AP-42, CH 12.20: Electroplating
Total Page:16
File Type:pdf, Size:1020Kb
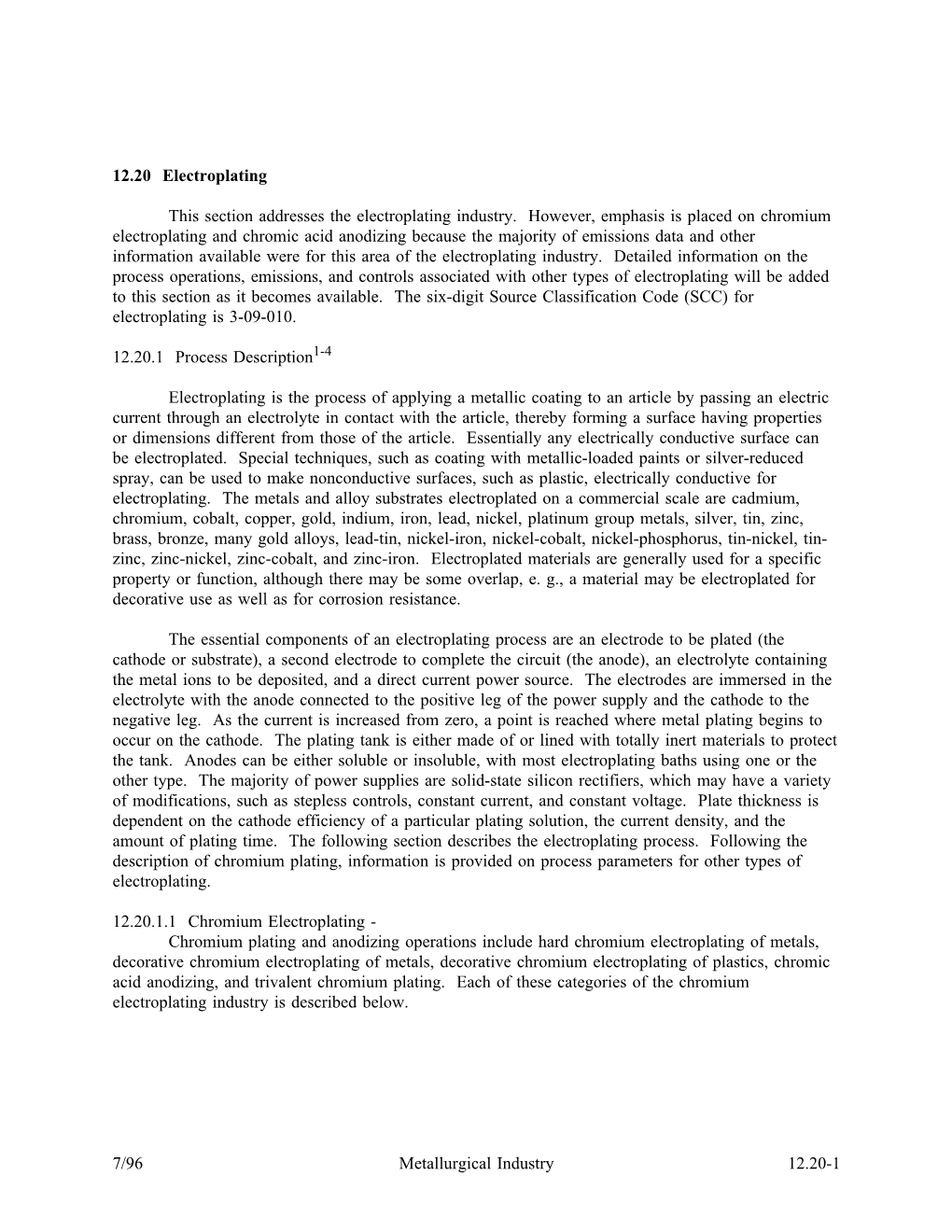
Load more
Recommended publications
-
Characterization of Copper Electroplating And
CHARACTERIZATION OF COPPER ELECTROPLATING AND ELECTROPOLISHING PROCESSES FOR SEMICONDUCTOR INTERCONNECT METALLIZATION by JULIE MARIE MENDEZ Submitted in partial fulfillment of the requirements For the degree of Doctor of Philosophy Dissertation Advisor: Dr. Uziel Landau Department of Chemical Engineering CASE WESTERN RESERVE UNIVERSITY August, 2009 CASE WESTERN RESERVE UNIVERSITY SCHOOL OF GRADUATE STUDIES We hereby approve the thesis/dissertation of _____________________________________________________ candidate for the ______________________degree *. (signed)_______________________________________________ (chair of the committee) ________________________________________________ ________________________________________________ ________________________________________________ ________________________________________________ ________________________________________________ (date) _______________________ *We also certify that written approval has been obtained for any proprietary material contained therein. TABLE OF CONTENTS Page Number List of Tables 3 List of Figures 4 Acknowledgements 9 List of Symbols 10 Abstract 13 1. Introduction 15 1.1 Semiconductor Interconnect Metallization – Process Description 15 1.2 Mechanistic Aspects of Bottom-up Fill 20 1.3 Electropolishing 22 1.4 Topics Addressed in the Dissertation 24 2. Experimental Studies of Copper Electropolishing 26 2.1 Experimental Procedure 29 2.2 Polarization Studies 30 2.3 Current Steps 34 2.3.1 Current Stepped to a Level below Limiting Current 34 2.3.2 Current Stepped to the Limiting -
Methods to Improve the Corrosion Performance of Microporous Nickel Deposits
Methods to Improve The Corrosion Performance Of Microporous Nickel Deposits By Robert A. Tremmel During the last several years, nickel, which is essentially sulfur- microporous nickel-chromium free, plus a thinner layer of bright coatings have been critically nickel. Duplex nickel provides scrutinized by the automotive corrosion protection that is far industry. Today these coatings must superior to single layer systems. In be free of all surface defects, even these duplex systems, when corrosion after long-term exposure to acceler- occurs through a pore in the chro- ated tests and in real-life service. mium plate, the bright nickel is While proper control of all the rapidly penetrated until the semi- multi-layer nickel deposits is bright nickel is reached. Because the important, blemish-free surfaces electrochemical potential of the semi- Fig. 1—Corrosion mechanism of decorative nickel- can only be obtained when the chromium deposits. bright deposit is greater than that of microdiscontinuity and the activity the bright nickel deposit, thereby of the post-nickel strike are prop- making it more noble, the bright erly achieved and maintained. This also be free of surface defects1. nickel layer will corrode preferen- edited version of a paper presented Simply meeting porosity specifica- tially to the semi-bright nickel layer. at SUR/FIN® ’96—Cleveland shows tions is not enough. The size of the As the pit widens, however, some that research indicates that the pores is important, as well as the attack will eventually occur in the most important factor is the electrochemical potential of the semi-bright nickel layer and ulti- electrochemical potential of the microporous nickel strike. -
Troubleshooting Decorative Electroplating Installations, Part 5
