Study of Translucent Glass Concrete
Total Page:16
File Type:pdf, Size:1020Kb
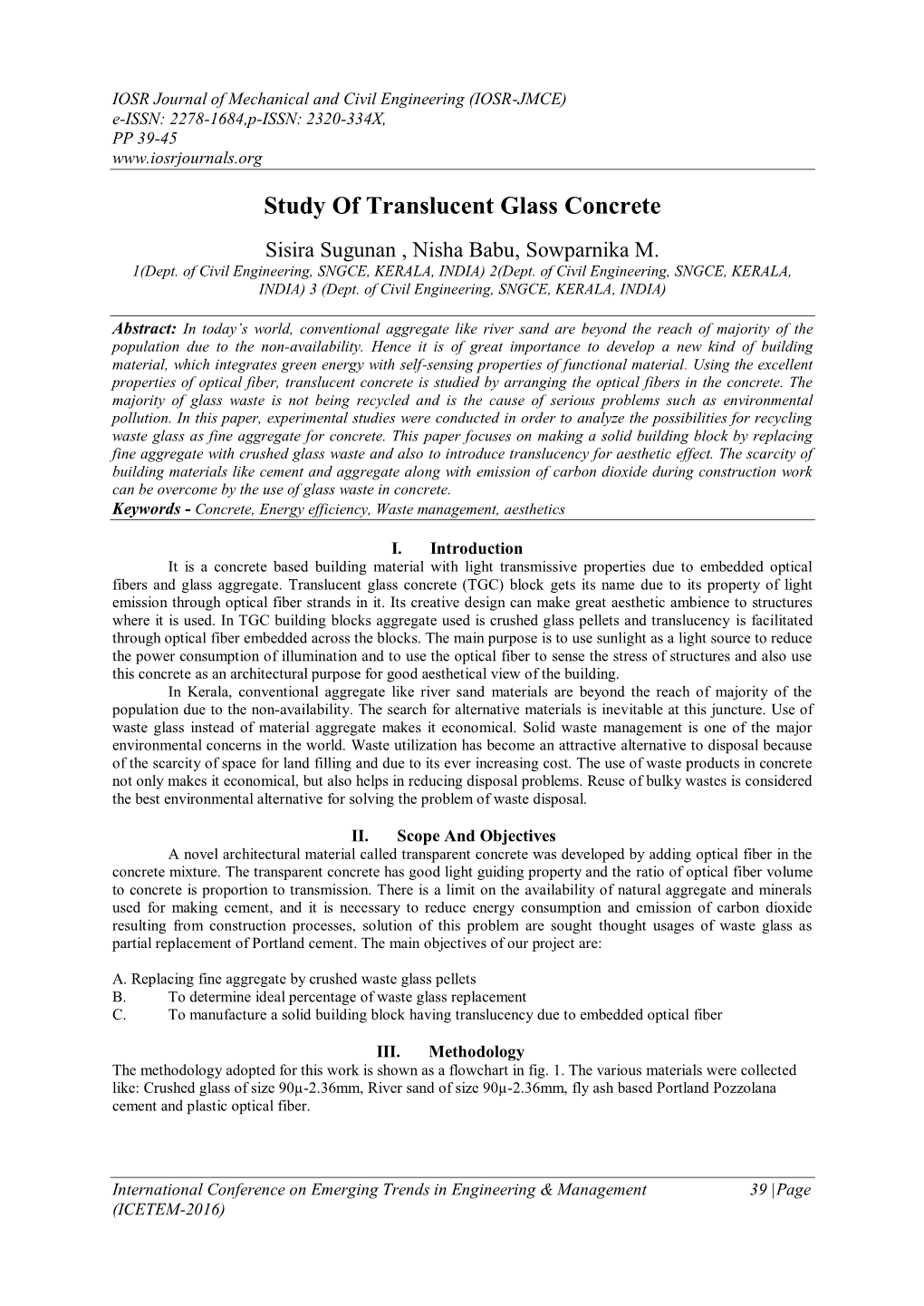
Load more
Recommended publications
-
Experimental Study on Flyash and Lime with Gypsum in Concrete
International Journal of Application or Innovation in Engineering & Management (IJAIEM) Web Site: www.ijaiem.org Email: [email protected] Volume 8, Issue 3, March 2019 ISSN 2319 - 4847 Experimental Study on Flyash and Lime With Gypsum in Concrete T.Subramani1, Akshay Vijayan2, P.Mohammed Fayas3, Jestin Thomas4, S.Priyanka5 1Professor & Dean, Department of Civil Engineering, VMKV Engineering College, Vinayaka Missions Research Foundation (Deemed to be University), Salem, India 2,3,4,5UG Student, , Department of Civil Engineering, VMKV Engineering College, Vinayaka Missions Research Foundation (Deemed to be University), Salem, India ABSTRACT Conventional concrete is responsible for amount of carbon-dioxide emission to some Extent. So to reduce the emission, various types of concrete are developed using waste products from industries and agricultural use like blast furnace slag, silica fume, fly ash which requires low Amount of energy and also cause least harm to the environment. Falg concrete is a new technology developed now days to reduce the effect on environment by production of cement. Cement contains high amount of carbon-di- oxide which harms the environment drastically, so by replacing the cement by various materials which causes harm to the environment we not only reduce the problem of disposal of these materials but we reduce the emission of carbon-di-oxide from cement. This study concerns with the use of fly ash and lime to improve the strength of concrete. An experimental investigation has been carried out by replacing the cement with falg by 0%. 10% and 20% for M30 grade of concrete. The main aim of this project is to investigate the compressive strength, split tensile strength and water absorption of M30 grade of concrete. -
Vysoké Učení Technické V Brně Brno University of Technology
VYSOKÉ UČENÍ TECHNICKÉ V BRNĚ BRNO UNIVERSITY OF TECHNOLOGY FAKULTA STAVEBNÍ FACULTY OF CIVIL ENGINEERING ÚSTAV TECHNOLOGIE STAVEBNÍCH HMOT A DÍLCŮ INSTITUTE OF TECHNOLOGY OF BUILDING MATERIALS AND COMPONENTS VLIV VLASTNOSTÍ VSTUPNÍCH MATERIÁLŮ NA KVALITU ARCHITEKTONICKÝCH BETONŮ INFLUENCE OF INPUT MATERIALS FOR QUALITY ARCHITECTURAL CONCRETE DIPLOMOVÁ PRÁCE DIPLOMA THESIS AUTOR PRÁCE Bc. Veronika Ondryášová AUTHOR VEDOUCÍ PRÁCE prof. Ing. RUDOLF HELA, CSc. SUPERVISOR BRNO 2018 1 2 3 Abstrakt Diplomová práce se zaměřuje na problematiku vlivu vlastností vstupních surovin pro výrobu kvalitních povrchů architektonických betonů. V úvodní části je popsána definice architektonického betonu a také výhody a nevýhody jeho realizace. V dalších kapitolách jsou uvedeny charakteristiky, dávkování či chemické složení vstupních materiálů. Kromě návrhu receptury je důležitým parametrem pro vytvoření kvalitního povrchu betonu zhutňování, precizní uložení do bednění a následné ošetřování povrchu. Popsány jsou také jednotlivé druhy architektonických betonů, jejich způsob vyrábění s uvedenými příklady na konkrétních realizovaných stavbách. V praktické části byly navrženy 4 receptury, kde se měnil druh nebo dávkování vstupních surovin. Při tvorbě receptur byl důraz kladen především na minimální segregaci čerstvého betonu a omezení vzniku pórů na povrchu ztvrdlého betonu. Klíčová slova Architektonický beton, vstupní suroviny, bednění, separační prostředky, cement, přísady, pigment. Abstract This diploma thesis focuses on the influence of properties of feedstocks for the production of quality surfaces of architectural concrete. The introductory part describes the definition of architectural concrete with the advantages and disadvantages of its implementation. In the following chapters, the characteristics, the dosage or the chemical composition of the input materials are given. Besides the design of the mixture, important parameters for the creation of a quality surface of concrete are compaction, precise placement in formwork and subsequent treatment of the surface. -
