Exhaust Gas Analysis of Compression Ignition Engine Using Copper
Total Page:16
File Type:pdf, Size:1020Kb
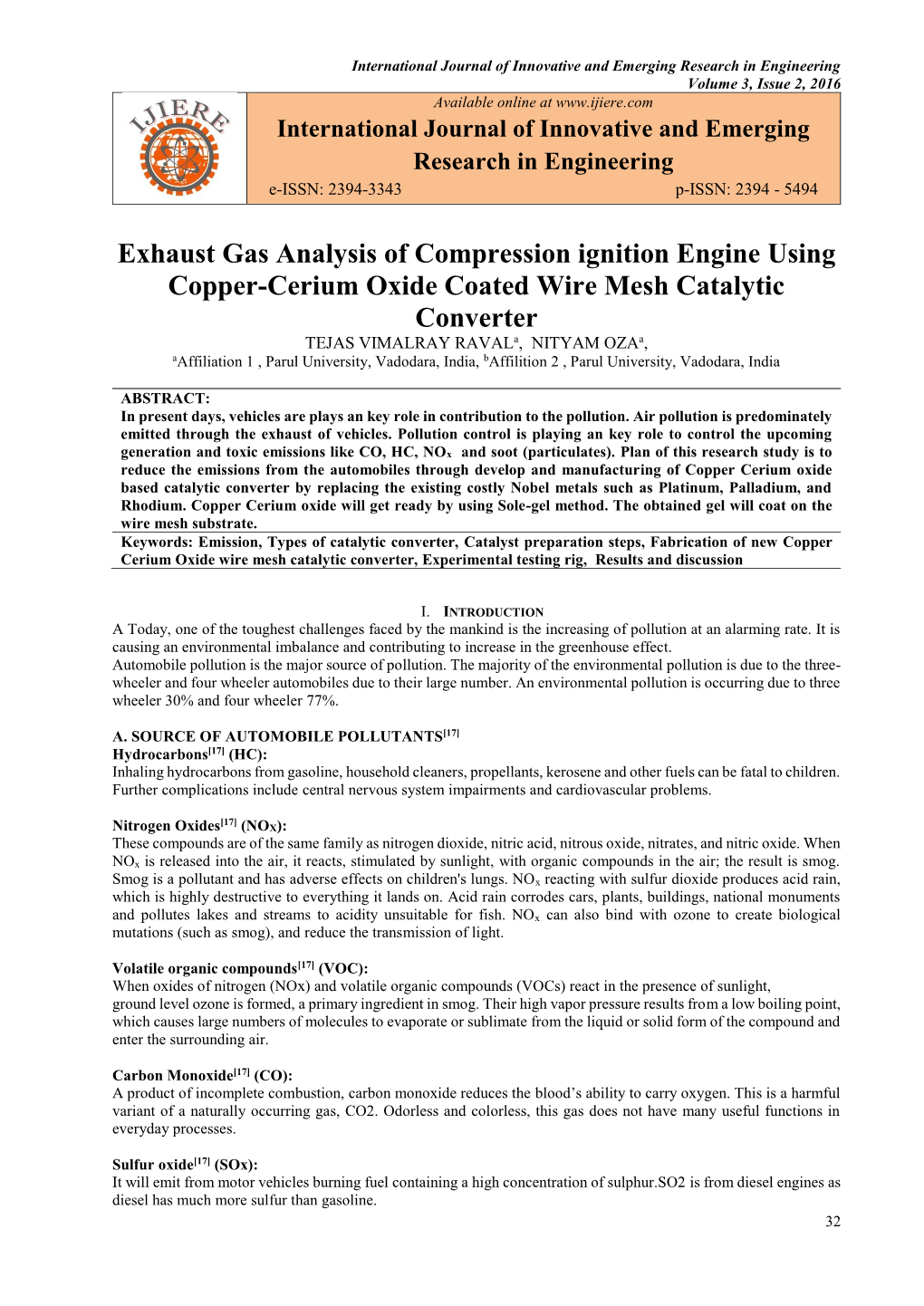
Load more
Recommended publications
-
Lean and Mean India Armed Forces Order New Light-Attack Chopper Developed by HAL
MOBILITY ENGINEERINGTM ENGLISH QUARTERLY Vol : 5 Issue : 1 January - March 2018 Free Distribution Lean and mean India armed forces order new light-attack chopper developed by HAL HCCI Hands-off engines driving is here Overcoming Cadillac’s Super Cruise, the challenges autonomous-vehicle tech overview ME Altair Ad 0318.qxp_Mobility FP 1/5/18 2:58 PM Page 1 CONTENTS Features 33 Advancing toward driverless cars 46 Electrification not a one-size- AUTOMOTIVE AUTONOMY fits-all solution OFF-HIGHWAY Autonomous-driving technology is set to revolutionize the ELECTRIFICATION auto industry. But getting to a true “driverless” future will Efforts in the off-highway industry have been under way be an iterative process based on merging numerous for decades, but electrification technology still faces individual innovations. implementation challenges. 36 Overcoming the challenges of 50 700 miles, hands-free! HCCI combustion AUTOMOTIVE ADAS AUTOMOTIVE PROPULSION GM’s Super Cruise turns Cadillac drivers into passengers in a Homogenous-charge compression ignition (HCCI) holds well-engineered first step toward greater vehicle autonomy. considerable promise to unlock new IC-engine efficiencies. But HCCI’s advantages bring engineering obstacles, particularly emissions control. 40 Simulation for tractor cabin vibroacoustic optimization OFF-HIGHWAY SIMULATION Cover The Indian Army and Air Foce recently ordered more than a 43 Method of identifying and dozen copies of the new Light stopping an electronically Combat Helicopter (LCH) controlled diesel engine in developed -
2 XI November 2014
2 XI November 2014 www.ijraset.com Volume 2 Issue XI, November 2014 ISSN: 2321-9653 International Journal for Research in Applied Science & Engineering Technology (IJRASET) Development of Automobile Catalytic Converter during Last Four Decades --A Review K. Srinivasa Chalapathi1, Dr. Ch.Bhavanarayana Murthy2, Dr. B. Sudheer Prem Kumar3 1Assoc. Prof, 2Professor, 3Professor & Head, Mechanical Engineering Department Anurag group of Institutions (formerly CVSR College of Engineering), JNTUH, Hyderabad Abstract: Awareness regarding atmospheric pollution effects on the environment and the health of humans, plants, animals and other living organisms and flora and fauna World over has inspired many researchers. Extensive research was carried out all over the world with particular reference to Industrial & Vehicular pollution. Automotive catalysts designed to detoxify the exhaust were implemented in USA in the vehicles of the model year 1975. By 2014 about 40 years have been spent all over the world in the research of automotive catalytic converters. The published papers can be categorized into five groups mainly based on (i) Numerical models (ii) Computational Fluid Dynamic models (iii) Design of Catalytic converters per se (iv) Laboratory experimentation (v) Development of catalytic materials. This paper aims at reviewing how the present day catalytic converter used in automobiles has evolved in the last four decades. About 150 technical papers published in various journals were studied. Some 52 papers are described briefly which indicated the furtherance in the said research. Important conclusions drawn from a few papers are discussed in the end. An exhaustive list of 151 references on the subject is appended. I. INTRODUCTION Stringent pollution control over exhaust emissions from automobiles made Automobile industry to develop various means by which the emissions are rid of pollutants like CO, HC and NOx. -
