Chapter on Wind Power Systems
Total Page:16
File Type:pdf, Size:1020Kb
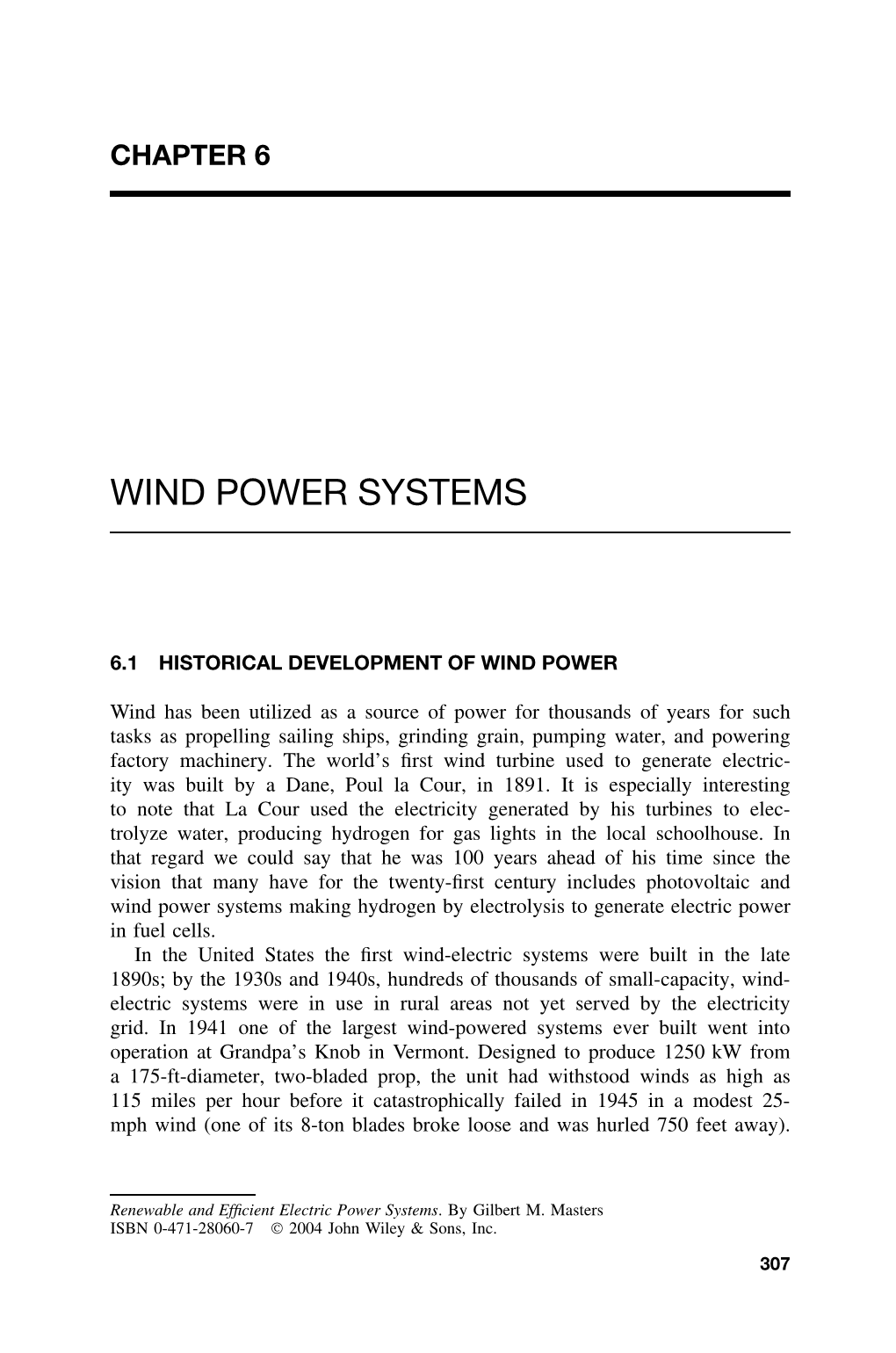
Load more
Recommended publications
-
Wind Energy Department Annual Progress Report 2001
Risø-R-1317(EN) Wind Energy Department Annual Progress Report 2001 Birthe Skrumsager, Søren E. Larsen and Peter Hauge Madsen (Eds) Risø National Laboratory, Roskilde October 2002 Abstract The report describes the work of the Wind Energy Department at Risø National Laboratory in 2001. The research of the department aims to develop new opportunities in the exploitation of wind energy and to map and alleviate atmospheric aspects of environmental problems. The expertise of the depart- ment is utilised in commercial activities such as wind turbine testing and certification, training pro- grammes, courses and consultancy services to industry, authorities and Danish and international or- ganisations on wind energy and atmospheric environmental impact. A summary of the department’s activities in 2001 is shown, including lists of publications, lectures, committees and staff members. ISBN 87-550-2997-3 ISBN 87-550-2998-1 (internet) ISSN 0106-2840 ISSN 1397-8969 Print: Pitney Bowes Management Services Denmark A/S, 2002 Contents 1 Introduction 5 2 Status 2001 for the Department 7 2.1 Social and industrial relevance in Denmark and abroad 9 2.2 International evaluation 10 2.3 Collaboration with universities 11 2.4 Collaboration with other governmental research institutions 11 2.5 The Danish Research Consortia for Wind Energy 12 3 Summary of the Performances, Research Programmes and Tasks 13 4 Projects of the Department 25 4.1 Aeroelastic Design (AED) 25 4.2 Atmospheric Physics (ATM) 29 4.3 Electric Design and Control (EDS) 37 4.4 Wind Power Meteorology (VKM) 40 4.5 Wind Turbines (VIM) 45 4.6 Wind Turbine Diagnostics (VMD) 51 4.7 International Consulting (INR) 56 4.8 Wind Turbine Testing (VMD(PRV) 60 4.9 Type Approval and Certification (SPK) 62 5 Committees and Group Memberships 64 6 Publications 68 6.1 International publications 68 6.2 Danish publications 72 6.3 Conference lectures 77 6.4 Internal reports 86 6.5 Publications for a broad readership 88 6.6 Unpublished lectures incl. -
Experience Curves: a Tool for Energy Policy Assessment
Experience Curves: A Tool for Energy Policy Assessment AUTHORS: Lena Neij, Lund University, Sweden Per Dannemand Andersen, Ris0 National Laboratory, Denmark Michael Durstewitz, Institut fur Solare Energieversorgungstechnik e.V., Germany Peter Helby, Lund University, Sweden Martin Hoppe-Kilpper, Institut fur Solare Energieversorgungstechnik e.V., Germany Poul Erik Morthorst, Ris0 National Laboratory, Denmark ADDITIONAL CONTRIBUTORS: Wind Energy Department, IDAE, Spain Helge V. Larsen, Ris0 National Laboratory, Denmark Carolina Leon Vegas, Lund University, Sweden Kerstin Astrand, Lund University, Sweden Research funded in part by The European Commission within the Fifth Framework: Energy, Environment and Sustainable Development (Contract ENG1-CT2000-00116). Project title: Experience curves - a tool for energy policy programmes assessment (EXTOOL) © 2003, Lena Neij et al. Printed by KFS AB, Lund 2003 IMES/EESS Report No. 40 Deapartment of Technology and Society, Environmental and Energy Systems Studies, Sweden ISSN 1102-3651 ISRN LUTFD2/TFEM—03/3034—SE+(1-146) ISBN 91-88360-56-3 Cover design by Uta Werner, Institut fur Solare Energieversorgungstechnik e.V., Germany Distributed by: Environmental and Energy Systems Studies Lund University Gerdagatan 13 SE -223 62 Lund Sweden Summary The objective of the project, Experience curves: a tool for energy policy assessment (EXTOOL), was to analyse the experience curve as a tool for the assessment of energy policy measures. This is of special interest, since the use of experience curves for the assessment of energy policy measures requires the development of the established experience curve methodology. This development raises several questions which have been addressed and analysed in this project. The analysis is based on case studies of wind power, an area with considerable experience in technology development, deployment and policy measures. -
