Production and Characterization of Copper Nanoparticles by Exploding
Total Page:16
File Type:pdf, Size:1020Kb
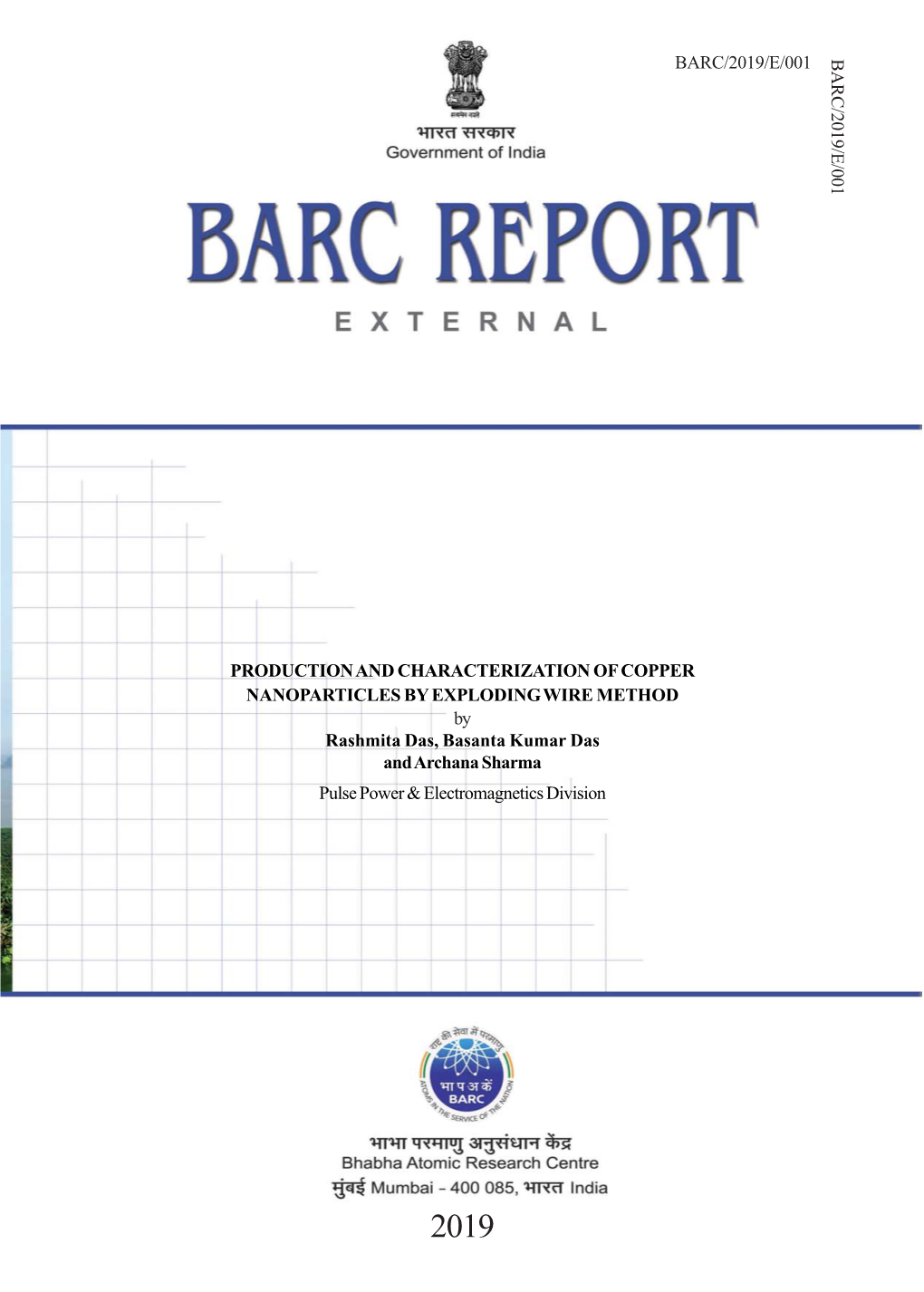
Load more
Recommended publications
-
A Spectroscopic and Structural Study of Fecosb Alloy دراﺳﺔ طﯾﻔﯾﺔ وﺗرﮐﯾﺑﯾﺔ
Iraqi Journal of Physics, 2019 Vol.17, No.41, PP. 67-74 DOI: 10.20723/ijp.17.41.67-74 A Spectroscopic and structural study of FeCoSb alloy Saba J. Kadhem Department of Physics, College of Science, University of Baghdad, Iraq E-mail: [email protected] Abstract Key words Fe, Co and Sb nanopowders were fruitfully prepared by Fe alloy , FeCoSb electrical wire explosion method in Double distilled and de-ionized alloy, exploding wire, water (DDDW) media. The formation of iron, cobalt and antimony nanoparticles, optical (FeCoSb) alloy nanopowder was monitored by X-ray diffraction. properties The x-ray diffraction pattern indicates that there are iron, cobalt and antimony peaks. Optical properties of this alloy nanoparticles were characterized by UV-Visible absorption spectra. The absorption peak position is shifted to the lower wavelengths when the current increases. That means the mean size of the nanoparticles controlled Article info. by changing the magnitude of the current. The surface morphological Received: Nov. 2018 analysis is carried out by employing Scanning Electron Microscope Accepted: Mar. 2019 (SEM). Particles with varies size were observed also from the images Published: Jun. 2019 the some particles have uneven shapes with agglomerate and the other have spherical shape. The exploding FeCoSb alloy wire plasma parameters is study by optical emission spectroscopy. The emission spectra of the plasma have been recorded and analyzed. The plasma electron temperature (Te), was determined by Boltzmann plot, and the electron density (ne), by Stark broadening for wire with diameter 0.3 mm and current of 75A in distilled water. دراسة طيفية وتركيبية لسبيكة FeCoSb صبا جواد كاظم لسى انفيسياء, كهيت انؼهىو , جايؼت بغذاد, انؼراق الخﻻصة حى حذضير جسيًاث ال Fe و Co و Sb انُاَىيت بُجاح بطريمت اﻷسﻻن انًخفجر كهربائيا داخم انًاء يمطر يرحيٍ ويُسوع اﻻيىَاث )DDDW(. -
(12) United States Patent (10) Patent No.: US 6,972,115 B1 Ballard (45) Date of Patent: Dec
USOO6972115B1 (12) United States Patent (10) Patent No.: US 6,972,115 B1 Ballard (45) Date of Patent: Dec. 6, 2005 (54) APPARATUS AND METHODS FOR THE 5,062.936 A 11/1991 Beaty et al. ................ 204/164 PRODUCTION OF POWDERS 5,091,253 A 2/1992 Smith et al. ...... ... 428/363 5,194,128 A 3/1993 Beaty et al. ...... ... 204/164 (75) Inventor: Stephen Gwyn Ballard, Hamden, CT 5,252,144 A 10/1993 Martis - - - - - - - - - - - - - - ... 148/121 (US) 5,294.242 A 3/1994 Zurecki et al. ............... 75/345 5,340,377 A 8/1994 Accary et al. ................ 75/334 (73) Assignee: American Inter-Metallics, Inc., West RE35,042 E 9/1995 Anderson, III et al. ..... 340/572 Warwick, RI (US) (Continued) (*) Notice: Subject to any disclaimer, the term of this FOREIGN PATENT DOCUMENTS patent is extended or adjusted under 35 EP O347386 12/1989 U.S.C. 154(b) by 405 days. (Continued) (21)21) Appl. NoNo.: 10/070,078/070, OTHER PUBLICATIONS (22) PCT Filed: Sep. 1, 2000 Kotov, Y.A. and Samatov, O.M., Production of Nanometer Sized AlN Powders by the Exploding Wire Method. 