The Use of Ptfe in the Clothing and Footwear Industry Is Harmful to the Environment and Health - and Thanks to Existing Alternatives, Not Essential
Total Page:16
File Type:pdf, Size:1020Kb
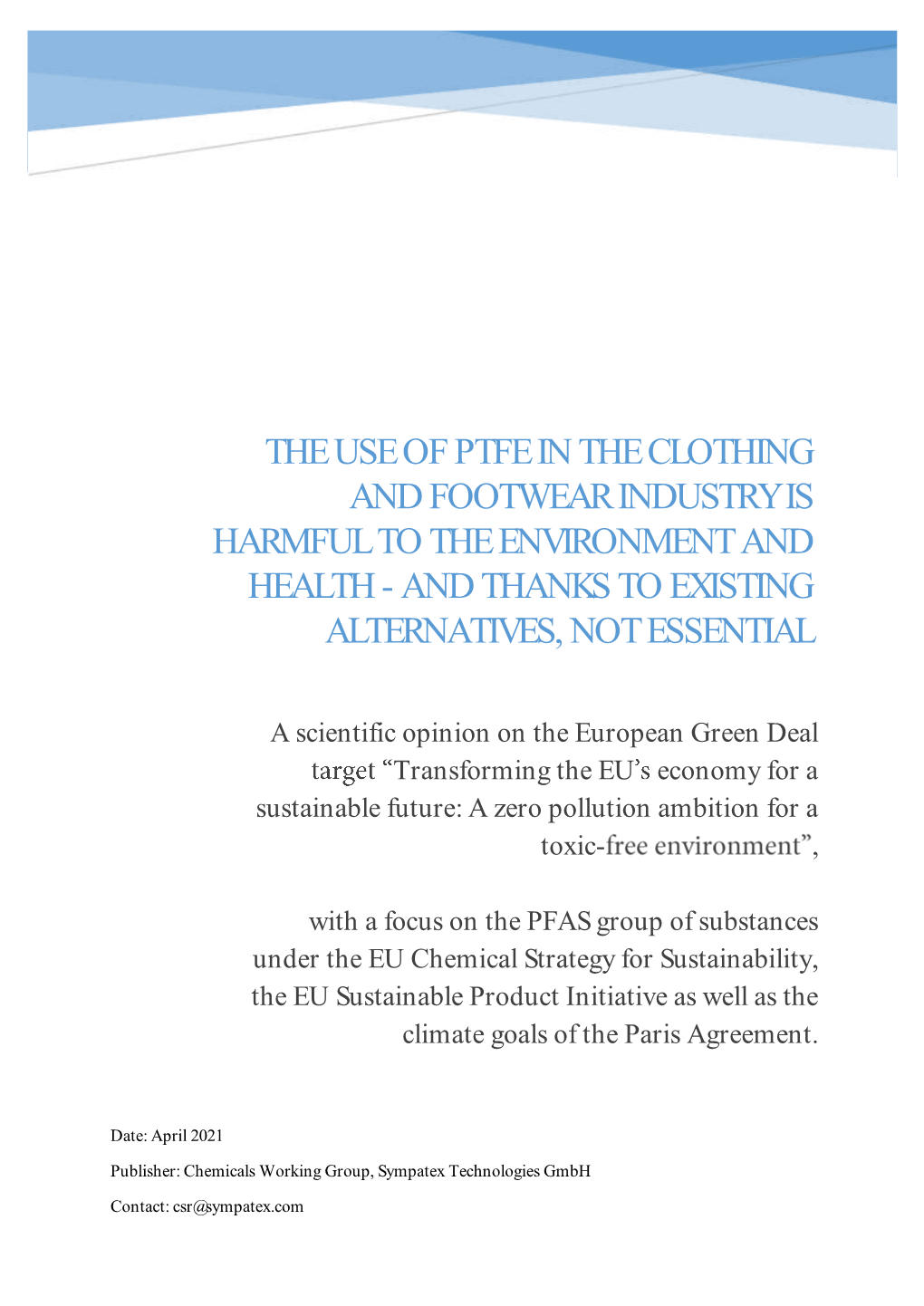
Load more
Recommended publications
-
Subpart L – Fluorinated Gas Production
Mandatory Greenhouse Gas Reporting Rule: EPA's Response to Public Comments Subpart L – Fluorinated Gas Production Subpart L – Fluorinated Gas Production U.S. Environmental Protection Agency Office of Atmospheric Programs Climate Change Division Washington, D.C. FOREWORD This document provides responses to public comments on the U.S. Environmental Protection Agency’s (EPA’s) Proposed Mandatory Greenhouse Gas Reporting Rule: Additional Sources of Fluorinated GHGs: Subpart L, Fluorinated Gas Production. EPA published a Notice of Proposed Rulemaking in the Federal Register (FR) on April 12, 2010 (75 FR 18652). EPA received comments on this proposed rule via mail, e-mail, and at a public hearing held in Washington D.C. on April 20, 2010. Copies of all comments submitted are available at the EPA Docket Center Public Reading Room. Comments letters and transcripts of the public hearings are also available electronically through http://www.regulations.gov by searching Docket ID EPA-HQ-OAR-2009-0927. EPA prepared this document in multiple sections, with each section focusing on a different broad category of comments on the rule. EPA’s responses to comments are generally provided immediately following each comment. In some cases, EPA provided responses to specific comments or groups of similar comments in the preamble to the final rulemaking. Rather than repeating those responses in this document, EPA has referenced the preamble. Comments were assigned to specific section of this document based on an assessment of the principal subject of the comment; however, some comments inevitably overlap multiple subject areas. For this reason, EPA encourages the public to read the other sections of this document relevant to their interests. -
Pfass and Alternatives in Food Packaging (Paper and Paperboard): Report on the Commercial Availability and Current Uses
PFASs and alternatives in food packaging (paper and paperboard): Report on the commercial availability and current uses Series on Risk Management No. 58 1 Series on Risk Management 0 No. 58 PFASs and Alternatives in Food Packaging (Paper and Paperboard) Report on the Commercial Availability and Current Uses PUBE Please cite this publication as: OECD (2020), PFASs and Alternatives in Food Packaging (Paper and Paperboard) Report on the Commercial Availability and Current Uses, OECD Series on Risk Management, No. 58, Environment, Health and Safety, Environment Directorate, OECD. Acknowledgements: The OECD would like to acknowledge the drafting of a consultancy report by Steve Hollins of Exponent International Ltd. upon which this report is based. It was prepared under the framework of the OECD/UNEP Global PFC Group and included the contribution of information by several organisations (see Annex A). The report is published under the responsibility of the OECD Joint Meeting of the Chemicals Committee and the Working Party on Chemicals, Pesticides and Biotechnology. © Photo credits: Cover: Yuriy Golub/Shutterstock.com © OECD 2020 Applications for permission to reproduce or translate all or part of this material should be made to: Head of Publications Service, [email protected], OECD, 2 rue André-Pascal, 75775 Paris Cedex 16, France ABOUT THE OECD 3 About the OECD The Organisation for Economic Co-operation and Development (OECD) is an intergovernmental organisation in which representatives of 36 industrialised countries in North and South America, Europe and the Asia and Pacific region, as well as the European Commission, meet to co-ordinate and harmonise policies, discuss issues of mutual concern, and work together to respond to international problems. -