A Study on Translucent Concrete and It's Properties
ISSN(Online): 2319-8753 ISSN (Print): 2347-6710 International Journal of Innovative Research in Science, Engineering and Technology (A High Impact Factor, Monthly, Peer Reviewed Journal) Visit: www.ijirset.com Vol. 6, Issue 10, October 2017 A Study on Translucent Concrete and it’s Properties Er.Rohan.R.Vaswani ¹ Dept. of Civil Engineering, Guru Nanak College of Engineering and Technology Rashtrasant Tukdoji Maharaj University Nagpur, India¹ ABSTRACT:Translucent concrete allow light to pass through it because of the presence of optical fibers within the opaque concrete wall. Light is transmitted from one surface of the said wall to the other, because of the presence of optical fiber strands along the width of the wall, which allows light to pass through. The principal objective of this project is to design translucent concrete blocks with the use of glass optical fibers, and then anallize their various properties and characteristics. All tests further performed on our concrete samples and on the optical fibers as such were done to ascertain the improvements of the casted blocks over normal concrete blocks of the same size and with the same design ratios, and to ascertain the practical utility of using translucent concrete as a building material for green building development KEYWORDS : Translucent concrete, Optical fibres,Applications, Properties, Proportion. I. INTRODUCTION In 2001 by Hungarian architect Aron Losonczi was First invented the translucent concrete at the Technical University of Budapest by using optical fibres into the concrete. LITRACON is a first transparent concrete block produced in 2003 by using the optical fibres. Due to globalization and construction of high-rise building, the space between buildings is reduced; this causes to increasing the use of non- renewable energy sources, so therefore there is a need of smart construction technique like green building andindoor thermal system.Translucent concrete is new technique different from normal concrete. -
Light Transmitting Concrete Using Eco Friendly Materials (Waste Materials) a Jayaraman1, S M Gowtham2, N Praveen3, V Hariharan4, M Refak Afrith5
International Journal of ChemTech Research CODEN (USA): IJCRGG, ISSN: 0974-4290, ISSN(Online):2455-9555 Vol.13 No.03, pp 240-250, 2020 Light Transmitting Concrete using Eco Friendly materials (Waste materials) A Jayaraman1, S M Gowtham2, N Praveen3, V Hariharan4, M Refak Afrith5, 1Assistant Professor, Department of Civil Engineering Bannari Amman Institute of Technology, Sathamangalam-638401, India 2, 3, 4,5 UG Students, Department of Civil Engineering Bannari Amman Institute of Technology, Sathamangalam-638401, India Abstract : Concrete is a composite material composed of fine and coarse aggregate bonded together with fluid cement that hardens over time. Now days mostly the construction researchers have been trying to improve the quality and reduced dead weight of the structure and enhance its performance. In this current situation there is a demand in natural sand so engineers are using manufactured sand. The aim of our project is to reduce the dead weight of the structure as well increase the strength of the concrete.So we developed light weight aggregate and sand by using waste plastic and glass materials. We developed a concrete by using crushed glass bottles and melted plastic which is considered as light weight concrete. Glass is an ideal material for recycling use of recycled glass helps in energy saving. This indicate that glass can be effectively used as a fine aggregate replacement without substantial change in strength and also we used aluminum metal powder for reducing the member weight by introduced air in concrete. For the innovative and aesthetic purpose we made the concrete to glow using plastic optical fiber which acts as a transmitting agent which also called as translucent concrete in which the optical fiber is inserted in parallel way. -
