Measurement of Impulsive Thrust from a Closed Radio Frequency Cavity
Total Page:16
File Type:pdf, Size:1020Kb
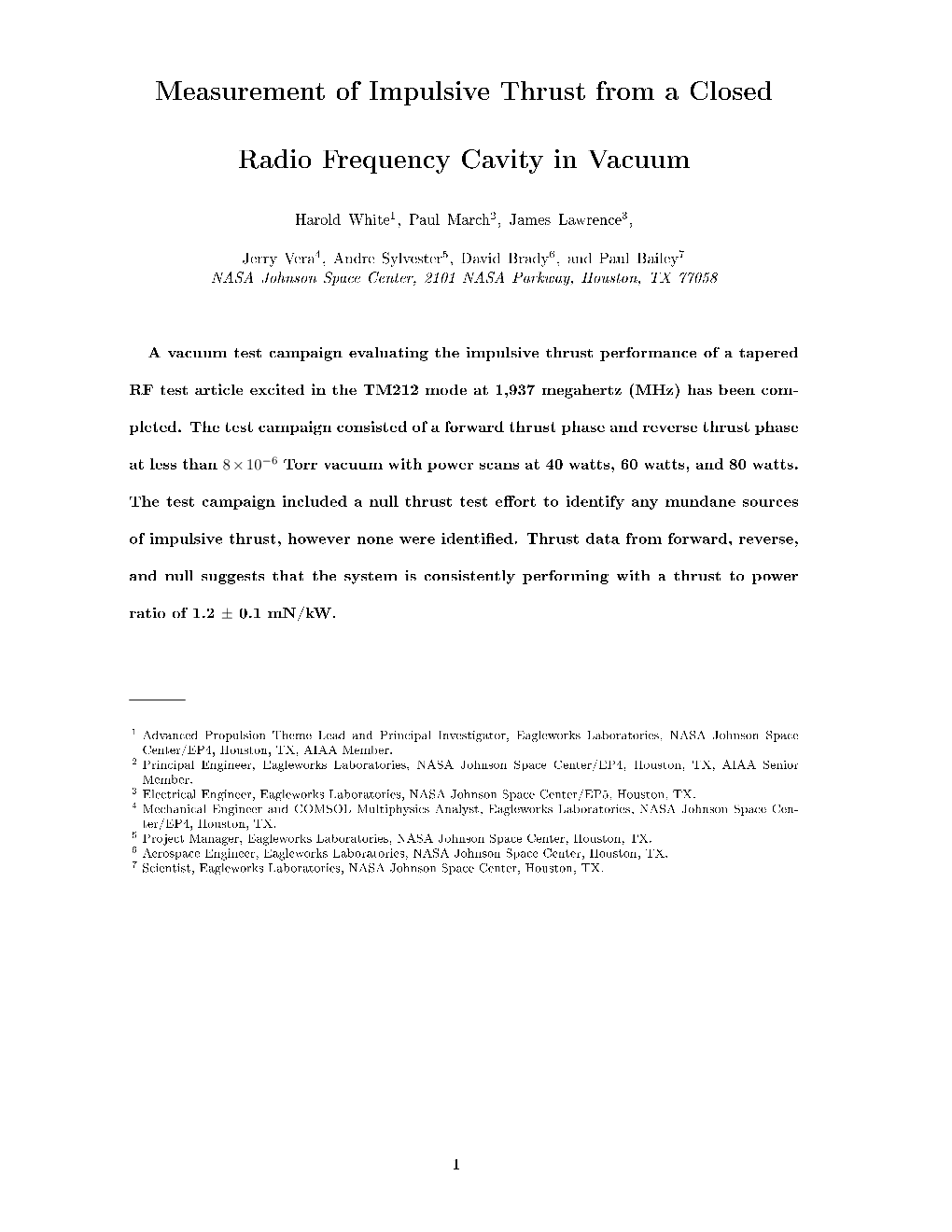
Load more
Recommended publications
-
In a Comprehensive New Test, the Emdrive Fails to Generate Any Thrust 7 April 2021, by Paul M
In a comprehensive new test, the EmDrive fails to generate any thrust 7 April 2021, by Paul M. Sutter conservation of momentum has been tested countless times over centuries—in fact, that principle forms the bedrock of almost every single theory of physics. So in essence, almost every time physics is tested, so is the conservation of momentum. The results of the Eagleworks experiment were not very strong. While the team claimed to measure a thrust, it wasn't statistically significant, and appeared to be a result of "cherry-picking"—the authors watching random fluctuations and waiting for the right time to report their results. But in the spirit of scientific replication, a team at the Dresden University of Technology led by Prof. Martin Tajmar rebuilt the Eagleworks experimental The EmDrive is a hypothetical rocket that setup. proponents claim can generate thrust with no exhaust. This would violate all known physics. In And they found squat. 2016, a team at NASA's Eagleworks lab claimed to measure thrust from an EmDrive device, the news Reporting their results in the Proceedings of Space of which caused quite a stir. The latest attempt to Propulsion Conference 2020, Prof. Tajmar said, replicate the shocking results has resulted in a "We found out that the cause of the 'thrust' was a simple answer: The Eagleworks measurement was thermal effect. For our tests, we used NASAs from heating of the engine mount, not any new EmDrive configuration from White et al. (which was physics. used at the Eagleworks laboratories, because it is best documented and the results were published in The EmDrive is a relatively simple device: It's an the Journal of Propulsion and Power.) empty cavity that isn't perfectly symmetrical. -
The Theory of (Exclusively) Local Beables
The Theory of (Exclusively) Local Beables Travis Norsen Marlboro College Marlboro, VT 05344 (Dated: June 17, 2010) Abstract It is shown how, starting with the de Broglie - Bohm pilot-wave theory, one can construct a new theory of the sort envisioned by several of QM’s founders: a Theory of Exclusively Local Beables (TELB). In particular, the usual quantum mechanical wave function (a function on a high-dimensional configuration space) is not among the beables posited by the new theory. Instead, each particle has an associated “pilot- wave” field (living in physical space). A number of additional fields (also fields on physical space) maintain what is described, in ordinary quantum theory, as “entanglement.” The theory allows some interesting new perspective on the kind of causation involved in pilot-wave theories in general. And it provides also a concrete example of an empirically viable quantum theory in whose formulation the wave function (on configuration space) does not appear – i.e., it is a theory according to which nothing corresponding to the configuration space wave function need actually exist. That is the theory’s raison d’etre and perhaps its only virtue. Its vices include the fact that it only reproduces the empirical predictions of the ordinary pilot-wave theory (equivalent, of course, to the predictions of ordinary quantum theory) for spinless non-relativistic particles, and only then for wave functions that are everywhere analytic. The goal is thus not to recommend the TELB proposed here as a replacement for ordinary pilot-wave theory (or ordinary quantum theory), but is rather to illustrate (with a crude first stab) that it might be possible to construct a plausible, empirically arXiv:0909.4553v3 [quant-ph] 17 Jun 2010 viable TELB, and to recommend this as an interesting and perhaps-fruitful program for future research. -
