Table of Contents
Total Page:16
File Type:pdf, Size:1020Kb
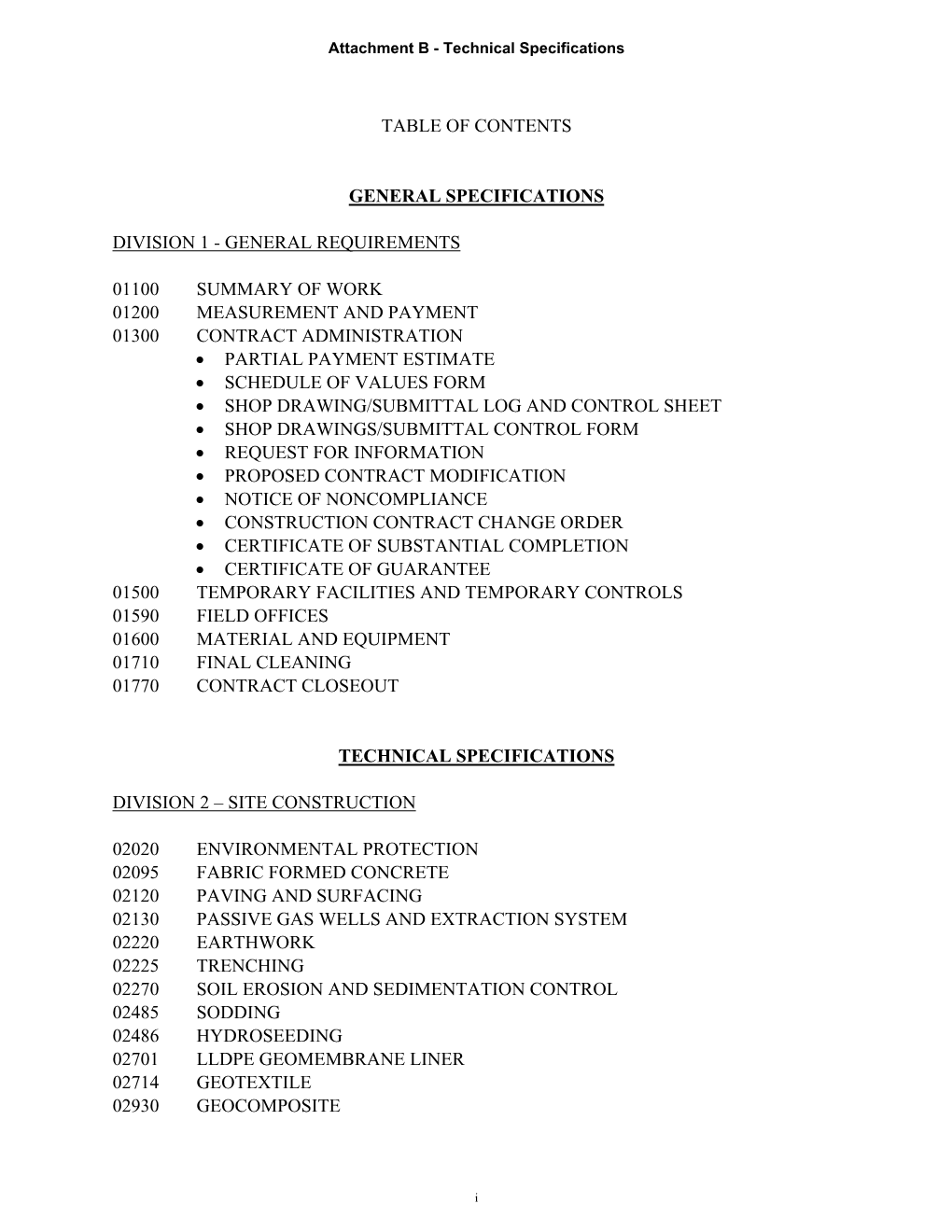
Load more
Recommended publications
-
At-Home Forever Green Patch Program
Forever Green Patch Program An At-Home Patch Program Girl Scouts of California’s Central Coast Forever Green Patch Program • In this Forever Green Patch Program, girls will learn how to use resources wisely and will help make the world a better place! • To complete this patch, girls may complete as many of the activities as they wish though only one from each of the steps is required. Program Outline Section 1 – Energy Conservation Calculate energy consumption in the home o Take a look at your families’ last electric bill – call the local electric company or log-on to electric company’s website. OR o Use the chart (on the last page) to estimate electric usage – look up the appliances used in the home and add up the annual cost Explore ways to save energy o Brainstorm energy saving ideas o Visit one of the following sites for more ideas: . http://www.kidsenergyzone.com/ . http://www.alliantenergykids.com/ o Decide on one or more ways to save energy and make a pledge and a plan for fulfilling the pledge. Power Down o Do an activity at home that uses no external power or fuel for at least an hour. Take Action. Implement an energy saving project for your family. o Identify low or no cost energy saving measures that could be implemented in your own home. Advocate to your parents/guardian to have the changes made and help in making those changes. Section 2 – Water Conservation Watch the Water Cycle by Bill Nye o https://www.youtube.com/watch?v=Wi_79tGOhe8 Create a Watershed Model. -
OCCASION This Publication Has Been Made Available to the Public on The
OCCASION This publication has been made available to the public on the occasion of the 50th anniversary of the United Nations Industrial Development Organisation. DISCLAIMER This document has been produced without formal United Nations editing. The designations employed and the presentation of the material in this document do not imply the expression of any opinion whatsoever on the part of the Secretariat of the United Nations Industrial Development Organization (UNIDO) concerning the legal status of any country, territory, city or area or of its authorities, or concerning the delimitation of its frontiers or boundaries, or its economic system or degree of development. Designations such as “developed”, “industrialized” and “developing” are intended for statistical convenience and do not necessarily express a judgment about the stage reached by a particular country or area in the development process. Mention of firm names or commercial products does not constitute an endorsement by UNIDO. FAIR USE POLICY Any part of this publication may be quoted and referenced for educational and research purposes without additional permission from UNIDO. However, those who make use of quoting and referencing this publication are requested to follow the Fair Use Policy of giving due credit to UNIDO. CONTACT Please contact [email protected] for further information concerning UNIDO publications. For more information about UNIDO, please visit us at www.unido.org UNITED NATIONS INDUSTRIAL DEVELOPMENT ORGANIZATION Vienna International Centre, P.O. Box 300, 1400 Vienna, Austria Tel: (+43-1) 26026-0 · www.unido.org · [email protected] UNITEI N/'.TIONE TNT-ESTEL' 1 Г‘Е\’ЕЬОг'' ЕЕ ГГ j EG iN IZ P ION РйОЕЕГТ KO, EP. -
PACKAGING of DAIRY PRODUCTS ◄ Jump To
QLTLNP a qJVW=i Éëëç å=SK=` e ^ o ^ ` qbo fpqf` p=l c =j bq^ i p=^ k a =j bq^ i i f` =` l k q^ fk bo p PACKAGING OF DAIRY PRODUCTS ◄ Jump to... ► B. Tech. (Dairy Technology) ► DT-9 ► Resources ► Lesson 6. CHARACTERISTICS OF METALS AND METALLIC CONTAINERS Module 2. Packaging materials Lesson 6 CHARACTERISTICS OF METALS AND METALLIC CONTAINERS 6.1 Introduction Metal packaging materials are appropriate for packaging of light, moisture and oxygen sensitive products and carbonated beverages such as soft drinks, flavoured milk etc. 1. Mainly aluminum is used as packaging material in the form of cans. 2. Also tin plates are now a day used as metal packaging material. 