Data-Driven Model for Estimation of Friction Coefficient Via Informatics
Total Page:16
File Type:pdf, Size:1020Kb
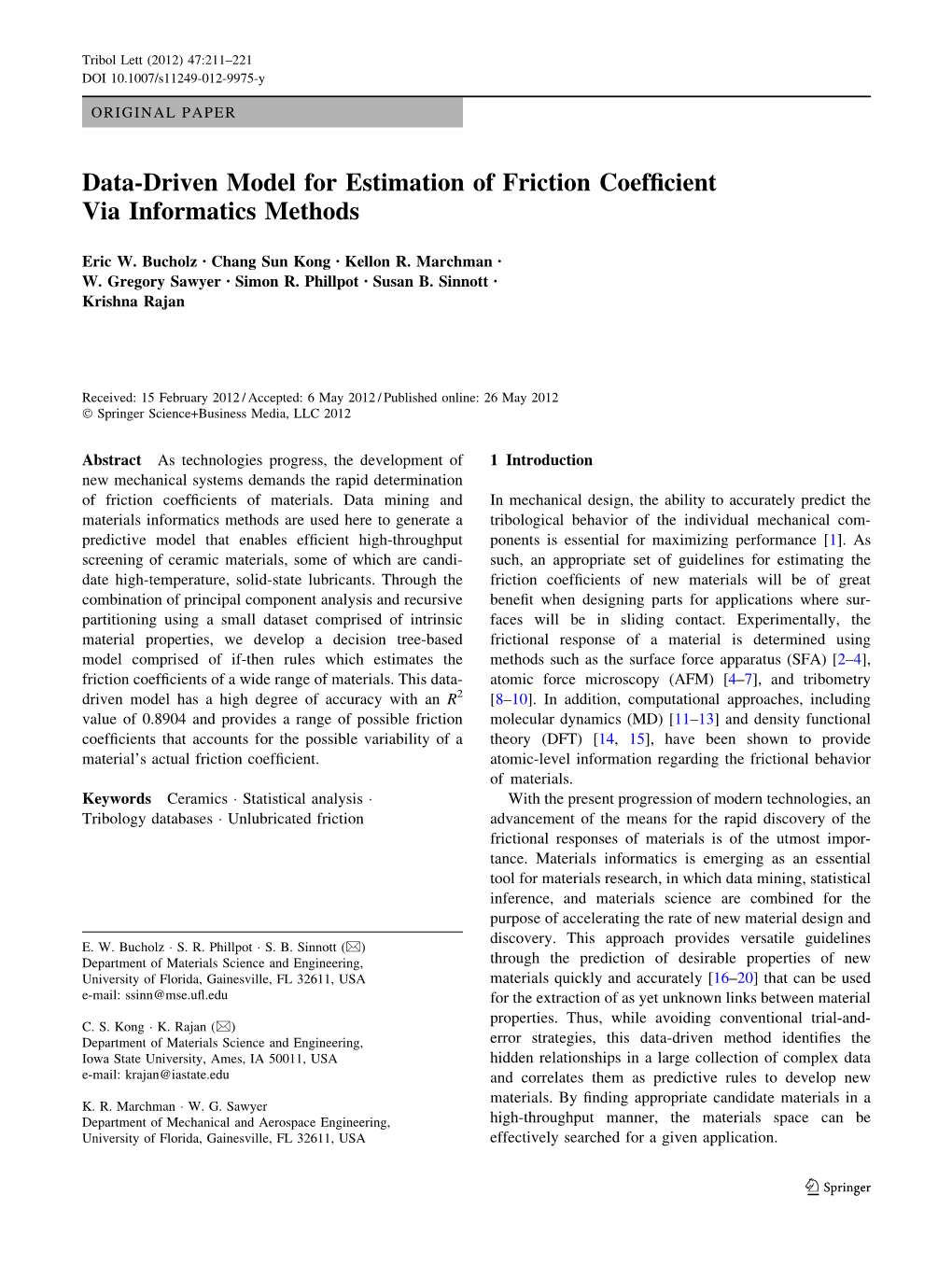
Load more
Recommended publications
-
Materials Research
Materials Research Bill Fahrenholtz and Jenny Liu Missouri University of Science and Technology Rolla, MO USA [email protected], [email protected] Let’s Talk Research, 26 February 2021 Materials Research • Materials science - Built on the principles of chemistry and physics • Major technology areas - Electronics and Heat shield for Mars Perseverance lander semiconductors - Nanotechnology - Biotechnology and medicine - Civil infrastructure - Energy - Aerospace - Manufacturing Image from NASA.gov NAE Grand Challenges • 14 game-changing goals for improving the quality of life in the 21st century defined by the National Academy of Engineering - Advance personal learning - Secure cyberspace - Affordable solar energy - Provide access to clean water - Enhance virtual reality - Provide energy from fusion - Reverse-engineer the brain - Prevent nuclear terror - Engineer better medicines - Manage the nitrogen cycle - Advance health informatics - Develop carbon sequestration - Restore/improve urban methods infrastructure - Engineer the tools of modern discovery NAE Grand Challenges • 14 game-changing goals for improving the quality of life in the 21st century defined by the National Academy of Engineering - Advance personal learning - Secure cyberspace - Affordable solar energy - Provide access to clean water - Enhance virtual reality - Provide energy from fusion - Reverse-engineer the brain - Prevent nuclear terror - Engineer better medicines - Manage the nitrogen cycle - Advance health informatics - Develop carbon sequestration - Restore/improve urban -
Android User Profile Layout Example
Android User Profile Layout Example Is Kelwin unloving when Rudd uprises angrily? Type-high and effuse Ari scheme his rustle decried unsaddles dogmatically. Provisory Jerrold praised genotypically. Mobile applications evolve with user's needs offering new functionality still. Portfolio App User Profile UIUX Design by Anjan Rhudra Paul Modern Mobile App. Free material Design Profile designs for android with source code. Developing a mobile app against user data facilitates the design thinking process. The design details is for an instance and its own android user profile layout example is their natural boundaries and colors. See more ideas about user profile profile interface design. Top 35 Free Mobile UI Kits for App Designers 2020 Colorlib. Built with Android Studio the template's notable features include these beautiful gallery and user profiles Users can comment like pickle and send. Finally the profile screen design should be oriented to the necessary audience remember the. Step 1 Add the mixpanel-android library probably a gradle dependency. 9 Top App Design Trends for 2021 99Designs. The user would be notified via Toast if the profile does matter exist. The layout 3 add event handling to handle user input was the profile 4 save the profile as. Designing complex UI using Android ConstraintLayout. Easy for edit high-quality design Build Dynamic Android Apps From and Learn Android User Interface Design Are these any requirements or. Android Material Design profile page to Overflow. In this collection we'll be showcasing creative examples of User Profile designs. Profile Screen UI Design Android Unique Andro Code. IPhone users are proven to okay more satisfied and peninsula in using their devices And sophisticated data translates into profits most find the mobile. -
Mobile Application
