Lime Softening—The Forgotten Technology: Optimization Case Studies from South Florida
Total Page:16
File Type:pdf, Size:1020Kb
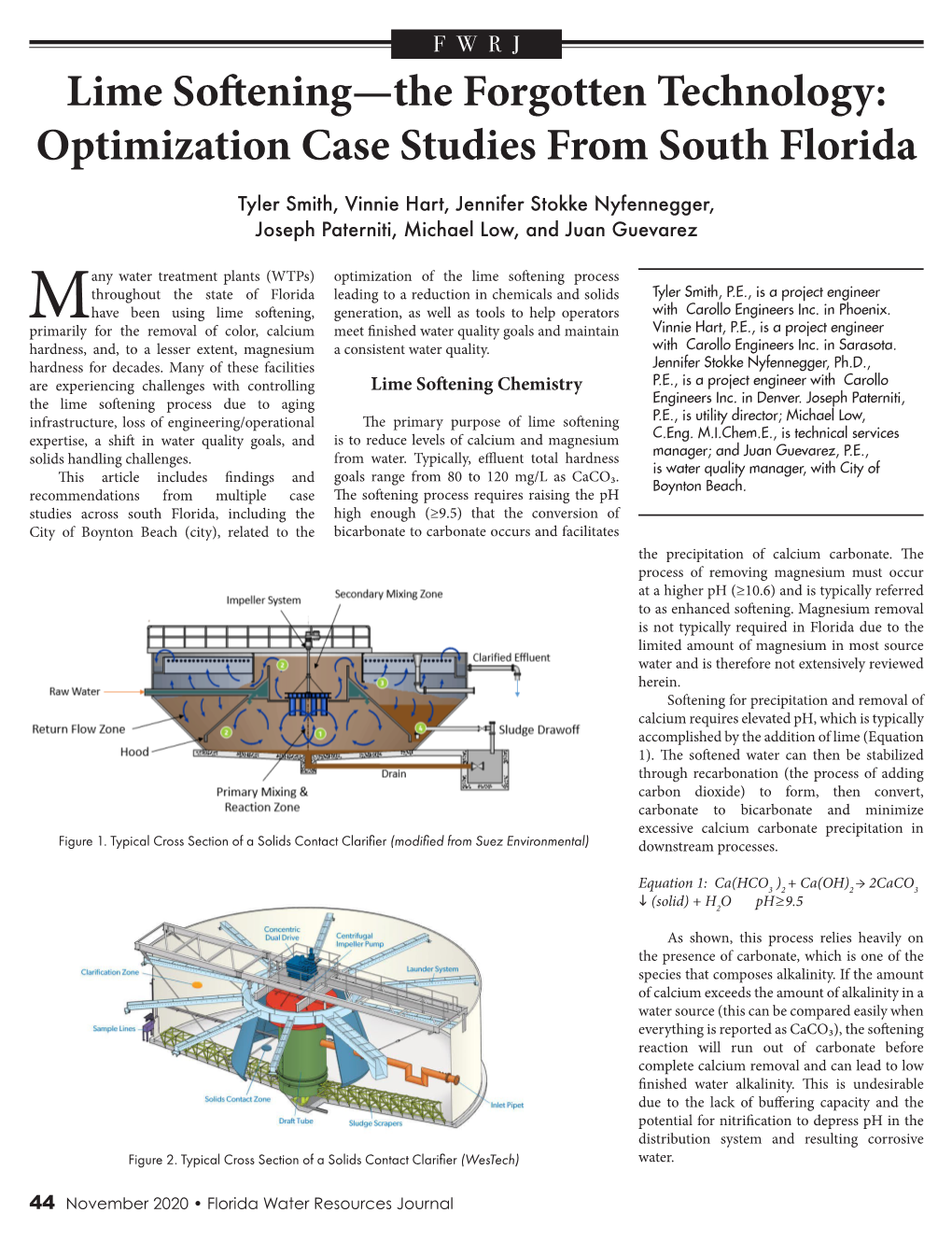
Load more
Recommended publications
-
Module 22: Inorganics Removal Basics
Drinking Water Operator Certification Training Module 22: Inorganics Removal Basics Revised May 4, 2018 This course module was developed by the Pennsylvania Department of Environmental Protection. Content sources are referenced at the end of every module unit. 1 2 DISCLAIMER: This module was designed as a training module for Pennsylvania drinking water operators to study prior to taking the drinking water subclass 9 ion exchange and greensand exam. The focus of this exam is the removal of inorganic constituents from drinking water using the treatment processes ion exchange or greensand filtration. As a result, this training module focuses on the treatment methods of ion exchange units and greensand filters. In addition, there is a focus on the removal of some of the inorganic contaminants common in Pennsylvania groundwater systems: nitrates, iron, and manganese. Since arsenic, barium and mercury, may sporadically be found in Pa. groundwater, treatment options for these contaminants will also be mentioned in this module. Because radionuclides, radon, and hydrogen sulfide may also be found in Pa groundwaters, they are also briefly mentioned. Water softening is also discussed. Note that since lead and copper treatment is covered in Module 20: Corrosion Control and Sequestering, treatment of those inorganic contaminants is not discussed in this module. The 2006 version of the Pa. DEP Inorganic Contaminant Removal module has detailed advanced treatment information on this topic and can be obtained by e-mailing the Pa. DEP Safe Drinking Water Training Section at [email protected] to request a copy. This advanced module has additional information on the removal of various inorganic contaminants as well as on oxidation, ion exchange, activated alumina and sequestration. -
Sulfate Scale
TECHNICAL SERVICE GUIDE Sulfate Scale The following are general recommendations for controlling sulfate scale in systems using reverse osmosis (RO) and nanofiltration (NF) elements. For additional information on pretreatment or cleaning elements, please see MANN+HUMMEL Water & Fluid Solutions Pretreatment and Cleaning Guides or contact MANN+HUMMEL Water & Fluid Solutions Technical Service. INTRODUCTION Scaling is when sparingly soluble salts precipitate and deposit on the surface of a membrane element. The solubility of barium, calcium and strontium is low and may lead to scale formation on the membrane surface where the salts are most concentrated. This typically affects the elements in the last stage first and then gradually affects the stages upstream. Barium sulfate (BaSO4) is the most insoluble of all the alkaline-earth sulfates. When present in water, it may precipitate and act as a catalyst for calcium and strontium sulfate scaling. Typically, barium can be found in well waters, with typical concentrations less than 0.05 ppm to 0.2 ppm. However, in most natural waters, barium is present at a level that may cause barium sulfate scaling. The critical feed concentration of barium may be as low as 0.015 ppm in seawaters, 0.005 ppm in brackish waters or even 0.002 ppm if sulfuric acid is dosed to brackish waters. Early detection of sulfate scaling is essential to prevent possible damage on the membrane surface. A number of factors can affect the rate of scale formation including temperature and pH control, as well as the use of antiscalants. If the scaling potential for barium, calcium and/or strontium sulfates is high, some common methods to control scaling potential include: • The use of a scale inhibitor or antiscalant is the most common method to reduce sulfate scale • Decreasing the calcium and alkalinity concentrations in the feed solution by means of lime or lime-soda ash softening to lower pHs (the pH of saturation). -
