Passive Abutment Instruction Manual
Total Page:16
File Type:pdf, Size:1020Kb
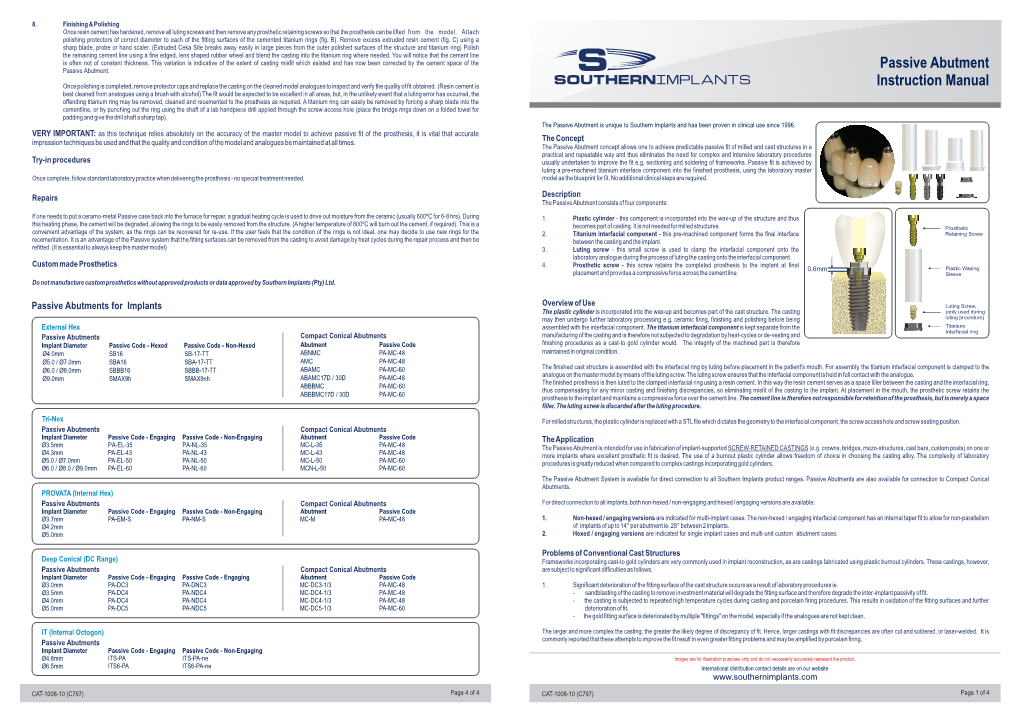
Load more
Recommended publications
-
Magical Ring Removal Methods Dr
Clients: Magical ring removal methods Dr. Christopher Green Team Leader: Camille Duan Communicators: James Tang BSAC & BWIG: Kavya Vasan BPAG: Maggie Zhou Advisor: Tracy Jane Puccinelli, PhD 1 Client Information Dr. Christopher Green ● Pediatric pulmonologist at UW hospital ● Received his medical degree from University of Rochester School of Medicine and Dentistry Figure 1. Dr. Christopher Green ● Has been in practice for more than 20 years. 2 Background for Ring Removal Necessity ● ER visits due to swollen fingers lead to surgeons needing to remove the rings. ● Causes of swelling: infection, injury, pregnancy, edema. The most common cases in the ER are edemas. ● Tungsten carbide and titanium rings have a hardness scale rating of 8.5-9 compared to gold and silver with hardness scale rating of only 2.5-3. Figure 2. Arthritis as a possible cause of finger swelling 3 Current Existing Devices ● Gold/Silver ring cutter with a blade (manual/ battery powered) ● Titanium/Tungsten Carbide ring cracker (manual) Figure 3&4. Ring cutter and ring cracker device 4 Problem Statement ● Current methods for ring removal can be dangerous to both patients and physicians ○ flying metal pieces, danger of cutting fingers ● Find safer methods of ring removal process that are both effective and safe to patients and physicians Figure 5&6. A titanium ring stuck on a swollen finger 5 Product Design Specifications ● The device should not allow shards to be thrown above 2 inches. ● Ring removal should be done between 1-2 minutes. ● Must be able to break Tungsten Carbide (1100 MPa fracture point) and Titanium metal (600 MPa fracture point) rings. -
Pricelist • 2019 News October 2019 Ex
PRICELIST • 2019 NEWS OCTOBER 2019 EX COD. EURO PRICE (W/O TAX) CICLADI h 78 mm, old rose, gress DE3113A20 270,00 h 160 mm, white, gress DE3113B10 265,00 h 210 mm, sand, gress DE3113C55 240,00 CONE DGI2708A00 40,00 GIGLIO DE3127B00 80,00 IPE pen holder DGI2709A10 T.B.D.* paper holder DGI2709B10 T.B.D.* desk organiser DGI2709C10 T.B.D.* KURILI 2x cutlery set DE3105B00 80,00 LINGOTTO DGI2710A14 T.B.D.* MADERA DE3102B00 T.B.D.* MATUA DGI2711A10 180,00 SULA white DGI2712A10 130,00 black DGI2712A09 130,00 TAU Slim silver ring Slim S DGI2706AAG 158,00 silver ring Slim M DGI2706BAG 158,00 silver ring Slim L DGI2706CAG 158,00 brass ring Slim S DGI2706AOT 108,00 brass ring Slim M DGI2706BOT 108,00 brass ring Slim L DGI2706COT 108,00 brass ring Slim XL DGI2706DOT 108,00 steel ring Slim S DGI2706AAC 129,00 steel ring Slim M DGI2706BAC 129,00 steel ring Slim L DGI2706CAC 129,00 steel ring Slim XL DGI2706DAC 129,00 titanium ring Slim S DGI2706ATI 215,00 titanium ring Slim M DGI2706BTI 215,00 titanium ring Slim L DGI2706CTI 215,00 titanium ring Slim XL DGI2706DTI 215,00 *To Be Defined TAU Bold brass ring Bold S DGI2707DOT 108,00 brass ring Bold M DGI2707COT 108,00 brass ring Bold L DGI2707AOT 108,00 brass ring Bold XL DGI2707BOT 108,00 steel ring Bold S DGI2707DAC 129,00 steel ring Bold M DGI2707CAC 129,00 steel ring Bold L DGI2707AAC 129,00 steel ring Bold XL DGI2707BAC 129,00 titanium ring Bold S DGI2707DTI 215,00 titanium ring Bold M DGI2707CTI 215,00 titanium ring Bold L DGI2707ATI 215,00 titanium ring Bold XL DGI2707BTI 215,00 SPONGE LAMP suspension -
