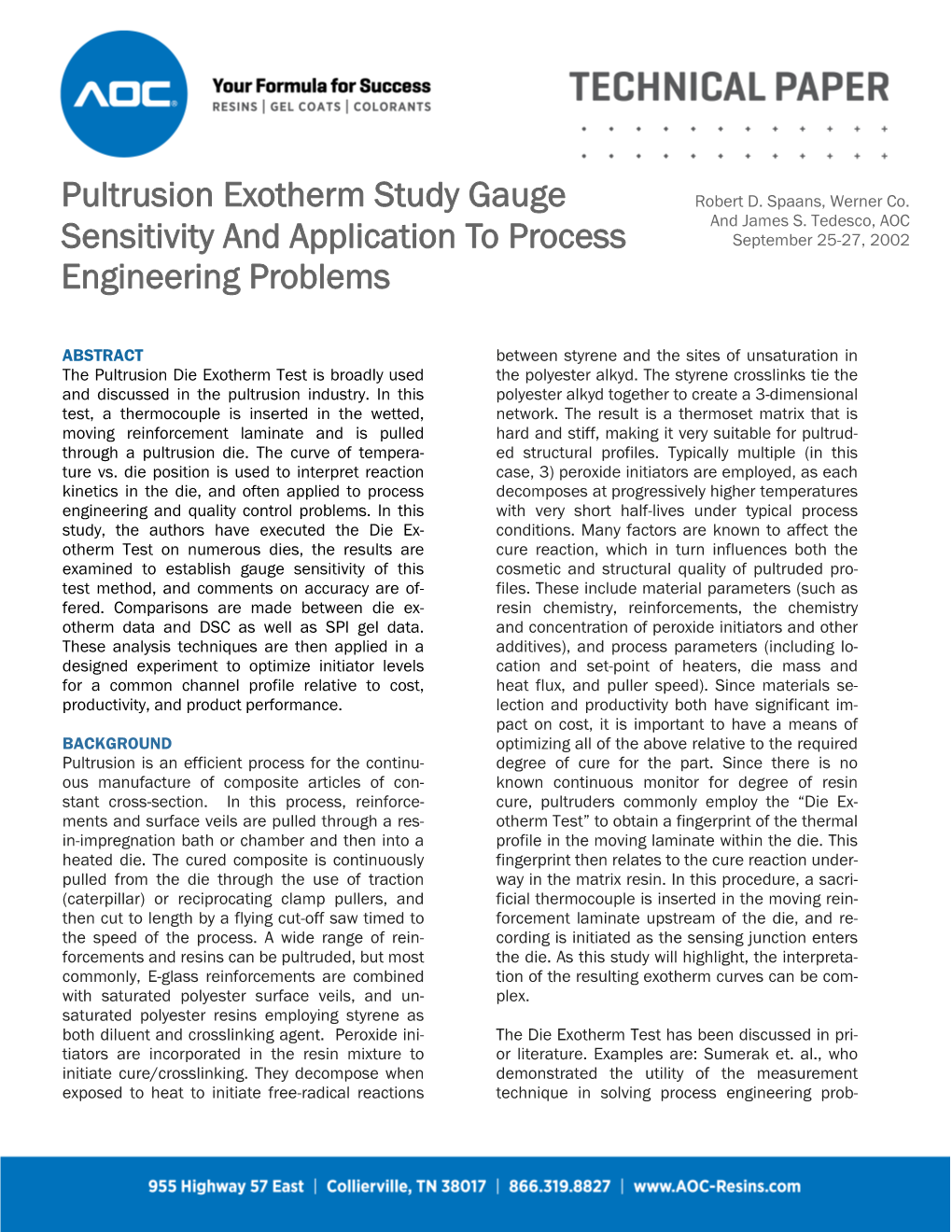
Load more
Recommended publications
-
Coupled Glass-Fiber Reinforced Polyoxymethylene Gekoppeltes Glasfaserverstärktes Polyoxymethylen Polyoxyméthylène Renforcé Par Fibre De Verre Couplée
(19) TZZ ZZ__T (11) EP 2 652 001 B1 (12) EUROPEAN PATENT SPECIFICATION (45) Date of publication and mention (51) Int Cl.: of the grant of the patent: C08G 18/56 (2006.01) C08G 18/76 (2006.01) 26.12.2018 Bulletin 2018/52 C08K 7/14 (2006.01) C08J 5/04 (2006.01) (21) Application number: 11769886.0 (86) International application number: PCT/EP2011/067992 (22) Date of filing: 14.10.2011 (87) International publication number: WO 2012/049293 (19.04.2012 Gazette 2012/16) (54) COUPLED GLASS-FIBER REINFORCED POLYOXYMETHYLENE GEKOPPELTES GLASFASERVERSTÄRKTES POLYOXYMETHYLEN POLYOXYMÉTHYLÈNE RENFORCÉ PAR FIBRE DE VERRE COUPLÉE (84) Designated Contracting States: (74) Representative: Lahrtz, Fritz et al AL AT BE BG CH CY CZ DE DK EE ES FI FR GB Isenbruck Bösl Hörschler LLP GR HR HU IE IS IT LI LT LU LV MC MK MT NL NO Patentanwälte PL PT RO RS SE SI SK SM TR Prinzregentenstrasse 68 81675 München (DE) (30) Priority: 14.10.2010 EP 10187614 (56) References cited: (43) Date of publication of application: EP-A1- 1 630 198 WO-A1-2006/105918 23.10.2013 Bulletin 2013/43 DE-A1- 2 162 345 US-A1- 2005 107 513 (73) Proprietor: Celanese Sales Germany GmbH • DATABASE WPI Week 201025 Thomson 65843 Sulzbach (DE) Scientific, London, GB; AN 2010-D80494 XP002615422, -& WO 2010/035351 A1 (72) Inventors: (POLYPLASTICS KK) 1 April 2010 (2010-04-01) • MARKGRAF, Kirsten • K. KAWAGUCHI, E. MASUDA, Y. TAJIMA: 69469 Weinheim (DE) "Tensile Behavior of Glass-Fiber-Filled • LARSON, Lowell Polyacetal: Influence of the Functional Groups of Independence, KY 41051 (US) Polymer Matrices", JOURNAL OF APPLIED POLYMER SCIENCE, vol. -
Fiber Reinforced Polymer (FRP) Composites
Fiber Reinforced Polymer (FRP) Composites Gevin McDaniel, P.E. Roadway Design Standards Administrator & Chase Knight, PhD Composite Materials Research Specialist Topics Covered Overview of FRP Composites Currently Available National Specifications FDOT Design Criteria and Specifications Acceptable FDOT Applications Research on FRP Composites District 7 Demonstration Project Chase Knight, PhD - Usage (Characteristics/Durability) Questions 2 FRP Overview: What is FRP? General Composition Carbon, Glass, Etc. Polymer 3 FRP Overview: Fibers Common Fiber Types: Aramid - Extremely sensitive to environmental conditions Glass (Most Widely Used) - Subject to creep under high sustained loading - Subject to degradation in alkaline environment Carbon - Premium Cost Basalt - The future of FRP fibers? 4 FRP Overview: Fibers Used in many different forms: Short Fibers Chopped Fibers Long Fibers Woven Fibers 5 FRP Overview: Resins Two Categories: Thermoset Resins (most common for structural uses) - Liquid state at room temperature prior to curing - Impregnated into reinforcing fibers prior to heating - Chemical reaction occurs during heating/curing - Solid after heating/curing; Can’t be reversed/reformed Thermoplastic Resins - Solid at room temperature (recycled plastic pellets) - Heated to liquid state and pressurized to impregnate reinforcing fibers - Cooled under pressure; Can be reversed/reformed 6 FRP Overview: Resins Common Thermoset Resin Types Polyester - Lowest Cost Vinyl ester - Industry Standard Polyurethane - Premium Cost -
CV TJH January 2021