4 (86) PCT No.: PCT/US00/24143 Intern. Confer. On NanoStructured Materials. Jun. 14-19, S371 (c)(1) Stockholm, Sweden, no year available. (2), (4) Date: Mar. 1, 2002 (Continued) (87) PCT Pub. No.: WO01/17671 Primary Examiner-Kishor Mayekar (74) A ttorney, AAgent, Or Firm-WigginFi W andd DDana LLP PCT Pub. Date: Mar. 15, 2001 Gregory S. Rosenblatt; Anthony P. Gangemi Related U.S. Application Data (57) ABSTRACT (60) flignal application No. -
United States Patent (10) Patent No.: US 7,306,823 B2 Sager Et Al
USOO7306823B2 (12) United States Patent (10) Patent No.: US 7,306,823 B2 Sager et al. (45) Date of Patent: Dec. 11, 2007 (54) COATED NANOPARTICLES AND QUANTUM 4,104,134 A 8, 1978 Roberts et al. ............... 204,37 DOTS FOR SOLUTION-BASED FABRICATION OF PHOTOVOLTAC CELLS (75) Inventors: Brian M. Sager, Menlo Park, CA (US); (Continued) Dong Yu, Menlo Park, CA (US); FOREIGN PATENT DOCUMENTS Matthew R. Robinson, East Palo Alto, CA (US) DE 2741954 3, 1979 (73) Assignee: Nanosolar, Inc., Palo Alto, CA (US) (*) Notice: Subject to any disclaimer,- 0 the term of this (Continued) patent is extended or adjusted under 35 OTHER PUBLICATIONS U.S.C. 154(b) by 305 days. Freeman et al., Ag-Clad Au Nanoparticles: Novel Aggregation, Optical, and Surface-Enhanced Raman Scattering Properties, J. (21) Appl. No.: 10/943,657 Phys. Chem., vol. 100, 1996, pp. 718-724.* (22) Filed: Sep. 18, 2004 (Continued) (65) Prior Publication Data Primary Examiner M. Wilczewski (74) Attorney, Agent, or Firm—Joshua D. Isenberg; JDI US 2006/OO629O2 A1 Mar. 23, 2006 Patent (51) Int. Cl. (57) ABSTRACT B05D 5/2 (2006.01) B05D 700 (2006.01) B05D L/36 (2006.01) CIGS absorber layers fabricated using coated semiconduct (52) U.S. Cl. ........................ 427/217; 427/76, 977/773; ing nanoparticles and/or quantum dots are disclosed. Core 977/857 nanoparticles and/or quantum dots containing one or more (58) Field of Classification Search ................ 427/123, elements from group IB and/or IIIA and/or VIA may be 427/124, 125, 126.1, 126.4, 126.5, 215, 216, coated with one or more layers containing elements group 427/217, 250, 74,76; 977/773,857, 890, IB, IIIA or VIA. -
Shock Vaporization of Silica and the Thermodynamics of Planetary Impact Events R
JOURNAL OF GEOPHYSICAL RESEARCH, VOL. 117, E09009, doi:10.1029/2012JE004082, 2012 Shock vaporization of silica and the thermodynamics of planetary impact events R. G. Kraus,1 S. T. Stewart,1 D. C. Swift,2 C. A. Bolme,3 R. F. Smith,2 S. Hamel,2 B. D. Hammel,2 D. K. Spaulding,4 D. G. Hicks,2 J. H. Eggert,2 and G. W. Collins2 Received 15 March 2012; revised 17 August 2012; accepted 18 August 2012; published 28 September 2012. [1] The most energetic planetary collisions attain shock pressures that result in abundant melting and vaporization. Accurate predictions of the extent of melting and vaporization require knowledge of vast regions of the phase diagrams of the constituent materials. To reach the liquid-vapor phase boundary of silica, we conducted uniaxial