Intelligent Control: an Overview of Techniques ∗
Total Page:16
File Type:pdf, Size:1020Kb
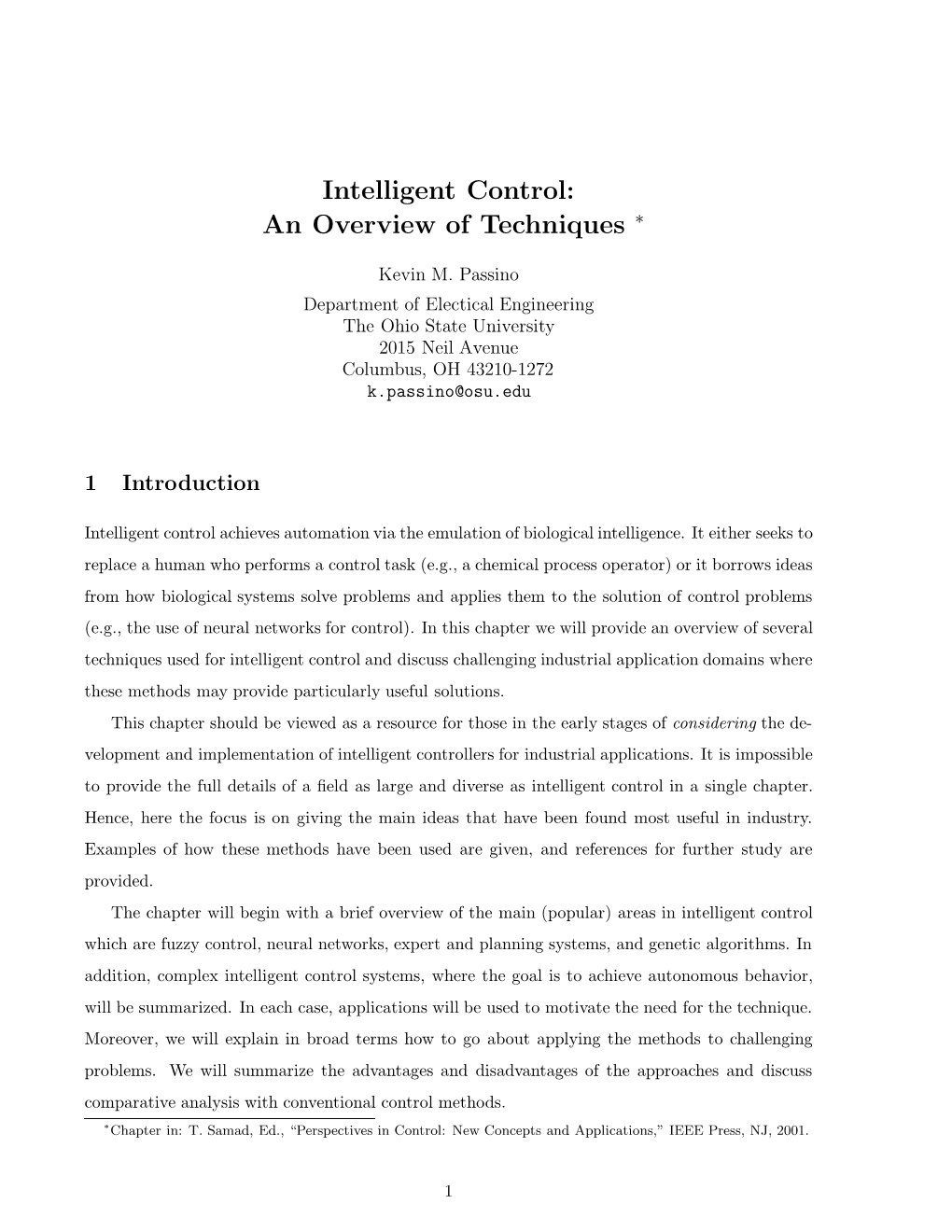
Load more
Recommended publications
-
Intelligent Multi-Agent Fuzzy Control System Under
INTELLIGENT MULTI -AGENT FUZZY CONTROL SYSTEM UNDER UNCERTAINTY Ben Khayut 1, Lina Fabri 2 and Maya Abukhana 3 1Department of R&D, IDTS at Intelligence Decisions Technologies Systems, Ashdod, Israel [email protected] 2Department of R&D, IDTS at Intelligence Decisions Technologies Systems, Ashdod, Israel [email protected] 3Department of R&D, IDTS at Intelligence Decisions Technologies Systems, Ashdod, Israel [email protected] ABSTRACT The traditional control systems are a set of hardware and software infrastructure domain and qualified personnel to facilitate the functions of analysis, planning, decision-making, management and coordination of business processes. Human interaction with the components of these systems is done using a specified in advance script dialogue "menu", mainly based on human intellect and unproductive use of navigation. This approach doesn't lead to making qualitative decision and effective control, where the situations and processes cannot be structured in advance. Any dynamic changes in the controlled business process make it necessary to modify the script dialogue. This circumstance leads to a redesign of the components of the entire control system. In the autonomous Fuzzy Control System, where the situations are unknown in advance, fuzzy structured and artificial intelligence is crucial, the redesign described above is impossible. To solve this problem, we propose the data, information and knowledge based technology of creation Situational, Intelligent Multi-agent Control System, which interacts with users -
Fuzzy Controllers
Fuzzy Controllers PRELIMS.PM5 1 6/13/97, 10:19 AM To my son Dmitry and other students PRELIMS.PM5 2 6/13/97, 10:19 AM Fuzzy Controllers LEONID REZNIK Victoria University of Technology, Melbourne, Australia PRELIMS.PM5 3 6/13/97, 10:19 AM Newnes An imprint of Butterworth-Heinemann Linacre House, Jordan Hill, Oxford OX2 8DP A division of Reed Educational and Professional Publishing Ltd A member of the Reed Elsevier plc group OXFORD BOSTON JOHANNESBURG MELBOURNE NEW DELHI SINGAPORE First published 1997 © Leonid Reznik 1997 All rights reserved. No part of this publication may be reproduced in any material form (including photocopying or storing in any medium by electronic means and whether or not transiently or incidentally to some other use of this publication) without the written permission of the copyright holder except in accordance with the provisions of the Copyright, Designs and Patents Act 1988 or under the terms of a licence issued by the Copyright Licensing Agency Ltd, 90 Tottenham Court Rd, London, England W1P 9HE. Applications for the copyright holder’s written permission to reproduce any part of this publication should be addressed to the publishers. British Library Cataloguing in Publication Data A catalogue record for this book is available from the British Library ISBN 0 7506 3429 4 Library of Congress Cataloguing in Publication Data A catalogue record for this book is available from the Library of Congress Typeset by The Midlands Book Typesetting Company, Loughborough, Leicestershire, England Printed in Great Britain by Biddles -
Temperature Control Using Fuzzy Logic
