Buffet-Onset Constraint Formulation for Aerodynamic Shape Optimization
Total Page:16
File Type:pdf, Size:1020Kb
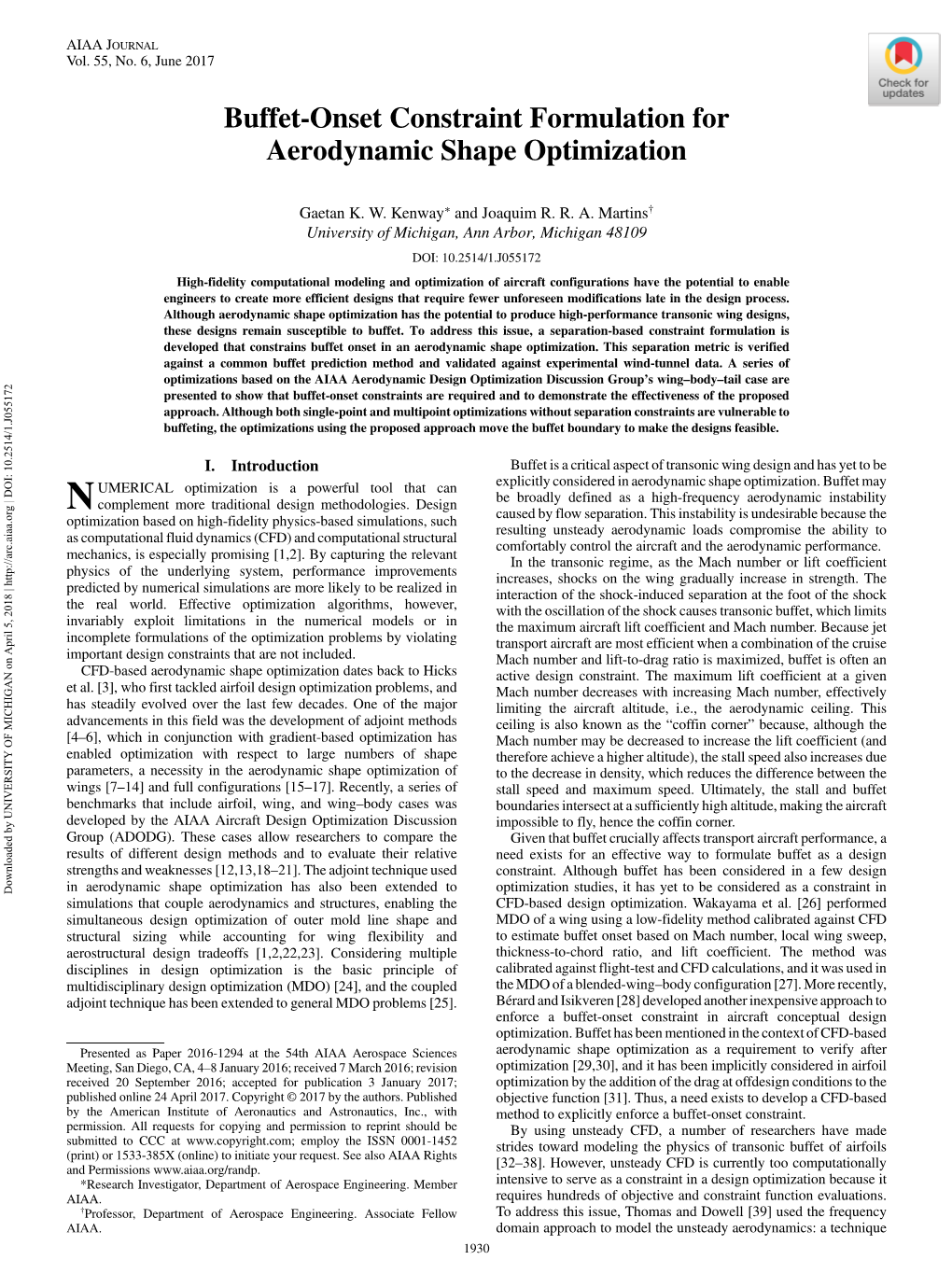
Load more
Recommended publications
-
Fly-By-Wire - Wikipedia, the Free Encyclopedia 11-8-20 下午5:33 Fly-By-Wire from Wikipedia, the Free Encyclopedia
Fly-by-wire - Wikipedia, the free encyclopedia 11-8-20 下午5:33 Fly-by-wire From Wikipedia, the free encyclopedia Fly-by-wire (FBW) is a system that replaces the Fly-by-wire conventional manual flight controls of an aircraft with an electronic interface. The movements of flight controls are converted to electronic signals transmitted by wires (hence the fly-by-wire term), and flight control computers determine how to move the actuators at each control surface to provide the ordered response. The fly-by-wire system also allows automatic signals sent by the aircraft's computers to perform functions without the pilot's input, as in systems that automatically help stabilize the aircraft.[1] Contents Green colored flight control wiring of a test aircraft 1 Development 1.1 Basic operation 1.1.1 Command 1.1.2 Automatic Stability Systems 1.2 Safety and redundancy 1.3 Weight saving 1.4 History 2 Analog systems 3 Digital systems 3.1 Applications 3.2 Legislation 3.3 Redundancy 3.4 Airbus/Boeing 4 Engine digital control 5 Further developments 5.1 Fly-by-optics 5.2 Power-by-wire 5.3 Fly-by-wireless 5.4 Intelligent Flight Control System 6 See also 7 References 8 External links Development http://en.wikipedia.org/wiki/Fly-by-wire Page 1 of 9 Fly-by-wire - Wikipedia, the free encyclopedia 11-8-20 下午5:33 Mechanical and hydro-mechanical flight control systems are relatively heavy and require careful routing of flight control cables through the aircraft by systems of pulleys, cranks, tension cables and hydraulic pipes. -
Birds Change the Shape of Their Wings in Flight. Now, Aircraft Designers Have Come up with the Mission Adaptive Wing to Give Aircraft Some of the Same Advantages
Birds change the shape of their wings in flight. Now, aircraft designers have come up with the Mission Adaptive Wing to give aircraft some of the same advantages. Pilot Report: AFTI F-111 BY MAJ. SCOTT E. PARKS, USAF IRDS are beautiful and efficient Prior to the jet age, optimizing The Mission Adaptive flying machines. I have often wing shape was not a concern be- Wing, a radically new B concept, enables an observed hawks flying high above cause of limitations in aircraft al- aircraft to change the desert at Edwards AFB, Calif., titudes and airspeeds. Later expan- wing shape continu- effortlessly positioning their wings sion of the flight envelope, with the ously and smoothly to the optimum shape dictated by advent of jet-powered supersonic while in flight for greatly improved instinct and learned through experi- fighters and bombers, forced de- agility and perfor- ence. They soar smoothly in the signers to recognize the critical mance. Shown at summer afternoon thermals with need for a variable shape wing. right is the Advanced wings comfortably forward, only to High-performance aircraft need a Fighter Technology dive suddenly for an unsuspecting wing that is efficient at high sub- Integration (AFTI) test craft, a special F-111 target at high speed with wings sonic and supersonic speeds and fitted with the devel- swept back. Landings, on the other that at the same time can minimize opmental wing. hand, require the hawk's wing to be approach speeds for landing. Flaps forward and highly curved, or cam- are one answer to this dilemma. -
Level Flight Performance and Level Flight Envelope
