CAST-IN-PLACE CONCRETE (Revised 06/02/16) 03 30 00-1 4
Total Page:16
File Type:pdf, Size:1020Kb
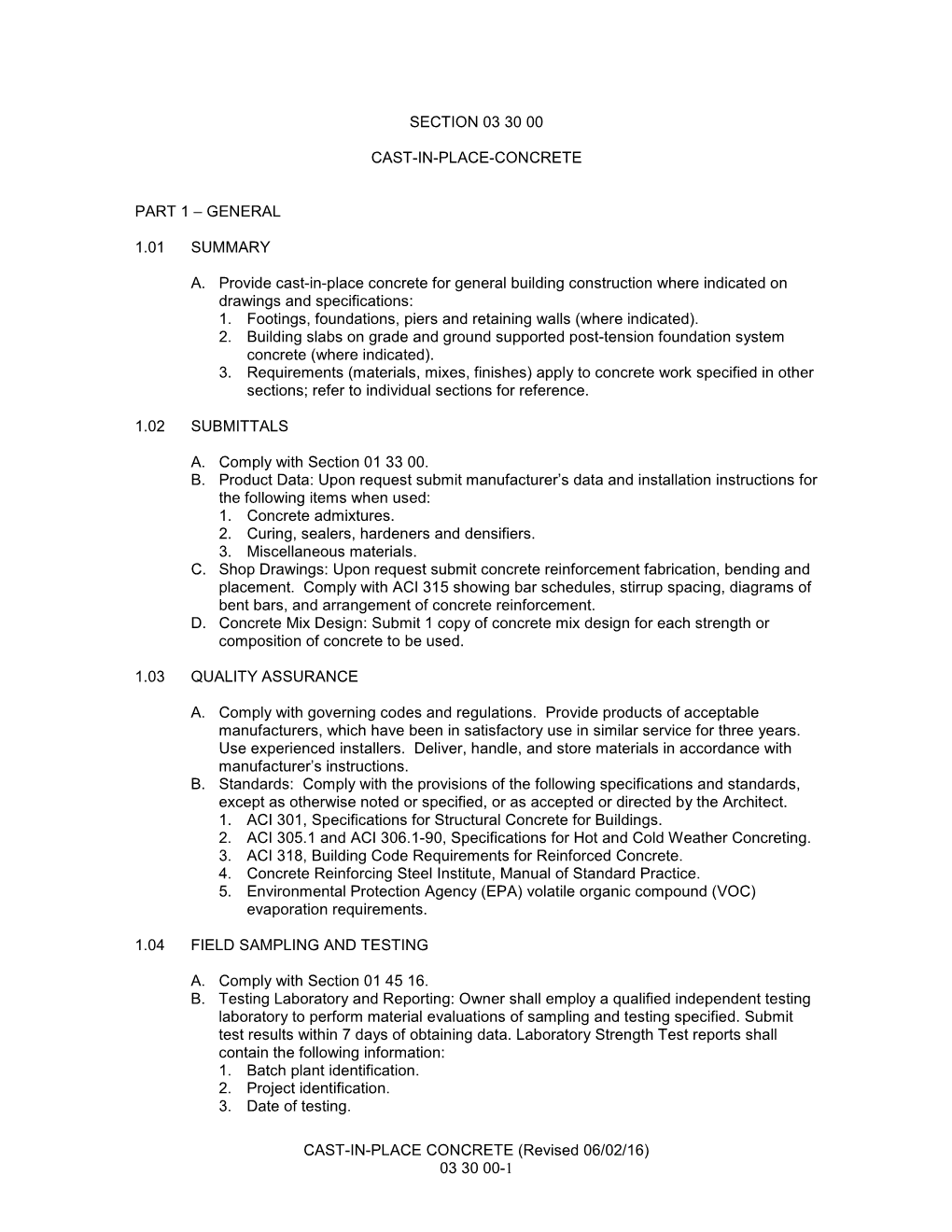
Load more
Recommended publications
-
Best Practice Guidelines for Selecting Concrete Bridge Deck Sealers
BEST PRACTICE GUIDELINES FOR SELECTING CONCRETE BRIDGE DECK SEALERS GENERAL Penetrating sealers are used on highway Portland Cement Concrete bridge decks to reduce the rate of chloride attack on the reinforcing steel corrosion thereby extending service life and reducing life-cycle structure costs of the bridge deck (preventative maintenance). By applying penetrating sealers to existing concrete surfaces, the permeability of the concrete is reduced by up to one order of magnitude. The permeability of the concrete is one of the most important factors which will effect the rate of deterioration of rebar corrosion, alkali-aggregate reaction, carbonation, and the effects of freeze-thaw cycles of which all could occur at the same time. HISTORY Concrete sealing has a long history in Alberta; in the 1960’s boiled linseed oil was used for maintenance of existing bridge curbs. Epoxies and other types of sealers were also tried in the 60’s. The first epoxy-wearing surface in Alberta was in 1963 at Morley. Dehydratine, a black tarry substance, was routinely used on abutments, since the late 1960’s. Epoxy and acrylic sealers were routinely used on standard precast girders starting in the middle of 1970’s. Penetrating Silane sealers were first used in Alberta on concrete bridge decks in 1986. CONCRETE PROPERTIES • Concrete is a conglomerate of sand and rock glued together by cement paste (hydrated cement – cement reacted with water to form calcium silicate chemical bonds). • Concrete is a synergistic material; the whole has greater structural properties -
Project Manual
PROJECT MANUAL OWNER or TENANT O’Reilly Automotive Stores, Inc., A Missouri Corporation (formerly known as O’Reilly Automotive, Inc.) Corporate Offices 233 South Patterson Springfield, MO 65802 417-862-2674 Phone New O’Reilly Auto Parts Store 1101 N. Illinois Street Harrisburg, Arkansas Date: April 26, 2021 ARCHITECT pb2 architecture + engineering 2809 Ajax Avenue, Suite 100 Rogers, Arkansas 72758 Project Number: 2021.0102 DOCUMENT 00 01 05 CERTIFICATION PAGE HARRISBURG, AR TO THE BEST OF MY PROFESSIONAL KNOWLEDGE AND BELIEF, THESE CONTRACT DOCUMENTS HAVE BEEN PREPARED IN ACCORDANCE WITH LOCAL AND STATE CODE REQUIREMENTS. ARCHITECT Scott Joseph Broadbent 2809 Ajax Avenue, Suite 100 Rogers, AR 72758 Architect of Record Date CERTIFICATION PAGE (Revised 09/01/17) 00 01 05-1 MECHANICAL ENGINEER Josh Dale McCall 2809 Ajax Avenue, Suite 100 Rogers, AR 72758 Mechanical Engineer of Record Date CERTIFICATION PAGE (Revised 09/01/17) 00 01 05-1 ELECTRICAL ENGINEER Keith Allen Williams 2809 Ajax Avenue, Suite 100 Rogers, AR 72758 Electrical Engineer of Record Date CERTIFICATION PAGE (Revised 09/01/17) 00 01 05-1 DOCUMENT 00 01 10 TABLE OF CONTENTS HARRISBURG, AR INTRODUCTORY INFORMATION 00 01 01 Project Title Page 00 01 05 Certification Page (Revised 09/01/17) 00 01 10 Table of Contents (Revised 02/21/20) 00 01 15 List of Drawings (Revised 07/10/18) BIDDING REQUIREMENTS, CONTRACT FORMS, AND CONDITIONS OF THE CONTRACT 00 21 00 Instructions to Bidders (Revised 06/26/13) 00 31 00 Information Available to Bidders (Revised 04/25/19) 00 40 00 Bid Form -
Classic Gray a Stylish Terrace at a New Italian Auditorium Secrets of Self-Levelers
