Fabrication of Microwave Devices Based on Magnetic Nanowires Using a Laser-Assisted Process
Total Page:16
File Type:pdf, Size:1020Kb
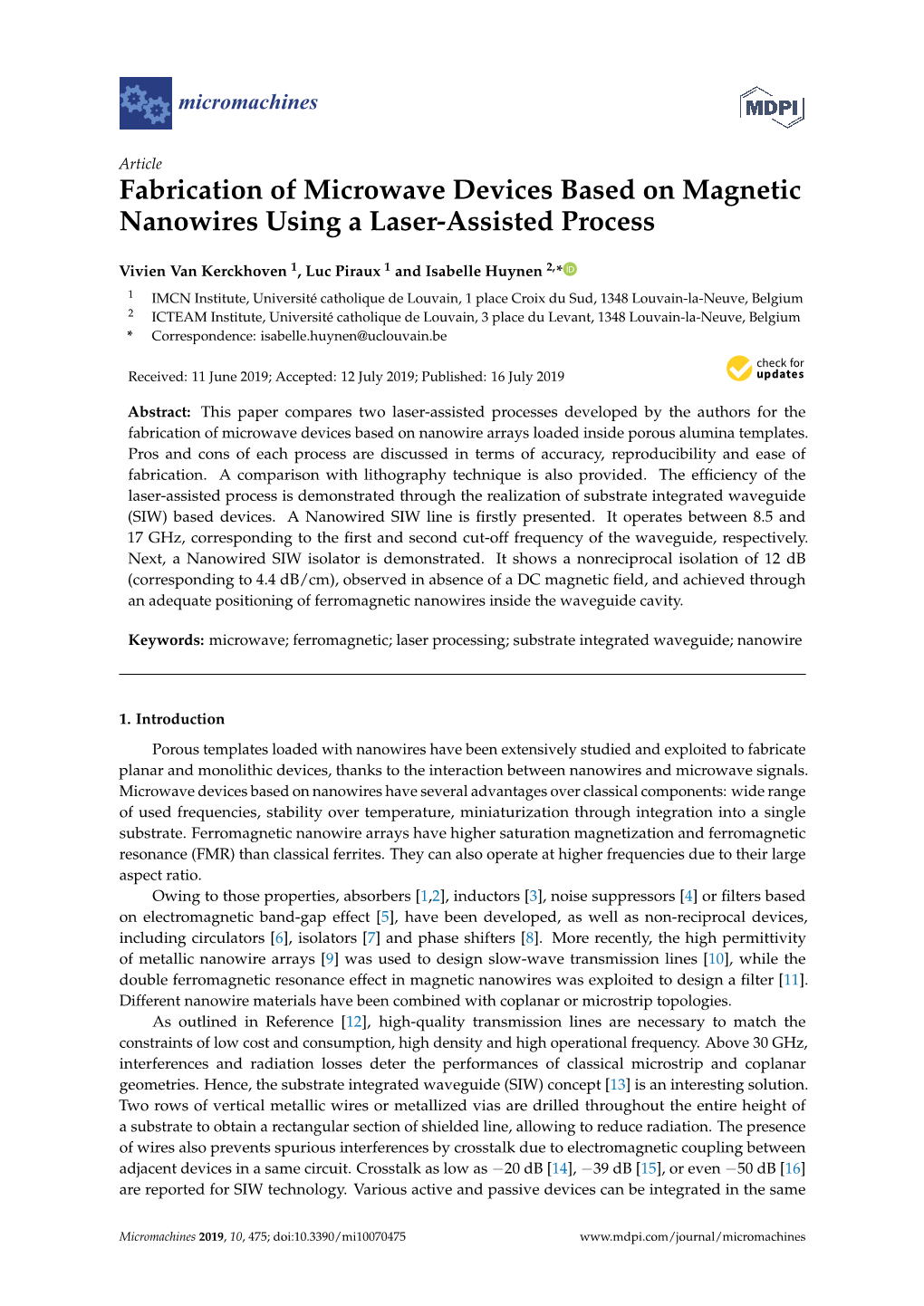
Load more
Recommended publications
-
Quality Factor of a Transmission Line Coupled Coplanar Waveguide Resonator Ilya Besedin1,2* and Alexey P Menushenkov2
Besedin and Menushenkov EPJ Quantum Technology (2018)5:2 https://doi.org/10.1140/epjqt/s40507-018-0066-3 R E S E A R C H Open Access Quality factor of a transmission line coupled coplanar waveguide resonator Ilya Besedin1,2* and Alexey P Menushenkov2 *Correspondence: [email protected] Abstract 1National University for Science and Technology (MISiS), Moscow, Russia We investigate analytically the coupling of a coplanar waveguide resonator to a 2National Research Nuclear coplanar waveguide feedline. Using a conformal mapping technique we obtain an University MEPhI (Moscow expression for the characteristic mode impedances and coupling coefficients of an Engineering Physics Institute), Moscow, Russia asymmetric multi-conductor transmission line. Leading order terms for the external quality factor and frequency shift are calculated. The obtained analytical results are relevant for designing circuit-QED quantum systems and frequency division multiplexing of superconducting bolometers, detectors and similar microwave-range multi-pixel devices. Keywords: coplanar waveguide; microwave resonator; conformal mapping; coupled transmission lines; superconducting resonator 1 Introduction Low loss rates provided by superconducting coplanar waveguides (CPW) and CPW res- onators are relevant for microwave applications which require quantum-scale noise levels and high sensitivity, such as mutual kinetic inductance detectors [1], parametric amplifiers [2], and qubit devices based on Josephson junctions [3], electron spins in quantum dots [4], and NV-centers [5]. Transmission line (TL) coupling allows for implementing rela- tively weak resonator-feedline coupling strengths without significant off-resonant pertur- bations to the propagating modes in the feedline CPW. Owing to this property and ben- efiting from their simplicity, notch-port couplers are extensively used in frequency mul- tiplexing schemes [6], where a large number of CPW resonators of different frequencies are coupled to a single feedline. -
Superconducting Coplanar Waveguide Resonators for Quantum Computing
Master’s degree: Advanced nanoscience and nanotechnology Autonomous University of Microelectronics Institute of High Energy physics institute Barcelona (UAB) Barcelona (IMB-CNM) (IFAE) SUPERCONDUCTING COPLANAR WAVEGUIDE RESONATORS FOR QUANTUM COMPUTING FINAL MASTER PROJECT Author: Alberto Lajara Corral Supervisor: Gemma Rius Co-Supervisor: Pol Forn-Diaz Contents Acronyms i 1 Introduction 1 1.1 Presentation of topic . 1 1.2 Methodologies . 3 1.3 Project structure . 3 2 Transmission line theory for microwave resonators 4 2.1 Microwave theory for transmission lines . 4 2.2 Resonator model . 5 2.2.1 Parallel resonant circuit . 5 2.2.2 Transmission line resonators: Open-Circuited ¸/2 line . 6 2.2.3 Quality factors of the resonator . 7 3 Design of coplanar waveguide resonators 8 3.1 Materials and geometry choice . 8 3.1.1 Substrate . 8 3.1.2 Metal layer . 8 3.1.3 Coplanar waveguide geometry . 9 3.1.4 Capacitor geometry . 10 3.2 Equivalent circuit . 11 3.3 Simulation results . 13 3.3.1 First design . 14 3.3.2 Optimized design . 15 4 Fabrication of the CPW resonator 19 4.1 Introduction to fabrication . 19 4.2 Basicprocedure................................... 20 4.3 GLADE design . 21 4.4 Exposure strategy . 22 4.5 Fabrication results . 24 4.5.1 Before pattern transfer . 24 4.5.2 After pattern transfer . 26 5 Conclusion 29 A Extension of Transmission line theory i A.1 Lumped-element circuit model for a TL . i A.2 Propagation on a Transmission Line . ii A.3 Lossless transmission line . ii A.4 The terminated transmission line . -
