Large Scale Automated Manufacturing Production System Logistics
Total Page:16
File Type:pdf, Size:1020Kb
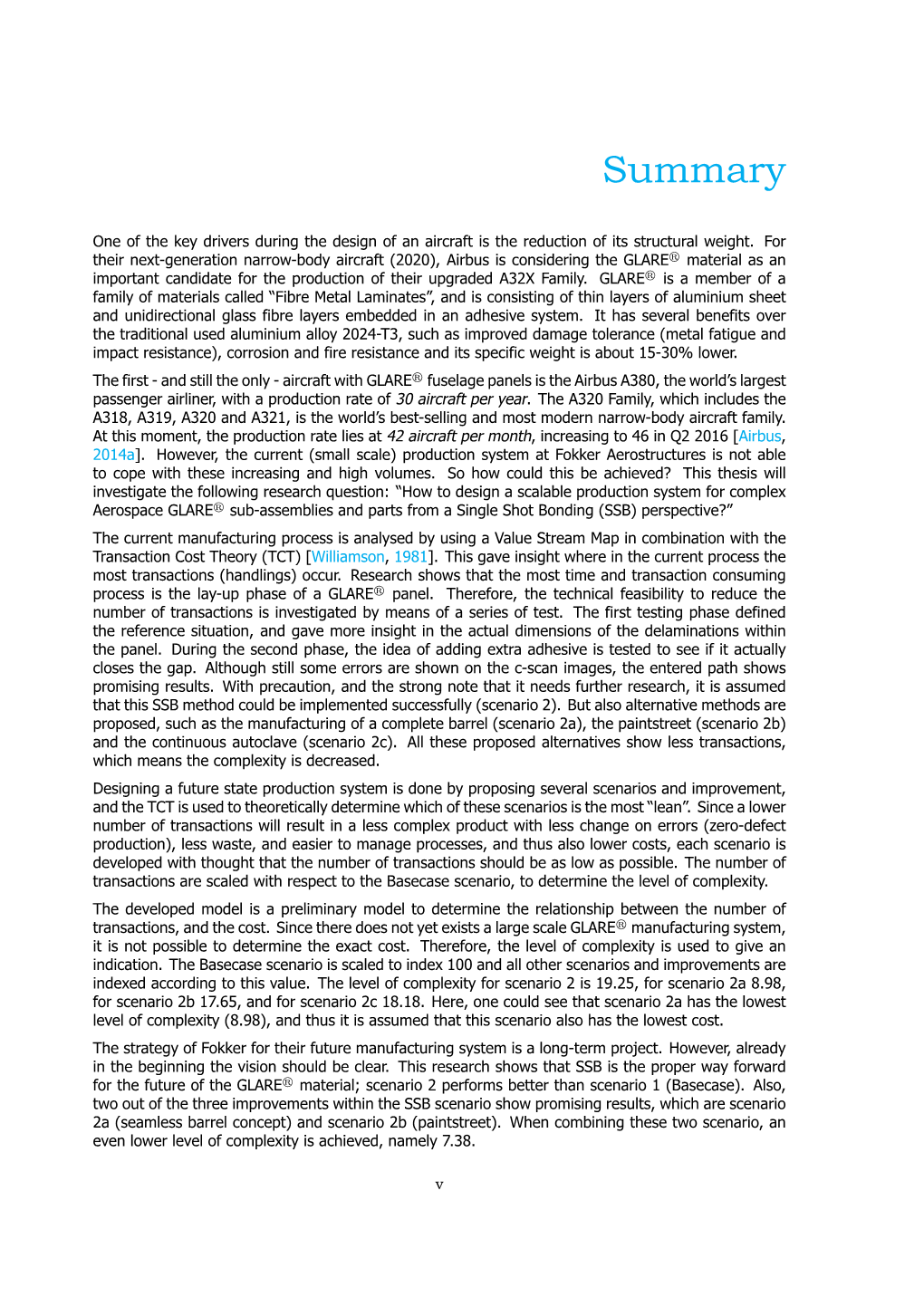
Load more
Recommended publications
-
The Residual Stress Characteristics and Mechanical Behavior of Shot Peened Fiber Metal Laminates Based on the Aluminium-Lithium Alloy
Delft University of Technology The residual stress characteristics and mechanical behavior of shot peened fiber metal laminates based on the aluminium-lithium alloy Li, Huaguan; Wang, Hao; Alderliesten, René; Xiang, Junxian; Lin, Yanyan; Xu, Yingmei; Zhao, Haidan; Tao, Jie DOI 10.1016/j.compstruct.2020.112858 Publication date 2020 Document Version Final published version Published in Composite Structures Citation (APA) Li, H., Wang, H., Alderliesten, R., Xiang, J., Lin, Y., Xu, Y., Zhao, H., & Tao, J. (2020). The residual stress characteristics and mechanical behavior of shot peened fiber metal laminates based on the aluminium- lithium alloy. Composite Structures, 254, [112858]. https://doi.org/10.1016/j.compstruct.2020.112858 Important note To cite this publication, please use the final published version (if applicable). Please check the document version above. Copyright Other than for strictly personal use, it is not permitted to download, forward or distribute the text or part of it, without the consent of the author(s) and/or copyright holder(s), unless the work is under an open content license such as Creative Commons. Takedown policy Please contact us and provide details if you believe this document breaches copyrights. We will remove access to the work immediately and investigate your claim. This work is downloaded from Delft University of Technology. For technical reasons the number of authors shown on this cover page is limited to a maximum of 10. Green Open Access added to TU Delft Institutional Repository 'You share, we take care!' - Taverne project https://www.openaccess.nl/en/you-share-we-take-care Otherwise as indicated in the copyright section: the publisher is the copyright holder of this work and the author uses the Dutch legislation to make this work public. -
Compressive Strength of the Glare Composite Laminates After Impact Load
IJISET - International Journal of Innovative Science, Engineering & Technology, Vol. 2 Issue 3, March 2015. www.ijiset.com ISSN 2348 – 7968 Compressive Strength of the Glare Composite Laminates after Impact Load 1 2 P SanthoshP Kumar D, M.Tech , P Dr.R.AsokanP ,Professor, [email protected],Hindustan university. [email protected], Hindustan university ABSTRACT composites simultaneously. GLARE is widely used in aircraft skins. GLARE got some serious attentions in recent days due GLARE is a hybrid composite consisting of thin to its large amount usage in the skin of AIRBUS A-380. aluminium and glass/epoxy layers. GLARE has good impact resistance and has high resistance to fatigue loading.This paper In the past investigation of GLARE , some scholars like SeyedYaghoubi et al (2012) presented the experimental and presents the experimental behaviour of the GLARE and numerical investigations on ballistic impact behaviours of investigate its impact damage. The analysis involved for various GLARE 5 fibre-metal laminated (FML) beams of various thickness of the aluminium fibre. The thickness of the aluminum thicknesses and also analysed using 3D finite element (FE) sheet is 0.2.After investigated the laminate in impact testing it is code, LS-DYNA and compared the results.Alderliesten et al tested in the compression testing. (2012) calculated the impact loading using the combination of suitable properties of metals and fibre reinforced composites, Key words -GLARE,Impact test,Compression test used superior impact properties as well as considerable improvement in fatigue performance.The results for different 1.INTRODUCTION material is studied .Hamedahmadi et al( 2011) studied the 2/1 GLARE laminates that are manufactured and impacted by The aircraft industry is very conservative in the adoption of cylindrical projectiles at energies up to that required to new designs and technologies. -
