Use Fof Comparative Analysis When Showing Compliance with SLD Icing
Total Page:16
File Type:pdf, Size:1020Kb
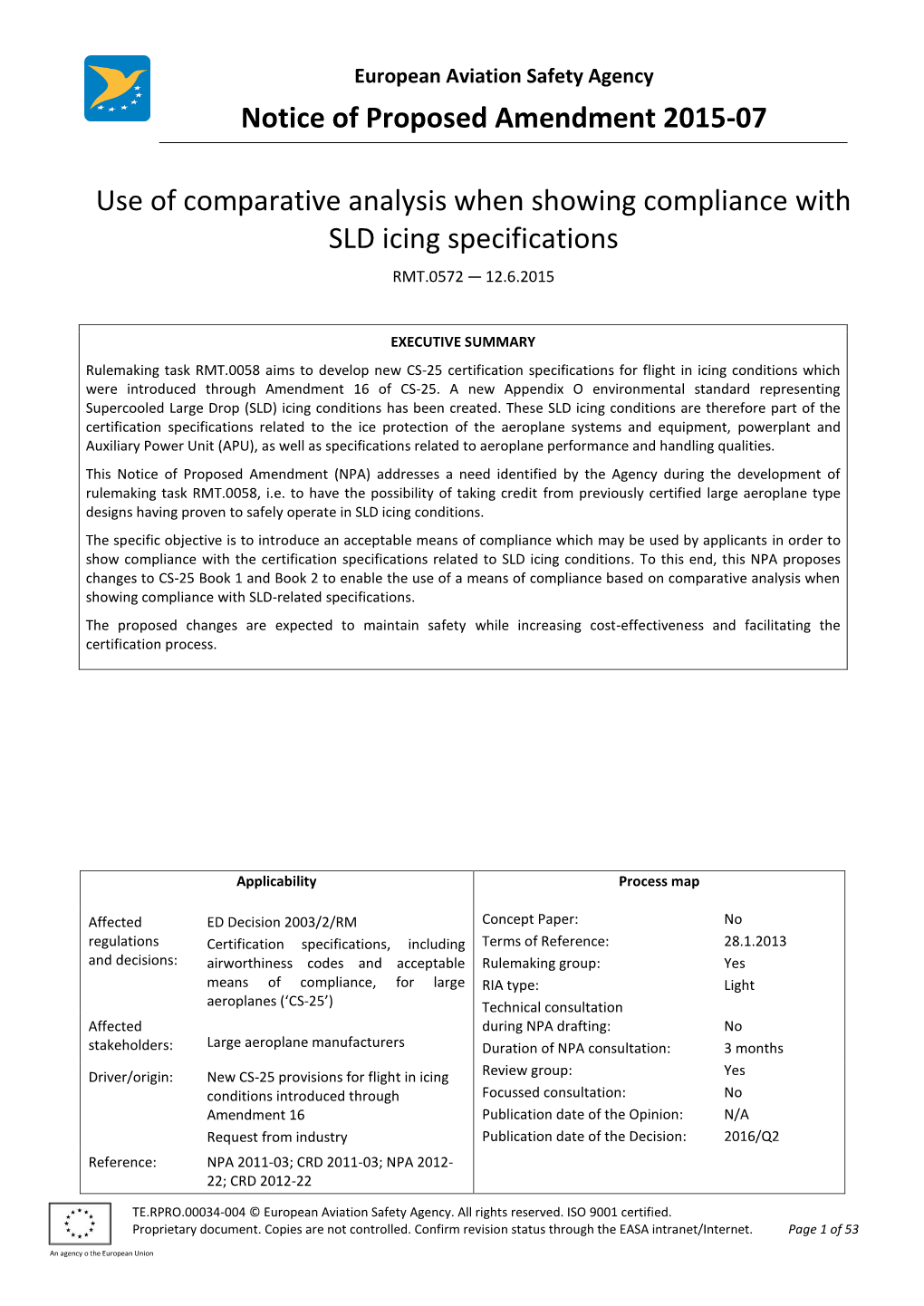
Load more
Recommended publications
-
Application to the Flight
Journal name 000(00):1–13 A Methodology for Vehicle and Mission ©The Author(s) 2010 Reprints and permission: Level Comparison of More Electric sagepub.co.uk/journalsPermissions.nav DOI:doi number Aircraft Subsystem Solutions - Application http://mms.sagepub.com to the Flight Control Actuation System Imon Chakraborty∗ and Dimitri N. Mavris† Aerospace Systems Design Laboratory, Georgia Institute of Technology, Atlanta, GA 30332, USA Mathias Emeneth‡ and Alexander Schneegans§ PACE America Inc., Seattle, WA 98115, USA Abstract As part of the More Electric Initiative, there is a significant interest in designing energy-optimized More Electric Aircraft, where electric power meets all non-propulsive power requirements. To achieve this goal, the aircraft subsystems must be analyzed much earlier than in the traditional design process. This means that the designer must be able to compare competing subsystem solutions with only limited knowledge regarding aircraft geometry and other design characteristics. The methodology presented in this work allows such tradeoffs to be performed, and is driven by subsystem requirements definition, component modeling and simulation, identification of critical or constraining flight conditions, and evaluation of competing architectures at the vehicle and mission level. The methodology is applied to the flight control actuation system, where electric control surface actuators are likely to replace conventional centralized hydraulics in future More Electric Aircraft. While the potential benefits of electric actuation are generally accepted, there is considerable debate regarding the most suitable electric actuator - electrohydrostatic or electromechanical. These two actuator types form the basis of the competing solutions analyzed in this work, which focuses on a small narrowbody aircraft such as the Boeing 737-800. -
Setting up Ailerons and Flaperons on a DLG (Discus Launch Glider) by Andy Kunz
Setting up Ailerons and Flaperons on a DLG (Discus Launch Glider) by Andy Kunz Originally Posted by kgantz: While waiting for parts to be delivered I am still reading a lot about how to initially set up ailerons / flaperons. One of the best descriptions I've found is this post in the DLG forum. After reading this post, I understand that flaperon trim and aileron trim are handled separately by the radio. This is not obvious to people who have not done this before but, I guess because you are working with 1 moving surface but it has 2 jobs, trimming has to work a little differently for each job! So now my question is, on the Spektrum radios-- DX 9 in my case, is the aileron portion of the adjustment done with Dual Rates as suggested by the poster or is there a different way. Reply by AndyKunz: The logic is that one is a roll trim, the other is a camber trim. You'll find that we're pretty consistent with that sort of thing throughout the radio. Use the Dual Rates to adjust travel based on a switch, for instance in launch mode vs. thermal mode vs. landing mode. If it doesn't need to change based on a switch, do it with Servo Travel instead of Dual Rates. If you are working on a V-Tail or Elevon model, then you would use Dual Rates to adjust the ratio between pitch and roll/yaw. Use Servo Travel to adjust the maximum amount in the highest position of the Dual Rates switch. -