Troubleshooting Decorative Electroplating Installations, Part 5: Plating Problems Caused Article By Heat & Bath Temperature Fluctuations by N.V. Mandich, CEF, AESF Fellow Technical Technical In previous parts of this series, emphasis was given The fast-machining steels must then be carburized to troubleshooting of the sequences for pre-plating or case-hardened to obtain a surface with the hardness and electroplating over metals, Parts 1 and 2;1 required to support the top chromium electroplate. the causes, symptoms and troubleshooting for Case hardening is the generic term covering several pores, pits, stains, blistering and “spotting-out” processes applicable to steel or ferrous alloys. It changes phenomena, Part 3;2 and troubleshooting plating on the surface composition of the top layer, or case, by plastic systems, Part 4.3 Here in Part 5, causes and adsorption of carbon, nitrogen or a mixture of the two. some typical examples of problems that occur in By diffusion, a concentration gradient is created. The electroplating as a result of a) thermal, mechanical heat-treatments and the composition of the steel are surface treatments, b) the metallurgy of the part to additional variables that should be addressed and taken be plated or c) effects of plating bath temperature into account in the electroplating procedure. on plating variables and quality of the deposits When discussing the effect of heat-treatment on are discussed. subsequent electroplating processes it is necessary to zero in on the type of heat-treatment involved. We Nearly every plater has at one time or another had the can defi ne the heat-treatment process as changing the experience of trying to plate parts that simply would characteristics of the parts by heating above a certain not plate. -
Ri Wkh% Lrorjlfdo (Iihfwv Ri 6Hohfwhg &Rqvwlwxhqwv
Guidelines for Interpretation of the Biological Effects of Selected Constituents in Biota, Water, and Sediment November 1998 NIATIONAL RRIGATION WQATER UALITY P ROGRAM INFORMATION REPORT No. 3 United States Department of the Interior Bureau of Reclamation Fish and Wildlife Service Geological Survey Bureau of Indian Affairs 8QLWHG6WDWHV'HSDUWPHQWRI WKH,QWHULRU 1DWLRQDO,UULJDWLRQ:DWHU 4XDOLW\3URJUDP LQIRUPDWLRQUHSRUWQR *XLGHOLQHVIRU,QWHUSUHWDWLRQ RIWKH%LRORJLFDO(IIHFWVRI 6HOHFWHG&RQVWLWXHQWVLQ %LRWD:DWHUDQG6HGLPHQW 3DUWLFLSDWLQJ$JHQFLHV %XUHDXRI5HFODPDWLRQ 86)LVKDQG:LOGOLIH6HUYLFH 86*HRORJLFDO6XUYH\ %XUHDXRI,QGLDQ$IIDLUV 1RYHPEHU 81,7('67$7(6'(3$570(172)7+(,17(5,25 %58&(%$%%,776HFUHWDU\ $Q\XVHRIILUPWUDGHRUEUDQGQDPHVLQWKLVUHSRUWLVIRU LGHQWLILFDWLRQSXUSRVHVRQO\DQGGRHVQRWFRQVWLWXWHHQGRUVHPHQW E\WKH1DWLRQDO,UULJDWLRQ:DWHU4XDOLW\3URJUDP 7RUHTXHVWFRSLHVRIWKLVUHSRUWRUDGGLWLRQDOLQIRUPDWLRQFRQWDFW 0DQDJHU1,:43 ' %XUHDXRI5HFODPDWLRQ 32%R[ 'HQYHU&2 2UYLVLWWKH1,:43ZHEVLWHDW KWWSZZZXVEUJRYQLZTS Introduction The guidelines, criteria, and other information in The Limitations of This Volume this volume were originally compiled for use by personnel conducting studies for the It is important to note five limitations on the Department of the Interior's National Irrigation material presented here: Water Quality Program (NIWQP). The purpose of these studies is to identify and address (1) Out of the hundreds of substances known irrigation-induced water quality and to affect wetlands and water bodies, this contamination problems associated with any of volume focuses on only nine constituents or the Department's water projects in the Western properties commonly identified during States. When NIWQP scientists submit NIWQP studies in the Western United samples of water, soil, sediment, eggs, or animal States—salinity, DDT, and the trace tissue for chemical analysis, they face a elements arsenic, boron, copper, mercury, challenge in determining the sig-nificance of the molybdenum, selenium, and zinc. -
