Gas-To-Liquids Conversion
Total Page:16
File Type:pdf, Size:1020Kb
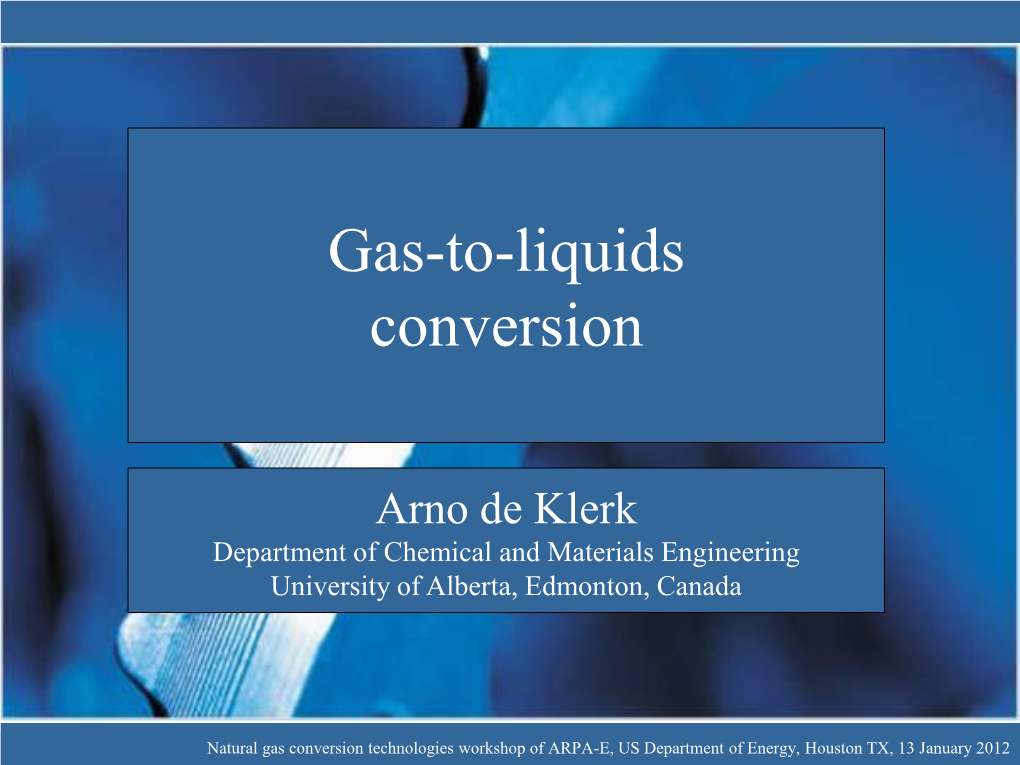
Load more
Recommended publications
-
Techno-Economic Analysis of Synthetic Fuels Pathways Integrated with Light Water Reactors
INL/EXT-20-59775 Revision 0 Light Water Reactor Sustainability Program Techno-Economic Analysis of Synthetic Fuels Pathways Integrated with Light Water Reactors September 2020 U.S. Department of Energy Office of Nuclear Energy DISCLAIMER This information was prepared as an account of work sponsored by an agency of the U.S. Government. Neither the U.S. Government nor any agency thereof, nor any of their employees, makes any warranty, expressed or implied, or assumes any legal liability or responsibility for the accuracy, completeness, or usefulness, of any information, apparatus, product, or process disclosed, or represents that its use would not infringe privately owned rights. References herein to any specific commercial product, process, or service by trade name, trade mark, manufacturer, or otherwise, does not necessarily constitute or imply its endorsement, recommendation, or favoring by the U.S. Government or any agency thereof. The views and opinions of authors expressed herein do not necessarily state or reflect those of the U.S. Government or any agency thereof. INL/EXT-20-59775 Revision 0 Techno-Economic Analysis of Synthetic Fuels Pathways Integrated with Light Water Reactors L. Todd Knighton, Daniel S. Wendt (INL) Lesley Snowden-Swan, Jeromy Jenks, Shuyun Li, Steven Phillips, and Jalal Askander (PNNL) September 2020 Prepared for the U.S. Department of Energy Office of Nuclear Energy Page intentionally left blank EXECUTIVE SUMMARY Synthetic fuels (synfuels) and chemicals (synchems) are produced by synthesis from chemical building blocks rather than by conventional petroleum refining. Synthesis gas or syngas (carbon monoxide and hydrogen) is a common intermediate building block in the production of synfuels and synchems. -
Comparative Evaluation of Semi-Synthetic Jet Fuels
COMPARATIVE EVALUATION OF SEMI-SYNTHETIC JET FUELS FINAL REPORT Prepared for Coordinating Research Council, Inc. 3650 Mansell Road, Suite 140 Alpharetta, GA 30022 Universal Technology Corporation 1270 North Fairfield Road Dayton, OH 4432 Prepared by Clifford A. Moses Consultant New Braunfels, Texas CRC Project No. AV-2-04a Funded by U.S. Air Force Research Laboratories Contract F33415-02-D-2299 through Universal Technology Corporation September 2008 This page intentionally left blank for back-to-back printing COMPARATIVE EVALUATION OF SEMISYNTHETIC JET FUELS EXECUTIVE SUMMARY This report compares the properties and characteristics of five blends of individual synthetic paraffinic kerosenes with petroleum-based Jet A, Jet A-1 or JP-8 fuel to make semi-synthetic jet fuels (SSJF). The study was requested by the aviation fuel community to provide technical support for the acceptance of synthetic paraffinic kerosenes (SPK) derived from synthesis gas as blending streams up to 50%(v) in fuel specifications for aviation turbine fuel. The methodology for comparison was to be the properties and characteristics used in the original evaluation of the Sasol semi-synthetic jet fuel (SSJF) which has experienced 9 years of successful service since it was approved for use as commercial jet fuel by DEF STAN 91-91 in 1998. The SPK used by Sasol in the original SSJF was produced by a Fischer-Tropsch (F-T) process using synthesis gas derived from coal. The synthesis gases for the four new candidates were produced from natural gas. The details of the F-T process conditions and the downstream processing differed among the five SPK fuels. -
Secure Fuels from Domestic Resources ______Profiles of Companies Engaged in Domestic Oil Shale and Tar Sands Resource and Technology Development
