History of the Use of Hydrogen Peroxide As a Propellant
Total Page:16
File Type:pdf, Size:1020Kb
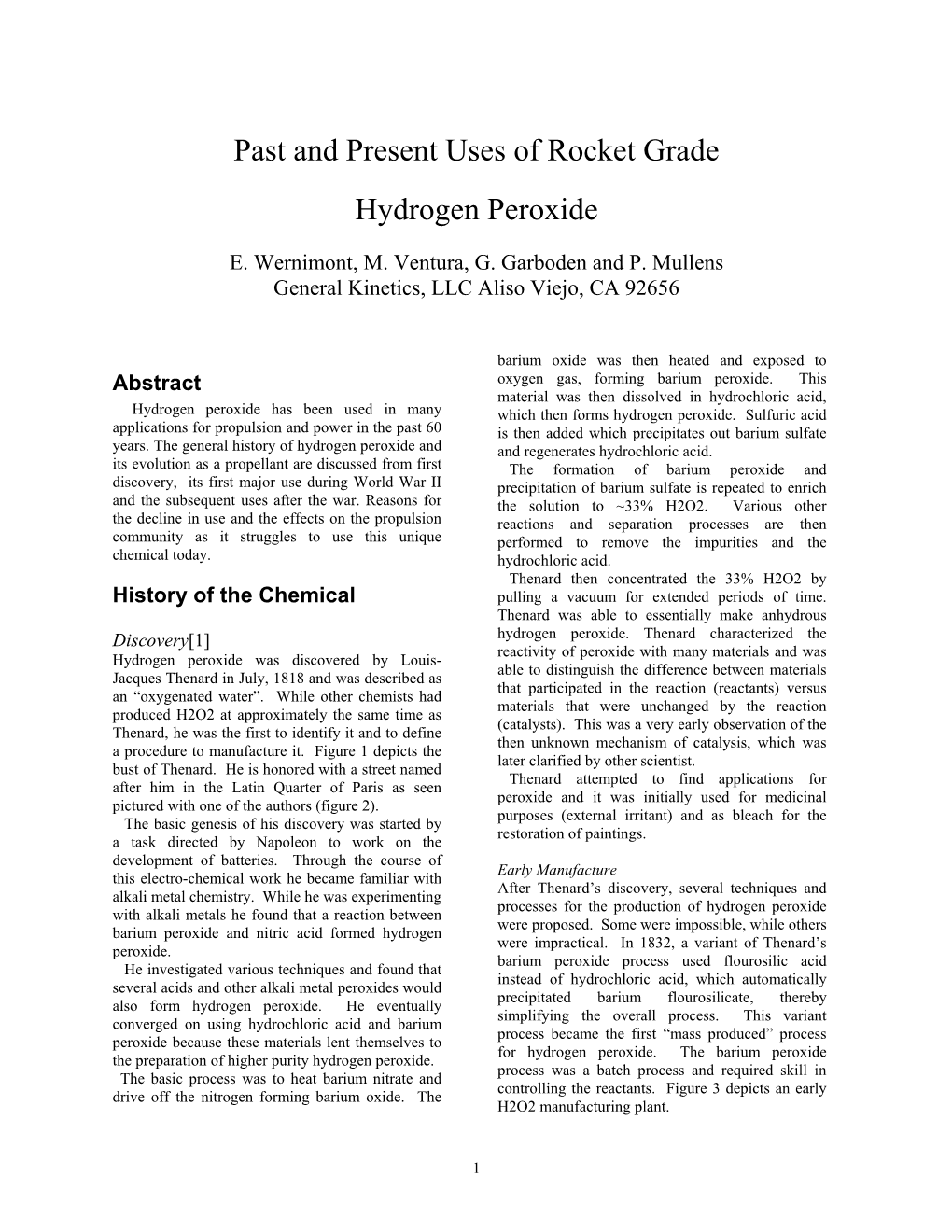
Load more
Recommended publications
-
Back to the the Future? 07> Probing the Kuiper Belt
SpaceFlight A British Interplanetary Society publication Volume 62 No.7 July 2020 £5.25 SPACE PLANES: back to the the future? 07> Probing the Kuiper Belt 634089 The man behind the ISS 770038 Remembering Dr Fred Singer 9 CONTENTS Features 16 Multiple stations pledge We look at a critical assessment of the way science is conducted at the International Space Station and finds it wanting. 18 The man behind the ISS 16 The Editor reflects on the life of recently Letter from the Editor deceased Jim Beggs, the NASA Administrator for whom the building of the ISS was his We are particularly pleased this supreme achievement. month to have two features which cover the spectrum of 22 Why don’t we just wing it? astronautical activities. Nick Spall Nick Spall FBIS examines the balance between gives us his critical assessment of winged lifting vehicles and semi-ballistic both winged and blunt-body re-entry vehicles for human space capsules, arguing that the former have been flight and Alan Stern reports on his grossly overlooked. research at the very edge of the 26 Parallels with Apollo 18 connected solar system – the Kuiper Belt. David Baker looks beyond the initial return to the We think of the internet and Moon by astronauts and examines the plan for a how it helps us communicate and sustained presence on the lunar surface. stay in touch, especially in these times of difficulty. But the fact that 28 Probing further in the Kuiper Belt in less than a lifetime we have Alan Stern provides another update on the gone from a tiny bleeping ball in pioneering work of New Horizons. -
The Argonauta
ARGONAUTA The Newsletter of The Canadian Nautical Research Society / Société canadienne pour la recherche nautique Volume XXXVI Number 2 Spring 2019 ARGONAUTA Founded 1984 by Kenneth MacKenzie ISSN No. 2291-5427 Editors Isabel Campbell and Colleen McKee Winston (Kip) Scoville ~ Production/Distribution Manager Argonauta Editorial Office e-mail submissions to: [email protected] or [email protected] ARGONAUTA is published four times a year—Winter, Spring, Summer and Autumn Chair of the Editorial Board: Roger Sarty Editor The Northern Mariner/ William Glover Le marin du nord: Webmaster: Paul Adamthwaite Executive Officers President: Richard Gimblett 1st Vice President: Walter Lewis 2nd Vice President: Faye Kert Treasurer: Errolyn Humphreys Secretary: Michael Moir Membership Secretary: Sam McLean Councillor/Communications: Kip Scoville Councillor: Richard Goette Councillor: Tom Malcomson Councillor: David More Councillor: Jeff Noakes Councillor: Margaret Schotte Councillor: Ian Yeates Membership Business: P.O. Box 34029 Station B, Ottawa, Ontario, K2J 4B1, Canada e-mail: [email protected] Annual Membership including four issues of ARGONAUTA and four issues of THE NORTHERN MARINER/LE MARIN DU NORD: Canadian International Digital Only Individual $70 $80 $30 Benefactor $250 Institutional $95 $105 n/a Corporate $500 Student $35 $35 $35 Patron $1000 or above NASOH n/a n/a $30 Our Website: http://www.cnrs-scrn.org Copyright © CNRS/SCRN and all original copyright holders In this issue of the Argonauta Editorial 1 President’s Corner -
Monopropellant System
