Performance Simulation of Two-Bed Adsorption Refrigeration Chiller
Total Page:16
File Type:pdf, Size:1020Kb
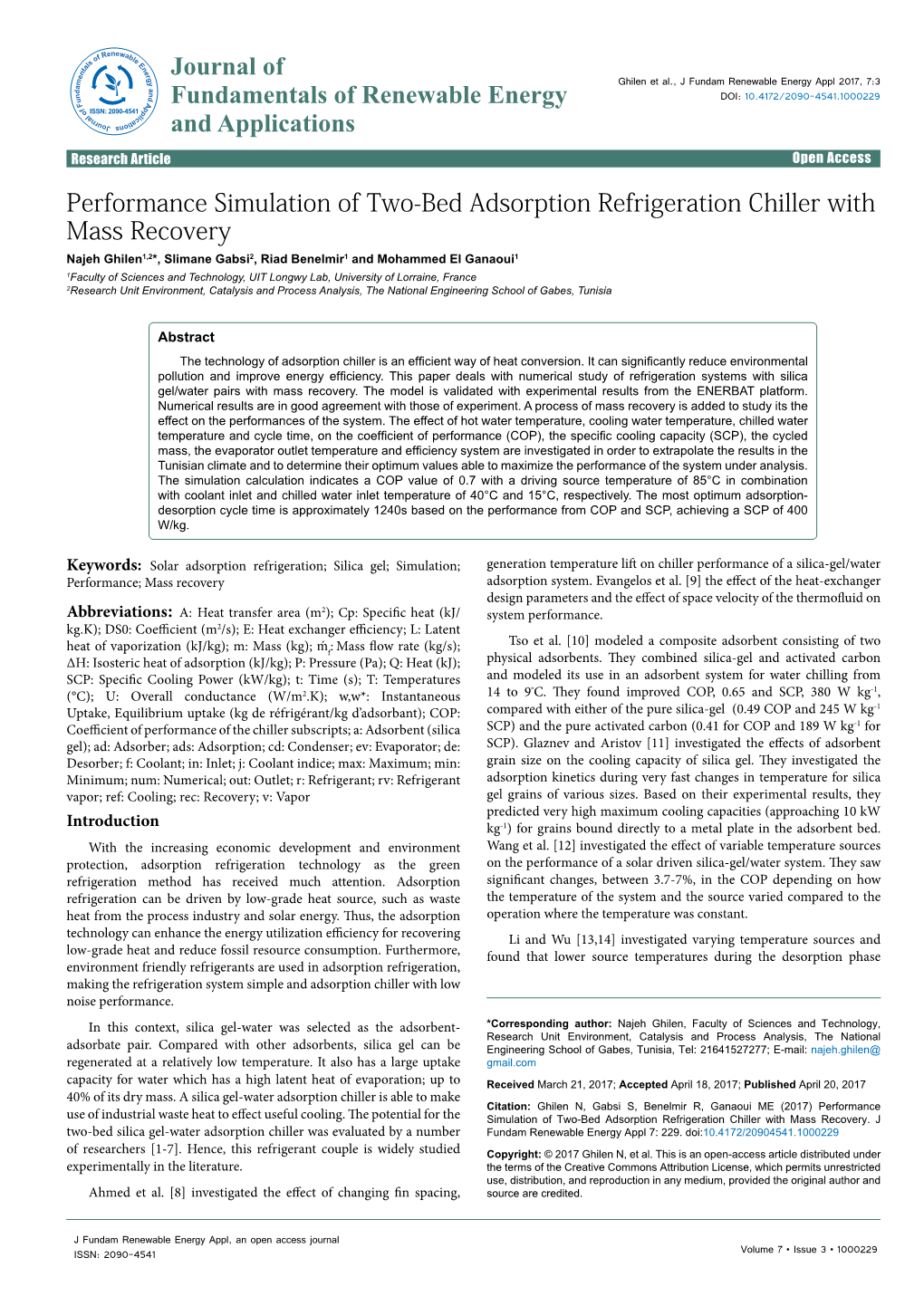
Load more
Recommended publications
-
A Statistical Approach to Optimize the Solar Adsorption Refrigeration System
ISSN 1923-8460[PRINT] Energy Science and Technology ISSN 1923-8479[ONLINE] Vol. 3, No. 2, 2012, pp. 18-28 www.cscanada.net DOI:10.3968/j.est.1923847920120302.216 www.cscanada.org A Statistical Approach to Optimize the Solar Adsorption Refrigeration System Ghassan M. Tashtoush[a],* [a]Mechanical Engineering Department, Jordan University of Science and Technology, P.O.Box 3030 Irbid 22110, JORDAN. NOMENCLATURE *Corresponding author. A: collector area (m²) . Received 2 February 2012; accepted 3 April 2012 C: specific heat (J/kg K) h: convective heat transfer coefficient (W/m².K) I: total incident solar radiation on south facing inclined Abstract surface (W/m²) Solar-powered refrigeration based on adsorption cycles k: thermal conductivity (W/m.K) is simple, quiet in operation and adaptable to small L: Insulation thickness (m) medium or large systems. Application potentials include m: adsorbent mass (kg) storage of vaccines for immunization against killer P: pressure (Pa) diseases in remote areas, preservation of foodstuff Q: heat transfer rate (W) for future use and manufacture of ice. Already Solar U: thermal resistance (m².K/W) Adsorption Refrigeration (SAR) is a technical success, T: temperature (C) but it is not commercially competitive with either the U: overall heat loss coefficient (W/m².K) conventional vapor compression or PV refrigerators. 3 Further developmental research is, therefore, required ∆x: Adsorbent concentration (kg/m ) for improvements in existing designs either to increase Greek symbols system overall performances significantly or to reduce ε: emissivity system unit cost or both. In this study a statistical η: efficiency approach was used to optimize of solar adsorption air θ: angle of inclination conditioning or refrigeration unit using ANOVA analysis. -
Modelling of Adsorption‑Based Refrigeration System
This document is downloaded from DR‑NTU (https://dr.ntu.edu.sg) Nanyang Technological University, Singapore. Modelling of adsorption‑based refrigeration system Liu, Yue 2005 Liu, Y. (2005). Modelling of adsorption‑based refrigeration system. Doctoral thesis, Nanyang Technological University, Singapore. https://hdl.handle.net/10356/6070 https://doi.org/10.32657/10356/6070 Nanyang Technological University Downloaded on 01 Oct 2021 21:27:45 SGT ATTENTION: The Singapore Copyright Act applies to the use of this document. Nanyang Technological University Library MODELLING OF ADSORPTION-BASED REFRIGERATION SYSTEMS Liu Yue SCHOOL OF MECHANICAL AND AEROSPACE ENGINEERING NANYANG TECHNOLOGICAL UNIVERSITY 2005 ATTENTION: The Singapore Copyright Act applies to the use of this document. Nanyang Technological University Library MODELLING OF ADSORPTION-BASED REFRIGERATION SYSTEMS Submitted by Liu Yue SCHOOL OF MECHANICAL AND AEROSPACE ENGINEERING A thesis submitted to the Nanyang Technological University in fulfillment of the requirements for the degree of Doctor of Philosophy 2005 ATTENTION: The Singapore Copyright Act applies to the use of this document. Nanyang Technological University Library ABSTRACT This thesis presents several numerical models including thermodynamic model, lumped model and heat and mass transfer model for different zeolite/water adsorption refrigeration cycles to investigate the effects of parametric and operating conditions on system performance. Experiments were also carried out to validate the heat and mass transfer model. Firstly, a thermodynamic model based on the first and second laws of thermodynamics is presented. The effects of operating conditions on the coefficient of performance (COP) for different cycles were investigated using a first law approach. The results show that the COP can be greatly improved (about 44%) when compared with the intermittent cycle by using heat recovery, while the mass recovery cycle can only increase the COP by 6%. -
