Drive-Train Basics
Total Page:16
File Type:pdf, Size:1020Kb
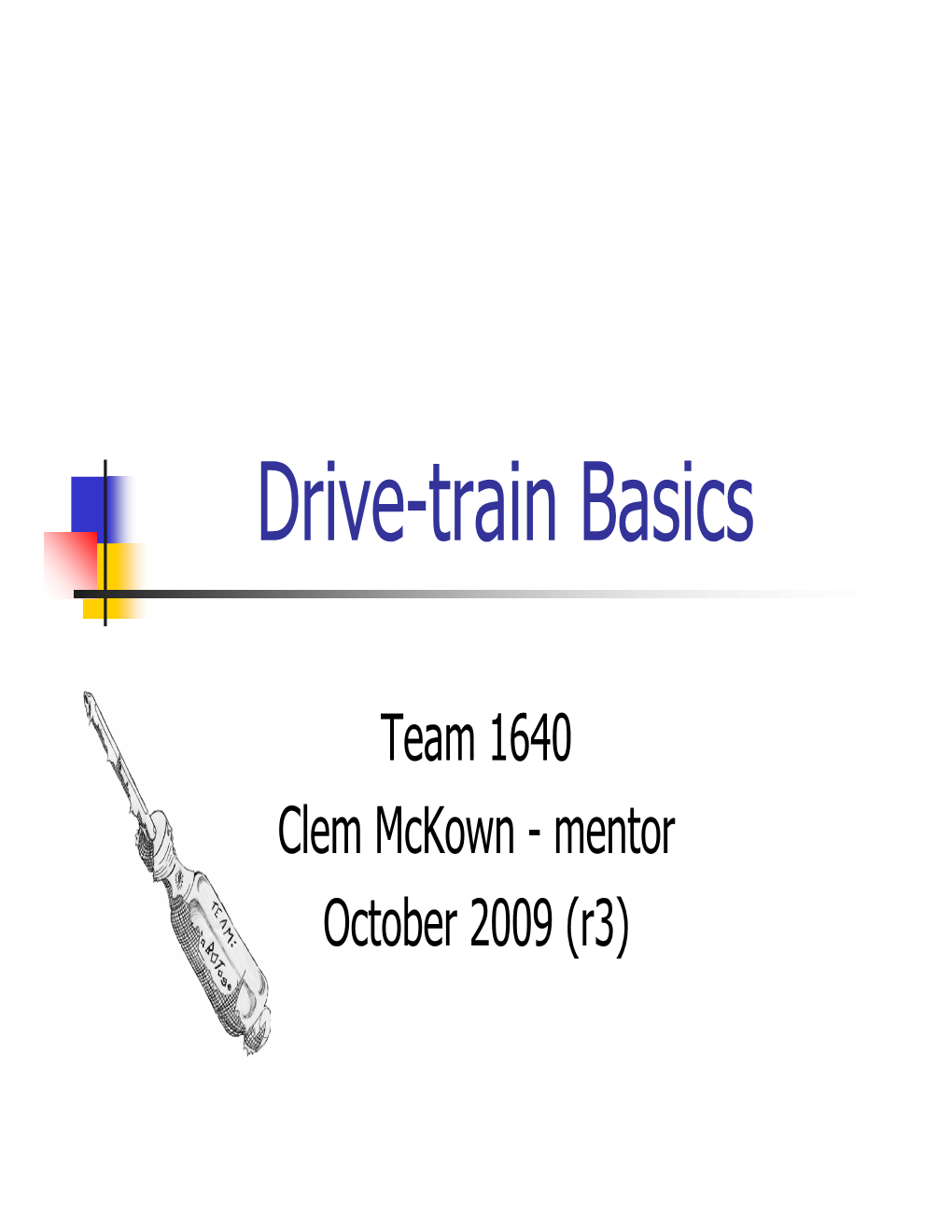
Load more
Recommended publications
-
RC Baja: Drivetrain Nick Paulay [email protected]
Central Washington University ScholarWorks@CWU All Undergraduate Projects Undergraduate Student Projects Winter 2019 RC Baja: DriveTrain Nick Paulay [email protected] Follow this and additional works at: https://digitalcommons.cwu.edu/undergradproj Part of the Mechanical Engineering Commons Recommended Citation Paulay, Nick, "RC Baja: DriveTrain" (2019). All Undergraduate Projects. 79. https://digitalcommons.cwu.edu/undergradproj/79 This Undergraduate Project is brought to you for free and open access by the Undergraduate Student Projects at ScholarWorks@CWU. It has been accepted for inclusion in All Undergraduate Projects by an authorized administrator of ScholarWorks@CWU. For more information, please contact [email protected]. Central Washington University MET Senior Capstone Projects RC Baja: Drivetrain By Nick Paulay (Partner: Hunter Jacobson-RC Baja Suspension & Steering) 1 Table of Contents Introduction Description Motivation Function Statement Requirements Engineering Merit Scope of Effort Success Criteria Design and Analyses Approach: Proposed Solution Design Description Benchmark Performance Predictions Description of Analyses Scope of Testing and Evaluation Analyses Tolerances, Kinematics, Ergonomics, etc. Technical Risk Analysis Methods and Construction Construction Description Drawing Tree Parts list Manufacturing issues Testing Methods Introduction Method/Approach/Procedure description Deliverables Budget/Schedule/Project Management Proposed Budget Proposed Schedule Project Management Discussion Conclusion Acknowledgements References Appendix A – Analyses Appendix B – Drawings Appendix C – Parts List Appendix D – Budget Appendix E – Schedule Appendix F - Expertise and Resources 2 Appendix G –Testing Data Appendix H – Evaluation Sheet Appendix I – Testing Report Appendix J – Resume 3 Abstract The American Society of Mechanical Engineers (ASME) annually hosts an RC Baja challenge, testing a RC car in three events: slalom, acceleration and Baja. -
Atlas Motion Platform Split-Axle Mecanum Wheel Design
ATLAS MOTION PLATFORM SPLIT-AXLE MECANUM WHEEL DESIGN Jane M. Schwering, Mila J.E. Kanevsky, M. John D. Hayes, Robert G. Langlois Department of Mechanical and Aerospace Engineering, Carleton University, Ottawa, ON K1S 5B6, Canada Email: [email protected]; [email protected]; [email protected]; [email protected] ABSTRACT The Atlas motion platform was conceptually introduced in 2005 as a 2.90 m diameter thin-walled compos- ite sphere housing a cockpit. Three active mecanum wheels provide three linearly independent torque inputs enabling the sphere to enjoy a 100% dexterous reachable workspace with unbounded rotations about any axis. Three linearly independent translations of the sphere centre, decoupled from the orientation workspace, are provided by a translational 3-DOF platform. Small scale and half-scale demonstrators introduced in 2005 and 2009 respectively gave us the confidence needed to begin the full-scale design. Actuation and control of Atlas full-scale is nearing completion; however, resolution of several details have proven extremely illusive. The focus of this paper is on the design path of the 24 passive mecanum wheels. The 12 passive wheels below the equator of the sphere help distribute the static and dynamic loads, while 12 passive wheels above the equator, attached to a pneumatically actuated halo, provide sufficient downward force so that the normal force between the three active wheel contact patches and sphere surface enable effective torque transfer. This paper details the issues associated with the original twin-hub passive wheels, and the resolution of those issues with the current split-axle design. Results of static and dynamic load tests are discussed. -
Development of a Ball Balancing Robot with Omni Wheels