Arrabon Technologies Limited Dr Trevor J. Hutley MBA Global Polymer Industry Consultant Research & Innovation Advisor Technical & Management Consultant Experience Summary A career polymer and petrochemical industry specialist with global experience in many pioneering and complex situations. An unusual combination of broad and deep technology and science knowledge; an understanding of intellectual property; combined with finance, marketing, manufacturing and business experience, deployed in technical service, problem solving, new product / new market / new business development and technology commercialisation, in industry, business and educational spheres, in many cultural contexts. A continuous track record of the commercial development and application of technology and science in a multitude of market sectors. Kaizen [continuous improvement] is part of his DNA. Very strong market and customer focus. A strategic and global business thinker. High energy, serious commitment to the task. Very pro-active. Passionate. Analytical driver. Very high personal standards of achievement with impeccable integrity, and a good sense of humour. A very fast learner, with a teachable spirit. Adaptable. Flexible. Highly creative. Excellent presentation and communication skills, confident public speaker. A frequently invited speaker, chairman and moderator at international conferences. Credentials Brunel University UK BTech First Class Polymer Technology Cranfield Institute of Technology PhD in Polymer Engineering Business School, Lausanne CH MBA summa cum -
Development of Thermoplastic Pultrusion with Modeling And
Development of Thermoplastic Pultrusion with Modeling and Experiments Khongor Jamiyanaa and Uday Vaidya University of Alabama at Birmingham (UAB) GATE Scholar Project ID: LM085 Project No: DE-EE-0005580 Program Manager: Adrienne Riggi This presentation does not contain any proprietary or confidential information Project Summary* (The budget below represents the entire GATE Center. This presentation is only a sub-set of the DOE GATE effort.) Barriers Timeline • Limited information on Project Start - Oct 2011 advanced materials Project End – Sep 2016 database 72.6 % complete • Lack of high temperature properties Budget (Overall GATE Center) Total project: $750,000* Partners DOE portion: $600,000 • ORNL University Cost Share: $150,000 • MIT- RCF $447,420 DOE • Owens Corning $325,000 Expended • Polystrand, PPG 72.6% complete • CIC, Canada Khongor Jamiyanaa (GATE Scholar) - Background • Graduated from Colorado State Univ. in 2010 • BS in Mechanical Engineering, Minor in Mathematics • Graduated from Univ. of Alabama at Birmingham in 2014 • MS in Materials Science and Engineering • Research Thesis: Design and modeling of Thermoplastic Pultrusion Process • 1yr Co-op internship at Owens Corning Science & Technology center in 2013. • Application Development Engineer RELEVANCE Pultrusion Applications in Automotive, Truck and Mass Transit Wide Ranges of Pultrusion Offers: cosmetic and structural Frame • High strength-to- Members applications: weight ratio • Transportation Brackets Grates • Corrosion • Truck frame resistance members Pultrusion • Vehicle -
Pultex Pultrusion Design Manual of Standard and Custom Fiber Reinforced Polymer Structural Profiles Imperial Version Volume 5 – Revision 3