Design and Thermodynamic Analysis of Waste Heat-Driven Zeolite–Water Continuous-Adsorption Refrigeration and Heat Pump System for Ships
energies Article Design and Thermodynamic Analysis of Waste Heat-Driven Zeolite–Water Continuous-Adsorption Refrigeration and Heat Pump System for Ships Cüneyt Ezgi Department of Marine Engineering, Piri Reis University, 34940 Istanbul, Turkey; [email protected]; Tel.: +90-216-581-0051 Abstract: Strict International Maritime Organization (IMO) rules enable ships to maximize fuel consumption and compliance with the climate. Cooling and heat-pumping technology powered by waste heat makes a substantial contribution to lowering ship gas emissions. This study explores, technically studies, and thermodynamically analyzes the efficiency of ongoing adsorption refrig- eration and heating systems using a zeolite–water pair onboard a naval surface ship. An updated Dubin-in-Astakhov equation calculates the equilibrium adsorption potential of the operating pair used in the system. The coefficient of performance (COP) and specific cooling power (SCP)/specific heating power (SHP) values were between 0.109 and 0.384 and between 69.13 and 193.58 W kg−1 for cooling mode, and between 66.16 and 185.26 W kg−1 based on exhaust gas temperature and regeneration, respectively. Up to 27.64% and 52.91% met the cooling and heating load of the case vessel at a full load by the zeolite–water-adsorbed refrigeration/heat-pumping system. The COP of the heat pump and cooling systems was compared to that of adsorption cooling/heat pumps in Citation: Ezgi, C. Design and the literature. Thermodynamic Analysis of Waste Heat-Driven Zeolite–Water Keywords: zeolite; water; adsorption; refrigeration; heat pump; ship Continuous-Adsorption Refrigeration and Heat Pump System for Ships. Energies 2021, 14, 699. -
Refrigeration Roadmap
working with Refrigeration Road Map Contents Introduction 1 Refrigeration Road Map 2 Introduction to the Refrigeration Road Map 4 Abbreviations 5 How was the Refrigeration Road Map developed? 5 The baseline supermarket 6 Direct emissions 6 Indirect emissions 6 How should the Refrigeration Road Map be used? 7 CO2e saving options that can be retrofitted 10 CO2e saving options suitable for a store refit 25 Future technologies 48 Appendix 1. Summary of technologies 51 Introduction Reducing energy use makes perfect business sense; it saves money, enhances corporate reputation and helps everyone in the fight against climate change. The Carbon Trust provides simple, effective advice to help businesses take action to reduce carbon emissions, and the simplest way to do this is to use energy more efficiently. This Refrigeration Road Map introduces the main energy saving opportunities for refrigeration use in the retail sector and demonstrates how simple actions save energy use, cut costs and increase profit margins. 2 Carbon Trust Refrigeration Road Map The Refrigeration Road Map was developed to identify technologies that can be implemented by retailers to enable them to save energy and CO2e. Application timescale 2010 Short Med ium Technologies available now to retrofit Technologies available for store refit • Refrigerant change to R407A • Cabinet selection • Training • Secondary systems (with NCs) • Cleaning and maintenance • CO2 refrigeration technology • Re-commissioning • Borehole condensing • Floating head pressure • Dynamic demand • Store -