2010/11 Decorative Concrete Buyer’s Guide Vol. 10 No. 4 • May/June 2010 • $6.95 ® Classic Gray A stylish terrace at a new Italian auditorium Secrets of Self-Levelers MARCH 15–18, 2011 NASHVILLE www.ConcreteDecorShow.com A Professional Trade Publications Magazine Have You Topp e d Yo u r s e l f Lately? Concrete Decor magazine is seeking submissions for the 2010 Concrete Countertop Design Competition. Submit your favorite projects today! Countertop submissions may be submitted in two categories: Residential and Commercial/Public. Each entry will be evaluated by a panel of experts on the following criteria: - Aesthetic appeal - Functionality - Creativity and originality - Design challenges that were overcome - How well the countertop complements its surroundings Each entry must include a brief explanation of the project, describing the ways in which it meets these criteria. Entries must also include print-quality photos of the finished project. Winners will receive prize packages worth more than $1,000 supplied by our industry- leading sponsors. Note: Only projects completed on or after January 1, 2009, are eligible. Deadline: All entries must be submitted by July 14, 2010. To enter: Access the nomination form at www.concretedecor.net/Forms/ Concrete_Countertop_Contest.cfm Questions? Contact: [email protected] (877) 935-8906 x204 SPONSORED BY Publisher’s Letter Dear Readers, I was talking with one of our advertisers this past week, and we agreed that business is steadily improving. Refl ecting on our days as contractors, May/June 2010 • Volume 10 we also were of the opinion that any contractor who Issue No. 4 • $6.95 wants to be busy will fi nd the work. -
General Product Catalogue
Solutions In Concrete Construction GENERAL PRODUCT CATALOGUE Other Available Catalogues • Concrete Forming Systems • Bridge Deck Forming and Hanging Systems • Precast Concrete Products • Concrete Anchoring Systems • Rock Anchoring and Bolt Systems www.nca.ca Call Us Toll Free: 1-888-777-9272 LOCATIONS Alberta Western Division Calgary Edmonton Red Deer 14760 - 116th Avenue NW 3834 54th Avenue S. E. 14760 - 116th Avenue NW #5, 7803 - 50 Avenue With over 45 years of experience, National Concrete Accessories (NCA), is Canada’s Edmonton, AB T5M3G1 Calgary, AB T2C2K9 Edmonton, AB T5M3G1 Red Deer, AB T4P1M8 leading manufacturer and distributor of concrete accessories. With 14 branches across Tel: (780) 451-1212 Tel: (403) 279-7089 Tel: (780) 451-1212 Tel: (403) 342-0210 Canada, including manufacturing plants in Toronto and Edmonton, we are your one-stop Fax: (780) 455-0827 Fax: (403) 279-4397 Fax: (780) 455-0827 Fax: (403) 341-3245 shop for concrete form hardware, accessories and construction products. Specializing in product variety, quality and superior service, we distribute a complete line of construction British Columbia and restoration products, including tools & equipment, decorative concrete, and building envelope products. NCA works in partnership with premium brands such as, Acrow- Burnaby Kamloops Kelowna Prince George Richmond, DOW, Sika, Makita, W.R. Meadows, Bosch, Mapei, Titebond, UCAN, 7885 Venture Street 855 Laval Crescent 1948 Dayton Street #101- 2050 Robertson Road Husqvarna, Xypex, Butterfield Color, Marshalltown and Chapin to provide you with the Burnaby, BC V5A1V1 Kamloops, BC V2C5P2 Kelowna, BC V1Y7W6 Prince George, BC V2N1X6 Tel: (604) 435-6700 Tel: (250) 374-6295 Tel: (250) 717-1616 Tel: (250) 614-1212 best cost-effective solutions to meet your concrete job requirements. -
Makes It Easy