The Pultex® Pultrusion Design Manual of Standard and Custom Fiber Reinforced Polymer Structural Profiles Imperial Version Volume 5 – Revision 3 Featuring PultexStandard Structural Profiles Pultex SuperStructural Profiles Nuclear test tower constructed using Pultex® Standard Structural Profiles Creative Pultrusions, Inc. reserves the right to edit and modify literature, please consult the web site for the most current version of this document. “The first Pultex® Design Manual was published in 1973. The New and Improved Pultex® Pultrusion Design Manual of Standard and Custom Fiber Reinforced Polymer Structural Profiles, 2004 Edition, Volume 5 – Revision 3 is a tool for engineers to specify Pultex® pultruded standard structural profiles. Creative Pultrusions, Inc. consistently improves its information to function as a solid reference for engineers.” “No portion of this Design Manual may be reproduced in any form without the prior written consent of Creative Pultrusions, Inc.” Volume 5 - Revision 3 Copyright© 2016 by Creative Pultrusions, Inc. All Rights Reserved Creative Pultrusions®, Flowgrip®, Pultex®, Supergrate®, SUPERPILE®, Superplank®, SuperLoc® and Superdeck® are registered trademarks of Creative Pultrusions, Inc. Superstud!™, Superstud!™/Nuts!, SUPURTUF™, Tuf-dek™, SuperWale™, SuperCap™ and SuperRod™are trademarks of Creative Pultrusions, Inc. i The New and Improved Pultex® Pultrusion Global Design Manual Contents The New and Improved Pultex® Pultrusion Design Manual of Standard and Custom Fiber Reinforced Polymer Structural Profiles, -
A Review of Long Fibre-Reinforced Thermoplastic Or Long Fibre Thermoplastic (LFT) Composites
International Materials Reviews ISSN: 0950-6608 (Print) 1743-2804 (Online) Journal homepage: https://www.tandfonline.com/loi/yimr20 A review of Long fibre-reinforced thermoplastic or long fibre thermoplastic (LFT) composites Haibin Ning, Na Lu, Ahmed Arabi Hassen, Krishan Chawla, Mohamed Selim & Selvum Pillay To cite this article: Haibin Ning, Na Lu, Ahmed Arabi Hassen, Krishan Chawla, Mohamed Selim & Selvum Pillay (2019): A review of Long fibre-reinforced thermoplastic or long fibre thermoplastic (LFT) composites, International Materials Reviews, DOI: 10.1080/09506608.2019.1585004 To link to this article: https://doi.org/10.1080/09506608.2019.1585004 Published online: 11 Mar 2019. Submit your article to this journal Article views: 1 View Crossmark data Full Terms & Conditions of access and use can be found at https://www.tandfonline.com/action/journalInformation?journalCode=yimr20 INTERNATIONAL MATERIALS REVIEWS https://doi.org/10.1080/09506608.2019.1585004 A review of Long fibre-reinforced thermoplastic or long fibre thermoplastic (LFT) composites Haibin Ning a,NaLub, Ahmed Arabi Hassenc, Krishan Chawlaa, Mohamed Selima and Selvum Pillaya aDepartment of Materials Science and Engineering, Materials Processing and Applications Development (MPAD) Centre, University of Alabama at Birmingham, Birmingham, AL, USA; bLyles School of Civil Engineering, School of Materials Engineering, Purdue University, West Lafayette, IN, USA; cManufacturing Demonstration Facility (MDF), Oak Ridge National Laboratory (ORNL), Knoxville, TN, USA ABSTRACT ARTICLE HISTORY Long fibre-reinforced thermoplastic or long fibre thermoplastic (LFT) composites possess Received 8 August 2018 superior specific modulus and strength, excellent impact resistance, and other advantages Accepted 15 February 2019 such as ease of processability, recyclability, and excellent corrosion resistance. -
Miniaturised Rod-Shaped Polymer Structures with Wire Or Fibre Reinforcement—Manufacturing and Testing