WIND TURBINE ACCIDENT COMPILATION ©2006 Caithness
WIND TURBINE ACCIDENT COMPILATION Last updated at 01/01/2006 Compiled by David Craig Accident type Date Site/area State/Country Turbine type Details Info source Web Alternate web reference/link reference/link 1 Fatal 1975 Choteau MT, USA 2kw Tim McCartney, Wind Energy -- http://www.wind- atop tower The Breath of works.org/article removing small Life or the Kiss of s/BreathLife.html turbine. Death: Contemporary Wind Mortality Rates, by Paul Gipe 2 Fatal 1981 Boulevard California, USA 40kw Terry Mehrkam, Wind Energy -- http://www.wind- atop nacelle, The Breath of works.org/article run-away rotor, Life or the Kiss of s/BreathLife.html no lanyard. Death: Contemporary Wind Mortality Rates, by Paul Gipe 3 Fatal 1982 Bushland Texas, USA 40kw Pat Acker, 28, Wind Energy -- http://www.wind- rebar cage for The Breath of works.org/article foundation came Life or the Kiss of s/BreathLife.html in contact with Death: overhead power Contemporary lines Wind Mortality Rates, by Paul Gipe 4 Fatal 1982 Denmark 50kw Jens Erik Wind Energy -- http://www.wind- Madsen, during The Breath of works.org/article servicing of Life or the Kiss of s/BreathLife.html controller Death: ©2006 Caithness Windfarms Information Forum Contemporary Wind Mortality Rates, by Paul Gipe 5 Fatal 1983 Palm Springs California, USA 500kw Eric Wright on Wind Energy -- http://www.wind- experimental The Breath of works.org/article VAWT - came Life or the Kiss of s/BreathLife.html down with man Death: basket Contemporary Wind Mortality Rates, by Paul Gipe 6 Fatal 1984 Altamont Pass California, USA 65kw J.A. -
Wind Energy Final PEIS: Appendix D
D-1 APPENDIX D: WIND ENERGY TECHNOLOGY OVERVIEW D-2 D-3 APPENDIX D: WIND ENERGY TECHNOLOGY OVERVIEW Modern wind energy technologies rely heavily on the very complex scientific discipline of fluid dynamics (which includes the study of the atmosphere) and the equally complex engineering discipline of aerodynamics. A comprehensive treatment of either of these disciplines is well beyond the scope of this programmatic environmental impact statement (PEIS). The discussions that follow are intended only to establish a basic understanding of wind technology and the factors that control its evolution. References are provided for those who wish to have a more detailed understanding of wind technology. This appendix provides an overview of the fundamentals of wind energy and wind energy technologies, describes the major components of modern wind turbines, and introduces terms that are unique to the field of electric power generation using wind energy. Important site characteristics and critical engineering aspects of wind energy technologies are presented, and their respective influences on future development decisions are discussed.1 An overview of the current state of wind energy technology and ongoing research and development (R&D) is provided. Descriptions of a typical wind energy project and the major actions associated with each phase of development — site monitoring and testing, construction, operation, and decommissioning — are presented in Chapter 3 of this PEIS. D.1 IMPORTANT TERMS AND CONVENTIONS Discussions in the following sections introduce important terms and conventions, some of which are unique to the wind energy industry. The terms and conventions are described in the text where they are first introduced.