Natural Fiber Composites Alternative Solutions for Reinforcement Of
Total Page:16
File Type:pdf, Size:1020Kb
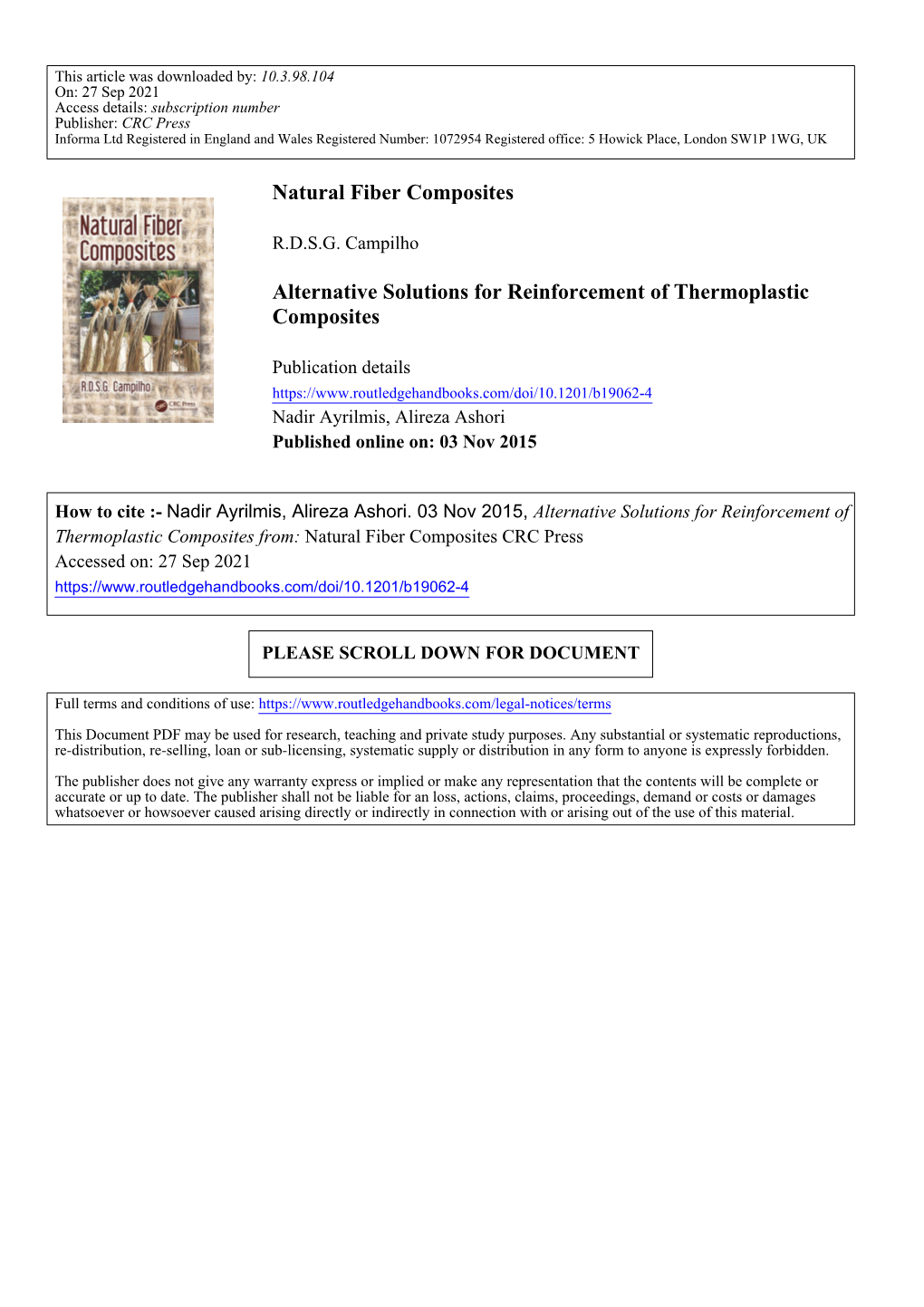
Load more
Recommended publications
-
Stability Analysis of Selected Jute (Corchorus Capsularis L.) Genotypes in Saline and Non-Saline Soils of Bangladesh
The Agriculturists 13(2): 25-35 (2015) ISSN 2304-7321 (Online), ISSN 1729-5211 (Print) A Scientific Journal of Krishi Foundation Indexed Journal Stability Analysis of Selected Jute (Corchorus capsularis L.) Genotypes in Saline and Non-saline Soils of Bangladesh M. Billah, B. Sikder, M. A. Latif* and A. K. Chowdhury Department of Genetic and Plant Breeding, Patuakhali Science and Technology University, Dumki, Patuakhali-8602, Bangladesh *Corresponding author and Email: [email protected] Received: 04 April 2015 Accepted: 12 December 2015 Abstract Ten white jute genotypes (Corchorus capsularis L.) were evaluated across three different locations including saline and non-saline soils of Bangladesh during 2014 to assess genotype × environment interaction and stability for plant height, base diameter, fresh weight with leaves, dry stick weight and dry fiber weight. Additive Main Effect Multiplicative Interaction (AMMI) model was used to assess the additive and multiplicative interaction of jute genotypes for these characters across three environments. Significant variations in genotype environment interaction were observed for all characters except plant height and base diameter. Based on stability parameters bi 1 and bi o, the genotype C-3465 showed stability for plant height, D-154 for base diameter and fresh weight with leaves. The genotypes C-2753 showed stability for fresh weight with leaves, without leaves and dry stick weight, CVL-1 for fresh weight without leaves, C-2760 for fresh weight with leaves, without leaves and for dry fiber weight across saline and non- saline area. Heritability in broad sense was quite high for all characters (85-90%) except plant height (17%) indicating less environmental fluctuation. -
Corchorus L. and Hibiscus L.: Molecular Phylogeny Helps to Understand Their Relative Evolution and Dispersal Routes
Corchorus L. and Hibiscus L.: Molecular Phylogeny Helps to Understand Their Relative Evolution and Dispersal Routes Arif Mohammad Tanmoy1, Md. Maksudul Alam1,2, Mahdi Muhammad Moosa1,3, Ajit Ghosh1,4, Waise Quarni1,5, Farzana Ahmed1, Nazia Rifat Zaman1, Sazia Sharmin1,6, Md. Tariqul Islam1, Md. Shahidul Islam1,7, Kawsar Hossain1, Rajib Ahmed1 and Haseena Khan1* 1Molecular Biology Lab, Department of Biochemistry and Molecular Biology, University of Dhaka, Dhaka 1000, Bangladesh. 2Department of Molecular and Cell Biology, Center for Systems Biology, University of Texas at Dallas, Richardson, TX 75080, USA. 3Graduate Studies in Biological Sciences, The Scripps Research Institute, 10550 North Torrey Pines Road, La Jolla, CA 92037, USA. 4Plant Molecular Biology, International Centre for Genetic Engineering and Biotechnology, Aruna Asaf Ali Marg, New Delhi 110067, India. 