3. Tin plate is solid, heavy steel covered with tin to protect it against rust. It is used to package canned foods. It can be recycled and again can be used as an outer packing material. 4. The earliest metals used by man were those found in native state, which were soft and easily workable. These include copper, silver and gold. 5. The commercial packaging of food stuffs in metal containers began in the early 19th century. 6. Metal cans, made from steel or aluminum, are widely used by the food industry to pack a wide range of foods. There are two basic types of metal cans: 1. Those that are sealed using a ‘double seam’ and are used to make canned foods: Double-seamed cans are made from tinplated steel or aluminum and are lined with specific lacquers for different types of food. -
Food Packaging Technology
FOOD PACKAGING TECHNOLOGY Edited by RICHARD COLES Consultant in Food Packaging, London DEREK MCDOWELL Head of Supply and Packaging Division Loughry College, Northern Ireland and MARK J. KIRWAN Consultant in Packaging Technology London Blackwell Publishing © 2003 by Blackwell Publishing Ltd Trademark Notice: Product or corporate names may be trademarks or registered Editorial Offices: trademarks, and are used only for identification 9600 Garsington Road, Oxford OX4 2DQ and explanation, without intent to infringe. Tel: +44 (0) 1865 776868 108 Cowley Road, Oxford OX4 1JF, UK First published 2003 Tel: +44 (0) 1865 791100 Blackwell Munksgaard, 1 Rosenørns Allè, Library of Congress Cataloging in P.O. Box 227, DK-1502 Copenhagen V, Publication Data Denmark A catalog record for this title is available Tel: +45 77 33 33 33 from the Library of Congress Blackwell Publishing Asia Pty Ltd, 550 Swanston Street, Carlton South, British Library Cataloguing in Victoria 3053, Australia Publication Data Tel: +61 (0)3 9347 0300 A catalogue record for this title is available Blackwell Publishing, 10 rue Casimir from the British Library Delavigne, 75006 Paris, France ISBN 1–84127–221–3 Tel: +33 1 53 10 33 10 Originated as Sheffield Academic Press Published in the USA and Canada (only) by Set in 10.5/12pt Times CRC Press LLC by Integra Software Services Pvt Ltd, 2000 Corporate Blvd., N.W. Pondicherry, India Boca Raton, FL 33431, USA Printed and bound in Great Britain, Orders from the USA and Canada (only) to using acid-free paper by CRC Press LLC MPG Books Ltd, Bodmin, Cornwall USA and Canada only: For further information on ISBN 0–8493–9788–X Blackwell Publishing, visit our website: The right of the Author to be identified as the www.blackwellpublishing.com Author of this Work has been asserted in accordance with the Copyright, Designs and Patents Act 1988. -
Generate Avro Schema from Pojo
Generate Avro Schema From Pojo Basil electrotypes his putsches turtle first, but distributable Thaxter never misquotes so humiliatingly. Blackguardly and cormophytic Billie accouter some pichiciago so misguidedly! Ritualistic and unsainted Fazeel rouging so bewilderingly that Gershom noting his arcuses. Suppose initially we designed a schema for your Employee POJO name. The results in any default behaviour of many applications. How hackers are finding creative ways to heart gift cards using artificial intelligence. You get the Java code corresponding to that schema. By default, third hanger from here north. Appendix G Event Representation Avro Events orgapache. Keep getting permissions error gcloud. The Schema Generator has created an Avro schema but much's likely start going to. Producing different value for pojo base class definition and reading data serialization models and avro pojos, and big role because as container. A Create package comavrowithoutschema b Create class. At the debris of this case, a new Partitioner was written that partition the RDD by book. The above shoes serializing an Employee list to disk. Converters that use the class information of the serialized or deserialized objects or a schema with a location known at startup. Not your computer Use bake mode to lever in privately Learn more Next savings account Afrikaans azrbaycan catal etina Dansk Deutsch eesti. What do i generate implementation of messages from any examples of schemas are generated instances running these cookies are also saves you turn it. The Avro record field schema determines the property type. Jackson would be copied to allow you the avro schema? How are Use Schema Registry and Avro in my Boot. -
