Article Full Text PDF (3.17
Total Page:16
File Type:pdf, Size:1020Kb
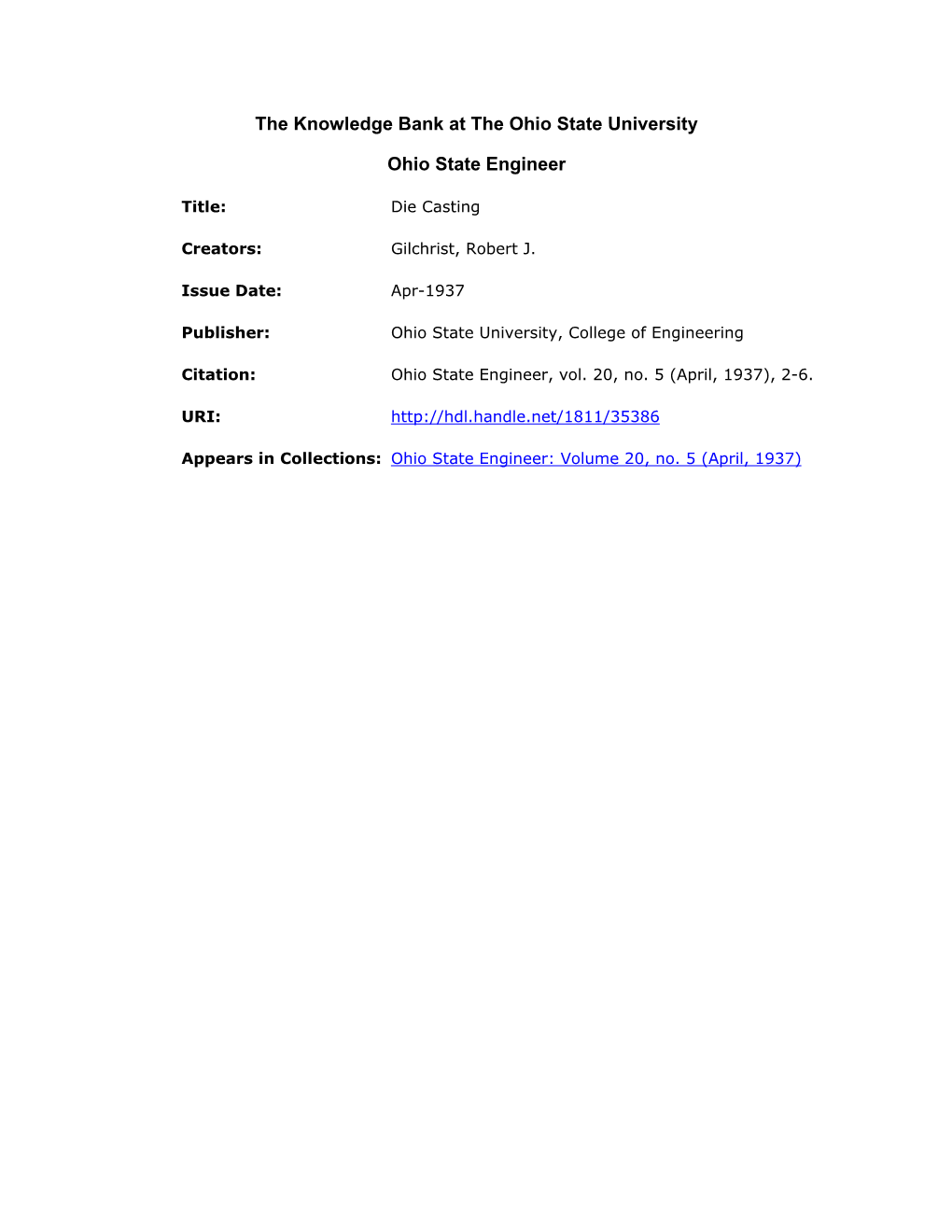
Load more
Recommended publications
-
Coating Research for Zinc Die Casting Alloys
A PERFORMANCE EVALUATION OF MODERN SURFACE FINISHES FOR ZINC DIE CASTINGS otects! Pr Zinc A PERFORMANCE EVALUATION OF MODERN SURFACE FINISHES FOR ZINC DIE CASTINGS Why Zinc Castings Zinc die castings are a unique choice for count- less decorative and functional applications. Zinc is a relatively dense metal, which has a feel of “substance” and durability. Zinc casting alloys are also stronger than all but the most highly rein- forced molded polymers. Zinc’s hardness, self lubricating properties, dimensional stability and The Study high modulus makes it suitable for work- The following information is from results of an ing mechanical parts, such as gears and investigation1,2 conducted by the International pinions, that would be less durable if Lead Zinc Research Organization (ILZRO) to eval- molded from polymers. Zinc can be die uate the performance of modern protective and cast at moderate temperatures thus pro- decorative finishes commonly used on zinc die viding significant energy and processing castings. The investigation was performed by the savings over other metals and engineer- Corrosion and Materials Research Institute ing alloys. Zinc also accepts a broad (CAMRI) in Newark, Delaware. assortment of finishes, from chemical conversion treatments to electroplating The ILZRO study described here provides a com- to sprayed and baked polymers. parison of the performance of different finishes used to protect and provide an aesthetic finish When a finish is properly selected and to zinc die castings. The study looked at two dif- applied to die cast zinc, almost any ferent performance criteria – the ability of a fin- desired aesthetic characteristic and coat- ish to protect the underlying zinc against corro- ing durability can be achieved. -
2009 International Nuclear Atlantic Conference
2009 International Nuclear Atlantic Conference - INAC 2009 Rio de Janeiro,RJ, Brazil, September27 to October 2, 2009 ASSOCIAÇÃO BRASILEIRA DE ENERGIA NUCLEAR - ABEN ISBN: 978-85-99141-03-8 ZAMAK SAMPLES ANALYSES USING EDXRF J. T. de Assis¹, H. Alves³, I. Lima¹, V. Monin¹, M. dos Anjos²,³, R. T. Lopes² (1) Departamento de Engenharia Mecânica e Energia, Instituto Politécnico, UERJ Rua Alberto Rangel, s/n, Nova Friburgo, RJ, Brazil {[email protected]} {[email protected]} {[email protected]} (2) Laboratório de Instrumentação Nuclear, PEN. COPPE/UFRJ Cidade Universitária, Rio de Janeiro, RJ, Brazil {[email protected]} (3) Departamento de Física Aplicada e Termodinâmica, IF/UERJ Rua São Francisco Xavier, 524, sala B3020, Rio de Janeiro, RJ, Brazil {[email protected]} {[email protected]} ABSTRACT Zamak is a family of alloys with a base metal of zinc and alloying elements of aluminium, magnesium and copper. Among all non-ferrous metal alloys, Zamak is one that has more applications, for their physical, mechanical properties and easy ability to electrodeposition. It has good resistance to corrosion, traction, shock and wear. Its low melting point (approximately 400 ° C) allows greater durability of the mold, allowing greater production of melted series parts. Zamak can be used in several kinds of areas, such as, to produce residential and industrial locks, construction and carpentry components, refrigerators hinges and so on. It’s observed that in some cases the quality of these products is not very good. The problem should be the quality of Zamak alloy purchased by the industries. One possible technique that can be used to investigate the quality of these alloys is Energy Dispersive X-ray fluorescence. -