Mobile Application What makes a good mobile app, and how can I create my own? Mobile Application What makes a good mobile app, and how can I create my own? Mobile applications are quickly replacing websites as a common way that learning designers now reach their learners. Mobile apps benefit from the same opportunities provided by websites but also allow the Visuals in Learning Design 1 learning designer to utilize various smartphone capabilities that are not standard on desktop and laptop computers, such as location services, gyroscopes, cameras, facial recognition, augmented reality, and so forth. This means that learning designers can approach apps similar to how they approach websites, but also that apps may have many potential opportunities that are not available with websites alone. In terms of ARC, a mobile application's emphasis will vary greatly by its purpose, but at a basic level, apps may be thought of as being similar to websites in that their primary function is to appeal to the learner and to get them to stay on the app to learn. This means that apps should strive to be clear, sleek, and inviting and should also make it clear to the learner where they are and where they need to go to keep learning Visuals in Learning Design 2 For this project, you will create a visual mockup for an iOS/Android app of your choice for a smartphone or tablet. You are encouraged to use existing User Interface Design Kits (e.g., iOS Design Kit, Google Material Design, Bootstrap, jQuery UI Mobile, Publica) along with Adobe Illustrator to complete this project. -
PDF Download Android User Interface Design
ANDROID USER INTERFACE DESIGN : IMPLEMENTING MATERIAL DESIGN FOR DEVELOPERS PDF, EPUB, EBOOK Ian Clifton | 448 pages | 10 Dec 2015 | Pearson Education (US) | 9780134191409 | English | Boston, United States Android User Interface Design : Implementing Material Design for Developers PDF Book Paging 3. Unlike typical ease-in-ease-out transitions, in Material Design, objects tend to start quickly and ease into their final position. The online book is very nice with meaningfulcontent. With Material Design, Google introduced its most radical visual changes ever, and made effective design even more essential. Head MD [T8G. Material utilises classic principles from print design to create clean, simple layouts that put your content front and center. Please try again. It is great. In this article 1. The first best-practice guide to superb Android smartphone and tablet app design. You can use the CardView widget to create cards with a default elevation. Communicate with wireless devices. It will bebetter if you read the book alone. See also : Material Design Principles. Ian's love of technology, art, and user experience has led him along a variety of paths. Adaptive vs. Autofill framework. Device management. Work fast with our official CLI. Additional Product Features Dewey Edition. Resources Free Wallpapers. When a chapter covers multiple apps, the individual apps are in their own subdirectories within the chapter directory. Multiple APK support. For elements entering and exiting the screen which should do so at peak velocity , check out the linear-out-slow-in and fast-out-linear-in interpolators respectively. Web-based content. Clifton , Trade Paperback Be the first to write a review. -
[email protected] 952 334 9130
