Project Magnet Pit to Port PCS Implementation
Total Page:16
File Type:pdf, Size:1020Kb
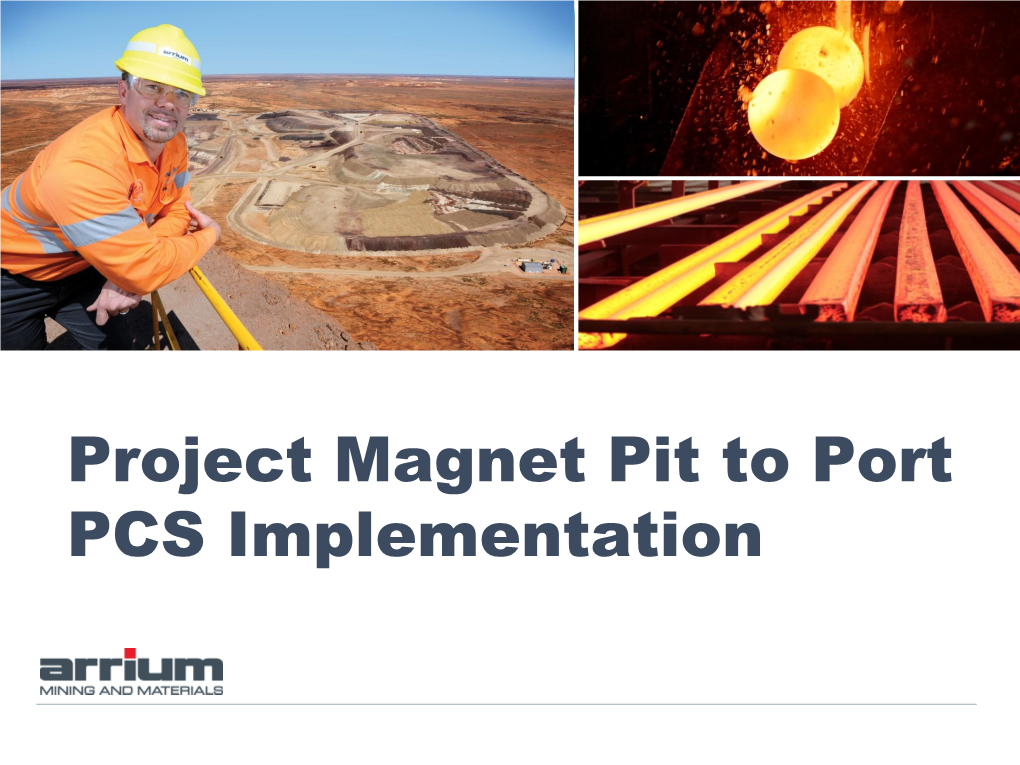
Load more
Recommended publications
-
MARLA-OODNADATTA DISTRICT PROFILE: Characteristics4 and Challenges1,2
MARLA-OODNADATTA DISTRICT PROFILE: Characteristics4 and challenges1,2 South Australian Arid Lands NRM region Marla ABOUT THE MARLA- Oodnadatta OODNADATTA DISTRICT Algebuckina Innamincka Moomba The Marla-Oodnadatta Marla-Oodnadatta Marree-Innamincka district covers an area of Anna Creek approximately 132,000 Coober Pedy square kilometres (12% Coward Springs of South Australia in Curdimurka the north-west pastoral Marree region and is bounded Arkaroola Village Kingoonya by the Simpson Desert Andamooka Tarcoola Roxby Downs Leigh Creek and Lake Eyre to the Kingoonya Glendambo North Flinders Ranges east, the Great Victoria Woomera Desert to the west and Parachilna the Northern Territory border to the north. Hawker Gawler Ranges Legend North East Olary Port Augusta Iron Knob Waterways and Lakes Yunta Iron Baron National Parks and Reserves Whyalla Dog Fence COMMUNITIES VEGETATION WATER The permanent population of the district Major vegetation types include: The Great Artesian Basin provides an is approximately 2,000 people. Townships Plains: Mitchell grass, glassworts, poverty important source of water within the include Coober Pedy, Marla, Oodnadatta bush, saltbush, cannonball, neverfail, district. Natural venting occurs in the form and William Creek. bluebush, sea heath, samphire, twiggy sida, of mound springs, found predominately cottonbush, copper burr, pigface, prickly near the Oodnadatta Track. Waterholes CLIMATE wattle, mulga, lignum, cane grass. are found along major and minor drainage lines, some with the capacity to hold water The climate of the district is very arid Sandplains: Mulga, senna, marpoo, emu for over 12 months. with hot to extremely hot summers and bush, woollybutt, sandhill canegrass, mild, dry winters. Average annual rainfall copper burr, corkwood, dead finish, ranges between 120mm to 210mm across bluebush, saltbush. -
Mining in South Australia the AUSTLIAN MINING REVIEW
OCTOBER 2016 20 MINING IN SOUTH AUSTRALIA THE AUSTLIAN MINING REVIEW BHP Billiton’s world-class Olympic Dam project. Image: BHP Billiton. A bright future Home to 68 per cent of the nation’s copper and 25 per cent of the world’s known uranium, South Australia’s resources industry is an irrefutable force. Additional State Government support, which aims to kick-start investment and sector growth, reflects its importance. ELIZABETH FABRI SOUTH Australia, affectionately known as the ‘Copper Kingdom’, has been a key contributor to Australia’s mining industry as far back as the 1800s, and today boasts the world’s largest uranium deposit and the country’s largest underground mine, Olympic Dam. In 2014/15 the State’s minerals and petroleum sector had a gross value of product at $5.958 billion and regionally the industry contributed a gross regional product of $6.377bn. While established operations are peppered across the State, the region maintains more than 700 exploration licenses and more than 20 advanced projects in exploration, feasibility and resource definition phases, signifying great promise for the future. In addition to copper and uranium, commodities such as iron ore, gold, graphite, zinc and zircon are generating interest. However, the fate of the sector is resting on a rapid solution to the high energy prices experienced across the State in recent years. The Whyalla steelworks operation is a recipient of State budget funding. Image: Arrium. Photography Sean Kelly. “At this point in time electricity is the number one, two and three thing that needs dollars to be put into South Australia.” a globally competitive resources sector, the community of Whyalla. -