Performance 11. Level Flight Performance and Level flight Envelope We are interested in determining the maximum and minimum speeds that an aircraft can fly in level flight. If we do this for all altitudes, the locus of theses points as they change with altitude describes the flight envelope. It is important to characterize aircraft into two categories: 1) those whose power plant outputs are measured in terms of thrust (turbojets, and turbofans), and 2) those whose power plant outputs are measured in terms of power (piston propeller combinations and turboprops) Power Plant Output in Terms of Thrust - General - Arbitrary Drag Polar It is natural to look at these types of vehicles first since the equations that have to be satisfied for level flight are: (1) From the previous work on thrust and drag models, we know the functional form of both the thrust and drag. The drag (or thrust required) depends on the density (altitude), airspeed, and the vehicle weight, and therefore has the general form: Thrust required: (2) The thrust available (the output of the engine) depends on the density (altitude), airspeed, and the throttle setting, and therefore has the general form: Thrust available: (3) Consequently, for a given altitude, weight, and throttle setting, the thrust available, and the thrust required (drag) become a function of only airspeed or Mach number. Then for level flight, we must satisfy Eq. (1). To solve this equation for a given throttle setting, altitude, and weight, we can plot the thrust available, and thrust required (drag), vs airspeed or Mach number and observe where the graphs cross. -
The Pennsylvania State University the Graduate School Department of Aerospace Engineering an INVESTIGATION of PERFORMANCE BENEFI
The Pennsylvania State University The Graduate School Department of Aerospace Engineering AN INVESTIGATION OF PERFORMANCE BENEFITS AND TRIM REQUIREMENTS OF A VARIABLE SPEED HELICOPTER ROTOR A Thesis in Aerospace Engineering by Jason H. Steiner 2008 Jason H. Steiner Submitted in Partial Fulfillment of the Requirements for the Degree of Master of Science August 2008 ii The thesis of Jason Steiner was reviewed and approved* by the following: Farhan Gandhi Professor of Aerospace Engineering Thesis Advisor Robert Bill Research Associate , Department of Aerospace Engineering George Leisuietre Professor of Aerospace Engineering Head of the Department of Aerospace Engineering *Signatures are on file in the Graduate School iii ABSTRACT This study primarily examines the main rotor power reductions possible through variation in rotor RPM. Simulations were based on the UH-60 Blackhawk helicopter, and emphasis was placed on possible improvements when RPM variations were limited to ± 15% of the nominal rotor speed, as such limited variations are realizable through engine speed control. The studies were performed over the complete airspeed range, from sea level up to altitudes up to 12,000 ft, and for low, moderate and high vehicle gross weight. For low altitude and low to moderate gross weight, 17-18% reductions in main rotor power were observed through rotor RPM reduction. Reducing the RPM increases rotor collective and decreases the stall margin. Thus, at higher airspeeds and altitudes, the optimal reductions in rotor speed are smaller, as are the power savings. The primary method for power reduction with decreasing rotor speed is a decrease in profile power. When rotor speed is optimized based on both power and rotor torque, the optimal rotor speed increases at low speeds to decrease rotor torque without power penalties. -
Approaches to Assure Safety in Fly-By-Wire Systems: Airbus Vs