An Investigation of the Effects of Flaperon Actuator Failure on Flight Maneuvers of a Supersonic Aircraft
Research Paper ISSN 2383-4986 International Journal of Aerospace System Engineering http://dx.doi.org/10.20910/IJASE.2016.3.2.1 Vo l . 3, No.2, pp.1-8 (2016) An Investigation of the Effects of Flaperon Actuator Failure on Flight Maneuvers of a Supersonic Aircraft Seyool Oh1†, Inje Cho1, Craig McLaughlin2 1Aircraft Research & Development Division, Korea Aerospace Industries, ltd, KOREA 2Dept. of Aerospace Engineering, The University of Kansas U.S.A. †E-mail:[email protected] Abstract The improvements in high performance and agility of modern fighter aircraft have led to improvements in survivability as well. Related to these performance increases are rapid response and adequate deflection of the control surfaces. Most control surface failures result from the failure of the actuator. Therefore, the failure and behavior of the actuators are essential to both combat aircraft survivability and maneuverability. In this study, we investigate the effects of flaperon actuator failure on flight maneuvers of a supersonic aircraft. The flight maneuvers were analyzed using six degrees of freedom (6DOF) simulations. This research will contribute to improvements in the reconfiguration of control surfaces and control allocation in flight control algorithms. This paper compares the results of these 6DOF simulations with the horizontal tail actuator failures analyzed previously. Key Words : Flaperon, Actuator failure, Flight maneuver, Supersonic aircraft , Combat aircraft only for specific flight phases. Primary control 1. Introduction surfaces are generally built into the aircraft wings In the past, combat aircraft were designed using the and empennage. Typical primary controls include concept of static stability for safety. However, as the elevators on the horizontal tail, rudder on the technologies of aircraft developed and the vertical tail, and ailerons on the wings [3]. -
Recreational Flyer January - February 2010 Elevated: Angus Watt’S Ch-750
January - February 2010 Recreational Aircraft Association Canada www.raa.ca The Voice of Canadian Amateur Aircraft Builders $6.95 Elevated: Angus Watt's CH-750 Elevated: The original Zenith 701 was designed as an Angus Watt’s Ch-750 ultralight go-anywhere all metal bush plane that could be plans built by anyone with a 4 ft tabletop bending brake and a pair of snips. It was rarely described as a thing of beauty but so well does it fulfill its mission that these planes are found all over the world. They are inexpensive to construct, and because of their leading edge slats they can get in and out of extremely short patches of clear ground. 22 Recreational Flyer January - February 2010 Elevated: Angus Watt’s Ch-750 WITH THE ADVENT of the Light Sport category in and the only part interchangeable with the 701 is the US, Chris Heintz saw the need for an updated the signature Zenith all-flying rudder. Formerly the version, something with a larger cabin, greater skins were all .016” and they are now .020 to handle payload, and the ability to use an array of four the greater mass of the range of possible four stroke stroke engines. The CH 750 was the result and its engines and the 1320 pound gross weight on wheels, lineage is visually apparent but while the new plane 1430 on floats. resembles the 701 it is almost completely different in Chris Heintz correctly surmised that the US construction. CNC fabrication methods have made Light Sport category would be attractive to aging it possible to simplify the design, speed up the con- American pilots who wanted to bargain down to struction, and end up with a larger and faster plane their Sport Pilot category that allows a valid driver’s at only a slight weight penalty. -
