Thermal Energy Storage Using Calcium Chloride Hexahydrate
Total Page:16
File Type:pdf, Size:1020Kb
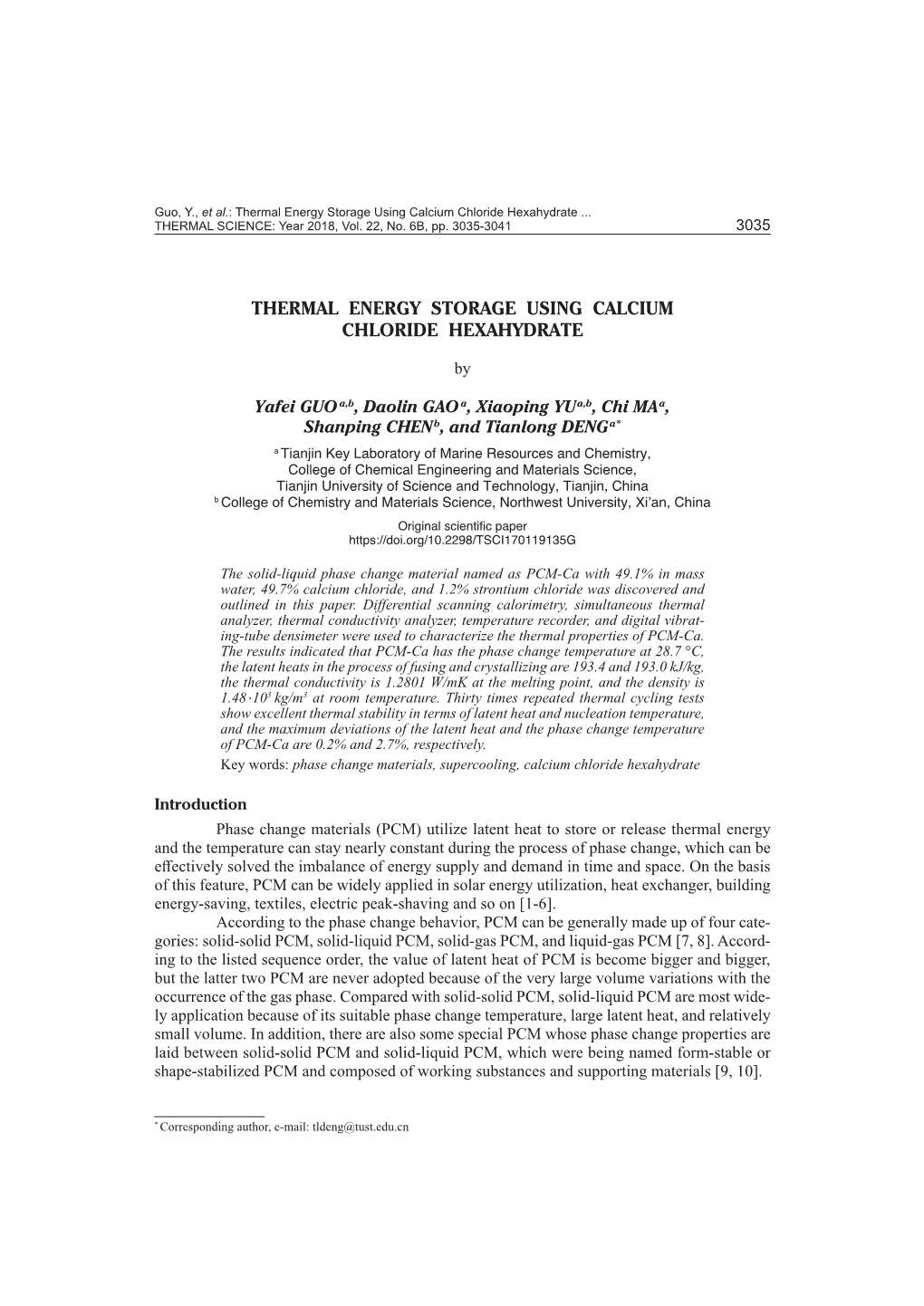
Load more
Recommended publications
-
Preparation of Barium Strontium Titanate Powder from Citrate
APPLIED ORGANOMETALLIC CHEMISTRY Appl. Organometal. Chem. 13, 383–397 (1999) Preparation of Barium Strontium Titanate Powder from Citrate Precursor Chen-Feng Kao* and Wein-Duo Yang Department of Chemical Engineering, National Cheng Kung University, Tainan, 70101, Taiwan TiCl4 or titanium isopropoxide reacted with INTRODUCTION citric acid to form a titanyl citrate precipitate. Barium strontium citrate solutions were then BaTiO3 is ferroelectric and piezoelectric and has added to the titanyl citrate reaction to form gels. extensive applications as an electronic material. It These gels were dried and calcined to (Ba,Sr)- can be used as a capacitor, thermistor, transducer, TiO3 powders. The gels and powders were accelerometer or degausser of colour television. characterized by DSC/TGA, IR, SEM and BaTiO3 doped with strontium retains its original XRD analyses. These results showed that, at characteristics but has a lower Curie temperature 500 °C, the gels decomposed to Ba,Sr carbonate for positive temperature coefficient devices under and TiO2, followed by the formation of (Ba,Sr)- various conditions. TiO3. The onset of perovskite formation oc- Besides solid-state reactions, chemical reactions curred at 600 °C, and was nearly complete at have also been used to prepare BaTiO3 powder. 1 1000 °C. Traces of SrCO3 were still present. Among them the hydrolysis of metal alkoxide , The cation ratios of the titanate powder oxalate precipitation in ethanol2, and alcoholic prepared in the pH range 5–6 were closest to dehydration of citrate solution3 are among the more the original stoichiometry. Only 0.1 mol% of the attractive methods. In 1956 Clabaugh et al.4 free cations remained in solution. -
Material Safety Data Sheet Version 3.4 Revision Date 09/03/2012 Print Date 02/06/2014
SIGMA-ALDRICH sigma-aldrich.com Material Safety Data Sheet Version 3.4 Revision Date 09/03/2012 Print Date 02/06/2014 1. PRODUCT AND COMPANY IDENTIFICATION Product name : Strontium chloride solution Product Number : 69042 Brand : Sigma Supplier : Sigma-Aldrich 3050 Spruce Street SAINT LOUIS MO 63103 USA Telephone : +1 800-325-5832 Fax : +1 800-325-5052 Emergency Phone # (For : (314) 776-6555 both supplier and manufacturer) Preparation Information : Sigma-Aldrich Corporation Product Safety - Americas Region 1-800-521-8956 2. HAZARDS IDENTIFICATION Emergency Overview OSHA Hazards Irritant GHS Classification Skin irritation (Category 3) Eye irritation (Category 2A) GHS Label elements, including precautionary statements Pictogram Signal word Warning Hazard statement(s) H316 Causes mild skin irritation. H319 Causes serious eye irritation. Precautionary statement(s) P305 + P351 + P338 IF IN EYES: Rinse cautiously with water for several minutes. Remove contact lenses, if present and easy to do. Continue rinsing. HMIS Classification Health hazard: 2 Flammability: 0 Physical hazards: 0 NFPA Rating Health hazard: 2 Fire: 0 Reactivity Hazard: 0 Potential Health Effects Inhalation May be harmful if inhaled. Causes respiratory tract irritation. Skin May be harmful if absorbed through skin. Causes skin irritation. Sigma - 69042 Page 1 of 6 Eyes Causes eye irritation. Ingestion May be harmful if swallowed. 