International Journal of Instrumentation and Control Systems (IJICS) Vol.4, No.1, January 2014 Temperature Control using Fuzzy Logic P. Singhala1, D. N. Shah2, B. Patel3 1,2,3Department of instrumentation and control, Sarvajanik College of Engineering and Technology Surat, Gujarat, INDIA Abstract The aim of the temperature control is to heat the system up todelimitated temperature, afterwardhold it at that temperature in insured manner. Fuzzy Logic Controller (FLC) is best way in which this type of precision control can be accomplished by controller. During past twenty yearssignificant amount of research using fuzzy logichas done in this field of control of non-linear dynamical system. Here we have developed temperature control system using fuzzy logic. Control theory techniques are the root from which convention controllers are deducted. The desired response of the output can be guaranteed by the feedback controller. Keywords Fuzzy logic, Fuzzy Logic Controller (FLC) and temperature control system. 1. Introduction Low cost temperature control using fuzzy logic system block diagram shown in the fig. in this system set point of the temperature is given by the operator using 4X4 keypad. LM35 temperature sensor sense the current temperature. Analog to digital converter convert analog value into digital value and give to the Fuzzy controller. Fig: 1 Temperature control system Controller calculates error between set point value and current value and consider as Input function of fuzzy logic. By fuzzification process controller calculate it membership. After in rule base and inference system output membership value calculated. Defuzzification process calculates actual value of PWM for heater and fan which is output of the temperature control system. -
Fuzzy Controlled Anti-Lock Braking System
International Journal of Engineering Research and Application www.ijera.com ISSN : 2248-9622, Vol. 7, Issue 7, ( Part -10) July 2017, pp.80-83 RESEARCH ARTICLE OPEN ACCESS Fuzzy Controlled Anti-Lock Braking System M M Sahu1, Manoj Kumar Nayak2, Nirmalendu Hota3 1,3Assistant Professor, Department of Mechanical Engineering, Gandhi Institute For Technology (GIFT), Bhubaneswar 2Assistant Professor, Department of Mechanical Engineering, Gandhi Engineering College, Bhubaneswar ABSTRACT:This thesis describes an intelligent approach to control an Antilock Braking System (ABS) employing a fuzzy controller. Stopping a car in a hurry on a slippery road can be very challenging. Anti-lock braking systems (ABS) take a lot of the challenge out of this sometimes nerve-wracking event. In fact, on slippery surfaces, even professional drivers can't stop as quickly without ABS as an average driver can with ABS. Anti-lock Brake improves the controllability of vehicles in compare with brake systems lacking ABS. Fuzzy is a multi-valued logic developed to deal with imprecise or vague data. Classical logic holds that everything can be expressed in binary terms: 0 or 1; in terms of Boolean algebra, everything is in one set or another but not in both. Fuzzy logic allows for partial membership in a set, values between 0 and 1. When the approximate reasoning of fuzzy logic is used with an expert system, logical inferences can be drawn from imprecise relationships. Fuzzy anti-lock Braking systems were developed to reduce skidding and maintain steering control when brakes are used in an emergency situation. Fuzzy controllers are potential candidates for the control of non-linear, time variant and complicated systems. -
Fuzzy Logic in Control Systems: Fuzzy Logic Controller, Part I1