Comparative Study of Tensile and Flexural Behaviour for Glass-Fiber- Reinforced Aluminium (Glare) Laminates and Aluminum
Asian Journal of Computer Science and Technology (AJCST) Vol1.No.1 2013 pp 5-13. available at: www.goniv.com Paper Received :19-02-2013 Paper Published:20-03-2013 Paper Reviewed by: 1. John Arhter 2. Hendry Goyal Editor : Prof. P.Muthukumar COMPARATIVE STUDY OF TENSILE AND FLEXURAL BEHAVIOUR FOR GLASS-FIBER- REINFORCED ALUMINIUM (GLARE) LAMINATES AND ALUMINUM Asha Melba.V, Senthil Kumar.A, Vino.A # Department of CAD /CAM Engineering Sethu Institute of Technology, pulloor-626 115. [email protected] [email protected] [email protected] ABSTRACT The objective of this research article was investigated to evaluate tensile and flexural properties of Glass-fiber-Reinforced Aluminium (Glare) laminates as well as Aluminium sheets of same thickness. In addition to that the tensile and flexural strength of Glare laminates were compared with values of aluminium sheets. In this article, the aluminium based FMLs were fabricated using hand layup technique and cut as per ASTM standards. Three types of layers such as 2/1 Glare, 3/2 Glare and 5/4 Glare laminates were prepared. Computer controlled UTM machine used to determine the tensile, flexural properties and failure mode of the Glare laminates and Plain aluminium sheets with same thickness. From the test results the graphs were plotted for load vs displacement, tensile and flexural strength vs layers thickness. It shows that tensile and flexural strength of Glass-fiber-Reinforced Aluminium (Glare) laminates purely depend on the volume percentage of fibre and it exhibits improvement over the properties of aluminium sheets. Keywords: Glass-fiber-Reinforced Aluminium laminates (Glare), aluminium sheet, hand lay-up technique, tensile property and flexural property. -
HPC Sept 02 Airbus A380
Commercial Aircraft Extra large by any measure Advanced composites play a big role in the success of the world’s largest commercial aircraft. t 555 passengers and a maximum take-off According to Airbus’ current plans, the A380 weight of 1,235,000 lb (560 metric tons), will carry 30 metric tons/66,000 lb of structural A“huge” is the most appropriate word to composites, primarily of carbon-fiber/epoxy, or 16 describe the Airbus A380-800, the world’s largest percent of its airframe weight (approx. 170 metric jet airliner, set to begin regular service in 2006. tons), making it the most composite-intensive The plane itself is an enormous achievement, but commercial aircraft to date. Due to the higher so is its impact on the worlds of commercial avia- stiffness-to-weight performance of carbon fiber tion, advanced materials and composite manufac- composites, this is equivalent to the replacement turing technologies. Over a decade in the planning of 20 percent of conventional aluminum struc- and design phase, the first flying aircraft is cur- ture. This figure could rise to 35 metric tons (77,000 lb) as the final component designs near completion. Wing leading edges will take advan- tage of economies realized in the use of glass-rein- forced thermoplastics. And 4 percent of the air- Source: Airbus Industrie frame will be GLARE (GLAss fiber-REinforced aluminum), a multi-layer laminate of fiberglass/epoxy and aluminum to be used in the upper fuselage panels (discussed below and in HPC May/June 1996, p. 28). Beyond the structural composites under discussion here, as many as 30 metric tons of composites, mainly fiberglass/phe- nolic, may be used in each plane’s interior. -