Designs of Substrate Integrated Waveguide (SIW) and Its Transition to Rectangular Waveguide
Designs of Substrate Integrated Waveguide (SIW) and Its Transition to Rectangular Waveguide by Ya Guo A thesis submitted to the Graduate Faculty of Auburn University in partial fulfillment of the requirements for the Degree of Master of Science Auburn, Alabama May 10, 2015 Keywords: Substrate Integrated Waveguide (SIW), Rectangular Waveguide (RWG), Waveguide transition, high frequency simulation software (HFSS), genetic algorithm (GA) Copyright 2015 by Ya Guo Approved by Michael C. Hamilton, Chair, Assistant Professor of Electrical & Computer Engineering Bogdan M. Wilamowski, Professor of Electrical & Computer Engineering Michael E. Baginski, Associate Professor of Electrical & Computer Engineering Abstract There has been an ever increasing interest in the study of substrate integrated waveguide (SIW) since 1998. Due to its low loss, planar nature, high integration capability and high compactness, SIW has been widely used to develop the components and circuits operating in the microwave and millimeter-wave region. For the integrated design of SIW and other transmission lines, the design of feasible and effective transitions between them is the key. In this work, substrate integrated waveguides for E-band, V-band and Q-band are designed and accurately modeled, their high frequency performances are simulated and analyzed with the Ansys’ High Frequency Structure Simulator (HFSS). Additionally, two kinds of transitions between RWG and SIW are explored for narrow band 76-77 GHz and broad bands 77-81 GHz, 56-68 GHz and 40-50 GHz, and they are simulated in HFSS. The loss of the transition portion is extracted by linear fitting method. Genetic algorithm is also used to find the optimal dimensions and placements of the transitions for broad operative bands. -
Design of CPW Antenna for Future Wireless Application
ISSN (Online) 2278-1021 IJARCCE ISSN (Print) 2319-5940 International Journal of Advanced Research in Computer and Communication Engineering Vol. 8, Issue 5, May 2019 Design of CPW Antenna for Future Wireless Application S.Monisha1, U.Surendar2 PG Scholar, Department of ECE, K.Ramakrishnan College of Engineering, Trichy, India1 Assistant Professor, Department of ECE, K.Ramakrishnan College of Engineering, Trichy, India2 Abstract: A hexagonal shaped Co-Planar Waveguide (CPW) fed antenna is proposed with Electric Field Coupled Resonator (ELC) structure for LTE application. The antenna consists of hexagonal slot in the patch with meta-material structure at the centre. Using ELC structure, the impedance matching is occurred efficiently. The frequency band covered by this proposed antenna is 2.6GHz with the return loss of -23dB. The total size of the antenna is . The dielectric constant used for this antenna is FR4 substrate. The optimal VSWR and Radiation pattern characteristics are obtained for this frequency band. The proposed antenna is designed and simulated using High Frequency Structure Simulator (HFSS). Keywords: Coplanar Waveguide, Electric Field Coupled Resonator, Impedance Matching, Meta-Material, VSWR I. INTRODUCTION In recent days, Wireless communication plays a major role in communication systems. The total populations were connected with global audience through wireless communication. The lack of physical infrastructure makes the wireless communication desirable for wide applications. In wireless communication the great role has been made by antenna [15]. Nowadays the antenna with broad bandwidth and smaller size were the difficult challenges in the wireless area. And also wearable antenna is also used for biosignal monitoring [11] (bio-signal communication). -
Arxiv:1702.01149V2 [Cond-Mat.Supr-Con] 21 Sep 2017