5th Edition Secure Fuels from Domestic Resources ______________________________________________________________________________ Profiles of Companies Engaged in Domestic Oil Shale and Tar Sands Resource and Technology Development Prepared by INTEK, Inc. For the U.S. Department of Energy • Office of Petroleum Reserves Naval Petroleum and Oil Shale Reserves Fifth Edition: September 2011 Note to Readers Regarding the Revised Edition (September 2011) This report was originally prepared for the U.S. Department of Energy in June 2007. The report and its contents have since been revised and updated to reflect changes and progress that have occurred in the domestic oil shale and tar sands industries since the first release and to include profiles of additional companies engaged in oil shale and tar sands resource and technology development. Each of the companies profiled in the original report has been extended the opportunity to update its profile to reflect progress, current activities and future plans. Acknowledgements This report was prepared by INTEK, Inc. for the U.S. Department of Energy, Office of Petroleum Reserves, Naval Petroleum and Oil Shale Reserves (DOE/NPOSR) as a part of the AOC Petroleum Support Services, LLC (AOC- PSS) Contract Number DE-FE0000175 (Task 30). Mr. Khosrow Biglarbigi of INTEK, Inc. served as the Project Manager. AOC-PSS and INTEK, Inc. wish to acknowledge the efforts of representatives of the companies that provided information, drafted revised or reviewed company profiles, or addressed technical issues associated with their companies, technologies, and project efforts. Special recognition is also due to those who directly performed the work on this report. Mr. Peter M. Crawford, Director at INTEK, Inc., served as the principal author of the report. -
Verification of Shell GTL Fuel As CARB Alternative Diesel
Verification of Shell GTL Fuel as CARB Alternative Diesel Ralph A. Cherrillo, Mary Ann Dahlstrom, Anne T. Coleman – Shell Global Solutions (US) Inc. Richard H. Clark – Shell Global Solutions (UK) COPYRIGHT @ 2007 Shell Global Solutions (US) Inc. Outline • Introduction Future Fuel Demand GTL as a Future Fuel • GTL Demonstrations CARB Verification Testing Fleet Tests • GTL Outlook 2 Future Fuel Demand A Forecast of Global Automotive Fuel Demand Energy Demand (x1018 J ) ¾Significant uncertainty in Hydrogen Gaseous plateau of ‘conventional Fuels oil mountain’ 300 Gas Electricity 250 ¾Increased environmental pressures 200 Synthetic fuel and biofuels ¾Plethora of potential 150 Liquid vehicle-fuel solutions Fuels 100 Diesel / Gasoline ¾Common denominator ought to be cost 50 Heavy Oil effectiveness. 2000 2020 2040 2060 2080 2100 (Source: a WEC scenario) 3 GTL Fuel –Synthetic and Alternative Fuel GTL Fuel is one class of Synthetic fuels, which refers to liquids from: gas (GTL) coal (CTL) biomass (BTL) waste (WTL) Alternative Fuels comprise synthetic fuels, biofuels, and fuels such as water-fuel emulsions, ethanol-diesel blends 4 What is Gas to Liquids? GTL is a process that converts natural gas to clean fuels and high quality products via the Fischer-Tropsch process CO + 2H2 –(CH2)n – Natural Syngas Syngas Synthesis Hydrocracking • LPG Manufacture Synthesis Hydrocracking Gas Manufacture • Condensate CH4 • Naphtha • Gasoil • Base oils • Chemicals O H2O O22 Shell’s proprietary process: Shell Middle Distillate Synthesis (SMDS) 5 Why -- Shell GTL Fuel ¾ Strategic diversification of energy supply ¾ Compatible with existing infrastructure ¾ GTL provides a bridge to Biomass to Liquids and Coal to Liquids technologies ¾ Life cycle analysis: GTL vs. -
Oil Shale Tracing Federal Support for Oil Shale Development in the U.S
SUBSIDIZING OIL SHALE TRACING FEDERAL SUPPORT FOR OIL SHALE DEVELOPMENT IN THE U.S. www.taxpayer.net OIL SHALE SPECIMEN. Image Courtesy of United States Geological Survey OIL SHALE SPECIMEN. Image Courtesy of United States Geological Survey lthough the oil shale industry is still in reserves were created to ensure a military oil supply. its commercial infancy, it has a long his- In response, the Bureau of Mines program began A tory of government support that continues research into exploiting oil shale technology and in today. The Bureau of Land Management recently the 1960s private industry followed. But significant issued two new research, development and demon- action was limited until the 1970s, when in response stration leases and new federal regulations for com- to the gas shortages Congress intervened in oil shale mercial leases and royalty rates are expected any day. development, in hopes of creating a domestic fuel Before the federal government goes down that road alternative. Their unsuccessful attempt to spur large- it’s important to take a look back and ask whether we scale commercial development of oil shale and other should be throwing good money after bad. unconventional fossil fuels became a notorious waste Oil shale, or kerogen shale, is a sedimentary rock of federal funds. that contains liquid hydrocarbons that are released Since then federal support has continued in vari- when heated. Considered an oil precursor, kerogen ous forms. Although not a key part of the overall is fossil organic matter that has not had exposure energy policy agenda, federal subsidies continue to to high enough temperatures or been in the ground appear in legislation and administrative actions. -