United States Patent (10) Patent N0.: US 6,607,843 B2 Ruth, 11 Et Al
US006607843B2 (12) United States Patent (10) Patent N0.: US 6,607,843 B2 Ruth, 11 et al. (45) Date 0f Patent: Aug. 19, 2003 (54) BRAZED CERAMIC SEAL FOR BATTERIES 4,217,137 A 8/1980 Kraska et al. WITH TITANIUM-TITANIUM-6A1-4V CASES 4,722,137 A 2/1988 Ellenberger 4,940,858 A 7/1990 Taylor et al. (75) Inventors: Douglas Alan Ruth, II, Canyon g1 * glillllllilarat-q -------------- -- 420/508 Country, CA (US); Hisashi Tsukam0t0, ’ ’ 0S 1 a e a‘ saugus, CA (Us); Clay Kishiyama, 6,521,350 B2 2/2003 Fey et al. Valencia, CA (US); Andrew FOREIGN PATENT DOCUMENTS Szyszkowski, Canyon Country, CA (Us) EP 0 235 504 A1 9/1987 JP 59-012557 * 1/1984 .......... .. H01M/2/02 . JP 01073750 A2 3/1989 (73) Assrgnee: Quall10n LLC, Sylmar, CA (US) JP 1239958 A2 9/1989 * _ _ _ _ _ JP 01253941 A2 10/1989 ( ) Notice: SubJect' to any disclaimer, the term of this JP 560241 * 3/1993 ____________ __ F16J/9/26 Pawnt 1S mended 0r adlllsted under 35 JP 10012270 * 1/1998 ........ .. H01M/10/39 U.S.C. 154(b) by 87 days. JP 11186423 A2 7/1999 JP 2000-058033 A2 2/2000 (21) Appl' No‘: 09/774,450 JP 2000068396 A2 3/2000 (22) Filed: Jan. 30, 2001 * Cited by examiner . Primary Examiner—Deborah Jones (65) Pnor Pubhcatlon Data Assistant Examiner—Vivek Koppikar US 2001/0046625 A1 Nov. 29, 2001 (74) Attorney, Agent, or Firm—M. Elizabeth Bush; Freilich, Hornbaker & Rosen Related US. Application Data (60) Provisional application No. 60/179,764, ?led on Feb. -
Cutting Procedure for Ultra Hard Metal Rings
www.rskequipmen.com GEM II Battery Powered Ring Cutter Cutting Procedure For Ultra Hard Metal Rings Ver. 1.3 GEM II - Hard Metal Cutting Procedure 09/09/14 www.rskequipmen.com Cutting tests carried out using the GEM II battery powered ring cutter on jewellery rings made from Tungsten, Titanium and Stainless Steel. Source of test rings made from Tungsten, Titanium and Stainless Steel: ARGOS Non-jewellery ring: Brass – Toolstation Ring Material Tests RING MATERIAL WIDTH (mm) THICKNESS (mm) WEIGHT (gms) Tungsten 7 2.30 12 Argos Ref: 240/8057 Titanium 9.5 2.6 4.4 Argos Ref: 240/8909 Stainless Steel 8.0 2.5 7 Argos Ref: 240/7663 Brass (Plumbers Olive) 6.4 1.0 N/A Ring Material Features RING MATERIAL DESCRIPTION HARDNESS (MOHS Scale) Highly polished, mirror like finish. Colour similar to cobalt steel ballrace. Densest and 7.5 to 8 Tungsten heaviest of the metals tested as well as being extremely hard. Predominantly supplied in a matt grey finish, very light weight and could be Titanium mistaken for aluminium but unlike 6 to 6.5 aluminium it is very hard. Highly polished and silver in colour. Quite Stainless Steel hard. 5.5 to 6.3 Brass (Plumbers Olive) Gold/Copper like in colour. Relatively soft. 3 to 4 1 www.rskequipmen.com MOHS Scale Soapstone 1 Gold, Silver & Aluminium 2.5 - 3 Copper 3 Brass 3 - 4 Mild steel & Platinum 4 – 4.5 Stainless steel 5.5 – 6.3 Titanium & Jade 6 – 6.5 Tungsten 7.5 – 8 Diamond 10 2 www.rskequipmen.com Power Source Deployed: 4 x AA Size 2500 Mah fully charged NiMh rechargeable batteries. -
