Fiberspectrum Issue 15 - No.1/2007 the Magazine of Andritz Pulp&Paper
Total Page:16
File Type:pdf, Size:1020Kb
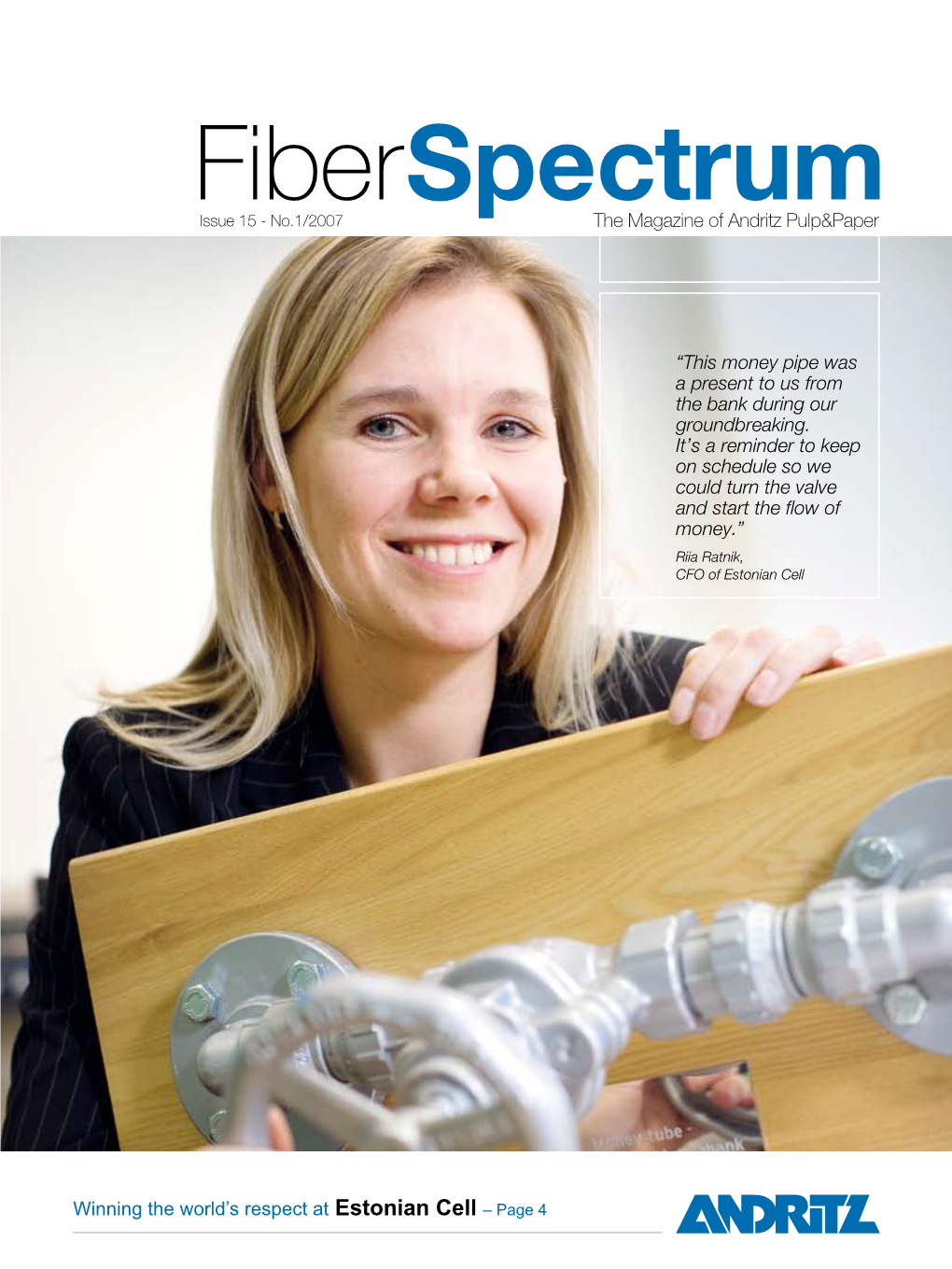
Load more
Recommended publications
-
Natural Gas in China's Power Sector
December 2020 Natural gas in China’s power sector: Challenges and the road ahead China’s pledge to peak its emissions before 2030 suggests that decarbonization of its coal-dominant power sector will be key to fulfilling this goal. Natural gas emits around 50 per cent less greenhouse gases than coal when used in electricity generation.1 With the rapid deployment of variable renewables, gas-fired power plants could also enhance the flexibility of the power system and boost renewables integration. However, the development of natural gas in China’s power sector has been slow, with installed gas-fired capacity standing at 97 GW by October 2020 out of 2,100 GW total installed generating capacity, according to the latest data by the China Electricity Council.2 This falls short of the target of 110 GW by 2020, set out in the 13th Five Year plan (2016–2020). Gas-fired generation only accounted for 3.2 per cent of China’s total power production in 2019, significantly below coal’s share of 62 per cent. Average running hours were 2,646 last year, indicating that gas-fired power plants have been underutilized. This analysis discusses the latest developments in China’s gas-fired power generation, the main challenges, and the road ahead both in the context of the upcoming 14th Five-Year Plan and the recently announced 2060 carbon neutrality goal. Expensive imported gas, costly turbine technology, and the lack of fully competitive electricity markets have been the main obstacles limiting the role of natural gas in China’s power sector. -
"Running Man" to "Mission X": Variety Shows As Cultural Representation of Local Identities
From "Running Man" to "Mission X": Variety Shows as Cultural Representation of Local Identities Nurul Laili Nadhifah, Universitas Brawijaya, Indonesia The Asian Conference on Media, Communication & Film 2018 Official Conference Proceedings Abstract Running Man, as one of Korean successful variety shows, never fails to advertise parts of Korean culture like food, K-Pop, cultural values, traditional games, history, even historical sites. With quite a huge amount of fans not only from South Korea but also from other countries as well, Running Man also occasionally encourages interactions between the hosts and their fans in some games, indirectly introducing Korean culture to all over the world, resulting in the increase of consumption on Korean culture’s products. This reality show concept is, then, adapted into Indonesian variety show called Mission X. Quite different from Running Man, Mission X has its own ways in introducing Indonesia and its culture. This study aims to analyze the way Running Man and Mission X represent themselves as the platforms of advertising their local identities by applying Fiske’s vertical intertextuality and cultural identity theories. Drawing on data collected from the shows as the main texts and SNS as secondary texts, while data of fans’ reactions are gathered by doing random interview online. This research, through comparative studies, intents to explain the similarities and differences of cultural representations shown on those shows. The findings show different aspects of local culture displayed by those variety shows caused different methods of representing them. While Running Man introducing different aspects and values of culture like food or history through games and certain themes, Mission X tends to introduce cultural aspects more through display of setting. -
