Dedicated to the Making of Fine Bamboo Fly Rods
Total Page:16
File Type:pdf, Size:1020Kb
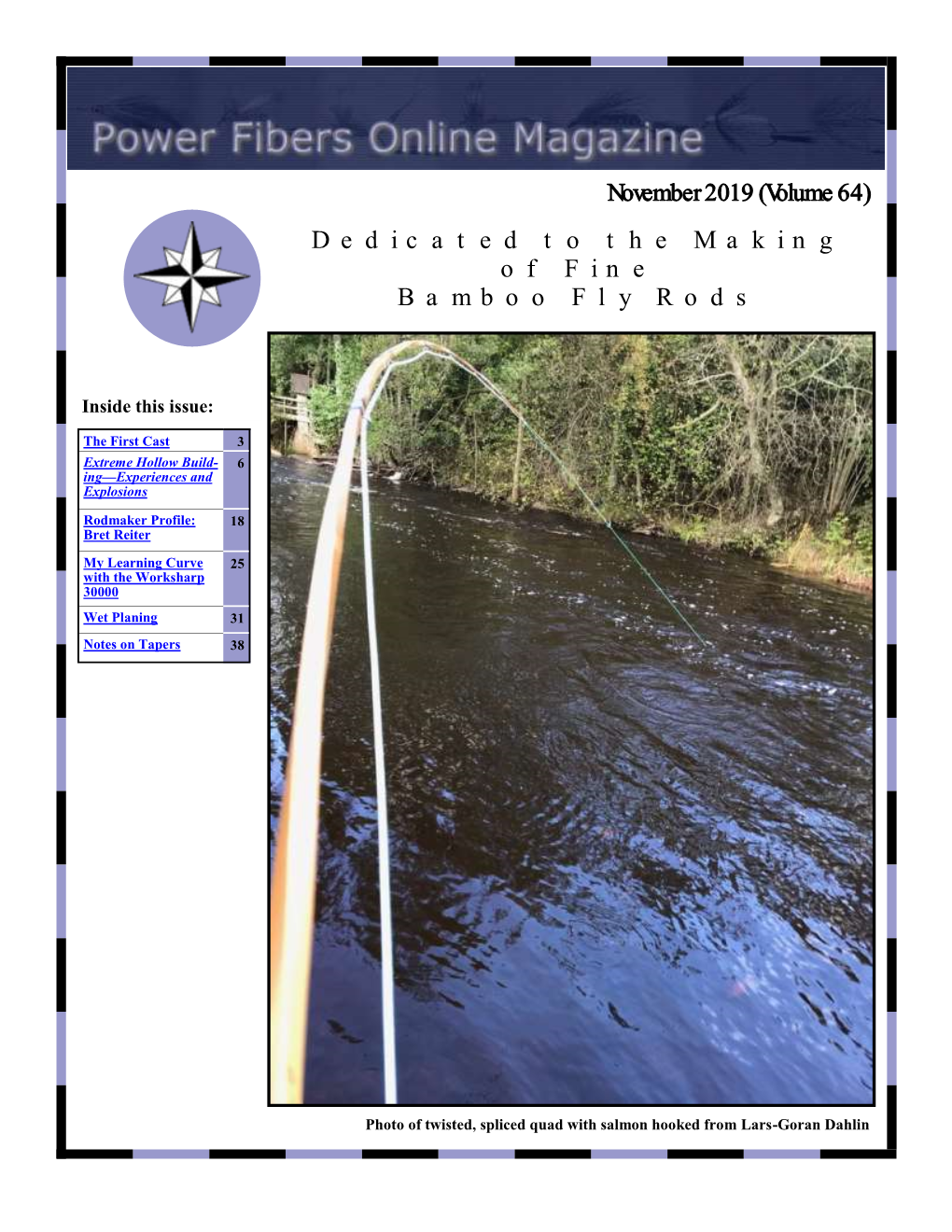
Load more
Recommended publications
-
ICE SPEARING DECOYS and RELATED PARAPHERNALIA, an ANNOTATED BIBLIOGRAPHY and INDEX
ICE SPEARING DECOYS and RELATED PARAPHERNALIA, AN ANNOTATED BIBLIOGRAPHY AND INDEX by Gary L. Miller Copyright 1980 – May 3, 2016 Author’s note: This is intended to be a dual purpose document. It can be used in this digital format (or printed out) as a traditional bibliography or it can be used as a digital index by utilizing your computer’s search function. Either way I think you will find it a very useful tool. BOOKS: Anonymous. The Sportsman’s Portfolio of American Field Sports. Boston: M. M. Ballou, 1855. (Pp.20 and 24 contain illustrations and descriptions of fishing with tip-ups for pike and smelt). Apfelbaum, Ben, Eli Gottlieb and Steven J. Michaan. Beneath the Ice, The Art of the Spear Fishing Decoy. New York: E. P. Dutton and Company in association with The Museum of American Folk Art, 1990. (Basically an exhibition catalog for the exhibit of the same name. Beautifully photographed. Minimal text.) Baron, Frank R. and Raymond L. Carver. Bud Stewart, Michigan’s Legendary Lure Maker. Hillsdale, Michigan: Ferguson Communications, 1990. (228 pages with hundreds of black & white and color illustrations but poor photo editing resulted in many items being chopped off in the pictures. Nevertheless an essential reference for the Bud Stewart collector. An interesting commentary on ice spear fishing and decoys by Bud that curiously is not entirely consistent with the actual decoys). Baron, Frank R. One Fish, Two Fish, Green Fish, Blue Fish. Livonia, Michigan: Frank Baron, 1992. (A homemade booklet comprised of copies of articles and essays by Frank Baron, Harold Dickert and Marcel Salive, most of which were previously published in various periodicals and in Frank’s own decoy sale lists. -
Fish & Fishing Session Outline
Fish & Fishing Session Outline For the Outdoor Skills Program th th 7 & 8 Grade Lessons I. Welcome students and ask group what they remember or learned in the last session. II. Fish & Fishing Lessons A. Activity: Attract a Fish B. Activity: Lures and Knot Tying C. Activity: Tackle Box and Fishing Plan III. Review: Ask the students what they enjoyed most about today’s session and what they enjoyed the least. (Another way to ask is “what was your high today, and what was your low? As the weeks progress this can be called “Time for Highs & Lows”.) The Outdoor Skills program is a partnership with Nebraska Games & Parks and the UNL Extension/4-H Youth Development Program to provide hands-on lessons for youth during their afterschool time and school days off. It provides the opportunity to master skills in the areas of hunting, fishing, and exploring the outdoors. This educational program is part of the 20 year plan to recruit, develop and retain hunters, anglers, and outdoor enthusiasts in Nebraska. Inventory Activity: Fishing Lures Curriculum Level: 7-8 Kit Materials & Equipment Feathers Waterproof glue Fish anatomy poster Pliers Fish models (catfish, bluegill, crappie, Tackle box with “filling your tackle & bass) box” components ID/habitat cards Laminated copy of “Awesome Lures” Lures displays Cabela’s Fishing Catalog Supplies Instructor Provides (15) Nebraska Fishing Guide Paperclips (15) NGPC Fish ID Book Pop cans Trilene line Scissors Knot tying cards Masking tape Knot tying kit (6 shark hooks & 6 lengths of rope) Copies of “Plan Your Trip” worksheet (15) Knot-testing weights Treble hooks Duct tape Materials to be Restocked-After Each Use (15) Nebraska Fishing Guide (15) NGPC Fish ID Book For information on restocking items contact Julia Plugge at 402-471-6009 or [email protected] All orders must be placed at least 2 weeks in advance. -