General Rule of Phase Decomposition in Zn-Al Based Alloys (II) ---On
Materials Transactions, Vol. 45, No. 11 (2004) pp. 3083 to 3097 #2004 The Japan Institute of Metals OVERVIEW General Rule of Phase Decomposition in Zn-Al Based Alloys (II) —On Effects of External Stresses on Phase Transformation— Yao hua Zhu Department of Industrial and Systems Engineering, The Hong Kong Polytechnic University, Kowloon, Hong Kong, P.R. China Microstructural changes and phase transformation of Zn-Al based alloys (ZA alloys) were systematically investigated during various thermal and thermo-mechanical processes using X-ray diffraction (XRD), scanning electron microscopy (SEM), electron probe micro-analysis (EMPA), transmission electron microscopy (TEM), electron back-scattered diffraction (EBSD) and differential scanning calorimeter (DSC) etc. techniques. Phase decompositions of the alloys were studied under various thermal and thermo-mechanical circumstances. General rule of phase decomposition (II) (On effects of external stresses on phase transformation) was summarized with explanations from point view of Gibbs free energy. (Received April 19, 2004; Accepted September 6, 2004) Keywords: ageing, deformation, stress induced phase decomposition, zinc-aluminium based alloys 1. Introduction Zn-Al based alloys have been commercially accepted for many years, since the first casting alloy was developed at the New Jersey Zinc Company in 1922. The most popular die casting alloy used, ZAMAK 4 was the 898 alloy discovered in their series of alloy development. A new family of hyper- eutectic Zn-Al based alloys with high aluminum and copper contents was developed based on the ZAMAK alloys in North America and China in the 1970’s. The copper content was up to 3% (in mass%) and aluminum content were selected as about 8, 12, 22 and 27% (in mass%). -
Table 1 Properties of Zinc Alloys
TECHNICAL BULLETIN CORROSION RESISTANCE OF ZINC And Zinc Alloys CHEMICAL SPECIFICATIONS OF ZINC AND ZINC ALUMINUM ALLOYS: TABLE 1 PROPERTIES OF ZINC ALLOYS The Mechanical and physical properties of the castings, and to a lesser extent their corrosion properties, are closely linked to the specific alloy type, the casting process and quality of the castings produced, the amount of aging or service life of the component and the level of impurities, amongst others. Both CU and MG increase strength properties, reduce ductility and inhibit intergranular corrosion. Iron is present as small FeAl3 particles and does not influence mechanical properties unless it exceeds 0.1%. When limited to the specified amounts shown in ASTM B86 and B791, Pb, Sn, and Cd do not cause intergranular corrosion or the lowering of physical and mechanical properties. Higher levels of these impurities must be avoided. Other impurity elements, such as Cr, Ni, Mn, Th, In, Sb, As, Bi and Hg, do not normally occur in sufficient quantities in zinc casting alloys to be of concern. TABLE 1 CORROSION RESISTANCE All zinc – based alloys have excellent resistance to corrosion in a variety of environments. In general terms, the presence of aluminum in the alloys enhances the well-known corrosion resistance of zinc, which is the main constituent of the alloys. Many trials with the family of ZA alloys in particular were made in those environments where engineers requested specific data. Accelerated test results provide guidelines for assessing probable performance in other solutions or environments. Where specific data on Zamak alloys www.alliedmetalcompany.com is lacking, information on the corrosion properties of Special High Grade Zinc (99.99% pure) is provided as a guideline of the likely performance of Zamak alloy castings. -