Title Synthetic Studies on Perfluorinated Compounds
View metadata, citation and similar papers at core.ac.uk brought to you by CORE provided by Kyoto University Research Information Repository Synthetic Studies on Perfluorinated Compounds by Direct Title Fluorination( Dissertation_全文 ) Author(s) Okazoe, Takashi Citation Kyoto University (京都大学) Issue Date 2009-01-23 URL http://dx.doi.org/10.14989/doctor.r12290 Right Type Thesis or Dissertation Textversion author Kyoto University Synthetic Studies on Perfluorinated Compounds by Direct Fluorination Takashi Okazoe Contents Chapter I. General Introduction 1 I-1. Historical Background of Organofluorine Chemistry -Industrial Viewpoint- 2 I-1-1. Incunabula 2 I-1-2. Development with material industry 5 I-1-3. Development of fine chemicals 17 I-2. Methodology for Synthesis of Fluorochemicals 24 I-2-1. Methods used in organofluorine industry 24 I-2-2. Direct fluorination with elemental fluorine 27 I-3. Summary of This Thesis 33 I-4. References 38 Chapter II. A New Route to Perfluoro(Propyl Vinyl Ether) Monomer: Synthesis of Perfluoro(2-propoxypropionyl) Fluoride from Non-fluorinated Compounds 47 II-1. Introduction 48 II-2. Results and Discussion 49 II-3. Conclusions 55 II-4. Experimental 56 II-5. References 60 i Chapter III. A New Route to Perfluorinated Vinyl Ether Monomers: Synthesis of Perfluoro(alkoxyalkanoyl) Fluorides from Non-fluorinated Substrates 63 III-1. Introduction 64 III-2. Results and Discussion 65 III-2-1. Synthesis of PPVE precursors 65 III-2-2. Synthesis of perfluoro(alkoxyalkanoyl) fluorides via perfluorinated mixed esters 69 III-3. Conclusions 75 III-4. Experimental 77 III-5. References 81 Chapter IV. Synthesis of Perfluorinated Carboxylic Acid Membrane Monomers by Liquid-phase Direct Fluorination 83 IV-1. -
Minnesota's Water Quality Monitoring Strategy
Water Quality Monitoring August 2021 Minnesota’s Water Quality Monitoring Strategy 2021-2031 Minnesota’s strategy to ensuring that our waters are monitored and evaluated; developed for the U.S. Environmental Protection Agency. Authors Lindsay Egge Pam Anderson Lee Ganske Contributors/acknowledgements MPCA: Jesse Anderson, Ryan Anderson, Anna Bosch, Michael Bourdaghs, Jordan Donatell, Lindsay Egge, Michael Feist, Aaron Luckstein, Shannon Martin, Miranda Nichols, Scott Niemela, Kelly O’Hara, Cindy Penny, Tiffany Schauls, Erik Smith, Laurie Sovell, Mike Trojan, Steve Weiss, Jim Ziegler Partner organizations: Dan Henely, Metropolitan Council Environmental Services Heather Johnson, Bill VanRyswyk, Minnesota Department of Agriculture Joy Loughry, Steve Kloiber, Minnesota Department of Natural Resources, Steve Robertson, Tracy Lund, Minnesota Department of Health Minnesota Pollution Control Agency 520 Lafayette Road North | Saint Paul, MN 55155-4194 | 651-296-6300 | 800-657-3864 | Or use your preferred relay service. | [email protected] This report is available in alternative formats upon request, and online at www.pca.state.mn.us. Document number: p-gen1-10 Contents Contents ............................................................................................................................................ i Introduction ......................................................................................................................................1 Minnesota’s overarching approach to water management ........................................................................... -
Building a Better World