3. COMPOSITION/INFORMATION ON INGREDIENTS Synonyms : Strontium chloridesolution Additive Screening Solution 27/Fluka kit no 78374 Component Classification Concentration Strontium chloride CAS-No. 10476-85-4 Skin Irrit. 2; Eye Dam. 1; 1 - 5 % EC-No. 233-971-6 STOT SE 3; H315, H318, H335 For the full text of the H-Statements and R-Phrases mentioned in this Section, see Section 16 4. -
The Role of Calcium and Strontium As the Most Dominant Elements During
crystals Article The Role of Calcium and Strontium as the Most Dominant Elements during Combinations of Different Alkaline Earth Metals in the Synthesis of Crystalline Silica-Carbonate Biomorphs Mayra Cuéllar-Cruz 1,2,* and Abel Moreno 2,* 1 Departamento de Biología, División de Ciencias Naturales y Exactas, Campus Guanajuato, Universidad de Guanajuato, Noria Alta S/N, Col. Noria Alta, Guanajuato C.P. 36050, Mexico 2 Instituto de Química, Universidad Nacional Autónoma de México, Av. Universidad 3000, Ciudad Universitaria, Ciudad de México 04510, Mexico * Correspondence: [email protected] (M.C.-C.); [email protected] (A.M.) Received: 22 June 2019; Accepted: 22 July 2019; Published: 24 July 2019 Abstract: The origin of life from the chemical point of view is an intriguing and fascinating topic, and is of continuous interest. Currently, the chemical elements that are part of the different cellular types from microorganisms to higher organisms have been described. However, although science has advanced in this context, it has not been elucidated yet which were the first chemical elements that gave origin to the first primitive cells, nor how evolution eliminated or incorporated other chemical elements to give origin to other types of cells through evolution. Calcium, barium, and strontium silica-carbonates have been obtained in vitro and named biomorphs, because they mimic living organism structures. Therefore, it is considered that these forms can resemble the first structures that were part of primitive organisms. Hence, the objective of this work was to synthesize biomorphs starting with different mixtures of alkaline earth metals—beryllium (Be2+), magnesium (Mg2+), calcium (Ca2+), barium (Ba2+), and strontium (Sr2+)—in the presence of nucleic acids, RNA and genomic DNA (gDNA). -
Experiment 1 ·∙ Hydrates