On the Foundations of Eurhythmic Physics: a Brief Non Technical Survey
International Journal of Philosophy 2017; 5(6): 50-53 http://www.sciencepublishinggroup.com/j/ijp doi: 10.11648/j.ijp.20170506.11 ISSN: 2330-7439 (Print); ISSN: 2330-7455 (Online) On the Foundations of Eurhythmic Physics: A Brief Non Technical Survey Paulo Castro 1, José Ramalho Croca 1, 2, Rui Moreira 1, Mário Gatta 1, 3 1Center for Philosophy of Sciences of the University of Lisbon (CFCUL), Lisbon, Portugal 2Department of Physics, University of Lisbon, Lisbon, Portugal 3Centro de Investigação Naval (CINAV), Portuguese Naval Academy, Almada, Portugal Email address: To cite this article: Paulo Castro, José Ramalho Croca, Rui Moreira, Mário Gatta. On the Foundations of Eurhythmic Physics: A Brief Non Technical Survey. International Journal of Philosophy . Vol. 5, No. 6, 2017, pp. 50-53. doi: 10.11648/j.ijp.20170506.11 Received : October 9, 2017; Accepted : November 13, 2017; Published : February 3, 2018 Abstract: Eurhythmic Physics is a new approach to describe physical systems, where the concepts of rhythm, synchronization, inter-relational influence and non-linear emergence stand out as major concepts. The theory, still under development, is based on the Principle of Eurhythmy, the assertion that all systems follow, on average, the behaviors that extend their existence, preserving and reinforcing their structural stability. The Principle of Eurhythmy implies that all systems in Nature tend to harmonize or cooperate between themselves in order to persist, giving rise to more complex structures. This paper provides a brief non-technical introduction to the subject. Keywords: Eurhythmic Physics, Principle of Eurhythmy, Non-Linearity, Emergence, Complex Systems, Cooperative Evolution among a wider range of interactions. -
The Dark Side of the Emdrive
The Dark Side of the EMDrive Michael Harney The current debate over the theoretical operation of the EMDrive has created a controversy that may upset our current theories of physics and if validated, gives us a gateway to space travel that we have not known before. If it is true that the EMDrive and its variants (such as the Cannae drive) are producing a tiny thrust for just the input of microwave power into a cavity without the requirement to carry any propellant into space, the promise of distant space travel is open before us. With no requirement of the storage of a propellant, the mass of a rocket ship is lowered drastically when considering distant voyages. If the mass of EMDrive and its power source (let’s say solar cells or a Plutonium battery) were only 1 Kg, for instance, it can reach a phenomenal speed in a short period of time with just a little thrust from the EMDrive. For a 1 Kg mass that is generating a thrust of 0.1 Newtons in the vacuum of space, this little ship will have a constant acceleration of 0.1 meters per second-squared and can reach 9,460,800 meters per second (about 3% the speed of light) in three years. The kinetic energy it has amounts to 89,506,736,640,000 Joules of energy, which is equivalent to a 21 Kiloton nuclear device, similar to what was dropped on Nagasaki during World War II. This is all from a 1 Kg EMDrive launched out of Earth’s gravity and directed around the solar system to increase its speed for 3 years based on currently plausible EMDrive thrusts. -