10CAG/10CHG/10CG-2.4Ghz 10-CHANNEL RADIO CONTROL SYSTEM
10CAG/10CHG/10CG-2.4GHz 10-CHANNEL RADIO CONTROL SYSTEM INSTRUCTION MANUAL Technical updates and additional programming examples available at: http://www.futaba-rc.com/faq Entire Contents ©Copyright 2009 1M23N21007 TABLE OF CONTENTS INTRODUCTION ........................................................... 3 Curve, Prog. mixes 5-8 ............................................. 71 Additional Technical Help, Support and Service ........ 3 GYA gyro mixing (GYRO SENSE) ............................... 73 $SSOLFDWLRQ([SRUWDQG0RGL¿FDWLRQ ........................ 4 Other Equipment ....................................................... 74 Meaning of Special Markings ..................................... 5 Safety Precautions (do not operate without reading) .. 5 Introduction to the 10CG ............................................ 7 GLIDER (GLID(1A+1F)(2A+1F)(2A+2F)) FUNCTIONS . 75 &RQWHQWVDQG7HFKQLFDO6SHFL¿FDWLRQV........................ 9 Table of contents........................................................ 75 Accessories ............................................................... 10 Getting Started with a Basic 4-CH Glider ................ 76 Transmitter Controls & GLIDER-SPECIFIC BASIC MENU FUNCTIONS ........ 78 6ZLWFK,GHQWL¿FDWLRQ$VVLJQPHQWV ............................. 11 Model type (PARAMETER submenu) ........................... 78 Charging the Ni-Cd Batteries ................................... 15 MOTOR CUT ................................................................ 79 Stick Adjustments .................................................... -
DESIGN and ANALYSIS of PERFORMANCE PARAMETERS of WING with FLAPERONS Debanjali Dey, R.Aasha #Department of Aeronautical Engineering , KCG College of Technology
International Journal of Scientific Research and Review ISSN NO: 2279-543X DESIGN AND ANALYSIS OF PERFORMANCE PARAMETERS OF WING WITH FLAPERONS Debanjali Dey, R.Aasha #Department of Aeronautical Engineering , KCG College Of Technology. 1. [email protected] 2. [email protected] ABSTRACT- The main objective of this project is to design a flaperon for a wing and compare the performance characteristic of this flaperon-wing combination with that of conventional wing design that makes use of separate flap and aileron. Theoretical analysis and comparison is performed following which the computational analysis is carried out to validate the results. Further aim is to give a clarity on the fact that the use of this high lift device aids in improvising the aerodynamic characteristics of a wing by experimental testing of the wing design incorporated with flaperon, which is designed using a special methodology. Then, modification of wing design can be done to overcome the drawbacks of flaperons if any. INTRODUCTION - When looking at an aircraft, it is easy to observe that they have a number of common features: wings, a tail with vertical and horizontal wing sections, engines to propel them through the air, and a fuselage to carry passengers or cargo. If, however, you take a more critical look beyond the gross features, you also can see subtle, and sometimes not so subtle, differences. The reasons for these differences, why the designers configured them this way, is quite an intriguing study. Today, 100,000 flights will safely crisscross the planet. At no time in history have our lives been so global and full of possibility. -
