Photoelasticity
Total Page:16
File Type:pdf, Size:1020Kb
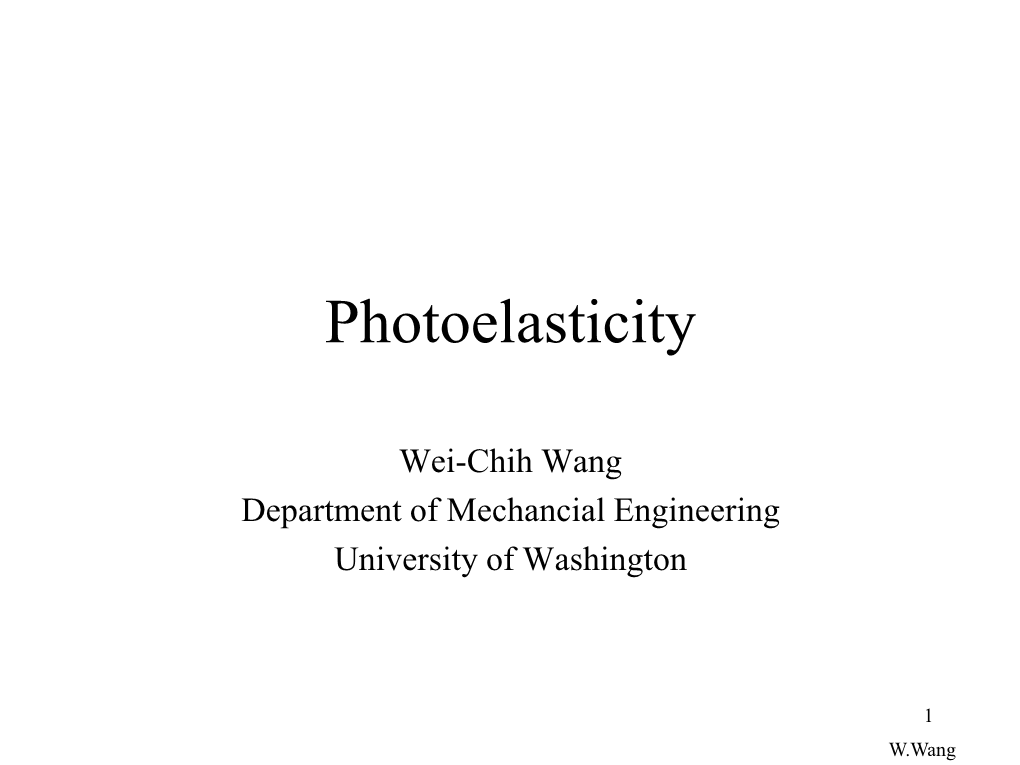
Load more
Recommended publications
-
Processor U.S
USOO5926295A United States Patent (19) 11 Patent Number: 5,926,295 Charlot et al. (45) Date of Patent: Jul. 20, 1999 54) HOLOGRAPHIC PROCESS AND DEVICE 4,602,844 7/1986 Sirat et al. ............................. 350/3.83 USING INCOHERENT LIGHT 4,976,504 12/1990 Sirat et al. .. ... 350/3.73 5,011,280 4/1991 Hung.............. ... 356/345 75 Inventors: Didier Charlot, Paris; Yann Malet, 5,081,540 1/1992 Dufresne et al. ... ... 359/30 Saint Cyr l’Ecole, both of France 5,081,541 1/1992 Sirat et al. ...... ... 359/30 5,216,527 6/1993 Sharnoff et al. ... 359/10 73 Assignee: Le Conoscope SA, Paris, France 5,223,966 6/1993 Tomita et al. .......................... 359/108 5,291.314 3/1994 Agranat et al. ......................... 359/100 21 Appl. No.: 08/681,926 22 Filed: Jul. 29, 1996 Primary Examiner Jon W. Henry Attorney, Agent, or Firm Michaelson & Wallace; Peter L. Related U.S. Application Data Michaelson; John C. Pokotylo 62 Division of application No. 08/244.249, filed as application 57 ABSTRACT No. PCT/FR92/01095, Nov. 25, 1992, Pat. No. 5,541,744. An optical device for generating a signal based on a distance 30 Foreign Application Priority Data of an object from the optical device. The optical device includes a first polarizer, a birefringent crystal positioned Nov. 27, 1991 FR France ................................... 91. 14661 optically downstream from the first polarizer, and a Second 51) Int. Cl. .............................. G03H 1/26; G01B 9/021 polarizer arranged optically downstream from the birefrin 52 U.S. Cl. ................................... 359/30; 359/11; 359/1; gent crystal. -
Lab 8: Polarization of Light
Lab 8: Polarization of Light 1 Introduction Refer to Appendix D for photos of the appara- tus Polarization is a fundamental property of light and a very important concept of physical optics. Not all sources of light are polarized; for instance, light from an ordinary light bulb is not polarized. In addition to unpolarized light, there is partially polarized light and totally polarized light. Light from a rainbow, reflected sunlight, and coherent laser light are examples of po- larized light. There are three di®erent types of po- larization states: linear, circular and elliptical. Each of these commonly encountered states is characterized Figure 1: (a)Oscillation of E vector, (b)An electromagnetic by a di®ering motion of the electric ¯eld vector with ¯eld. respect to the direction of propagation of the light wave. It is useful to be able to di®erentiate between 2 Background the di®erent types of polarization. Some common de- vices for measuring polarization are linear polarizers and retarders. Polaroid sunglasses are examples of po- Light is a transverse electromagnetic wave. Its prop- larizers. They block certain radiations such as glare agation can therefore be explained by recalling the from reflected sunlight. Polarizers are useful in ob- properties of transverse waves. Picture a transverse taining and analyzing linear polarization. Retarders wave as traced by a point that oscillates sinusoidally (also called wave plates) can alter the type of polar- in a plane, such that the direction of oscillation is ization and/or rotate its direction. They are used in perpendicular to the direction of propagation of the controlling and analyzing polarization states. -
How Significant an Influence Is Urban Form on City Energy Consumption for Housing and Transport?
