Track Elements
Total Page:16
File Type:pdf, Size:1020Kb
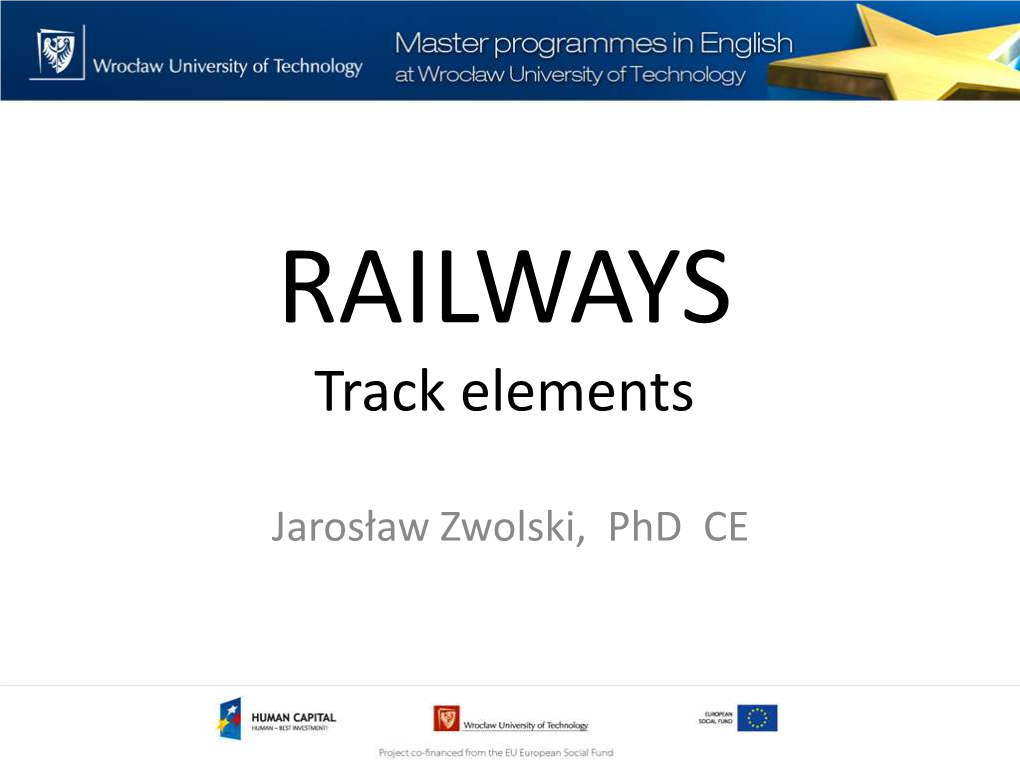
Load more
Recommended publications
-
Advanced Prestressed Concrete
ADVANCED PRESTRESSED CONCRETE. Author: A.Pon Arul Yesu Raja, V.Manikandan. 3rd year Civil Engineering. College Name Here [email protected] Abstract: Pre-stressed concrete sleepers are the main components of railway track systems. To carry and transfer the dynamic wheel loads from the rails to the ground, their current design and construction are limited by allowable flexural stress constraints under service conditions. In current design practice for such a component, the dynamic load effects due to wheel/rail interactions are treated as a quasi-static load using a dynamic impact factor. Then, the allowable stresses eliminate a crack initiation. In reality, the impact events are frequently recorded because of the uncertainties of wheel or rail irregularities such as flat wheels and dipped rails. These effects cause cracking in the concrete sleepers, resulting in excessive maintenance. Limit states design philosophy for the pre-stressed concrete sleepers, containing ultimate and fatigue limit states, has been recently proposed based on structural reliability concept to rationalise the design method and minimise the maintenance.On the basis of probabilistic approach, the high-magnitude low-cycle fatigue limit states, which are more significant in terms of damage evolution, have been addressed in this article. Series of repeated impact tests for the in-situ pre-stressed concrete sleepers were carried out using the Australian largest high-capacity drop weight impact testing machine at the University of Wollongong. The impact forces have been simulated in relation to the probabilistic track force distribution obtained from a heavy haul rail network. This article focuses on the impact responses of the cumulatively damaged sleepers. -
Typical Questions 1
TYPICAL QUESTIONS 1. Describe various functions of rail. Compare Bull headed rail vis-à-vis flat footed rail. 2. Give the details of various standard rail section being used on Indian Railways for B.G., M.G. & N.G. 3. What are various type of rail joints which are provided on Indian Railway ? Give details of supported rail joints and suspended rail joints. 4. Describe briefly the composition of rail steel. Give briefly the purpose of various elements of rail steels. 5. What do you understand by creep of rails ? Discuss various causes of creep of rails and how does if affect the track ? 6. Discuss various methods of prevention of creep. 7. Write short notes on (i) Bull headed rails; (ii) Flat footed rails; (iii)Staggered rail joints; (iv) Square rail joints. 8. What are the main function of sleepers ? Describe briefly the requirements of an ideal sleeper. 9. What is the standard size of wooden sleeper being used on Indian Railways. Describe briefly the purpose of adzing and augering of wooden sleepers. 10. What do you understand by CST-9 sleepers ? Describe briefly the limitation of CST-9 sleepers. 11. Describe the design of steel trough sleeper with the help of sketch. What are the advantages and disadvantages of concrete sleeper. 12. What are the prohibited locations for laying of concrete sleepers ? Describe briefly salient fea tures of maintenance of concrete sleeper. 13. What is the function of fish plates ? Draw sketch of fish plate giving various elements of the same. 14. What is the difference between ordinary fish plate and combination fish plate. -
Track Report 2006-03.Qxd
DIRECT FIXATION ASSEMBLIES The Journal of Pandrol Rail Fastenings 2006/2007 1 DIRECT FIXATION ASSEMBLIES DIRECT FIXATION ASSEMBLIES PANDROL VANGUARD Baseplate Installed on Guangzhou Metro ..........................................pages 3, 4, 5, 6, 7 PANDROL VANGUARD Baseplate By L. Liu, Director, Track Construction, Guangzhou Metro, Guangzhou, P.R. of China Installed on Guangzhou Metro Extension of the Docklands Light Railway to London City Airport (CARE project) ..............pages 8, 9, 10 PANDROL DOUBLE FASTCLIP installation on the Arad Bridge ................................................pages 11, 12 By L. Liu, Director, Track Construction, Guangzhou Metro, Guangzhou, P.R. of China PANDROL VIPA SP installation on Nidelv Bridge in Trondheim, Norway ..............................pages 13,14,15 by