Life Cycle Cost Analysis of Translucent Concrete
International Journal of Innovative Technology and Exploring Engineering (IJITEE) ISSN: 2278-3075, Volume-8 Issue-4, February 2019 Life Cycle Cost Analysis of Translucent Concrete Nadeem Gulzar Shahmir, Manzoor Ahmad Tantray Abstract: Translucent concrete permits the daylight specifically productive [1]. The TC boards have the particular property of to go starting with one of its end then onto the next end. This is to sunlight transmission, which makes them valuable for vitality be finished by embedding plastic optical filaments in concrete proficient building envelopes. [2] The straightforwardness of which is chiefly utilized for correspondence reason and the optical its development, moderately low cost (except if we talk about strands take a shot at the premise of Nano optics; in this paper cost the solid with costly added substances), the likelihood of examination on execution of translucent concrete in room (translucent concrete room) is talked about. The examination giving the form any ideal shape, gives concrete an depends on the estimations and analyses, computations are done extraordinary preferred standpoint over other building on the suppositions that plastic optical filaments of 2mm width are materials [3]. This concrete adds to new choices of concrete utilized in the room having specific measurements. By using these for economic development [4]. The best an incentive for the plastic optical filaments in concrete was checked for the expense utilization of industrially can be determined as 0.934% optical as well as checked for the light force going crosswise over casted strands by volume, which gives us a compressive quality as concrete blocks. Lux meter was utilized for estimating power of high as 20 N/mm2 [5]. -
Light Weight Translucent Concrete Blocks for Load Bearing Components
International Research Journal of Engineering and Technology (IRJET) e-ISSN: 2395-0056 Volume: 06 Issue: 05 | May 2019 www.irjet.net p-ISSN: 2395-0072 Light Weight Translucent Concrete Blocks for Load Bearing Components Praveen Mathew1, Bibin Raju2, Kiran Venugopal3, Maya Eldho4, Rose Thomas5 1,2,3,4Department of Civil Engineering, Mar Athanasius College of Engineering, Kothamangalam 5(APJ Abdul Kalam Kerala Technological University) ---------------------------------------------------------------------***--------------------------------------------------------------------- Abstract - With innovation in the field of material sciences and by combining fibre optics with concrete technology, led to the development of translucent concrete, which contribute to more cozy, artistic, safe and energy efficient structures. It serves as an innovative building envelope that allows day light permeability through the opaque parts of exterior facades and roofs. This project incorporates the use of optical fibre for the light guiding properties, glass fibres to improve the mechanical performance and expanded clay aggregate for easy handling and development of slender and highly reinforced structural members. The project exploits the use of self-compacting concrete which is a highly flowable and stable concrete without any segregation or consolidation and resolves any delays and additional cost of projects. Samples of desired proportions are cast and tested for optimum dosages and its performance on compression is tested translucent concrete masonry blocks. These masonry blocks would act more beneficial on commercial buildings which make a significant use of artificial day lighting sources and where safety is prime concern. The project provides a new alternative to entrench the concept of sustainability and translucent concrete can regarded as a green energy saving construction materials. Key Words: translucent concrete, self-compacting concrete, optical fibre, glass fibre, expanded clay aggregates. -