How significant an influence is urban form on city energy consumption for housing and transport? Authored by: Dr Alan Perkins South Australian Department of Transport and Urban Planning and University of South Australia [email protected] How significant an influence is urban form on city energy consumption for housing & transport? Perkins URBAN FORM AND THE SUSTAINABILITY OF CITIES The ecological sustainability of cities can be measured, at the physical level, by the total flow of energy, water, food, mineral and other resources through the urban system, the ecological impacts involved in the generation of those resources, the manner in which they are used, and the manner in which the outputs are treated. The gap between the current unsustainable city and the ideal of the sustainable city has been described in the following way (Haughton, 1997). Existing cities are characterised by: The Sustainable city would be A high degree of external dependence, characterised by: extensive externalisation of Intensive internalisation of economic environmental costs, open systems, and environmental activities, circular linear metabolism and ‘buying-in’ metabolism, bioregionalism and additional carrying capacity. urban autarky. Urban forms are required therefore which will be best suited to the conception of the more self-sustaining, less resource hungry and waste profligate city. As cities seek to make their energy, water, biological and materials sub-systems more sustainable, the degree to which the intensification of urban development is supportive of these aims will become clearer. Nevertheless, many who have sought to portray what constitutes sustainable urban form from this broader perspective have included intensification, both urban and regional, as a key element (Berg et al, 1990; Register et al, 1990; Owens, 1994; Trainer, 1995; Breheny & Rookwood, 1996; Newman & Kenworthy, 1999; Barton & Tsourou, 2000). -
Principles of Retarders
Polarizers PRINCIPLES OF RETARDERS etarders are used in applications where control or Ranalysis of polarization states is required. Our retarder products include innovative polymer and liquid crystal materials. Crystalline materials such as quartz and Retarders magnesium fluoride are also available upon request. Please call for a custom quote. A retarder (or waveplate) is an optical device that resolves a light wave into two orthogonal linear polarization components and produces a phase shift between them. The resulting light wave is generally of a different polarization form. Ideally, retarders do not polarize, nor do they induce an intensity change in the Crystals Liquid light beam, they simply change its polarization form. state. The transmitted light leaves the retarder elliptically All standard catalog Meadowlark Optics’ retarders are polarized. made from birefringent, uniaxial materials having two Retardance (in waves) is given by: different refractive indices – the extraordinary index ne = tր and the ordinary index no. Light traveling through a retarder has a velocity v where: dependent upon its polarization direction given by  = birefringence (ne - no) Spatial Light Modulators v = c/n = wavelength of incident light (in nanometers) t = thickness of birefringent element where c is the speed of light in a vacuum and n is the (in nanometers) refractive index parallel to that polarization direction. Retardance can also be expressed in units of length, the By definition, ne > no for a positive uniaxial material. distance that one polarization component is delayed For a positive uniaxial material, the extraordinary axis relative to the other. Retardance is then represented by: is referred to as the slow axis, while the ordinary axis is ␦Ј ␦  referred to as the fast axis. -
Response of a Nonlinear String to Random Loading1
discussion the barreling of the specimen were not large enough to be noticea- Since ble. The authors believe the effects of lateral inertia are small and 77" ^ DL much less serious than the end conditions. Referring again to ™ = g = Wo Fig. 4, the 1.5, 4.5, 6.5, and 7.5 fringes are nearly uniformly dis- tributed over the width of the specimen. The other fringes are and not as well distributed, but it is believed that the conditions at DL the ends of the specimen produced the irregularities rather than 7U72 = VV^ tr,2 = =-, lateral inertia effects. f~1 3ft 7'„ + AT) If the material were perfectly elastic and if one neglected lateral one has inertia effects, the fringes would build up as a consequence of wave propagation and reflection. Thus a difference in the fringe t/7W = (i + at/To)-> = (i + ffff./v)-1 (5) order over the length of the specimen woidd always exist. Inspec- tion of Fig. 4 shows this wave-propagation effect for the first which is Caughey's result for aai.