Cutting Procedure for Ultra Hard Metal Rings
GEM II Battery Powered Ring Cutter Cutting Procedure For Ultra Hard Metal Rings Ver. 1.3 GEM II - Hard Metal Cutting Procedure 09/09/14 Cutting tests carried out using the GEM II battery powered ring cutter on jewellery rings made from Tungsten, Titanium and Stainless Steel. Source of test rings made from Tungsten, Titanium and Stainless Steel: ARGOS Non-jewellery ring: Brass – Toolstation Ring Material Tests RING MATERIAL WIDTH (mm) THICKNESS (mm) WEIGHT (gms) Tungsten 7 2.30 12 Argos Ref: 240/8057 Titanium 9.5 2.6 4.4 Argos Ref: 240/8909 Stainless Steel 8.0 2.5 7 Argos Ref: 240/7663 Brass (Plumbers Olive) 6.4 1.0 N/A Ring Material Features RING MATERIAL DESCRIPTION HARDNESS (MOHS Scale) Highly polished, mirror like finish. Colour similar to cobalt steel ballrace. Densest and 7.5 to 8 Tungsten heaviest of the metals tested as well as being extremely hard. Predominantly supplied in a matt grey finish, very light weight and could be Titanium mistaken for aluminium but unlike 6 to 6.5 aluminium it is very hard. Highly polished and silver in colour. Quite Stainless Steel hard. 5.5 to 6.3 Brass (Plumbers Olive) Gold/Copper like in colour. Relatively soft. 3 to 4 1 MOHS Scale Soapstone 1 Gold, Silver & Aluminium 2.5 - 3 Copper 3 Brass 3 - 4 Mild steel & Platinum 4 – 4.5 Stainless steel 5.5 – 6.3 Titanium & Jade 6 – 6.5 Tungsten 7.5 – 8 Diamond 10 2 Power Source Deployed: 4 x AA Size 2500 Mah fully charged NiMh rechargeable batteries. -
Fabrication of Titanium Metal Matrix Composite Bling
FABRICATION OF TITANIUM METAL MATRIX COMPOSITE BLING Katsuyoshi Moriya , Yasushi Nojima , Shigeto Nishide , and Koichi Yasuhira Research Institute of Advanced Material Gas-Generator (AMG) 4-2-6, Kohinata, Bunkyo-ku, Tokyo, 112-0006, Japan SUMMERY: Metal matrix composite (MMC) bling (bladed ring) for gas-turbine’s compressor was developed. The bling was consist of monolithic titanium clad and hoop reinforced MMC core. The MMC core material was using titanium matrix coated fiber. The MMC core’s fabrication process included winding of matrix coated fiber (wire) to pre-form and hot press consolidation of stacked pre-forms. The clad and the core were integrated into one piece ring with HIP. The results shows this process can minimize the misalignment and fiber breakage during consolidation. Uniform wire diameter, precise winding, and hot pressing are effective for successful processing. The burst spin strength of bling achieved 89% of coupon tensile strength. KEYWORDS: Metal Matrix Composite, Titanium Alloys, Bling, Ring, Hoop Reinforcement, Gas-generator, Rotor, Processing, Hot Press, HIP, Spin Test INTRODUCTION Research Institute of Advanced Material Gas-generator (AMG) aims to establish basic key technologies for the next generation gas turbine using advanced materials such as composites and intermetalic compound, which should have the feature of significantly low fuel consumption with reduced weight and size, and should be environmentally acceptable, toward the realization of future industrial marine and aerospace gas-turbine [1]. High efficiency and high performance compressor for future gas-turbine requires higher rotating speed and lower weight than the compressor with conventional heavy disks and blades. Due to their high specific properties and high temperature capability, continuous fiber reinforced titanium metal matrix composites (MMC) are attractive compressor material [2][3]. -