APPROACHES TO ASSURE SAFETY IN FLY-BY-WIRE SYSTEMS: AIRBUS VS. BOEING Andrew J. Kornecki, Kimberley Hall Embry Riddle Aeronautical University Daytona Beach, FL USA <[email protected]> ABSTRACT The aircraft manufacturers examined for this paper are Fly-by-wire (FBW) is a flight control system using Airbus Industries and The Boeing Company. The entire computers and relatively light electrical wires to replace Airbus production line starting with A320 and the Boeing conventional direct mechanical linkage between a pilot’s 777 utilize fly-by-wire technology. cockpit controls and moving surfaces. FBW systems have been in use in guided missiles and subsequently in The first section of the paper presents an overview of military aircraft. The delay in commercial aircraft FBW technology highlighting the issues associated with implementation was due to the time required to develop its use. The second and third sections address the appropriate failure survival technologies providing an approaches used by Airbus and Boeing, respectively. In adequate level of safety, reliability and availability. each section, the nature of the FBW implementation and Software generation contributes significantly to the total the human-computer interaction issues that result from engineering development cost of the high integrity digital these implementations for specific aircraft are addressed. FBW systems. Issues related to software and redundancy Specific examples of software-related safety features, techniques are discussed. The leading commercial aircraft such as flight envelope limits, are discussed. The final manufacturers, such as Airbus and Boeing, exploit FBW section compares the approaches and general conclusions controls in their civil airliners. The paper presents their regarding the use of FBW technology. -
UAS FLIGHT TEST for SAFETY and for EFFICIENCY Seamus M
UAS FLIGHT TEST FOR SAFETY AND FOR EFFICIENCY Seamus M. McGovern, U.S. DOT National Transportation Systems Center, Cambridge, Massachusetts Abstract (e.g., SAE International technical standards and recommended practices) but also takes advantage of Manned aircraft that operate in the National competitive racing in order to evaluate new Airspace System (NAS) typically undergo technologies and materials (as it turns out, this may certification flight test to ensure they meet a have applicability to UASs as well with the advent of prescribed level of safety—dependent on their several organizations and sanctioning bodies category—before they are able to enter service [for including the European Rotor Sports Association and example, Federal Aviation Administration (FAA) the Drone Racing League). Other aviation-related advisory circular (AC) 25-7C is the flight-test guide tests and test formats not discussed here include the for certification of transport-category airplanes]. typically Department of Defense-focused With the integration of unmanned aircraft systems developmental test and evaluation; operational test (UAS) into the NAS, in the future some type of and evaluation; and research, development, test, and certification flight test may ultimately be required, evaluation structures. however, even lacking such a requirement UAS manufacturers can find value in flight testing UASs In terms of flight test, the military services have using familiar experimental and certification flight- their own criteria for evaluating their various aircraft. test procedures, the results of which can enhance the These requirements are often bound by contractual safety of the design, the safety of the operation, agreements between the service and the vendor, and/or the efficiency of the operation. -