~™ mil ii ii nun mi iiiii iiiii (19) J European Patent Office Office europeen des brevets (11) EP 0 950 648 A1 (12) EUROPEAN PATENT APPLICATION (43) Date of publication:ation: (51) Int. CI.6: C06D 5/08 20.10.1999 Bulletin 1999/42 (21) Application number: 98201190.0 (22) Date of filing: 15.04.1998 (84) Designated Contracting States: (72) Inventors: AT BE CH CY DE DK ES Fl FR GB GR IE IT LI LU • van den Berg, Ronald Peter MC NL PT SE 2291 KJ Wateringen (NL) Designated Extension States: • Mul, Johannes Maria AL LT LV MK RO SI 2013 AE Haarlem (NL) • Elands, Petrus Johannes Maria (71) Applicant: 2804 LK Gouda (NL) NEDERLANDSE ORGANISATIE VOOR TOEGEPAST-NATUURWETENSCHAPPELIJK (74) Representative: ONDERZOEK Smulders, Theodorus A.H.J., Ir. et al TNO Vereenigde Octrooibureaux 2628 VK Delft (NL) Nieuwe Parklaan 97 2587 BN 's-Gravenhage (NL) (54) Monopropellant system (57) The invention is directed to a monopropellant composition for propulsion and/or gas generation, com- prising a solution of hydrazinium nitroformate (HNF) and/or ammonium dinitramide (ADN) in water and/or an alkanol. < CO CO o LO o Q_ LU Printed by Xerox (UK) Business Services 2.16.7/3.6 EP 0 950 648 A1 Description [0001] The present invention is in the area of monopropellant composition systems, for instance for spacecraft pro- pulsion, in emergency systems for jet fighters or in emergency gasgeneration systems for submarines. 5 [0002] Spacecraft propulsion is defined as that needed for the orientation (attitude control) and positioning (orbit con- trol including de-orbiting) of spacecraft after delivery into the required orbit by the launch vehicle. -
Development of Turbopump for LE-9 Engine
Development of Turbopump for LE-9 Engine MIZUNO Tsutomu : P. E. Jp, Manager, Research & Engineering Development, Aero Engine, Space & Defense Business Area OGUCHI Hideo : Manager, Space Development Department, Aero Engine, Space & Defense Business Area NIIYAMA Kazuki : Ph. D., Manager, Space Development Department, Aero Engine, Space & Defense Business Area SHIMIYA Noriyuki : Space Development Department, Aero Engine, Space & Defense Business Area LE-9 is a new cryogenic booster engine with high performance, high reliability, and low cost, which is designed for H3 Rocket. It will be the first booster engine in the world with an expander bleed cycle. In the designing process, the performance requirements of the turbopump and other components can be concurrently evaluated by the mathematical model of the total engine system including evaluation with the simulated performance characteristic model of turbopump. This paper reports the design requirements of the LE-9 turbopump and their latest development status. Liquid oxygen 1. Introduction turbopump Liquid hydrogen The H3 rocket, intended to reduce cost and improve turbopump reliability with respect to the H-II A/B rockets currently in operation, is under development toward the launch of the first H3 test rocket in FY 2020. In rocket development, engine is an important factor determining reliability, cost, and performance, and as a new engine for the H3 rocket first stage, an LE-9 engine(1) is under development. A rocket engine uses a turbopump to raise the pressure of low-pressure propellant supplied from a tank, injects the pressurized propellant through an injector into a combustion chamber to combust it under high-temperature and high- pressure conditions. -
AIR-INDEPENDENT PROPULSION – AIP Technology Creates a New Undersea Threat Page 1 of 6