Cold Lime Softening Soda Ash May Be Added to Remove Calcium Hardness Hard Water Is Water That Has High Mineral Content
The WWETCO FlexFilter™ from WesTech provides an innovative solution for industrial water pretreatment and/or tertiary treatment. The combination of tapered media compression, porosity gradient within the media bed, and a low flow backwash system make the WWETCO FlexFilter™ one of the most versatile and efficient filters on the market. Cold Lime Softening Soda ash may be added to remove calcium hardness Hard water is water that has high mineral content. if the raw water does contain sufficient alkalinity The name comes from the hard scale that forms when for complete removal of hardness. Settled solids this water is boiled. It is not harmful to human react with lime and soda ash to form larger and health, but in the industrial setting it causes costly faster settling particles. The clarified water flows breakdowns in boilers, cooling towers, and other over weirs and the solids (sludge) are scraped to the water handling equipment. The divalent cations center for removal and dewatering. The overflow Mg and Ca are the most frequently found minerals typically has less than 10 mg/L of suspended solids. causing hard water. These ions enter water supplies The amount of hardness remaining will depend on by leaching from minerals in underground aquifers. the water chemistry and proper chemical addition. Cold lime softening is the addition of chemicals Recarbonation to remove the calcium and magnesium ions by After softening, the pH is lowered to less than 8 to precipitation. Cold (ambient temperature) lime stop the softening reaction. This prevents what is softening is used when the mineral content of the called “post-precipitation” where softening continues source water ranges from 150 ppm – 500 ppm. -
Lime Softening Sources, Have Relatively Stable Water Which and the Complexity of the Chemistry of Variable Source Water Quality Quality
A NATIONAL DRINKING WATER CLEARINGHOUSE FACT SHEET Lime Softening Summary Hard water can cause scaling problems in water heaters and soap does not lather well in hard water. Therefore, some water utilities soften water to improve its quality for domestic use. Lime softening is best suited to groundwater sources, which have relatively stable water quality. The combination of variable source water quality and the complexity of the chemistry of lime softening may make lime softening too complex for small systems that use surface water sources. Although lime softening has been used successfully by groundwater systems serving fewer than 3,000 people, it is unlikely to be suitable for ○○○○○○○○○○○○ treating groundwater in systems serving 500 or fewer people unless those systems have some form of contract or satellite operation that would enable a trained operator to monitor the treatment process. Prefabricated lime softening equipment is available for small systems. Also, there is an American Water Works Association Standard for quicklime and hydrated lime (ANSI/AWWA B202-93) that provides purchasers, manufacturers, and suppliers with the minimum requirements, including physical, chemical, packaging, shipping, and testing requirements. Either hydrated lime [Ca(OH)2] or quicklime (CaO) may be used in the softening process. The choice depends upon economic factors, such as the○○○○○○○○○○○○○○○○○○○○○○○○○○○○○○○○○○○○○○○○○○○ relative cost per ton of the two materials as well as the size and equipment of the softening plant. Hydrated lime is generally used more in smaller plants because it stores better and does not require slaking (producing a chemical change in lime by combining it with water) equipment. On the other hand, quick- lime costs less per ton of available calcium oxide and is thus more economical for use in large plants. -