Genesee & Wyoming Inc. 2016 Annual Report
Genesee & Wyoming Inc. 2016 Annual Report Genesee & Wyoming Inc.*owns or leases 122 freight railroads worldwide that are organized into 10 operating regions with approximately 7,300 employees and 3,000 customers. * The terms “Genesee & Wyoming,” “G&W,” “the company,” “we,” “our,” and “us” refer collectively to Genesee & Wyoming Inc. and its subsidiaries and affiliated companies. Financial Highlights Years Ended December 31 (In thousands, except per share amounts) 2012 2013 2014 2015 2016 Statement of Operations Data Operating revenues $874,916 $1,568,643 $1,639,012 $2,000,401 $2,001,527 Operating income 190,322 380,188 421,571 384,261 289,612 Net income 52,433 271,296 261,006 225,037 141,096 Net income attributable to Genesee & Wyoming Inc. 48,058 269,157 260,755 225,037 141,137 Diluted earnings per common share attributable to Genesee & Wyoming Inc. common stockholders: Diluted earnings per common share (EPS) $1.02 $4.79 $4.58 $3.89 $2.42 Weighted average shares - Diluted 51,316 56,679 56,972 57,848 58,256 Balance Sheet Data as of Period End Total assets $5,226,115 $5,319,821 $5,595,753 $6,703,082 $7,634,958 Total debt 1,858,135 1,624,712 1,615,449 2,281,751 2,359,453 Total equity 1,500,462 2,149,070 2,357,980 2,519,461 3,187,121 Operating Revenues Operating Income Net Income Diluted Earnings ($ In Millions) ($ In Millions) ($ In Millions) 421.61,2 Per Common Share 2 2,001.5 401.6 1 $2,000 2,000.4 $400 394.12 $275 271.3 $5.00 1 2 4.79 1 374.3 1 380.21 384.3 261.0 4.581 1,800 250 4.50 350 1,639.0 225.01 225 2 1 1,600 233.5 4.00 2 3.89 1,568.6 4.10 2 300 2 200 213.9 213.3 2 3.78 2 1,400 1 3.50 3.69 289.6 183.32 3.142 250 175 1,200 3.00 211. -
THE MAKING of the NEWCASTLE INDUSTRIAL HUB 1915 to 1950
THE MAKING OF THE NEWCASTLE INDUSTRIAL HUB 1915 to 1950 Robert Martin Kear M.Bus. (University of Southern Queensland) A thesis submitted in fulfilment of the requirements for the degree of a Master of Philosophy in History January 2018 This research was supported by an Australian Government Research Training Program (RTP) Scholarship STATEMENT OF ORIGINALITY I hereby certify that the work embodied in the thesis is my own work, conducted under normal supervision. The thesis contains no material which has been accepted, or is being examined, for the award of any other degree or diploma in any other university or other tertiary institution and, to the best of my knowledge and belief, contains no material previously published or written by another person, except where due reference has been made in the text. I give consent to the final version of my thesis being made available worldwide when deposited in the University’s Digital Repository, subject to the provisions of the Copyright Act 1968 and any approved embargo. Robert Kear ii ABSTRACT Aim of this Thesis The aim of this thesis is to chart the formation of the Newcastle Industrial Hub and to identify the men who controlled it, in its journey from Australian regional obscurity before 1915, to be the core of Australian steel manufacturing and technological development by 1950. This will be achieved through an examination of the progressive and consistent application of strategic direction and the adoption of manufacturing technologies that progressively lowered the manufacturing cost of steel. This thesis will also argue that, coupled with tariff and purchasing preferences assistance, received from all levels of government, the provision of integrated logistic support services from Newcastle’s public utilities and education services underpinned its successful commercial development. -