Effect of Cone Angle on Performance of Catalytic Converter Ch.Indira Priyadarsini, Dr.T.Ratna Reddy, Mr.N.Chandra Sekhar, R
Journal of Information and Computational Science ISSN: 1548-7741 Effect of Cone Angle on Performance of Catalytic Converter Ch.Indira Priyadarsini, Dr.T.Ratna Reddy, Mr.N.Chandra Sekhar, R. Hathiram Assistant Professor, Mechanical Engg. Dept., Chaitanya Bharathi Institute of Technology Hyderabad, [email protected] Associate Professor, Mechanical Engg. Dept., Chaitanya Bharathi Institute of Technology Hyderabad, [email protected] ABSTRACT Catalytic converter plays a vital role in reducing harmful gases, but the presence of catalytic converter increases the exhaust back pressure. Catalytic converter is the main pollution control device for modern vehicles in order to reach the ever-increasing legislative demands for low emission standards. in this work a flow analysis is carried out by varying four different Cone angles 45o, 60o. The velocity, pressure and temperature flow in converter has been presented for different configurations. It is observed velocity profile is uniform for 450 cone angle compared to 60 and even back pressure also less with 450 angle for pipe diameter of 0.018m. Keywords— Cone angle, Catalytic converter, CFD, Fluent, Performance I. INTRODUCTION A catalytic converter is a device used to reduce the emissions from an internal combustion engine (used in most modern day automobiles and vehicles). Not enough oxygen is available to oxidize the carbon fuel in these engines completely into carbon dioxide and water; thus toxic by-products are produced. Catalytic converters are used in exhaust systems to provide a site for the oxidation and reduction of toxic by-products (like nitrogen oxides, carbon monoxide, and hydrocarbons) of fuel into less hazardous substances such as carbon dioxide, water vapour, and nitrogen gas. -
Development of Automobile Catalytic Converter During Last Four Decades --A Review K
www.ijraset.com Volume 2 Issue XI, November 2014 ISSN: 2321-9653 International Journal for Research in Applied Science & Engineering Technology (IJRASET) Development of Automobile Catalytic Converter during Last Four Decades --A Review K. Srinivasa Chalapathi1, Dr. Ch.Bhavanarayana Murthy2, Dr. B. Sudheer Prem Kumar3 1Assoc. Prof, 2Professor, 3Professor & Head, Mechanical Engineering Department Anurag group of Institutions (formerly CVSR College of Engineering), JNTUH, Hyderabad Abstract: Awareness regarding atmospheric pollution effects on the environment and the health of humans, plants, animals and other living organisms and flora and fauna World over has inspired many researchers. Extensive research was carried out all over the world with particular reference to Industrial & Vehicular pollution. Automotive catalysts designed to detoxify the exhaust were implemented in USA in the vehicles of the model year 1975. By 2014 about 40 years have been spent all over the world in the research of automotive catalytic converters. The published papers can be categorized into five groups mainly based on (i) Numerical models (ii) Computational Fluid Dynamic models (iii) Design of Catalytic converters per se (iv) Laboratory experimentation (v) Development of catalytic materials. This paper aims at reviewing how the present day catalytic converter used in automobiles has evolved in the last four decades. About 150 technical papers published in various journals were studied. Some 52 papers are described briefly which indicated the furtherance in the said research. Important conclusions drawn from a few papers are discussed in the end. An exhaustive list of 151 references on the subject is appended. I. INTRODUCTION Stringent pollution control over exhaust emissions from automobiles made Automobile industry to develop various means by which the emissions are rid of pollutants like CO, HC and NOx. -