Water Chemistry Evaluation City of Mt. Pleasant June 2000
WATER CHEMISTRY EVALUATION CITY OF MT. PLEASANT JUNE 2000 1.0 EXECUTIVE SUMMARY The raw water supply for the City of Mt. Pleasant (City) is characterized by high hardness, high iron and manganese, and high total dissolved solids. In December 1995, the new City of Mt. Pleasant Water Treatment Facility, a lime softening plant, went into service. Prior to this, most City water customers utilized in-home softening units to treat their water. The new treatment plant utilizes lime, caustic soda, and other chemicals to treat the water to remove the iron and manganese, and reduce the hardness and total dissolved solids. The new plant now delivers water to City customers that has low hardness, very low iron and manganese concentrations, and lower total dissolved solids. Even though the water quality is greatly improved since the new treatment has been online, the City has continued to receive some water quality complaints. The complaints typically involve rusty colored water or premature hot water heater failure. This engineering investigation was authorized by the City to evaluate the water chemistry, determine the cause of the water quality complaints, and recommend operational changes or other methods to improve water quality. During this investigation, we evaluated water treatment plant operating data, reviewed customer complaint records, and compiled and evaluated lead and copper sampling data and Michigan Department of Environmental Quality (MDEQ) routine monitoring results. In addition, a sampling program was developed and samples at various locations throughout the water supply and distribution system were collected and analyzed. The data from the water samples were utilized to characterize the water chemistry and to calculate the calcium carbonate stability index. -
High Recovery Inland Desalination: a Technical and Economic
University of Texas at El Paso DigitalCommons@UTEP Open Access Theses & Dissertations 2018-01-01 High Recovery Inland Desalination: A Technical And Economic Performance Evaluation Of Zero Discharge Desalination And Other Technologies Malynda Aragon Cappelle University of Texas at El Paso, [email protected] Follow this and additional works at: https://digitalcommons.utep.edu/open_etd Part of the Civil Engineering Commons Recommended Citation Cappelle, Malynda Aragon, "High Recovery Inland Desalination: A Technical And Economic Performance Evaluation Of Zero Discharge Desalination And Other Technologies" (2018). Open Access Theses & Dissertations. 1406. https://digitalcommons.utep.edu/open_etd/1406 This is brought to you for free and open access by DigitalCommons@UTEP. It has been accepted for inclusion in Open Access Theses & Dissertations by an authorized administrator of DigitalCommons@UTEP. For more information, please contact [email protected]. HIGH RECOVERY INLAND DESALINATION: A TECHNICAL AND ECONOMIC PERFORMANCE EVALUATION OF ZERO DISCHARGE DESALINATION AND OTHER TECHNOLOGIES MALYNDA ARAGON CAPPELLE Doctoral Program in Civil Engineering APPROVED: W. Shane Walker, Ph.D., Chair Anthony Tarquin, Ph.D. Pei Xu, Ph.D. Mark Engle, Ph.D. Charles Ambler, Ph.D. Dean of the Graduate School Copyright © by Malynda Cappelle 2018 Dedication This dissertation is dedicated to my loving parents who have always encouraged me to pursue my dreams, to my incredible husband who supports me in every way, and to all teachers for guiding me on my journey in -