Key Railway Crossings Overlay 113411.4 94795 ! Port Augusta ! !
N O R T H E R N T E R R I T O R Y Amata ! Kalka Kanpi ! ! Nyapari Pipalyatjara ! ! Pukatja ! Yunyarinyi ! Umuwa ! QUEENSLAND Kaltjiti ! !113411.4 94795 Indulkana ! Mimili ! Watarru ! 113411.4 94795 Mintabie ! ! ! Marla Oodnadatta ! Innamincka Cadney Park ! ! Moomba ! WESTERN AUSTRALIA William Creek ! Coober Pedy ! Oak Valley ! Marree ! ! Lyndhurst Arkaroola ! Andamooka ! Roxby Downs ! Copley ! ! Nepabunna Leigh Creek ! Tarcoola ! Beltana ! 113411.4 94795 !! 113411.4 94795 Kingoonya ! Glendambo !113411.4 94795 Parachilna ! ! Blinman ! Woomera !!113411.4 94795 Pimba !113411.4 94795 Nullarbor Roadhouse Yalata ! ! ! Wilpena Border ! Village ! Nundroo Bookabie ! Coorabie ! Penong ! NEW SOUTH WALES ! Fowlers Bay FLINDERS RANGES !113411.4 94795 Planning and Design Code ! 113411.4 94795 ! Ceduna CEDUNA Cockburn Mingary !113411.4 94795 ! ! Phase 1 !113411.4 94795 Olary ! Key Railway Crossings Overlay 113411.4 94795 ! Port Augusta ! ! !113411.4 94795 Manna Hill ! STREAKY BAY Key Railway Crossings Yunta ! Iron Knob Railway MOUNT REMARKABLE ± Phase 1 extent PETERBOROUGH 0 50 100 150 km Iron Baron ! !!115768.8 17888 WUDINNA WHYALLA KIMBA Whyalla Produced by Department of Planning, Transport and Infrastructure Development Division ! GPO Box 1815 Adelaide SA 5001 Port Pirie www.sa.gov.au NORTHERN Projection Lambert Conformal Conic AREAS Compiled 11 January 2019 © Government of South Australia 2019 FRANKLIN No part of this document may be reproduced, stored in a retrieval system, or transmitted PORT in any form, or by any means, without the prior written permission of the publisher, HARBOUR Department of Planning, Transport and Infrastructure. PIRIE ELLISTON CLEVE While every reasonable effort has been made to ensure that this document is correct at GOYDER the time of publication, the State of South Australia and its agencies, instrumentalities, employees and contractors disclaim any and all liability to any person in respect to anything or the consequence of anything done or omitted to be done in reliance upon the whole or any part of this document. -
Meeting Details Report
Voting report for the period 1 July 2015 to 31 December 2015 Meeting Date ASX Code Company Name Summary CareSuper Vote 7/07/15 INT INT Corporation Limited Approve the Consolidation of Shares and Options For 7/07/15 INT INT Corporation Limited Approve the Change in Nature and Scale of the Company's Activities For 7/07/15 INT INT Corporation Limited Approve the Acquisition of Relevant Interest For 7/07/15 INT INT Corporation Limited Approve the Issuance of Consideration Securities to Non-Related Party Investors For 7/07/15 INT INT Corporation Limited Approve the Issuance of Consideration Shares to Shauna Mei For 7/07/15 INT INT Corporation Limited Approve the Issuance of Consideration Securities to Sachin Devand For 7/07/15 INT INT Corporation Limited Approve the Executive and Employee Incetive Plan For 7/07/15 INT INT Corporation Limited Approve the Issuance of Incentive Securities to Shauna Mei, Director of the Company For 7/07/15 INT INT Corporation Limited Approve the Issuance of Incentive Securities to Sachin Devand, Director of the Company For 7/07/15 INT INT Corporation Limited Approve the Grant of 44.44 Million New Shares to Investors For 7/07/15 INT INT Corporation Limited Approve the Grant of 166,667 New Shares to Mike Hill, Director of the Company For 7/07/15 INT INT Corporation Limited Elect Shauna Mei as Director For 7/07/15 INT INT Corporation Limited Elect Sachin Devand as Director For 7/07/15 INT INT Corporation Limited Approve the Change of Company Name to AHAlife Holdings Limited For 14/07/15 CSR Csr Ltd. -
