Changes in Motorsport Regulations Are Prompting Fresh Developments in Engine Valve Technology, As Wayne Ward Reports
Total Page:16
File Type:pdf, Size:1020Kb
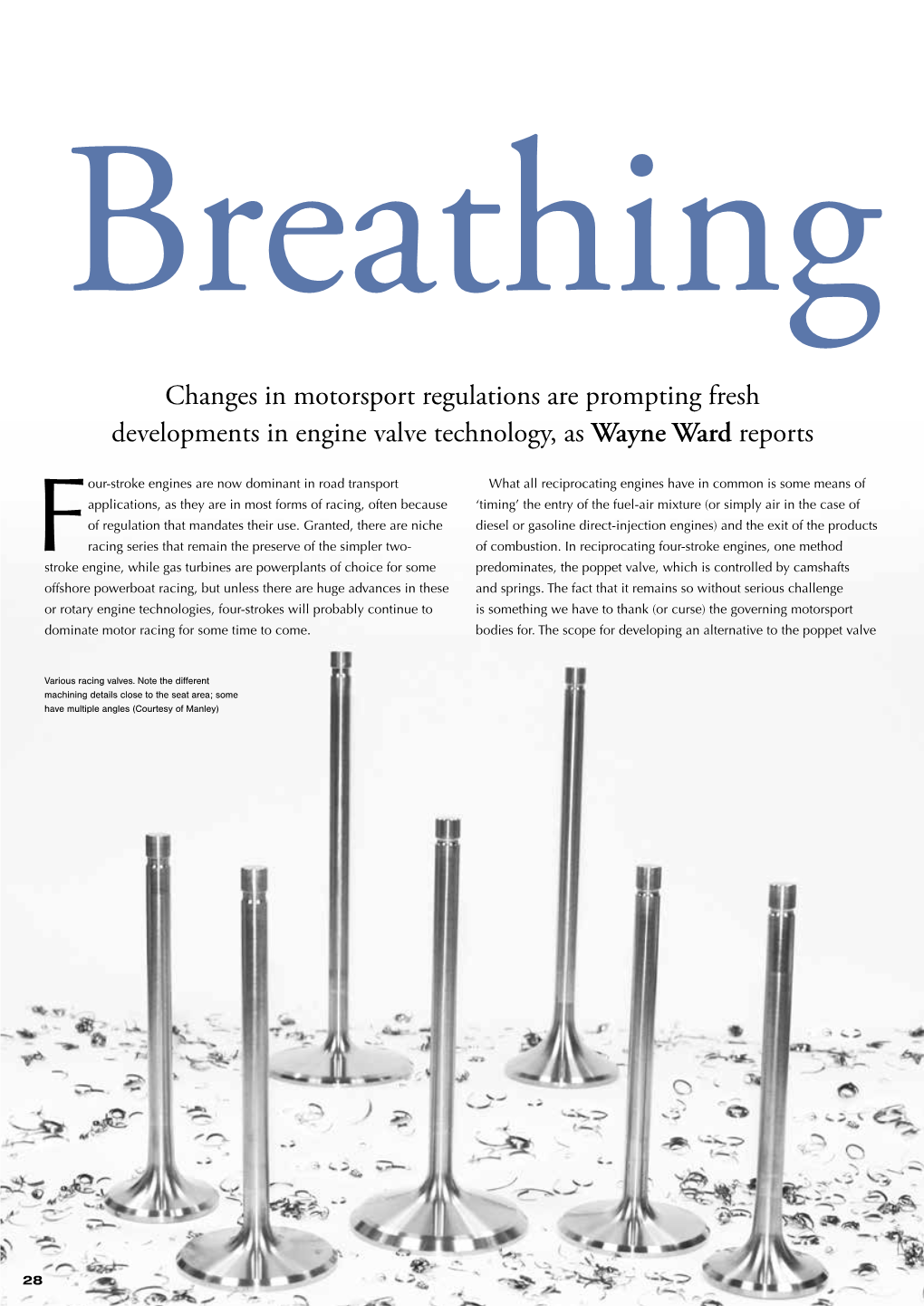
Load more
Recommended publications
-
Desmodromics Mick Walker Explains How Ducati Beat Tbe World with Spring-Less Valve Operation
og , Desmodromics Mick Walker explains how Ducati beat tbe world with spring-less valve operation HE WORD desmodmmic wil! not be the bounce and get a higher-revving engine successful and was not developed, but in found in the Oxford or any other - in theory. the 1920s several other manufacturers tried T English dictionaries. It was coined This had been known since the early days variants of it. One layout, the Vagova, from two Greek words, meaning 'controlled of the internal combustion engine but for utilized a cam track embodying inner and run' and its mechanical function is to elimi- many years no designer managed to success- outer cam forms which guided a roller nate one of the phenomenon of valve float, fully harness it. One of the first examples of attached to one end of a 'rocker', the other or 'bounce'. This happens at high revs when completely positive mechanical valve oper- end of the rocker was forked to embrace the valve springs are unable to respond ation was used by the French Delage concern the valve stem. To provide the required quickly enough to close the valve back on in its grand prix car of 1914 - and the freedom for seating, the pivot of the rocker their seats. 11le desmodromic idea was to French knew the method as desmod- was given a small amount of spring-Ioaded replace troublesome springs with a romique. float parallel to the valve axis. me(\. jcal closing system much like that The Delage engine employed four valves Alternative methods investigated were to usedló open them. -
A Camshaft Non-Linear Model for the Desmodromic Valve Train Simulation
A Camshaft Non-Linear Model for the Desmodromic Valve Train Simulation A. Rivola, *A. Carlini DIEM – Mechanical Engineering Department, University of Bologna viale Risorgimento, 2 – I40136, Bologna, Italy email: [email protected] *Test Bench Engineer, DucatiCorse s.r.l., via Cavalieri Ducati, 3 – I40132, Bologna, Italy Abstract In this paper the dynamic behaviour of the desmodromic valve train of a motorbike engine is simulated and analysed. The valve train model takes into account the mass distribution, the link elastic flexibility, and the presence of several non-linearities. The camshafts, which are supported by hydrodynamic journal bearings, are modelled by means of finite rotating elements based on Timoshenko beams with the effect of gyroscopic moment. The non-linear bearing forces are analytically obtained under the finite-length bearing assumption. The comparison between the numerical results and the experimental data – in terms of valve acceleration and camshaft angular velocity – shows that the effectiveness of the model is satisfactorily assessed. The paper mainly focuses on two points: the validation procedure of the finite element model of the camshafts, and the study of the simulated camshaft centreline trajectories. 1 Introduction This paper deals with a kineto-elastodynamic model of the desmodromic valve train of a Ducati motorbike engine. The desmodromic train is a mechanism with positive-drive cams and – in comparison with the widely-used trains having a closing spring [1–3] – presents different dynamic behaviour, as shown in [4– 7]. When operating at high-speed, a mechanism shows a dynamic behaviour which is affected by the link elastic flexibility and mass distribution, as well as the effects of backlashes and friction in joints. -