Lime Softening
A NATIONAL DRINKING WATER CLEARINGHOUSE FACT SHEET Lime Softening Summary Hard water can cause scaling problems in water heaters and soap does not lather well in hard water. There- fore, some water utilities soften water to improve its quality for domestic use. Lime softening is best suited to groundwater sources, which have relatively stable water quality. The combination of variable source water quality and the complexity of the chemistry of lime softening may make lime softening too complex for small systems that use surface water sources. Although lime softening has been used successfully by groundwater systems serving fewer than 3,000 people, it is unlikely to be suitable for treating groundwater in systems serving 500 or fewer people unless those systems have some form of contract or satellite operation that would enable a trained operator to monitor the treatment process. Prefabricated lime softening equipment is available for small systems. Also, there is an American Water Works Association Standard for quicklime and hydrated lime (ANSI/AWWA B202-93) that pro- vides purchasers, manufacturers, and suppliers with the minimum requirements, including physical, chemical, packaging, shipping, and testing requirements. Either hydrated lime [Ca(OH)2] or quicklime (CaO) may be used in the softening process. The choice depends upon economic factors, such as the relative cost per ton of the two materials as well as the size and equipment of the softening plant. Hydrated lime is generally used more in smaller plants because it stores better and does not require slaking (producing a chemical change in lime by combining it with water) equipment. -
Scale Control-Lime Softening
Tech Manual Excerpt Water Chemistry and Pretreatment Scale Control Lime Softening Lime softening can be used to remove carbonate hardness by adding hydrated lime: → Ca(HCO3)2 + Ca(OH)2 2 CaCO3 + 2 H2O → Mg(HCO3)2 + 2 Ca(OH)2 Mg(OH)2 + 2 CaCO3 + 2H2O The noncarbonate calcium hardness can be further reduced by adding sodium carbonate (soda ash): → CaCl2 + Na2CO3 2 NaCl + CaCO3 The lime-soda ash process can also be used to reduce the silica concentration. When sodium aluminate and ferric chloride are added, the precipitate will include calcium carbonate and a complex with silicic acid, aluminum oxide, and iron. With the hot lime silicic acid removal process at 60 – 70°C, silica can be reduced to 1 mg/L by adding a mixture of lime and porous magnesium oxide. With lime softening, barium, strontium, and organic substances are also reduced significantly. The process requires a reactor with a high concentration of precipitated particles serving as crystallization nuclei. This is usually achieved by upflow solids- contact clarifiers. The effluent from this process requires media filtration and pH adjustment prior to the RO elements. Iron coagulants with or without polymeric flocculants (anionic and nonionic) may be used to improve the solid-liquid separation. Lime softening should be considered for brackish water plants larger than 200 m3/h (880 gpm). More details are described in water treatment textbooks. /3, 4, 5/ Page 1 of 2 Form No. 45-D01549-en, Rev. 4 April 2020 Excerpt from FilmTec™ Reverse Osmosis Membranes Technical Manual (Form No. 45-D01504-en), Chapter 2, "Water Chemistry and Pretreatment." Have a question? Contact us at: All information set forth herein is for informational purposes only. -