!Err TRANSACTIONS ON SYSTEMS, MAN. ANI) C’YHT.RNT.TI(‘S, VOI.. 20, NO. 2. MAR(.II/APRII. 1000 419 Fuzzy Logic in Control Systems: Fuzzy Logic Controller, Part I1 Abstract -During the past several years, fuzzy control has emerged as I) Basic Properties of a Fuuy Implication Function: one of the most active and fruitful areas for research in the applications The choice of a fuzzy implication function involves a of fuzzy set theory, especially in the realm of industrial processes, which number of criteria, which are discussed in [31, [241, [2l, do not lend themselves to control by conventional methods because of a lack of quantitative data regarding the input-output relations. Fuzzy [711, [181, [521, [191, [116], [SI, [72], and [96]. In particular, control is based on fuzzy logic-a logical system that is much closer in Baldwin and Pilsworth [3] considered the following basic spirit to human thinking and natural language than traditional logical characteristics of a fuzzy implication function: fundamen- systems. The fuzzy logic controller (FLC) based on fuzzy logic provides a tal property, smoothness property, unrestricted inference, means of converting a linguistic control strategy based on expert knowl- symmetry of generalized modus ponens and generalized edge into an automatic control strategy. A survey of the FLC is pre- sented; a general methodology for constructing an FLC and assessing its modus tollens, and a measure of propagation of fuzziness. performance is described; and problems that need further research are All of these properties are justified on purely intuitive pointed out. In particular, the exposition includes a discussion of grounds. -
Fuzzy Expert Control Systems: Knowledge Base Validation - Pedro Albertos and Antonio Sala
CONTROL SYSTEMS, ROBOTICS AND AUTOMATION – Vol. XVII - Fuzzy Expert Control Systems: Knowledge Base Validation - Pedro Albertos and Antonio Sala FUZZY EXPERT CONTROL SYSTEMS: KNOWLEDGE BASE VALIDATION Pedro Albertos and Antonio Sala Universidad Politécnica de Valencia, Spain Keywords: Fuzzy systems, Expert systems, Fuzzy logic, Fuzzy control, Expert control, Learning systems, Knowledge-based systems, Knowledge validation, Rulebase validation. Contents 1. Introduction 2. Integrated Control Systems 2.1. The Knowledge Base 3. Fuzzy Expert Control System Methodology 3.1. Fuzzy Control System 3.2.Expert Control System 3.3. Fuzzy Expert Control System 4. Knowledge in Fuzzy Expert Control Systems 5. Main Design Issues 5.1. General and Knowledge Base Structure Issues 5.2. Rule Design and Inference 5.3. User Interface 5.4. The Role of Formal Methods in Expert Fuzzy Control 6. Objectives of Knowledge Validation for Control 7. Inference 7.1. Rules as Equations or Inequalities 7.2. Validation Definitions 7.3. Inference Error 8. Validation of Fuzzy Expert Controllers 8.1. Validation of Rulebases 8.2. Validation of Interpolative Inference Algorithms 8.3.Rule Extraction 8.4. Validation and Rule Extraction in the Zadeh-Mamdani Approach 9. UncertainUNESCO Models – EOLSS 10. Conclusions and Perspectives Glossary Bibliography SAMPLE CHAPTERS Biographical Sketches Summary The integral control of a complex system requires not only well-designed, specific controllers but a common framework to interrelate the local controllers and to coordinate their implicit knowledge. This knowledge is not only expressed by algorithms but also by rules and facts. The use of possibly large rulebases, in expert systems for control, raises a number of questions about the reliability of the system. -
A Comprehensive Study on Fuzzy Inference System and Its Application in the Field of Engineering Sheena a D, M