Pilot-Wave Hydrodynamics
FL47CH12-Bush ARI 1 December 2014 20:26 Pilot-Wave Hydrodynamics John W.M. Bush Department of Mathematics, Massachusetts Institute of Technology, Cambridge, Massachusetts 02139; email: [email protected] Annu. Rev. Fluid Mech. 2015. 47:269–92 Keywords First published online as a Review in Advance on walking drops, Faraday waves, quantum analogs September 10, 2014 The Annual Review of Fluid Mechanics is online at Abstract fluid.annualreviews.org Yves Couder, Emmanuel Fort, and coworkers recently discovered that a This article’s doi: millimetric droplet sustained on the surface of a vibrating fluid bath may 10.1146/annurev-fluid-010814-014506 self-propel through a resonant interaction with its own wave field. This ar- Copyright c 2015 by Annual Reviews. ticle reviews experimental evidence indicating that the walking droplets ex- All rights reserved hibit certain features previously thought to be exclusive to the microscopic, Annu. Rev. Fluid Mech. 2015.47:269-292. Downloaded from www.annualreviews.org quantum realm. It then reviews theoretical descriptions of this hydrody- namic pilot-wave system that yield insight into the origins of its quantum- Access provided by Massachusetts Institute of Technology (MIT) on 01/07/15. For personal use only. like behavior. Quantization arises from the dynamic constraint imposed on the droplet by its pilot-wave field, and multimodal statistics appear to be a feature of chaotic pilot-wave dynamics. I attempt to assess the po- tential and limitations of this hydrodynamic system as a quantum analog. This fluid system is compared to quantum pilot-wave theories, shown to be markedly different from Bohmian mechanics and more closely related to de Broglie’s original conception of quantum dynamics, his double-solution theory, and its relatively recent extensions through researchers in stochastic electrodynamics. -
Pilot-Wave Theory, Bohmian Metaphysics, and the Foundations of Quantum Mechanics Lecture 8 Bohmian Metaphysics: the Implicate Order and Other Arcana
Pilot-wave theory, Bohmian metaphysics, and the foundations of quantum mechanics Lecture 8 Bohmian metaphysics: the implicate order and other arcana Mike Towler TCM Group, Cavendish Laboratory, University of Cambridge www.tcm.phy.cam.ac.uk/∼mdt26 and www.vallico.net/tti/tti.html [email protected] – Typeset by FoilTEX – 1 Acknowledgements The material in this lecture is largely derived from books and articles by David Bohm, Basil Hiley, Paavo Pylkk¨annen, F. David Peat, Marcello Guarini, Jack Sarfatti, Lee Nichol, Andrew Whitaker, and Constantine Pagonis. The text of an interview between Simeon Alev and Peat is extensively quoted. Other sources used and many other interesting papers are listed on the course web page: www.tcm.phy.cam.ac.uk/∼mdt26/pilot waves.html MDT – Typeset by FoilTEX – 2 More philosophical preliminaries Positivism: Observed phenomena are all that require discussion or scientific analysis; consideration of other questions, such as what the underlying mechanism may be, or what ‘real entities’ produce the phenomena, is dismissed as meaningless. Truth begins in sense experience, but does not end there. Positivism fails to prove that there are not abstract ideas, laws, and principles, beyond particular observable facts and relationships and necessary principles, or that we cannot know them. Nor does it prove that material and corporeal things constitute the whole order of existing beings, and that our knowledge is limited to them. Positivism ignores all humanly significant and interesting problems, citing its refusal to engage in reflection; it gives to a particular methodology an absolutist status and can do this only because it has partly forgotten, partly repressed its knowledge of the roots of this methodology in human concerns. -