shock-and-release experiments, where quartz was shocked to a state sufficient to initiate vaporization upon isentropic decompression (hundreds of GPa). The apparent temperature of the decompressing fluid was measured with a streaked optical pyrometer, and the bulk density was inferred by stagnation onto a standard window. To interpret the observed post-shock temperatures, we developed a model for the apparent temperature of a material isentropically decompressing through the liquid-vapor coexistence region. Using published thermodynamic data, we revised the liquid-vapor boundary for silica and calculated the entropy on the quartz Hugoniot. The silica post-shock temperature measurements, up to entropies beyond the critical point, are in excellent qualitative agreement with the predictions from the decompressing two-phase mixture model. Shock-and-release experiments provide an accurate measurement of the temperature on the phase boundary for entropies below the critical point, with increasing uncertainties near and above the critical point entropy. -
Instant, Non-Transverse Actions: Ampèrian Forces in an Electric Universe
Instant, Non-Transverse Actions: Ampèrian Forces in an Electric Universe Sébastien Renault* Abstract. We lay out the basics of an integration-based model assuming the multiscale nature of non-Lorentzian angular-dependent forces and longitudinal effects in an Electric Universe; and offer some overview of our research pertaining to the history, physics, and epistemology of E&M. Introduction How did electrodynamics turn into the synthesized electromagnetic theory we have today? The answer essentially lies in the relativity basis of the Lorentz force (starting with the introduction of the modifying concepts of Lorentz’s microscopic electrodynamics). The key ingredient to that synthesis is the decreed speed limit of information travel (the postulate that nothing travels faster than light, per Special Relativity’s requirement that light travels at the same speed c in any inertial reference frame). Key likewise to that synthesis is the rise of “force fields,” introducing a specific view of Nature wherein classical electromagnetic theory (having essentially blanked out the electrodynamic formulations of Ampère, Gauss, Weber, Neumann, and Ritz) finds comprehensive explanation only in the framework of relativity theory. Indeed, the view that the theory of Special Relativity (originally named the Lorentz-Einstein theory) provides the ultimate framework for the unification of electricity and magnetism in effect forces the original field-free description of electrodynamics (as Ampère initiated it) into the field-based theory of Faraday, Maxwell, Heaviside, Lorentz, and… Einstein. Magnetism is consequently interpreted as a relativistic effect, and relativity itself is accordingly seen as deriving from magnetism. What we have in our hands then is exactly the synthesis by which the original science of electrodynamics was redefined into the study of electromagnetic waves. -
Syllabus of M.Sc. in Physics, DDE,VU