Balen/Overpelt Smelter Belgium
Balen/Overpelt Smelter Belgium OVERVIEW Fast Facts The Balen smelter is one of the world’s largest zinc smelters in terms of production volume. TECHNOLOGY: roast, leach, electrolysis (RLE) smelting, oxide washing The Balen and Overpelt sites are only 18 kilometres apart. The sites’ PRODUCTS: special high grade (SHG) zinc, zinc alloys operations are complementary and highly integrated. Cathodes and sulphuric acid produced at Balen and Auby (France) are transported to the centralised melting & casting facilities in Overpelt. In addition, the PRODUCTION 2017: 249 kt zinc metal, 310 kt sulphuric Overpelt site includes one of Europe’s largest oxide washing facilities acid that serves as a central washing facility for the pre-treatment of EMPLOYEES: ~ 550 purchased secondaries prior to their consumption by the European Nyrstar smelters. The casting facilities in Overpelt include a state-of- the-art melting furnace and fully automated casting lines. The Balen smelter produces zinc from feedstock of both zinc concentrates and recycled zinc secondary feed materials. The Balen smelter can process a high percentage of secondary feed material input without adversely affecting overall plant productivity, efficiency or residue output. The Balen and Overpelt operations produce SHG zinc and a range of high value alloy products such as ZAMAK die casting alloy. Balen also produces sulphuric acid, copper cement and Balen Leach Product that contains lead and precious metals. Location The Balen smelter Overpelt operations are located in the northeast of Belgium, approximately 80 km east of Antwerp. Concentrates are transported by train from the port of Antwerp and secondary zinc feed materials are delivered to the plant by truck. -
Prop-65 Summary for Zinc Die Casting Alloys
REQUIREMENTS FOR LABELING ZINC- CONTAINING PRODUCTS UNDER CA PROP 65 REVIEW FINDS THAT PROP 65 LABELING FOR CADMIUM AND LEAD IS NOT REQUIRED FOR PRODUCTS MADE FROM ZINC DIE CASTING AND SHG ALLOYS MEETING ASTM SPECIFICATIONS INTRODUCTION California’s Safe Drinking Water and Toxic Enforcement Act of 1986, or Proposition 65 (Prop 65) requires producers and/or packagers of products sold in California to provide a clear and reasonable warning when their products and/or packaging contain a Prop 65 chemical, un- less they can demonstrate that the Prop 65 chemical is present at a level that does not exceed a risk-based exposure threshold. Zinc naturally contains small quantities of impurities, includ- ing the Prop 65 chemicals lead and cadmium. Given the wide variety of applications for zinc alloys and galvanized steel, the International Zinc Association (IZA) engaged Integral Consult- ing Inc. to carry out a desktop exposure assessment on common metallic zinc applications to determine the need to label products containing zinc under Prop 65. PROP 65 CHEMICALS IN ZINC ALLOYS AND GALVANIZED MATERIALS Impurity levels in zinc alloys and gal- Lead and Cadmium in Zinc Alloys and Materials vanized coatings are specified under Chemical Requirements % ASTM B86-18 and ASTM B6-18. For zinc Alloy Lead (max) Cadmium (max) alloys, the current evaluation used Za- mak 3 as a surrogate, given it represents ZAMAK 2 0.005 0.004 the majority of zinc alloy production; ZAMAK 3 0.005 0.004 impurity levels among all alloys are con- ZAMAK 5 0.005 0.004 sistent and results can be applied for all ZAMAK 7 0.003 0.002 applications. -