5Department of Pathology and Cell Biology, University of South Florida, 12901 Bruce B. Downs Blvd., Tampa, FL 33612, USA. 6Department of Kidney Development, Institute of Molecular Embryology and Genetics, Kumamoto University, 2-2-1 Honjo, Kumamoto 860-0811, Japan. 7Breeding Division, Bangladesh Jute Research Institute (BJRI), Dhaka 1207, Bangladesh. ABSTRACT: Members of the genera Corchorus L. and Hibiscus L. are excellent sources of natural fibers and becoming much important in recent times due to an increasing concern to make the world greener. The aim of this study has been to describe the molecular phylogenetic relationships among the important members of these two genera as well as to know their relative dispersal throughout the world. Monophyly of Corchorus L. is evident from our study, whereas paraphyletic occurrences have been identified in case of Hibiscus L. -
Copper Uptake and Accumulation, Ultra-Structural Alteration, and Bast
plants Article Copper Uptake and Accumulation, Ultra-Structural Alteration, and Bast Fibre Yield and Quality of Fibrous Jute (Corchorus capsularis L.) Plants Grown under Two Different Soils of China Muhammad Hamzah Saleem 1, Shafaqat Ali 2,3,* , Sana Irshad 4, Muhammad Hussaan 5, Muhammad Rizwan 2 , Muhammad Shoaib Rana 6, Abeer Hashem 7,8, Elsayed Fathi Abd_Allah 9 and Parvaiz Ahmad 7,10,* 1 MOA Key Laboratory of Crop Ecophysiology and Farming System in the Middle Reaches of the Yangtze River, College of Plant Science and Technology, Huazhong Agricultural University, Wuhan 430070, China; [email protected] 2 Department of Environmental Sciences and Engineering, Government College University Allama Iqbal Road, 38000 Faisalabad, Pakistan; [email protected] 3 Department of Biological Sciences and Technology, China Medical University, Taichung 40402, Taiwan 4 School of Environmental Studies, China University of Geosciences, Wuhan 430070, China; [email protected] 5 Department of Botany, Government College University, Allama Iqbal Road, 38000 Faisalabad, Pakistan; [email protected] 6 Key Laboratory of Arable Land Conservation (Middle and Lower Reaches of Yangtze River), Ministry of Agriculture, Microelements Research Center, College of Resource and Environment, Huazhong Agricultural University, Wuhan 430070, China; [email protected] 7 Botany and Microbiology Department, College of Science, King Saud University, P.O. Box. 2460, Riyadh 11451, Saudi Arabia; [email protected] 8 Mycology and Plant Disease Survey Department, Plant Pathology Research Institute, ARC, Giza 12511, Egypt 9 Plant Production Department, College of Food and Agricultural Sciences, King Saud University, P.O. Box. 2460, Riyadh 11451, Saudi Arabia; [email protected] 10 Department of Botany, S.P. -
Corchorus Olitorius Linn) and Scent Leaf (Ocimum Gratissimum Linn) Diet Supplementation on Mnu-Induced Colon Cancer in Wistar Rats