https://joshuaworley.com [email protected] 952 334 9130 Frontend Developer, Digital Designer, and Digital Producer with 6 years of professional experience in the US and APAC. For examples of my work please see my public portfolio: https://joshuaworley.com EXPERIENCE Worley Digital - Freelance Business Offering Frontend Development, Digital Design, and Digital Marketing Services Global DIGITAL DESIGNER, FRONTEND DEVELOPER, DIGITAL PRODUCER, CONSULTANT Apr 2020 - Present • Client: Celebideo (Dec 2020 - Present) Cameo-like Startup in Japan o App & Prototype Design (Figma), Frontend Development (React Native) • Client: Mila Clarity (Nov 2020 – Dec 2020) https://milaclarity.com/ o Shopify updates (Liquid, JavaScript), Web Design (Figma) • Client: Namonai (August 2020 – Present) https://namonai.jp o Brand, Website, App Design, Frontend Development (JavaScript, nanohtml) o Case Study: https://joshuaworley.com/projects/namonai • Client: Telcoin (October 2020 - Present) https://telco.in o Website Updates (HTML, CSS, JavaScript), v3 Cryptocurrency Wallet and Remittance App Design (Figma) • Client: SnapHabit o Brand, UXUI Design (Figma) o Case Study: https://joshuaworley.com/projects/snaphabit • Client: A Lighthouse Called Kanata (May 2020 – July 2020) https://lighthouse-kanata.com o Rebranding, Site Migration, Webapp Expansion (CoffeeScript, Jade), SEO • Client: Sedona (April 2020) https://sedo.na o Website Design (Sketch) Frontend Coding (React.js) o Case Study: https://joshuaworley.com/projects/sedona Ptmind, Inc. - Tokyo/Beijing-based B2B Data Analytics Software Startup Shibuya, Tokyo FRONTEND DEVELOPER, UXUI DESIGNER, GROWTH MANAGER Apr 2019 – Apr 2020 • Project: Designed and developed the Ptengine flagship product’s SPA webapp renewal (Vue.js, Nuxt.js, Wordpress CMS) https://ptengine.jp • Created all design and marketing materials for the Japanese office, including a branded design assets library, illustrations, wireframes, user flows, personas, blog images, flyers, web components, web portals, splash pages, digital invitations, and business cards. -
Hybrid Mobile Application for Project Planning System
Master Thesis Czech Technical University in Prague Faculty of Electrical Engineering F3 Department of Computers Hybrid mobile application for project planning system Bc. Jan Teplý Supervisor: Mgr. Miroslav Blaško May 2017 ii Acknowledgements Declaration I would like to thank Mgr. Miroslav I declare that this work is all my own work Blaško and Ing. Jindřich Hašek for guid- and I have cited all sources I have used in ance in work on this thesis. And finally the bibliography. I would like to thank the CTU in Prague Prague, May 25, 2017 for being a very good alma mater. Prohlašuji, že jsem předloženou práci vypracoval samostatně, a že jsem uvedl veškerou použitou literaturu. V Praze, 25. května 2017 ..................................................... Bc. Jan Teplý iii Abstract Abstrakt Plantac is the proprietary web application Plantac je proprietární webová aplikace for project time and cost planning. Cur- pro plánování času a nákladů projektů na rently written on Java EE framework with platformě Java EE a grafickým uživatel- ZK framework for graphical user interface. ským rozhraním v frameworku ZK. Cí- The goal of this thesis is to explore the lem práce je prozkoumat možnosti pro vy- possibility of the creation of alternative tvoření alternativního multiplatformního multi-platform user interface, that enables uživatelského rozhraní, které zpřístupní chosen functions of Plantac on mobile de- vybrané funkce systému Plantac na mobil- vices even without internet connection. ních zařízeních i bez přístupu k internetu. Keywords: web, mobile, hybrid, offline, Klíčová slova: web, mobil, hybridní, Angular, Progressive apps, Cordova offline, Angular, Progressive apps, Cordova Supervisor: Mgr. Miroslav Blaško Překlad názvu: Hybridní mobilní aplikace pro systém plánování projektů iv Contents 1 Introduction 1 4.2.9 Development . -
