Iapd Thermoplastics Rectangle Imidized
Total Page:16
File Type:pdf, Size:1020Kb
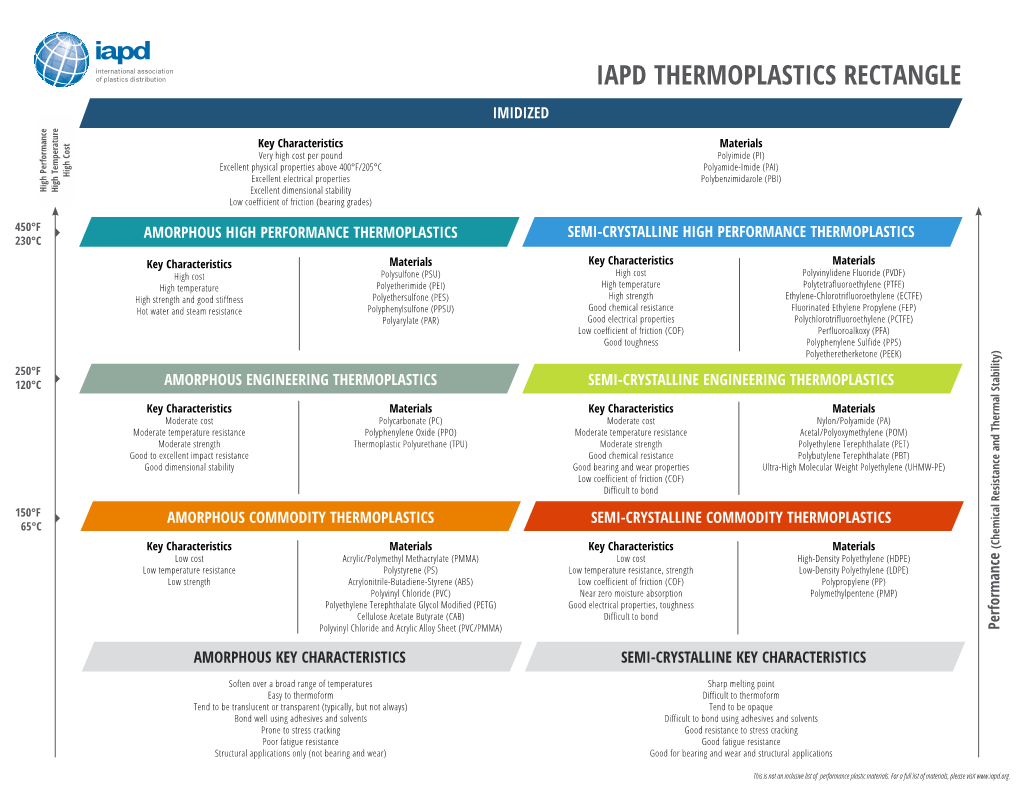
Load more
Recommended publications
-
Chlorine Dioxide Compatibility Assessment
Chlorine Dioxide Compatibility Assessment DRF3366 - TECH-COMM-001 Created by: Tristel Solutions Limited, Lynx Business Park, Cambs, UK, CB8 7NY Copyright © Tristel Solutions T +44 (0) 1638 721500 – E [email protected] – W www.tristel.com January 2018 Key - Excellent - no change at all in the device - Good - slight cosmetic change/ decolourisation – material/device still fully functional - Fair – slight damage is observed– material/device still fully functional - Poor – visible pitting, breaking, brittle METALS Materials of construction 1 2 3 4 (Excellent) (Good) (Fair) (Poor) Stainless Steel 317 (Pure) X Stainless Steel 316 (pure, fully X austenitic with no ferric content) Stainless Steel 304 X (High grade, low ferric content) Hastelloy X Titanium X Aluminium X Aluminium (Anodised) X Brass X Copper X Chrome X Mild Steel X DRF3366 - TECH-COMM-001 Created by: Tristel Solutions Limited, Lynx Business Park, Cambs, UK, CB8 7NY Copyright © Tristel Solutions T +44 (0) 1638 721500 – E [email protected] – W www.tristel.com January 2018 PLASTICS Materials of construction 1 2 3 4 (Excellent) (Good) (Fair) (Poor) Perfluoroelastomer X PEEK X X Polypropylene X PVDF X X Polycarbonate X Polysulphone (natural) X Polysulphone (white) X PET-P X PMMA X Polyamide X Polyethylene X Polyoxymethylene X Acetal X ABS X Polymethylpentene (TPX) (PMP) X DRF3366 - TECH-COMM-001 Created by: Tristel Solutions Limited, Lynx Business Park, Cambs, UK, CB8 7NY Copyright © Tristel Solutions T +44 (0) 1638 721500 – E [email protected] – W www.tristel.com January 2018 PLASTICS -
Kocetal Polyoxymethylene 1 1 Business Area
® Engineering Plastic KOCETAL POLYOXYMETHYLENE 1 1 BUSINESS AREA Seoul Ofce (Sales Division) Seoul Office (Sales Division) 1Seoul0th floor Ofce, Kolon (Sales Tow Division)er annex 1-22, Seoul Ofce (Sales Division) Byulyang-Dong, Gwacheon City, 10F, an annex to Kolon Tower 1-22, 10th floor, Kolon Tower annex 1-22, Seoul Ofce (Sales Division) ByulyGyunggi-Do,ang-Dong Korea, Gwacheon City, Byeolyang-dong, Gwacheon City, Gyunggi-Do, Korea Gyunggi-Do, Korea www.kolonplastics.com Headquarters and Plant www.kolonplastics.com Headquarters and Plant Headquarters, Factory and R&D Division Headquarters, Factory and R&D Division 1018, Eungmyeong-dong, Gimcheon-si, 101Headquarters,8, Eungmyung-dong Factory, Gimcand heon-CitR&D Divisiony, Gyeongsangbuk-do, Korea 101GyeongSangBukDo,8, Eungmyung-dong Korea, Gimcheon-City, GyTel:eongSangBukDo, +82-54-420-8491, K 8477orea TFel:ax: +82-54-420-8491, +82-54-420-8369 8477 Fax: +82-54-420-8369 Contact for further information If you want to inquire more detail information on product of KOLONPLASTIC,INC. follow the process written below. 1. Access the Internet hompage of KOLONPLASTIC, INC. www.kolonplastics.com/enghome 2. ‘SALES CONTACT’ category. 3. Then you can see contact number on E-mail, Tel or Fax according to regional groups. About Kolon Plastics Kolon Plastics-Growing with our customers as a POM Global Leader Kolon Plastics was established in March 1996 as a joint venture between Kolon Industries Inc. in Korea and Toray Industries Inc. in Japan. Production began in 1998 with capacity and sales of 25,000MT/year. After the 2nd factory line was completed, we produce 57,000MT of POM and 50,000MT of the other compouding materials a year. -