Design of an Effective Timing System for ICE
Design of an Effective Timing System for ICE Andrea Miraglia∗ and Giuseppe Monteleoney yDepartment of Electrical, Electronics, and Informatics Engineering, University of Catania, Catania Italy ∗Istituto Nazionale di Fisica Nucleare - Laboratori Nazionali del Sud, Catania Italy Abstract—The present paper describes the design and the a four-stroke engine, generally conical valves are employed; prototype realization process of a new effective timing system they open under the action of cams, fitted on the camshaft par- for ICE (internal combustion engine). In particular, the present allel to and activated by the crankshaft, subsequently closing paper outlines the dynamic behavior and related performance of the innovative timing system applied to a two cylinder engine. at the position due to the push by appropriate calibrated coil The procedure to validate the prototype, based on experimental springs [1], [2], [3], [4], [5]. tests carried out on a test bench, is presented and discussed. The traditional finite elements method and computational fluid A. The main timing elements dynamics (CFD) analysis are used to estimate the dynamic performance of the engine with the new timing system. The The main elements of a timing system are: comparison with the data reported in bibliography shows the • Camshaft effectiveness of the new timing system. The study indicates that the proposed system is of great significance for the development • Valves (guides, seals and springs) of timing system in an automotive engine. • Tappets • Pushrods Keywords-Specific power; Computational dynamic analysis; 3D modeling; CFD analysis; Reliability. • Rocker arms The most common valve train system involves pushrods I. INTRODUCTION and rocker arms; however, there are other valve train systems The idea of a new timing system originated from the passion available, offering such solutions as single or double camshaft. -
Modelling the Elastodynamic Behaviour of a Desmodromic Valve Train
Modelling the Elastodynamic Behaviour of a Desmodromic Valve Train Alessandro RIVOLA (*), Andrea CARLINI (*), and Giorgio DALPIAZ (**) (*) DIEM - University of Bologna Viale Risorgimento, 2, I - 40136 Bologna, Italy e-mail: [email protected] (**) Dept. of Engineering, University of Ferrara Via Saragat, 1, I - 44100 Ferrara, Italy e-mail: [email protected] Abstract This paper deals with a lumped-parameter model of a motorbike engine’s desmodromic valve train. The model of such an uncommon cam system is developed and validated with the aid of experimental measurements carried out on a test bench which operates the cam mechanism by means of an electrically powered driveline. The model describes the mechanical system taking into account the mass distribution, the link elastic flexibility, and the presence of several non-linearities. The model parameter estimation is discussed and the effectiveness of the model is assessed by a comparison with experimental results. In addition, the model is employed to estimate the magnitude of contact forces and to predict the system behaviour as a consequence of changes in some design parameters; therefore, it may be used as a tool both in design optimisation and diagnostics. 1 Introduction train of a Ducati motorbike engine. Only works on widely-used trains with closing spring were found in Nowadays the study of the dynamic response of literature [7–9]; in those cases the valve spring plays flexible mechanisms operating at high speed is an important role in the system dynamics. becoming more and more important and several Conversely, in the case of desmodromic valve trains studies can be found in literature [1–4]. -