AIR-INDEPENDENT PROPULSION – AIP Technology Creates a New Undersea Threat Page 1 of 6 AIR-INDEPENDENT PROPULSION AIP Technology Creates a New Undersea Threat Walter Type XVIIB up on the stocks. Pictured above is the German Walter Type XVIIB U-1406, partially dismantled shortly after the end of World War II. U-1406 was turned over to the U.S. Navy as a war prize and soon disposed of, but the Royal Navy later operated her sister ship, U-1407, as HMS Meteorite to gain experience in hydrogen-peroxide propulsion technologies. As interest mounts in "Air-Independent Propulsion" (AIP) for enhancing the performance of small, defensive submarines, a serious new underwater threat is developing in littoral waters. Increasingly, smaller nations unwilling or unable to accept the high cost of nuclear power to achieve greater underwater endurance and longer range are turning to lower-priced and less ambitious alternatives that still offer significant operational advantages over conventional diesel- electric submarines. The best of the latter boats, such as the German-designed Type 209 or the Russian KILO, can remain submerged on battery at slow speed for periods on the order of three to five days. But now, several AIP schemes in development or already in operation can increase slow-speed endurance to as much as three weeks or a month. While still dwarfed by the potential of nuclear power, AIP offers diesel submarines a remarkable increase in capability. AIP - The Early History Despite their initial successes, submarine pioneers were still eager to find some means to free their boats from the necessity of surfacing frequently for access to the atmospheric oxygen demanded by the gasoline or diesel engines that charged the batteries. -
Combustion Tap-Off Cycle
College of Engineering Honors Program 12-10-2016 Combustion Tap-Off Cycle Nicole Shriver Embry-Riddle Aeronautical University, [email protected] Follow this and additional works at: https://commons.erau.edu/pr-honors-coe Part of the Aeronautical Vehicles Commons, Other Aerospace Engineering Commons, Propulsion and Power Commons, and the Space Vehicles Commons Scholarly Commons Citation Shriver, N. (2016). Combustion Tap-Off Cycle. , (). Retrieved from https://commons.erau.edu/pr-honors- coe/6 This Article is brought to you for free and open access by the Honors Program at Scholarly Commons. It has been accepted for inclusion in College of Engineering by an authorized administrator of Scholarly Commons. For more information, please contact [email protected]. Honors Directed Study: Combustion Tap-Off Cycle Date of Submission: December 10, 2016 by Nicole Shriver [email protected] Submitted to Dr. Michael Fabian Department of Aerospace Engineering College of Engineering In Partial Fulfillment Of the Requirements Of Honors Directed Study Fall 2016 1 1.0 INTRODUCTION The combustion tap-off cycle is also known as the “topping cycle” or “chamber bleed cycle.” It is an open liquid bipropellant cycle, usually of liquid hydrogen and liquid oxygen, that combines the fuel and oxidizer in the main combustion chamber. Gases from the edges of the combustion chamber are used to power the engine’s turbine and are expelled as exhaust. Figure 1.1 below shows a picture representation of the cycle. Figure 1.1: Combustion Tap-Off Cycle The combustion tap-off cycle is rather unconventional for rocket engines as it has only been put into practice with two engines. -
Materials for Liquid Propulsion Systems