PROUDLY SUPPORTED BY PROUD MEDIA PARTNER CONCRETE INSTITUTE of AUSTRALIA CONSTRUCTION ENGINEERING AUSTRALIA APRIL 2017 V3.02 ACRS MAKES IT EASY CONSTRUCTION Expert, Independent, CIVIL WORKS Third-Party Steel Certification CIVIL ENGINEERING to Australian and PRINT POST APPROVED - 100001889 New Zealand Standards Keynote Speakers Professor Tim Ibell Professor Karen Scrivener Ms Louise Adams Professor Doug Hooton Mr Peter McBean Professor Des Bull Invited Speakers Mr Mike Schneider Dr Stuart Matthews Conference Registration Now Open Concrete 2017 includes • Quality Technical Program Early Bird Registration pricing • Cement and Durability Workshops will close 26 June 2017 • Huge Trade Exhibition • Gala “Awards for Excellence in Concrete” Dinner • Social and Networking Events 28th Biennial Conference hosted by Conference Partner www.concrete2017.com.au APRIL 2017 contents Volume 3 Number 2 Published by: 2 Editorial Editorial and Publishing Consultants Pty Ltd ABN 85 007 693 138 PO Box 510, Broadford 4 Industry News Victoria 3658 Australia Phone: 1300 EPCGROUP (1300 372 476) Int’l: +61 3 5784 3438 Fax: +61 3 5784 2210 10 Cover Feature: ACRS www.epcgroup.com Publisher and Managing Editor Project Brief: State Library Victoria Anthony T Schmidt 14 8 Phone: 1300 EPCGROUP (1300 372 476) Mobile: 0414 788 900 Email: [email protected] 16 Performance Flooring Deputy Editor Rex Pannell Mobile: 0433 300 106 20 Acoustic Design Email: [email protected] National Advertising Sales Manager 22 Special Report: IFS Servitisation Yuri Mamistvalov Phone: 1300 EPCGROUP -
Sika Annual Report 2011 1 → Content
Online Annual Report 2011 → www.annualreport.sika.com 2011 � Sika Annual Report For Jean Nouvel, a 32000 m² façade clad with 6500 perfectly jointed glass panels. � For Daniel Libeskind, a 1400 m² roof that Freedom of Design Acceleration The precision-designed Sikasil® silicone joints are essential to Sika superplasticizers and shrinkage-reducing admixtures were the glass façade's filigree aesthetic, rigorous color scheme and instrumental in delivering a handsome fair-faced concrete finish environmental control performance. and to keep the tight construction schedule. reads as a fifth façade, sloping at 37° from 90 to 180 meters in height. Turning architects’ visions into reality, drawing on in-depth experience and know-how to translate ideas into buildings and works of art – that is one side to Sika's definition of customer focus. The other is to offer variety, deliver quality and build trust. In all aspects of technology, materials and practical application. Its mission is to create fresh scope for ideas, formal designs and connecting assemblies which, in many cases, are still waiting to be discovered. Sika Annual Report 2011 1 → Content Content Robust Growth Customer Focus 3 Letter to Shareholders 66 Freedom of Design 72 i-Cure Technology Investing in Sika 75 Acceleration 7 Stock price development 9 Risk Management Financial Report 80 Consolidated Financial Statements Strategy & Focus 85 Appendix to the Consolidated 13 Group Strategy Financial Statements 14 The Sika Brand 133 Five-Year Reviews 15 Customers & Markets 140 Sika AG Financial -
Concrete Polishing System 3