Article Miniaturised Rod-Shaped Polymer Structures with Wire or Fibre Reinforcement—Manufacturing and Testing Michael Kucher , Martin Dannemann * , Ansgar Heide, Anja Winkler and Niels Modler Institute of Lightweight Engineering and Polymer Technology (ILK), Technische Universität Dresden, Holbeinstraße 3, 01307 Dresden, Germany; [email protected] (M.K.); [email protected] (A.H.); [email protected] (A.W.); [email protected] (N.M.) * Correspondence: [email protected]; Tel.: +49-351-463-38134 Received: 29 May 2020; Accepted: 26 June 2020; Published: 27 June 2020 Abstract: Rod-shaped polymer-based composite structures are applied to a wide range of applications in the process engineering, automotive, aviation, aerospace and marine industries. Therefore, the adequate knowledge of manufacturing methods is essential, covering the fabrication of small amounts of specimens as well as the low-cost manufacturing of high quantities of solid rods using continuous manufacturing processes. To assess the different manufacturing methods and compare the resulting quality of the semi-finished products, the cross-sectional and bending properties of rod-shaped structures obtained from a thermoplastic micro-pultrusion process, conventional fibre reinforced epoxy resin-based solid rods and fibre reinforced thermoplastic polymers manufactured by means of an implemented shrink tube consolidation process, were statistically analysed. Using the statistical method one-way analysis of variance (ANOVA), the differences between groups were calculated. The statistical results show that the flexural moduli of carbon fibre reinforced polymers were statistically significantly higher than the modulus of all other investigated specimens (probability value P < 0.001). The discontinuous shrink tube consolidation process resulted in specimens with a smooth outer contour and a high level of roundness. -
Sustainable Plastics Strategy
Sustainable Plastics Strategy suschem.org Contributing partners: SusChem Cefic PlasticsEurope EuPC ECP4 Sustainable Plastic Strategy Edition 2, December 2020 Content 4 Sustainable Recycling 28 1 1. Plastic stream preparation (waste pre-treatment) 28 2. Plastic waste preparation 29 Introduction 7 3. Sorting and separation 29 2 3.1. Improve sorting 31 3.2. Improve separation 32 Methodology 11 4. Recycling technologies 34 4.1. Chemical recycling of plastics waste by pyrolysis 36 3 4.2. Chemical recycling of plastic waste by gasification 37 4.3. Chemical recycling of plastics Sustainable-by-Design 16 waste by depolymerization/solvolysis 38 1. Material design 16 4.4. Recycling by dissolution of 1.1. Extend lifetime 16 multi-polymer systems 38 1.2. Material usage vs 4.5. Mechanical recycling 39 performance 19 5. Post-processing 40 1.3. Increase recyclability 19 1.4. Biodegradation 21 1.5. Addressing micro 5 and nano-plastics 22 2. Article Design 24 Alternative Feedstock 43 2.1. Design for dismantling 24 1. Agricultural and forest 2.2. Decrease material usage 24 biomass waste based raw 2.3. Monolayer pouch and in-mold labelling 25 materials 43 2.4. Refillable and recyclable 2. CO2/CO-based 44 PET bottles 26 6 Glossary 49 About the partners 50 About Suschem 51 6 • SUSTAINABLE PLASTICS STRATEGY Introduction Plastic waste is ending up in the environment, feedstock for pure polymers by using chemical and unmanaged, is amongst the greatest recycling. global environmental challenges of our time12. As an industry, we believe plastic waste in the We need a holistic approach to plastic waste environment is unacceptable and represents a based on a measurable science-based massive loss of a valuable resource. -
Plastics Engineering Doctoral Thesis List 11/13/08