Name___________________________________________________________Lab Day__________Lab Time_________ Experiment 1 · Hydrates Pre-lab questions Answer these questions and hand them to the TF before beginning work. (1) What is the purpose of this experiment? ______________________________________________________________________ (2) What is a hydrate? ______________________________________________________________________ (3) You will heat a crucible to “constant weight”: how will you know that the crucible will have attained constant weight? ______________________________________________________________________ (4) You will drive off the water from a hydrate by heating it. What do you expect to see as the dehydration takes place? How will you know when the dehydration is complete? ______________________________________________________________________ (5) The slope m of the best straight line through the dehydration data has an associated un- certainty σm. How is the value of x in the hydrate MB·xH2O related to m and to σm? ______________________________________________________________________ Experiment 1 · Hydrates 1-1 Experiment 1 Hydrates Even people who have never studied chemistry know that wa- ter is represented by the formula H2O. But how are the formu- las of chemical compounds established? One method involves determining the relative amount by weight of each element in the compound. For example, let’s say you raid an illegal drug lab and find a white powder that you suspect is cocaine. When you heat 1.00 g of the white powder, it decomposes into 0.40 g of carbon (C, M = 12.01 g/mol) and 0.60 g of water (H2O, M = 18.02 g/mol). The number of moles of carbon in the sample is ⎛ 0.40 g C⎞ ⎛ mol C ⎞ ⎜ ⎟ ⎜ ⎟ = 0.033 mol C ⎝ ⎠ ⎝ 12.01 g C⎠ and the number of moles of water in the sample is ⎛ 0.60 g H2O⎞ ⎛ mol H2O ⎞ ⎜ ⎟ ⎜ ⎟ = 0.033 mol H2O ⎝ ⎠ ⎝ 18.02 g H2O⎠ There is one mole of carbon per mole of water in the sample. -
Strontium Chloride Solution, 1M MSDS # 723.40
Material Safety Data Sheet Page 1 of 2 Strontium Chloride Solution, 1M MSDS # 723.40 Section 1: Product and Company Identification Strontium Chloride Solution, 1M Synonyms/General Names: N/A Product Use: For educational use only Manufacturer: Columbus Chemical Industries, Inc., Columbus, WI 53925. 24 Hour Emergency Information Telephone Numbers CHEMTREC (USA): 800-424-9300 CANUTEC (Canada): 613-424-6666 ScholAR Chemistry; 5100 W. Henrietta Rd, Rochester, NY 14586; (866) 260-0501; www.Scholarchemistry.com Section 2: Hazards Identification White crystals; no odor. HMIS (0 to 4) Health 2 CAUTION! Slightly toxic by ingestion and body tissue irritant. Fire Hazard 0 Target organs: None known Reactivity 0 This material is considered hazardous by the OSHA Hazard Communication Standard (29 CFR 1910.1200). Section 3: Composition / Information on Ingredients Strontium Chloride, Hexahydrate (10025-70-4), 26.6%. Water (7732-18-5), 73.4%. Section 4: First Aid Measures Always seek professional medical attention after first aid measures are provided. Eyes: Immediately flush eyes with excess water for 15 minutes, lifting lower and upper eyelids occasionally. Skin: Immediately flush skin with excess water for 15 minutes while removing contaminated clothing. Ingestion: Call Poison Control immediately. Rinse mouth with cold water. Give victim 1-2 cups of water or milk to drink. Induce vomiting immediately. Inhalation: Remove to fresh air. If not breathing, give artificial respiration. Section 5: Fire Fighting Measures When heated to decomposition, emits acrid fumes. 0 Protective equipment and precautions for firefighters: Use foam or dry chemical to extinguish fire. 1 0 Firefighters should wear full fire fighting turn-out gear and respiratory protection (SCBA). -