International Journal of Engineering Trends and Technology (IJETT) – Volume 54 Number 1 December 2017 A Comprehensive Study on Fuzzy Inference System and its Application in the field of Engineering Sheena A D, M. Ramalingam, B. Anuradha *Research Scholar, Anna University Chennai & Assistant Professor, JSRREC, Chennai **Rtd. Director, Institute of Remote Sensing, Anna University Chennai & Principal, JCE Chennai *** Professor & Head, MIET, Chennai Abstract - This paper presents a study report on of fuzzy control systems for the Sendai railway. Fuzzy Control and Fuzzy Inference System (FIS) When railway lines were opened in 1987, fuzzy highlighting the application for Engineering projects. systems were used to control accelerating, braking, Based on the project focus, FIS model is very much and stopping; Takeshi Yamakawa demonstrated an helpful to identify a project performance evaluation. "inverted pendulum" through a set of simple The reasoning processes of a structure of fuzzy rules, dedicated fuzzy logic chips, in experiment in which a the knowledge base of the system is excellent. By vehicle tries to keep a pole mounted on its top by a applying this, with reasoning it is practical to have a hinge. Yamakawa made the demonstration by quantitative assessment of the progress of projects mounting a wine glass containing water and even a and challenges by visualization. In addition, it is live mouse to the top of the pendulum while the possible to identify the positives and negatives of the system maintained stability in both cases. Likewise, planning and execution process for making decisions Japanese engineers developed a fuzzy systems for where improvement is required. Fuzzy concepts are industrial and consumer applications. -
Iterative Learning Fuzzy Inference System
Iterative Learning Fuzzy Inference System S. Ashraf*, E. Muhammad**, F. Rashid and M. Shahzad, * NUST, Rawalpndi, Pakistan, ** NUST, Rawalpindi, Pakistan, *** PAEC, Pakistan, **** NUST, Pakistan Abstract—This paper presents a learning fuzzy controller were published in another seminal paper [5]. Since then which can adapt with changing performance requirements. fuzzy controllers have found many successful industrial During the past decade we have witnessed a rapid growth in applications, have shown significant improvements in the number and variety of applications of fuzzy logic system performance and have proved to be more robust ranging from consumer electronics and industrial process than conventional controllers [6,7,8]. control to decision support system and financial systems. The challenging tasks associated with fuzzy control The fuzzy controller designer faces the challenge of choosing design has always been, to choose appropriate the appropriate membership functions, minimum rule base membership functions, minimum rule base and the most and the most suitable fuzzifier and defuzzifier. Having made suitable fuzzifier and defuzzifiers. Having made these these choices, the fuzzy controller has to be tuned to deliver choices, the fuzzy controller has to be tuned to deliver the the desired response. Multiple simultaneous adjustments desired response. Multiple simultaneous adjustments (rules, membership functions and gains) make the optimum (rules, membership functions and gains) make the tuning even more difficult. It is now realized that complex optimum tuning even more difficult. Many techniques real world problems require intelligent systems that combine knowledge, techniques and methodologies from have been used to overcome this difficulty including various sources. These intelligent systems are supposed to neural networks [9,10], a phase plane technique for FPI possess humanlike expertise within a specific domain, adapt rule base design [11], and gain phase margin analysis themselves and learn to do better in changing environment. -