https://ntrs.nasa.gov/search.jsp?R=20160008869 2019-08-29T17:47:59+00:00Z CHAPTER 12 Materials for Liquid Propulsion Systems John A. Halchak Consultant, Los Angeles, California James L. Cannon NASA Marshall Space Flight Center, Huntsville, Alabama Corey Brown Aerojet-Rocketdyne, West Palm Beach, Florida 12.1 Introduction Earth to orbit launch vehicles are propelled by rocket engines and motors, both liquid and solid. This chapter will discuss liquid engines. The heart of a launch vehicle is its engine. The remainder of the vehicle (with the notable exceptions of the payload and guidance system) is an aero structure to support the propellant tanks which provide the fuel and oxidizer to feed the engine or engines. The basic principle behind a rocket engine is straightforward. The engine is a means to convert potential thermochemical energy of one or more propellants into exhaust jet kinetic energy. Fuel and oxidizer are burned in a combustion chamber where they create hot gases under high pressure. These hot gases are allowed to expand through a nozzle. The molecules of hot gas are first constricted by the throat of the nozzle (de-Laval nozzle) which forces them to accelerate; then as the nozzle flares outwards, they expand and further accelerate. It is the mass of the combustion gases times their velocity, reacting against the walls of the combustion chamber and nozzle, which produce thrust according to Newton’s third law: for every action there is an equal and opposite reaction. [1] Solid rocket motors are cheaper to manufacture and offer good values for their cost. -
H2O2) Is Commonly Used for Cleaning Cuts and Sores, and That a Bottle of Hydrogen Peroxide Can Turn a Brunette Into a Blonde
Hydrogen Peroxide and Sugar Most people know that Hydrogen Peroxide (H2O2) is commonly used for cleaning cuts and sores, and that a bottle of hydrogen peroxide can turn a brunette into a blonde. Yet, how many people know that hydrogen peroxide can also be used as a powerful rocket fuel? And how many people know that hydrogen peroxide accelerated the jet car Peroxide Thunder to 450 mph in 3.4 seconds? Hydrogen peroxide is commonly used (in very low concentrations, typically around 5%) to bleach human hair, hence the phrases "peroxide blonde" and "bottle blonde". It burns the skin upon contact in sufficient concentration. In lower concentrations (3%), it is used medically for cleaning wounds and removing dead tissue. Combined with urea as carbamide peroxide, it is used for whitening teeth. Hydrogen peroxide tends to decompose exothermically into water and oxygen gas. The rate of decomposition is dependent on the temperature and concentration of the peroxide, as well as the presence of impurities and stabilizers. The use of a catalyst (such as manganese dioxide, silver, or the enzyme catalase) vastly increases the rate of decomposition of hydrogen peroxide. High strength peroxide (also called high-test peroxide, or HTP) must be stored in a vented container to prevent the buildup of pressure leading to the eventual rupture of the container. In the 1930s and 40s, Hellmuth Walter pioneered methods of harnessing the rapid decomposition of hydrogen peroxide in gas turbines and rocket engines. Hydrogen peroxide works best as a propellant in extremely high concentrations of 90% or higher. Hydrogen peroxide - Wikipedia Online Encyclopedia Hydrogen peroxide (H2O2) can store energy in the form of chemical energy, similar to hydrogen. -
The Last Achievements in the Development of a Rocket Grade Hydrogen Peroxide Catalyst Chamber with Flow Capacity of 1 Kg/S