Analysis of Hard Chromium Coating Defects and Its Prevention Methods
International Journal of Engineering and Advanced Technology (IJEAT) ISSN: 2249 – 8958, Volume-2, Issue-5, June 2013 Analysis of Hard Chromium Coating Defects and its Prevention Methods L.Maria Irudaya Raj, Sathishkumar.J, B.Kumaragurubaran, P.Gopal Abstract — This paper mainly deals with various Chromium coating defects that occur while electro plating of different II. COATING mechanical components and methodology adopted to prevent it. It also covers suggestions to minimize this problem. This paper Coating may be defined as a coverage that is applied over contains new suggestions to minimize the problems by using the surface of any metal substrate part/object. The purpose of recent technological developments. Since the chemicals used for applying coatings is to improve surface properties of a bulk chromium coating are posing threat to environment it is need of material usually referred to as a substrate. One can improve the hour to minimise the use such chemical consumption. The amongst others appearance, adhesion, wetability, corrosion reduction in defective components will increase productivity as resistance, wear resistance, scratch resistance, etc. well as protect the environment to some extent It also describes the various alternate coating methods for chromium coating through III. HARD CHROME COATING PROCESS which we can achieve the required surface properties. India being a Developing country .for various coating application chromium The coating process consists of Chrome Chemical Bath, is used. Since the process is slow and involves lengthy cycle time Anode, Cathode potentials, part to be coated, Heaters, unless the defects are minimized the products cannot be delivered rectifiers & Electrical control systems. Initially the bath has to in time which will create loss to the Industries. -
Carpenter Ants and Control in Homes Page 1 of 6
Carpenter Ants and Control in Homes Page 1 of 6 Carpenter Ants and Control in Homes Fact Sheet No. 31 Revised May 2000 Dr. Jay B Karren, Extension Entomologist Alan H. Roe, Insect Diagnostician Introduction Carpenter ants are members of the insect order Hymenoptera, which includes bees, wasps, sawflies, and other ants. Carpenter ants can be occasional pests in the home and are noted particularly for the damage they can cause when nesting in wood. In Utah they are more of a nuisance rather than a major structural pest. Carpenter ants, along with a number of other ant species, utilize cavities in wood, particularly stumps and logs in decayed condition, as nesting sites. They are most abundant in forests and can be easily found under loose bark of dead trees, stumps, or fallen logs. Homeowners may bring them into their homes when they transport infested logs from forests to use as firewood. Description Carpenter ants include species that are among the largest ants found in the United States. They are social insects with a complex and well-defined caste system. The worker ants are sterile females and may occur in different sizes (majors and minors). Members of the reproductive caste (fertile males and females) are usually winged prior to mating. All ants develop from eggs deposited by a fertilized female (queen). The eggs hatch into grub-like larvae (immatures) which are fed and cared for by the workers. When fully grown, the larvae spin a cocoon and enter the pupal stage. The pupal stage is a period of transformation from the larva to adult. -