ISSN 0280-5316 ISRN LUTFD2/TFRT--5897--SE Development of a ball balancing robot with omni wheels Magnus Jonason Bjärenstam Michael Lennartsson Lund University Department of Automatic Control March 2012 Lund University Document name MASTER THESIS Department of Automatic Control Date of issue Box 118 March 2012 SE-221 00 Lund Sweden Document Number ISRN LUTFD2/TFRT--5897--SE Author(s) Supervisor Magnus Jonason Bjärenstam Anders Robertsson, Dept. of Automatic Michael Lennartsson Control, Lund University, Sweden Rolf Johansson, Dept. of Automatic Control, Lund University, Sweden (examiner) Sponsoring organization Title and subtitle Development of a ball-balancing robot with omni-wheels (Bollbalanserande robot med omnihjul) Abstract The main goal for this master thesis project was to create a robot balancing on a ball with the help of omni wheels. The robot was developed from scratch. The work covered everything from mechanical design, dynamic modeling, control design, sensor fusion, identifying parameters by experimentation to implementation on a microcontroller. The robot has three omni wheels in a special configuration at the bottom. The task to stabilize the robot is based on the simplified model of controlling a spherical inverted pendulum in the xy-plane with state feedback control. The model has accelerations in the bottom in the x- and y-directions as inputs. The controlled outputs are the angle and angular velocity around the x- and y-axes and the position and speed along the same axes.The goal to stabilize the robot in an upright -
Analysis of the Fuel Economy Benefit of Drivetrain Hybridization
NREL/CP-540-22309 ● UC Category: 1500 ● DE97000091 Analysis of the Fuel Economy Benefit of Drivetrain Hybridization Matthew R. Cuddy Keith B. Wipke Prepared for SAE International Congress & Exposition February 24—27, 1997 Detroit, Michigan National Renewable Energy Laboratory 1617 Cole Boulevard Golden, Colorado 80401-3393 A national laboratory of the U.S. Department of Energy Managed by Midwest Research Institute for the U.S. Department of Energy under contract No. DE-AC36-83CH10093 Work performed under Task No. HV716010 January 1997 NOTICE This report was prepared as an account of work sponsored by an agency of the United States government. Neither the United States government nor any agency thereof, nor any of their employees, makes any warranty, express or implied, or assumes any legal liability or responsibility for the accuracy, completeness, or usefulness of any information, apparatus, product, or process disclosed, or represents that its use would not infringe privately owned rights. Reference herein to any specific commercial product, process, or service by trade name, trademark, manufacturer, or otherwise does not necessarily constitute or imply its endorsement, recommendation, or favoring by the United States government or any agency thereof. The views and opinions of authors expressed herein do not necessarily state or reflect those of the United States government or any agency thereof. Available to DOE and DOE contractors from: Office of Scientific and Technical Information (OSTI) P.O. Box 62 Oak Ridge, TN 37831 Prices available by calling 423-576-8401 Available to the public from: National Technical Information Service (NTIS) U.S. Department of Commerce 5285 Port Royal Road Springfield, VA 22161 703-605-6000 or 800-553-6847 or DOE Information Bridge http://www.doe.gov/bridge/home.html Printed on paper containing at least 50% wastepaper, including 10% postconsumer waste 970289 Analysis of the Fuel Economy Benefit of Drivetrain Hybridization Matthew R. -
Design of an Omnidirectional Universal Mobile Platform
Design of an omnidirectional universal mobile platform R.P.A. van Haendel DCT 2005.117 DCT traineeship report Supervisors: prof. M. Ang. Jr, National University of Singapore Prof. Dr. Ir. M. Steinbuch, Eindhoven University of Technology National University of Singapore Department of Mechanical Engineering Robotics and Mechatronics group Eindhoven University of Technology Department of Mechanical Engineering Dynamics and Control Technology Group Eindhoven, September 2005 2 Contents 1 Introduction 1 2 Omnidirectional mobility 3 3 Specifications 5 3.1 Dimensions ..................................... 5 3.2 Dynamics ...................................... 5 3.3 Control ....................................... 5 4 Concepts 7 4.1 Specialwheeldesigns.. .. .. .. .. .. .. ... 7 4.1.1 Omniwheel ................................. 7 4.1.2 Mecanumwheel .............................. 8 4.1.3 Orthogonalwheels ............................. 8 4.2 Conventionalwheeldesign. .... 9 4.2.1 Poweredcastorwheel ........................... 9 4.2.2 Poweredoffsetcastorwheel . 9 4.3 Otherdesigns.................................... 10 4.3.1 Omnitracks ................................. 10 4.3.2 Legs..................................... 10 5 choice of concepts 13 5.1 Selection....................................... 13 6 System design 15 6.1 Mechanicalsystem ................................ 15 6.2 Electricalsystem ................................ 15 6.3 Software....................................... 16 7 Modelling 17 7.1 Kinematics ..................................... 17 -