PREVENTIVE EFFECT OF DIFFERENT LEVELS OF JEW‟S MALLOW (CORCHORUS OLITORIUS LINN) AND SCENT LEAF (OCIMUM GRATISSIMUM LINN) DIET SUPPLEMENTATION ON MNU-INDUCED COLON CANCER IN WISTAR RATS BY KUNLE OGUNGBEMI DEPARTMENT OF BIOCHEMISTRY FACULTY OF SCIENCE AHMADU BELLO UNIVERSITY, ZARIA, NIGERIA SEPTEMBER, 2015 i PREVENTIVE EFFECT OF DIFFERENT LEVELS OF CORCHORUS OLITORIUS LINN AND OCIMUM GRATISSIMUM LINN DIET SUPPLEMENTATION ON MNU-INDUCED COLON CANCER IN WISTAR RATS BY Kunle OGUNGBEMI BSC BIOCHEMISTRY (ABU) 2011 MSc/SCIEN/22990/2012-2013 A THESIS SUBMITTED TO THE SCHOOL OF POSTGRADUATE STUDIES, AHMADU BELLO UNIVERSITY, ZARIA IN PARTIAL FULFILLMENT OF THE REQUIREMENTS FOR THE AWARD OF A MASTERS DEGREE IN BIOCHEMISTRY DEPARTMENT OF BIOCHEMISTRY FACULTY OF SCIENCE AHMADU BELLO UNIVERSITY, ZARIA NIGERIA SEPTEMBER, 2015 ii DECLARATION I declare that the work in this Dissertation entitled „PREVENTIVE EFFECT OF DIFFERENT LEVELS OF CORCHORUS OLITORIUS LINN AND OCIMUM GRATISSIMUM LINN DIET SUPPLEMENTATION ON MNU INDUCED COLON CANCER IN WISTAR RATS‟ has been carried out by me in the Department of Biochemistry. The information derived from the literature has been duly acknowledged in the text and a list of references provided. No part of this thesis was previously presented for another degree at this or any other institution. Ogungbemi Kunle __________________ _______________ MSc/Sci/22990/2012-2013 Signature Date iii CERTIFICATION I declare that the work in this Dissertation entitled PREVENTIVE EFFECT OF DIFFERENT LEVELS OF CORCHORUS OLITORIUS LINN AND OCIMUM GRATISSIMUM LINN DIET SUPPLEMENTATION ON MNU INDUCED COLON CANCER IN WISTAR RATS by Ogungbemi Kunle (MSc/Sci/22990/2012-2013), meets the regulations governing the award of the degree of Masters in Biochemistry of the Ahmadu Bello University, and is approved for its contribution to knowledge and literary presentation. -
Comparative Genomics of Two Jute Species and Insight Into Fibre
LETTERS PUBLISHED: 30 JANUARY 2017 | VOLUME: 3 | ARTICLE NUMBER: 16223 OPEN Comparative genomics of two jute species and insight into fibre biogenesis Md Shahidul Islam1,2,3*,JenniferA.Saito1,4, Emdadul Mannan Emdad1, Borhan Ahmed1,2,3, Mohammad Moinul Islam1,2,3, Abdul Halim1,2,3, Quazi Md Mosaddeque Hossen1,2,3, Md Zakir Hossain1,2,3, Rasel Ahmed1, Md Sabbir Hossain1, Shah Md Tamim Kabir1, Md Sarwar Alam Khan1, Md Mursalin Khan1, Rajnee Hasan1, Nasima Aktar1,UmmayHoni1, Rahin Islam1, Md Mamunur Rashid1,XuehuaWan1,4, Shaobin Hou1,4, Taslima Haque3, Muhammad Shafiul Azam3, Mahdi Muhammad Moosa3, Sabrina M. Elias3,A.M.MahediHasan3, Niaz Mahmood3, Md Shafiuddin3,SaimaShahid3, Nusrat Sharmeen Shommu3, Sharmin Jahan3, Saroj Roy3,5, Amlan Chowdhury3,5, Ashikul Islam Akhand3,5, Golam Morshad Nisho3,5, Khaled Salah Uddin3,5,TaposhiRabeya3,5,S.M.EkramulHoque3,5, Afsana Rahman Snigdha3,5, Sarowar Mortoza3,5, Syed Abdul Matin3,5,MdKamrulIslam3,5,M.Z.H.Lashkar3,5, Mahboob Zaman3,5, Anton Yuryev1,6, Md Kamal Uddin1,2, Md Sharifur Rahman1,7, Md Samiul Haque1,2,3, Md Monjurul Alam1,2,3, Haseena Khan3,8 and Maqsudul Alam1,3,4† Jute (Corchorus sp.) is one of the most important sources of We performed whole-genome shotgun (WGS) sequencing with natural fibre, covering ∼80% of global bast fibre production1. the Roche/454 platform (Supplementary Table 1) and assembled Only Corchorus olitorius and Corchorus capsularis are commer- the genomes using CABOG6. The resulting assemblies were cially cultivated, though there are more than 100 Corchorus 445 Mb (scaffold N50 length, 3.3 Mb; longest scaffold, 45.5 Mb) species2 in the Malvaceae family. -