Plastics Engineering Doctoral Thesis List 11/13/08 1989 PL-1* Li-Kuo Sun,“The Effect of Plasticizer Structure on Plasticizer Solvency, Permanence and Efficiency” (Advisor: S.P. McCarthy). 1990 PL-1* •David A. Cinquegrana, “Knowledge-Based Injection Mold Design Automation” (Advisor: S.P. McCarthy). PL-2* •John J. DeLuca , “Development of Turbine Containments for Aircraft” (Advisor: ). PL-3* Amar Khelifi, “Compatibilization of Polyethylene Terephthalate and High Density Polyethylene” (Advisor: F.S. Lai). PL-4* Young Roak Kim, “Behavior of Fiber Reinforcements and Resin Flow During the Injection-Pultrusion Process” (Advisor: S.P. McCarthy). 1991 PL-1* •Jong-Liang Wu, “Cavity Pressure-Based Expert System for Injection Molding - A Coupled Numerical and Rule-Based Approach” (Advisor: S.J. Chen). PL-1* Ling C. Yang, “Solidification of Polymer Melt Flowing in a Round Tube” (Advisor: S.J. Chen). PL-2* Toshikazu Katoh, “Processing of Liquid Crystalline Polymer and Engineering Plastics Blends” (Advisor: N.R. Schott). PL-3* Han-Hsiu Tseng, “Software Design and Experimental Verification of Polymer Flow Through a Pipe Extrusion Die” (Advisor: F.S. Lai). 1992 PL-1* Chongkue Yoon, “Fiber Degradation During Reciprocating-Screw Plastication” (Advisor: R.E. Nunn). PL-2* David C. Raia, “Design of a Professional High-Powered Loudspeaker and Its System Integration” (Advisor: N.R. Schott). PL-3* Sang Wook , Park“A Study of the Processing Effect on the Morphology of Biodegradable Blends of Polystyrene and Hydroxypropylcellulose” (Advisor: S.P. McCarthy). PL-4* Gaurang V. Shah, “Toughened Composites for Personal Safety” (Advisors: R.E. Nunn/N.R. Schott). PL-5* Ho-Seon Jin, “γ Radiation-Induced Changes in the Chemical and Physical Structure of Poly (Ethylene Terephthalate)” (Advisor: A.M. -
Competitive Analysis of the Polymer Plastics Industry on the Island Of
A Competitiveness Analysis of the Polymer and Plastics Industry on the Island of Ireland ACKNOWLEDGEMENTS InterTradeIreland would like to thank SQW Ltd, Rapra Technology Ltd, the Northern Ireland Polymer Association, Plastics Ireland and the members of the Steering Panel and the consultees who participated in the research, for their assistance with the development of this report. Steering Panel Members Aidan Gough InterTradeIreland Richard Christie Invest Northern Ireland Gerry Farrell Plastics Ireland Brian Gaffney Enterprise Ireland Marion McAneney InterTradeIreland Brian McCann Northern Ireland Polymer Association Gerry McNally Queen’s University Belfast DISCLAIMER InterTradeIreland is confident that the information and opinions contained in this document have been compiled by the authors from sources believed to be reliable and in good faith, but no representation or warranty, express or implied, is made to their accuracy, completeness or correctness. All opinions or estimates contained in this document constitute the authors’ judgement as of the date of this document and are subject to change without notice. This publication is intended to provide general information to its readers concerning the subject matter of the publication. It is not intended to provide a comprehensive statement of the subject matter of the publication and does not necessarily reflect the views of InterTradeIreland. While care has been taken in the production of the publication, no responsibility is accepted by InterTradeIreland for any errors or omissions -
Modeling the Pultrusion Process to Obtain Low Void Fraction Composites