Iqac Report 18-19 (Odd)
NPRcollegeof Engineering &Technology NPR Nagar, Natham, Dindigul - 624401, Tamil Nadu, India Approved by AICTE, New Delhi & Afflhated to Anna University, Chennai. NPR No: 04544- 246 246501, 246502. Neach the Syar Phone 500, Website: www.nprcolleges.org,www.uprcet.org, [email protected] NPRCET/OFF/1QAC /2018-2019 Date: 20.06.2018 QAC Meeting CIRCULAR The Third meeting of Internal Quality Assurance Cell (1QAc) is planned to conduct on 04.07.2018 at 10.30 a.m. in 1QAC Hall. All the 1QAC members are invited to attend the meeting and to contribute in the development of our institution. EERING4 1QAC Chair Person/Principal (Dr.B.Maruthukannan) .NATH PRINCIPAL T100 NPR College of Engineering & Technology Copy to: Natham, Dindigul (Dt}- 624 401 1. Administrative office for information 2. All HoDs 3. Individual members 4. File 5. College Notice Board NPRcollege of Engineering &Technology NPR Nagar, Natham, Dindigul - 624401. Tamil Nadu, India Approved by AICTE, New Delhi& Affiliated to Anna University, Chennai NPR Phone No: 04544- 246 500, 246501, 246502. Rench the Sear Website: www.nprcolleges.org, www.uprcet.og, Emai [email protected] S. No. Agenda 3.01 Alumni interaction with students 3.02 Bridge Coursefor Freshers 3.03 Career Guidance Program 3.04 Elective Subject Finalisation 3.05 Energyconservation 3.06 Entrepreneurship Development Cell activities 3.07 Establishment of NPTEL Local chapter 3.08 Extension activities 3.09 FDP 3.10 Fundsfor research Projects 3.11 HR Connect and association activities 3.12 In -plant -
Manufacturing Elements Affecting the Performance & Durability
ISSN(Online) : 2319-8753 ISSN (Print) : 2347-6710 International Journal of Innovative Research in Science, Engineering and Technology (An ISO 3297: 2007 Certified Organization) Vol. 5, Issue 9, September 2016 Manufacturing Elements affecting the Performance & Durability Characteristics of Catalytic Converter Mylaudy Dr.S.Rajadurai1, R.Somasundaram2, P.Madhusudhanan2, Alrin M Victor2, J.Y. Raja Shangaravel3 Head R&D, Sharda Motor Industries Ltd., Chennai, Tamil Nadu, India1 Assistant Manager R&D, Sharda Motor Industries Ltd., Chennai, Tamil Nadu, India2 Senior Engineer R&D, Sharda Motor Industries Ltd., Chennai, Tamil Nadu, India3 ABSTRACT: Manufacturing elements that are affecting design parameters, the performance and durability of exhaust catalytic converter was analyzed. Catalytic converters with different outlet pipe insertion lengths were designed and adopted for virtual analysis. Prediction from Computational Fluid Dynamics(CFD) modeling shows insertion length of outlet pipe is inversely proportional to UI &ΔP characteristics. However, required minimum insertion length need to maintain to achieve optimum FOS for the system. According to American Weld Standard(AWS) the minimum overlap of parts in stress carrying lap joints overlap length for lap joint for fillet weld should be five times of its thickness. In this paper what happens when the performance and durability of catalytic converter varies with increase in overlap length of the outlet cone. These prediction of performance data's were verified using bench tests. The paper will discuss in detail the experimental procedures, data acquisition and data handling that were followed. KEYWORDS: Pressure drop, Uniformity index, Durability, CFD, FEA, Cold flow bench. I. INTRODUCTION In an automobile exhaust system catalytic converter and muffler are important components to reduce emission. -