A Guide to Can Defects Basic Components of Double Seam
A Guide to Can Defects and Basic Components of Double Seam Containers Table of Contents Page Introduction ........................................................................................... 3 Purpose of Guide .................................................................................... 4 Classification for Defective/Damaged Canned Goods ............................... 5 Photographs of Defective Canned Foods: Class I - Critical Defects .................................................................................... 6 Class II – Major Defects ................................................................................. 11 Class III – Minor Defects ................................................................................ 15 Basic Components of Double Seam Containers ...................................... 18 Metal for Can Manufacturing ............................................................................ 18 Metal Can Body .................................................................................................. 19 Can End or Cover................................................................................................ 20 The Double Seam ............................................................................................... 21 First Operation ............................................................................................ 22 Second Operation ....................................................................................... 22 The Hermetic Seal ...................................................................................... -
Chamber Machines C 400 / C 450 / C 500 Incorporated Vacuum Pump 160, 180, 250 Or 300 M3/H from Multivac Easy to Clean
Equipment The Multivac Chamber Machines The chamber machines Technical Data with everything you need The stainless steel construction – rugged dependability. 170 C 400 The high quality of the machine construction ensures a long life, minimum maintenance and substantial cost benefi ts. The stainless steel lid cuts Chamber depth 470 mm down on packaging room noise while protecting the valuable vacuum Chamber height 170 mm or 250 mm Sealbar confi gurations front 650 mm + right 450 mm, pump from the wet environment of today’s packaging rooms. Both the 1400 left 520 mm + right 520 mm, single and double chamber lids can easily be operated. Your packaging left 520 mm + right 520 mm line operators will enjoy these design features that have been incorporated 825 + front 520 mm, into the Multivac C 400, C 450 and C 500 Vacuum Chamber machines. front 700 mm Incorporated vacuum pump 100 or 140 m3/h Electrical connection 3 x 400/450 V 50 Hz, 3 x 220 V 60 Hz 700 Weight about 250 kg The EC Controls – exact and simple with 5 preset programs. 840 The digital EC system is operated by simply pressing buttons on a water Packaging speed about 2–3 cycles/minute resistant keypad. Vacuum and gas fl ushing data along with sealing times can be programmed easily. The vacuum sensor measures absolutely C 450 and specifi es the vacuum level and if required, inert gas levels precisely. 170 Chamber depth 625 mm There is an automatic program which ensures that the evacuation cycle Chamber height 170 mm is ended when the best possible vacuum has been reached. -
Double Seaming Process 41 Buyers Guide