Chapter 9 Energy
VOLUME I PERFORMANCE FLIGHT TEST PHASE CHAPTER 9 ENERGY >£>* ^ AUGUST 1991 USAF TEST PILOT SCHOOL EDWARDS AFB, CA I Approved for public rate-erne; ! Distribution Uni;: r<cA 19970116 079 Table of Contents 9.1 INTRODUCTION 9.1 9.1.1 AIRCRAFT PERFORMANCE MODELS 9.1 9.1.2 NEED FOR NONSTEADY STATE MODELS 9.1 9.2 STEADY STATE CLIMBS AND DESCENTS 9.2 9.2.1 FORCES ACTING ON AN AIRCRAFT IN FLIGHT 9.2 9.2.2 ANGLE OF CLIMB PERFORMANCE 9.5 9.2.3 RATE OF CLIMB PERFORMANCE 9.9 9.2.4 TIME TO CLIMB DETERMINATION 9.14 9.2.5 GLIDING PERFORMANCE 9.16 9.2.6 POLAR DIAGRAMS 9.18 9.3 BASIC ENERGY STATE CONCEPTS 9.22 9.3.1 ASSUMPTIONS 9.22 9.3.2 ENERGY DEFINITIONS 9.23 9.3.3 SPECD7IC ENERGY 9.24 9.3.4 SPECD7IC EXCESS POWER 9.24 9.4 THEORETICAL BASIS FOR ENERGY OPTIMIZATIONS 9.25 9.5 GRAPHICAL TOOLS FOR ENERGY APPROXIMATION 9.25 9.5.1 SPECD7IC ENERGY OVERLAY 9.26 9.5.2 SPECmC EXCESS POWER PLOTS 9.28 9.6 TIME OPTIMAL CLIMBS 9.36 9.6.1 GRAPHICAL APPROXIMATIONS TO RUTOWSKI CONDITIONS 9.36 9.6.2 MINIMUM TIME TO ENERGY LEVEL PROFILES 9.37 9.6.3 SUBSONIC TO SUPERSONIC TRANSITIONS 9.38 9.7 FUEL OPTIMAL CLIMBS 9.40 9.7.1 FUEL EFFICIENCY 9.41 9.7.2 COMPARISON OF FUEL OPTIMAL AND TIME OPTIMAL PATHS 9.43 9.8 MANEUVERABILITY 9.44 9.9 INSTANTANEOUS MANEUVERABILITY 9.44 9.9.1 LIFT BOUNDARY LIMITATION 9.45 9.9.2 STRUCTURAL LIMITATION 9.46 9.9.3 qLIMTTATION 9.46 9.9.4 PILOT LIMITATIONS 9.46 9.10 THRUST LIMITATIONS/SUSTAINED MANEUVERABILITY 9.47 9.10.1 SUSTAINED TURN PERFORMANCE 9.47 9.10.2 FORCES IN ATURN 9.47 9.11 VERTICAL TURNS 9-52 9.12 OBLIQUE PLANE MANEUVERING 9.53 9.13 -
Full Flight-Envelope Simulation and Piloted Fidelity Assessment of a Business Jet Using a Model Stitching Architecture
Full Flight-Envelope Simulation and Piloted Fidelity Assessment of a Business Jet Using a Model Stitching Architecture Eric L. Tobias∗ San Jose State University Foundation, Moffett Field, CA Mark B. Tischlery U.S. Army Aviation Development Directorate { AFDD, Moffett Field, CA Tom Bergerz Steven G. Hagerottx University Affiliated Research Center, Moffett Field, CA Cessna Aircraft Company, Wichita, KS This paper presents the development and piloted assessment of a full flight-envelope simulation model of a light business jet using a model stitching architecture. Individual state-space models and trim data for discrete flight conditions were combined to produce a continuous simulation model, which was integrated into a fixed-base simulation facility. Back-to-back flight/simulation piloted evaluations of a similar light business jet in flight and the stitched model in simulation were performed to assess the fidelity of the stitched model. Overall pilot impressions were that the stitched simulation model was representative of the actual aircraft. Simulation Fidelity Ratings were given to quantify simulation fidelity for each of the evaluated qualitative tasks, in which mostly Fidelity Level 1 ratings were assigned, suggesting full transfer of training for those tasks. Guidance on flight testing for the development of fixed-wing aircraft stitched models is provided. Nomenclature A; B; C; D State-space matrix representation of dynamic system model F External force vector [lb] g Acceleration due to gravity [ft/sec2] I Inertia tensor 2 Ixx;Iyy;Izz Moments -
Ac 61-107A - Operations of Aircraft at Altitudes Above 25,000 Feet Msl And/Or Mach Numbers (Mmo) Greater Than .75