Hamiltonian Formulation of the Pilot-Wave Theory Has Also Been Developed by Holland [9]
Hamiltonian Formulation of the Pilot-Wave Theory Dan N. Vollick Irving K. Barber School of Arts and Sciences University of British Columbia Okanagan 3333 University Way Kelowna, B.C. Canada V1V 1V7 Abstract In the pilot-wave theory of quantum mechanics particles have definite positions and velocities and the system evolves deterministically. The velocity of a particle is deter- mined by the wave function of the system (the guidance equation) and the wave function evolves according to Schrodinger’s equation. In this paper I first construct a Hamiltonian that gives Schrodinger’s equation and the guidance equation for the particle. I then find the Hamiltonian for a relativistic particle in Dirac’s theory and for a quantum scalar field. arXiv:2101.10117v1 [quant-ph] 21 Jan 2021 1 1 Introduction In the standard approach to quantum mechanics the wave function provides a complete description of any system and is used to calculate probability distributions for observ- ables associated with the system. In the pilot-wave theory pioneered by de Broglie [1, 2] in the 1920’s, particles have definite positions and velocities and are “guided” by the wave function, which satisfies Schrodinger’s equation. A similar approach was developed by Bohm [3, 4] in the early 1950’s (see [5] and [6] for extensive reviews). For a single particle in the non-relativistic theory the velocity of the particle is given by dX~ = J~(X,~ t) , (1) dt where X~ is the particle’s position and h¯ J~ = ψ∗ ~ ψ ψ ~ ψ∗ . (2) 2im ψ 2 ∇ − ∇ | | h i Particle trajectories are, therefore, integral curves to the vector field J~. -
Closed Complex Inertial Systems
IJIREEICE ISSN (Online) 2321-2004 ISSN (Print) 2321- 5526 International Journal of Innovative Research in Electrical, Electronics, Instrumentation and Control Engineering CAEE-2018 Conference on Advances in Electronics Engineering 2018 Thakur College of Engineering and Technology, Thakur Vol. 6, Special Issue 1, February 2018 Closed Complex Inertial Systems Anirudh Pednekar, Ankita Jha, Shubham Patil, Aditi Jain Student TE ETRX, TCET, Mumbai, India Abstract: Closed system inertial devices are the devices that can produce a one directional force that would propel any given mass relative to it and hence forth would not follow the fundamental laws of Physics. It does not produce equal and opposite reaction as it uses specific arrangement of weights that can move within the device hence forth capable of moving the body without giving an equal and opposite reaction to move the body. The best way of proving such a device is to conduct an experiment in space or in mid-air so as to have least frictional resistance and no physical contact to other solid particles as of such. Keywords: closed system, inertia, laws of physics I. INTRODUCTION Closed system means a system of engine or any physical quantity of a particular device having its propulsion medium isolated from the immediate surrounding. The body/vehicle has a special kind of device that uses peculiar type of accelerator which would use electricity for the engine hence forth has no such emission that is expelled outside the system. The system having no emission as such produces no equal and opposite reactional forces as well hence forth doesn’t follow the Newtons 3rd law of motion. -
Hydrodynamic Quantum Field Theory: the Free Particle