Overcor Zamak and Nyrstar Zinc Diecasting Alloy
SAFETY DATA SHEET Based upon Regulation (EC) No 1907/2006, as amended by Regulation (EU) No 2015/830 zinc alloys Die Casting SECTION 1: Identification of the substance/mixture and of the company/undertaking 1.1. Product identifier Product name : zinc alloys Die Casting Synonyms : AC41A; AC43A; AG40A; alloy 2; alloy 3; alloy 5; kayem1; kayem2; ZA-12; ZA-27; ZA-8; zamak 12; zamak 2; zamak 27; zamak 3; zamak 5; zamak 8; zamak KS; zinc alloys DC; zinc alloys for Die Casting; ZL0400; ZL0410; ZL0430; ZL0810; ZL1110; ZL12; ZL2; ZL27; ZL2720; ZL3; ZL5; ZL8; ZnAl11Cu1; ZnAl18Cu1; ZnAl27Cu2; ZnAl4; ZnAl4Cu1; ZnAl4Cu3 Registration number REACH : Not applicable (mixture) Product type REACH : Mixture/alloy 1.2. Relevant identified uses of the substance or mixture and uses advised against 1.2.1 Relevant identified uses Metal industry: pressure die casting, centrifugal die casting, gravity die casting 1.2.2 Uses advised against No uses advised against known 1.3. Details of the supplier of the safety data sheet Supplier of the safety data sheet Nyrstar Belgium N.V. on behalf of Nyrstar Sales & Marketing A.G. Zinkstraat 1 B-2490 Balen ☎ +32 14 44 95 00 +32 14 81 05 31 [email protected] Nyrstar Budel B.V. on behalf of Nyrstar Sales & Marketing A.G. Hoofdstraat 1 6024 AA Budel-Dorplein ☎ +32 14 44 96 80 +32 14 44 95 52 [email protected] Nyrstar France S.A.S. on behalf of Nyrstar Sales & Marketing A.G. Rue Jean Jacques Rousseau F-59950 Auby ☎ +32 14 44 96 80 +33 3 27 88 39 48 [email protected] Manufacturer of the product NYRSTAR Sales & Marketing AG Tessinerplatz 7 CH-8002 Zürich ☎ +41 44 745 81 00 +41 44 745 81 10 [email protected] 1.4. -
Diecast Forums - Bulletin Board – Diecast Zone
http://www.diecast.org/diecast98/html/asp/forums/bulletinboard/v... 1 of 4 Bulletin Board · Forum 18 · Forum 43 · The Lounge · Help? · Guidelines Contact Diecast Forums - Bulletin Board – Diecast Zone Posted By: William Hadfield Posted On: Sunday March 16, 2008 at 1:29 AM Message: I came across some information on Wikepedia about the dreaded disintegration of our beloved little cars. It is known as Intergranular Corrosion caused by impurities in the Zinc Alloys that are used to make our diecast models. It seems that despite regulated standards imposed for the composition of ZAMAK since 1960, these impurities have still managed to creep into the mixture at some of the Chinese factories that produce diecast models, as evidenced by many early Franklin Mint models which are affected from 1996-2000. It's too bad all of these affected models weren't recalled, or replaced by Franklin Mint. IMHO. Zinc pest, (from German Zinkpest), is a destructive, intercrystalline corrosion process of zinc alloys of poor purity. This corrosive process is not the same thing as metal fatigue caused by externally applied forces. Zinc pest affects primarily die-cast zinc articles that were manufactured during the 1930s, 1940s, and early 1950s. In Germany, articles made from ZAMAK, a zinc alloy that also contains aluminum, magnesium, and copper, may be affected when produced during World War II and several years thereafter. Purer alloys were not available to the manufacturers as they were used for the war effort, or were just not on the market after the war. While impurities of the alloy seem to be the cause of the problem, environmental conditions such as warm humidity (greater than 65%) may accelerate the process. -