Gyrator Operation Using Josephson Mixers Baleegh Abdo, Markus Brink, and Jerry M. Chow IBM T. J. Watson Research Center, Yorktown Heights, New York 10598, USA. (Dated: October 15, 2018) Nonreciprocal microwave devices, such as circulators, are useful in routing quantum signals in quantum networks and protecting quantum systems against noise coming from the detection chain. However, commercial, cryogenic circulators, now in use, are unsuitable for scalable superconducting quantum architectures due to their appreciable size, loss, and inherent magnetic field. We report on the measurement of a key nonreciprocal element, i.e., the gyrator, which can be used to realize a circulator. Unlike state-of-the-art gyrators, which use a magneto-optic effect to induce a phase shift of π between transmitted signals in opposite directions, our device uses the phase nonreciprocity of a Josephson-based three-wave-mixing device. By coupling two of these mixers and operating them in noiseless frequency-conversion mode, we show that the device acts as a nonreciprocal phase shifter whose phase shift is controlled by the phase difference of the microwave tones driving the mixers. Such a device could be used to realize a lossless, on-chip, superconducting circulator suitable for quantum-information-processing applications. I. INTRODUCTION (a) Port 1 휋 Port 2 Performing high-fidelity, quantum nondemolition mea- surements in the microwave domain is an important 1 2 requirement for operating a superconducting quantum (b) 90° 90° 90° 90° computer. Such a requirement is enabled, in various 휋 3 4 schemes, by using nonreciprocal microwave devices hav- 90° hybrid 90° hybrid ing asymmetrical transmission through their ports, such as circulators [1{9] and low-noise, directional amplifiers 2 [4, 10{14]. -
Substrate-Integrated Waveguide Transitions to Planar Transmission-Line Technologies
Substrate-Integrated Waveguide Transitions To Planar Transmission-Line Technologies Farzaneh Taringou1, David Dousset2, Jens Bornemann1 and Ke Wu2 1Department of Electrical and Computer Engineering, University of Victoria, Victoria, BC, Canada V8W 3P6 2Poly–Grames Research Center, Département de Génie Electrique, École Polytechnique de Montréal, Montréal, QC, Canada H3T 1J4 [email protected] Abstract — For the purpose of integrating active, nonlinear substrate and that wideband interfaces with more than 40 and surface-mount components in substrate-integrated percent bandwidth can be realized. waveguide (SIW) technology, this paper presents a variety of new and modified transitions from SIW to other planar transmission lines. Typical performances are shown involving connections to II. RESULTS AND DISCUSSION microstrip, coplanar waveguide (both conductor-backed and regular), coplanar strip line and slot line technologies. Both Typical to all transitions involving SIWs is the requirement modified and new transition examples in the 18 – 27 GHz range that the TE10-mode-like field in the SIW be adapted to the demonstrate the feasibility of such interfaces for bandwidths in fundamental mode of the transmission line it is interfaced the order of 40 percent. Measurements and full-wave simulations validate the proposed designs. with. Due to the similarity between the fundamental Index Terms — Substrate-integrated waveguide, microstrip, waveguide and microstrip modes, the SIW-to-microstrip coplanar waveguide, coplanar strip line, slot line, interfaces, transition was the first one proposed [5], and design guidelines transitions. are well understood [6]. Fig. 1 shows a photograph and performance of a back-to- back microstrip-to-SIW transition on RT/Duroid 5880 I. INTRODUCTION ε δ substrate with r=2.2, tan =0.0009, substrate height Substrate-Integrated Waveguide (SIW) components have h=0.508mm, metallization thickness t=17.5μm, and emerged as a viable alternative to all-metal waveguide and conductivity σ=5.8x107S/m. -