Ammonia/Ethanol Mixture for Adsorption Refrigeration
energies Article Ammonia/Ethanol Mixture for Adsorption Refrigeration Mauro Luberti, Chiara Di Santis and Giulio Santori * School of Engineering, Institute for Materials and Processes, the University of Edinburgh, Sanderson Building, King0s Buildings, Robert Stevenson Road, Edinburgh EH9 3FB, UK; [email protected] (M.L.); [email protected] (C.D.S.) * Correspondence: [email protected] Received: 29 January 2020; Accepted: 19 February 2020; Published: 22 February 2020 Abstract: Adsorption refrigeration has become an attractive technology due to the capability to exploit low-grade thermal energy for cooling power generation and the use of environmentally friendly refrigerants. Traditionally, these systems work with pure fluids such as water, ethanol, methanol, and ammonia. Nevertheless, the operating conditions make their commercialization still unfeasible, especially owing to safety and cost issues as a consequence of the working pressures, which are higher or lower than 1 atm. The present work represents the first thermodynamic insight in the use of mixtures for adsorption refrigeration and aims to assess the performance of a binary system of ammonia and ethanol. According to the Gibbs’ phase rule, the addition of a component introduces an additional degree of freedom, which allows to adjust the pressure of the system varying the composition of the mixture. The refrigeration process was simulated with isothermal- isochoric flash calculations to solve the phase equilibria, described by the Peng-Robinson-Stryjek-Vera (PRSV) equation of state for the vapor and liquid phases and by the ideal adsorbed solution theory (IAST) and the multicomponent potential theory of adsorption (MPTA) for the adsorbed phase. -
Modelling and Optimization of an Adsorption Cooling System for Automotive Applications (Doctoral Program of Energy Technology)
UNIVERSIDAD POLITÉCNICA DE VALENCIA DEPARTAMENTO DE TERMODINÁMICA APLICADA Modelling and optimization of an adsorption cooling system for automotive applications (Doctoral Program of Energy Technology) Author Maria Verde Trindade Supervisor Dr. Eng. José Miguel Corberán Salvador Valencia, July 2015 i ii Tesis doctoral Modelling and optimization of an adsorption cooling system for automotive applications Realizada por: Maria Verde Trindade Dirigida por: Dr. D. José Miguel Corberán Salvador Tribunal Calificador: Presidente: Dr. D. Joan Carles Bruno Argilaguet Secretario: Dr. D. José Gonzálvez Maciá Vocales: Dr. D. José Ramón Garcia Cascales Valencia, Julio 2015 iii iv “It's only those who do nothing that make no mistakes, I suppose.” Joseph Conrad, An Outcast of the Islands “I don't like work - no man does - but I like what is in the work - the chance to find yourself. Your own reality - for yourself not for others - what no other man can ever know. They can only see the mere show, and never can tell what it really means.” Joseph Conrad, Heart of Darkness v vi ACKNOWLEDGEMENTS I would like to express my deep appreciation and thanks to my thesis supervisor, Prof. José Miguel Corberán, for giving me the opportunity and motivation to undertake this work. His continuous encouragement, suggestions, advice and guidance throughout this entire course have been a beneficial contribution to this study. Sincere gratitude is also due to Robert de Boer and Simon Smeding of the Energy Research Centre of the Netherlands (ECN), and also Angelo Freni and Alessio Sapienza of the Institute for Advanced Energy Technologies "Nicola Giordano" (CNR-ITAE) for their constant helpfulness and productive collaboration throughout this study. -