BUILDING A BETTER WORLD Eliminating Unnecessary PFAS in Building Materials This report was developed by the Green Science Policy Institute, whose mission is to facilitate safer use of chemicals to protect human and ecological health. Learn more at www.greensciencepolicy.org AUTHORS Seth Rojello Fernández, Carol Kwiatkowski, Tom Bruton EDITORS Arlene Blum, Rebecca Fuoco, Hannah Ray, Anna Soehl EXTERNAL REVIEWERS* Katie Ackerly (David Baker Architects) Brent Ehrlich (BuildingGreen) Juliane Glüge (ETH Zurich) Jen Jackson (San Francisco Department of the Environment) David Johnson (SERA Architects) Rebecca Staam (Healthy Building Network) DESIGN Allyson Appen, StudioA2 ILLUSTRATIONS Kristina Davis, University of Notre Dame * External reviewers provided helpful comments and discussion on the report but do not endorse the factual nature of the content. THE BUILDING INDUSTRY HAS THE WILL AND THE KNOW-HOW TO REDUCE ITS USE OF PFAS CHEMICALS. UNDERSTANDING WHERE PFAS ARE USED AND FINDING SAFER ALTERNATIVES ARE CRITICAL. 1 TABLE OF CONTENTS 3 Executive Summary 6 Introduction 7 List of Abbreviations 8 Background 9 PFAS in Humans and the Environment 11 Health Hazards of PFAS 11 Who is at Risk? 12 Non-essential Uses 13 PFAS Use in Building Materials 14 Roofing 17 Coatings 20 Flooring 22 Sealants and Adhesives 24 Glass 25 Fabrics 26 Wires and Cables 27 Tape 28 Timber-Derived Products 28 Solar Panels 29 Artificial Turf 29 Seismic Damping Systems 30 From Building Products to the Environment 32 Moving forward 32 Managing PFAS as a Class 32 The Need for Transparency 34 Safer Alternatives 35 What Can You Do? 36 List of References 45 Appendix 2 EXECUTIVE SUMMARY 3 er- and polyfluoroalkyl substances (PFAS) consumers and some governments are call- are synthetic chemicals that are useful in ing for limits on the production and use of P many building materials and consumer all PFAS, except when those uses are truly products but have a large potential for harm. -
Polytetrafluoroethylene: Synthesis and Characterization of the Original Extreme Polymer
Polytetrafluoroethylene: Synthesis and Characterization of the Original Extreme Polymer Gerard J. Putsa, Philip Crousea and Bruno M. Amedurib* aDepartment of Chemical Engineering, University of Pretoria, Pretoria 0002, South Africa. b Ingenierie et Architectures Macromoléculaires, Institut Charles Gerhardt, UMR 5253 CNRS, UM, ENSCM, Place Eugène Bataillon, 34095 Montpellier Cedex 5, France. Correspondence to: Bruno Ameduri (E-mail: [email protected]) 1 ABSTRACT This review aims to be a comprehensive, authoritative, and critical review of general interest to the chemistry community (both academia and industry) as it contains an extensive overview of all published data on the homopolymerization of tetrafluoroethylene (TFE), detailing the TFE homopolymerization process and the resulting chemical and physical properties. Several reviews and encyclopedia chapters on the properties and applications of fluoropolymers in general have been published, including various reviews that extensively report copolymers of TFE (listed below). Despite this, a thorough review of the specific methods of synthesis of the homopolymer, and the relationships between synthesis conditions and the physico-chemical properties of the material prepared, has not been available. This review intends to fill that gap. As known, PTFE and its marginally modified derivatives comprise some 6065 % of the total international fluoropolymer market with a global increase of ca. 7 % per annum of its production. Numerous companies, such as Asahi Glass, Solvay Specialty Polymers, Daikin, DuPont/Chemours, Juhua, 3F and 3M/Dyneon, etc., produce TFE homopolymers. Such polymers, both high molecular-mass materials and waxes, are chemically inert, hydrophobic, and exhibit an excellent thermal stability as well as an exceptionally low co-efficient of friction. These polymers find use in applications ranging from coatings and lubrication to pyrotechnics, and an extensive industry (electronic, aerospace, wires and cables, as well as textiles) has been built around them. -