Syllabus of M.Sc. in Physics, DDE,VU Marks distribution for Theory examinations of M.Sc. Part – I in Physics, DDE, VU For 20 Marks No of questions to be Marks per answered question 02 (out of 04) 2 02 × 2 = 04 01 (out of 02) 4 04 × 1 = 04 01 (out of 02) 8 08 × 1 = 08 Internal Assessment 04 Total 20 For 30 Marks No of questions to be Marks per answered question 04 (out of 06) 2 02 × 4 = 08 02 (out of 04) 4 04 × 2 = 08 01 (out of 02) 8 08 × 1 = 08 Internal Assessment 06 Total 30 For 40 Marks No of questions to be Marks per answered question 04 (out of 06) 2 02 × 4 = 08 04 (out of 06) 4 04 × 4 = 16 01 (out of 02) 8 08 × 1 = 08 Internal Assessment 08 Total 40 For 50 Marks No of questions to be Marks per answered question 04 (out of 06) 2 02 × 4 = 08 04 (out of 06) 4 04 × 4 = 16 02 (out of 04) 8 08 × 2 = 16 Internal Assessment 10 Total 50 For 60 Marks No of questions to be Marks per answered question 04 (out of 06) 2 02 × 4 = 08 04 (out of 06) 4 04 × 4 = 16 03 (out of 05) 8 08 × 3 = 24 Internal Assessment 12 Total 60 Scheme of syllabus and number distribution: Part-I Paper *Paper name Marks Paper Duration of Group Total examination 1A Classical Mechanics 40 90 4 hours Paper-1 1B Solid State Physics-1 30 1C Semiconductor Physics 20 2A Quantum Mechanics - I 60 90 Paper- 2 4 hours 2B Molecular Spectroscopy 30 3A Electrodyanamics 40 90 3B Plasma Physics 30 Paper-3 4 hours Material Preparation and 20 3C characterization 4A Analog Electronics 50 90 Paper-4 4 hours 4B Digital Electronics 40 Numerical analysis & 40 5A Computer Programming 90 4 hours -
Double Click on the Seminar Number to Jump to Th
Papers Published in the Proceedings of the International Pyrotechnics Seminars (double click on the Seminar number to jump to that location) 1 Estes Park, Colorado, USA 1968 2 Snowmass-at-Aspen Colorado, USA 1970 3 Colorado Springs, Colorado, USA 1972 4 Steamboat Village, Colorado, USA 1974 5 Vail, Colorado, USA 1976 6 Estes Park, Colorado, USA 1978 7 Vail, Colorado, USA 1980 8 Steamboat Springs, Colorado, USA 1982 9 Colorado Springs, Colorado, USA 1984 10 Karlsruhe, Germany 1985 11 Vail, Colorado, USA 1986 12 Juan les Pins, France 1987 13 Grand Junction, Colorado, USA 1988 14 Jersey, Channel Islands, UK 1989 15 Boulder, Colorado, USA 1990 16 Jönköping, Sweden 1991 17 Beijing, China 1991 18 Breckenridge, Colorado, USA 1992 19 Christchurch, New Zealand 1994 20 Colorado Springs, Colorado, USA 1994 21 Moscow, Russia 1995 22 Fort Collins, Colorado, USA 1996 23 Tsukuba, Japan 1997 24 Monterey, California, USA 1998 25 Brest, France 1999 26 Nanjing, Jiangsu, P.R.. China 1999 27 Grand Junction, Colorado, USA 2000 28 Adelaide, Australia 2001 29 Westminster, Colorado, USA 2002 30 Saint Malo, France 2003 31 Fort Collins, Colorado, USA 2004 32 Karlsruhe, Germany 2005 33 Fort Collins, Colorado, USA 2006 34 Beaune, France 2007 35 Fort Collins, Colorado, USA 2008 36 Rotterdam, The Netherlands 2009 37 Reims, France 2011 38 Denver, Colorado, USA 2012 39 Valencia, Spain 2013 1st Seminar 1968 index Estes Park, Colorado, USA page 1 Pyro research areas for further exploratory development. Hamrick J T 1 2 Colored smoke signals: castable compositions. Lane G A and Janowiak E 25 M 3 Ignition and output characteristics of pyrotechnics for electro-explosive 39 device applications. -