Drink-10-User-Manual-2020.Pdf
WOSON Medical System Technical Publications ASS0010 REV-A DRINK10 Water Distiller Operation Manual Operation Documentation Copyright © 2013 By Ningbo Woson Medical Instrument Co., Ltd.. Woson Medical Instrument Co., Ltd Address: No.19, Lane 346, Changxing Road, Jiangbei District, Ningbo 315032, China Tel: 86-574-83022668 Fax:86-574-87639376 Website:http://www.woson.com.cn E-mail: [email protected] DRINK10 Distiller Operation Manual Regulatory Requirement This product complies with regulatory requirements of the following European Directive 93/42/EEC concerning medical devices. Revision History Rev Issue Date Reason For Change Rev-A 2011.01.28 First Issue Rev-B 2013.06.01 Updating Please verify that you are using the latest revision of this document. Information pertaining to this document is maintained on manufactory. If you need to know the latest revision, please contact your distributor, sales representative, or our service dept. Regulatory Requirements Conformance Standards The content of this instruction is fit for water distiller. Above water distiller in accordance with the requirements of 93/42/EEC EN 61010-1 Certifications Manufacturer is ISO 9001 and ISO 13485 certified. REV-B Page 1 of 14 DRINK10 Distiller Operation Manual Content Regulatory Requirement ............................................................................................................ 1 Revision History ......................................................................................................................... 1 Regulatory Requirements -
Adoption, Orphanages, and Children with Disabilities
CHINA’S CHILDREN: ADOPTION, ORPHANAGES, AND CHILDREN WITH DISABILITIES ROUNDTABLE BEFORE THE CONGRESSIONAL-EXECUTIVE COMMISSION ON CHINA ONE HUNDRED SEVENTH CONGRESS SECOND SESSION OCTOBER 21, 2002 Printed for the use of the Congressional-Executive Commission on China ( Available via the World Wide Web: http://www.cecc.gov U.S. GOVERNMENT PRINTING OFFICE 83–513 PDF WASHINGTON : 2003 For sale by the Superintendent of Documents, U.S. Government Printing Office Internet: bookstore.gpo.gov Phone: toll free (866) 512–1800; DC area (202) 512–1800 Fax: (202) 512–2250 Mail: Stop SSOP, Washington, DC 20402–0001 VerDate 11-MAY-2000 09:17 Jan 07, 2003 Jkt 000000 PO 00000 Frm 00001 Fmt 5011 Sfmt 5011 83513.TXT China1 PsN: China1 CONGRESSIONAL-EXECUTIVE COMMISSION ON CHINA LEGISLATIVE BRANCH COMMISSIONERS Senate House MAX BAUCUS, Montana, Chairman DOUG BEREUTER, Nebraska, Co-Chairman CARL LEVIN, Michigan JIM LEACH, Iowa DIANNE FEINSTEIN, California DAVID DREIER, California BYRON DORGAN, North Dakota FRANK WOLF, Virginia EVAN BAYH, Indiana JOE PITTS, Pennsylvania CHUCK HAGEL, Nebraska SANDER LEVIN, Michigan BOB SMITH, New Hampshire MARCY KAPTUR, Ohio SAM BROWNBACK, Kansas SHERROD BROWN, Ohio TIM HUTCHINSON, Arkansas JIM DAVIS, Florida EXECUTIVE BRANCH COMMISSIONERS PAULA DOBRIANSKY, Department of State GRANT ALDONAS, Department of Commerce D. CAMERON FINDLAY, Department of Labor LORNE CRANER, Department of State JAMES KELLY, Department of State IRA WOLF, Staff Director JOHN FOARDE, Deputy Staff Director (II) VerDate 11-MAY-2000 09:17 Jan 07, 2003 Jkt 000000 PO 00000 Frm 00002 Fmt 0486 Sfmt 0486 83513.TXT China1 PsN: China1 C O N T E N T S Page STATEMENTS Robertson, Nancy, president and CEO, the Grace Children’s Foundation, New York, NY .............................................................................................................. -
Oil & Gas Pipeline Monitoring and SCADA Communication Network