Detection and Evaluation of Pre-Preg Gaps and Overlaps in Glare Laminates
Delft University of Technology Detection and Evaluation of Pre-Preg Gaps and Overlaps in Glare Laminates Nardi, Davide; Abouhamzeh, Morteza; Leonard, Rob; Sinke, Jos DOI 10.1007/s10443-018-9679-z Publication date 2018 Document Version Final published version Published in Applied Composite Materials: an international journal for the science and application of composite materials Citation (APA) Nardi, D., Abouhamzeh, M., Leonard, R., & Sinke, J. (2018). Detection and Evaluation of Pre-Preg Gaps and Overlaps in Glare Laminates. Applied Composite Materials: an international journal for the science and application of composite materials, 1-17. https://doi.org/10.1007/s10443-018-9679-z Important note To cite this publication, please use the final published version (if applicable). Please check the document version above. Copyright Other than for strictly personal use, it is not permitted to download, forward or distribute the text or part of it, without the consent of the author(s) and/or copyright holder(s), unless the work is under an open content license such as Creative Commons. Takedown policy Please contact us and provide details if you believe this document breaches copyrights. We will remove access to the work immediately and investigate your claim. This work is downloaded from Delft University of Technology. For technical reasons the number of authors shown on this cover page is limited to a maximum of 10. Appl Compos Mater https://doi.org/10.1007/s10443-018-9679-z Detection and Evaluation of Pre-Preg Gaps and Overlaps in Glare Laminates Davide Nardi1 & Morteza Abouhamzeh1 & Rob Leonard2 & Jos Sinke 1 Received: 6 February 2018 /Accepted: 22 February 2018 # The Author(s) 2018 Abstract Gaps and overlaps between pre-preg plies represent common flaws in composite materials that can be introduced easily in an automated fibre placement manufacturing process and are potentially detrimental for the mechanical performances of the final laminates. -
An Example for the Use of New UT Array Inspection Systems
ECNDT 2006 - Tu.2.1.1 In-Service Inspection Concept for GLARE® – An Example for the Use of New UT Array In- spection Systems Wolfgang BISLE, Theodor MEIER, Sascha MUELLER, Sylvia RUECKERT Airbus, Bremen Abstract. UT phased arrays and array transducers for FIT (Field Inspection Technology) open new chances for NDT of complex structure materials in aeronautics. GLARE® is such a new material which will widely be used on the new Airbus A380. Even as GLARE® in the A380 needs no scheduled NDT inspections, it is usual to be prepared for accidental damages like impacts, lightning strike, etc. to secure the integrity of the affected area. Well fitted for quality control of GLARE® in the production the UT array technique also proved to be a powerful tool for unexpected maintenance tasks. The pres- entation will show how this new technique deals with the complexity of that new mate- rial providing reliable diagnostics for maintenance. 1. General Due to the continuously increasing requirement for cost savings in aeronautics there is a need for improving manufacturing process and material properties of aircraft parts. Aircraft manu- facturers have to provide cost-effective but safely operating aircrafts. High performance mate- rials allow to smart-up the design and structure of aircraft parts. This results in significant weight savings and, finally, cost savings, too. One of these high-tech materials recently large-scale introduced into AIRBUS A380 design and manufacturing is GLARE®. Related to its specific build-up the Fibre Metal Lami- nate (FML) allows to adapt its material properties to specific stress and fatigue requirements by locally optimised lay-up configurations. -
Bell Unveils Air-Taxi Concept