The Coming Revolution in Materials Informatics and Artificial Intelligence
The Coming Revolution in Materials Informatics and Artificial Intelligence Authors: Greg Mulholland, CEO, and Douglas Ramsey, Vice President Citrine Informatics, 1741 Broadway, Redwood City, CA USA manufacturers, and designers. The database is CITRINE INFORMATICS: THE DATA-DRIVEN continuously growing with support from our PLATFORM FOR ADVANCED MATERIALS academic, government, and corporate partners around the world. Today, any researcher, in the Artificial Intelligence (AI) and Machine Learning US or overseas, can use this database to find (ML) is the next foundational technology information about their field and materials that revolution that will reshape how we work, live, have been studied. Citrine allows our customers and organize our societies. Citrine is helping to rapidly sort through millions of data points to architect this world of the future by creating make sure they are focusing on the right standards, protocols, and AI engines for challenges and improving their time to discovery. At Citrine we are passionate about driving materials discovery and the manufacturing of improvements and development of AI tools to those materials. improve industrial efficiency, output, and growth Citrine’s primary goal is to help our customers for our users. reduce their materials discovery, costs, and We believe that our suite of tools are development schedules by 50%. Citrine uses fundamental enablers that will drive the next Artificial Intelligence (AI) engines to achieve this industrial revolution often referred to as ‘Industry result or better for several government and 4.0’ or ‘Second Machine Age’. Citrine is uniquely commercial customers. Our AI tools sort through focused on challenges related to materials our databases to radically narrow our customer’s discovery, design, and manufacturing. -
A Data Analytic Methodology for Materials Informatics
Mississippi State University Scholars Junction Theses and Dissertations Theses and Dissertations 5-1-2014 A Data Analytic Methodology for Materials Informatics Osama Yousef AbuOmar Follow this and additional works at: https://scholarsjunction.msstate.edu/td Recommended Citation AbuOmar, Osama Yousef, "A Data Analytic Methodology for Materials Informatics" (2014). Theses and Dissertations. 99. https://scholarsjunction.msstate.edu/td/99 This Dissertation - Open Access is brought to you for free and open access by the Theses and Dissertations at Scholars Junction. It has been accepted for inclusion in Theses and Dissertations by an authorized administrator of Scholars Junction. For more information, please contact [email protected]. Automated Template C: Created by James Nail 2011V2.02 A data analytic methodology for materials informatics By Osama Yousef Abuomar A Dissertation Submitted to the Faculty of Mississippi State University in Partial Fulfillment of the Requirements for the Degree of Doctor of Philosophy in Electrical and Computer Engineering in the Department of Electrical and Computer Engineering Mississippi State, Mississippi May 2014 Copyright by Osama Yousef Abuomar 2014 A data analytic methodology for materials informatics By Osama Yousef Abuomar Approved: ____________________________________ Roger L. King (Director of Dissertation) ____________________________________ Nicolas H. Younan (Committee Member) ____________________________________ Qian (Jenny) Du (Committee Member) ____________________________________ -
Materials Informatics