Comptes Rendus Mécanique Yuval Dagan and John W. M. Bush Hydrodynamic quantum field theory: the free particle Volume 348, issue 6-7 (2020), p. 555-571. <https://doi.org/10.5802/crmeca.34> Part of the Thematic Issue: Tribute to an exemplary man: Yves Couder Guest editors: Martine Ben Amar (Paris Sciences & Lettres, LPENS, Paris, France), Laurent Limat (Paris-Diderot University, CNRS, MSC, Paris, France), Olivier Pouliquen (Aix-Marseille Université, CNRS, IUSTI, Marseille, France) and Emmanuel Villermaux (Aix-Marseille Université, CNRS, Centrale Marseille, IRPHE, Marseille, France) © Académie des sciences, Paris and the authors, 2020. Some rights reserved. This article is licensed under the Creative Commons Attribution 4.0 International License. http://creativecommons.org/licenses/by/4.0/ Les Comptes Rendus. Mécanique sont membres du Centre Mersenne pour l’édition scientifique ouverte www.centre-mersenne.org Comptes Rendus Mécanique 2020, 348, nO 6-7, p. 555-571 https://doi.org/10.5802/crmeca.34 Tribute to an exemplary man: Yves Couder Bouncing drops, memory / Bouncing drops, memory Hydrodynamic quantum field theory: the free particle a b,* Yuval Dagan and John W. M. Bush a Faculty of Aerospace Engineering, Technion - Israel Institute of Technology, Haifa, Israel b Department of Mathematics, Massachusetts Institute of Technology, Cambridge, MA, USA E-mails: [email protected] (Y. Dagan), [email protected] (J. W. M. Bush) Abstract. We revisit de Broglie’s double-solution pilot-wave theory in light of insights gained from the hy- drodynamic pilot-wave system discovered by Couder and Fort [1]. de Broglie proposed that quantum parti- cles are characterized by an internal oscillation at the Compton frequency, at which rest mass energy is ex- changed with field energy. -
Pilot-Wave Theory, Bohmian Metaphysics, and the Foundations of Quantum Mechanics Lecture 6 Calculating Things with Quantum Trajectories
Pilot-wave theory, Bohmian metaphysics, and the foundations of quantum mechanics Lecture 6 Calculating things with quantum trajectories Mike Towler TCM Group, Cavendish Laboratory, University of Cambridge www.tcm.phy.cam.ac.uk/∼mdt26 and www.vallico.net/tti/tti.html [email protected] – Typeset by FoilTEX – 1 Acknowledgements The material in this lecture is to a large extent a summary of publications by Peter Holland, R.E. Wyatt, D.A. Deckert, R. Tumulka, D.J. Tannor, D. Bohm, B.J. Hiley, I.P. Christov and J.D. Watson. Other sources used and many other interesting papers are listed on the course web page: www.tcm.phy.cam.ac.uk/∼mdt26/pilot waves.html MDT – Typeset by FoilTEX – 2 On anticlimaxes.. Up to now we have enjoyed ourselves freewheeling through the highs and lows of fundamental quantum and relativistic physics whilst slagging off Bohr, Heisenberg, Pauli, Wheeler, Oppenheimer, Born, Feynman and other physics heroes (last week we even disagreed with Einstein - an attitude that since the dawn of the 20th century has been the ultimate sign of gibbering insanity). All tremendous fun. This week - we shall learn about finite differencing and least squares fitting..! Cough. “Dr. Towler, please. You’re not allowed to use the sprinkler system to keep the audience awake.” – Typeset by FoilTEX – 3 QM computations with trajectories Computing the wavefunction from trajectories: particle and wave pictures in quantum mechanics and their relation P. Holland (2004) “The notion that the concept of a continuous material orbit is incompatible with a full wave theory of microphysical systems was central to the genesis of wave mechanics. -
What Can Bouncing Oil Droplets Tell Us About Quantum Mechanics?