^N small, which it must be for 6 frames as the one-half fringe propagates down the specimen the analysis to be consistent. It is obvious that the new linear Downloaded from http://asmedigitalcollection.asme.org/appliedmechanics/article-pdf/27/2/369/5443489/370_1.pdf by guest on 27 September 2021 and reflects from the right-hand pendulum. However, from system with tension To + AT will satisfy equipartition. frame 7 on there is little evidence of wave propagation and the The work just referred to does not use equation (1) but rather fringe order at both ends of the specimen is equal. -
Impact Response of Strengthened Glass with Ultrahigh Residual Compressive Stresses
IMPACT RESPONSE OF STRENGTHENED GLASS WITH ULTRAHIGH RESIDUAL COMPRESSIVE STRESSES By PHILLIP A. JANNOTTI A DISSERTATION PRESENTED TO THE GRADUATE SCHOOL OF THE UNIVERSITY OF FLORIDA IN PARTIAL FULFILLMENT OF THE REQUIREMENTS FOR THE DEGREE OF DOCTOR OF PHILOSOPHY UNIVERSITY OF FLORIDA 2015 © 2015 Phillip A. Jannotti To my hero ACKNOWLEDGMENTS Thanks to my family and friends for their support during my graduate studies, without which my time as a graduate student would not be have been as enjoyable. A special thanks to my girlfriend, Jen, who put up with me during my time here at Florida. Through good times and bad, it is with all of your support that I have reached this point in my life. Thanks to my graduate committee, Dr. Ghatu Subhash, Dr. Peter Ifju, Dr. Nagaraj Arakere, and Dr. John Mecholsky, for their time and attention reviewing my work. Their insight and suggestions have been invaluable to my research. I would like to especially express gratitude to my advisor, Dr. Ghatu Subhash. I sincerely appreciate everything you have done for me, for reading and re-reading every manuscript revision, and for watching and re-watching every presentation. I truly appreciate the countless hours you have invested in me. This research was made with Government support under and awarded by DOD, AirForce Office of Scientific Research, National Defense Science and Engineering Graduate (NDSEG) Fellowship, 32 CFR 168a, and by Saxon Glass Technologies. 4 TABLE OF CONTENTS page ACKNOWLEDGMENTS ...............................................................................................................4 -
Characterizing the Oblique Incidence Response and Noise Reduction Techniques for Luminescent Photoelastic Coatings
CHARACTERIZING THE OBLIQUE INCIDENCE RESPONSE AND NOISE REDUCTION TECHNIQUES FOR LUMINESCENT PHOTOELASTIC COATINGS By JOHN C. NICOLOSI JR. A THESIS PRESENTED TO THE GRADUATE SCHOOL OF THE UNIVERSITY OF FLORIDA IN PARTIAL FULFILLMENT OF THE REQUIREMENTS FOR THE DEGREE OF MASTER OF SCIENCE UNIVERSITY OF FLORIDA 2004 Copyright 2004 by John C. Nicolosi Jr. ACKNOWLEDGMENTS I would like to thank my advisors, Dr. Peter Ifju and Dr. Paul Hubner, for all of their support and guidance. I would also like to thank Dr. Leishan Chen for all of the assistance he provided me, and Dr. Bhavani Sankar for his valuable advice. I would also like to thank my family members for all of the support they have given me over the years. iii TABLE OF CONTENTS page ACKNOWLEDGMENTS ................................................................................................. iii LIST OF FIGURES .......................................................................................................... vii ABSTRACT....................................................................................................................... ix CHAPTER 1 INTRODUCTION ........................................................................................................1 1.1 Historical Background of Photoelasticity..............................................................1 1.2 Research History at the University of Florida .......................................................3 1.3 Research Objectives...............................................................................................4 -
Optical and Thin Film Physics Polarisation of Light