Review - Design of Adsorption Refrigeration System Driven by Engine Exhaust Gas for Vehicles
Journal of Information and Computational Science ISSN: 1548-7741 REVIEW - DESIGN OF ADSORPTION REFRIGERATION SYSTEM DRIVEN BY ENGINE EXHAUST GAS FOR VEHICLES 1 2 3 VINEETH P. BABU , R. VASANTH , VARUN BABU M K 1Post Graduate in Thermal Engineering, R.V.S College of Engineering And Technology, Coimbatore, TamilNadu. 2Assistant Professor, Department of Mechanical Engineering, R.V.S College of Engineering And Technology, Coimbatore, TamilNadu. 3Post Graduate in Thermal Engineering, R.V.S College of Engineering And Technology, Coimbatore, TamilNadu. Abstract Heat generated cooling is a technique of refrigeration where the required cooling effect is obtained by using heat energy as input. At present, the conventional cooling systems used in automobiles are engine driven Vapour Compression Refrigeration (VCR) systems. Some of the alternative heat generated cooling technologies suggested by researchers in their work, which can replace engine driven systems are - solid adsorption cooling systems, absorption cooling, Sterling cycle cooling, thermo acoustic refrigeration etc. In this study, a comparison of vapour compression, vapour absorption and vapour adsorption refrigeration systems is carried out. Literature review suggests that the adsorption refrigeration can be a suitable option for mobile applications and for smaller capacities. The vapour adsorption system has a strong potential to be used as an alternative cooling system. The estimated availability of exhaust gas energy suggests the capacity of cooling which can be greatly enhanced for a dedicated system. This thesis proposes an innovative, compact, and improved adsorption refrigeration system design review, powered by engine exhaust heat. 1. Introduction In India road transportation is a major mode of transport for goods over large distances using trucks. -
A Review on Adsorption Heat Pump: Problems and Solutions
ARTICLE IN PRESS Renewable and Sustainable Energy Reviews 12 (2008) 2381–2403 www.elsevier.com/locate/rser A review on adsorption heat pump: Problems and solutions Hasan Demira, Moghtada Mobedib,Ã, Semra U¨lku¨a aDepartment of Chemical Engineering, Izmir Institute of Technology, Gulbahce Campus, 35430 Izmir, Turkey bDepartment of Mechanical Engineering, Izmir Institute of Technology, Gulbahce Campus, 35430 Izmir, Turkey Received 14 April 2007; accepted 20 June 2007 Abstract Adsorption heat pumps have considerably sparked attentions in recent years. The present paper covers the working principle of adsorption heat pumps, recent studies on advanced cycles, developments in adsorbent–adsorbate pairs and design of adsorbent beds. The adsorbent–adsorbate pair features for in order to be employed in the adsorption heat pumps are described. The adsorption heat pumps are compared with the vapor compression and absorption heat pumps. The problems and troubles of adsorption heat pumps are classified and researches to overcome the difficulties are discussed. r 2007 Elsevier Ltd. All rights reserved. Keywords: Adsorption heat pump; Renewable; Zeolite Contents 1. Introduction . 2382 2. Adsorption heat pump cycle . 2382 3. Advantage and disadvantage of adsorption heat. 2386 4. Comparison of heat pumps . 2387 5. Adsorption heat pump: problems and solutions . 2393 5.1. Advanced adsorption heat pump cycles. 2394 5.1.1. Uniform temperature adsorber process . 2394 ÃCorresponding author. Tel.: +90 232 750 78 03; fax: +90 232 750 65 05. E-mail address: [email protected] (M. Mobedi). 1364-0321/$ - see front matter r 2007 Elsevier Ltd. All rights reserved. doi:10.1016/j.rser.2007.06.005 ARTICLE IN PRESS 2382 H. -