Chemistry of Strontium in Natural Water
Chemistry of Strontium in Natural Water GEOLOGICAL SURVEY WATER-SUPPLY PAPER 1496 This water-supply paper was printed as separate chapters A-D UNITED STATES GOVERNMENT PRINTING OFFICE, WASHINGTON : 1963 UNITED STATES DEPARTMENT OF THE INTERIOR STEWART L. UDALL, Secretary GEOLOGICAL SURVEY Thomas B. Nolan, Director The U.S. Geological Survey Library has cataloged this publication as follows: U.S. Geological Survey. Chemistry of strontium in natural water. Washington, U.S. Govt. Print. Off., 1962. iii, 97 p. illus., diagrs., tables. 24 cm. (Its Water-supply paper 1496) Issued as separate chapters A-D. Includes bibliographies. 1. Strontium. 2. Water-Analysis. I. Title. (Series) CONTENTS [The letters in parentheses preceding the titles are those used to designate the separate chapters] Page (A) A survey of analytical methods for the determination of strontium in natural water, by C. Albert Horr____________________________ 1 (B) Copper-spark method for spectrochemical determination of strontirm in water, by Marvin W. Skougstad-______-_-_-_--_~__-___-_- 19 (C) Flame photometric determination of strontium in natural water, by C. Albert Horr_____._____._______________... 33 (D) Occurrence and distribution of strontium in natural water, by Margin W. Skougstad and C. Albert Horr____________.___-._-___-. 55 iii A Survey of Analytical Methods fc r The Determination of Strontium in Natural Water By C. ALBERT HORR CHEMISTRY OF STRONTIUM IN NATURAL rVATER GEOLOGICAL SURVEY WATER-SUPPLY PAPER 1496-A This report concerns work done on behalf of the U.S. Atomic Energy Commission and is published with the permission of the Commission UNITED STATES GOVERNMENT PRINTING OFFICE, WASHINGTON : 1959 UNITED STATES DEPARTMENT OF THE INTERIOR FRED A. -
Flame Test Demo I
FLAME TEST DEMO I. PURPOSE TO BETTER UNDERSTAND COLOR SPECTRUM BY IDENTIFYING SUBSTANCES WITH A FLAME TEST BACKGROUND MATERIALS CAN BE IDENTIFIED BY THE COLOR OF THE FLAME THAT THEY PRODUCE WHEN BURNED. ELEMENTS ARE THE UNITS FROM WHICH ALL MATTER IS MADE. ELEMENTS ARE LOCATED ON THE PERIODIC TABLE. SUBSTANCES CAN BE TESTED TO DETERMINE THEIR COMPOSITION. FLAME TESTS ARE USED TO ANALYZE WHAT IS IN A SUBSTANCE. THE FLAME TEST DETERMINES THE TYPE OF METAL OF AN IONIC SALT THAT IS PRESENT. THE NUMEROUS METALS BURN DIFFERENT COLORS. THE SPECIFIC COLOR INDICATES WHAT METAL IS PRESENT, JUST LIKE A FINGERPRINT OR DNA TEST IS USED TO DETERMINE THE EXACT PERSON. THE FLAME COLOR MAY BE SIMILAR, BUT NO 2 ELEMENTS BURN THE SAME EXACT COLOR. SPECTROSCOPY CAN BE USEFUL IN HELPING SCIENTISTS UNDERSTAND HOW AN OBJECT LIKE A BLACK HOLE OPERATES, HOW AN ACTIVE GALAXY PRODUCES LIGHT, HOW FAST A GALAXY IS MOVING, AND OF WHAT ELEMENTS A STAR IS MADE. THE COLORS OF FIREWORKS COME FROM THE BURNING OF METALLIC SALTS. ORIGINALLY, ONLY 2 COLORS WERE USED. IN 1630, 1 COLOR WAS ADDED. BY THE 1850’s, FORMULAS FOR THE COLORS USED IN FIREWORKS WERE CREATED. MANY OF THE SALTS ARE STILL BEING USED TODAY. FIREWORKS WERE NOT THE ONLY USE FOR THE COLORS EMITTED BY THESE SALTS. SCIENTISTS WERE USING FLAME TESTS TO OBSERVE THE COLORS GIVEN OFF WHEN A CHEMICAL IS BURNED AND CONSEQUENTLY IDENTIFY THE MATERIAL. COMPOUNDS CAN ALSO BE IDENTIFIED. SODIUM CHLORIDE BURNS YELLOW, POTASSIUM CHLORIDE BURNS PURPLE, AND LITHIUM CHLORIDE BURNS RED. -