SPACE PROPULSION 2014, ST-RCS-85, 19th to 22nd May 2014, Cologne, Germany THE LAST ACHIEVEMENTS IN THE DEVELOPMENT OF A ROCKET GRADE HYDROGEN PEROXIDE CATALYST CHAMBER WITH FLOW CAPACITY OF 1 KG/S Ognjan Božić German Aerospace Center (DLR), Institute of Aerodynamics and Flow Technology, Germany, [email protected] Dennis Porrmann, Daniel Lancelle and Stefan May German Aerospace Center (DLR), Institute of Aerodynamics and Flow Technology, Germany ABSTRACT ABBREVIATIONS Worldwide, the hybrid rocket propulsion technology gained in importance recently. A new innovative hybrid AHRES Advanced Hybrid Rocket Engine rocket engine concept is developed at the German Simulation Aerospace Center (DLR) within the program “AHRES”. H2O Water This rocket engine is based on hydroxyl-terminated H2O2 Hydrogen peroxide polybutadiene with metallic additives as solid fuel and O2 Oxygen rocket grade hydrogen peroxide (high test peroxide: HTP) HRE Hybrid Rocket Engine as liquid oxidiser. Instead of a conventional ignition HTPB Hydroxyl-terminated Polybutadiene system, a catalyst chamber with a silver mesh catalyst is HTP High Test Peroxide designed, to decompose the HTP to steam and oxygen at LRE Liquid rocket engine high temperatures up to 615 °C. The newly modified NTO Dinitrogen Tetraoxide (N2O4) catalyst chamber is able to decompose up to 1.3 kg/s of SHAKIRA Simulation of High test peroxide Advanced 87,5% HTP. Used as a monopropellant thruster, this (K)Catalytic Ignition system for Rocket equals an average thrust of 1600 N. Applications The catalyst chamber consists of the catalyst itself, a mount for the catalyst material, a retainer, an injector NOMENCLATURE manifold and a casing. -
Alternative Power Sources for Submarines
Special brandstoffen By ing. R.P. Dingemanse Alternative Power Sources for Submarines The turn of the twentieth century marked a change in the development of submarines. Diesel electric propulsion would become the dominant power system. Batteries were used for running submerged and gasoline or diesel engines were used on the surface and during snorting to recharge the batteries. Early boats used gasoline, but quickly gave way to diesel, because of reduced flammability. Yet, over the years, other power sources have been investigated, and successfully applied. The key aspect of any submarine is its stealth. Submarines operate tonnes, 22-metre-submarine, the V 80, was secretly tested at the quietly, submerged in hostile waters, mainly to gather information. Friedrich Krupp Germaniawerft in Kiel. Having to recharge the submarine’s batteries is a huge disadvan- Highly concentrated hydrogen peroxide is very unstable. When the tage for these covert operations. Conventional submarines rely on “Walter technology” was used in the 1950s, some serious accidents snorting to charge their batteries while staying just below the sur- happened and the technology was abandoned for submarine use. face. However, the air intake and diesel exhaust mast and peri- When looking at ways to increase submerged endurance, important scope make them vulnerable to detection by radar or visually. Fur- aspects are reducing power demand when submerged (propulsion thermore, running diesel engines is a noisy operation. A submarine’s and auxiliary loads), enlarging the battery capacity, and generating indiscretion rate is defined as the percentage of time a submarine power without the need for outside air. spends snorting. -
Modular Impulsive Green Monopropellant Propulsion System (MIMPS-G): for Cubesats in LEO and to the Moon