Opinion & Information on Boric Acid
Opinion & Information on Boric Acid By Michael R. Cartwright, Sr. (Michael R. Cartwright, Sr. is a third generation licensed professional in the fields of structural pest control and building construction and is also licensed in agriculture pest control. His qualifications are too extensive to print but are available on request from The Reporter.) Over the past years I have seen, in many homes and restaurants, boric acid covering everything. Carpets, floors, toys and furniture, in kitchen cabinets, on counter tops and tables, in refrigerators, clothing, etc. Why? Because environmentalists, helped by an uninformed news media, tell them to. Why don't the news media also explain the possible dangers of applying something not normally found in the home environment, that you or your animals will come in direct contact with? I'm writing this article even though a California environmentalist group advised me not to say anything against boric acid and that I would pay dearly for only trying to mislead the public. My company uses a lot of boric acid, but not as described above. Under an OSHA Hazard Communication Standard, based on animal chronic toxicity studies of inorganic borate chemicals, boric acid and/or borates are Hazardous Materials. California has identified boric acid as a hazardous waste. The above information is taken from Material Safety Data Sheet (MSDS) 25-80-2320 (Section 2 and 13) supplied by U.S. Borax Inc. (the major supplier of borax to many industries). The National Academy of Sciences reports that children may be uniquely sensitive to chemicals and pesticide residues because of their rapid tissue growth and development. -
Resume Wonsub Chung
Resume Wonsub Chung Contact Information Wonsub Chung, ph.D. Professor Division of Material Science & Engineering Pusan National University 2, Busandaehak-ro 63beon-gil, Geumjeong-gu Busan, 46241 Korea e-mail:[email protected] Tel: +82-51-510-2386 H.P. : +82-10-8517-0855 Fax : +82-51-514-4457 Personal DOB : 1-23-1957, Male, Married, Born in South Korea Education Ph.D., Materials Science and Engineering. 1985-1989 Kyushu University, Hukuoka, Japan(Advisor: Prof. Ono Yoichi) Thesis: A Basic Study on Gas Reduction of Calcium Ferrite M.S., Materials Science and Engineering, 1983-1985 Pusan National University, Busan, South Korea (Advisor: Prof. Kyusub Song) Thesis: B.S., Materials Science and Engineering, 1978-1983 Pusan National University, Busan, South Korea, Major Career ∎ 1989-1992 Chief Researcher RIST(Research Institute of Industrial Science & Technology) Iron Ore Melting Reduction Research Project Team ∎ 1993-Present : Professor Pusan National University Division of Material Science & Engineering ∎ 1999-2000 Exchange professor Colorado School of Mines, Colorado, USA Research Interests Energy saving and Radiation Heat transfer and dissipation Study on Water Electrolysis Using Radiation and Electrical Energy Study on Reduction of Covalent Bonding Energy of Reaction Using Radiation and Electric Energy A study on the gasification reaction of coal using radiant energy Electrochemical anodic oxidation and deposition Corrosion and prevention of metallic materials (Mg, Al alloys and steels) Surface physics and chemistry Expertise -
UDDEHOLM STAVAX® ESR © UDDEHOLMS AB No Part of This Publication May Be Reproduced Or Transmitted for Commercial Purposes Without Permission of the Copyright Holder