OPTICAL AND THIN FILM PHYSICS POLARISATION OF LIGHT An electromagnetic wave such as light consists of a coupled oscillating electric field and magnetic field which are always perpendicular to each other; by convention, the "polarization" of electromagnetic waves refers to the direction of the electric field. In linear polarization, the fields oscillate in a single direction. In circular or elliptical polarization, the fields rotate at a constant rate in a plane as the wave travels. The rotation can have two possible directions; if the fields rotate in a right hand sense with respect to the direction of wave travel, it is called right circular polarization, while if the fields rotate in a left hand sense, it is called left circular polarization. On the other side of the plate, examine the wave at a point where the fast-polarized component is at maximum. At this point, the slow-polarized component will be passing through zero, since it has been retarded by a quarter-wave or 90° in phase. Moving an eighth wavelength farther, we will note that the two are the same magnitude, but the fast component is decreasing and the slow component is increasing. Moving another eighth wave, we find the slow component is at maximum and the fast component is zero. If the tip of the total electric vector is traced, we find it traces out a helix, with a period of just one wavelength. This describes circularly polarized light. Left-hand polarized light is produced by rotating either the waveplate or the plane of polarization of the incident light 90° . -
Stokes Polarimetry
photoelastic modulators Stokes Polarimetry APPLICATION NOTE by Dr. Theodore C. Oakberg beforehand. The polarimeter should be aligned so that the James Kemp’s version of the photoelastic modulator was passing axis of the modulator is at 45 degrees to the known invented for use as a polarimeter, particularly for use in linear polarization direction, as shown. The polarizer is oriented astronomy. The basic problem is measuring net polarization at right angles to the plane of the incident linear polarization components in what is predominantly an unpolarized light component. source. Dr. Kemp was able to measure a polarization The circular polarization component will produce a signal at the component of light less than 106 below the level of the total modulator frequency, 1f. If the sense of the circular polarization light intensity. is reversed, this will be shown by an output of opposite sign The polarization state of a light source is represented by four from the lock-in amplifi er. This signal is proportional to Stokes numerical quantities called the “Stokes parameters”.1,2 These Parameter V. correspond to intensities of the light beam after it has passed The linear polarization component will give a signal at twice the through certain devices such as polarized prisms or fi lms and modulator frequency, 2f. A linearly polarized component at right wave plates. These are defi ned in Figure 1. angles to the direction shown will produce a lock-in output with I - total intensity of light beam opposite sign. This signal is proportional to Stokes Parameter U. y DETECTOR y A linear component of polarization which is at 45 degrees to the I x x I x x direction shown will produce no 2f signal in the lock-in amplifi er. -
Fringe Season 1 Transcripts
PROLOGUE Flight 627 - A Contagious Event (Glatterflug Airlines Flight 627 is enroute from Hamburg, Germany to Boston, Massachusetts) ANNOUNCEMENT: ... ist eingeschaltet. Befestigen sie bitte ihre Sicherheitsgürtel. ANNOUNCEMENT: The Captain has turned on the fasten seat-belts sign. Please make sure your seatbelts are securely fastened. GERMAN WOMAN: Ich möchte sehen wie der Film weitergeht. (I would like to see the film continue) MAN FROM DENVER: I don't speak German. I'm from Denver. GERMAN WOMAN: Dies ist mein erster Flug. (this is my first flight) MAN FROM DENVER: I'm from Denver. ANNOUNCEMENT: Wir durchfliegen jetzt starke Turbulenzen. Nehmen sie bitte ihre Plätze ein. (we are flying through strong turbulence. please return to your seats) INDIAN MAN: Hey, friend. It's just an electrical storm. MORGAN STEIG: I understand. INDIAN MAN: Here. Gum? MORGAN STEIG: No, thank you. FLIGHT