PUBLICATIONS Vol.50 | No.2 $9.00 FEBRUARY 2019 | ainonline.com The Bell Nexus will initially feature human operation and a hybrid- electric propulsion system powering six ducted fans. Airshows New models on deck for Heli-Expo page 43 Safety U.S. bizjet accidents rise in 2018 page 14 Maintenance Industry looks to build tech pipeline page 51 Industry One Aviation works on bankruptcy page 27 Bell unveils air-taxi concept ATC First digital tower opens by Rob Finfrock in the UK page 12 Highlighting the increasing awareness and challenges in the vertical dimension,” said landing skids, and a modified V tail topped by appeal of vertical takeoff and landing (VTOL) Bell president and CEO Mitch Snyder. “We a short horizontal stabilizer. The flight model solutions outside the traditional domains of believe the design, taken with our strategic will use a hybrid/electric distributed propul- the rotorcraft industry, Bell returned to the approach to build this infrastructure, will sion system feeding six tilting ducted fans, annual Consumer Electronics Show (CES) in lead to the successful deployment of the each powered by individual electric motors. Las Vegas last month with its “full vision” of a Bell Nexus to the world.” The six-fan design is a compromise practical urban air taxi, dubbed the Bell Nexus. The full-scale Nexus display builds upon between quad- and octo-rotor configurations “As space at the ground level becomes the fuselage mockup unveiled at last year’s seen on other urban VTOL designs to provide limited, we must solve transportation CES and features a central wing, integrated continues on page 16 Read Our SPECIAL REPORT Shutdown weighs on bizav Amazing apps by Kerry Lynch It has been less than a decade since the introduction of Apple’s iPad, but the The failure of the White House and Con- withheld, and deliveries delayed, industry device—and those that followed—has gress to reach agreement on border wall groups reported as the shutdown became been embraced by operators, who are funding in late December touched off a the longest in history. -
Composite Materials in the Airbus A380 - from History to Future
Composite Materials in the Airbus A380 - From History to Future - Jérôme PORA Airbus, Large Aircraft Division 1 Rond Point Maurice Bellonte 31707 BLAGNAC Cedex, FRANCE Summary Applications of composite materials and technologies on A380 are reviewed. Also, the “lessons learned” from the existing fleet. Decision for applications of composite materials is consistent with an evolution within the Airbus family. To step into primary structure with a new technology first time requires special attention and careful preparation, including hardware tests and full-scale manufacturing demonstrators. The Material and Technology down-selection Process used by Airbus is described. Finally the remaining limitations to composite introduction on airframe, such as reliability of cost prediction, are highlighted. 1. A380 : a unique technology platform Market pressure for a larger aircraft continues to increase. Growth, congestion, economic and environmental factors are driving the need to develop new solutions. Airbus’s answer is the A380 family. Airbus forecasts a market of about 1,300 aircraft in the A380 size category over the next 20 years. By the end of 1999, enough technical detail on the aircraft was fixed to permit the aircraft specification to be presented to potential customer airlines. This has allowed Airbus to make commercial offers since mid-2000 and launch commitments the same year. This will result in Entry Into Service (EIS) of the 555-seat, double-deck A380-800 during 1st quarter 2006, as shown in Figure 1. As the flagship of the 21st century, the A380 will not only be the most spacious civil aircraft ever built, it will also be the most advanced - representing a unique technology platform from which all future commercial aircraft programmes will evolve. -