EXIT a. Remove existing floor coatings and level floor by grinding with 80-grit metal-bonded diamonds. Depending on the existing flooring conditions. Substitutions: This is a closed specification, no substitutions allowed for system or materials provided by these Multiple passes may be required. vendors. Vendor contact names could possibly change, if so, ask for new contact for Family Dollar account. 2. Apply concrete densifier to deeply saturate floor. CONCRETE POLISHING SYSTEM 3. Floor Closure Polishing: 2.02 EQUIPMENT TO BE USED FOR INSTALLATION a. Remove 80-grit metal-bonded diamond scratches by grinding 100-grit resin-bonded diamonds. Multiple passes may be required. PART 1 GENERAL b. Remove 100-grit resin-bonded diamond scratches by grinding 400-grit resin-bonded diamonds. Multiple passes may be required. A. Floor Grinder: c. Achieve light-reflective finish when viewed from a distance of 30 feet by grinding with 800-grit resin-bonded diamonds. Multiple passes may be 1.01 SUMMARY 1. Model: Concrete Polishing Solutions "G-320". (or equivalent) required. 2. Type: Multi-orbital, planetary-action, opposing-rotational, diamond-headed floor grinder. 4. Perimeter Polishing: A. Work in this section applies to polishing concrete floor surfaces to a desired finish with the incorporation of concrete densifier(s). 3. Weight: 850 pounds. a. Maintain a 6" unfinished perimeter around Sales Floor. When completed with polishing, paint ´ strip semi-glass Low V.O.C. Black by Benjamin 4. Grinding Pressure: 675 pounds. Moore. B. Related Work: 5. Grinding Width: 32 inches. b. 0DLQWDLQDXQILQLVKHGSHULPHWHUDURXQG6DOHV6XSSRUW$UHD)ORRU:KHQFRPSOHWHGZLWKSROLVKLQJSDLQW´VWULSVHPLJODVV/RZ92& 1. Section Cast in Place Concrete 6. -
GENERAL 1.01 DESCRIPTION the WORK of This Section Includes Providing Concrete Formwork, Bracing
SECTION 03100 FORMWORK PART 1 -- GENERAL 1.01 DESCRIPTION The WORK of this Section includes providing concrete formwork, bracing, shoring, supports and formwork requirements for concrete construction. 1.02 RELATED SECTIONS The WORK of the following Sections applies to the WORK of this Section. Other Sections of the Specifications, not referenced below, shall also apply to the extent required for proper performance of the WORK. 1. Section 03200 Concrete Reinforcement 2. Section 03290 Joints in Concrete Structure 3. Section 03300 Cast-in-Place Concrete 4. Section 03600 Grout 1.03 STANDARD SPECIFICATIONS Except as otherwise indicated in this Section of the Specifications, the CONTRACTOR shall comply with the Standard Specifications for Public Works Construction (SSPWC), as specified in Section 01071 Standard References. 1.04 QUALITY ASSURANCE A. REFERENCES: This section contains references to the documents listed below. They are a part of this section as specified and modified. Where a referenced document cites other standards, such standards are included as references under this section as if referenced directly. In the event of conflict between the requirements of this section and those of the listed documents, the requirements of this section shall prevail. Unless otherwise specified, references to documents shall mean the documents in effect at the time of Advertisement for Bids or Invitation to Bid (or on the effective date of the Agreement if there were no Bids). If referenced documents have been discontinued by the issuing organization, references to those documents shall mean the replacement documents FORMWORK DECEMBER 2014 PWS CONTRACT NO. 13-40UTIL 03100-1 issued or otherwise identified by that organization or, if there are no replacement documents, the last version of the document before it was discontinued. -
Determining the Slag Fraction, Water/Binder Ratio and Degree of Hydration in 2 Hardened Cement Pastes 3 4 * 5 M.H.N