In Situ Oil Sands Technology Trends
STUDY NO. 193 DECEMBER 2020 IN SITU OIL SANDS TECHNOLOGY TRENDS 3512 - 33 Street NW, #150, Calgary, AB T2L 2A6 350 Sparks Street, #805, Ottawa, ON K1R 7S8 403.282.1231 | www.ceri.ca | [email protected] @ceri_canada Canadian Energy Research Institute In Situ Oil Sands Technology Trends Authors: Evar Umeozor, Madie Zamzadeh, Dinara Millington Recommended Citation (Author-date style): Umeozor, Evar, Madie Zamzadeh, and Dinara Millington. 2021. “In Situ Oil Sands Technology Trends.” Study No. 193 Calgary, AB: Canadian Energy Research Institute. https://ceri.ca/assets/files/Study_193_Full_Report.pdf Recommended Citation (Numbered style): E. Umeozor, M. Zamzadeh and D. Millington, “In Situ Oil Sands Technology Trends,” Canadian Energy Research Institute, Calgary, AB, Study No. 193, 2021. URL: https://ceri.ca/assets/files/Study_193_Full_Report.pdf Copyright © Canadian Energy Research Institute, 2021 Sections of this study may be reproduced in magazines and newspapers with acknowledgment to the Canadian Energy Research Institute January 2021 Printed in Canada Acknowledgements: The authors of this report would like to extend their thanks and sincere gratitude to all CERI staff involved in the production and editing of the material. ABOUT THE CANADIAN ENERGY RESEARCH INSTITUTE Founded in 1975, the Canadian Energy Research Institute (CERI) is an independent, registered charitable organization specializing in the analyses of economic and environmental issues in the energy production, transportation and consumption sectors. Our studies examine the most relevant energy issues affecting Canadians, painting a comprehensive picture of the impact policies and business decisions can have so that decision-makers in government, industry and other market segments can make sound decisions to help move Canada forward. -
Oil and Gas Produced Water Management and Beneficial Use in the Western United States
Science and Technology Program Report No. 157 Oil and Gas Produced Water Management and Beneficial Use in the Western United States U.S. Department of the Interior Bureau of Reclamation September 2011 REPORT DOCUMENTATION PAGE Form Approved OMB No. 0704-0188 Public reporting burden for this collection of information is estimated to average 1 hour per response, including the time for reviewing instructions, searching existing data sources, gathering and maintaining the data needed, and completing and reviewing this collection of information. Send comments regarding this burden estimate or any other aspect of this collection of information, including suggestions for reducing this burden to Department of Defense, Washington Headquarters Services, Directorate for Information Operations and Reports (0704-0188), 1215 Jefferson Davis Highway, Suite 1204, Arlington, VA 22202-4302. Respondents should be aware that notwithstanding any other provision of law, no person shall be subject to any penalty for failing to comply with a collection of information if it does not display a currently valid OMB control number. PLEASE DO NOT RETURN YOUR FORM TO THE ABOVE ADDRESS. 1. REPORT DATE (DD-MM-YYYY) 2. REPORT TYPE 3. DATES COVERED (From - To) September 2011 Final 10/2006 to 9/2010 4. TITLE AND SUBTITLE 5a. PROJECT NUMBER Oil and Gas Produced Water Management and Beneficial Use in the 3180 Western United States 5b. GRANT NUMBER 5c. PROGRAM ELEMENT NUMBER 6. AUTHOR(S) 5d. PROJECT NUMBER Katie Guerra, Katharine Dahm, Steve Dundorf 5e. TASK NUMBER 5f. WORK UNIT NUMBER 7. PERFORMING ORGANIZATION NAME(S) AND ADDRESS(ES) 8. PERFORMING ORGANIZATION REPORT U.S. -