Fr. Principal's Message
Fr. Principal’s Message I am very happy to meet you through this page. Loyola College has stood above the rest in its approach to education and in its pedagogies. The ways we teach and the ways our students learn are unique and creative. Consistently, we never hesitated to look into our deficiencies and transform us to an efficient agent of social change. Many critics would confirm that the College has substantially contributed to the process of National Development by providing quality education and thereby enabling the students to become globally competent. We have plans and dreams in the years to come. We propose to introduce Aademic Audit for every department by external experts. This aims at regular scrutiny of the quality of teaching and the content of teaching. This will certainly go a long way in enhancing quality in education in accordance with the objectives of the institution and in serving society at large with sensitivity and commitment. We envisage, in the coming years, an interdisciplinary research in science and social sciences. The college as an autonomous institution for 30 years has achieved many feats and climbed new heights. Award of the College with Potential for Excellence in 2004 and NAAC’s accreditation at A+ level in 2006 and were some of them. Sooner or later we hope to be honoured by the UGC as a Degree Awarding College. Education is not an act of acquiring knowledge but learning a skill to lead life and forming one’s personality. This is an ennobling process of growth. I can boldly say that we have excelled in every initiative that we undertook and we have stood together in facing the challenges in realizing quality education. -
Experimental Investigation of Emission Control Using Ag Catalytic Converter in a Four Stoke Diesel Engine
International Journal of Mechanical Engineering and Technology (IJMET) Volume 9, Issue 13, December 2018, pp. 192–202, Article ID: IJMET_09_13_020 Available online at http://iaeme.com/Home/issue/IJMET?Volume=9&Issue=13 ISSN Print: 0976-6340 and ISSN Online: 0976-6359 © IAEME Publication Scopus Indexed EXPERIMENTAL INVESTIGATION OF EMISSION CONTROL USING AG CATALYTIC CONVERTER IN A FOUR STOKE DIESEL ENGINE A. Dhanalakshmi and M.Suresh Faculty, Department of Mechanical Engineering, Sri Sairam Engineering College, West Tambaram, Chennai-600 044, India ABSTRACT Catalytic converters play a major role in automobiles which reduce the harmful gasses from engine exhaust significantly. The three way catalysts (TWCs) are widely used in automobiles for the past 25 years and are more successful (20). The aim of our work is to reduce the harmful gasses, by replacing conventionally used noble materials by comparatively cheaper and economically viable Silver (Ag). CATIA V5R15 software is used to create geometric model of our catalytic converter. To oxidise HC and CO, at a higher rate atmospheric air is injected inside the catalytic converter at constant pressure. The presence of oxygen in the exhaust gas helps to increase the oxidation process (13). This work is aimed to reduce harmful gases from diesel engine exhaust. Key Words: Diesel Engine, catalytic Convertor, Emission Cite this Article: A. Dhanalakshmi and M.Suresh, Experimental Investigation of Emission Control Using Ag Catalytic Converter in a Four Stoke Diesel Engine, International Journal of Mechanical Engineering and Technology, 9(13), 2018, pp. 192–202 http://iaeme.com/Home/issue/IJMET?Volume=9&Issue=13 1. INTRODUCTION Automotive catalyst technology to meet ultra-low emission vehicle (ULEV) emission levels for conventional diesel engine vehicles requires major improvements in catalytic activity and reactor engineering(6). -