Type Material Name Abbreviation Plastic Acrylonitrile Butadiene
Type Material Name Abbreviation Plastic Acrylonitrile butadiene styrene ABS Plastic Acrylonitrile butadiene styrene - High-Temp ABS - high temp Plastic Acrylonitrile butadiene styrene + Polycarbonate ABS + PC Plastic Acrylonitrile butadiene styrene + Polycarbonate + Glass Fill ABS + PC + GF Plastic Acrylonitrile styrene acrylate ASA Plastic Nylon 6-6 + 10% Glass Fill PA66 + 10% GF Plastic Nylon 6-6 + 20% Glass Fill PA66 + 20% GF Plastic Nylon 6-6 + 30% Glass Fill PA66 + 30% GF Plastic Nylon 6-6 + 50% Glass Fill PA66 + 50% GF Plastic Nylon 6-6 Polyamide PA66 Plastic Polyamide 12 PA12 Plastic Polybutylene terephthalate PBT Plastic Polybutylene terephthalate + 30% Glass Fill PBT+ 30% GF Plastic Polycaprolactam PA6 Plastic Polycaprolactam + 20% Glass Fill PA6 + 20% GF Plastic Polycaprolactam + 30% Glass Fill PA6 + 30% GF Plastic Polycaprolactam + 50% Glass Fill PA6 + 50% GF Plastic Polycarbonate PC Plastic Polycarbonate + Glass Fill PC + GF Plastic Polycarbonate + 10% Glass Fill PC + 10% GF Plastic Polycarbonate + Acrylonitrile butadiene styrene + 20% Glass Fill + 10% Stainless Steel fiber PC + ABS + 20% GF + 10% SS Fiber Plastic Polyether ether ketone PEEK Plastic Polyetherimide + 30% Glass Fill Ultem 1000 + 30% GF Plastic Polyetherimide + 40% Glass Fill (Ultem 2410) PEI + 40% GF (Ultem 2410) Plastic Polyetherimide + Ultem 1000 PEI + Ultem 1000 Plastic Polyethylene PE Plastic Polyethylene - High-Density HDPE, PEHD Plastic Polyethylene - Low-Density LDPE Plastic Polyethylene terephthalate PET Plastic Polymethyl methacrylate PMMA Plastic Polyoxymethylene -
TPX® Datasheet
Metals & Materials for Research and Industry TPX® Datasheet GOODFELLOW & MITSUI & CO. EUROPE PLC TPX® Polymethylpentene (PMP) TPX®, a 4-methylpentene-1 based polyolefin manufactured solely by Mitsui Chemicals, Inc. is now available in small order lots from Goodfellow. This lightweight, functional polymer displays a unique combination of physical properties and characteristics due to its distinctive molecular structure. Because of its superb chemical resistance and optical clarity TPX® is an ideal choice when replacing polycarbonate or acrylic in some chemically demanding environments. • High heat resistance (melt temperature 236°C) • Lowest specific gravity of any known polymer (0.833 g/cc) CH CH2 CH CH2 • Superior steam sterilisation capabilities • Superior transparency to visible light CH CH • Excellent UV transmission characteristics 2 2 • Lower refractive index than other transparent resins CH CH • Excellent acoustic properties • Excellent chemical resistance H C CH H C CH • High gas and moisture permeability 3 3 3 3 • Outstanding dielectric properties The properties of TPX® make it ideal for extruding items such as film and paper coating, injection moulded items and blow moulded components, and we list some of the possible applications below: • Release film • Release paper for synthetic leather • LED moulds • Mandrels and sheaths for hose and cable use • Cosmetic caps and tubes • Heat resistant non-woven fabric and fibres • Chemical tubes • Animal cages • Sterilisation containers Goodfellow Cambridge Ltd [email protected] Ermine -
Process for Producing Polyoxymethylene-Polyurethane Type Alloy