Expert System, Fuzzy Logic, and Neural Network Applications in Power Electronics and Motion Control
Expert System, Fuzzy Logic, and Neural Network Applications in Power Electronics and Motion Control BIMAL K. BOSE, FELLOW, IEEE Invited Paper Artificial intelligence (AI) tools, such as expert system, fuzzy are difficult to solve in traditional way? In early age, it logic, and neural network are expected to usher a new era in power was perceived that human brain takes decision on the basis electronics and motion control in the coming decades. Although of “yes-no” or “true-false” reasoning. In 1854, George these technologies have advanced significantly in recent years and have found wide applications, they have hardly touched the power Boole first published his article “Investigations on the electronics and mackine drives area. The paper describes these laws of thought,” and Boolean algebra and set theory Ai tools and their application in the area of power electronics were born as a result. Gradually, the advent of electronic and motion control. The body of the paper is subdivided into logic and solid state IC’s ushered the modem era of Von three sections which describe, respectively, the principles and Neumann type digital computation. Digital computers were applications of expert system, fuzzy logic, and neural network. The theoretical portion of each topic is of direct relevance to defined as “intelligent” machines because of their capability the application of power electronics. The example applications to process human thought-like yes (Itno (0) logic. Of in the paper are taken from the published literature. Hopefully, course, using the same binary logic, computers can solve the readers will be able to formulate new applications from these complex scientific, engineering, and other data processing examples. -
Part IV Nonadaptive Fuzzy Control
Part IV Nonadaptive Fuzzy Control When fuzzy systems are used as controllers, they are called fuzzy controllers. If fuzzy systems are used to model the process and controllers are designed based on the model, then the resulting controllers also are called fuzzy controllers. Therefore, fuzzy controllers are nonlinear controllers with a special structure. Fuzzy control has represented the most successful applications of fuzzy theory to practical problems. Fuzzy control can be classified into nonadaptive fuzzy control and adaptive fuzzy control. In nonadaptive fuzzy control, the structure and parameters of the fuzzy controller are fixed and do not change during real-time operation. In adaptive fuzzy control, the structure orland parameters of the fuzzy controller change during real- time operation. Nonadaptive fuzzy control is simpler than adaptive fuzzy control, but requires more knowledge of the process model or heuristic rules. Adaptive fuzzy control, on the other hand, is more expensive to implement, but requires less information and may perform better. In this part (Chapters 16-22), we will study nonadaptive fuzzy control. In Chapter 16, we will exam the trial-and-error approach to fuzzy controller design through two case studies: fuzzy control of a cement kiln and fuzzy control of a wastewater treatment process. In Chapters 17 and 18, stable and optimal fuzzy controllers for linear plants will be designed, respectively. In Chapters 19 and 20, fuzzy controllers for nonlinear plants will be developed in such a way that stability is guaranteed by using the ideas of sliding control and supervisory control. A fuzzy gain scheduling for PID controllers also will be studied in Chapter 20. -