Fluorine Mass Balance in Wildlife and Consumer Products
Lara Schultes Fluorine mass balance in wildlife and consumer products Fluorine mass balance in wildlife and consumer products balance in Fluorine mass How much organofluorine are we missing? Lara Schultes ISBN 978-91-7797-596-0 Department of Environmental Science and Analytical Chemistry Doctoral Thesis in Applied Environmental Science at Stockholm University, Sweden 2019 Fluorine mass balance in wildlife and consumer products How much organofluorine are we missing? Lara Schultes Academic dissertation for the Degree of Doctor of Philosophy in Applied Environmental Science at Stockholm University to be publicly defended on Friday 17 May 2019 at 10.00 in Nordenskiöldsalen, Geovetenskapens hus, Svante Arrhenius väg 12. Abstract Per- and polyfluoroalkyl substances (PFASs) are a class of anthropogenic pollutants. Many PFASs are highly persistent and have been linked to adverse effects in humans. According to latest estimates, there are more than 4700 PFASs in global commerce, which poses immense challenges for environmental monitoring. This thesis aims at the development, validation and application of total fluorine (TF) and extractable organic fluorine (EOF) methods to consumer products and wildlife in order to estimate the fraction of unidentified organic fluorine in these samples via fluorine mass balance calculations. Fluoropolymer-coated food packaging materials and reference materials were used in paper I to validate and compare the performance of three different TF methods. Combustion ion chromatography (CIC), particle-induced gamma ray emission spectroscopy (PIGE) and instrumental neutron activation analysis (INAA) revealed excellent analytical agreement and precision under most circumstances. PIGE and INAA had the advantage of being non-destructive, while CIC was favored due to low detection limits. -
Report on the State of the Art Technical and Environmental Data of the Selected Conventional and Alternative DWOR
MIDWOR - LIFE14 ENV/ES/000670 With the contribution of the LIFE financial instrument of the European Commission PROJECT MIDWOR Deliverable A2.1 Report on the state of the art technical and environmental data of the selected conventional and alternative DWOR MIDWOR - LIFE14 ENV/ES/000670 With the contribution of the LIFE financial instrument of the European Commission Project acronym: MIDWOR-LIFE Project full title: Mitigation of environmental impact caused by DWOR textile finishing chemicals studying their nontoxic alternatives Grant agreement no.: LIFE14 ENV/ES/000670 Responsible partner for deliverable: LEITAT Contributing partners: CETIM Author(s): Jordi Mota (JM), Julio Fierro (JF), Cristina Martinez (CM) Nature 1: R Dissemination level 2: CO Total number of pages: 32 Version: 0.3 Contract delivery date: 30/06/2016 Actual delivery date: 30/06/2016 Version control Number Date Description Publisher Reviewer 0.1 20/06/2016 Initial version JM JM 0.2 23/06/2016 First review JM JF, CM 0.3 27/06/2016 Added “ State of the art of JF, CM JM environmental data ” 1 Nature of Deliverable : P= Prototype, R= Report, S= Specification, T= Tool, O= Other. 2 Dissemination level : PU = Public, RE = Restricted to a group of the specified Consortium, PP = Restricted to other program participants (including Commission Services), CO = Confidential, only for members of the Consortium (including the Commission Services) REPORT ON THE TECHNICAL STATE OF ART Page 2 MIDWOR - LIFE14 ENV/ES/000670 With the contribution of the LIFE financial instrument of the European Commission Contents 1. Introduction ............................................................................................................ 4 2. Products selected ................................................................................................... 4 3. State of the art of technical data ........................................................................... -