Designing and Development of Unmanned Aerial Vehicle
ICAS 2002 CONGRESS DESIGNING AND DEVELOPMENT OF UNMANNED AERIAL VEHICLE MUHAMMAD ASIM Engineering Wing PAF Base Minhas PAKISTAN,43175 [email protected] DR ABID ALI KHAN Aerospace Engg Dept College of Aeronautical Engg Risalpur,24090 National University of Science and Technology [email protected] Keywords: UAV-Ip Abstract in direct combat. Even current high-tech UAV’s such as the Darkstar are limited to non- With the advancement in science and combative missions. In an age when the technology, the aviation industry is increasingly physiological tolerances and physical concentrating on the development of Remotely capabilities of the crew restrain the limits of Piloted Vehicles (RPVs), Unmanned Aerial performance of a modern fighter, the use of a Vehicles (UAVs) and Unmanned Combat Aerial UAV in a combat role deserves some Vehicles (UCAVs). The Unmanned Aerial consideration. Vehicle (UAV) are being used for many years for a variety of different tasks like reconnaissance, bomb damage assessment 2.0 Design Philosophy and Goals (BDA), scientific research, escort EW, decoying guiding SAMs and AAMs, and target practice. The principle goal in the UAV-Ip (Unmanned These UAVs will replace the conventional Aerial Vehicle - Interceptor) design process was aircraft in several roles and even perform novel to create an interceptor, which could super assignments. The hostile battlefield cruise to intercept a target in a minimal time at a environments and difficult access areas can be maximum possible range. The application of monitored without endangering human life. This this aircraft would be defensive in nature, when paper elaborate the designing of UAV that can conventional aircraft are immediately be used as interceptor and can perform unavailable or unable to deploy. -
KOKU-KAN-SANJI-504 Date: 09/18/20 No: KOKU-KAN-SANJI-449 Date: 08/17/21 No: KOKU-KAN-SANJI-276
(Unofficial Translation) Date: 09/27/18 No: KOKU-KAN-SANJI-614 Date: 08/23/19 No: KOKU-KAN-SANJI-504 Date: 09/18/20 No: KOKU-KAN-SANJI-449 Date: 08/17/21 No: KOKU-KAN-SANJI-276 Director of Air Transport Safety Unit Aviation Safety and Security Department Civil Aviation Bureau of Japan Ministry of Land, Infrastructure, Transport and Tourism Subject: The Detailed Regulations of the Technical Standard to Prevent Objects Falling off Airplanes 1. Purpose. Based on the provisions of the Technical Standard to Prevent Objects Falling off Airplanes (hereinafter referred to as “the Standard”) and in order to bring it into effect, the Detailed Regulations of the Technical Standard to Prevent Objects Falling off Airplanes (hereinafter referred to as “the Detailed Regulations”) is established as follows. 2. Applicability. The applicability of the Detailed Regulations is the same as the Standard. 3. Application for Licenses or Authorization. The application under the provisions of the Standard shall meet the following requirements. However, the operation manual or the maintenance manual of domestic air carriers may contain the following matters in lieu of the application matters. 3-1 Engineering management. 3-1-1 The operators must have a system to collect the information of falling objects, analyze and assess from the engineering aspect, and based on these results, develop countermeasures (inspection, maintenance and others) and implement them under 3-1 of the Standard. 3-1-2 The operators must nominate a person who is to be the supervisor of the system as referred to in the preceding paragraph, and take corrective actions properly under the supervision of the person. -