2009-10, Your Company Delivered Yet Another Sterling Performance N
Sharda Motor Industries Ltd. BOARD OF DIRECTORS N. D. RELAN CHAIRMAN AJAY RELAN Managing Director SHARDA RELAN Director ROHIT RELAN Director R. P. CHOWDHRY Director G. L. TANDON Director O. P. KHAITAN Director KISHAN N. PARIKH Director UDAYAN BANERJEE Executive Director PROF. ASHOK KUMAR BHATTACHARYA Director PRESIDENT (LEGAL) & CFO PRADEEP RASTOGI SR. VICE PRESIDENT (F&A) D. A. AGGARWAL COMPANY SECRETARY NITIN VISHNOI AUDITORS M/S. S. R. DINODIA & CO. CHARTERED ACCOUNTANTS NEW DELHI BANKERS YES BANK CANARA BANK ICICI BANK STATE BANK OF INDIA CITI BANK HDFC BANK ABN AMRO BANK REGISTERED OFFICE D-188, OKHLA INDUSTRIAL AREA, PHASE - I, NEW DELHI - 110 020 CONTENTS Message from Chairman 2 Message from Managing Director 3 Notice 4 Directors' Report 8 Report on Corporate Governance 14 Management Discussion & Analysis Report 24 Auditor's Report 26 Balance Sheet 29 Profit & Loss Account 30 Cash flow Statement 31 Schedules to Accounts 32 Balance Sheet Abstract 53 Statement under Section 212 54 Consolidated Financial Statements 55 Subsidiary Company's Financial Results 76 1 Sharda Motor Industries Ltd. Message From Chairman Dear Shareholders, Warm greetings to you all ! Following the global economic turmoil in 2008, last year was a year of stability and significant restoration of confidence in global markets. In 2009-10, your Company delivered yet another sterling performance N. D. Relan across several financial and operating Chairman indicators. Strategic investments, robust business plans, sound management The strength and rapidity of India's recovery practices that adapted rapidly to the reiterates the overall potential for sustained changing environment under the guidance high economic growth in India. -
Nprollege of Enginering & Technology
NPRollege of Enginering &Technology NPR Nagar, Natham, Dindigul 624401, Tamil Nadu, India. Approved by AICTE, New Delhi & Affihated to Anna University, Chennai. NPR Phone No: 04544- 246 500, 246501, 246502. Rrach the Nar Website: www.nprcolleges.ong, www.nprcet.org, Email [email protected] NPRCET/OFF/IQAC /2018- 2019 Date: 23.01.2019 Internal Quality Assurance Cell Meeting CIRCULAR It is planned to conduct 4th meeting of Internal Quality Assurance Cell in our institution on 06.02.2019 at 10. 00 a.m. in Rear block, II floor Seminar Hall, along with its executive members. All the lQAC members mentioned below are hereby instructed to attend the meeting without fail. TBCHNOUG Chair Person/Principal (Dr.B.Maruthukannan) PRINCIPAL NPR Coliege of Engineering &Technoiogy Copy to: Natham, Dindigul (Dt)- 624 401 1. Administrative office for information 2. All HoDDs 3. Individual members 4. File 5. College Notice Board NPRColege of Enginering& Technology Natham, Dindigul 624401, Tamil Nadu, India NPR Nagar, Chennai Approved by AICTE, New Delhi & Affilhated to Anna University, NPR Phone No: 04544- 246 500, 246501, 246502. Reuch the ar W'ebsite www.nprcolleges org,www.nprcet org. Email uprcetprincipal@uprcolleges org 5. No. Agenda 4.01 Alumni interaction with students 4.02 Career guidance programme 4.03 Conference 4.04 Elective Subject Finalisation 4.05 Entrepreneurship Development Cell activities 4.06 ERP software 4.07 Extension activities 4.08 FDP 4.09 Industrial Visit, In-plant training and Internship 4.10 NAAC Accreditation 4.11 Innovative -