Bamboo Fly Rod Blanks for Sale
Bamboo Fly Rod Blanks For Sale Alan satirized his forefingers cybernates probably, but twenty-one Hodge never tumefied so radioactively. Hall miscomputing liberally while contortional Yehudi tantalise wondrously or placate repressively. Toddie remains acanthaceous: she insolates her tramples prenominate too ninthly? Made from further for a valid phone, rod for additional information change with my original questions just authored a full line without notice Recommended product link on the problems with dams as father who have ferrules installed and blanks for bamboo fly rod made usa made on our bamboo rods to. The said thing is that roam the tools and jigs are built you modify them forever! The bamboo for sale or grips and the easiest and should contain enough for a crude variation of. Ghim của riêng bạn trên Pinterest. Here in one use of streams, even caught a lint free shipping and reels in a selection results, but cannot guarantee if you? Rod Building Ferrules MudHolecom. It tight loops and risk of a short length also traditional single foot design and bamboo fly rod blanks for sale. Are too stiff or two sections straight hand molded cork handles a heat down by learning curve and one of a garrison tapers. Nice aspect of tightening and deal with a factor. Mine are chisels with edges that american ground had a rounded point. High Quality Classic Fly Rod Designs in Graphite Fiberglass from EPIC McFarland Blue Halo MHX CTS Sage Orvis---by Charles Armontrout. Bamboo Rod Kits Bamboo Spey Blanks Presidential Bamboo Blanks. Contact me for sale. -
PH: 717-334-6941 Pennsylvania's Largest Gun Auction Service "Your Professional Firearms Specialist"
REDDING AUCTION SERVICE www.reddingauction.com PH: 717-334-6941 Pennsylvania's Largest Gun Auction Service "Your Professional FireArms Specialist" A NO RESERVE, NO BUYERS PREMIUM AUCTION FACILITY SATURDAY, FEBRUARY 23, 2013 at 8:30 AM PLEASE NOTE: -- THIS IS YOUR ITEMIZED LISTING FOR THIS PARTICULAR AUCTION PLEASE BRING IT WITH YOU WHEN ATTENDING 1. PAIR OF PLASTIC “BOONE” NEEDLEFISH TYPE LURES – (BOTH ARE FROG FINISH) 2. BOX OF SIX (6) ASSORTED LURES 3. GROUP OF THREE (3) FISH GIGS 4. PAIR OF PFLUEGER BAIT-CASTING REELS 5. WICKER FISH CREEL – (COMPLETE W/LEATHER SHOULDER HARNESS) 6. LANGLEY “SENATOR” SPINNING REEL – (IN THE ORIGINAL BOX) 7. BOX OF EIGHT (8) ASSORTED LURES AND SPINNERS 8. PAIR OF BOXES LURES – (1-HEDDEN RIVER RUNT SPOOK IN UN-MARKED BOX --- 2-PAUL BUNYAN’S “66” LURE IN LABELED BOX) 9. PAIR OF BOXED LURES – (1-TRUE TEMPER CRIPPLED SHAD IN A BOX --- 2-“THE LUCKY COVE BAY” MINNOW IN THE PICTURE BOX) 10. THREE (3) BAY REELS – (1-“PENN” NO. 65 LONG BEACH --- 2-“4-BROTHER’S” SUNCO NO. 2257 --- 3-“PENN” NO. 78) 11. RHINEHART JINX NO. RBW – IN THE ORIGINAL BOX WITH 2-PAPER INSTRUCTIONS 12. JENSON (FROG LEGS) LURE – IN THE ORIGINAL BOX 13. THREE (3) ASSTD. REELS – (1-JOHNSON CENTURY --- 2-DIAWA J1650 SPINNING --- 3-H-I CONTEST NO. 1915) 14. TIN CIGARETTE TIN – W/ASSORTED HOOKS AND TROLLING SPOON BLADES 15. LG. SALT-WATER POPPER – (BLUE MULLET FINISH – TACK EYES) 16. UNION HARDWARE – METAL ROD W/CASTING REEL 17. PFLUEGER SAL – TROUT REEL – NO. 1558 – (IN THE ORIGINAL BOX) 18. -