~" ' MM II II II II II INI Ml I Ml II I II J European Patent Office _ _ _ _ © Publication number: 0 276 080 B1 Office_„. europeen des brevets © EUROPEAN PATENT SPECIFICATION © Date of publication of patent specification: 10.06.92 © Int. CI.5: C08G 18/66, C08L 59/00 © Application number: 88300257.8 @ Date of filing: 13.01.88 © Process for producing polyoxymethylene-polyurethane type alloy. © Priority: 23.01.87 JP 12294/87 © Proprietor: NIPPON POLYURETHANE INDUS- TRY CO. LTD. @ Date of publication of application: 2-8, Toranomon 1-chome 27.07.88 Bulletin 88/30 Mlnato-ku Tokyo(JP) © Publication of the grant of the patent: @ Inventor: Yano, Norlyoshl 10.06.92 Bulletin 92/24 1-13, Zushl 7-chome Zushl-shl Kanagawa-ken(JP) © Designated Contracting States: Inventor: Fujlta, Toshlhlko DE FR GB 422-14, Karlba-cho Hodogaya-ku Yokohama-shl Kanagawa-ken(JP) © References cited: EP-A- 0 167 369 US-A- 3 697 624 © Representative: West, Alan Harry et al R.G.C. Jenkins & Co. 26 Caxton Street "Polyurethanes Chemistry and Technology" London SW1H ORJ(GB) (Sauders,Frlsch) Krleger Pub. USA 1983, p. 401 "Textbook of Polymer Science" (Blllmeyer) Wiley Pub. USA 1971, p.237 "Properties of Polymers" (Krevelen), El- 00 sevier Pub. NL, 1976, p.495 00 CO CM O Note: Within nine months from the publication of the mention of the grant of the European patent, any person ^ may give notice to the European Patent Office of opposition to the European patent granted. Notice of opposition qj shall be filed in a written reasoned statement. -
Polymer Properties and Classification
Polymer Characterization LDPE Polyethylene low density HDPE Polyethylene high density ABS Acrylonitrile-butadiene-styrene SAN Styrene-acrylonitrile copolymer EVA Polyethylene co-vinyl acetate PVA Polyvinyl acetate PerkinElmer Solutions for Polymer Characterization Tg(ºC): -130 to 100 Cp (J/g*K): 1,8 to 3,4 Tg(ºC): -130 to 100 Cp (J/g*K): 1,8 to 3,4 Tg(ºC): 110 to 125 CpJ/(g*K): 1,25 to 1,7 Tg(ºC): 95 to 110 CpJ/(g*K): 1,2 Tg(ºC): -45 to 20 CpJ/(g*K): 2,3 Tg(ºC): 25 to 35 CpJ/(g*K): - Tm(ºC): 100 to 120 DHf (J/g): - Tm(ºC): 130 to 140 DHf (J/g): 293 Tm(ºC): - DHf (J/g): - Tm(ºC): - DHf (J/g): - Tm(ºC): 30 to 100 DHf (J/g): 10 to 100 Tm( ºC ): - DHf (J/g): - Td(ºC): 490 to 500 Td(ºC): 490 to 500 Td(ºC): 420 Td(ºC): 420 Td(ºC): 480 Td(ºC): - PP Polypropylene PS PMMA Polymethylmethacrylate PBMA CA Polystyrene Polybuthylmethacrylate Cellulose acetate EP Epoxy resin Molecular Spectroscopy FTIR Differential Scanning Calorimetry Tg(ºC): -20 to -5 CpJ/(g*K): 1,8 Tg(ºC): 90 to 110 Cp (J/g*K): 1,8 to 3,4 Tg(ºC): 85 to 100 CpJ/(g*K): 1,45 to 1,5 Tg(ºC): 15 to 25 CpJ/(g*K): - Tg(ºC): 45 to 60 CpJ/(g*K): - Tg(ºC): 50 to 200 CpJ/(g*K): 1,6 to 2,1 Identify and quantitate organic molecules and compounds, Glass transition & melting temperatures, crystallinity, heat of Understand chemical & physical composition of laminates & fusion, reaction rates, specific heat & heat capacity, curing, Tm(ºC): 165 to 175 DHf (J/g): 207 Tm(ºC): - DHf (J/g): - Tm(ºC): - DHf (J/g): - Tm(ºC): - DHf (J/g): - Tm(ºC): - DHf (J/g): - Tm( ºC): - DHf (J/g): - adhesives , Troubleshoot -
238 Subpart a [Reserved] Subpart B—Substances For