Fiber Metal Laminate Structures - from Laboratory to Application Overview and Selected Items Contents
Presented to the Royal Aerospace Society Hamburg Branch at Hamburg University of Applied Sciences, 29.10.2009 Download this file from http://hamburg.dglr.de Presented by Dr. Thomas Beumler Airbus Deutschland GmbH Fiber Metal Laminate Structures - from Laboratory to Application Overview and Selected Items Contents • Advantage of Bonded Structures • Why Fiber Metal Laminates ? • Towards A380 Certification - From Laboratory to Application / Selected Items © AIRBUS DEUTSCHLAND GmbH. document. All Confidential rights and proprietary reserved. Beumler, EDSAS Page 2 Advantage of Bonded Structures WW2: The Havilland Mosquito First time bonding of wood to metal in a high loaded primary structure. The start of metal bonding. © AIRBUS DEUTSCHLAND GmbH. document. All Confidential rights and proprietary reserved. Beumler, EDSAS Page 3 Crack Bridging Metal Bonded Structures (Fokker, Boeing, Lockheed, Douglas, Airbus Saab, ...) Metal Technology 1st Metal Laminates application F-27 Metal Reinforced Composites (Schliekelmann/Bijlmer) Fiber Metal Laminate Concept, Delft FML Technology Fiber Metal Laminates 1st FML application, ARALL on C-17 Development of „Standard-Glare“ A380 Carbon Fiber Reinforced Plastics Composite Technology F-18 B787 Glas Fiber Reinforced Plastics De Bruijne application F-27 Laminated wood (Fokker, de Havilland) 1900 1920 1940 1960 1980 2000 2020 © AIRBUS DEUTSCHLAND GmbH. document. All Confidential rights and proprietary reserved. Beumler, EDSAS Page 4 Advantage of Bonded Structures Advantage of bonded structures compared with riveted or integral structures: • Multiple load path structures • ... allows to join materials tailored to their specific tasks • ... without introduction of fatigue sensitive items (i.e. holes) • ... leading to high stress allowables and therefore low weight structures. • Static advantage: Large load carrying width between skin and stiffener increases onset-of-buckling load. -
The Investigation of Damage Mechanisms of Thermally Aged 4/3 Glare with Cone Beam Computed Tomography
Crimson Publishers Research Article Wings to the Research The Investigation of Damage Mechanisms of Thermally Aged 4/3 Glare with Cone Beam Computed Tomography Hamdi Fidan1, Mustafa Özgür Bora2*, Onur Çoban2 and Eyüp Akagündüz3 1Turkish Airlines Technic Inc, Turkey 2Kocaeli University, Faculty of Aeronautics and Astronautics, Turkey 3TUBITAK-MAM, Materials Institute, Turkey Abstract In this paper, the effect of thermal cycles on the flexural properties of 4/3 configured Glass Reinforced Aluminum (GLARE) has been evaluated with Cone Beam Computed Tomography (CBCT). GLARE is manufactured by Turkish Airlines Technic Inc. composite workshop with autoclave method. After manufacturing process, GLARE samples are subjected to thermal cycles (0, 25, 50, 100, 200 and 300 cycles) in a full function climatic chamber at temperature ranges -30 °C to +40 °C for 120min. Three- point bending tests are applied to thermally aged GLARE samples by using Zwick Z-250 universal test machine. The variation on the flexural modulus and strength values of GLARE samples is determined. From test results, the decrements of the flexural strength and modulus of GLARE samples are occurred for 300 thermal cycles as 4.95% and 4.85%, respectively. From CBCT observations, it is determined that *Corresponding author: Mustafa delaminationKeywords: and metallic layer fractures are the main damage mechanisms. Abbreviations:Ageing; Composites; Damage zone; Mechanical properties; Nondestructive technique Kocaeli,Özgür Bora, Turkey Kocaeli University, Faculty of Aeronautics and Astronautics, 41285, CBCT: Cone Beam Computed Tomography; FMLs: Fiber Metal Laminates; NDT: Non- Destructive Testing; SRM: Structure Repair Manuel; GLARE: Glass Reinforced Submission: Introduction Published: March 30, 2021 Structural weight of an aircraft has an extreme importance on fuel consumption, transport June 03, 2021 Volume 2 - Issue 1 capacity and flight performance due to the ratio (maximum payload)/(maximum take-off How to cite this article: weight). -