PGI Annual 2012
PRINCIPAL GLOBAL INVESTORS FUNDS An umbrella trust governed by the laws of Ireland Annual Report and Audited Financial Statements For the year ended 30 September 2012 PRINCIPAL GLOBAL INVESTORS FUNDS ANNUAL REPORT AND AUDITED FINANCIAL STATEMENTS FOR THE YEAR ENDED 30 SEPTEMBER 2012 CONTENTS General Information ............................................................................................................................................................. 3 Investment Adviser’s Report ........................................................................................................................................... 5 Independent Auditor’s Report ................................................................................................................................... 12 Trustee’s Report ..................................................................................................................................................................... 14 Statement of Manager’s and Trustee’s Responsibilities ........................................................................... 15 Portfolio of Investments Global Equity Fund ................................................................................................................................................... 16 Asian Equity Fund ...................................................................................................................................................... 18 European Equity Fund ........................................................................................................................................... -
Regolith-Landforms and Plant Biogeochemical Expression of Buried Mineralisation Targets in the Northern Middleback Ranges, (“Iron Knob South”) South Australia
Regolith-Landforms and plant biogeochemical expression of buried mineralisation targets in the Northern Middleback Ranges, (“Iron Knob South”) South Australia Louise Thomas Geology and Geophysics, School of Earth and Environmental Science, University of Adelaide, Adelaide SA 5005, Australia A manuscript submitted for the Honours Degree of Bachelor of Science, University of Adelaide, 2011 Supervised by Dr. Steven M. Hill 2 ABSTRACT South of the town Iron Knob on the northern Eyre Peninsula, a tenement scale plant biogeochemical survey and regolith-landform mapping, combined to define areas with elevated Cu, Zn and Au contents that are worthy of follow-up exploration. Plant biogeochemistry was conducted within a 6 Km2 area with 1 Km spacing between each E-W trending transect and 200 m spacing between each sample. A regolith-landform map presents the distribution of regolith materials and associated landscape processes to help constrain geochemical dispersion. A Philips XL30 SEM provided insight into how the plants uptake certain elements and distribute them within the organs structure. Two zones of elevated trace metals (e.g. Cu, Au and Zn) were defined either side of a NW-SE structure crossing over the N-S trending „Katunga‟ ridge. Both targets were located on similar regolith-landform units of sheet-flood fans and alluvial plains. Copper and Zn results were best represented by the western myall species while the bluebush species was best at detecting Au. A follow up study targeting the NW-SE structure with closer sample spacing is recommended in further constraining drilling targets. For the tenement holding company, Onesteel Ltd, these results are significant as they define two new areas of interest for possible IOCG mineralisation. -