ATTENDANT: Mein Herr, sie müssen sich hinsetzen! (sir, you must sit down) Beruhigen sie sich! (calm down!) Beruhigen sie sich! (calm down!) Entschuldigen sie bitte! Gehen sie zu ihrem Sitz zurück! [please, go back to your seat!] FLIGHT ATTENDANT: (on phone) Kapitän! Wir haben eine Notsituation! (Captain, we have a difficult situation!) PILOT: ... gibt eine Not-... (... if necessary...) Sprechen sie mit mir! (talk to me) Was zum Teufel passiert! (what the hell is going on?) Beruhigen ... (...calm down...) Warum antworten sie mir nicht! (why don't you answer me?) Reden sie mit mir! (talk to me) ACT I Turnpike Motel - A Romantic Interlude OLIVIA: Oh my god! JOHN: What? OLIVIA: This bed is loud. JOHN: You think? OLIVIA: We can't keep doing this. -
Computer Architecture Techniques for Power-Efficiency
MOCL005-FM MOCL005-FM.cls June 27, 2008 8:35 COMPUTER ARCHITECTURE TECHNIQUES FOR POWER-EFFICIENCY i MOCL005-FM MOCL005-FM.cls June 27, 2008 8:35 ii MOCL005-FM MOCL005-FM.cls June 27, 2008 8:35 iii Synthesis Lectures on Computer Architecture Editor Mark D. Hill, University of Wisconsin, Madison Synthesis Lectures on Computer Architecture publishes 50 to 150 page publications on topics pertaining to the science and art of designing, analyzing, selecting and interconnecting hardware components to create computers that meet functional, performance and cost goals. Computer Architecture Techniques for Power-Efficiency Stefanos Kaxiras and Margaret Martonosi 2008 Chip Mutiprocessor Architecture: Techniques to Improve Throughput and Latency Kunle Olukotun, Lance Hammond, James Laudon 2007 Transactional Memory James R. Larus, Ravi Rajwar 2007 Quantum Computing for Computer Architects Tzvetan S. Metodi, Frederic T. Chong 2006 MOCL005-FM MOCL005-FM.cls June 27, 2008 8:35 Copyright © 2008 by Morgan & Claypool All rights reserved. No part of this publication may be reproduced, stored in a retrieval system, or transmitted in any form or by any means—electronic, mechanical, photocopy, recording, or any other except for brief quotations in printed reviews, without the prior permission of the publisher. Computer Architecture Techniques for Power-Efficiency Stefanos Kaxiras and Margaret Martonosi www.morganclaypool.com ISBN: 9781598292084 paper ISBN: 9781598292091 ebook DOI: 10.2200/S00119ED1V01Y200805CAC004 A Publication in the Morgan & Claypool Publishers -
Understanding the Effects of Compositional Changes in Ion Exchange
Understanding the effects of compositional changes in ion exchange By: Hande Özbayraktar A thesis submitted in partial fulfilment of the requirements for the degree of Doctor of Philosophy The University of Sheffield Faculty of Engineering Department of Materials Science and Engineering APRIL 2021 1 Acknowledgments First and foremost, I gratefully acknowledge the financial support for my doctoral study provided by Mr Erol Güral, Deputy Chairman of Gürok Company. I would like to express my gratitude and sincere thanks to my supervisor, Professor Russel J. Hand for, his kind supervision throughout my research. I could not have completed this thesis without his guidance, support, encouragement and patience. I would also like to express my sincere gratitude to my second supervisor Dr Adrian Leyland for his kind support and encouragement. Special thanks to our wonderful technicians and people at the University of Sheffield, especially Dr Lisa Hollands for glass melting, Neil Hind for helping me out with the heat treatment, Dr Dawn Bussey for her guidance during my indentation runs, Tes Monaghan for micro preparation, Dr Nik Reeves-McLaren for Raman Spectroscopy and XRF. Special thanks to all my great friends for all the good times we had together in Sheffield. I would like to express my gratitude and appreciation to my mum, Sadiye, my dad, Gürbüz and my brother, Eray, for their unconditional love, understanding, constant support and encouragement. I owe special thanks to my beloved husband Semih for his love, continual support, encouragement and patience, especially during difficult times. Last, but of course, not least, I thank my precious daughter, Zeynep who joined us right after I finished my PhD.