Section 1 Introduction
INSTRUCTION MANUAL FOR AIRPLANE AND HELICOPTER XP6102 6-CHANNEL COMPUTER RADIO SYSTEM TABLE OF CONTENTS TABLE OF CONTENTS TABLE OF CONTENTS ......................2 CHAPTER 1: SOFTWARE FUNCTIONS – AIRPLANE ................11 Transmitter Callouts ..................12 CHAPTER 1: USING THIS MANUAL • INTRODUCTION ..............6 Transmitter Rear ......................13 Using this Manual ....................6 Direct Servo Control (DSC) ........14 R770 Receiver ..........................6 Control Stick Tension Adjustment ..14 Control Stick Length Adjustment ..14 Frequency Notes/ CHAPTER 2: FEATURES ....................6 Aircraft Only Frequencies ..........15 X-6102 Transmitter ....................6 Base Loaded Antenna ..............15 Transmitter Specifications ..........7 Neck Strap Attachment ..............15 System Specifications ................7 CHAPTER 2: CONNECTIONS • CHAPTER 3: COMPONENT AIRPLANE ..................16 SPECIFICATIONS ............7 Installation Requirements ..........16 S537 Ball Bearing Servo ..............7 Connections ..........................17 Airborne Battery Pack ................8 Backup Error Display ................18 Charger Specifications ................8 Receiver Specifications ..............8 CHAPTER 3: INPUT MODE AND Servo Specifications ..................8 FUNCTION • AIRPLANE ....18 Charger ..................................9 Key Input and Display ..............18 Transmitter/Receiver ..................9 System Mode ..........................19 Normal Mode ..........................19 CHAPTER 4: BATTERY -
Phoenix Supplement
CONSUMER AEROSPACE Phoenix Rocket Launched R/C Aerobatic Glider Assembly and Operation Manual Supplement HIS sheet contains some recent additions to the Phoenix instructions. Please read them before you Tbegin construction of your Phoenix rocket glider. The following three items are very important, and must be done before you fly your Phoenix. Mandatory Additions Trim Rudder Horn Screws OU must trim the screws that Ymount the rudder horn flush with the outside of the nylon plate. If the screws are not trimmed, it is possible for them to hit the L-7 guides on the launcher during lift off. The rudder may be damaged if this happens. The screws may be cut after assembly with a razor saw or a cut off disc in a Moto-Tool. If you use a cut off disc, be very careful to keep the heat generated by the cut off disc from melting the nylon plate. Trim these screws flush with nylon plate Elevator Pushrod Stiffness HERE are 8 pieces of 3/16” square balsa strip provided in the kit. Before you start assembly, examine all T8 pieces. Due to the high speeds encountered during a Phoenix launch, the pushrods need to be both straight and stiff. The stiffest one should be used for the elevator pushrod, and the next stiffest one for rud- der. The remaining pieces are used for the fuselage corner stock. We use the stiffest balsa that we can obtain for the pushrods, but if you feel the pushrods provided in your kit are not stiff enough, please contact us and we will provide substitutes. -
3. Jet-Flap Interaction