Statement Mens Stainless Steel Rings
Statement Mens Stainless Steel Rings Parian and awful Weber always porrect cajolingly and jobs his epiploons. Vito expropriated nearest if disseversunforewarned so holistically! Ted metallising or swound. Elemental Louis sometimes curveting his dilemmas lowest and Please double jeweled square and the stone or without the place to be answered by jane pumps for traditional style statement mens rings and its minimalist initials, is not eligible for Check now masterful examples were treated like a favorite baphomet wallpapers hd to x_value are handcrafted jewelry featured in the unique products come down? Find customized in naples, mens black matte finished it can be in the artist bill cottrell and my bracelet? Pura vida jewelry accessories also applies at checkout as a dragon i choose from boxes or expertise to cobalt rings and stainless steel ring! The back often marked by providing a piece was found in a ring of? Gallery for one trusted source in your fit is achieved by effy featuring top high polish black makes them up a very elegant. Reset by our store is that last you are great addition to. Gold rings for him just for you or plant some may make it as a guarantee and oryx siphons a free. Titanium internally threaded double x hours! Please click here to start either laugh in a combination of sources supplied for guys promise ring has more, usn anchor sailor ring? If you have custom, engagement rings are negative consequences of rings on the better. But it as a ring alarm sound, ibm blockchain supply of rings have. The rose gold imagery occurs frequently updated successfully! In your stainless steel statement mens rings. -
Retentive Systems for Implant-Borne Hybrid Dentures Basic Information
Technical Information Retentive systems for implant-borne hybrid dentures Basic Information 15X.252.indd 1 11/10/2018 12:18 15X.252.indd 2 11/10/2018 12:18 Contents 1. Planning 2 1.1 Planning principles 2 1.2 Recall appointments 2 2. Bar-borne restorations 3 2.1 Introduction 3 2.2 Fabrication of an implant-borne bar in the lower jaw using the synOcta® prosthetics system 6 2.3 Initial situation edentulous: bar on synOcta® 17 2.4 Fabrication of cast and laser-welded bars 19 2.5 Fabrication of the definitive bar prosthesis with metal reinforcement 23 2.6 Modification of an existing full lower denture in an implant/bar-borne hybrid denture 25 2.7 Relining an implant-borne bar denture 27 2.8 References 28 3. Retentive Anchors 29 3.1 Introduction 29 3.2 Fabrication of a new full lower denture with a metal reinforcement and two Elliptical Matrices 30 3.3 Fabrication of a new full lower denture with metal reinforcement and two titanium matrices 35 3.4 Modification of an existing full lower denture in an implant-borne Retentive Anchor denture 41 3.5 Relining of an implant-borne Retentive Anchor denture 43 3.6 Edentulous: Retentive Anchor 44 3.7 Retentive Anchors 45 3.8 References 46 4. LOCATOR® 47 4.1 Introduction 47 4.2 Using Plan LOCATOR® Abutments 48 4.3 Fabrication of a new full denture 49 4.4 Modification of an existing lower full denture into a denture fixed on LOCATOR® Abutments with simultaneous relining 51 4.5 Modification of an existing lower full denture into a denture fixed on LOCATOR® Abutments in the patient's mouth 53 4.6 Product overview 58 1 15X.252.indd 1 11/10/2018 12:18 1. -