Neuro‐Fuzzy Control System for a Non‐Deterministic Object in Real Time
Neuro‐fuzzy Control System for a Non‐deterministic Object in Real Time Sergey Ivanova, Nataliia Maksyshkoa and Mykola Ivanova a Zaporizhzhia National University, Zhukovsky str., 66, Zaporizhzhia, 69063, Ukraine Abstract In this paper discusses the use of neuro-fuzzy control systems as a tool for managing non- deterministic objects in real time. This paper discusses modern control tools structural models of a discrete quasi-invariant automated control system. In this paper the analysis of an automated control system is presented, which is based on the use of typical models of discrete automated control systems. According to the proposed solution in the automated control system in real time it is proposed to use a neuro-fuzzy control system as a function of the object and the system's transfer ratio. The neuro-fuzzy control system is based on the learning process of an artificial neural network (ANN), which allows to define the rules of fuzzy inference (FIS). The paper proposes the ANFIS model, which is implemented by using the fuzzy system Takagi T., Sugeno M., also is considered an algorithm based on seven fuzzy rules. In this paper is presented a technique for implementing a neuro-fuzzy control system for non-deterministic objects by using Matlab. The use of Matlab made possible to create a model of an adaptive neuro-fuzzy inference system. The paper describes the process of training a neural network, where a hybrid method is chosen, which is a combination of the least squares method and the method of decreasing the inverse gradient. The results of testing a neuro-fuzzy control system of a non-deterministic object are presented, which confirmed the possibility of using a neuro-fuzzy control model. -
Flobida Po Veii Affiliatf
FLOBIDA PO_VEII AFFILIATF._ _.;>.,";."_ 7/" J_ x / PV Array Driven Adjustable Speed Drive For A Lunar Base Heat Pump December 31, 1995 Final Report (Phase I) Prepared by Alexander Domijan, Jr. Tariq Aslam Buehh Associate Professor and Director Graduate Research Associate Florida Power AlTdiates and Power Eleetl'onic, Consortium Department of Electrical and Computer Engineering University of Florida 332 Benton Hall, P.O. Box 116200 GainesvilIe, Florida 32611 Tel (352) 392=0290, Fax (352) 392 8671 Prepared for National Aeronautics and Space Administration (NASA) submitted to Mr. Michael Ewert Mail Code EC-7,B7, Room 127 NASA - Johnson Space Center 2101 NASA Road 1 Houston, TX 77058 Tel # (713) 483-9134; Fax# (713) 483-9167 Florida's Center tor Electric Power Engineering TABLE OF CONTENTS AB STAR CT , AC MOTOR DRIVES Introduction 1.1. Induction Motor Drive. 1.2. Permanent Magnet Brushless dc Motor Drive. 1.3. Switched Reluctance Motor Drive. e SUITABILITY FOR AEROSPACE APPLICATION Introduction 2.1. Case I. Heat Pump Powered by the System Power. 2.2. Case II. Heat Pump Powered by an Independent PV Array. 2.3. Case UF- I. Heat Pump Powered from an Independent PV Array with enhanced reliability. "_' 2°4. Requirements of the Aerospace Application. 2.5. Comparison of the three ac Drive Systems. 1 INDUCTION MOTOR DRIVE FED FROM A PV ENERGY SOURCE - Application and Performance. 4. CONTROL OF INDUCTION MACHINES. 4.1. Unear Feedback Methods. 4.2. Nonlinear Control Technique. 4.3. Vector Control Technique. 4.4. Fuzzy Logic Control. 4.5. Fuzzy Logic Control for AC Motor Drives.