Analytical Determination of Participation in Superconducting Coplanar Architectures Conal E
1 Analytical determination of participation in superconducting coplanar architectures Conal E. Murray, Jay M. Gambetta, Douglas T. McClure and Matthias Steffen Abstract—Superconducting qubits are sensitive to a variety values obtained with this approach can be highly dependent of loss mechanisms which include dielectric loss from interfaces. on the discretization scheme used to tessellate the various The calculation of participation near the key interfaces of planar structures due to the singular behavior of the electric fields designs can be accomplished through an analytical description of the electric field density based on conformal mapping. In this near the corners and edges of conductors. Hybrid schemes way, a two-dimensional approximation to coplanar waveguide that can involve power law approximations have also been and capacitor designs produces values of the participation as proposed [1], [3] to account for divergences in the electric a function of depth from the top metallization layer as well field distributions. as the volume participation within a given thickness from this A more robust method to calculate surface participation surface by reducing the problem to a surface integration over the region of interest. These quantities are compared to finite element can be implemented based on a two-dimensional, analytical method numerical solutions, which validate the values at large formulation of the electric field distributions generated by distances from the coplanar metallization but diverge near the metallization features on dielectric substrates [6], [7]. This edges of the metallization features due to the singular nature of approach, which assumes that the metallization is composed the electric fields. A simple approximation to the electric field of two sheets and is perfectly conducting, incorporates the energy at shallow depths (relative to the waveguide width) is also −0:5 presented that closely replicates the numerical results based on singular nature of the electric fields [8] which scale as r conformal mapping and those reported in prior literature. -
Microwave Circuit Analysis of Multi Transmon Qubit System
MICROWAVE CIRCUIT ANALYSIS OF MULTI TRANSMON QUBIT SYSTEM MSC ELECTRICAL ENGINEERING THESIS MICROWAVE CIRCUIT ANALYSIS OF MULTI TRANSMON QUBIT SYSTEM MSC ELECTRICAL ENGINEERING THESIS Jonathan GNANADHAS MSc in Electrical Engineering, Signals and Systems Thesis Supervisors: prof. dr. A. Yarovoy Delft University of Technology dr. ir. S.N. Nadia QuTech, TNO Thesis Committe: prof. dr. A. Yarovoy Delft University of Technology prof. dr. L. Dicarlo Delft University of Technology prof. dr. B.J. Kooij Delft University of Technology CONTENTS 1 Introduction1 1.1 Background of Research..........................1 1.2 Research Problem..............................2 1.3 Research Approach.............................2 2 Components and Circuit Quantum Electrodynamics of a Transmon Qubit5 2.1 Josephson’s Junction............................5 2.2 SQUID...................................7 2.3 Superconducting Qubits..........................8 2.4 LC Quantum Device............................8 2.5 Transmon Qubit.............................. 10 3 Classical Electrodynamics Analysis of a Transmon Qubit 15 3.1 Surface Impedance............................. 16 3.2 Fields, Inductance and Capacitance of CPW structure........... 17 3.2.1 Geometrical Inductance and Capacitance.............. 17 3.2.2 Kinetic Inductance.......................... 19 3.3 Half Wavelength Resonators........................ 21 3.4 Stability of Superconductivity Surface Impedance model.......... 22 3.5 Impact of Resistive Component of Surface Impedance........... 27 3.5.1 Characteristic Line Impedance.................... 27 3.5.2 Propagation Constant........................ 28 3.5.3 Impedance of a Transmission Line Resonator............ 28 3.5.4 Resonant Frequency of a Transmission Line Resonator....... 28 3.5.5 Impact on Quality Factor of a Transmission Line Resonator..... 29 3.5.6 Physical Implication of the Added Surface Resistance........ 29 4 Equivalent Circuit Model of a Qubit and Estimation of Parameters 31 4.1 Qubit Unit Cell.............................. -