Industrializing the Ethernet, Simplifying Industrial Communication www.kyland.com Head Office,Asia Pacific and China EMEA (Europe, Middle East, Africa) Americas Kyland Technology Co.,Ltd. Kyland Technology EMEA GmbH KYLAND CORPORATION AMERICAS Address: Building No.2, Shixing Avenue 30# Address: Esslingerstrasse 7 (BOC) Address: 2010 Crow Canyon Place Ste. 100, San Shijingshan District, Beijing, 100144, China 70771 Leinfelden-Echterdingen, Germany Ramon, CA 94583, USA Tel: +86-10-88798888 Tel: +49 (0) 711 997606-200 Tel: +1-510-717-4082 Fax: +86-10-88796678 Fax: +49 (0) 711 997606-211 Email: [email protected] Email: [email protected] Email: [email protected] V2.0 OIL&GAS AUTOMATION SOLUTIONS Industrializing the Ethernet, Simplifying Industrial Communication www.kyland.com Company Profile Kyland Technology Co. Ltd. is focusing on the research and implementation of industrial control networking total solutions. We are a leading Chinese company of industrial networking technology innovation and exploration. Our mission is to build the next generation industrial control ecosystem based on internet connectivity. Kyland's primary R&D directions are: industrial Ethernet communications technologies, IP-based industrial fieldbus technologies, network-based field controller technologies, cloud-based industrial controlling server technologies, network-based controlling precise time/clock technologies, control message communication security technologies. Kyland has been involved in the 3 international standards for industrial automation: IEC61158, IEC62439, IEEE C37.238, and the Chinese national standard GBT 30094. With the well-known test and certificates such as KEMA, CE/ FCC, UL508, ATEX/IECEx, Class1 Div.2, DNV... etc., our products have been deployed worldwide, and have been proven to meet the requirements of rigorous environments like nuclear power plants, substations, oil & gas fields, railway & public transportation, ITS, marine, and military. -
A Shared Recommendation List for Summer Leisure Time Chinese/Taiwanese-American Films and Books
A Shared Recommendation List for Summer Leisure Time Chinese/Taiwanese-American films and books FILM LIST [In random order] Documentary Film: Minding the Gap (2018) Director: Bing Liu With: Keire Johnson, Zack Mulligan, Bing Liu Three childhood friends united in their love for skateboarding grow up in a small Illinois town in front of our eyes in filmmaker Bing Liu’s Oscar-nominated documentary, with searing observations on race, class and masculinity. Read a review: https://www.nytimes.com/2018/08/16/movies/minding-the-gap-review- documentary.html Feature Film: Chan is Missing Feature Film: Saving Face (2004) Director: Alice Wu Cast: Michelle Krusiec, Joan Chen, Lynn Chen A young surgeon keeps her sexual identity a secret from her mom, who has secrets of her own. A hallmark of lesbian cinema and a beloved comedy of Chinese American women negotiating family honor. Feature Film: Better Luck Tomorrow (2002) Director: Justin Lin Cast: Parry Shen, Jason Tobin, Sung Kang, Roger Fan “Fast & Furious” franchise helmer Justin Lin made his solo directing debut with this Sundance hit, a high school crime drama about Asian American overachievers breaking bad that sent the model minority myth spinning. It remains a milestone for ferociously defiant Asian American storytelling. Read a Review: https://www.theatlantic.com/entertainment/archive/2018/08/how-better-luck- tomorrow-argued-for-its-existence-15-years-ago/568045/ Films that will be screened in Chinese Classes: Chinese 101 The Farewell ALC 325 Chinese Cinema: Ideology and the Box office The Joy -
Announcement of Interim Results for the Six Months Ended 30 June 2020