Drive Train Selection
Selecting the best drivetrains for your fleet vehicles Drivetrain Basics FWD RWD AWD 4WD Front-wheel drive Rear-wheel drive All-wheel drive (AWD) 4WD generally (FWD) is the most (RWD) is regaining vehicles drive all four requires manually common form of popularity due to wheels. AWD is used switching between engine/transmission consumer demand to market vehicles two-wheel drive for layout; the engine for performance; the that switch from two streets and a drives only the front engine drives only drive wheels to four four-wheel drive for wheels. the rear wheels. as needed. low traction areas. Two-wheel drive (2WD) is used to describe vehicles able to power two wheels at most. For vehicles with part-time four-wheel drive (4WD), the term refers to the mode when 4WD is deactivated and power is applied to only two wheels. Sedans | Minivans | Crossovers Pickups | Full-Size Vans | SUVs Generally FWD, RWD and AWD Generally 2WD and 4WD Element Fleet Management ® Acquisition Cost FWD RWD AWD 2WD 4WD FWD less expensive RWD can be more AWD generally most due to fewer expensive due to more expensive due to more 4WD is more expensive than 2WD due to components and more components and parts than FWD and heavier-duty components efficient manufacturing additional time to RWD assemble Select vehicles based on intended function and operating environment rather than acquisition cost, as these factors largely dictate operating costs Operating Expenses: Fuel Efficiency FWD RWD AWD 2WD 4WD FWD more efficient More parts for RWD More parts for AWD 2WD gets better -
Improved Mecanum Wheel Design for Omni-Directional Robots
Proc. 2002 Australasian Conference on Robotics and Automation Auckland, 27-29 November 2002 Improved Mecanum Wheel Design for Omni-directional Robots Olaf Diegel, Aparna Badve, Glen Bright, Johan Potgieter, Sylvester Tlale Mechatronics and Robotics Research Group Institute of technology and Engineering, Massey University, Auckland [email protected] , mechatronics.massey.ac.nz Abstract wheels to the desired direction whenever it needs to travel Omni-directional is used to describe the ability of in a trajectory with non-continuous curvatures a system to move instantaneously in any (Dubowsky, Skwersky, Yu, 2000). direction from any configuration. Omni- directional robotic platforms have vast Most special wheel designs are based on a concept that advantages over a conventional design in terms achieves traction in one direction and allow passive of mobility in congested environments. They are motion in another, thus allowing greater flexibility in capable of easily performing tasks in congested environments (West and Asada, 1997). One of environments congested with static and dynamic the more common omni-directional wheel designs is that obstacles and narrow aisles. These environments of the Mecanum wheel, invented in 1973 by Bengt Ilon, are commonly found in factory workshops an engineer with the Swedish company Mecanum AB. offices, warehouses, hospitals and elderly care Many of the other commonly currently used designs are facilities. based on Ilon’s original concept. This paper proposes an improved design for a 2 The conventional Mecanum wheel Mecanum wheel for omni-directional robots. Ilon’s Mecanum wheel is based on the principle of a This design will improve the efficiency mobile robots by reducing frictional forces and thereby central wheel with a number of rollers placed at an angle around the periphery of the wheel. -
Selection of Wheels in Robotics Jigar J