§ 177.1010 21 CFR Ch. I (4–1–11 Edition) 177.1637 Poly(oxy-1,2- 177.2800 Textiles and textile fibers. ethanediyloxycarbonyl-2,6- 177.2910 Ultra-filtration membranes. naphthalenediylcarbonyl) resins. AUTHORITY: 21 U.S.C. 321, 342, 348, 379e. 177.1640 Polystyrene and rubber-modified polystyrene. SOURCE: 42 FR 14572, Mar. 15, 1977, unless 177.1650 Polysulfide polymer-polyepoxy res- otherwise noted. ins. 177.1655 Polysulfone resins. EDITORIAL NOTE: Nomenclature changes to 177.1660 Poly (tetramethylene part 177 appear at 61 FR 14482, Apr. 2, 1996, 66 terephthalate). FR 56035, Nov. 6, 2001, 66 FR 66742, Dec. 27, 177.1670 Polyvinyl alcohol film. 2001, 68 FR 15355, Mar. 31, 2003, and 70 FR 177.1680 Polyurethane resins. 72074, Dec. 1, 2005. 177.1810 Styrene block polymers. 177.1820 Styrene-maleic anhydride copoly- Subpart A [Reserved] mers. 177.1830 Styrene-methyl methacrylate co- polymers. Subpart B—Substances for Use as 177.1850 Textryls. Basic Components of Single 177.1900 Urea-formaldehyde resins in molded and Repeated Use Food Con- articles. 177.1950 Vinyl chloride-ethylene copoly- tact Surfaces mers. 177.1960 Vinyl chloride-hexene-1 copoly- § 177.1010 Acrylic and modified acrylic mers. plastics, semirigid and rigid. 177.1970 Vinyl chloride-lauryl vinyl ether Semirigid and rigid acrylic and modi- copolymers. fied acrylic plastics may be safely used 177.1980 Vinyl chloride-propylene copoly- as articles intended for use in contact mers. with food, in accordance with the fol- 177.1990 Vinylidene chloride/methyl acry- late copolymers. lowing prescribed conditions. The 177.2000 Vinylidene chloride/methyl acry- acrylic and modified acrylic polymers late/methyl methacrylate polymers. -
Labware Chemical Resistance Table
Labware Chemical Resistance Table Interpretation of Chemical Resistance The Chemical Resistance Chart that follows is a general guide only. Because so many factors can affect the chemical resistance of a given product, you should test under your own conditions. Effects of Chemicals on Plastics Chemicals can affect the strength, flexibility, surface appearance, color, dimensions or weight of plastics. The basic modes of interaction which cause these changes are: (1) chemical attack on the polymer chain, with resultant reduction in physical properties, including oxidation; reaction of functional groups in or on the chain; and depolymerization; (2) physical change, including absorption of solvents, resulting in softening and swelling of the plastic; permeation of solvent through the plastic; dissolution in a solvent; and (3) stress cracking from the interaction of a “stress cracking agent” with internal or external stresses. Mixing and/or dilution of certain chemicals can be potentially dangerous. The reactive combination of different chemicals or compounds of two or more classes may cause an undesirable chemical effect or result in an increased temperature, which can affect chemical resistance (as temperature increases, resistance to attack decreases). Other factors affecting chemical resistance include pressure and internal or external stresses (e.g. centrifugation), length of exposure, and concentra tion of the chemical. 608 www.thermoscientifi c.com appendix Environmental Stress Cracking Environmental stress cracking is the failure of a plastic material in the presence of certain types of chemicals. This failure is not a result of chemical attack. Simultaneous presence of three factors causes stress cracking: tensile stress, a stress cracking agent and the inherent susceptability of the plastic to stress cracking. -
Adhesive Bonding of Polyolefin Edward M