A Conductor Backed, Coplanar Waveguide Fed, Linear Array
A CONDUCTOR BACKED, COPLANAR WAVEGUIDE FED, LINEAR ARRAY COMPRISED OF BOWTIE ANTENNAS FOR A VARACTOR TUNED RADIATION PATTERN Thesis Submitted to The School of Engineering of the UNIVERSITY OF DAYTON In Partial Fulfillment of the Requirements for The Degree of Master of Science in Electrical Engineering By Satya Parthiva Sri Sumanam Dayton, Ohio August, 2016 A CONDUCTOR BACKED, COPLANAR WAVEGUIDE FED, LINEAR ARRAY COMPRISED OF BOWTIE ANTENNAS FOR A VARACTOR TUNED RADIATION PATTERN Name: Sumanam, Satya Parthiva Sri APPROVED BY: __________________________________ ______________________________ Robert P. Penno, Ph.D. Guru Subramanyam, Ph.D. Advisory Committee Chairman Committee Member Professor Professor/Chair Electrical and Computer Engineering Electrical and Computer Engineering ________________________________ Monish Chatterjee, Ph.D. Committee Member Professor Electrical and Computer Engineering _________________________________ _____________________________ Robert J. Wilkens, Ph.D., P.E. Eddy M. Rojas, Ph.D., M.A., P.E. Associate Dean for Research and Innovation Dean, School of Engineering Professor School of Engineering ii © Copyright by Satya Parthiva Sri Sumanam All Rights Reserved 2016 iii ABSTRACT A CONDUCTOR BACKED, COPLANAR WAVEGUIDE FED, LINEAR ARRAY COMPRISED OF BOWTIE ANTENNAS FOR A VARACTOR TUNED RADIATION PATTERN Name: Sumanam, Satya Parthiva Sri University of Dayton Advisor: Dr. Robert Penno The main objective of this research is to develop an antenna array that can tune its radiation pattern over a fixed frequency of operation. For this purpose, a novel printed antenna array for beam peak shifting applications is presented. This antenna array consists of two bowtie slots separated over a distance of half wavelength. A conductor backed coplanar waveguide (CBCPW) is designed with signal line of one wavelength connected to the bowtie antenna linear array. -
Chapter 3 Conductor Loss Calculation of Coplanar Waveguide
22 Chapter 3 Conductor Loss Calculation of Coplanar Waveguide 3.1 : Introduction Characterization of coplanar waveguides (CPW) on a lossless substrate is important in understanding base line CPW behavior, especially the conductor losses in both the low and high frequency regimes. Conductor loss evaluation still remains one of the more difficult problems in transmission line analysis. To calculate the conductor loss in a CPW configuration, a new quasi-static approach is shown in this chapter that uses a conformal mapping technique. This novel technique uses no fitting parameter to match the experimental results: only the dimensions, metal conductivity, and the substrate dielectric constant are required to accurately predict the complex propagation constant. This method takes into consideration both the skin effect and current crowding in the conductors. It is also numerically efficient when compared with some fullwave calculations [Heinrich 1990] to measure the conductor loss. Later in this chapter, this technique is compared with other existing quasi-static approaches to show the clear superiority of this method. One of the advantages of this technique is that the methodology can easily be applied to other transmission line structures, such as co-axial cables, twin-lead, parallel square bars, microstrip lines, or co-planar strip lines to calculate conductor losses [Tuncer et al. 1994]. Traditional approaches such as incremental inductance rules [Ramo et al. 1984] or conventional conformal mapping techniques [Collin 1992] fail to adequately model the transition from low frequency to high frequency behavior, especially for small dimension (micron size) interconnects. When modeling the propagation of broad bandwidth time-domain pulses, such as in digital systems, the dispersion induced by this transition can be very significant. -