Alternative Fuel Policy
The City of Ypsilanti Alternative Fuel Policy Prepared by John Sherwood Mechanic Department of Public Services ALTERNATIVE FUEL POLICY EXECUTIVE SUMMARY The City of Ypsilanti seeks to be at the forefront of the implementation of alternative fuel technology. The City’s goal is to increase the usage of alternative fuel vehicles (AFVs) each year as technology allows while monitoring each new technological advancement to suit the application and departmental needs. Currently, the capital costs for AFVs are greater than conventional vehicles. In addition, some alternative fuels are also more expensive than conventional unleaded or diesel fuels. It is recommended that the City purchase three types of Alternative Fuel Vehicles (AFV) (1) Compressed Natural Gas (CNG) vehicles, (2) Flex Fuel vehicles, and (3) Hybrid vehicles. If the City actively pursues these AFV options, an expanded alternative fuel infrastructure must be developed either as a city-owned facility or in partnership with other agencies in Washtenaw County. Capital improvements needed for the alternative fuel infrastructure will be costly. Although the City is not mandated by federal or state regulations to purchase alternative fuel vehicles (AFVs) or use alternative fuels, considerable efforts have been made since 1999 to analyze available alternative fuel vehicle options for City use. The City has made vehicle and equipment purchasing decisions based upon operational issues, fiscal concerns and responsible environmental stewardship. When selecting AFVs, consideration is given to the end user application and their operational functions since the size and location of fuel tanks impact the storage, functionality and useful bed space of the vehicles. Other issues include availability of fuel supply, ability to refuel without long delays, driving range between fuel stops, vehicle usage by on-call staff including responding to emergency or disaster situations and the availability of original equipment manufacturer (OEM) vehicles. -
Summary of Current Status of Alternative Fuels and Vehicles
1. INTRODUCTION Motor vehicles are the underlying source for two major global issues the United States (U.S.) faces: 1) the dependence on foreign oil from unstable political regions, and 2) the increase in carbon dioxide (CO2) emissions, a leading contributor of greenhouse gases (GHGs) that affect Earth’s climate. There are 200 million drivers traveling 10 trillion vehicle miles each year in the U.S. In the Denver region alone, vehicles are driven more than 70 million miles each day. Dependence on foreign oil: A matter of U.S. Security The U.S. uses about 14.5 million barrels of oil per day for transportation (which equates to 609 million gallons) and imports more than 60% of its petroleum, two-thirds of which is used to fuel vehicles in the form of gasoline and diesel. The demand for petroleum imports is increasing and with much of the worldwide petroleum resources located in politically volatile countries, the U.S. is vulnerable to supply disruptions. Climate Change While the U.S. contains only 5% of the world’s population, it is responsible for 25% of global GHG emissions. Transportation accounts for 28% of GHG emissions in the U.S., second to electric power Figure 1 (Figure 1). It is the 2006 U.S. Greenhouse Gas Emissions fastest growing by sector (Million Metric Tons CO2 Equivalent) source of GHGs, Residential accounting for 47% of Commericial 5% the net increase in 6% total U.S. GHG Agriculture emissions since 1990. 8% Trends in Colorado are similar, with Electric Power electric power being 34% the lead source of Industry 19% CO2 emissions at 42%, followed by transportation at 31% Transportation (Figure 2). -
The Role of E-Fuels in the Transport System in Europe (2030–2050) (Literature Review)