Stein Lundgreen, Senior Engineer, Jernbanverket Head Office The city of Guangzhou is the third largest track form has to be used to control railway VANGUARD vibration control rail fastening The Port Authority Transit Corporation (PATCO) goes High Tech with Rail Fastener............pages 16, 17, 18 in China, has more than 10 million vibration transmission in environmentally baseplates on Line 1 of the Guangzhou Metro by Edward Montgomery, Senior Engineer, Delaware River Port Authority / PACTO inhabitants and is situated in the south of sensitive areas. Pandrol VANGUARD system has system (Figure 1) in China was carried out in the country near Hong Kong. Construction been selected for these requirements on Line 3 January 2005. The baseplates were installed in of a subway network was approved in and Line 4 which are under construction. place of the existing fastenings in a tunnel on PANDROL FASTCLIP 1989 and construction started in 1993. Five the southbound track between Changshoulu years later, the city, in the south of one of PANDROL VANGUARD TRIAL ON and Huangsha stations. -
Railway Technology Review
ISSN 0013-2845 September 2015 Railway Technology ETR Review INTERNATIONAL EDITION Planning ETCS Innovation in track components Inspection and maintenance Hybrid Drive Economic The next step - Ecologic Ergonomic The Hybrid Machine Sylomer® under-sleeper pads Use of Sylomer® under-sleeper pads to reduce ballast wear on a Scandi- navian heavy-haul railway line The heavy-haul railway line between Luleå and Narvik can conveniently be considered in two parts: the Swedish section (Malmbanan) and the Norwegian section (Ofotbanen). This line has been carrying continuously increasing loads, and so the infrastructure manager decided in 2014 to insert under-sleep- er pads as a means of improving the quality of the track geometry. This decision was influenced by the positive experience that the Austrian Federal Railways (ÖBB) had had with the use of pads under con- crete sleepers and also by projects such as Innotrack and RIVAS. This article contains a brief description of the Iron Ore Line in Scandinavia and the challenges due to heavy train loads. It also explains how under-sleeper pads work and describes the approaches tried out for switches and crossings. 1. OVERVIEW AND FACTS irunavaara Aktiebolag), the Swedish opera- Mag.(FH) Harald Steger Product management tor of the iron mines. These last-mentioned Getzner Werkstoffe GmbH Malmbanan is a railway line providing a trains can have up to 68 wagons with an axle [email protected] route for heavy freight trains in the north of load of 30 t and they run over Malmbanan Scandinavia, linking the sea ports of Luleå at 60 km/h in a laden state and at 70 km/h if (Sweden) and Narvik (Norway). -
HSL Report Template. Issue 1. Date 04/04/2002
Harpur Hill, Buxton, SK17 9JN Telephone: 01298 218000 Facsimile: 01298 218590 E Mail: [email protected] A survey of UK tram and light railway systems relating to the wheel/rail interface FE/04/14 Project Leader: E J Hollis Author(s): E J Hollis PhD CEng MIMechE Science Group: Engineering Control DISTRIBUTION HSE/HMRI: Dr D Hoddinott Customer Project Officer/HM Railway Inspectorate Mr E Gilmurray HIDS12F Research Management LIS (9) HSL: Dr N West HSL Operations Director Dr M Stewart Head of Field Engineering Section Author PRIVACY MARKING: D Available to the public HSL report approval: Dr M Stewart Date of issue: 14 March 2006 Job number: JR 32107 Registry file: FE/05/2003/21511 (Box 433) Electronic filename: Report FE-04-14.doc © Crown Copyright (2006) ACKNOWLEDGEMENTS To the people listed below, and their colleagues, I would like to express my thanks for all for the help given: Blackpool Borough Council Brian Vaughan Blackpool Transport Ltd Bill Gibson Croydon Tramlink Jim Snowdon Dockland Light Railway Keith Norgrove Manchester Metrolink Steve Dale Tony Dale Mark Howard Mark Terry (now with Rail Division of Mott Macdonald) Midland Metro Des Coulson Paul Morgan Fred Roberts Andy Steel (retired) National Tram Museum David Baker Geoffrey Claydon Mike Crabtree Allan Smith Nottingham Express Transit Clive Pennington South Yorkshire Supertram Ian Milne Paul Seddon Steve Willis Tyne & Wear Metro (Nexus) Jim Davidson Peter Johnson David Walker Parsons Brinkerhoff/Permanent Way Institution Joe Brown iii Manchester Metropolitan University Simon Iwnicki Julian Snow Paul Allen Transdev Edinburgh Tram Andy Wood HM Railway Inspectorate Dudley Hoddinott Dave Keay Ian Raxton iv CONTENTS 1 Introduction............................................................................................................. -