Adsorption Refrigeration
SORPTION REFRIGERATION - ADSORPTION SYSTEMS Description of technology Sorption refrigeration technologies such as absorption and/or adsorption are thermally driven systems, in which the conventional mechanical compressor of the common vapour compression cycle is replaced by a ‘thermal compressor’ and a sorbent. The sorbent can be either solid in the case of adsorption systems or liquid for absorption systems. When the sorbent is heated, it desorbs the refrigerant vapour at the condenser pressure. The vapour is then liquefied in the condenser, flows through an expansion valve and enters the evaporator. When the sorbent is cooled, it reabsorbs vapour and thus maintains low pressure in the evaporator. The liquefied refrigerant in the evaporator absorbs heat from the refrigerated space and vaporises, producing the cooling effect. Adsorption refrigeration unlike absorption and vapour compression systems, is an inherently cyclical process and multiple adsorbent beds are necessary to provide approximately continuous capacity. Adsorption systems inherently require large heat transfer surfaces to transfer heat to and from the adsorbent materials which automatically makes cost an issue. High efficiency systems require that heat of adsorption be recovered to provide part of the heat needed to regenerate the adsorbent. These regenerative cycles consequently need multiples of two-bed heat exchangers and complex heat transfer loops and controls to recover and use waste heat as the heat exchangers cycle between adsorbing and desorbing refrigerant. State of Development Adsoprtion systems for air conditioning applications are already commercially available from a small number of manufacturers . "MYCOM", Mayekawa Mfg. Co., Ltd. are producing Silica- gel/water adsorption chiller (ADREF- models) with ranges between 35 and 350 kW for use in the air-conditioning industry. -
Optimisation of Operation of Adsorption Chiller with Desalination Function
energies Article Optimisation of Operation of Adsorption Chiller with Desalination Function Karol Sztekler Faculty of Energy and Fuels, AGH University of Science and Technology, Mickiewicza 30, 30-059 Krakow, Poland; [email protected] Abstract: The demand for electricity is growing rapidly along with economic development and increasing population. At present, its production is mainly based on non-renewable sources, which has negative impacts on the environment and contributes to global warming. A large proportion of the produced electricity is consumed by refrigeration equipment. Climate change and the progress of civilisation are additionally increasing the demand for cooling, with increasing electricity consump- tion as a consequence. One of the options for obtaining eco-friendly cooling is the use of adsorption chillers. These devices are powered by low-temperature heat and their operation only requires a small amount of electrical energy. The source of low-temperature heat can be, e.g., waste heat generated in many industrial processes. Its use allows one to increase energy efficiency and achieve additional financial benefits. However, adsorption chillers are characterised by low coefficients of performance. This paper presents possibilities to improve their performance. It also presents the results of tests carried out on a three-bed adsorption chiller with desalination function. The aim of the investigation was to determine the effect of the cycle time on the coefficient of performance (COP) and specific cooling power (SCP). The working pair was silica gel and water. The results confirmed the effect of the duration of adsorption and desorption on the COP and SCP of the adsorption chiller. -