Potential Healing Powers with Jute Plant- a Review
International Journal of Sciences: Basic and Applied Research (IJSBAR) ISSN 2307-4531 (Print & Online) http://gssrr.org/index.php?journal=JournalOfBasicAndApplied -------------------------------------------------------------------------------------------------------------------------- Potential Healing Powers with Jute Plant- A Review Md. Mahabub Alia, Balaram Rayb, Begum Rokeyac, Mst. Aleya Nasreend, Zakaria Ahmede* a,d,eBiochemistry and Microbiology Department, Bangladesh Jute research Institute, Manik Mia Avenue, Dhaka–1207, Bangladesh bDepartment of Chemistry, Hajee Danesh Science & Technology University, Dinajpur, Bangladesh cDepartment of Pharmacology, Bangladesh University of Health Science, Mirpur, Dhaka, Bangladesh aEmail: [email protected] , dEmail: [email protected] eEmail: [email protected] bEmail: [email protected] cEmail: [email protected] , cEmail: [email protected] Abstract Jute (Corchorus spp) can be a potential medicinal product for the treatment of many diseases. In traditional medicinal practices, it is used to treat constipation, demulcent, dysentery, worm, carminative anthalmitic, intestinal antiseptic, ascites, pain, piles, tumors, dysuria, febrifuge, stomachic, cystitis etc. Till now more than 80 compounds, including glycosides, triterpenes, ionones, phenolics, phytosterols, organic acids, lignins, alkaloids have been isolated and identified from jute plant. The main phytochemical compounds are cardiac glycosides, corchorin, corchotoxin, helveticoside, corchoroside A and B, olitoriside, -
JRC 9057 (Ishani): a Newly Developed White Jute (Corchorus Capsularis L
The Pharma Innovation Journal 2018; 7(7): 164-167 ISSN (E): 2277- 7695 ISSN (P): 2349-8242 NAAS Rating: 5.03 JRC 9057 (Ishani): a newly developed white jute TPI 2018; 7(7): 164-167 © 2018 TPI (Corchorus capsularis L.) variety for enhanced fibre www.thepharmajournal.com Received: 23-05-2018 yield and improved quality textile fibre Accepted: 24-06-2018 Sanjoy Shil Sanjoy Shil and Jiban Mitra Asst. Professor, Bidhan Chandra Krishi Viswavidyalaya (Bankura Campus), Chhatna, Susunia, Abstract Bankura, West Bengal, India Jute is one of the most affordable natural fibers and it is second only to cotton in amount produced and variety of uses of vegetable fibers. Jute fibres are eco-friendly, biodegradable and recyclable in nature Jiban Mitra and hence it create pollution free environment. In modern era of growing environmental friendly crops, DUS Testing Laboratory, the role of jute as ‘Green Crop’ may be highlighted and the significance of this commercial crop will be Division of Crop Improvement, not only to produce fibre for industries as raw material but also the equivalent impact on balancing and ICAR-Central Research Institute