What can bouncing oil droplets tell us about quantum mechanics? Peter W. Evans∗1 and Karim P. Y. Th´ebault†2 1School of Historical and Philosophical Inquiry, University of Queensland 2Department of Philosophy, University of Bristol June 16, 2020 Abstract A recent series of experiments have demonstrated that a classical fluid mechanical system, constituted by an oil droplet bouncing on a vibrating fluid surface, can be in- duced to display a number of behaviours previously considered to be distinctly quantum. To explain this correspondence it has been suggested that the fluid mechanical system provides a single-particle classical model of de Broglie’s idiosyncratic ‘double solution’ pilot wave theory of quantum mechanics. In this paper we assess the epistemic function of the bouncing oil droplet experiments in relation to quantum mechanics. We find that the bouncing oil droplets are best conceived as an analogue illustration of quantum phe- nomena, rather than an analogue simulation, and, furthermore, that their epistemic value should be understood in terms of how-possibly explanation, rather than confirmation. Analogue illustration, unlike analogue simulation, is not a form of ‘material surrogacy’, in which source empirical phenomena in a system of one kind can be understood as ‘stand- ing in for’ target phenomena in a system of another kind. Rather, analogue illustration leverages a correspondence between certain empirical phenomena displayed by a source system and aspects of the ontology of a target system. On the one hand, this limits the potential inferential power of analogue illustrations, but, on the other, it widens their potential inferential scope. In particular, through analogue illustration we can learn, in the sense of gaining how-possibly understanding, about the putative ontology of a target system via an experiment. -
Hyperspace NASA BPP Program Books 8
Advanced Space Propulsion Concepts for Interstellar Travel Gregory V. Meholic [email protected] Planets HR 8799 140 LY 11/14/08 Updated 9/25/2019 1 Presentation Objectives and Caveats ▪ Provide a high-level, “evolutionary”, information-only overview of various propulsion technology concepts that, with sufficient development (i.e. $), may lead mankind to the stars. ▪ Only candidate concepts for a vehicle’s primary interstellar propulsion system will be discussed. No attitude control No earth-to-orbit launch No traditional electric systems No sail-based systems No beamed energy ▪ None of the following will be given, assumed or implied: Recommendations on specific mission designs Developmental timelines or cost estimates ▪ Not all propulsion options will be discussed – that would be impossible! 2 Chapters 1. The Ultimate Space Mission 2. The Solar System and Beyond 3. Challenges of Human Star Flight 4. “Rocket Science” Basics 5. Conventional Mass Ejection Propulsion Systems State-of-the-Art Possible Improvements 6. Alternative Mass Ejection Systems Nuclear Fission Nuclear Fusion Matter/Antimatter Other Concepts 7. Physics-Based Concepts Definitions and Things to Remember Space-Time Warp Drives Fundamental Force Coupling Alternate Dimension / Hyperspace NASA BPP Program Books 8. Closing Information 3 Chapter 1: The Ultimate Space Mission 4 The Ultimate Space Mission For humans to travel to the stars and return to Earth within a “reasonable fraction” (around 15 years) of a human lifetime. ▪ Why venture beyond our Solar System? Because we have to - humans love to explore!!! Visit the Kuiper Belt and the Oort Cloud – Theoretical home to long-period comets Investigate the nature of the interstellar medium and its influence on the solar system (and vice versa) – Magnetic fields, low-energy galactic cosmic rays, composition, etc.