The Cooling Effect by Adsorption-Desorption Cycles
E3S Web of Conferences 14 , 01052 (2017) DOI: 10.1051/ e3sconf/20171401052 Energy and Fuels 2016 The cooling effect by adsorption-desorption cycles Eliza Wolak1,* 1AGH University of Science and Technology, Faculty of Energy and Fuels, Cracow, Poland Abstract. Adsorption appliances may turn out to be an alternative to compression-type refrigerators. The adsorption refrigeration machine may be driven by a low-grade heat source, especially solar energy. Solar adsorption cooling systems are environment-friendly and have zero ozone depletion potential. Therefore, the adsorption refrigeration is one kind of energy saving refrigeration methods. The merits of the adsorption refrigeration systems will be more significant especially when it is used in vehicles (automobiles, ships and locomotives), to preserve food and medicines and in air-conditioning. The paper presents the advantages and disadvantages as well as the evolution of the technology of adsorptive refrigeration systems. The methods of improving of adsorption refrigeration systems through improvements in adsorbents properties, use of advanced cycles and hybrid systems is also presented. Possible applications and perspectives for development of adsorption cooling systems are also analyzed. The paper describes a test stand of the adsorption-desorption refrigeration. The present investigations have been carried out utilizing the activated carbon granules as an adsorbent and methanol as an adsorbate. The paper demonstrates the measurement of temperature changes in the adsorbent bed and condenser during adsorption-desorption cycles. 1 Introduction The energy problem has already been known since the global energy crisis broke out in the 1970s. In the process of the primary energy utilization a great amount of waste heat is discharged into the environment. -
Review on Adsorption Refrigeration System
IOSR Journal of Mechanical and Civil Engineering (IOSR-JMCE) e- ISSN: 2278-1684,p-ISSN: 2320-334X PP. 01-04 www.iosrjournals.org Review On Adsorption Refrigeration System B. K. Manmode1, B.B. Aher2 1(Department of Mechanical Engineering, JSPM NTC, Pune India) 2((Department of Mechanical Engineering, JSPM NTC, Pune India) Corresponding Author: B. K. Manmode Abstract : “Energy can neither be created nor be destroyed”- first law of thermodynamics. the energy potential of the world is constant , so we have to save the energy as much as possible .as the refrigeration is needed everywhere in the world and it is the major user of energy. The energy that could be used for the adsorption refrigeration is powered by low grade heat. the low grade heat can be obtain from industrial waste heat, exhaust gases from the engines or heat from solar thermal collector. Moreover it uses environment kindly refrigerants and avoids the global warming and ozone depletion.. Keywords: Adsorption, adsorption system working pairs, waste heat. I. Introduction Everywhere in our world, refrigeration is a major energy user. In poor areas off grid refrigeration is a critically important need. Refrigeration is an interesting application of solar energy because the incident radiation and the need for cold production both reach maximum levels in the same period. all of these considerations point the way toward refrigeration using renewable energy, as part of a sustainable way of life. Solar-powered refrigeration is a real and exciting possibility. Due to the increasing concentration of green house gases and climate changes, the need for renewable energy sources is greater than ever.