Engineering Specification Concrete Sleepers
ENGINEERING SPECIFICATION CONCRETE SLEEPERS CRN CP 232 Version: 1.2 Owner: Manager Engineering Services Approved by: M Wright, Principal Track and Civil Engineer Authorised by: J Zeaiter, Manager Engineering Services CRN Engineering Specification - Track CRN CP 232] Concrete Sleepers Document control Revision Date of Approval Summary of change 1.0 January, 2012 First Issue. Includes content from the following former RIC standards: C 3109 1.1 May, 2016 Various - Changed wording for consistency of presentation; 2.1 - Updated standards references to remove dates; 4.2 - Correction of format error 1.2 April, 2019 See Summary of changes below Summary of changes from previous version Section Summary of change Various Rebranded to the new JHG style 4 Alignment of layout with CRN CP 234 Disclaimer. This document was prepared for use on the CRN Network only. John Holland Rail Pty Ltd makes no warranties, express or implied, that compliance with the contents of this document shall be sufficient to ensure safe systems or work or operation. It is the document user’s sole responsibility to ensure that the copy of the document it is viewing is the current version of the document as in use by JHR. JHR accepts no liability whatsoever in relation to the use of this document by any party, and JHR excludes any liability which arises in any manner by the use of this document. Copyright. The information in this document is protected by Copyright and no part of this document may be reproduced, altered, stored or transmitted by any person without the prior consent of JHG. -
Evolution of the Re System Two Clips and a Flat Pad) the New Design from Pandrol Featured Just Three Components; Two Clips with a Toe Insulator Per Rail Seat
Maximising uptime DEVELOPMENT PROCESS The original Re System was introduced in 2012 as a replacement for the Pandrol e-Clip on older types of sleeper. Instead of having five components (two separate insulators, Evolution of the Re System two clips and a flat pad) the new design from Pandrol featured just three components; two clips with a toe insulator per rail seat. With the Re System, the rail pad is supplied with the Reducing the cost of installing rail fastenings and improving side post insulators already attached, which reduces time safety during the re-railing process are a constant focus and labour costs when laying out and installing the for Pandrol’s R&D team. In 2012, Pandrol developed the components on site. Re System, a rail fastening that not only delivers significant The system is also supplied with toe insulators already in place savings in manpower during the re-railing process, but also on the toe of the clip, again reducing installation time and the number of loose components on site. The design improves improves the durability of the rail fastening components rail threading and clipping rates and this leads directly to a installed on older types of concrete or steel sleepers. In reduced manpower requirement on re-railing sites. 2018 the system was evolved with the development of a The Re System also adopts the two-part insulator concept that version for the UK’s F40 sleeper. was developed with the Pandrol Fastclip system. The separate parts can be made from the same or different materials to further tune track performance. -
Toughness of Railroad Concrete Crossties with Holes and Web Openings
infrastructures Technical Note Toughness of Railroad Concrete Crossties with Holes and Web Openings Erosha K. Gamage 1, Sakdirat Kaewunruen 1,2,*, Alex M. Remennikov 3 and Tetsuya Ishida 4 1 Department of Civil Engineering, School of Engineering, The University of Birmingham, Edgbaston B15 2TT, UK; [email protected] 2 Birmingham Centre for Railway Research and Education, School of Engineering, The University of Birmingham, Edgbaston B15 2TT, UK 3 School of Civil, Mining, and Environmental Engineering, University of Wollongong, Northfield Ave, Wollongong, NSW 2522, Australia; [email protected] 4 Concrete Laboratory, Department of Civil Engineering, University