conditioning the soil-air-environment. So the production of jute fibres assumes high socio-economic as Jute & Allied Fibres (ICAR- well as environmental significance. Among the two species of jute (Corchorus olitorius L. and CRIJAF), Barrackpore, Kolkata, Corchorus capsularis L.) fibre made from C. capsularis is whiter and of a higher quality than that made West Bengal, India from C. olitorius. The cultivation of white jute (C. capsularis L.) is very specific and native to India particularly to Eastern states. -
PLANT SCIENCE TODAY, 2021 Vol 8(2): 416–424 HORIZON E-Publishing Group ISSN 2348-1900 (Online)
PLANT SCIENCE TODAY, 2021 Vol 8(2): 416–424 HORIZON https://doi.org/10.14719/pst.2021.8.2.1083 e-Publishing Group ISSN 2348-1900 (online) RESEARCH ARTICLE Responses and screening of white jute (Corchorus capsularis L.) genotypes against salinity stresses Sadia Afrin Jui1, Md. Mia Mukul1*, Md. Harun Or Rashid1, Iffat Jahan Nur1, Ranjit Kumar Ghosh1, Md. Golam Mostofa1, Nargis Akter1, Md. Tipu Sultan2 1Breeding Division, Bangladesh Jute Research Institute (BJRI), Manik Mia Avenue, Dhaka, Bangladesh 2Jute Research Regional Sub-Station, BJRI, Pakhimara, Patuakhali, Bangladesh *Email: [email protected] ARTICLE HISTORY ABSTRACT Received: 03 January 2021 Soil salinity, a serious threat to jute cultivation in saline areas (southern parts) of Bangladesh. Accepted: 12 March 2021 Bangladesh Jute Research Institute (BJRI) has developed a moderately salt tolerant White Jute variety Published: 01 May 2021 (BJRI Deshi pat-8; BJC 2197) in 2013 which can’t grow well in saline areas having more than 8.0 dSm-1 salinity stress. Hence, 23 whitejute accessions and one control variety (BJC 2197) were tested to isolate the salt tolerant accession(s) for hybridization purpose followed by augmented design in farmers’ field KEYWORDS having nearly 8.0-9.0 dSm-1 salinity at Patuakhali district during mid-March to mid-August 2019. The Jute breeding; Corchorus capsularis; 2 Genotype; Salinity Tolerance; Soil experimental plot size was 3.0 m (3 m × 1 m) for each genotype having 3 lines of 1.0 m length, plant- salinity plant: 10-15 cm and line- line: 30 cm distance. Soil salinity was recorded during sowing, vegetative and plant maturity stages. -
The Contents and Pharmacological Importance of Corchorus Capsularis- a Review
IOSR Journal Of Pharmacy www.iosrphr.org (e)-ISSN: 2250-3013, (p)-ISSN: 2319-4219 Volume 6, Issue 6 Version. 3 (June 2016), PP. 58-63 The contents and pharmacological importance of Corchorus capsularis- A review Prof Dr Ali Esmail Al-Snafi Department of Pharmacology, College of Medicine, Thi qar University, Iraq. Abstract: Seeds of Corchorus capsularis contained cardiac glycosides, corchorin, corchortoxin helveticoside, corchoroside A and B, biosides, olitoriside, erysimoside, strophantidol glycosides, oliogosaccaride and olitoriside; while leaves contained flavonoids, triterpenes, saponins, glucoside, capsularin steroids and many other secondary metabolites. The pharmacological studied revealed that te plant possessed