Cement & Concrete Research (2014) 56, 171-181 1 Determining the slag fraction, water/binder ratio and degree of hydration in 2 hardened cement pastes 3 4 * 5 M.H.N. Yio , J.C. Phelan, H.S. Wong and N.R. Buenfeld 6 7 8 Concrete Durability Group, Department of Civil and Environmental Engineering, Imperial College London, SW7 2AZ, 9 UK 10 11 12 Abstract 13 14 15 A method for determining the original mix composition of hardened slag-blended cement-based materials based on 16 analysis of backscattered electron images combined with loss on ignition measurements is presented. The method does 17 not require comparison to reference standards or prior knowledge of the composition of the binders used. Therefore, it 18 is well-suited for application to real structures. The method is also able to calculate the degrees of reaction of slag and 19 cement. Results obtained from an experimental study involving sixty samples with a wide range of water/binder (w/b) 20 ratios (0.30 to 0.50), slag/binder ratios (0 to 0.6) and curing ages (3 days to 1 year) show that the method is very 21 promising. The mean absolute errors for the estimated slag, water and cement contents (kg/m3), w/b and s/b ratios were 22 9.1%, 1.5%, 2.5%, 4.7% and 8.7%, respectively. 91% of the estimated w/b ratios were within 0.036 of the actual values. 23 24 25 Keywords: Backscattered electron imaging; Image analysis; Slag; Water-binder ratio; Degree of hydration 26 27 28 29 30 31 32 * Corresponding author. -
Feasibility Study of Functionalized Graphene for Compatibility With
Feasibility study of functionalized graphene for compatibility with cement hydrates and reinforcement steel Master of Science Thesis in the Master’s Program Structural Engineering and Building Technology SOFIA SIDERI Department of Civil and Environmental Engineering Division of Building Technology Building Materials CHALMERS UNIVERSITY OF TECHNOLOGY Gothenburg, Sweden 2014 Master’s Thesis 2014:93 MASTER’S THESIS 2014:93 Feasibility study of functionalized graphene for compatibility with cement hydrates and reinforcement steel Master of Science Thesis in the Master’s Program Structural Engineering and Building Technology SOFIA SIDERI Department of Civil and Environmental Engineering Division of Building Technology Building Materials CHALMERS UNIVERSITY OF TECHNOLOGY Gothenburg, Sweden 2014 Feasibility study of functionalized graphene for compatibility with cement hydrates and reinforcement steel Master of Science Thesis in the Master’s Program SOFIA SIDERI © SOFIA SIDERI, 2014 Examensarbete / Institutionen för bygg- och miljöteknik, Chalmers tekniska högskola 2014:93 Department of Civil and Environmental Engineering Division of Building Technology Building Materials Chalmers University of Technology SE-412 96 Gothenburg Sweden Telephone: + 46 (0)31-772 1000 Cover: Graphene’s structure Department of Civil and Environmental Engineering Gothenburg, Sweden, 2014 Feasibility study of functionalized graphene for compatibility with cement hydrates and reinforcement steel SOFIA SIDERI Department of Civil and Environmental Engineering Division of Building Technology Building Materials Chalmers University of Technology Abstract Cement-based concrete is a widely used material for a great variety of constructions. Although, cement has great properties and high performance, its intrinsic brittleness is a weakness that requires further investigation for improvement. Graphene demonstrates a number of excellent properties, such as high flexibility, 1 TPa Young’s modulus, 130 GPa tensile strength, high electrical and thermal conductivity. -
Formation of Polymer Micro-Agglomerations in Ultralow-Binder-Content Composite Based on Lunar Soil Simulant