of Tokyo, 7 Chome-3-1 Hongo, Bunkyo, Tokyo 113-8656, Japan; [email protected] * Correspondence: [email protected]; Tel.: +44-121-414-2670 Academic Editors: Higinio González Jorge and Pedro Arias-Sánchez Received: 30 June 2016; Accepted: 6 January 2017; Published: 11 January 2017 Abstract: Prestressed concrete sleepers (or railroad ties) are principally designed in order to carry wheel loads from the rails to the ground of railway tracks, as well as to secure rail gauge for safe train travels. Their design takes into account static and dynamic loading conditions. In spite of prestressed concrete crossties being most commonly used in railway tracks, there have always been many demands from rail engineers to improve the serviceability and functionality of concrete crossties. For example, signaling, fiber optic, equipment cables are often damaged either by ballast corners or by the tamping machine. There has been a need to re-design concrete crossties to incorporate cables internally so that they would not experience detrimental or harsh environments. -
University of Birmingham Asymmetrical Effects on Railway
University of Birmingham Asymmetrical effects on railway turnout bearers due to wheelset impact over a crossing nose Kaewunruen, Sakdirat; Ngamkhanong, Chayut; Goto, Keiichi; Janeliukstis, Rims DOI: 10.5592/CO/CETRA.2018.664 License: Creative Commons: Attribution (CC BY) Document Version Publisher's PDF, also known as Version of record Citation for published version (Harvard): Kaewunruen, S, Ngamkhanong, C, Goto, K & Janeliukstis, R 2018, Asymmetrical effects on railway turnout bearers due to wheelset impact over a crossing nose. in The 5th International Conference on Road and Rail Infrastructure. University of Zagreb, pp. 623-629, The 5th International Conference on Road and Rail Infrastructure , Zadar, Croatia, 17/05/18. https://doi.org/10.5592/CO/CETRA.2018.664 Link to publication on Research at Birmingham portal Publisher Rights Statement: Checked for eligibility: 24/05/2018 "Authors retain copyright over their work, while allowing the conference to place this unpublished work under a Creative Commons Attribution License, which allows others to freely access, use, and share the work, with an acknowledgement of the work's authorship and its initial presentation at this conference." General rights Unless a licence is specified above, all rights (including copyright and moral rights) in this document are retained by the authors and/or the copyright holders. The express permission of the copyright holder must be obtained for any use of this material other than for purposes permitted by law. •Users may freely distribute the URL that is used to identify this publication. •Users may download and/or print one copy of the publication from the University of Birmingham research portal for the purpose of private study or non-commercial research. -
Prestressed Concrete Sleepers
AS 1085.14:2019 Railway track material Part 14: Prestressed concrete sleepers Infrastructure Standard Please note this is a RISSB Australian Standard Draft Document content exists for RISSB product development purposes only and should not be relied upon or considered as final published content. Any questions in relation to this document or RISSB’s accredited development process should be referred to RISSB. RISSB Office Phone: Email: Web: (07) 7 3724 0000 [email protected] www.rissb.com.au Overseas: +61 7 3724 0000 AS 1085.14:2019 Railway track material Part 14: Prestressed concrete sleepers Assigned Development Manager Name: Anthony McDermott Phone: (07) 3724 0000 Email: [email protected] AS 1085.14:2019 Railway track material Part 14: Prestressed concrete sleepers This Australian Standard® AS 1085.14 Railway track material Part 14: Prestressed concrete sleepers was prepared by a Rail Industry Safety and Standards Board (RISSB) Development Group consisting of representatives from the following organisations: Click here to enter the organisations represented on the Development Group. Tab between them. The Standard was approved by the Development Group and the Enter Standing Committee Standing Committee in Select SC approval date. On Select Board approval date the RISSB Board approved the Standard for release. Choose the type of review Development of the Standard was undertaken in accordance with RISSB’s accredited process. As part of the approval process, the Standing Committee verified that proper process was followed in developing the Standard. RISSB wishes to acknowledge the positive contribution of subject matter experts in the development of this Standard. Their efforts ranged from membership of the Development Group through to individuals providing comment on a draft of the Standard during the open review. -