THE PHYSICAL CHEMISTRY of METALS in THEIR MOLTEN HALIDES THESIS Presented for the Degree of DOCTOR of PHILOSOPHY in the UNIVERSI
THE PHYSICAL CHEMISTRY OF METALS IN THEIR MOLTEN HALIDES THESIS presented for the degree of DOCTOR OF PHILOSOPHY in the UNIVERSITY OF LONDON By Lars-Ingvar Staffansson, Bergsingenjor, (Stockholm). London, December 1959, ABSTRACT The phase diagrams of the systems calcium- calcium chloride, calcium-calcium bromide and calcium- calcium iodide have been established by solubility measurements and differential thermal analysis. Each of the systems was found to have a eutectic a mono- tectic and a large miscibility gap. The eutectics are 3.3, 3.2 and 6.8 mole % calcium respectively, and the corresponding temperatures are 763, 728 and 760°C. The monotectics are at 99.5, 99.6 and 99.7 mole % calcium respectively and the corresponding temperatures are 826, 828 and 831°C. The consolute points are at 1338, 1335 and 1380°C and the corresponding compositions are 62, 64 and 74 mole % calcium. Discrepancies between this and previous work are mainly attributed to composition changes of the phases during quenching. A method has been developed that overcomes this difficulty. The depression of the freezing point of strontium by strontium chloride has also been determined. From the results of this work a model for the mutal solubility of metalS and their molten halides has been suggested. CONTENTS Page CHAPTER 1: INTRODUCTION 1 1.1 General Introduction 1 1.2 Relevant previous work on metal-molten salts. 4 1.2.1 General 4 1.2.2 Alkaline earth metal-metal halide systems. 12 CHAPTER 2: EXPERIMENTAL 24 2.1 Programme 24 2.2 Preparation and purity of materials 25 2.2.1 Calcium 25 2.2.2 Strontium 26 2.2.3 Calcium Chloride 26 2.2.4 Calcium Bromide 28 2.2.5 Calcium Iodide 28 2.2.6 Strontium Chloride 29 2.2.7 Pure Iron 30 2.2.8 Gases 31 2.3 Dry-box. -
Separation of Strontium and Cesium from Ternary and Quaternary Lithium Chloride-Potassium Chloride Salts Via Melt Crystallization
Nucl Eng Technol 47 (2015) 867e874 Available online at www.sciencedirect.com ScienceDirect journal homepage: http://www.journals.elsevier.com/nuclear- engineering-and-technology/ Original Article SEPARATION OF STRONTIUM AND CESIUM FROM TERNARY AND QUATERNARY LITHIUM CHLORIDE-POTASSIUM CHLORIDE SALTS VIA MELT CRYSTALLIZATION * AMMON N. WILLIAMS a, , MICHAEL PACK b, and SUPATHORN PHONGIKAROON a a Department of Mechanical and Nuclear Engineering, Virginia Commonwealth University, 401 West Main Street, Richmond, VA 23284, USA b Department of Chemical and Materials Engineering and Nuclear Engineering Program, University of Idaho, 