19FFL-0023 2-Stroke Engine Options for Automotive Use: a Fundamental Comparison of Different Potential Scavenging Arrangements for Medium-Duty Truck Applications
Citation for published version: Turner, J, Head, RA, Chang, J, Engineer, N, Wijetunge, RS, Blundell, DW & Burke, P 2019, '2-Stroke Engine Options for Automotive Use: A Fundamental Comparison of Different Potential Scavenging Arrangements for Medium-Duty Truck Applications', SAE Technical Paper Series, pp. 1-21. https://doi.org/10.4271/2019-01-0071 DOI: 10.4271/2019-01-0071 Publication date: 2019 Document Version Peer reviewed version Link to publication The final publication is available at SAE Mobilus via https://doi.org/10.4271/2019-01-0071 University of Bath Alternative formats If you require this document in an alternative format, please contact: [email protected] General rights Copyright and moral rights for the publications made accessible in the public portal are retained by the authors and/or other copyright owners and it is a condition of accessing publications that users recognise and abide by the legal requirements associated with these rights. Take down policy If you believe that this document breaches copyright please contact us providing details, and we will remove access to the work immediately and investigate your claim. Download date: 27. Sep. 2021 Paper Offer 19FFL-0023 2-Stroke Engine Options for Automotive Use: A Fundamental Comparison of Different Potential Scavenging Arrangements for Medium-Duty Truck Applications Author, co-author (Do NOT enter this information. It will be pulled from participant tab in MyTechZone) Affiliation (Do NOT enter this information. It will be pulled from participant tab in MyTechZone) Abstract For the opposed-piston engine, once the port timing obtained by the optimizer had been established, a supplementary study was conducted looking at the effect of relative phasing of the crankshafts The work presented here seeks to compare different means of on performance and economy. -
Desmosedici Twinpulse Engine to Power Ducati Attack on Motogp Championship
DESMOSEDICI TWINPULSE ENGINE TO POWER DUCATI ATTACK ON MOTOGP CHAMPIONSHIP Four-cylinder 989cc ‘L’ engine, with simultaneous firing order in cylinders of the same bank and desmodromic timing – Track tests to get underway in July also in traditional firing layout – Race debut with two riders at first round of MotoGP 2003. Bologna, 4 February 2002 - Nine months after the start of the MotoGP project, announced last May at Jerez de la Frontera, Ducati Corse has completed the design stage of its new engine, called Desmosedici (16-valve Desmo), which will begin testing on the dyno within the next three months. Ducati Corse Managing Director Claudio Domenicali explained the decision-making process behind the choice of the new engine: “After analysing all the possibilities offered by the regulations and on the basis of computer simulations, we are convinced that a massive power output is required to be competitive in MotoGP. It would have been difficult to obtain this power with conventional twin-cylinder engines, which amongst other things are only given a 10 kg weight advantage over 4 and 5 cylinder engines in the regulations. As a result, the bore size would have to be taken to an extremely high value, with the risk of incurring serious combustion problems.” “For this reason, in the preliminary study phase, we considered a twin-cylinder oval piston engine to be an excellent layout for the new regulations. With the same weight as 4 and 5 cylinder engines, this layout combines the typical advantages of a twin in terms of power output and delivery, with the performance necessary to compete at the same level as the multi-cylinder units”. -