cardiac, antioxidant, antiinflammmatory, analgesic, antipyretic, antimicrobial, insecticidal and many other pharmacological effects. This review was designed to highlight the chemical constituents and pharmacological effects of Corchorus capsularis Keywords: pharmacology, constituents, pharmacognosy, Corchorus capsularis I. INTRODUCTION During the last few decades there has been an increasing interest in the study of medicinal plants and their traditional use in different parts of the world(1). Plants generally produce many secondary metabolites which were constituted an important source of many pharmaceutical drugs(2-21). Seeds of Corchorus capsularis contained cardiac glycosides, corchorin, corchortoxin helveticoside, corchoroside A and B, biosides, olitoriside, erysimoside, strophantidol glycosides, oliogosaccaride and -
New Evidence for Jute (Corchorus Capsularis L.) in the Indus Civilization
Archaeol Anthropol Sci DOI 10.1007/s12520-012-0088-1 ORIGINAL PAPER New evidence for jute (Corchorus capsularis L.) in the Indus civilization Rita P. Wright & David L. Lentz & Harriet F. Beaubien & Christine K. Kimbrough Received: 17 October 2011 /Accepted: 9 January 2012 # Springer-Verlag 2012 Abstract In this paper, we report the results of an analysis allow trace evidence to be preserved. The discovery of the of a preserved structure of jute on a ceramic artifact from the preserved structure of jute fibers on an artifact securely site of Harappa that is dated to 2200–1900 (cal.) BC (Fig. 1). dated to 2200–1900 (cal.) BC is the earliest evidence for Jute cloth has not previously been identified at this early date the use of this plant for textiles in the Indus civilization. in the Indus civilization. Since fiber remains are rare in pre- historic South Asia, we briefly review the evidence for seed and fiber remains used in textile production in this region. Evidence for plant fibers in the Indus and beyond Keywords Jute cloth . Corchorus capsularis L. Indus Evidence for cloth produced from plant fibers is rare before civilization the third millennium BC at Indus-related sites. The earliest evidence for the use of plant fibers is from cotton (Gossypium arboreum L.) found as a mineralized thread inside of a copper Introduction bead from a Neolithic burial at the site of Mehrgarh dated to the 6th millennium BC (Moulherat et al. 2002). Other The study of archaeological textiles produced from plant evidence for cotton from Mehrgarh is from charred seed crops in South Asia has advanced significantly in the past remains dated to the 5th millennium BC (Costantini 1984). -
Floral Biology of Jute Classification
FLORAL BIOLOGY OF JUTE CLASSIFICATION JUTE • Botanical name - Corchorus capsularis Corchorus olitorius • Chromosome no.