141 Production of Kanthal-D Nanoparticles Using Exploding Wire Method Betül SOSLU , İbrahim Yücel ÖZBEK
Erzincan Üniversitesi Erzincan University Fen Bilimleri Enstitüsü Dergisi Journal of Science and Technology 2021, 14(1), 141-149 2021, 14(1), 141-149 ISSN: 1307-9085, e-ISSN: 2149-4584 DOI: 10.18185/erzifbed.892535 Araştırma Makalesi Research Article Production of Kanthal-D Nanoparticles Using Exploding Wire Method Betül SOSLU , İbrahim Yücel ÖZBEK* Department of Electrical and Electronic Engineering, Faculty of Engineering, Ataturk University, Erzurum, Turkey Geliş / Received: 07/03/2021, Kabul / Accepted: 23/03/2021 Abstract This work examines the production of nanoparticles using exploding wire method (EWM). It is applied by the sudden discharge of a high voltage energy, stored on a power source, through a thin wire. The required high voltage energy was obtained with the use a voltage multiplier circuit which was first designed in the simulation environment. Then the circuit realized by the circuit elements’ parameters obtained through the simulation. Kanthal-D (FeCrAl alloy) wire was chosen as the thin metal, and all wire exploding experiments were carried out in air environment. The obtained nanoparticles were examined by SEM, and point analysis was applied to a target area on the SEM image. It is observed that the dimensions of obtained Kanthal-D nanoparticles in this study vary between 0-250 nm. In addition, EDS chemical microanalysis was performed to reveal obtained nanoparticles’ composition. Fe (71-7-74-7%), Al (4.8%) and Cr (20.5-23.5%) atoms were detected in the exploded nanoparticles. With this study, it has been shown for the first time in the literature that the stored energy obtained by a voltage multiplier circuit can be used in the EWM to produce nanoparticles in appropriate sizes Keywords: exploding wire, nanoparticles, voltage multiplier, SEM Tel patlatma yöntemi ile Kanthal-D nanotanecik üretimi Öz Bu çalışmada tel patlatma yöntemi ile nanotanecik üretilmesi gerçekleştirilmiştir. -
Nanomaterials in Pyrotechnics
View metadata, citation and similar papers at core.ac.uk brought to you by CORE provided by Defence Science Journal Defence Science Journal, Vol. 58, No. 4, July 2008, pp. 486-495 Ó 2008, DESIDOC REVIEW PAPER Nanomaterials in Pyrotechnics R.G. Sarawadekar1 and J.P. Agrawal2 1High Energy Materials Research Laboratory, Pune-411 021 2Directorate of Materials, DRDO HQrs, New Delhi-110 105 ABSTRACT Pyrotechnics consist of metallic powders as fuels and different oxidisers which generally have particle size of > 5 m. The use of nano materials is expected to increase intimate contact between fuel oxidiser, and therefore, development of nano pyrotechnics based on nano fuels oxidizers along with their synthetic routes is considered of great interest. In this review, methods for the preparation of powders of nanometals: aluminium (Al), nickel (Ni), copper (Cu), titanium (Ti), iron (Fe), silver (Ag), and cobalt (Co) and; metallic oxides: molybdenum trioxide (MoO ), 3 tungsten trioxide (WO ), iron (III) oxide (Fe O ), copper (I) oxide (Cu O), antimony trioxide (Sb O ), 3 2 3 2 2 3 nickel oxide (NiO), manganese dioxide (MnO ), and zirconium dioxide (ZrO ) along with their 2 2 characterisation are discussed. Some nano oxidisers such as PbCO , Mg(OH) , NH ClO , NH NO 3 2 4 4 4 3 have also been reported. Further, some nano pyrotechnic formulations Al-MO , Al-WO , Al- 3 3 Fe O , Al-AP, Al-Bi O , Al-CaO based on nanofuels oxidisers have also been formulated. 