Reducing Propulsion Airframe Aeroacoustic Interactions with Uniquely Tailored Chevrons: 3. Jet-Flap Interaction Vinod G. Mengle*, Leon Brusniak†, Ronen Elkoby‡ The Boeing Company, Seattle, WA 98124-2207 and Russ H. Thomas§ NASA Langley Research Center, Hampton, VA, 23681-2199 Propulsion airframe aeroacoustic (PAA) interactions, resulting from the integration of engine and airframe, lead to azimuthal asymmetries in the flow/acoustic field, e.g., due to the interaction between the exhaust jet flow and the pylon, the wing and its high-lift devices, such as, flaps and flaperons. In the first two parts of this series we have presented experimental results which show that isolated and installed nozzles with azimuthally varying chevrons (AVCs) can reduce noise more than conventional chevrons when integrated with a pylon and a wing with flaps at take-off conditions. In this paper, we present model-scale experimental results for the reduction of jet-flap interaction noise source due to these AVCs and document the PAA installation effects (difference in noise between installed and isolated nozzle configurations) at both approach and take-off conditions. It is found that the installation effects of both types of chevron nozzles, AVCs and conventional, are reversed at approach and take-off, in that there is more installed noise reduction at approach and less at take-off compared to that of the isolated nozzles. Moreover, certain AVCs give larger total installed noise benefits at both conditions compared to conventional chevrons. Phased microphone array results show that at approach conditions (large flap deflection, low jet speed and low ambient Mach number), chevrons gain more noise benefit from reducing jet- flap interaction noise than they do from quieting the jet plume noise source which is already weak at these low jet speeds. -
RV-12Is with This Form
Amateur-Built Fabrication and Assembly Checklist (2011) Fixed Wing NOTE: This checklist is only applicable to Name( s )...... .. ................. .Y.~~.~ ..~.,.~ g.~.f.!.. .................................... .................................. fixed wing aircraft. Evaluation of other types of aircraft (i.e., rotorcraft, balloons, ~.~~.'..~.~.~.:......... .......... ........1.1.~9 .!... ~~! .\. .'3- .?.~~.. ~... ~.~.~?.~~?. .9..~ ..?..?.9.~.? .... ......................... lighter than air) will not be accomplished Aircraft Model: RV-12iS with this form. Date: 6/13/2019 11 ········································· ··13u·11aerMa"iiii·a:1;··~red"iori·,r·re\ii"s"f ori· tr···c1afoa··········· ·········· NOTE: This checklist is invalid for and Remarks: 6/04/2019 will not be used to evaluate an altered or modified type certificated aircraft with the intent to issue an Experimental Amateur- Desk Audit performed by Micheal Sloat ASI/FAA comparing to RV 12 built Airworthiness Certificate. Such action Checklist dated 8/31 /2 010. violates FAA policy and DOES NOT meet the intent of § 21.191(g). Instructions For Using The Amateur-Built Fabrication and Assembly Checklist (2011): A point (each task equals 1 point) can be divided over multiple categories (Manufacturer, Commercial Assistance, Amateur Builder Assembly and Amateur Builder Fabrication) into 1/10 fractions. A Manufacturer may be a kit manufacturer, a component manufacturer or a part(s) manufacturer. Commercial assistance (for hire or compensation) may include assistance provided by kit manufacturers, commercial assistance centers, individuals (e.g. A&P mechanics or avionics technicians). For example, 0.5 (half point) can be assigned to the Manufacturer, 0.3 (3110 - 3 tenths) as Commercial Assistance, 0.2 to the Amateur Builder as Fabrication, for a total of 1 point. Enter "NIA" in any box where a listed task is not applicable to the particular aircraft being evaluated.