Pattakon Vvas –A Solution for the Idling Problem of the Known Throttle-Less Vvas
pattakon VVAs –A solution for the idling problem of the known throttle-less VVAs. –Mechanical VVAs with independently variable lift and duration. –Mechanical VVAs without valve springs (desmodromic) for racing engines. To the point Every motorcycle maker has in production a 1,000cc bike engine with top power at around 12,000 rpm and red line at 13,000 rpm or even higher. Such an engine cannot replace the engine of a heavy car. The peaky torque curve, the medium to low revs characteristics, the partial load response etc cannot meet the needs of a heavy vehicle. Think of replacing the conventional valve train of the 1,000cc bike engine by a high revving VVA. But, do high revving VVAs exist? pattakon VVAr 4cylinder, 1600cc (9,000rpm rev limiter) accelerating on a highway (click on the button) Rod-version and roller-version VVA prototypes pattakon VVAr, 4cylinder, 1600cc, 9000 rpm full version pattakon VVAr, 1600cc, 9000 rpm, full version pattakon VVAr, 4cylinder, 1600cc, 9000 rpm light version (intake side only) pattakon VVAr, 4cylinder, 1600cc, 9000 rpm light version (intake side only) VVAr parts. 0.150 Kp each “complete new rocker arm” versus 0.260 Kp of the original 2-mode. Control of the VVAr prototype engine (a modified B16A 1600cc) The rotation of the intake control shaft defines the lift of the intake valves. A rheostat is displaced by the intake control shaft and its signal is fed to the MAP input of the ECU (the original MAP sensor is removed: without a throttle valve the pressure just before the intake valves is always atmospheric). -
Four-Stroke Cycle
FOUR-STROKE CYCLE The four-stroke cycle (or Otto cycle) of an internal combustion engine is the cycle most commonly used for automotive and industrial purposes today (cars and trucks, generators, etc). It was conceptualized by the French engineer, Alphonse Beau de Rochas in 1862, and independently, by the German engineer Nikolaus Otto [[1]] in 1876. The four-stroke cycle is more fuel-efficient and clean burning than the two-stroke cycle, but requires considerably more moving parts and manufacturing expertise. Moreover, it is more easily manufactured in multi-cylinder configurations than the two-stroke, making it especially useful in high-output applications such as cars. The later-invented Wankel engine has four similar phases but is a rotary combustion engine rather than the much more usual, reciprocating engine of the four-stroke cycle. Four-stroke cycle (or Otto cycle) The Otto cycle is characterized by four strokes, or straight movements alternately, back and forth, of a piston inside a cylinder: intake (induction) stroke compression stroke power (combustion) stroke exhaust stroke The cycle begins at top dead center, when the piston is at its uppermost point. On the first downward stroke (intake) of the piston, a mixture of fuel and air is drawn into the cylinder through the intake (inlet) port. The intake (inlet) valve (or valves) then close(s), and the following upward stroke (compression) compresses the fuel-air mixture. The air-fuel mixture is then ignited, usually by a spark plug for a gasoline or Otto cycle engine, or by the heat and pressure of compression for a Diesel cycle of compression ignition engine, at approximately the top of the compression stroke. -