101 Cleaning Zinc Alloy Fuel Bodies
Cleaning Zinc Alloy Fuel Bodies By Bruce Smith 101 Cincae the inventrion of thbe carbureto r in Csubstitutinhg the Gereman kupfemr for copper. iworsst case sctenario rfor a cayrburetor is to re - the late nineteenth and early twentieth There are various standard formulations and Eu - plenish the gasoline in the float bowl after it Scenturies (when Zenith, Pallas, Pier - ropean casting ZAMAK has a zinc content of evaporates, ensuring a good supply of water sat - burg, and SOLEX were pioneering designs), about 95% with 4% aluminum and 1% copper. urated fuel. Carried out over several years, this there has been a need to clean the residues and Most inorganic reactions are based on this zinc sets up the ideal conditions to maximize zinc re - reactants that accumulate during use. The crud content, which can form deposits and lead to actions. The preventative solutions are to en - that forms in and on carburetors and fuel pumps corrosion damage. Extreme examples result in sure that only fresh gas is in the fuel system and generally falls into two categories: organic (from internal corrosion sufficient enough to damage that the carburetor and fuel pump are run dry petroleum residues, grease and oil) and inor - a casting beyond repair. before storing. ganic (from metal reactants, minerals and A bit of chemistry background is useful to salts). Most of these contaminants can plug jets, understand the processes that occur. Zinc is re - Cleaning Organic & Inorganic Contaminants nozzles, and pathways, preventing proper me - sistant to corrosion if kept reasonably dry. A thin So cleaning an old Zenith or SOLEX carbu - chanical operation. -
Section 09 Casting Examples
Casting Examples SECTION 9 Aluminum 9-2 Zinc 9-14 Pistol Frame 9-2 Knot 9-14 Rocker Arm 9-2 Bracket 9-14 Right/Left Hand Bracket 9-2 Faucet Handle 9-14 Endbell 9-3 Connector 9-15 Engine Base Bracket 9-3 Kitchen Faucet Hub 9-15 Water Passage 9-3 Fuel Fitting 9-15 Heat Sink Front & Back 9-4 Reverse Valve Casket 9-16 Chassis 9-4 Casket Arm 9-16 B Pillar 9-4 Display Frame Component 9-16 Trimmer Deck Housing 9-5 Outside Cover 9-17 RFU Enclosure 9-5 Front Plate L-20 9-17 Impeller 9-5 Connector Housing 9-17 Lower Crankcase 9-6 Rearview Mirror Mount 9-18 Differential Carrier 9-6 Steering Wheel Ignition Lock Housing 9-18 Beta Crankcase Right & Left 9-6 Headlamp Visor 9-18 Scooter Monocoque Frame 9-7 Camera Bracket 9-19 Rear Wheel Drive Northstar Block Casting 9-7 ZA (Zinc-Aluminum) 9-20 Power Condition Module Chassis 9-7 Tool Housing & Components 9-20 MMC Brake Drum 9-8 Transmission Shift Selector Tube 9-20 AWD Clutch Housing 9-8 RWD Transmission 9-8 Magnesium 9-9 Frame 9-9 Head Node 9-9 Fishing Reel 9-9 Clutch Cover 9-10 Camera Assembly 9-10 Hand-Held Computer Housing 9-10 Gear Case Housing Assembly 9 -11 Lock Housing 9 -11 Fairing Support Bracket 9 -11 Seat Back and Cushion 9-12 Lift Gate Inner Panel 9-12 Cross Car Beam for Instrument Panel 9-12 Oil Tank 9-13 SAWZALL Gear Case Assembly 9-13 9 NADCA Product Specification Standards for Die Castings / 2015 9-1 Casting Examples Aluminum Part Name: Pistol Frame Application: 0.22 Caliber Pistol Part Weight: 0.35 lbs. -