AC 61-107A - OPERATIONS OF AIRCRAFT AT ALTITUDES ABOVE 25,000 FEET MSL AND/OR MACH NUMBERS (MMO) GREATER THAN .75 {New-2003-09} Department of Transportation Federal Aviation Administration 1/2/03 Initiated by: AFS-820 1. PURPOSE. This advisory circular (AC) is issued to alert pilots who are transitioning from aircraft with less performance capability to complex, high-performance aircraft that are capable of operating at high altitudes and high airspeeds, of the need to be knowledgeable about the special physiological and aerodynamic considerations involved in these kinds of operations. 2. CANCELLATION. AC 61-107, Operations of Aircraft at Altitudes Above 25,000 Feet MSL and/or Mach Numbers (Mmo) Greater Than .75, dated January 23, 1991, is cancelled. 3. DEFINITIONS. a. Aspect Ratio is the relationship between the wing chord and the wingspan. A short wingspan and wide wing chord equal a low aspect ratio. b. Aileron buzz is a very rapid oscillation of an aileron, at certain critical air speeds of some aircraft, which does not usually reach large magnitudes nor become dangerous. It is often caused by shock- induced separation of the boundary layer. c. Drag Divergence is a phenomenon that occurs when an airfoil's drag increases sharply and requires substantial increases in power (thrust) to produce further increases in speed. This is not to be confused with MACH crit. The drag increase is due to the unstable formation of shock waves that transform a large amount of energy into heat and into pressure pulses that act to consume a major portion of the available propulsive energy. -
Comparative Analysis of Conventional Electronic and OZ Concept Displays for Aircraft Energy Management
Dissertations and Theses 8-2017 Comparative Analysis of Conventional Electronic and OZ Concept Displays for Aircraft Energy Management Erik Reese Baker Follow this and additional works at: https://commons.erau.edu/edt Part of the Aerospace Engineering Commons, and the Aviation Commons Scholarly Commons Citation Baker, Erik Reese, "Comparative Analysis of Conventional Electronic and OZ Concept Displays for Aircraft Energy Management" (2017). Dissertations and Theses. 352. https://commons.erau.edu/edt/352 This Dissertation - Open Access is brought to you for free and open access by Scholarly Commons. It has been accepted for inclusion in Dissertations and Theses by an authorized administrator of Scholarly Commons. For more information, please contact [email protected]. COMPARATIVE ANALYSIS OF CONVENTIONAL ELECTRONIC AND OZ CONCEPT DISPLAYS FOR AIRCRAFT ENERGY MANAGEMENT By Erik Reese Baker A Dissertation Submitted to the College of Aviation in Partial Fulfillment of the Requirements for the Degree of Doctor of Philosophy in Aviation Embry-Riddle Aeronautical University Daytona Beach, Florida August 2017 © 2017 Erik Reese Baker All Rights Reserved. ii ABSTRACT Researcher: Erik Reese Baker Title: COMPARATIVE ANALYSIS OF CONVENTIONAL ELECTRONIC AND OZ CONCEPT DISPLAYS FOR AIRCRAFT ENERGY MANAGEMENT Institution: Embry-Riddle Aeronautical University Degree: Doctor of Philosophy in Aviation Year: 2017 A repeated-measures, within-subjects design was conducted on 58 participant pilots to assess mean differences on energy management situation awareness response time and response accuracy between a conventional electronic aircraft display, a primary flight display (PFD), and an ecological interface design aircraft display, the OZ concept display. Participants were associated with a small Midwestern aviation university, including student pilots, flight instructors, and faculty with piloting experience. -
Fly-By-Wire Augmented Manual Control - Basic Design Considerations