Business Leadership: the Catalyst for Accelerating Change
BUSINESS LEADERSHIP: THE CATALYST FOR ACCELERATING CHANGE Follow us on twitter @30pctAustralia OUR OBJECTIVE is to achieve 30% of ASX 200 seats held by women by end 2018. Gender balance on boards does achieve better outcomes. GREATER DIVERSITY ON BOARDS IS VITAL TO THE GOOD GOVERNANCE OF AUSTRALIAN BUSINESSES. FROM THE PERSPECTIVE OF PERFORMANCE AS WELL AS EQUITY THE CASE IS CLEAR. AUSTRALIA HAS MORE THAN ENOUGH CAPABLE WOMEN TO EXCEED THE 30% TARGET. IF YOUR BOARD IS NOT INVESTING IN THE CAPABILITY THAT DIVERSITY BRINGS, IT’S NOW A MARKED DEPARTURE FROM THE WHAT THE INVESTOR AND BROADER COMMUNITY EXPECT. Angus Armour FAICD, Managing Director & Chief Executive Officer, Australian Institute of Company Directors BY BRINGING TOGETHER INFLUENTIAL COMPANY CHAIRS, DIRECTORS, INVESTORS, HEAD HUNTERS AND CEOs, WE WANT TO DRIVE A BUSINESS-LED APPROACH TO INCREASING GENDER BALANCE THAT CHANGES THE WAY “COMPANIES APPROACH DIVERSITY ISSUES. Patricia Cross, Australian Chair 30% Club WHO WE ARE LEADERS LEADING BY EXAMPLE We are a group of chairs, directors and business leaders taking action to increase gender diversity on Australian boards. The Australian chapter launched in May 2015 with a goal of achieving 30% women on ASX 200 boards by the end of 2018. AUSTRALIAN 30% CLUB MEMBERS Andrew Forrest Fortescue Metals Douglas McTaggart Spark Group Ltd Infrastructure Trust Samuel Weiss Altium Ltd Kenneth MacKenzie BHP Billiton Ltd John Mulcahy Mirvac Ltd Stephen Johns Brambles Ltd Mark Johnson G8 Education Ltd John Shine CSL Ltd Paul Brasher Incitec Pivot -
Growth in All the Right Places
Monday 18 May 2015 Growth in all the right places I want the negativity to stop now! There are some great things in this Budget for growth and if we all just get on with it, the economy might actually do better, which would be good for growth and good for stocks. Today I mention a few that are particularly set to do well. Also today, Tony Featherstone breaks down the BHP spinoff South32 and examines whether you should hold it and potentially buy more now, or later when all the institutional activity has died down. James Dunn has 5 remarkable REITs and Paul Rickard shares everything you need to know for a sector review. Buy, Sell, Hold – what the brokers say, has upgrades for ALS and Sirtex and our Super Stock Selectors single out Dulux and Hansen Technologies. Sincerely, Peter Switzer Inside this Issue 02 3 arguments for buying South32 by Tony Featherstone 05 Joe’s Viagra Budget will help these stocks by Peter Switzer 07 Everything you need to know for a sector update by Paul Rickard 10 5 remarkable REITs by James Dunn 13 Buy, Sell, Hold – what the brokers say 3 arguments for buying by Rudi Filapek-Vandyck South32 16 Shortlisted – Super Stock Selectors by Tony Featherstone by Penny Pryor 18 Steady as she goes for property 02 by Switzer Super Report Important information: This content has been prepared without taking account of the objectives, financial situation or needs of any particular individual. It does Switzer Super Report is published by Switzer Financial Group Pty Ltd AFSL No. -
Derailment of Ore Train 24KW Near Whyalla, South Australia, 7 July 2014