Report R118/2016 Economic Potential and Strategic Relevance of Fluorspar
REPORT R118/2016 ECONOMIC POTENTIAL AND STRATEGIC RELEVANCE OF FLUORSPAR DIRECTORATE: MINERAL ECONOMICS REPORT R118/2016 ECONOMIC POTENTIAL AND STRATEGIC RELEVANCE OF FLUORSPAR DIRECTORATE: MINERAL ECONOMICS Compilers: Mphonyana Modiselle [email protected] Tshegofatso Ndlovu [email protected] Acknowledgement: The cover picture by courtesy of various Google images Issued by and obtainable free of charge from The Director: Mineral Economics, Trevenna Campus, 70 Mentjies Street, Sunnyside 0001, Private Bag X59, Arcadia 0007 Telephone (012) 444 3536/3531, Telefax (012) 341 4134 Website: http://www.dmr.gov.za DEPARTMENT OF MINERAL RESOURCES Acting Director-General Mr. D Msiza MINERAL POLICY AND PROMOTION BRANCH Deputy Director General Mr. M Mabuza Chief Director: Mineral Promotion Ms. S Mohale DIRECTORATE: MINERAL ECONOMICS Director: Mr. TR Masetlana Acting Deputy Director: Industrial Minerals Mr. R Motsie THIS, THE FIRST EDITION, PUBLISHED IN 2016 ISBN: 978-0-621-44561-7 COPYRIGHT RESERVED DISCLAIMER & COPYRIGHT Whereas the greatest care has been taken in the compilation and the contents of this publication, the Department of Mineral Resources does no hold itself responsible for any errors or omissions. ABSTRACT Fluorspar, also called fluorite (CaF2) was identified by the British Geological Survey (BGS) as a strategic mineral in 2012, because it is vital for the production of a wide range of chemicals, including refrigerants, polymers, lubricants and pharmaceuticals. Two fluorspar grades are important in terms of traded volumes, which are acid grade fluorspar (acidspar) and metallurgical grade fluorspar (metspar). Acidspar which has a minimum of 97 percent CaF2 is fundamental for production of hydrogen fluoride (HF) and represents 49 percent of annual global consumption of fluorspar. -
Organofluorine Chemistry Principles and Commercial Applications
Organofluorine Chemistry Principles and Commercial Applications Edited by R. E. Banks The University of Manchester Institute ofScience and Technology (UMIST% Manchester, United Kingdom B. E. Smart DuPont Central Research & Development Wilmington, Delaware and J. C Tatlow Editorial Office of the Journal of Fluorine Chemistry Birmingham, United Kingdom Plenum Press • New York and London Contents 1. Organofluorine Chemistry: Nomenclature and Histoncal Landmarks R. E. Banks and J. C. Tatlow 1.1. Preamble 1 1.2. Nomenclature 2 1.2.1. Highly Fluorinated Compounds 2 1.2.2. Fluorocarbon Code Numbers 4 1.3. Historical Landmarks 5 1.3.1. The HF Problem 5 1.3.2. Synthesis ofC—F Bonds 6 1.3.3. Aliphatic Fluorides GoCommercial 12 1.3.4. Perfluorocarbons 14 1.3.5. Wartime Advances: The Manhattan Project 17 1.3.6. Postwar Progress 17 1.4. References . 21 2. Synthesis of Organofluorine Compounds R. E. Banks and J. C. Tatlow 2.1. Introduction 25 2.2. Synthesis Methodology 26 2.2.1. The Building-Block Approach 27 2.2.2. The Formation of Carbon-Fluorine Bonds 27 2.3. The Current Position 29 2.4. Tabular Summary of Fluorination Methods and Reagents 29 2.5. References 53 xi xii Contents 3. Characteristics of C-F Systems Bruce E. Smart 3.1. Introduction 57 3.2. Physical Properties 58 3.2.1. General 58 3.2.2. Solvent Polarity 64 3.2.3. Lipophilicity 66 3.2.4. Acidity and Basicity 67 3.2.5. Hydrogen Bonding 69 3.3. Chemical Properties 70 3.3.1. Bond Strengths and Reactivity 70 3.3.2. -
Synthesis of Organofluorine Compounds Using a Falling Film Microreactor: Process Development and Kinetic Modelling