2 3 2 3 Keywords: Nanomaterials, pyrotechnics, nanocomposites, nanometal powders, nanooxidisers 1. INTRODUCTION challenging and some of the methods generally Pyrotechnics are mixtures of metal powders and used for their preparation are described. -
Preliminary Report on the Thermodynamic Properties of Lithium
Historic, Archive Document Do not assume content reflects current scientific knowledge, policies, or practices. D_A DJIMAfiS NATIONAL BUREAU OF STANDARDS REPORT 6484 Preliminary Report on the Thermodynamic Properties of Lithium, Beryllium, Magnesium, Aluminum and Their Compounds With Hydrogen, Oxygen, Nitrogen, Fluorine, and Chlorine (Supplement to NBS Report 6297) July 1, 1959 U. S. DEPARTMENT OF COMMERCE NATIONAL BUREAU OF STANDARDS THE NATIONAL BUREAU OF STANDARDS Functions and Activities The functions of the National Bureau of Standards are set forth in the Act of Congress, March 3, 1901, as amended by Congress in Public Law 619, 1950. These include the development and maintenance of the national standards of measurement and the provision of means and methods for making measurements consistent with these standards; the determination of physical constants and properties of materials; the development of methods and instruments for testing materials, devices, and structures; advisory services to government agencies on scientific and technical problems; in- vention and development of devices to serve special needs of the Government; and the development of standard practices, codes, and specifications. The work includes basic and applied research, development, engineering, instrumentation, testing, evaluation, calibration services, and various consultation and information services. Research projects are also performed for other government agencies when the work relates to and supplements the basic program of the Bureau or when the Bureau’s unique competence is required. The scope of activities is suggested by the listing of divisions and sections on the inside of the back cover. Publications The results of the Bureau’s work take the form of either actual equipment and devices or pub- lished papers. -
Synthesis and Characterization of Nano Copper Particles
5 IV April 2017 http://doi.org/10.22214/ijraset.2017.4258 www.ijraset.com Volume 5 Issue IV, April 2017 IC Value: 45.98 ISSN: 2321-9653 International Journal for Research in Applied Science & Engineering Technology (IJRASET) Synthesis and Characterization of Nano Copper Particles Jerrin James1, Jivimon K Shaji2, Kohil S Kottarathil3 Electrical and Electronics Department, Mar Athanasius College of Engineering Kothamangalam Abstract: Nanoscience and Nanotechnology are the growing fields of scientific research and commercial development. Nanosize powders