Planar Transmission Lines
Adapted from notes by ECE 5317-6351 Prof. Jeffery T. Williams Microwave Engineering Fall 2018 Prof. David R. Jackson Dept. of ECE Notes 11 Waveguiding Structures Part 6: Planar Transmission Lines w ε0 ε r h 1 Planar Transmission Lines w w b ε h r εr Microstrip Stripline w w εr g g h εr g g h Coplanar Waveguide (CPW) Conductor-backed CPW s s εr h εr h Slotline Conductor-backed Slotline 2 Planar Transmission Lines (cont.) w w w w ε h εr s h r s Coplanar Strips (CPS) Conductor-backed CPS . Stripline is a planar version of coax. Coplanar strips (CPS) is a planar version of twin lead. 3 Stripline . Common on circuit boards ε,, µσd b . Fabricated with two circuit boards w . Homogenous dielectric (perfect TEM mode) TEM mode (also TE & TM Modes) Field structure for TEM mode: Electric Field Magnetic Field 4 Stripline (cont.) . Analysis of stripline is not simple. TEM mode fields can be obtained from an electrostatic analysis (e.g., conformal mapping). A closed stripline structure is analyzed in the Pozar book by using an approximate numerical method: b w b /2 ε,, µσd a ab>> 5 Stripline (cont.) Conformal mapping solution (S. Cohn): Exact solution: 30π Kk ( ) Z0 = K = complete elliptic Kk()′ integral of the first kind π /2 1 Kk( ) ≡ dθ ∫ 22 0 1− k sin θ π w k = sech 2b π w k′ = tanh 2b 6 Stripline (cont.) Curve fitting this exact solution: η b Z = 0 ln( 4) 0 ε ln(4) Note : = 0.441 4 r wb+ π e π Effective width Fringing term w 0 ;for ≥ 0.35 wwe b = − 2 bbww 0.35− ;for 0.1≤≤ 0.35 bb 1bb /2 η η b ideal 0 The factor of 1/2 in front is from the parallel Note: Z0 =η = = 24ww4w ε r combination of two ideal PPWs. -
Transmission Lines and Waveguides.Doc 1/3
2/20/2009 3 Transmission Lines and Waveguides.doc 1/3 Chapter 3 – Transmission Lines and Waveguides First, some definitions: Transmission Line – A two conductor structure that can support a TEM wave. Waveguide – A one conductor structure that cannot support a TEM wave. Q: What is a TEM wave? A: An electromagnetic wave wherein both the electric and magnetic fields are perpendicular to the direction of wave propagation. HO: WAVEGUIDE 3.5 Coaxial Line Reading Assignment: p. 130 The most prevalent type of transmission line is the coaxial transmission line. HO: COAXIAL TRANSMISSION LINES Jim Stiles The Univ. of Kansas Dept. of EECS 2/20/2009 3 Transmission Lines and Waveguides.doc 2/3 Coaxial transmission lines are attached to devices using microwave connectors. HO: COAXIAL CONNECTORS 3.7 Stripline Reading Assignment: pp. 137-140 Often, microwave devices or networks are built on dielectric substrates (e.g., “printed circuit boards”). Connecting these devices require printed circuit board transmission lines. HO: PRINTED CIRCUIT BOARD TRANSMISSION LINES One of the most popular PCB transmission lines is stripline. HO: STRIPLINE 3.8 Microstrip Reading Assignment: pp. 143-146 Another popular PCB transmission line is microstrip. HO: MICROSTRIP Jim Stiles The Univ. of Kansas Dept. of EECS 2/20/2009 3 Transmission Lines and Waveguides.doc 3/3 3.11 Summary of Transmission Lines and Waveguides Reading Assignment: pp. 154-157 Let’s compare transmission line characteristics! HO: A COMPARISON OF COMMON TRANSMISSION LINES AND WAVEGUIDES Jim Stiles The Univ. of Kansas Dept. of EECS 2/19/2007 Waveguide 1/2 Waveguide A waveguide is not considered to strictly be a transmission line, as it is not constructed with two separate conductors.