VALVE CONTROLS INFINITE POSSIBILITIES ROGER STONE, CAMCON AUTOMOTIVE TECHNICAL DIRECTOR Where All the Pieces Fall Into Place
The pan-European magazine of SAE International May/June 2013 VALVE CONTROLS INFINITE POSSIBILITIES ROGER STONE, CAMCON AUTOMOTIVE TECHNICAL DIRECTOR Where All the Pieces Fall Into Place Let’s face it; driveline design can be a real brainteaser. Reduced emissions. Improved fuel economy. Enhanced vehicle performance. Getting all the pieces to fit is challenging—especially when you can’t see the whole picture. That’s why you need one more piece to solve the driveline puzzle. Introducing DrivelineNEWS.com—a single, all-encompassing website exclusively dedicated to driveline topics for both on- and off-road vehicles. Log on for the latest news, market intelligence, technical innovations and hardware animations to help you find solutions and move your business forward. It takes ingenuity and persistence to succeed in today’s driveline market. Test your skills at DrivelineNEWS.com/Puzzle. Solve the puzzle to enter to win a Kindle Fire. © 2013 The Lubrizol Corporation. All rights reserved. 121569 Contents 12 12 Cover Story 5 Comment Valve controls Imagine a valve control system that is infinitely 6 variable irrespective of engine speed and load. News Impossible? Not according to Camcon Automotive’s • Exclusive: technical director Roger Stone, as Ian Adcock Engine knock discovers predicted 16 Biomimicry • Volvo diesel breakthrough Mother Nature knows best What can the automotive industry learn from nature • Driveline software when it comes to weight saving? Ryan Borroff has 20 been finding out • Four-way cat for petrol engines 20 Fuel injection systems Building up the pressure 11 Tony Lewin reports on the growing trend towards even The Columnist higher line pressures in injection systems. -
(12) United States Patent (10) Patent No.: US 6,311,659 B1 Pierik (45) Date of Patent: Nov
USOO6311659B1 (12) United States Patent (10) Patent No.: US 6,311,659 B1 Pierik (45) Date of Patent: Nov. 6, 2001 (54) DESMODROMIC CAM DRIVEN VARIABLE 1,740,790 12/1929 Stanton ............................. 123/90.25 VALVE TIMING MECHANISM 4,364,341 12/1982 Holtmann .......................... 123/90.17 5.988,125 11/1999 Hara et al. ........................ 123/90.16 (75) Inventor: Ronald Jay Pierik, Rochester, NY (US) * cited by examiner (73) Assignee: Delphi Technologies, Inc., Troy, MI (US) Primary Examiner Thomas Denion (*) Notice: Subject to any disclaimer, the term of this ASSistant Examiner Jaime Corrigan patent is extended or adjusted under 35 (74) Attorney, Agent, or Firm John A. Vanophen U.S.C. 154(b) by 0 days. (57) ABSTRACT (21) Appl. No.: 09/482,798 A desmodromic cam driven variable valve timing (VVT) (22) Filed: Jan. 13, 2000 mechanism includes dual rotary opening and closing cams Related U.S. Application Data for actuating a rocker mechanism that drives valve actuating (60) Provisional application No. 60/136,923, filed on Jun. 1, oscillating cams. The dual rotary cam drive positively actu 1999. ates the rocker mechanism in both valve opening and valve (51) Int. Cl." .................................................... F01L 1/30 closing directions and thus avoids the need to provide return (52) U.S. Cl. ..................................... 123/90.24; 123/90.15; Springs as required in prior cam driven mechanisms to bias 123/90.16; 123/90.17; 123/90.25 the mechanisms toward a valve closed position. A variable (58) Field of Search .............................. 123/90.16, 90.17, ratio Slide and slot control lever drive as well as a back force 123/90.24, 90.25 limiting worm drive for the control shaft are combined with (56) References Cited the desmodromic cam mechanism to provide additional System advantages. -