Hong Kong Exchanges and Clearing Limited and The Stock Exchange of Hong Kong Limited take no responsibility for the contents of this announcement, make no representation as to its accuracy or completeness and expressly disclaim any liability whatsoever for any loss howsoever arising from or in reliance upon the whole or any part of the contents of this announcement. (Stock Code: 0832) ANNOUNCEMENT OF INTERIM RESULTS FOR THE SIX MONTHS ENDED 30 JUNE 2020 FINANCIAL HIGHLIGHTS • Revenue for the six months ended 30 June 2020 amounted to RMB13,019 million, an increase of 43.6% compared with the corresponding period in 2019. • Gross profit margin for the period was 23.7%, a decrease of 3.6 percentage points compared with 27.3% for the corresponding period in 2019. • Profit attributable to equity shareholders of the Company for the period amounted to RMB727 million, an increase of 10.5% compared with the corresponding period in 2019. • Net profit margin for the period was 6.0%, a decrease of 2.5 percentage points compared with 8.5% for the corresponding period in 2019. • Basic earnings per share for the period was RMB26.43 cents, an increase of 9.8% compared with the corresponding period in 2019. • An interim dividend of HK11.0 cents per share for the six months ended 30 June 2020. 1 INTERIM RESULTS The board (the “Board”) of directors (the “Directors” and each a “Director”) of Central China Real Estate Limited (the “Company”) hereby announces the unaudited consolidated results of the Company and its subsidiaries (collectively, the “Group”) for -
Exploring Academic Socialization and Identity of Chinese Undergraduate Students in the U.S
Exploring Academic Socialization and Identity of Chinese Undergraduate Students in the U.S. Wei Zuo A dissertation submitted in partial fulfillment of the requirements for the degree of Doctor of Philosophy University of Washington 2015 Reading Committee: Sandra Silberstein, Chair Priti Sandhu Suhanthie Motha Stevan Harrell Program Authorized to Offer Degree: Department of English 1 ©Copyright 2015 Wei Zuo 2 University of Washington Abstract Exploring Academic Socialization and Identity of Chinese Undergraduate Students in the U.S. Wei Zuo Chair of the Supervisory Committee: Sandra Silberstein, Professor of English Department of English Under the worldwide trend of internationalization of higher education, the number of Chinese students studying in the U.S. has increased dramatically in the past ten years. In some American universities, such as a large research university in the Pacific Northwest of the U.S. where this research was conducted, Chinese students are the largest segment among all the international students. Through the lens of poststructuralist conceptualization of identity (Bloomberg & Volpe, 2008; Hall, 1996), communities of practice (Lave & Wenger, 1991; Wenger,1998), investment (Norton Peirce, 1995) and imagined communities (Kanno & Norton, 2003), this research focused on Chinese undergraduate students’ academic socialization experiences in the U.S., especially concerning their proficiency in English and academic knowledge, their interactions with professors, TAs and classmates, and their understandings of their identities over time. This study 3 offered opportunities for Chinese undergraduate students’ to have their voices heard and their stories shared. Through mixed qualitative methods with ethnographic characteristics, such as interviews and observations, the research interpreted experiences of six student participants, found differences and commonalities among them, and factors that influenced their experiences. -
SUMMER / 2013 Wang Anyi Yi Sha Bai Hua Bi Feiyu Li Hao Zang Di Jiang Yun Lu Nei Yang Li Speed Photo by Qiu Lei