SYNTHESIS OF ORGANOFLUORINE COMPOUNDS USING A FALLING FILM MICROREACTOR: PROCESS DEVELOPMENT AND KINETIC MODELLING Kuveshan Padayachee [BSc Eng, UKZN] University of KwaZulu-Natal Howard College A dissertation submitted in fulfilment of the requirements for the degree Master of Science in Engineering in Chemical Engineering, School of Engineering, College of Agriculture, Engineering and Science, University of KwaZulu-Natal June 2016 Supervisors: Doctor David Lokhat and Professor Deresh Ramjugernath As the candidate’s supervisor I agree to the submission of this dissertation: Dr. D. Lokhat Prof. D. Ramjugernath DECLARATION I, Kuveshan Padayachee declare that: The research reported in this dissertation/thesis, except where otherwise indicated, is my original work. 1. The research reported in this thesis, except where otherwise indicated, is my original research. 2. This thesis has not been submitted for any degree or examination at any other university. 3. This thesis does not contain other persons’ data, pictures, graphs or other information, unless specifically acknowledged as being sourced from other persons. 4. This thesis does not contain other persons' writing, unless specifically acknowledged as being sourced from other researchers. Where other written sources have been quoted, then: i. Their words have been re-written but the general information attributed to them has been referenced ii. Where their exact words have been used, then their writing has been placed in italics and inside quotation marks, and referenced. 5. This thesis does not contain text, graphics or tables copied and pasted from the Internet, unless specifically acknowledged, and the source being detailed in the thesis and in the References sections. Signed: ________________ Date: ________________ ii ACKNOWLEDGEMENTS This research is aligned with the aims of the Fluorochemical Expansion Initiative (FEI) endorsed and funded by the Department of Science and Technology. -
Federal Register/Vol. 68, No. 73/Wednesday, April 16, 2003/Notices
18626 Federal Register / Vol. 68, No. 73 / Wednesday, April 16, 2003 / Notices categorically excluded from the ADDRESSES: Submit your comments, regarding the applicability of this action preparation of an environmental identified by docket ID number OPPT– to a particular entity, consult the assessment or an environmental impact 2003–0012, online at http:// technical person listed under FOR statement. www.epa.gov/edocket/ (EPA’s preferred FURTHER INFORMATION CONTACT. method), or by mail to EPA Docket Determination Under Executive Order B. How Can I Get Copies of this Center (7407), Environmental Protection Document and Other Related 12866 Agency, 1200 Pennsylvania Ave., NW., Information? Western has an exemption from Washington, DC 20460–0001. For centralized regulatory review under additional comment submission 1. Docket. EPA has established an Executive Order 12866. This notice is methods and detailed instructions, go to official public docket for this action not required to be cleared by the Office Unit I.C. of the SUPPLEMENTARY under docket identification (ID) number of Management and Budget. INFORMATION. OPPT–2003–0012. The official public Dated: March 27, 2003. Submit your notification for docket consists of the documents ‘‘interested party’’ status separately from specifically referenced in this action, Michael S. Hacskaylo, any comments submitted, identified any public comments received, and Administrator. ‘‘Attention: PFOA ECA Notification’’ by other information related to this action. [FR Doc. 03–9325 Filed 4–15–03; 8:45 am] mail to Brigitte Farren, Chemical Although a part of the official docket, BILLING CODE 6450–01–P Control Division (7405M), Office of the public docket does not include Pollution Prevention and Toxics, Confidential Business Information (CBI) Environmental Protection Agency, 1200 or other information whose disclosure is ENVIRONMENTAL PROTECTION Pennsylvania Ave., NW., Washington, restricted by statute.