Raw Materials in the European Defence Industry
Raw materials in the European defence industry Claudiu C. Pavel & Evangelos Tzimas European Commission, Joint Research Centre Directorate for Energy, Transport & Climate Knowledge for Energy Union Unit - 2016 – Table of contents Acknowledgements ................................................................................................ 2 Executive summary ............................................................................................... 3 1. Introduction ...................................................................................................... 6 1.1 Background ............................................................................................... 6 1.1.1 EU Raw Materials Initiative and critical raw materials ................................ 6 1.1.2 Tackling the raw materials supply risks in Europe's defence industry ........... 7 1.2 Overview of international efforts to identify the raw materials used in the defence industry .............................................................................................. 7 1.3 An overview of the importance of raw, processed and semi-finished materials in the defence industry ................................................................................... 11 1.4 Scope of the study and approach ............................................................... 12 2. Overview of the EU defence industry .................................................................. 14 2.1 General considerations ............................................................................ -
An Experimental Investigation of GLARE and Restructured Fiber Metal Laminates
Dissertations and Theses 6-2012 An Experimental Investigation of GLARE and Restructured Fiber Metal Laminates Adelina Vanessa Benedict Embry-Riddle Aeronautical University - Daytona Beach Follow this and additional works at: https://commons.erau.edu/edt Part of the Aerospace Engineering Commons Scholarly Commons Citation Benedict, Adelina Vanessa, "An Experimental Investigation of GLARE and Restructured Fiber Metal Laminates" (2012). Dissertations and Theses. 22. https://commons.erau.edu/edt/22 This Thesis - Open Access is brought to you for free and open access by Scholarly Commons. It has been accepted for inclusion in Dissertations and Theses by an authorized administrator of Scholarly Commons. For more information, please contact [email protected]. AN EXPERIMENTAL INVESTIGATION OF GLARE AND RESTRUCTURED FIBER METAL LAMINATES by Adelina Vanessa Benedict A Thesis Submitted to the College of Engineering, Department of Aerospace Engineering in Partial Fulfillment of the Requirements for the Degree of Master of Science in Aerospace Engineering Embry-Riddle Aeronautical University Daytona Beach, Florida June 2012 ii iii Acknowledgements I dedicate this thesis to my advisor, Dr. David J. Sypeck. I cannot thank him enough for the tremendous amount of time and effort he has spent in helping me, for making me a more hands on student, for teaching me the value of patience and humbleness, and for giving me the opportunity to become a graduate teaching assistant, as the job was very meaningful to me. I sincerely thank Dr. Daewon Kim and Professor Weavil for taking time out of their schedules to provide me with feedback in the completion of this thesis. I would also like to thank Yi Zhang and Mathew Carlton for their help at the composites lab in some parts of this project.