White Paper Adhesives | Sealants | Tapes Adhesive Bonding of Polyolefin Edward M. Petrie | Omnexus, June 2013 Introduction Polyolefin polymers are used extensively in producing plastics and elastomers due to their excellent chemical and physical properties as well as their low price and easy processing. However, they are also one of the most difficult materials to bond with adhesives because of the wax-like nature of their surface. Advances have been made in bonding polyolefin based materials through improved surface preparation processes and the introduction of new adhesives that are capable of bonding to the polyolefin substrate without any surface pre-treatment. Adhesion promoters for polyolefins are also available that can be applied to the part prior to bonding similar to a primer. Polyolefin parts can be assembled via many methods such as adhesive bonding, heat sealing, vibration welding, etc. However, adhesive bonding provides unique benefits in assembling polyolefin parts such as the ability to seal and provide a high degree of joint strength without heating the substrate. This article will review the reasons why polyolefin substrates are so difficult to bond and the various methods that can be used to make the task easier and more reliable. Polyolefins and their Surface Characteristics Polyolefins represent a large group of polymers that are extremely inert chemically. Because of their excellent chemical resistance, polyolefins are impossible to join by solvent cementing. Polyolefins also exhibit lower heat resistance than most other thermoplastics, and as a result thermal methods of assembly such as heat welding can result in distortion and other problems. The most well-known polyolefins are polyethylene and polypropylene, but there are other specialty types such as polymethylpentene (high temperature properties) and ethylene propylene diene monomer (elastomeric properties). -
Material Selection Selection
alroplastics.com 800-877-ALRO 2 5 7 6 Material Selection Selection Advantages of Stock Shapes ...............................................10 Material General Selection Criteria ...............................................10-11 Product Descriptions ..................................................... 12-15 Product Selection Chart ................................................. 16-19 IAPD Thermoplastic Rectangle ...................................... 20-21 Property Comparison Charts Slide Wear .......................................................................22 Rotational Wear ..............................................................22 Temperature, Continuous Use .......................................23 Friction Comparison .......................................................23 Tensile Strength ..............................................................24 Impact Resistance ..........................................................24 Thermal Dimensional Stability ......................................25 Moisture Dimensional Stability .....................................25 Hardness Comparison ...................................................26 Weight Comparison ........................................................26 WARNING: These products can potentially expose you to chemicals including, 4-Dioxane, Acetaldehyde, Acrylonitrile, Bisphenol-A, Carbon Black, Chromium, Cumene, Dichloromethane, Ethyl Acrylate, Ethylbenzene, Ethylene Glycol, Formaldehyde, Glass Fibers, Hexachlorobenzene, Lead, Methanol, Nickel, Polyvinyl -
Surface Microhardness, Flexural Strength, and Clasp Retention And