(12) Patent Application Publication (10) Pub. No.: US 2013/0284.071 A1 Friedel Et Al
US 2013 0284071A1 (19) United States (12) Patent Application Publication (10) Pub. No.: US 2013/0284.071 A1 Friedel et al. (43) Pub. Date: Oct. 31, 2013 (54) COMPOSITION FOR BUILDING MATERIALS Publication Classification HAVING IMPROVED FREEZE-THAW RESISTANCE AND PROCESS FOR THE (51) Int. Cl. PRODUCTION THEREOF C04B 7/345 (2006.01) (52) U.S. Cl. (75) Inventors: Manuel Friedel, Zurich (CH); Giovanni CPC ...................................... C04B 7/345 (2013.01) Martinola, Buchs (CH); Stefan Meier, USPC ........................................... 106/708: 524/269 Wollerau (CH) (57) ABSTRACT (73) Assignee: Evonik Degussa GmbH, Essen (DE) A hydraulically curable composition, in particular for the (21) Appl. No.: 13/989,205 production of concrete, mortar, screed, or render having improved freeze-thaw resistance, as well as a process for (22) PCT Filed: Nov. 24, 2011 producing the composition. The composition includes the constituents cement, additional constituents, and organofunc (86). PCT No.: PCT/EP2011/070890 tional silicon compounds, and optionally aggregates and S371 (c)(1), admixtures. The composition also contains the additional (2), (4) Date: Jun. 25, 2013 constituents fly ash and silica dust, in each case independently based on the weight of cement, in an amount of from 1 to 25% (30) Foreign Application Priority Data by weight and the organofunctional silicon compounds in an amount of from 0.1 to 5% by weight based on the weight of Dec. 20, 2010 (DE) ...................... 10 2010 O63 561.8 Cement. US 2013/0284071 A1 Oct. 31, 2013 COMPOSITION FOR BUILDING MATERALS exclude elements that are found in the prior art or that affect HAVING IMPROVED FREEZE-THAW a basic or novel characteristic of the invention. -
Heat Treatment of Polystyrene Solar Energy
Heat Treatment of Polystyrene Solar Energy L. Aruova, A. Utkelbaeva, A. Budikova, N. Saktaganova, G. Karshyga, U. Sarabekova and U. Abdikerova Department of Architecture and Construction Industry, Polytechnic Institute, Kyzylorda State University, Kyzylorda, Kazakhstan Key words: Polystyrene concrete, solar energy, Abstract: Solar energy is a powerful reserve of energy at helio-camera, solar hot climate, temperatures the surface of the globe which is about 20 billion kW. This amount of energy is >100 times the amount of energy required for the entire planet; the use of this transmitter power is not related to polluting the planet with harmful substances. The use of solar energy today is very important, as is the particularly acute problem of traditional energy resources, due to their irreparable increase their value. In factories in the Republic of Kazakhstan, industrial manufacturing of building materials today outlined a trend for use of alternative forms of energy and basically solar heat treatment step which traditionally used steam heating. Solar thermal processing is a method of heat treatment of the sun and has many varieties. A certain type of building material is needed to select the optimum, cost-effective way solar thermal processing that the costs were minimal. These studies examined the development in the direction of heat Corresponding Author: treatment polystyrene concrete. The results of this study L. Aruova confirmed that the use of heat treatment methods of solar Department of Architecture and Construction Industry, thermal processing polystyrene is an effective medium for Polytechnic Institute, Kyzylorda State University, the weather in Kyzyl-Orda region, relating to areas with Kyzylorda, Kazakhstan dry hot climates necessary to carry out detailed studies of polystyrene in the weather conditions of high Page No.: 26-40 temperatures and to introduce them into production. -