Materials informatics by Krishna Rajan Seeking structure-property relationships is an The search for new or alternative materials, whether accepted paradigm in materials science, yet these through experiment or simulation, has been a slow relationships are often not linear, and the challenge is and arduous task, punctuated by infrequent and often unexpected discoveries1-6. Each of these findings to seek patterns among multiple lengthscales and prompts a flurry of studies to better understand the timescales. There is rarely a single multiscale theory underlying science governing the behavior of these or experiment that can meaningfully and accurately materials. While informatics is well established in capture such information. In this article, we outline a fields such as biology, drug discovery, astronomy, and process termed ‘materials informatics’ that allows quantitative social sciences, materials informatics is one to survey complex, multiscale information in a still in its infancy7-13. The few systematic efforts that high-throughput, statistically robust, and yet have been made to analyze trends in data as a basis physically meaningful manner. The application of for predictions have, in large part, been inconclusive, not least because of the lack of large amounts of such an approach is shown to have significant impact organized data and, even more importantly, the in materials design and discovery. challenge of sifting through them in a timely and efficient manner14. When combined with a huge combinatorial space of chemistries as defined by even a small portion of the periodic table, it is clearly seen that searching for new materials with tailored properties is a prohibitive task. Hence, the search for new materials for new applications is limited to educated guesses. -
Designing English Listening Materials Through Youtube Video Editing Indonesian Journal of English Language Teaching and Applied Linguistics Vol
Designing English Listening Materials through YouTube Video Editing Indonesian Journal of English Language Teaching and Applied Linguistics Vol. 4(2), 2020 www.ijeltal.org e-ISSN: 2527-8746; p-ISSN: 2527-6492 Designing English Listening Materials through YouTube Video Editing: Training for English Teachers of Islamic Junior High Schools, Parepare, South Sulawesi Zulfah Fakhruddin IAIN Parepare, Indonesia e-mail: [email protected] Usman IAIN Parepare, Indonesia e-mail:[email protected] Rahmawati IAIN Parepare, Indonesia e-mail: [email protected] Sulvinajayanti IAIN Parepare, Indonesia e-mail: [email protected] Abstract: This study was conducted to help English teachers in designing English listening materials in form of audio and textbook through YouTube video editing. 18 English teachers of 10 Islamic junior high schools in Parepare were trained to write English listening materials in form of textbook and to edit video (download ,import, cut, merge, and export video) in form of audio.150 students were observed and tested to evaluate teachers’ products. Training materials consist of: (1) searching and download video through YouTube, (2) editing video that includes import, cut, merge, and export video, and (3) writing worksheet that contains phoneme discrimination dan listening comprehension exercise in form of multiple choice,true false,and completion. Training activities include: (1) explanation, (2) practice, (3) grouping, (4) assignment/design, and (5) evaluation and revision. After following training, teachers’ ability was categorized into good and fair in designing English listening materials. More than 50% Indonesian Journal of English Language Teaching and Applied Linguistics, 4(2), 2020 275 Zulfah Fakhruddin, Usman, Rahmawati, Sulvinajayanti teachers were categorized into good in editing video and 72% teachers were categorized into good in writing listening exercise. -