Available online at www.sciencedirect.com ScienceDirect Advances in Space Research 61 (2018) 830–836 www.elsevier.com/locate/asr Formation of polymer micro-agglomerations in ultralow-binder-content composite based on lunar soil simulant Tzehan Chen a, Brian J. Chow b, Ying Zhong a, Meng Wang b, Rui Kou b, Yu Qiao a,b,⇑ a Program of Materials Science and Engineering, University of California – San Diego, La Jolla, CA 92093, USA b Department of Structural Engineering, University of California – San Diego, La Jolla, CA 92093-0085, USA Received 9 August 2017; received in revised form 25 October 2017; accepted 27 October 2017 Available online 6 November 2017 Abstract We report results from an experiment on high-pressure compaction of lunar soil simulant (LSS) mixed with 2–5 wt% polymer binder. The LSS grains can be strongly held together, forming an inorganic-organic monolith (IOM) with the flexural strength around 30–40 MPa. The compaction pressure, the number of loadings, the binder content, and the compaction duration are important factors. The LSS-based IOM remains strong from À200 °C to 130 °C, and is quite gas permeable. Ó 2017 COSPAR. Published by Elsevier Ltd. All rights reserved. Keywords: Binder content; Lunar regolith; Structural material; In-situ resource utilization 1. Introduction A major component of lunar soil is silica. While, once heated to above 1200 °C, silica grains can be fused In the next a few decades, building large-scale lunar together, the thermal processing consumes a large amount bases and/or research facilities on the Moon will probably of energy (Taylor and Meek, 2005). -
Section 033000A - Cast-In-Place Concrete (Landside)
IMPERIAL CARGO COMPLEX WATER LINE REPLACEMENT LOS ANGELES INTERNATIONAL AIRPORT SECTION 033000A - CAST-IN-PLACE CONCRETE (LANDSIDE) PART 1 - GENERAL 1.1 RELATED DOCUMENTS A. Drawings and general provisions of the Contract, including General and Supplementary Conditions and Division 01 Specification Sections, apply to this Section. 1.2 SUMMARY A. This Section specifies cast-in place concrete, including formwork, reinforcement, concrete materials, mixture design, placement procedures, and finishes, for the following components located within the LANDSIDE area (publicly accessible) of the project: 1. Pavement and equipment pads 2. Curb, gutter and sidewalk 3. Curb ramps 4. Thrust blocks B. Related Sections include the following: 1. Section 312317 – Unclassified Excavation and Embankment 2. Section 312323 – Structure Excavation and Backfill 3. Section 312333 – Trenching and Backfilling 4. Section 315000 – Excavation Support and Protection 1.3 DEFINITIONS A. Cementitious Materials: Portland cement alone or in combination with one or more of the following: blended hydraulic cement, fly ash and other pozzolans, ground granulated blast-furnace slag, and silica fume; subject to compliance with requirements. 1.4 SUBMITTALS A. General 1. Review of submittals is of a general nature only, and the responsibility for conformance with intent of drawings shall remain with the Contractor. Review does not imply or state that the fabricator has correctly interpreted the construction documents. 2. All submissions shall be in accordance with the submission schedule developed and agreed between the Engineer and Contractor at the commencement of the project. Submission shall include dates of order and delivery of materials to the shop and the site. 3. Shop drawing schedule shall allow adequate time for reviews.