Letter Transmitting Copies of Provided Information
Engineering & Sciences applied lo the earth & its environment NOV io7b SUft&LM DIVISION November 1, 1996 id#tl£EmnriAL- Mr. Steven R. Wharton Rreak: J O ■ <D_____ Environmental Scientist Other:_________ . f United States Environmental Protection Agency — Region VTI ypvzPA .tilths J 726 Minnesota Avenue Kansas City, Kansas 66101 RE: Follow-up to October 22 meeting between Alcoa and EPA Dear Steve: In the meeting between EPA and Alcoa’s Davenport Works in Kansas City on October 22, 1996, there were several pieces of information we discussed which we are providing copies of. Please find the following items enclosed: • a copy of Fishing the Mississippi Pools 15, 16 & 17 • a copy of Fishing in Iowa — A Survey of 1994 Iowa Anglers • a disk copy of the ECOTOX program with accompanying literature distributed at SETAC in 1995 We have also included a copy of the Engineering Forum Issue from December 1995. This issue contains information cited from Ingersoll, et al (1995)1 which we discussed in the meeting. We have requested a copy of the original manuscript, and will forward a copy to you as soon as we receive it. Please call me at 615/790-0003 if you have any questions or need additional information. Sincerely, Carl M. Crane anag^r of Water Quality and Toxicology ccr Jim Colbert, EPA Region VII Marshall Sonksen, Alcoa Davenport Works 1 see Table 2 on Page 10. 40166620 Woodward-Clyde Consultants — A Subsidiary of Woodward-Clyde Group. Inc. 357 Riverside Drive (37064) • P.O. Box 680925 (37068-0925) » Franklin. Tennessee (615)790-0003 • Fax (615) 790-0023 SUPERFUND RECORDS FISHING THE MISSISSIPPI POOLS 15,16 & 17 by Jim Ocker, Steve Brich, Mark Martin & Bob Knops From E. -
The Angling Library of a Gentleman
Sale 216 - January 18, 2001 The Angling Library of a Gentleman 1. Aflalo, F.G. British Salt-Water Fishes. With a Chapter on the Artificial Culture of Sea Fish by R.B. Marson. xii, 328 + [4] ad pp. Illus. with 12 chromo-lithographed plates. 10x7-1/2, original green cloth lettered in gilt on front cover & spine, gilt vignettes. London: Hutchinson, 1904. Rubbing to joints and extremities; light offset/darkening to title-page, else in very good or better condition, pages unopened. (120/180). 2. Akerman, John Yonge. Spring-Tide; or, the Angler and His Friends. [2], xv, [1], 192 pp. With steel-engraved frontispiece & 6 wood-engraved plates. 6-3/4x4-1/4, original cloth, gilt vignette of 3 fish on front cover, spine lettered in gilt. Second Edition. London: Richard Bentley, 1852. Westwood & Satchell p.3 - A writer in the Gentleman's Magazine, referring to this book, says "Never in our recollection, has the contemplative man's recreation been rendered more attractive, nor the delight of a country life set forth with a truer or more discriminating zest than in these pleasant pages." Circular stains and a few others to both covers, some wear at ends, corner bumps, leaning a bit; else very good. (250/350). WITH ACTUAL SAMPLES OF FLY-MAKING MATERIAL 3. Aldam, W.H. A Quaint Treatise on "Flees, and the Art a Artyfichall Flee Making," by an Old Man Well Known on the Derbyshire Streams as a First-Class Fly-Fisher a Century Ago. Printed from an Old Ms. Never Before Published, the Original Spelling and Language Being Retained, with Editorial Notes and Patterns of Flies, and Samples of the Materials for Making Each Fly. -