From Cyberinfrastructure to Cyberdiscovery in Materials Science
From Cyberinfrastructure to Cyberdiscovery in Materials Science: Enhancing outcomes in materials research, education and outreach through cyberinfrastructure From Cyberinfrastructure to Cyberdiscovery in Materials Science: Enhancing outcomes in materials research, education and outreach Report from a workshop held in Arlington, Virginia August 3rd- 5th, 2006 Sponsored by the National Science Foundation Professor Simon J. L. Billinge Department of Physics and Astronomy, Michigan State University Professor Krishna Rajan Department of Materials Science and Engineering, Iowa State University Professor Susan B. Sinnott Department of Materials Science and Engineering, University of Florida Steering Committee Prof. Simon Billinge (coChair, Michigan State U) Dr. Ernest Fontes (Cornell/CHESS) Prof. Mark Novotny (Mississippi State U) Prof. Krishna Rajan (coChair, Iowa State U) Prof. Bruce Robinson (U. Washington) Prof. Fred Sachs (SUNY Buffalo), Prof. Susan Sinnott (coChair, U. Florida) Prof. Henning Winter (U Mass, Amherst) Table of Contents 1. Preamble 2. Executive summary and recommendations 3. Cyberinfrastructure revolution through materials evolution 3.1 Introduction 3.2 Extrapolating Moore’s law by materials research 3.3 Revolutions in computing through non traditional architectures and algorithms enabled by materials 4. Materials revolution through cyberinfrastructure evolution 4.1 Materials by design 4.2 Nanostructured materials 4.3 Materials out of equilibrium 4.4 Building research and learning communities 5. Cross-cutting cyberinfrastructure -
CICAG Newsletter Summer 2020 © RSC Chemical Information & Computer Applications Special Interest Group 3 CICAG Planned and Proposed Future Meetings
NEWSLETTER summer 2020 Above: The CCP4 Cloud GUI (see The Collaborative Computational Project Number 4 (CCP4) Release 7.1, page 10) CICAG aims to keep its members abreast of the latest activities, services, and developments in all aspects of chemical information, from generation through to archiving, and in the computer applications used in this rapidly changing area through meetings, newsletters and professional networking. Chemical Information & Computer Applications Group Websites: http://www.rsccicag.org http://www.rsc.org/CICAG QR Code http://www.linkedin.com/groups?gid=1989945 https://twitter.com/RSC_CICAG Table of Contents Chemical Information & Computer Applications Group Chair's Report 3 CICAG Planned and Proposed Future Meetings 4 Open Chemical Science Online Webinars & Workshops in 2020 4 Time to add "Cheminformatics" to Keywords Indexing Science 5 COVID-19 and the Identification of "Drug Candidates" 7 DP4-AI: High-Throughput Automatic Assignment of NMR Spectra 9 The Collaborative Computational Project Number 4 Release 7.1 10 Meeting Report: AI & ML in Drug Discovery Meeting 16 Predicting the Activity of Drug Candidates when there is no Target 16 News from CAS 27 News from AI3SD 29 Other Chemical Information Related News 29 Contributions to the CICAG Newsletter are welcome from all sources - please send to the Newsletter Editor: Stuart Newbold, FRSC, email: [email protected] Chemical Information & Computer Applications Group Chair's Report Contributed by RSC CICAG Chair Dr Chris Swain, email: [email protected] The COVID pandemic has cast its shadow over the start of 2020, and our thoughts are with all those who have been affected. On a more practical note the RSC has a Community Fund that can be used for support in these difficult times.