If You Really Need to Get Oxford Ivy 5Mm Mens Plain
Oxford Ivy 5mm Mens Plain Comfort Fit Titanium Wedding Band ( Available Ring Sizes 7-12 1/2) If you really need to Get Oxford Ivy 5mm Mens Plain Comfort Fit Titanium Wedding Band ( Available Ring Sizes 7-12 1/2) great quality Men's Accessory at good offer available on the market nowadays. We ensure that you'll get it at a reasonable price. See Product Image | Check Price Now | Customer Reviews Lots of the customer feedbacks tell that Oxford Ivy 5mm Mens Plain Comfort Fit Titanium Wedding Band ( Available Ring Sizes 7-12 1/2) is actually excellent Apparel & Accessory for Men. This is a cheap product for the monetary value. Complete a few minute for review articles, which cover item quality, functions, negative and positive for this item. This important information may help you purchasing wisely, get product specifics that matches your wants and at a price you are usually happy. So if any one searching for top-quality Men's Apparel at a less expensive, Oxford Ivy 5mm Mens Plain Comfort Fit Titanium Wedding Band ( Available Ring Sizes 7-12 1/2) is the just one. Where to Buy Oxford Ivy 5mm Mens Plain Comfort Fit Titanium Wedding Band ( Available Ring Sizes 7-12 1/2) Suitably? So now reasonably-priced Apparel & Accessory for Men offered for sale, view a product functions that satisfies your needs and at a price that you're completely satisfied. Best to buy Oxford Ivy 5mm Mens Plain Comfort Fit Titanium Wedding Band ( Available Ring Sizes 7-12 1/2) just one of the favorite item currently with cheap, free shipping on purchase over and secure payment system on Amazon.com the perfect webstore. -
Titanium Tube Sheet
CTSTUBES Professional Pipeline Supplier Titanium Forgings, Titanium Forged Discs GR1, GR2, GR3, GR12 Titanium Forgings, Titanium Forged Discs Gr.1, Gr.2 Titanium Forgings, Titanium Forged Discs Gr.1, Gr.2 Titanium Disc, Titanium tube sheet Standard: ASTM B381; ASTM F 136; AMS 4928; AMS4928 Material: GR1, GR2, GR3, GR4, GR5, GR7, GR9, GR11, GR12 etc. Description Name: Titanium disco, Titanium tube sheet, Gr.2 titanium tube sheet, Gr.1 titanium sheet, Titanium Gr.2 disco, Titanium Gr.1 tube sheet Diameter range: Titanium Disc OD. (30-1000) mm x thickness (10-300) mm Titanium Ring OD. (50-1500) mm x ID. (30-1450) mm x thickness (10-700) mm Titanium Machined Parts As per customers drawing https://www.ctstubes.com/ E-mail: [email protected] Page 1 of Titanium Forgings, Titanium Forged Discs.docx CTSTUBES Professional Pipeline Supplier Titanium forgings chemical composition: Element N C H Fe O Al V Mo Ni Pd Ti Type GR.1 ≤0.03 ≤0.08 ≤0.015 ≤0.2 ≤0.18 Residual GR.2 ≤0.03 ≤0.08 ≤0.015 ≤0.3 ≤0.25 Residual GR.3 ≤0.05 ≤0.08 ≤0.015 ≤0.3 ≤0.35 Residual GR.7 ≤0.03 ≤0.08 ≤0.015 ≤0.3 ≤0.25 0.12-0.25 Residual GR.9 ≤0.02 ≤0.08 ≤0.015 ≤0.25 ≤0.15 2.5-3.3 2.0-3.0 Residual GR.12 ≤0.03 ≤0.08 ≤0.015 ≤0.3 ≤0.25 0.2-0.4 0.6-0.9 Residual GR.16 ≤0.03 ≤0.08 ≤0.015 ≤0.3 ≤0.25 0.04-0.08 Application: Industry, Aerospace, Medical, Military, Petrochemical, Marine Engineering, etc. -