Translucent Concrete Utilization of Waste Glass in Concrete
Eindhoven University of Technology MASTER Translucent concrete utilization of waste glass in concrete Rouvas, S. Award date: 2013 Link to publication Disclaimer This document contains a student thesis (bachelor's or master's), as authored by a student at Eindhoven University of Technology. Student theses are made available in the TU/e repository upon obtaining the required degree. The grade received is not published on the document as presented in the repository. The required complexity or quality of research of student theses may vary by program, and the required minimum study period may vary in duration. General rights Copyright and moral rights for the publications made accessible in the public portal are retained by the authors and/or other copyright owners and it is a condition of accessing publications that users recognise and abide by the legal requirements associated with these rights. • Users may download and print one copy of any publication from the public portal for the purpose of private study or research. • You may not further distribute the material or use it for any profit-making activity or commercial gain Department of the Built Environment Building Physics and Services Den Dolech 2, 5612 AZ Eindhoven P.O. Box 513, 5600 MB Eindhoven The Netherlands Author Spyridon Rouvas Final master project Student number 0788173 Translucent concrete: E-mail [email protected] Date Utilization of waste glass in 26 August 2013 concrete Spyridon Rouvas Personal information and supervisory committee Personal information Document type: Master project Project title: Translucent concrete: Utilization of waste glass in concrete Date: 26th August 2013 Student name: Spyridon Rouvas E-mail address: [email protected] Student number: 0788173 Study program related information Master: Architecture, Building & Planning (ABP) Speciality: Building Physics and Services Supervisory committee Chairman: prof.dr.ir. -
Translucent Concrete: Test of Compressive Strength and Transmittance
International Journal of Engineering Research & Technology (IJERT) ISSN: 2278-0181 Vol. 4 Issue 07, July-2015 Translucent Concrete: Test of Compressive Strength and Transmittance A. Karandikar N. Virdhi 1Student (BE/1430/2011), Student (BE/1530/2011), Department of Civil & Environmental Engineering, Birla Department of Civil & Environmental Engineering, Institute of Technology, Birla Institute of Technology, Mesra – 835215, Jharkhand, India Mesra – 835215, Jharkhand, India A. Deep 3Student (BE/1515/2011), Department of Civil & Environmental Engineering, Birla Institute of Technology, Mesra – 835215, Jharkhand, India Abstract - Translucent concrete allows light to pass through it In 2001, Hungarian architect Aron Losonczi invented because of the presence of optical fibers within the opaque LiTraCon, the first commercially available form of TC concrete wall. Light is transmitted from one surface of the which can allow 80% light through and only 30% of said wall to the other, because of the presence of optical fiber weight of common concrete. It was a combination of strands along the width of the wall, which allows light to pass optical fibers and fine concrete, combined in such a way through. that the material was both internally and externally The principal objective of this project is to design translucent homogeneous. It was manufactured in blocks and used concrete blocks with the use of glass optical fibers, and then primarily for decoration. LiTraCon presents the concept of analyze their various properties and characteristics. All tests light transmitting concrete in the form of a widely further performed on our concrete samples and on the optical applicable new building material. It can be used for interior fibers as such were done to ascertain the improvements of the or exterior walls, illuminated pavements or even in art or casted blocks over normal concrete blocks of the same size design objects. -