995 University Boulevard, Idaho Falls, ID 83401, USA article info abstract Article history: Separation of cesium chloride (CsCl) and strontium chloride (SrCl2) from the lithium Received 23 March 2015 chloride-potassium chloride (LiCl-KCl) salt was studied using a melt crystallization process Received in revised form similar to the reverse vertical Bridgeman growth technique. A ternary SrCl2-LiCl-KCl salt 22 July 2015 was explored at similar growth rates (1.8e5 mm/h) and compared with CsCl ternary results Accepted 9 August 2015 to identify similarities. Quaternary experiments were also conducted and compared with Available online 22 October 2015 the ternary cases to identify trends and possible limitations to the separations process. In the ternary case, as much as 68% of the total salt could be recycled per batch process. In the Keywords: quaternary experiments, separation of Cs and Sr was nearly identical at the slower rates; Melt Crystallization however, as the growth rate increased, SrCl2 separated more easily than CsCl. The qua- Molten Salt ternary results show less separation and rate dependence than in both ternary cases. -
United States Patent Office Patented Feb
3,495,953 United States Patent Office Patented Feb. 17, 1970 1 2 be removed by evaporation and filtration before further 3,495,953 proceSSIng. METHOD OF SEPARATING STRONTUM CHELORIDE FROMMXED SOLUTIONS The aqueous solution is selectively cooled to, e.g., 25 USENGETHANOL C. to 15 C., to crystallize a mixture of CaCl2.6H2O and Remigius A. Gaska, Midland, and Robert A. Canute, 5 SrCl2.2H2O having a CaCl to SrCl weight ratio of the Mount Pleasant, Mich., assignors to The Dow Chemical order to 20:1. The solid mixture is separated from the Company, Midland, Mich., a corporation of Delaware mother liquor by conventional means such as filtration or No Drawing. Filed June 17, 1968, Ser. No. 737,378 centrifugation. Int. C. C01f 11/32; B01d 9/02, 57/00 The solid mixture is heated to, e.g., 28° C. to 50° C. to U.S. C. 23-308 5 Claims O selectively melt the CaCl2.6H2O crystals. The melted por tion is separated from the solid SrCl2.2H2O by filtration or similar means. However, as previously disclosed the solid ABSTRACT OF THE DISCLOSURE strontium chloride still contains some impurities, e.g., 5-25 In a process of separating strontium chloride from brine percent CaCl2 as CaCl2.6H2O. solutions containing strontium chloride and calcium chlo We have unexpectedly discovered that washing this im ride comprising selectively crystallizing the brine, selec purity containing solid strontium chloride hydrate with tively melting the resulting precipitate to produce a solid -ethanol effectively removes substantially all the remaining strontium chloride containing calcium chloride impuri CaCl2.6H2O impurity. -
Solubility Patterns Double Replacement Reactions SCIENTIFIC