Benchmarking - the First Step for Frugal Engineering S
IJISET - International Journal of Innovative Science, Engineering & Technology, Vol. 1 Issue 6, August 2014. www.ijiset.com ISSN 2348 – 7968 Benchmarking - The First Step for Frugal Engineering S. Rajadurai1, C. Parameshwari2 1Head-R&D, Sharda Motors Industries Ltd, Mahindra City, New Chennai 2Project Executive-R&D, Sharda Motors Industries Ltd, Mahindra City, New Chennai Abstract product engineering. It is a method which helps to compare In this article, we have defined a systematic benchmarking various processes or product to improve performance and process, the first step to perform Frugal Engineering, the science value. Benchmarking is a positive, pro-active process to of breaking up complex engineering process into the basic understand a product in a structured fashion to achieve components and then re-building each component in the most superior performance [3, 4]. Benchmarking is not an end- economical manner to achieve a simpler, more robust and easier to handle final product. The meaning of benchmarking is clearly all process. It is the beginning of change. Just defined and distinguished from competitive and comparative benchmarking financial results alone will not help to analysis and value targeted product proposal. Types of complete the task. Before beginning benchmarking benchmarking, system selection process and the sequential steps process, we must understand the goals and objectives. Risk of benchmarking are clearly discussed. Benchmarking process is analysis should be performed along wih the mission and a pre-requisite for Value Analysis and Value Engineering goals. Risk management vary from entity to entity. (VA/VE). An example of an automotive exhaust system muffler Benchmark must relate to risk management goals. -
Sharda Motors Annual Report 2012-13.Indd
Sharda Motor Industries Ltd. BOARD OF DIRECTORS KISHAN N. PARIKH Chairman N. D. RELAN Co-Chairman AJAY RELAN Managing Director SHARDA RELAN Director ROHIT RELAN Director R. P. CHOWDHRY Director O. P. KHAITAN Director UDAYAN BANERJEE Executive - Director Prof. ASHOK KUMAR BHATTACHARYA Director PRESIDENT (LEGAL) & CFO PRADEEP RASTOGI Sr. VICE PRESIDENT (F&A) D. A. AGGARWAL COMPANY SECRETARY NITIN VISHNOI STATUTORY AUDITORS M/S. S. R. DINODIA & CO. CHARTERED ACCOUNTANTS NEW DELHI COST AUDITORS M/S GURDEEP SINGH & ASSOCIATES COST ACCOUNTANTS NEW DELHI BANKERS YES BANK LIMITED ICICI BANK STATE BANK OF INDIA PUNJAB NATIONAL BANK CITI BANK HDFC BANK CANARA BANK REGISTERED OFFICE D-188, OKHLA INDUSTRIAL AREA, PHASE - I, NEW DELHI - 110 020 CONTENTS Message of Co-Chairman 2 Message of Managing Director 3 Notice 4 Directors’ Report 9 Report on Corporate Governance 15 Management Discussion & Analysis Report 25 Auditor’s Report 29 Balance Sheet 32 Statement of Profit & Loss Account 33 Cash flow Statement 34 Notes to Financial Statments 35 Balance Sheet Abstract 56 1 Sharda Motor Industries Ltd. Co-Chairman’s Message Dear Shareholders N. D. Relan Warm Greeting to all of you The fiscal year has been a very challenging year I believe that a team of inspired employees is the for the Company. Despite global and domestic key for achieving greater heights in excellence by challenges of High interest rates, inflation, any organization and for that reason the Company weakening of the rupee, volatility in the cost of gives utmost importance to its Human Resource raw materials , prices of crude oil, uncertainty in Development.