Graduate Theses, Dissertations, and Problem Reports 2002 Modeling the pultrusion process to obtain low void fraction composites Adam Douglas Freed West Virginia University Follow this and additional works at: https://researchrepository.wvu.edu/etd Recommended Citation Freed, Adam Douglas, "Modeling the pultrusion process to obtain low void fraction composites" (2002). Graduate Theses, Dissertations, and Problem Reports. 1267. https://researchrepository.wvu.edu/etd/1267 This Thesis is protected by copyright and/or related rights. It has been brought to you by the The Research Repository @ WVU with permission from the rights-holder(s). You are free to use this Thesis in any way that is permitted by the copyright and related rights legislation that applies to your use. For other uses you must obtain permission from the rights-holder(s) directly, unless additional rights are indicated by a Creative Commons license in the record and/ or on the work itself. This Thesis has been accepted for inclusion in WVU Graduate Theses, Dissertations, and Problem Reports collection by an authorized administrator of The Research Repository @ WVU. For more information, please contact [email protected]. MODELING THE PULTRUSION PROCESS TO OBTAIN LOW VOID FRACTION COMPOSITES Adam Douglas Freed Thesis submitted to the College of Engineering and Mineral Resources at West Virginia University for the degree of Master of Science in Chemical Engineering Rakesh K. Gupta, Ph.D., Chair Hota V.S. GangaRao, Ph.D. Ray Yang, Ph.D. Department of Chemical Engineering Morgantown, West Virginia 2002 Keywords: pultrusion modeling, composites, void prediction, void measurement Copyright 2002 Adam D. Freed ABSTRACT MODELING THE PULTRUSION PROCESS TO OBTAIN LOW VOID FRACTION COMPOSITES Adam D. -
VINNAPAS® SOLID RESINS Low-Profile Additives for Composites Vinnapas® Polyvinyl Acetate As a Low-Profile Additive Applications in Fiber-Reinforced Plastics (FRP)
Creating tomorrow’s solutions COMPOSITES I ADDITIVES VINNAPAS® SOLID RESINS Low-Profile Additives for Composites VINNAPAS® POLYVINYL ACETATE AS A LOW-PROFILE ADDITIVE APPLICATIONS IN FIBER-REINFORCED PLASTICS (FRP) 1. General Information In addition to VINNAPAS® B and UW 2. Low Profile Technology homopolymer grades, WACKER also VINNAPAS® is a solid, homogeneous, manufactures carboxylated VINNAPAS® Unsaturated polyester composites odorless and nontoxic thermoplastic copolymer C grades based on vinyl for fiber-reinforced plastics comprise synthetic polyvinyl acetate resin. acetate and crotonic acid. unsaturated polyester resins compound- ed with styrene, various fillers, peroxide WACKER produces VINNAPAS® homo- VINNAPAS® (polyvinyl acetate) resins catalysts, thickening agents, mold polymer B and UW grades with varying are used as low-profile additives in FRP release agents, low-profile additives degrees of polymerization, varying mo- composites. The great versatility of and reinforcing glass fibers. Low-profile lecular weights and varying viscosities VINNAPAS® low-profile additive resins technology includes various compound- in solution. has led to many FRP applications, ing techniques and various molding successfully combining zero shrink, techniques depending on the desired Class A surface quality, full viscosity quality and shape of the molded parts. control and design flexibility. On the following pages, we introduce our VINNAPAS® (polyvinyl acetate) resins for use as low-profile additives in FRP composites. VINNAPAS® is a registered trademark of Wacker Chemie AG. GOOD COMPATIBILITY WITH ALL MAJOR COMPOUNDING TECHNIQUES 2.1 Description of the Compounding Other compounding techniques used to RTM: Resin Transfer Molding Techniques harden and transform unsaturated poly- In the RTM process, a combination of ester resin composites into functional continuous mat is laid in the mold cavity.