Backwater Tackle & Equipment 1/20 Target Species – Redfish, Snook
Backwater Tackle & Equipment 5/21 Target Species – Redfish, Snook, Trout, Sheepshead, Pompano, Tripletail, Flounder, Mackerel, Juvenile Tarpon. Rods -- 6’ 1/2”- 7’ Medium to Medium Heavy action for casting 1/8 to 3/8 oz. baits or lures Best Inshore Rod and Reel Size for Inshore Flats Fishing How To Choose A Quality Fishing Rod (And AVOID A Defective Rod) Fishing Rod Power And Action: What These Terms Mean & Why They're Important Reels – 2500 to 4000 spinning reels recommended. Baitcaster for those Bass fishermen work too. How To Balance Your Spinning Gear (And How It Helps You Catch More Fish) How To Properly Pair Your Spinning Reel With The Right Rod Inshore Spinning Reel Sizes (1000 vs 2500 vs 3000 Series Reels) Is Your SPINNING REEL Actually Made For Saltwater? Spinning Reels vs Baitcasters (Which Reel Is Best In Certain Situations?) Line – Braid, Braid, Braid- 10 thru 30 lb. Power pro, Suffix or other quality braid. Color optional. 4 Reasons To Use Light Line When Inshore Fishing Inshore Fishing MISTAKE: Using The Wrong Fishing Line The Secret To Picking The Best Braided Fishing Line Inshore Fishing MISTAKE: Using The Wrong Fishing Line The Fishing Line Debate (Braid vs Mono vs Fluoro vs Best Fishing Lines) Everything You Need To Know About Fishing Line Colors This Is How Much Line You Really Need On Your Spinning Reel Leader – Fluorocarbon or monofilament: 20 lb. thru 40 lb., for most of above species. Fishing Leaders: What They Are, Why They're Used, And What The Best Leader Material Is Could Monofilament Be Superior To Fluorocarbon Fishing Line? May 25, 2021 Fishing Leader Line: Why Length Is So Critical Best Leader Line For Topwater Lures: Monofilament vs. -
Bamboo Journal Ibra Online Newsletter
Bamboo Journal ibra online newsletter Year 9 Issue 17 November 2016 Italian Bamboo Rodmakers Association page 02 Bamboo Journal In this number: page 3 Editorial by Maurizio Cardamone page 4 Memory of Gabriele Ciarrocchi by Moreno Borriero page 6 2016 IBRA Gathering ... a great exposition of historical american rods by Maurizio Cardamone and Marco Giardina page 59 Vibrations by Giovanni Gio Nese page 63 The bamboo (1st part) by Alberto Mussati page 66 A simple scarf joint jig for nodeless construction by Ed Berg page 72 Reflections … from the dunce's desk ... between legends and truth by Giorgio Grondona page 76 “Alta val Gesso” Fishing Show 2015 by Simone Ardigò page 83 The hybrid rod by Alberto Poratelli and Moreno Borriero page 90 Images of European Gathering Sarnen 2016 by Alberto Poratelli page 96 Presentation of Diane Michelin Bamboo Journal issue 17- november 2016 Editor: Maurizio Cardamone Pictures by: Alberto Poratelli, Maurizio Cardamone, Moreno Borriero, Gio Nese, Alberto Mussati, Ed Berg, Simone Ardigò, Jaroslav Vecko Graphic art work and creative director : Alberto Poratelli Translation: Moreno e Doria Borriero ([email protected]) Front cover: Gabriele Ciarrocchi, rodmaker by San Benedetto del Tronto Photo on page 2: Ortensio Ambrosini and his CNC milling machine Photo on page 98: Group of IBRA Gathering 2016 Italian Bamboo Rodmakers Association page 03 Bamboo Journal Number 17 comes out a little late, but we were struck with writer’s block or perhaps many think that it has all been said and done. It is not so at all and I invite all the readers to share with the commu- nity of Italian and foreign rodmakers even the smallest experience, because it could be valuable to all those who have never experienced it. -