International Journal of Scientific & Engineering Research, Volume 5, Issue 10, October-2014 339 ISSN 2229-5518 Selection of Wheels in Robotics Jigar J. Parmar, Chirag V. Savant Abstract—Robotics is an emerging field in coming years. Today robots are used in wide applications, like material handling, mechanical controls, welding etc. For locomotive purpose robots are made with integrated driving system wherein wheels and driving motors are coupled to drive robots. This paper explains and gives details about the wheels and the significance of selecting the optimum one for the respective Robots which are required to compete in the challenge. The Wheels were selected on the factors and methods based on the degrees of freedom, weight distribution, wheel geometry, field material and wheel material. The system defined in this paper, is cost effective and rugged. This system can be implemented for various types of Robots and provides the perfect fit in terms of mobility, locomotion and ideal stability. Keywords—Holonomic drive, Mecanum wheels, Omni wheels, Robotics ———————————————————— 1-INTRODUCTION 1.1 Cylindrical wheels These are wheels that have a cylindrical periphery. The periphery may or may not have tracks on it. These can be conventionally made out of different materials by turning them on turn centres according to the required wheel base and diameter. To give additional friction to the surface some high traction material like, rubber or polyurethane grip can be put over it. Fig.2 Omni-Wheel with rollers 1.3 Mecanum wheels These are wheels quiet similar to Omni but the rollers are IJSERinclined at an angle of 45 degrees with respect to the axis of the base wheel. -
On Modeling and Control of Omnidirectional Wheels
Budapest University of Technology and Economics Department of Control Engineering and Information Technology Viktor Kálmán On modeling and control of omnidirectional wheels PhD. dissertation Advisor: Dr. László Vajta Budapest 2013. Abstract Mobile robots are more and more commonly used for everyday automated transportation and logistics tasks; they carry goods, parts and even people. When maneuvers in cluttered environments are executed with expensive loads the need for reliable, safe and efficient movement is paramount. This dissertation is written with the goal of solving some problems related to a special class of mobile transport robots. Omnidirectional wheels are well known in the robotics community, their exceptional maneuvering capabilities attract a lot of robot builders and several industrial applications are known as well. To fully exploit the advantages of these special wheels sophisticated mechanics and control methods are required. Since modern engineering uses simulation wherever possible, to eliminate design errors early in the development, the first objective of my research was to create an easy to use, yet realistic model in simulation for the general omnidirectional wheel. To create this model I used empirical tire models created for automotive simulation – to make advantage of the knowledge accumulated in this domain – and modified them to generate forces like an omnidirectional wheel, in essence transforming the longitudinal force component in the direction of the rollers. I created two embodiments as an example in Dymola environment and verified their functionality using kinematic equations and simple lumped robot models. Omnidirectional wheels have no side-force generating capabilities, this is the very attribute that allows them to generate holonomic movement. -
Status of Pure Electric Vehicle Power Train Technology and Future Prospects
Review Status of Pure Electric Vehicle Power Train Technology and Future Prospects Abhisek Karki 1,2,* , Sudip Phuyal 3,4,* , Daniel Tuladhar 1, Subarna Basnet 5 and Bim Prasad Shrestha 1 1 Department of Mechanical Engineering, Kathmandu University, Dhulikhel 45200, Nepal; [email protected] (D.T.); [email protected] (B.P.S.) 2 Aviyanta ko Karmashala Pvt. Ltd., Bhaktapur 44800, Nepal 3 Department of Electrical and Electronics Engineering, Kathmandu University, Dhulikhel 45200, Nepal 4 Institute of Himalayan Risk Reduction, Lalitpur 44700, Nepal 5 International Design Center, Massachusetts Institute of Technology, Cambridge, MA 02139, USA; [email protected] * Correspondence: [email protected] (A.K.); [email protected] (S.P.) Received: 14 July 2020; Accepted: 10 August 2020; Published: 17 August 2020 Abstract: Electric vehicles (EV) are becoming