FLY-BY-WIRE AUGMENTED MANUAL CONTROL - BASIC DESIGN CONSIDERATIONS Dominik Niedermeier∗ , Anthony A. Lambregts∗∗ ∗Deutsches Zentrum für Luft- und Raumfahrt e.V., ∗∗Federal Aviation Administration [email protected]; [email protected] Keywords: Fly-by-Wire, Manual augmented control, C∗ control algorithm, C∗U control algorithm Abstract manufacturer allowing reduced training re- quirements After the introduction of Fly-by-Wire (FBW) flight control in the late eighties, several thousands of com- • Weight and maintenance effort reduction by re- mercial FBW aircraft are in service today. Look- placing mechanical components (e.g. pulleys, ing back, it can be concluded that FBW has brought cables) an impressive improvement to handling qualities and • Introduction of flight envelope protection func- flight safety. However, after the long time of experi- tions for enhanced safety ence with the first generations of FBW aircraft, open questions and issues with respect to the design and • Introduction of maneuver/gust load alleviation the operation of FBW have been revealed. The main functions objective of this paper is to discuss those issues and to • Optimization of aerodynamic performance (e.g. point out further research needs in this field. The char- drag reduction by aft-shifted center of gravity) acteristics of manual augmented pitch control algo- rithms implemented in commercial FBW aircraft are Manufacturer Current Models No. of deliveries discussed in detail. Subsequently the paper describes Boeing B777 1003 particular features of Airbus and Boeing FBW control B787 8 systems that are not directly related to the chosen con- Airbus A318/319/320/321 5022 trol algorithm. Open questions and resulting research A330/340 1225 needs with special focus on recent incidents and acci- A380 71 Embraer E-170/190 802 dents are discussed. -
Flight Envelope Protection for Automatic and Augmented Manual Control
Proceedings of the EuroGNC 2013, 2nd CEAS Specialist Conference on FrAT3.5 Guidance, Navigation & Control, Delft University of Technology, Delft, The Netherlands, April 10-12, 2013 Flight Envelope Protection for Automatic and Augmented Manual Control Antonius A. Lambregts* Abstract Loss of Control (LOC) is currently the largest contributing category of catastrophic airplane accidents. A large percentage of the LOC accidents involve general aviation airplanes. The FAA is therefore has sponsored research to develop certification requirements for add-on envelope protection functions. This paper briefly discusses some of the LOC accidents and the deficiencies existing in many of the current GA and Transport airplane guidance and control systems that can lead to LOC. Next the paper discusses Envelope Protection (EP) design requirements, as well as functional, safety and performance objectives and design guidelines. Various approaches to designing envelope protection functions are discussed for airplanes under automatic or augmented manual Fly by Wire (FBW) control, to prevent stall, overspeed, excessive pitch and roll attitudes and excessive Normal Load Factor (NLF). Examples of simulation time history of what can be achieved are included. 1 Introduction In spite of the large strides made in recent years to improve flight safety, Loss of Control (LOC) continues to be the largest contributing cause of accidents and incidents. Loss of Control can occur during airplane operations under automatic and under manual control, on airplanes with conventional control systems, or FBW control systems. LOC accidents and incidents can be attributed to many causes, including pilot error, airplane upsets, design malfunctions, design deficiency. LOC accidents and incidents can be further classified by main types: airplane stall during manual speed control o pilot mishandling (e.g.