Track Modulus Assessment of Engineered Interspersed Concrete Sleepers in Ballasted Track
applied sciences Article Track Modulus Assessment of Engineered Interspersed Concrete Sleepers in Ballasted Track Arthur de Oliveira Lima, Marcus S. Dersch, Jaeik Lee and J. Riley Edwards * Rail Transportation and Engineering Center—RailTEC, Department of Civil and Environmental Engineering-CEE, University of Illinois at Urbana-Champaign—UIUC, 205 N. Mathews Ave., MC-250, Urbana, IL 61801, USA; [email protected] (A.d.O.L.); [email protected] (M.S.D.); [email protected] (J.L.) * Correspondence: [email protected] Abstract: Ballasted railway track is typically constructed using sleepers that are manufactured from a common material type within a given length of track. Timber and concrete are the two most common sleeper materials used internationally. Evidence from historical installations of interspersed concrete sleepers in timber sleeper track in North America has indicated inadequate performance, due largely to the heterogeneity in stiffnesses among sleepers. Theoretical calculations reveal that interspersed installation, assuming rigid concrete sleepers and supports, can result in rail seat forces more than five times as large as the force supported by the adjacent timber sleepers. Recently, engineered interspersed concrete (EIC) sleepers were developed using an optimized design and additional layers of resiliency to replace timber sleepers that have reached the end of their service lives while maintain- ing sleeper-to-sleeper stiffness homogeneity. To confirm that the concrete sleepers can successfully replicate the stiffness properties of the timber sleepers installed in track, field instrumentation was installed under revenue-service train operations on a North American commuter rail transit agency to measure the wheel–rail vertical loads and track displacement. The results indicated that there are minimal differences in median track displacements between timber (2.26 mm, 0.089 in.) and EIC sleepers (2.21 mm, 0.087 in). -
Concrete Sleeper Design, Process & Delivery Solutions
CONCRETE SLEEPER DESIGN, PROCESS & DELIVERY SOLUTIONS 1 SAFety, QUAlity, sustAinABility, innovAtion And EMployee trAining Are THE cornerstones OF AustrAK’S SUCCESS THE COMPANY Since its establishment in 1980, Austrak We have produced more than 18 million As a wholly-owned subsidiary of major has grown to become a world leader in the sleepers for medium and heavy duty rail, international construction company design and manufacture of pre-stressed and 800,000 sleepers for light rail and Laing O’Rourke, Austrak has the concrete sleepers. tramways. Over this time, we’ve created a backing of the largest privately owned broad range of products designed to meet construction firm in the United Kingdom. During more than 30 years of business, the varying needs of the rail industry. Laing O’Rourke provides Austrak with Austrak has cemented its place as the the backing of a global, multi-billion dollar largest concrete sleeper manufacturer Austrak partners with Swedish innovator organisation with operations in Europe, the and supplier in Australia. As a dedicated Abetong Teknik – a close relationship Middle East and Australasia. sleeper technology company our focus that enables the transfer of world-leading remains on achieving the best in sleeper technology and knowledge. Working Creativity, flexibility and an aligned focus design and manufacture. closely together, we ensure any new towards joint goals encapsulate Austrak’s developments in the field are quickly added business approach. Safety, quality, sustainability, to our available designs. innovation and employee training are the cornerstones of Austrak’s capability. As well as providing these pre-existing Working in close partnership with clients lines, we can work in partnership with provides an environment for driving clients to create new products that are innovation and change.