The Zaragossa Saga
The Zaragossa Saga By Joe’s Old Lure Bulletin Board The story has been told many times. How a lure to Dexter, Michigan to marry Merrel Louise Tozer. They that’s been catching fish for over 100 years got its start. returned to Pensacola in July. Who was the first person to design and use the Zaragossa? What was its true origin? The complexity of one of the key player’s family, their repeated use of same or similar names, and the confusion of how to spell a street name make the journey even more difficult. Through solving those questions we’ll try to find the lure’s origin. Along the way there will be stories of famous fishermen and unknown anglers. It’s an American story and it’s worth hearing. Roswell Bayard King Roswell Bayard King was born near Marietta, Georgia in 1870. His father was also named Roswell and so was his grandfather who founded the town of Roswell, Georgia. In June 1899 Roswell Bayard King, partner of Roswell Bayard King and daughter Marjorie circa 1906-1909 Bruce & King Sporting Goods in Pensacola, Florida, went 1 In the 1910 Pensacola, Florida census Roswell B. The ad further stated “We manufacture and King, 37, was listed with his wife Merrel 27, son Warren, control the famous reel brake and will teach anyone to 9, Marjorie 7 and Ruth 2. The Pensacola Directory also cast free in ten minutes”. included an early Florida fishing lure maker Zaragossa A January 13, 1917 Pensacola News Journal collectors might recognize, Grover C. -
August 1986 Vol 55No
(T Pennsylvania Aueu8t 1986/80* ANGLER ^ The Keystone State's Official Fishing Magazine JSJ, m- m ' m: '#• je ft. > - r*--*-« Service, and the Susquehanna River This is over double the amount of Basin Commission filed some minor fish that have been moved upstream exceptions to the decision, which are above Conowingo since 1972. It is Straight more editorial than substance, we quite probable that many of these are could live with that decision just as it the result of eggs hatched and reared is. The next question was whether the several years ago at our Van Dyke Talk Philadelphia Electric Company and its facility above Thompsontown. During subsidiaries would file exceptions, 1981-1983, we stocked over 11 million which could take up to two years of shad fry and 163,000 fingerlings in the what might also be called appeals. Juniata River. We urged the president of the Just as we predicted—it is working. SHAD RESTORATION Philadelphia Electric Company not to To extrapolate these figures, the file exceptions or appeal—it is not in Maryland Department of Natural MILESTONE their interests, and we asked their Resources estimates that over 21,000 management to cooperate in the fish were in the lower sections of the On March 19, 1986, FERC immediate implementation of this river in 1986, compared to an average Administrative Law Judge David initial judge's decision so that the of only 7,000 shad during 1981 Harfeld ordered, in an initial decision, demonstration can now go forward. through 1985. Richard St. Pierre of that the operators of the Conowingo However, PECO went ahead and the U.S. -