Evaluating Energy Consumption Saving from Translucent Concrete
Energy and Buildings 153 (2017) 448–460 Contents lists available at ScienceDirect Energy and Buildings j ournal homepage: www.elsevier.com/locate/enbuild Evaluating energy consumption saving from translucent concrete building envelope a b,∗ Aashish Ahuja , Khalid M. Mosalam a Department of Mechanical Engineering, University of California, Berkeley, CA 94720, USA b Department of Civil and Environmental Engineering, University of California, Berkeley, CA 94720, USA a r t i c l e i n f o a b s t r a c t Article history: The translucent concrete (TC) as a building envelope can offset some lighting energy that is consumed Received 16 February 2017 within a room in an office. It is constructed from concrete panels which are functionalized by embedding Received in revised form 6 May 2017 optical fibers during the manufacturing phase to transmit sunlight. From preliminary results, a volumetric Accepted 20 June 2017 fiber ratio of 6% used in the TC panel leads to savings in lighting energy by around 50%. The utility of panels is enhanced if it reduces the heating and cooling requirements of the office room. The sunlight channeled Keywords: by optical fibers can contribute in heating of room during winter but in summer months, it leads to spike Daylighting in cooling loads. Also, daylight reduces heat dissipation from lighting installations and positively impacts Energy utilization cooling loads. The conduction through walls allows heat to be removed from the room during morning Markov chain method but transmits heat from ambient environment into the room later in the afternoon and evening. The Solar radiation TC panels presented research combines thermal and lighting analyses to search for an optimal fiber volumetric Thermal analysis ratio for TC panels that would result in energy savings. -
Mechanical Properties of Translucent Concrete Using Plexiglass Bars and Fiberglass
Civil Engineering and Architecture 9(2): 293-300, 2021 http://www.hrpub.org DOI: 10.13189/cea.2021.090203 Mechanical Properties of Translucent Concrete Using Plexiglass Bars and Fiberglass Walid Fouad Edris1,2,*, Essam Odah3,4, Isam Abu-Qasmieh5, Amany Hendy6 1Department of Civil Engineering, Hijjawi Faculty for Engineering Technology, Yarmouk University, Irbid, 21163, Jordan 2Department of Civil Engineering, Giza High Institute of Engineering and Technology, Awel Misr Assiut El Zeraay Rd., El Monib – Giza, Egypt 3Department of Industrial Design, Faculty of Applied Design, Helwan University, Egypt 4Department of Architecture Engineering, Hijjawi Faculty for Engineering Technology, Yarmouk University, Irbid 21163, Jordan 5Department of Biomedical Systems and Informatics Engineering, Hijjawi Faculty for Engineering Technology, Yarmouk University, Irbid 21163, Jordan 6Department of Interior Design & Furniture, Faculty of Applied Design, Damietta University, Egypt Received November 13, 2020; Revised January 20, 2021; Accepted January 28, 2021 Cite This Paper in the following Citation Styles (a): [1] Walid Fouad Edris, Essam Odah, Isam Abu-Qasmieh, Amany Hendy , "Mechanical Properties of Translucent Concrete Using Plexiglass Bars and Fiberglass," Civil Engineering and Architecture, Vol. 9, No. 2, pp. 293 - 300, 2021. DOI: 10.13189/cea.2021.090203. (b): Walid Fouad Edris, Essam Odah, Isam Abu-Qasmieh, Amany Hendy (2021). Mechanical Properties of Translucent Concrete Using Plexiglass Bars and Fiberglass. Civil Engineering and Architecture, 9(2), 293 - 300. DOI: 10.13189/cea.2021.090203. Copyright©2021 by authors, all rights reserved. Authors agree that this article remains permanently open access under the terms of the Creative Commons Attribution License 4.0 International License Abstract This research aims to investigate the environmental sustainability in the field of architectural efficiency of using plexiglass material as an alternative to construction.