ORIGINAL RESEARCH Surface Microhardness, Flexural Strength, and Clasp Retention and Deformation of Acetal vs Poly-ether-ether Ketone after Combined Thermal Cycling and pH Aging Salma Mahmoudd Fathy1, Radwa Mohsen Kamal Emera2, Reham Mohamed Abdallah3 ABSTRACT Aim: To evaluate the effect of combined thermocycling and artificial saliva pH on flexural strength, surface microhardness, as well as clasp retention and deformation of two different thermoplastic polymers. Materials and methods: Three groups were created, heat-cured polymethyl methacrylate, acetal, and poly-ether-ether ketone (PEEK) resins. Specimens were wrapped in plastic bags containing artificial saliva with three pH values (acidic 5.8, neutral 7.2, and alkaline 8.3). Two Aker clasps materials (acetal and PEEK), for premolar and molar, were stored in neutral salivary pH. Specimens were subjected to 2,000 thermocycles (5–55°C). Surface microhardness, flexural strength, and clasp retention and deformation were evaluated before and after aging. Data were analyzed by ANOVA, Tukey’s test, Student’s t-test, and paired t-tests (p < 0.05). Results: Thermal cycling at acidic and alkaline pH significantly decreased flexural strength and surface microhardness of acetal. It had no significant effect on PEEK properties. Poly-ether-ether ketone showed statistically significant higher mechanical properties in all groups. Acetal clasps exhibited a statistically significant deformation and a corresponding decrease in retention after thermocycling at neutral pH. Conclusion: Mechanical properties of acetal, as well as its clasp retention and deformation, significantly decreased after combining thermal and pH aging and thermal cycling in neutral pH, respectively. Meanwhile, PEEK clasps were not significantly affected. Clinical significance: Different intraoral variables may significantly affect mechanical performance, retention, and deformation of TMs used for denture base and clasp construction. -
Thz Materials
THz Materials Terahertz (THz) radiation is located in the spectral region ~0.1-10 THz (~3 mm - 30 µm, 3 cm-1 - 300 cm-1 ) between the microwave and mid infrared range of the electromagnetic spectrum. In comparison with visible or infrared waves, THz radiation can penetrate into organic materials such as skin, plastics, cloth, or paper products. Because of low photon energy involved, it does not cause any damage associated with ionizing radiation (e.g. X-rays). THz waves do not penetrate into metals. These properties can be used in process (e.g. drugs manufacturing) and quality control as well as in THz imaging. It is also of great current interest for such applications as safety control, packaging inspection, semiconductor characterization, chemical composition analysis, and biomedical investigations, with great promise for spectroscopy, defense imaging, and security applications. Fig. 2. The THz signals transmitted through air and HRFZ-Si.(*) Traditionally for THz applications we use High Resistivity Float Zone The complex dielectric permittivity of silicon depends on its Silicon (HRFZ-Si) as it is the most investigated substance for operating conductivity (i.e. free-carrier concentration). Figure 3 shows the within this range and has a good transmission performance. In parallel dielectric permittivity of silicon at 1 THz with different impurity with this material we have been investigating other materials which concentration. For low impurity concentration the dielectric also can be utilized in THz range. permittivity is almost a real value, which is approximately equal Below you can see transmission spectra and other characteristics of to the high frequency dielectric permittivity.