UDDEHOLM STAVAX® ESR © UDDEHOLMS AB No part of this publication may be reproduced or transmitted for commercial purposes without permission of the copyright holder. This information is based on our present state of knowledge and is intended to provide general notes on our products and their uses. It should not therefore be construed as a warranty of specific properties of the products described or a warranty for fitness for a particular purpose. Classified according to EU Directive 1999/45/EC For further information see our “Material Safety Data Sheets”. Edition 11, 05.2013 The latest revised edition of this brochure is the English version, SS-EN ISO 9001 which is always published on our web site www.uddeholm.com SS-EN ISO 14001 UDDEHOLM STAVAX ESR UDDEHOLM STAVAX ESR Uddeholm Stavax ESR is a premium stainless mould steel for small and medium inserts and cores. Uddeholm Stavax ESR combines corrosion and wear resistance with excellent polishability, good machinability and stability in hardening. Mould maintenance requirement is reduced by assuring that core and cavity surfaces retain their original finish over extended operating periods. When compared with non stainless mould steel, Uddeholm Stavax ESR offers lower production costs by maintaining rust free cooling channels, assuring consistent cooling and cycle time. This classic stainless tool steel is the right choice when rust in production is unacceptable and where requirements for good hygiene are high, as within the medical industry, optical industry and for other high quality transparent parts. Uddeholm Stavax ESR is a part of the Uddeholm Stainless Concept 3 UDDEHOLM STAVAX ESR General Applications Uddeholm Stavax ESR is a premium grade Uddeholm Stavax ESR is recommended for all stainless tool steel with the following proper- types of moulding tools and its special proper- ties: ties make it particularly suitable for moulds •good corrosion resistance with the following demands: •excellent polishability • Corrosion/staining resistance, i.e. -
Electroless Copper Plating a Review: Part I
Electroless Copper Plating A Review: Part I By Cheryl A. Deckert Electroless, or autocatalytic, metal plating is a non- necessary components of an electro- electrolytic method of deposition from solution. The less plating solution are the metal salt minimum necessary components of an electroless and a reducing agent. The source of plating solution are a metal salt and an appropriate copper is a simple cupric salt, such as reducing agent. An additional requirement is that the copper sulfate, chloride or nitrate. solution, although thermodynamically unstable, is Various common reducing agents stable in practice until a suitable catalyzed surface is have been suggested7 for use in elec- introduced. Plating is then initiated upon the catalyzed troless copper baths, namely formal- surface, and the plating reaction is sustained by the dehyde, dimethylamine borane, boro- catalytic nature of the plated metal surface itself. This hydride, hypophosphite,8 hydrazine, definition of electroless plating eliminates both those sugars (sucrose, glucose, etc.), and solutions that spontaneously plate on all surfaces dithionite. In practice, however, vir- (“homogeneous chemical reduction”), such as silver tually all commercial electroless cop- mirroring solutions; also “immersion” plating solu- per solutions have utilized formalde- tions, which deposit by displacement a very thin film of hyde as reducing agent. This is a a relatively noble metal onto the surface of a sacrificial, result of the combination of cost, less noble metal. effectiveness, and ease -
OVERVIEW of FOUNDRY PROCESSES Contents 1