PATHLIGHT NEW CHINESE WRITING SUMMER / 2013 Wang Anyi Yi Sha Bai Hua Bi Feiyu Li Hao Zang Di Jiang Yun Lu Nei Yang Li Speed Photo by Qiu Lei PATHLIGHT / SUMMER - 2013 1 Photo by Wang Yan PATHLIGHT SUMMER / 2013 Summer 2013 ISBN 978-7-119-08377-3 © Foreign Languages Press Co. Ltd, Beijing, China, 2013 Published by Foreign Languages Press Co. Ltd. 24 Baiwanzhuang Road, Beijing 100037, China http://www.flp.com.cn E-mail: [email protected] Distributed by China International Book Trading Corporation 35 Chegongzhuang Xilu, Beijing 100044, China P.O. Box 399, Beijing, China Printed in the People’s Republic of China CONTENTS Fiction 004 Wang Anyi _ In the Belly of the Fog _ 4 Tradition and Rebellion: A Conversation with Wang Anyi _ 12 Bi Feiyu _ The Deluge _ 18 A Professional Interest in Suffering: A Conversation with Bi Feiyu _ 36 Jiang Yun _ The Red Detachment of Women _ 46 Li Hao _ The General _ 58 Lu Nei _ Keep Running, Little Brother _ 66 A Yi _ Two Lives _ 88 Ren Xiaowen _ I Am Fish _ 100 Su Cici _ The Zebra That Didn’t Exist _ 110 Sheng Tie _ The Train Was Clean and Cool _ 122 Poetry 132 Bai Hua _ Small Town Tale, Village, 1977, Mock Nursery Rhyme, The Illusion of Life, Thoughts Arising from the Pig _ 132 Yang Li _ Fated, An Old Poem, The White Horse, Courthouse (I) _ 138 Yi Sha _ Rhythm is What Matters, Memories Evoked by Reality, Notes on Mt. -
5G Industry Application - Differentiate, Synergy and Centralized Operation
Dan Chen Senior MEC Director, China Unicom New network demands for 5G industry application - Differentiate, Synergy and Centralized Operation Wide Area Internet of Multi- Smart AR/VR/MR Health Power Vehicles Sites Care City Business Local Area Demand Video surveillance Industrial control Industrial vision Cloud Network • Bandwidth: 4M~12M • Bandwidth: • Bandwidth: 4M~12M • Ultra low latency 80Mbps~500Mbps • latency: <10ms • Local Traffic Redirection • • Wide Converge • LBS(< 1meter) Lossless compression • Cross region connection • Local Traffic Redirection • Encryption protection • L2 Network • • • AI Cloud/Edge Orchestration Cross-region self-service • Unify Operation Differentiation SLA Determinative experience Business Iteration Self-service Network Isolation:Local traffic routing & Network Slicing Latency: 5-15ms Self-service portal for users Requirement dedicate network space Deployment:< 24 hr Function:LBS/Video/AI Availability :99.9%~99.9999% MEC: On-primise Monitoring, Management Differentiation MEC & 5G Cloud , Edge and Centralized Operation Operator Private Network Network Synergy • Customized private network section under • Central Cloud , Edge and network • Centralized support Capability Synergy public network • Automated operation • • Multi-region support Low latency, High security , • Self-service entry for clients • Edge Computing • 5G ecosystem • End-to-end 2 China Unicom 5G MEC - Low-latency network and high-quality edge computing 5G MEC =(Edge Network + Edge Computing)x Edge Ecosystem x Integrated Service A 5G-based platform over mobile edge network with edge computing capability providing end-to-end ICT services which Product , are integrated, open, synergy and elastic. It help users to deploy service close to business with better performance and better Definition cost-effective . 01. On-Site:Dedicated Model Edge FW Self-service Portal UPF/ VAS MEP ME-APP Edge L2 /L3 Network DP For 2B customers, to provide "plug and play integrated" dedicated services to meet intact user data for high security requirements. -
An Efficient Virtual Machine Consolidation Scheme For