Design and Modification of Cam Operated Spring-Less Valve System in IC Engine
IOSR Journal of Engineering (IOSR JEN) www.iosrjen.org ISSN (e): 2250-3021, ISSN (p): 2278-8719, || Special Issue || June-2019, || PP 04-09 || Design and Modification of Cam Operated Spring-less Valve System in IC Engine D. V. Bhise1, Aishwarya R. Kulkarni2, Omkar S. Khaire3, Prasad S. Darekar4, Shubham R. Kochale5, Sunny R. Dhadve6 1(D. V. Bhise, Associate Professor, Dept. of Mechanical Engineering, JSPM Narhe Technical Campus, Pune, Maharashtra, India) 2,3,4,5,6(Students,Department of Mechanical Engineering, S.P.P.U. University, J.S.P.M. Narhe Technical Campus, Pune, Maharashtra, India) Abstract: This project presents the spring less valve system used in the IC engines.This mechanism has a closing cam which does not allow cam jump as conventional valve system. It has helped us to find out how spring less valve system is better than conventional valve system. We have found out the real importance of this spring less system at higher rpm of engine and need of this system at higher rpm. This system improves the performance of IC engine by reducing power consumption for overcoming spring stiffness and avoid cam jump at high speed. Keyword: Springless valve system, closing cam, cam jump, IC Engine, Stiffness I. Introduction 1.1 Introduction to conventional Spring System IC Engine uses valves to handle charge in and out of the cylinder for their operation. There are intake valves and exhaust valves which are to be spring operated at right time when needed and remains close to seal the cylinder when compression and combustion is occurred. -
The Development of the Single Sleeve Valve Two-Stroke Engine Over the Last 110 Years
energies Review The Silent Path: The Development of the Single Sleeve Valve Two-Stroke Engine over the Last 110 Years Robert Head * and James Turner Mechanical Engineering, Faculty of Engineering and Design, University of Bath, Bath BA2 7AY, UK; [email protected] * Correspondence: [email protected]; Tel.: +44-0789-561-7437 Abstract: At the beginning of the 20th century the operational issues of the Otto engine had not been fully resolved. The work presented here seeks to chronicle the development of one of the alternative design pathways, namely the replacement for the gas exchange mechanism of the more conventional poppet valve arrangement with that of a sleeve valve. There have been several successful engines built with these devices, which have a number of attractive features superior to poppet valves. This review moves from the initial work of Charles Knight, Peter Burt, and James McCollum, in the first decade of the 20th century, through the work of others to develop a two-stroke version of the sleeve- valve engine, which climaxed in the construction of one of the most powerful piston aeroengines ever built, the Rolls-Royce Crecy. After that period of high activity in the 1940s, there have been limited further developments. The patent efforts changed over time from design of two-stroke sleeve-drive mechanisms through to cylinder head cooling and improvements in the control of the thermal expansion of the relative components to improve durability. These documents provide a foundation for a design of an internal combustion engine with potentially high thermal efficiency. Keywords: two-stroke; sleeve valves; patents Citation: Head, R.; Turner, J.