A look into the role of e-fuels in the transport system in Europe (2030–2050) (literature review) Introduction As part of Concawe’s Low Carbon Pathways project, this In December 2015, Parties to the United Nations Framework Convention on Climate Change convened article presents a literature in Paris for the 21st Conference of Parties (COP21). The conference was an important step towards review on e-fuels, which aims to addressing the risks posed by climate change through an agreement to keep the global temperature build a better understanding of increase ‘well below 2°C above pre-industrial levels’ and drive efforts to limit it to 1.5°C above pre- e-fuel production technologies industrial levels. To achieve these goals, the European Union (EU) is exploring different mid-century and implications in terms of scenarios leading to a low-carbon EU economy by 2050. efficiency, greenhouse gas reduction, technology readiness level, environmental impact, In line with the EU’s low-emissions strategy, Concawe’s cross-sectoral Low Carbon Pathways (LCP) investment, costs and potential programme is exploring opportunities and challenges presented by different low-carbon technologies to demand. It is a summary of the achieve a significant reduction in carbon dioxide (CO2) emissions associated with both the manufacture exhaustive literature review and use of refined products in Europe over the medium (2030) and longer term (2050). which is due to be published by the end of 2019. In the scenarios considered by the Commission (P2X, COMBO, 1.5 TECH and 1.5 LIFE) e-fuels are presented as a potential cost-effective technology that could be used to achieve the objectives of the Paris Agreement, i.e. -
Mini-Gtl Technology Bulletin
MINI-GTL TECHNOLOGY BULLETIN Volume 4, January 2018 INTRODUCTION This bulletin represents a 2017 year-end review of technology and commercial developments in the emerging small-scale GTL industry. There have been comings and goings and the field is consolidating. A key highlight is the first application of a micro-GTL plant to a flare in North Dakota by GasTechno. STATE OF THE MINI-GTL INDUSTRY Only one of the 5 commercial plants currently under development came on line in 2017, namely the ENVIA Energy’s GTL plant on the Waste Management landfill in Oklahoma. The plant, partially fed with landfill gas, announced its first finished, saleable products on June 30, but has not yet reached the 250 bpd design capacity. However, they are close: on October 30, they announced achieving 200 bpd production. Unfortunately, Velocys, the technology leader and partner in the project has announced that they will focus on renewable feedstocks only, taking them out of the gas flare monetization business for the time being. The start-up of the other 4 plants (Greyrock 1, Juniper GTL, Primus 1 and Primus 2) will now happen in 2018. The new owner of Juniper GTL, York Capital, will likely target future plant sizes of more than 5000 bpd (consuming 50 MMscfd of gas), clearly outside the gas flare range. However, both Greyrock and Primus GE continue strong business development efforts in the gas flare arena. Haldor Topsoe has joined forces with Modular Plant Solutions (MPS) and has designed and engineered a small-scale methanol plant called “Methanol-To-GoTM”. The size of the plant is similar to the Primus 1 and 2 plants with a gas feed rate of 7 MMscfd versus 5 MMscfd for the Primus GE plants. -
CO2-Based Synthetic Fuel: Assessment of Potential European Capacity and Environmental Performance
CO2-Based Synthetic Fuel: Assessment of Potential European Capacity and Environmental Performance Authors: Adam Christensen, Ph.D. Chelsea Petrenko, Ph.D. Copyright c 2017 This research was funded by European Climate Foundation and the International Council on Clean Trans- portation Final release, November 14, 2017 ii Contents 1 Executive Summary1 2 CO2-based synthetic fuels: Introduction6 2.1 Study Objectives........................................7 2.2 Scenarios............................................8 3 Economic Evaluation9 3.1 Basic Operation.........................................9 3.2 Methodology.......................................... 10 3.3 Literature Review........................................ 10 3.4 Financial Model......................................... 12 3.4.1 Fundamental Economic Parameters.......................... 12 3.4.2 Capital Costs...................................... 12 3.4.3 Feedstock Prices.................................... 14 Electricity........................................ 14 CO2 ........................................... 15 3.4.4 Exogenous Market Prices............................... 15 Diesel Fuel....................................... 15 3.4.5 Deployment....................................... 16 3.5 Results.............................................. 16 3.5.1 Policy Scenario 1.................................... 17 3.5.2 Policy Scenario 2.................................... 17 3.5.3 Policy Scenario 3.................................... 19 3.5.4 Policy Scenario 4................................... -