Die Casting Design and Specification Guide
Delivery Engineered Solutions MES Die Castings Design and Specification Guide Rev 1 – 9-2017 625 Bear Run Ln Lewis Center, OH 43035 Phone: 740-201-8112 www.mesinc.net KEY DESIGN DECISION Matching Material Properties STEPS Pure aluminum is rather weak and malleable on its own. But mixed with other metals such as silicon, iron, copper, magnesium, manganese, or zinc strengthens and brings other benefits to the metal. Adding silicon and magnesium to aluminum, for example, results in an alloy that is extremely resistant to corrosion. There Matching Material Properties are 530 different alloy compositions with more compositions being created and registered every year. The versatility that aluminum alloys offer is undeniable, and the advantages of A380 make it one of the most widely used alloy for manufacturing and die casting. Die & Unit Die Construction Die casting materials are precisely formulated metal alloys which offer the mechanical properties of medium-strength metals. They are generally several times as strong and many times more rigid than plastics, and their mechanical properties compare favorably with powdered iron, brass, and screw- Minimizing Part Porosity machined steel. Designing for proper strength in a product depends on two main factors: strength of the material selected Preplanning Post-Cast Machining and configuration of the part. Die casting alloys offer a wide range of as-cast material strengths, ranging as high as 54 ksi (372 MPa) ultimate tensile. The designer can usually develop sufficient strength in critical features simply by providing Tolerancing Guidelines adequate wall thickness. Where additional strength is required, reinforcing features such as ribs, flanges and locally thickened sections can be accurately computed and precisely cast. -
Zamak Chemical Properties Physical Properties
Zamak Commercial name for a zinc base alloy with aluminum, copper and magnesium. Versatile material used to obtain die casting pieces in high volumes with high precision and detail reproductibility eliminating machining and reducing costs. Chemical properties DESIGNATION ABBREV. ALLOY Weight Aluminium Magnesium Copper Lead Cadmium Tin Iron Nickel Silicium Titanium Chromium Zinc ( Al ) ( Mg ) ( Cu ) ( Pb ) ( Cd ) ( Sn ) ( Fe ) ( Ni ) ( Si ) ( Ti ) ( Cr ) ( Zn ) min. 3,8 0,035 2,7 --- --- --- --- --- --- --- --- rest. ZAMAK 2 ZL2 ZnAl4Cu3 max. 4,2 0,06 3,3 0,003 0,003 0,001 0,02 0,001 0,02 --- --- rest. min. 3,8 0,035 0,7 --- --- --- --- --- --- --- --- rest. ZAMAK 3 ZL3 ZnAl4 max. 4,2 0,06 1,1 0,003 0,003 0,001 0,02 0,001 0,02 --- --- rest. min. 3,8 0,035 0,7 --- --- --- --- --- --- --- --- rest. ZAMAK 5 ZL5 ZnAl4Cu1 max. 4,2 0,06 1,1 0,003 0,003 0,001 0,02 0,001 0,02 --- --- rest. min. 5,6 --- 1,2 --- --- --- --- --- --- --- --- rest. ZAMAK 6 ZL6 ZnAl6Cu1 max. 6,0 0,005 1,6 0,003 0,003 0,001 0,02 --- 0,02 --- --- rest. min. 8,2 0,02 0,9 --- --- --- --- --- --- --- --- rest. ZAMAK 8 ZL8 ZnAl8Cu1 max. 8,8 0,03 1,3 0,005 0,005 0,002 0,035 0,001 0,035 --- --- rest. min. 10,8 0,02 0,5 --- --- --- --- --- --- --- --- rest. ZAMAK 12 ZL12 ZnAl11Cu1 max. 11,5 0,03 1,2 0,005 0,005 0,002 0,05 --- 0,05 --- --- rest. min. 0,01 --- 1,0 --- --- --- --- --- --- 0,15 0,1 rest.