- 2n-14 • Order - Plantae • Family - Tiliaceae • Genus - Corchorus • Germination - Epigeal • Pollination - Self pollinated INTRODUCTION • Jute is an important fibre crop next to cotton. It is one of the major foreign exchange earners. Exported as manufactured goods and as raw fibre, it earns foreign exchange of around 3000 million rupees per annum. • The fibre is used extensively in the manufacture of gunny cloth, gunny bags, and other packaging materials for storing and transporting grains, pulses, spices, cement, sugar, cotton, fertilizers, wool, etc. all over the world. Origin • The greatest diversity of species of Corchorus is found in Afica. • Corchorus olitorius- Africa • Corchorus capsularis- Indo-Burma region Classification 1. Corchorus capsularis- hardy plant, tolerate water logging, more popular (70% area of total jute area), white fibre hence called ‘White Jute’(trade name), leaf is bitter in taste due to corchorin known as ‘Tita Pat’. Planting time late Feb. to March. 2. Corchorus olitorius- grown on well drained high lands only, fibre is fine, softer, stronger, yellow to red, tasteless leaf hence called ‘Mitha Pat’, higher yield, planted in April/May. Botanical Description • Jute belongs to genus Corchorus in the family Tiliaceae. It is a herbaceous annual. The plant has tap root system with numerous lateral branches. Although both the species of jute C. capsularis and C. olitorius are alike in general appearance, there are considerable differences between them as follows: Corchorus capsularis- • Plant height- Plant is shorter in height than C. olitouius usually 1.5 to 4 meters. -
Corchorus Capsularis
Tao et al. BMC Genomics (2017) 18:355 DOI 10.1186/s12864-017-3712-8 RESEARCH ARTICLE Open Access High-density genetic map construction and QTLs identification for plant height in white jute (Corchorus capsularis L.) using specific locus amplified fragment (SLAF) sequencing Aifen Tao1, Long Huang2, Guifen Wu3, Reza Keshavarz Afshar4, Jianmin Qi1*, Jiantang Xu1, Pingping Fang1, Lihui Lin1, Liwu Zhang1 and Peiqing Lin1 Abstract Background: Genetic mapping and quantitative trait locus (QTL) detection are powerful methodologies in plant improvement and breeding. White jute (Corchorus capsularis L.) is an important industrial raw material fiber crop because of its elite characteristics. However, construction of a high-density genetic map and identification of QTLs has been limited in white jute due to a lack of sufficient molecular markers. The specific locus amplified fragment sequencing (SLAF-seq) strategy combines locus-specific amplification and high-throughput sequencing to carry out de novo single nuclear polymorphism (SNP) discovery and large-scale genotyping. In this study, SLAF-seq was employed to obtain sufficient markers to construct a high-density genetic map for white jute. Moreover, with the development of abundant markers, genetic dissection of fiber yield traits such as plant height was also possible. Here, we present QTLs associated with plant height that were identified using our newly constructed genetic linkage groups. Results: An F8 population consisting of 100 lines was developed. In total, 69,446 high-quality SLAFs were detected of which 5,074 SLAFs were polymorphic; 913 polymorphic markers were used for the construction of a genetic map. The average coverage for each SLAF marker was 43-fold in the parents, and 9.8-fold in each F8 individual.