are solid particles with typical size in the range of 1 to 100 nm. Nanosize powders have very large specific surface area giving rise to many special physical and chemical properties. Exploding Wire Method (also known as EWM) is a high energy density process by which a rising current is applied to a thin electrically conductive wire. A fine wire of metal is exploded by applying by a high voltage. The high voltage is usually Impulse voltage. The heat vaporizes the wire, and an electric arc over that vapour creates a shock wave and explosion. Exploding Wire Method is the best method for production of metal nanoparticles. When Exploding Wire Method is performed in a standard atmosphere containing oxygen, metal oxides are formed. Pure metal nanoparticles can also be produced with EWM in an inert environment, usually argon gas or distilled water. Pure metal nanopowders must be kept in their inert environment because they ignite when exposed to oxygen in air. Keywords: Nano Particles, Wire Explosion Method, Trigatron Switch, XRD, SEM, TEM. I. INTRODUCTION Nanoscience and nanotechnology are the study and application of extremely small things and can be used across all the other science fields, such as chemistry, biology, physics, materials science, and engineering. -
Monday, September 9, 2013 K.Mo A1 Fusion Energy Research in Japan’S Nuclear Energy R&D Program
Monday, September 9, 2013 K.Mo_A1 Fusion Energy Research in Japan’s Nuclear Energy R&D Program Shunsuke KONDO Japan Atomic Energy Commission (JAEC) shunsuke [email protected] JAEC has been promoting nuclear energy R&D activities, recognizing that nuclear power will continue to be a stable base-load source of electricity if its sustainability is progressively improved, as it can contribute to energy security, reduce the impact of volatile fossil fuels prices and mitigate the effects of climate change in an era of increasing global energy demands. The objective of the short-term R&D activities is to utilize existing assets as effectively as possible and that of the mid-term R&D activities is to prepare technologies that should be introduced in due time for assuring the high sustainability of nuclear fission energy technology. The objective of the long-term R&D activities is, on the other hand, to explore radically new nuclear energy technologies and much of the activities in this category are devoted to nuclear fusion R&D. The objectives of the current nuclear fusion R&D activities are 1) construct ITER, 2) establish the basis for the development of tokamak demonstration power plant through advanced fusion plasma research utilizing JT-60SA and development of the neutron-resistant materials and an intense neutron source required for this activity, engaging in an engineering validation and design activity (EVEDA) for the IFMIF, 3) explore alternatives to tokamaks, such as the heliotron line and inertial fusion lines. As for inertial fusion approach, currently experimental progress has been focused on fast ignition by performing integrated experiment with the FIREX-I system and the LFEX laser system that utilizes Chirped Pulse Amplification (CPA) technique.