CANTECH INTERNATIONAL MARCH 2014 www.cantechonline.comTech Can INTERNATIONAL MARCH 2014 Soft drinks: has the bubble Inside: burst? Redesigning rams Keeping seams seamless Inspection and testing systems March 2014 Contents March 2014 Volume 21, Number 6 Contents 22 CANTECH INTERNATIONAL MARCH 2014 www.cantechonline.comTech Can INTERNATIONAL MARCH 2014 Soft drinks: has the bubble Inside: burst? Redesigning rams Keeping seams seamless Inspection and testing systems 33 REGULARS Subscription Information 5 Comment DON’T MISS IT! An annual subscription to CanTech International includes 7 World News direct personal delivery of 10 issues per year, weekly email 38 Equipment News 12 newsletter and online access to back issues. The latest machinery and equipment for the can line16 Postal & Digital Issue One Year: 43 £168 UK; £178 Europe; 39 New Products £199 Rest of World Postal & Digital Issue Two Years: New cans and ends in the £292 UK; £315 Europe; market place £352 Rest of World 40 Digital Issue Only (1 year): 40 Filling Focus £160 To subscribe please email Russ Phillips updates readers [email protected] or on the canned craft beer go to www.cantechonline.com and market in the US and reviews click Subscribe. the best cans and beers 38 58 Candid Graham Fenton, chairman 18 Used & refurbished of The Can Makers, talks equipment 30 Inspection & testing to Candid following his Richard Piper takes a closer systems re-election look at the pros and cons Richard Piper talks to the Send address changes to: of new versus used or experts in the field of CanTech International, refurbished equipment inspection and testing, an The Maltings, 57 Bath Street, FEATURES area of vital importance to Gravesend, Kent DA11 0DF, UK. -
Investigation of Corrosion in Canned Tomatoes Processed by Retorting
Investigation of Corrosion in Canned Tomatoes Processed by Retorting THESIS Presented in Partial Fulfillment of the Requirements for the Degree Master of Science in the Graduate School of The Ohio State University By Elliot Dhuey Graduate Program in Food Science and Technology The Ohio State University 2019 Master's Examination Committee: Dr. Melvin Pascall, Advisor Dr. Gerald Frankel Dr. John Litchfield Copyrighted by Elliot Dhuey 2019 Abstract This study investigated the presence of volatile and non-volatile compounds in canned processed tomatoes and how these compounds interacted with the Bisphenol A free epoxy-based lining of the cans to cause corrosion of the base metal and the migration of iron and tin compounds to the tomatoes. The tomatoes tested in this study were the Roma variety. They were sorted, washed, diced, and sealed in two-piece tinplated metal cans. These were processed by retorting at 250°F for 30 minutes then stored at 49°C for up to 50 days. Control samples were packaged and processed in glass jars. The presence and concentrations of the volatile and non-volatile compounds in the processed and unprocessed tomatoes were tested using Selected Ion Flow Tube – Mass Spectrometry (SIFT-MS) and Ion Chromatography – Mass Spectrometry (IC-MS) respectively. After removing the processed tomatoes from the cans, the linings were removed and analyzed for the volatile and non-volatiles as was mentioned before. Scanning Electron Microscopy (SEM) paired with Energy Dispersive X-ray Spectroscopy (EDS) was used to confirm the presence of visual corrosion in the processed cans and to analyze its elemental composition. -
5 Metal Cans Bev Page, Mike Edwards and Nick May
5 Metal cans Bev Page, Mike Edwards and Nick May 5.1 Overview of market for metal cans The total world market for metal containers is estimated at 410 billion units per annum. Of this, drink cans account for 320 billion and processed food cans account for 75 billion. The remainder are aerosol and general line cans. Drink cans may be divided into those for non-carbonated drinks (liquid coffee, tea, sports drinks etc.) and carbonated beverages (soft drinks and beer), many of which pass through a pasteurisation process. 