DerailmentInsert document of ore train title 24KW Locationnear Whyalla, | Date South Australia | 7 July 2014 ATSB Transport Safety Report Investigation [InsertRail Occurrence Mode] Occurrence Investigation Investigation XX-YYYY-####RO-2014-012 Final – 28 April 2015 Front cover: ATSB Released in accordance with section 25 of the Transport Safety Investigation Act 2003 Publishing information Published by: Australian Transport Safety Bureau Postal address: PO Box 967, Civic Square ACT 2608 Office: 62 Northbourne Avenue Canberra, Australian Capital Territory 2601 Telephone: 1800 020 616, from overseas +61 2 6257 4150 (24 hours) Accident and incident notification: 1800 011 034 (24 hours) Facsimile: 02 6247 3117, from overseas +61 2 6247 3117 Email: [email protected] Internet: www.atsb.gov.au © Commonwealth of Australia 2015 Ownership of intellectual property rights in this publication Unless otherwise noted, copyright (and any other intellectual property rights, if any) in this publication is owned by the Commonwealth of Australia. Creative Commons licence With the exception of the Coat of Arms, ATSB logo, and photos and graphics in which a third party holds copyright, this publication is licensed under a Creative Commons Attribution 3.0 Australia licence. Creative Commons Attribution 3.0 Australia Licence is a standard form license agreement that allows you to copy, distribute, transmit and adapt this publication provided that you attribute the work. The ATSB’s preference is that you attribute this publication (and any material sourced from it) using the following wording: Source: Australian Transport Safety Bureau Copyright in material obtained from other agencies, private individuals or organisations, belongs to those agencies, individuals or organisations. -
Arrium Mining GMUSG Gavin Hobart, General Manager Development
Arrium Mining GMUSG Gavin Hobart, General Manager Development 21 August 2013 This presentation contains certain forward-looking statements with respect to the financial condition, results of operations and business of Arrium and certain plans and objectives of the management of Arrium. Forward-looking statements can generally be identified by the use of words such as ‘project’, ‘foresee’, ‘plan’, ‘expect’, ‘aim’, ‘intend’, ‘anticipate’, ‘believe’, ‘estimate’, ‘may’, ‘should’, ‘will’ or similar expressions. All such forward looking statements involve known and unknown risks, significant uncertainties, assumptions, contingencies and other factors, many of which are outside the control of Arrium, which may cause the actual results or performance of Arrium to be materially different from any future results or performance expressed or implied by such forward looking statements. Such forward-looking statements speak only as of the date of this presentation. Factors that could cause actual results or performance to differ materially include without limitation the following: risks and uncertainties associated with the Australian and global economic environment and capital market conditions,TITLE the TEXT cyclical nature of the steel industry, the level of activity in the construction, manufacturing, mining, agricultural and automotive industries in Australia and North and South America and, to a lesser extent, the same industries in Asia and New Zealand, mining activity in the Americas, commodity price fluctuations, fluctuations in foreign currency exchange and interest rates, competition, Arrium's relationships with, and the financial condition of, its suppliers and customers, legislative changes, regulatory changes or other changes in the laws which affect Arrium's business, including environmental laws, a carbon tax, proposed mining tax and operational risk.