aerospace Article Modular Impulsive Green Monopropellant Propulsion System (MIMPS-G): For CubeSats in LEO and to the Moon Ahmed E. S. Nosseir 1,2,* , Angelo Cervone 1,* and Angelo Pasini 2,* 1 Department of Space Engineering, Faculty of Aerospace Engineering, Delft University of Technology (TU Delft), 2629 Delft, The Netherlands 2 Sede di Ingegneria Aerospaziale, Dipt. di Ingegneria Civile e Industriale, Università di Pisa (UniPi), 56122 Pisa, Italy * Correspondence: [email protected] or [email protected] (A.E.S.N.); [email protected] (A.C.); [email protected] (A.P.) Abstract: Green propellants are currently considered as enabling technology that is revolutioniz- ing the development of high-performance space propulsion, especially for small-sized spacecraft. Modern space missions, either in LEO or interplanetary, require relatively high-thrust and impulsive capabilities to provide better control on the spacecraft, and to overcome the growing challenges, particularly related to overcrowded LEOs, and to modern space application orbital maneuver require- ments. Green monopropellants are gaining momentum in the design and development of small and modular liquid propulsion systems, especially for CubeSats, due to their favorable thermophysical properties and relatively high performance when compared to gaseous propellants, and perhaps simpler management when compared to bipropellants. Accordingly, a novel high-thrust modular impulsive green monopropellant propulsion system with a micro electric pump feed cycle is pro- posed. MIMPS-G500mN is designed to be capable of delivering 0.5 N thrust and offers theoretical total impulse I from 850 to 1350 N s per 1U and >3000 N s per 2U depending on the burnt mono- Citation: Nosseir, A.E.S.; Cervone, tot A.; Pasini, A. -
Low Cost Catalysts for Hydrazine Monopropellant Thrusters
See discussions, stats, and author profiles for this publication at: https://www.researchgate.net/publication/268483024 Low Cost Catalysts for Hydrazine Monopropellant Thrusters Conference Paper · August 2009 DOI: 10.2514/6.2009-5232 CITATIONS READS 2 53 5 authors, including: Jose Nivaldo Hinckel National Institute for Space Research, Brazil 27 PUBLICATIONS 50 CITATIONS SEE PROFILE All content following this page was uploaded by Jose Nivaldo Hinckel on 27 June 2018. The user has requested enhancement of the downloaded file. Low Cost Catalysts for Hydrazine Monopropellant Thrusters Jos´eNivaldo Hinckel∗ INPE/DMC, S˜aoJos´edos Campos, SP, 12201-970, Brazil Jos´eA. R. Jorge†Tur´ıbioG. Soares Neto†Marisa A. Zacharias†Jalusa A. L. Palandi‡ INPE/LCP, Cachoeira Paulista, SP, 12630-000, Brazil Hydrazine monopropellant engines are widely used in space missions; mainly in reaction control systems. The most widely used catalyst is the aluminum oxide supported iridium. It is also very expensive. The cost of the catalyst weights heavily, especially in the high thrust, short life thrusters used for roll control of launch vehicles. In this paper we present the results of testing of low cost catalysts in a 35 newton thruster. The catalysts tested were aluminum oxide supported ruthenium and a homogeneous catalyst, tungsten carbide. The test sequence included pre-heated and cold starts, pulsed and continuous firing modes, a range of feed pressure and life cycle that exceed the requirements of roll control systems. The start and energetic performance of the thruster matched very closely the performance of the iridium catalyst. Nomenclature ∗ C [m/s] Characteristic Velocity Pc [MPa] Chamber Pressure Cf Thrust Coefficient tig [ms] Ignition time F [N] Thrust tresp [ms] Response time ◦ Isp [m/s] Specific Impulse Tin [ C] Initial Temperature Pi [MPa] Injection Pressure I.