sensors Article An Efficient Virtual Machine Consolidation Scheme for Multimedia Cloud Computing Guangjie Han 1,*, Wenhui Que 1, Gangyong Jia 2 and Lei Shu 3 1 Department of Information and Communication Systems, Hohai University, 200 North Jinling Road, Changzhou 213022, China; [email protected] 2 Department of Computer Science, Hangzhou Dianzi University, Hangzhou 310018, China; [email protected] 3 Guangdong Petrochemical Equipment Fault Diagnosis Key Laboratory, Guangdong University of Petrochemical Technology, Guangdong 525000, China; [email protected] * Correspondence: [email protected]; Tel.: +86-519-8519-1841; Fax.: +86-519-8519-1838 Academic Editor: Antonio Jara Received: 7 January 2016; Accepted: 14 February 2016; Published: 18 February 2016 Abstract: Cloud computing has innovated the IT industry in recent years, as it can delivery subscription-based services to users in the pay-as-you-go model. Meanwhile, multimedia cloud computing is emerging based on cloud computing to provide a variety of media services on the Internet. However, with the growing popularity of multimedia cloud computing, its large energy consumption cannot only contribute to greenhouse gas emissions, but also result in the rising of cloud users’ costs. Therefore, the multimedia cloud providers should try to minimize its energy consumption as much as possible while satisfying the consumers’ resource requirements and guaranteeing quality of service (QoS). In this paper, we have proposed a remaining utilization-aware (RUA) algorithm for virtual machine (VM) placement, and a power-aware algorithm (PA) is proposed to find proper hosts to shut down for energy saving. These two algorithms have been combined and applied to cloud data centers for completing the process of VM consolidation. -
02 山水自然保护中心 2016 年报 Publisher | Shan Shui Conservation Center
02 山水自然保护中心 2016 年报 Publisher | Shan Shui Conservation Center Editors-in-chief | Wang Yan Wen Cheng Editors-in-charge | Yu Lu Gao Xiangyu Proofreaders | Yu Lu Gao Xiangyu Feng Yanqiu Art editor | He Qinghua Translator | Hu Jing Address | Peking University Conservation Biology Building, Haidian District, Beijing, 100871, China Tel | 010-62761034 Fax | 010-62761035 Web | http://www.shanshui.org QR Code to Shan Shui's WeChat page Email | [email protected] The collared owlet / photo by Gao Xiangyu ◎ CONTENTS shan shui Foreword Value Chains | Guardians Alliance 04 Ten-Year Milestones Lancang River Conservation Fund 06 40 Conservation Story: We are Born in the Cross- 08 Director's Message 45 border Rainforest Shan Shui 2016 10 International Nature Watch Festival in Namsee 48 12 Work Map Great Valley When Nature Reserves Become National Parks: 49 Will Humans Drive Wildlife Away? Fellowship | Conservation Research Land-Trust Conservation: Baixiongping Station Nature Watch 53 16 The Guardians' Story | True and Romantic Natural Heritage Conservation 54 17 The Little Wood Cabin: 365 Days in the Mountains Conservation-based Research 18 Volunteer Scientists 60 Conservation Story: 20 “Submerged Forest”: Why Should We Care for Stray Tibetan Dogs? 61 An Army of Species Show Up in Summer Palace! Snow Leopard China: 63 Field Practice | Community-based A Nongovernmental Snow Leopard Research and Conservation Conservation Network Grassland: Sanjiangyuan Conservation on Tibet- About Us 28 an Plateau Board Members 64 Conservation Story: My Life with Snow Leopards 29 Financial Overview 65 Watersheds: Conservation in the Southwestern 33 Our Team Mountain Areas 65 Conservation Story: 33 The Guanba Community-based Protected Area: Acknowledgments What Our Village Might Look Like in 50 Years 66 Forest and Climate Change 37 Forest: The Yunlong Tianchi Forest Restoration 37 Fresh Water: Beijing Urban Wetland Restoration 37 Foreword The year 2016 ended as a year of action for NGOs in China.