more common mobility in the transportation sector in recent times. The dependence on oil as the source of energy for passenger vehicles has economic and political implications, and the crisis will take over as the oil reserves of the world diminish. As concerns of oil depletion and security of the oil supply remain as severe as ever, and faced with the consequences of climate change due to greenhouse gas emissions from the tail pipes of vehicles, the world today is increasingly looking at alternatives to traditional road transport technologies. EVs are seen as a promising green technology which could lead to the decarbonization of the passenger vehicle fleet and to independence from oil. There are possibilities of immense environmental benefits as well, as EVs have zero tail pipe emission and therefore are capable of curbing the pollution problems created by vehicle emission in an efficient way so they can extensively reduce the greenhouse gas emissions produced by the transportation sector as pure electric vehicles are the only vehicles with zero-emission potential. -
Sundancer Motor Home, Which Has Been Carefully All Times for Personal Reference
TO THE OWNER Congratulations! We welcome you to the exciting world of motor home travel and camping. You will find it convenient and enjoyable to have all the comforts of home and still enjoy the great outdoors wher- ever you choose to go. Your motor home has been carefully designed, engineered and manufactured to provide dependability as well as safety. Before sliding into the driver’s seat, take a few minutes to become familiar with opera- tions and features. This manual was prepared to aid you in the proper care and operation of the vehicle and equipment. We urge you to read it completely. In addition, spend some time with the dealer when you take delivery, you will want to learn all you can about your new motor home. Your new motor home is covered by a factory warranty against defects in material and workmanship. This warranty should be validated at once and returned to the factory by your dealer. About Safety Messages Used in This Manual Throughout this manual, certain items are labeled Note, Caution, Warning or Danger. These terms alert you to precautions that may involved damage to your vehicle or a risk to your personal safety. Read and follow them carefully. This SAFETY ALERT SYMBOL is used to draw your attention to issues which could involved potential personal injury. This symbol is used throughout this manual and/or on labels affixed on or near various equipment in this motor home. DANGER DANGER indicates a directly hazard- ous situation which, if not avoided, will result in death or serious personal injury. -
Drivetrain Design and Development
Drivetrain Design and Development Southwest Research Institute® (SwRI®) provides comprehensive design, development, test and evaluation services to clients from automotive, heavy-duty, off-road, marine, industrial and military industries. SwRI engineers have extensive experience in a comprehensive array of specialty design, test and development capabilities to assist manufacturers with new transmission design, transmission and drivetrain component development, vehicle development, benchmarking and resolution of drivetrain problems. This includes automatic, continuously variable, hybrid, and manual transmission drivetrains and their components. Test and Evaluation Assemblies • Transmissions • Transaxles • Transfer cases • Axles • All-wheel drive systems • Light and heavy duty • Hybrid electric/hydraulic systems Components • Torque converters • Clutches • Gears • Chains • CVT components • Pumps and hydraulics Tests • Engine firing pulse simulation • Engine inertia simulation • Dynamic road load • Drive cycle • Efficiency • Spin loss • Durability • Functionality • Development Design and Development Design • Automatic transmissions • Dual clutch transmissions • Continuously variable transmissions • Hybrid systems • Gearboxes • Engine geartrain Development • NVH • Shift calibration • Torsional vibration • Efficiency improvement • Clutches • Failure analysis • Benchmarking We welcome your inquiries. For more information, please contact: Randy McDonnell Powertrain Engineering Division Group Leader Drivetrain Design and Development swri.org 210.522.2558