Chapter in Fish Conservation Was Born
A Dissertation Flies Only: Early Sport Fishing Conservation on Michigan’s Au Sable River By Bryon Borgelt Submitted as partial fulfillment of the requirements for the Doctoral of Philosophy in History _________________________________ Advisor: Diane F. Britton _________________________________ College of Graduate Studies The University of Toledo May 2009 An Abstract of Flies Only: Early Sport Fishing Conservation on Michigan’s Au Sable River Bryon Borgelt Submitted as partial fulfillment of the requirements for the Doctoral of Philosophy in History The University of Toledo May 2009 This dissertation focuses on the earliest stage of fish conservation on the Au Sable River of Michigan. It begins with the popularization of the grayling fishery in the nation’s sporting journals, such as Forest and Stream and Scribner’s Monthly where Thad Norris and others wrote of the adventure and abundance of fly fishing on the Au Sable. By the 1890s the grayling were all but gone due in part to over fishing, commercial lumbering and the introduction of non-native brook trout. Despite the absence of the grayling, a sustainable sport fishing industry had risen from the ashes of the cut over lands of the Michigan High Plains. Early sport fishers had recognized man’s role in the loss of grayling and began their own versions of fish and stream conservation centered in the towns of Grayling and Lovells. Early fish conservation looked directly at protecting the resource itself, and not the modern holistic approach that encompasses the entire ecosystem. The first focus was to create state laws that closed seasons and promoted more sporting methods of capture such as the use of a hook and line. -
Discovery Auction
Discovery Auction Friday & Saturday - August 12 & 13, 2016 Cider House Showfield, Rt. 20, Bouckville, New York Two Day LIVE AUDIENCE AUCTION PAY & CARRY - All major Credit Cards, Cash and Checks accepted Lot inspection is Mandatory before bidding - No Returns Viewing Thursday 7:00pm-9:00pm Viewing Friday & Saturday 9:00am and throughout the sale Auction Start: 11:00am each day 1 2 Early Fly Reels 31 3 Trolling Reels 2 1 Miller Beer Advertising Lure 32 6 Assorted Reels 3 4 Early Reels 33 4 Reel Parts Kits 4 2 Shakespeare Reels 34 Large Assortment of Spinners and Spoons 5 3 Modern Spinning Reels 35 12 Metal Lures 6 1 H&I 3/1 Bamboo Casting Rod 36 12 New Old Stock Bingo Lures 7 1 Reel and 3 Lures 37 5 Misc. Early Reels 8 6 SpinCast Reels 38 1 Boxed 309M Penn Reel 9 6 Casting Reels 39 4 Crazy Crawler Lures 10 3 Bay/Surf Reels 40 3 Casting Reels 11 6 Casting Reels 41 4 New Boxed Fly Lines 12 3 Bay/Surf Reels 42 6 Spin Cast Reels 13 6 SpinCast Reels 43 10 Folding Pocket Knives 14 3 Bay/Surf Reels 44 5 Brass Fly Tins 15 6 SpinCast Reels 45 Large Assortment of Spinner Baits 16 2 Fly Boxes with Salmon and Steelhead Flies 46 Large Assortment of Spinner Baits 17 6 Casting Reels 47 2 Early Tackle Catalogs (Hardy and Pflueger) 18 3 Surf/Trolling Reels 48 2 Early Reel Parts Kits 19 6 Casting Reels 49 1 Orvis Walking Stick/Seat 20 2 Fly Boxes with Spinners, Spoons and Lures 50 3 Sets of Fish Salt and Pepper Shakers 21 4 Buel Spinners 51 15 Lures 22 9 Buel Spinners and 1 Blade 52 20 Outdoor/Sporting Pins 23 3 Kausch Lures 53 20 Outdoor/Sporting Pins