A Novel Brine Precipitation Process with the Aim of Higher Permeate Water Recovery
A Novel Brine Precipitation Process with the Aim of Higher Permeate Water Recovery Item Type text; Electronic Thesis Authors Azadi Aghdam, Mojtaba Publisher The University of Arizona. Rights Copyright © is held by the author. Digital access to this material is made possible by the University Libraries, University of Arizona. Further transmission, reproduction or presentation (such as public display or performance) of protected items is prohibited except with permission of the author. Download date 28/09/2021 02:16:14 Link to Item http://hdl.handle.net/10150/613571 A NOVEL BRINE PRECIPITATION PROCESS WITH THE AIM OF HIGHER PERMEATE WATER RECOVERY by Mojtaba AzadiAghdam A Thesis Submitted to the Faculty of the DEPARTMENT OF CHEMICAL AND ENVIRONMENTAL ENGINEERING In Partial Fulfillment of the Requirements For the Degree of MASTER OF SCIENCE WITH A MAJOR IN ENVRIONMENTAL ENGINEERING In the Graduate College THE UNIVERSITY OF ARIZONA 2016 STATEMENT BY AUTHOR The thesis titled A Novel Brine Precipitation Process with the Aim of Higher Permeate Water Recovery prepared by Mojtaba AzadiAghdam has been submitted in partial fulfillment of requirements for a master’s degree at the University of Arizona and is deposited in the University Library to be made available to borrowers under rules of the Library. Brief quotations from this thesis are allowable without special permission, provided that an accurate acknowledgement of the source is made. Requests for permission for extended quotation from or reproduction of this manuscript in whole or in part may be granted by the head of the major department or the Dean of the Graduate College when in his or her judgment the proposed use of the material is in the interests of scholarship. -
Drinking Water Softening/Scale Prevention Technology Assessment and Performance of Template Assisted Crystallization
Drinking Water Softening/Scale Prevention Technology Assessment and Performance of Template Assisted Crystallization by Lin Shen A thesis presented to the University of Waterloo in fulfillment of the thesis requirement for the degree of Master of Applied Science in Civil Engineering Waterloo, Ontario, Canada, 2019 ©Lin Shen 2019 AUTHOR'S DECLARATION I hereby declare that I am the sole author of this thesis. This is a true copy of the thesis, including any required final revisions, as accepted by my examiners. I understand that my thesis may be made electronically available to the public. ii Abstract Hard water typically has a hardness concentration over 120 mg/L CaCO3. Hardness is not a regulated drinking water parameter and does not have severe health effects. However, hard water causes more soap and detergent consumption and can cause scaling problems on household heating appliances, distribution pipes, and industrial cooling equipment. There are various approaches to soften hard water or prevent scale formation at the centralized and the household scale. In order to choose the best treatment for a specific set of conditions, an appropriate technology evaluation is necessary. Prior research have tested single technology or compared two or three technologies with respect to their performance. Not many papers have compared all available technologies using the same assessment criteria. At the household scale, point-of-entry (POE) devices are commonly used. Among these, ion exchange is the most widely applied POE device in Canada, though it has two major disadvantages: high sodium concentration in softened water and high chloride content in the brine which is often discharged into the sewer.