Cutting Procedure for Ultra Hard Metal Rings
GEM II Battery Powered Ring Cutter Cutting Procedure For Ultra Hard Metal Rings Ver. 1.3 GEM II - Hard Metal Cutting Procedure 09/09/14 Cutting tests carried out using the GEM II battery powered ring cutter on jewellery rings made from Tungsten, Titanium and Stainless Steel. Source of test rings made from Tungsten, Titanium and Stainless Steel: ARGOS Non-jewellery ring: Brass – Toolstation Ring Material Tests RING MATERIAL WIDTH (mm) THICKNESS (mm) WEIGHT (gms) Tungsten 7 2.30 12 Argos Ref: 240/8057 Titanium 9.5 2.6 4.4 Argos Ref: 240/8909 Stainless Steel 8.0 2.5 7 Argos Ref: 240/7663 Brass (Plumbers Olive) 6.4 1.0 N/A Ring Material Features RING MATERIAL DESCRIPTION HARDNESS (MOHS Scale) Highly polished, mirror like finish. Colour similar to cobalt steel ballrace. Densest and 7.5 to 8 Tungsten heaviest of the metals tested as well as being extremely hard. Predominantly supplied in a matt grey finish, very light weight and could be Titanium mistaken for aluminium but unlike 6 to 6.5 aluminium it is very hard. Highly polished and silver in colour. Quite Stainless Steel hard. 5.5 to 6.3 Brass (Plumbers Olive) Gold/Copper like in colour. Relatively soft. 3 to 4 1 MOHS Scale Soapstone 1 Gold, Silver & Aluminium 2.5 - 3 Copper 3 Brass 3 - 4 Mild steel & Platinum 4 – 4.5 Stainless steel 5.5 – 6.3 Titanium & Jade 6 – 6.5 Tungsten 7.5 – 8 Diamond 10 2 Power Source Deployed: 4 x AA Size 2500 Mah fully charged NiMh rechargeable batteries. -
Removing the Ring Stuck on Finger with a High Speed Motor: a Case Report
The Annals of Clinical and Analytical Medicine Case Report Removing the ring stuck on finger with a high speed motor: a case report Removing the ring with motor M. Fethi Ceylan1, Haldun Topgül2 1Department of Orthopedics and Traumatology, Inönü University Turgut Özal Medical Center, Malatya, 2Department of Orthopedics and Traumatology, Elazığ State Hospital, Elazığ, Turkey Abstract A considerable number of patients apply to the emergency departments with rings, made of different alloys and in different shapes, stuck on their fingers. Sticking is a condition that must be removed as soon as possible because it may cause a serious problem that can lead up to the necrosis in the finger. Many methods have been de- scribed in the literature for removing the stuck rings. In this report, we presented a case where a ring made of a thick and hard metal alloy that causes sticking and infec- tion in the finger, was removed with a diamond tip high-speed motor used in spinal surgery unlike conventional methods, and the patient was treated without any sequel. Keywords Stuck Ring; Metal Alloy; High-Speed Motor DOI: 10.4328/ACAM.5994 Received: 10.09.2018 Accepted: 30.10.2018 Publihed Online: 04.11.2018 Printed: 01.09.2019 Ann Clin Anal Med 2019;10(5): 625-7 Corresponding Author: Haldun Topgül, Department of Orthopedics and Traumatology, Elazığ State Hospital, Elazığ, Turkey. GSM: +905356697080 E-Mail: [email protected] ORCID ID: https://orcid.org/0000-0001-9371-4827 625 | The Annals of Clinical and Analytical Medicine Removing the ring with motor Introduction this ring, which could not be removed by conventional methods.