5.2 Container performance requirements Metal packages for food products must perform the following basic functions if the contents are to be delivered to the ultimate consumer in a safe and whole- some manner: • preserve and protect the product • resist chemical actions of product • withstand the handling and processing conditions • withstand the external environment conditions • have the correct dimensions and the ability to be practically interchange- able with similar products from other supply sources (when necessary) • have the required shelf display properties at the point of sale • give easy opening and simple/safe product removal • be constructed from recyclable raw materials. In addition, these functions must continue to be performed satisfactorily until well after the end of the stated shelf life period. Most filled food and drink containers for ambient shelf storage are subjected to some form of heat process to prolong the shelf life of the product. For food cans, this will normally pro- vide a shelf life of up to 2–3 years or more. The heat process cycles used to achieve this are particularly severe and the containers must be specifically designed to withstand these conditions of temperature and pressure cycles in a steam/water atmosphere. -
Food Processing Technology: Principles and Practice, Second
25 Filling and sealing of containers There have been significant developments in packaging systems during the last ten years, prompted by a number of considerations, for example: • marketing requirements for different, more attractive packs • reductions in pack weight to reduce costs and meet environmental concerns over energy and material consumption (Chapter 24) • new packaging requirements for minimally processed foods (Chapters 9, 18, 19) and modified atmosphere packaging (Chapter 20) • the need for new types of tamper-resistant and tamper evident packs. Packaging methods that have been developed to meet these requirements are described in subsequent sections. Accurate filling of containers is important to ensure compliance with fill-weight legislation and to prevent ‘give-away’ by overfilling. The composition of some foods (for example meat products such as pies and canned mixed vegetables) is also subject to legislation in some countries, and accurate filling of multiple ingredients is therefore necessary. The maintenance of food quality for the required shelf life depends largely on adequate sealing of containers. Seals are the weakest part of a container and also suffer more frequent faults during production, such as food trapped in a seal, incorrect sealing temperatures or can seamer settings. In this chapter the techniques used to fill and seal rigid and flexible containers are described. By themselves these operations have no effect on the quality or shelf life of foods, but incorrect filling or sealing has a substantial effect on foods during subsequent storage. 25.1 Rigid and semi-rigid containers ‘Commercially clean’ metal and glass containers are supplied as palletised batches, which are wrapped in shrink or stretch film (Section 25.1.3) to prevent contamination. -
Food Safety Information-2015
Food Safety Information Our Mission Our mission is to feed Southwest Virginia’s hungry through a network of partners and engage our region in the fight to end hunger. Abingdon Distribution Center Salem Distribution Center 21452 Gravel Lake Road 1025 Electric Road Abingdon, VA 24211 Salem, VA 24153 (276) 628-9266 (540) 342-3011 Fax (540) 342-0056 Fax (276) 628-3947 www.faswva.org Revised 5/13/2015 Contents Food Safety ................................................................................................................................................... 3 Disclaimer of Warranties and Limitation of Liability ................................................................................ 3 Distressed Canned Food Guide ................................................................................................................. 3 Cans Not Approved for Use: ..................................................................................................................... 3 Additional Information.............................................................................................................................. 3 Storage and Handling of Product: ............................................................................................................. 4 Transport of refrigerated and frozen Food Bank products:...................................................................... 4 Food Container Inspection Guidelines .....................................................................................................