Fisher–Tropsh Synthesis Technology Evolution - Anna Matuszewska Et Al
IOP Conference Series: Materials Science and Engineering PAPER • OPEN ACCESS Recent citations Fisher–Tropsh synthesis technology evolution - Anna Matuszewska et al To cite this article: N I Loseva et al 2019 IOP Conf. Ser.: Mater. Sci. Eng. 663 012067 View the article online for updates and enhancements. This content was downloaded from IP address 170.106.40.40 on 25/09/2021 at 21:27 ETSaP 2019 IOP Publishing IOP Conf. Series: Materials Science and Engineering 663 (2019) 012067 doi:10.1088/1757-899X/663/1/012067 Fisher–Tropsh synthesis technology evolution N I Loseva, I I Niyazbakiev and A V Silman Tyumen Industrial University, 38, Volodarsky St., Tyumen, 625000, Russia E-mail: [email protected] Abstract. the article considers the development stages of technologies for producing hydrocarbons based on syngas. XTL technology is based on the Fischer–Tropsch process. Carbon-containing substances in any aggregate state can be used as a raw material of XTL technology, which will affect the chemistry and process parameters. Currently, interest in these technologies has increased in connection with the advent of scientific and technological innovations. The latest generation of XTL technology has already entered the industrial production phase. The article presents the results of a comparative analysis of XTL technology of different generations, the main indicators of which were the state of raw materials, the type of reactor devices, the chemical composition of the catalytic systems and the resulting product. The advantages of the technology proposed by INFRA Technology Company involving an innovative reactor design for a high-performance multifunctional catalyst, are shown. -
Oil Shale Development in the United States: Prospects and Policy Issues
INFRASTRUCTURE, SAFETY, AND ENVIRONMENT THE ARTS This PDF document was made available from www.rand.org as CHILD POLICY a public service of the RAND Corporation. CIVIL JUSTICE EDUCATION Jump down to document ENERGY AND ENVIRONMENT 6 HEALTH AND HEALTH CARE INTERNATIONAL AFFAIRS The RAND Corporation is a nonprofit research NATIONAL SECURITY organization providing objective analysis and POPULATION AND AGING PUBLIC SAFETY effective solutions that address the challenges facing SCIENCE AND TECHNOLOGY the public and private sectors around the world. SUBSTANCE ABUSE TERRORISM AND HOMELAND SECURITY TRANSPORTATION AND Support RAND INFRASTRUCTURE Purchase this document WORKFORCE AND WORKPLACE Browse Books & Publications Make a charitable contribution For More Information Visit RAND at www.rand.org Explore RAND Infrastructure, Safety, and Environment View document details Limited Electronic Distribution Rights This document and trademark(s) contained herein are protected by law as indicated in a notice appearing later in this work. This electronic representation of RAND intellectual property is provided for non-commercial use only. Permission is required from RAND to reproduce, or reuse in another form, any of our research documents. This product is part of the RAND Corporation monograph series. RAND monographs present major research findings that address the challenges facing the public and private sectors. All RAND monographs undergo rigorous peer review to ensure high standards for research quality and objectivity. Oil Shale Development in the United States Prospects and Policy Issues James T. Bartis, Tom LaTourrette, Lloyd Dixon, D.J. Peterson, Gary Cecchine Prepared for the National Energy Technology Laboratory of the U.S. Department of Energy The research described in this report was conducted within RAND Infrastructure, Safety, and Environment (ISE), a division of the RAND Corporation, for the National Energy Technology Laboratory of the U.S.