Solubility Patterns Double Replacement Reactions SCIENTIFIC Introduction The alkaline earth metals are so-named because their oxides are highly basic (alkaline) and because they occur abundantly on Earth. Alkaline earth metal compounds—carbonates, sulfates, silicates—are abundant in minerals such as dolomite (calcium and magnesium carbonate), epsomite (magnesium sulfate), and baryte (barium sulfate). The solubilities of these compounds vary widely, depending on the metal cation. Are there any patterns or periodic trends in the solubility behavior of alkaline earth metal compounds? Concepts • Alkaline earth metals • Periodic trends • Solubility rules • Double-replacement reactions • Ionic compounds Materials Alkaline earth metal chlorides Testing Solutions Barium chloride solution, 0.1 M, BaCl2, 6 mL Ammonium oxalate solution, 0.25 M, (NH4)2C2O4, 4 mL Calcium chloride solution, 0.1 M, CaCl2, 6 mL Potassium iodate solution, 0.2 M, KIO3, 4 mL Magnesium chloride solution, 0.1 M, MgCl2, 6 mL Sodium carbonate solution, 1 M, Na2CO3, 4 mL Strontium chloride solution, 0.1 M, SrCl2, 6 mL Sodium sulfate solution, 1 M, Na2SO4, 4 mL Reaction plate, 24-well Safety Precautions Potassium iodate is moderately toxic and is irritating to skin, eyes, and the respiratory tract. Strontium and barium compounds are toxic by ingestion. Oxalates are toxic by ingestion and are irritating to body tissues. Avoid contact of all chemicals with eyes and skin. Wear chemical splash goggles, chemical-resistant gloves, and a chemical-resistant apron. Please review current Material Safety Data Sheets for additional safety, handling, and disposal information. Wash hands thoroughly with soap and water before leaving the laboratory. Procedure 1. -
Histomorphometric Assessment of Implant Coating with a Mixture Of
Available online at www.ijmrhs.com cal R edi ese M ar of c l h a & n r H u e o a J l l t h International Journal of Medical Research & a S n ISSN No: 2319-5886 o c i t i Health Sciences, 2018, 7(1): 152-157 e a n n c r e e t s n I • • IJ M R H S Histomorphometric Assessment of Implant Coating with A Mixture of Strontium Chloride and Hydroxyapatite at Different Concentration Jani Ghasak H1*, Al-Ameer Shatha S2 and Abdullah Bashar H3 1 Department of Prosthodontics, College of Dentistry, University of Baghdad, Iraq 2 Department of Prosthodontics, College of Dentistry, University of Baghdad, Iraq 3 Department of Oral and Maxillofacial Diagnosis, College of Dentistry, University of Baghdad, Iraq *Corresponding e-mail: [email protected] ABSTRACT Background/purpose: Surface properties are one of the major keys of successful implant osseointegration in addition to mechanical strength and excellent biocompatibility of implant material. The purpose of this study is to make histological and histomorphometric analysis of an implant coated with strontium chloride (SrCl2) mixed with hydroxyapatite (HA) at different concentrations, in rabbit tibia at 2 and 6 weeks of implantation time. Method: 48 commercially pure titanium screw shaped implants were placed in 24 healthy adult New Zeeland rabbits, each rabbit received 2 implants; one coated with mixture 1 (25% HA and 75% SrCl2) and the other coated with mixture 2 (75% HA and 25% SrCl2). Twelve rabbits were sacrificed at 2 weeks of healing and other twelve after 6 weeks.