Cleaner Production Manual for the Queensland Foundry Industry November 1999 PART 5: OVERVIEW OF FOUNDRY PROCESSES Contents 1. Overview of Casting Processes...................................................................... 3 2. Casting Processes.......................................................................................... 6 2.1 Sand Casting ............................................................................................ 6 2.1.1 Pattern Making ................................................................................... 7 2.1.2 Mould Making ..................................................................................... 7 2.1.3 Melting and Pouring ........................................................................... 8 2.1.4 Cooling and Shakeout ........................................................................ 9 2.1.5 Sand Reclamation .............................................................................. 9 2.1.6 Fettling, Cleaning and Finishing....................................................... 10 2.1.7 Advantages of Sand Casting............................................................ 10 2.1.8 Limitations ........................................................................................ 10 2.1.9 By-products Generated .................................................................... 10 2.2 Shell Moulding ........................................................................................ 13 2.2.1 Advantages...................................................................................... -
Metals and Metal Products Tariff Schedules of the United States
251 SCHEDULE 6. - METALS AND METAL PRODUCTS TARIFF SCHEDULES OF THE UNITED STATES SCHEDULE 6. - METALS AND METAL PRODUCTS 252 Part 1 - Metal-Bearing Ores and Other Metal-Bearing Schedule 6 headnotes: Materials 1, This schedule does not cover — Part 2 Metals, Their Alloys, and Their Basic Shapes and Forms (II chemical elements (except thorium and uranium) and isotopes which are usefully radioactive (see A. Precious Metals part I3B of schedule 4); B. Iron or Steel (II) the alkali metals. I.e., cesium, lithium, potas C. Copper sium, rubidium, and sodium (see part 2A of sched D. Aluminum ule 4); or E. Nickel (lii) certain articles and parts thereof, of metal, F. Tin provided for in schedule 7 and elsewhere. G. Lead 2. For the purposes of the tariff schedules, unless the H. Zinc context requires otherwise — J. Beryllium, Columbium, Germanium, Hafnium, (a) the term "precious metal" embraces gold, silver, Indium, Magnesium, Molybdenum, Rhenium, platinum and other metals of the platinum group (iridium, Tantalum, Titanium, Tungsten, Uranium, osmium, palladium, rhodium, and ruthenium), and precious- and Zirconium metaI a Iloys; K, Other Base Metals (b) the term "base metal" embraces aluminum, antimony, arsenic, barium, beryllium, bismuth, boron, cadmium, calcium, chromium, cobalt, columbium, copper, gallium, germanium, Part 3 Metal Products hafnium, indium, iron, lead, magnesium, manganese, mercury, A. Metallic Containers molybdenum, nickel, rhenium, the rare-earth metals (Including B. Wire Cordage; Wire Screen, Netting and scandium and yttrium), selenium, silicon, strontium, tantalum, Fencing; Bale Ties tellurium, thallium, thorium, tin, titanium, tungsten, urani C. Metal Leaf and FoU; Metallics um, vanadium, zinc, and zirconium, and base-metal alloys; D, Nails, Screws, Bolts, and Other Fasteners; (c) the term "meta I" embraces precious metals, base Locks, Builders' Hardware; Furniture, metals, and their alloys; and Luggage, and Saddlery Hardware (d) in determining which of two or more equally specific provisions for articles "of iron or steel", "of copper", E.