Sleeve Valve Engines.Pdf
Total Page:16
File Type:pdf, Size:1020Kb
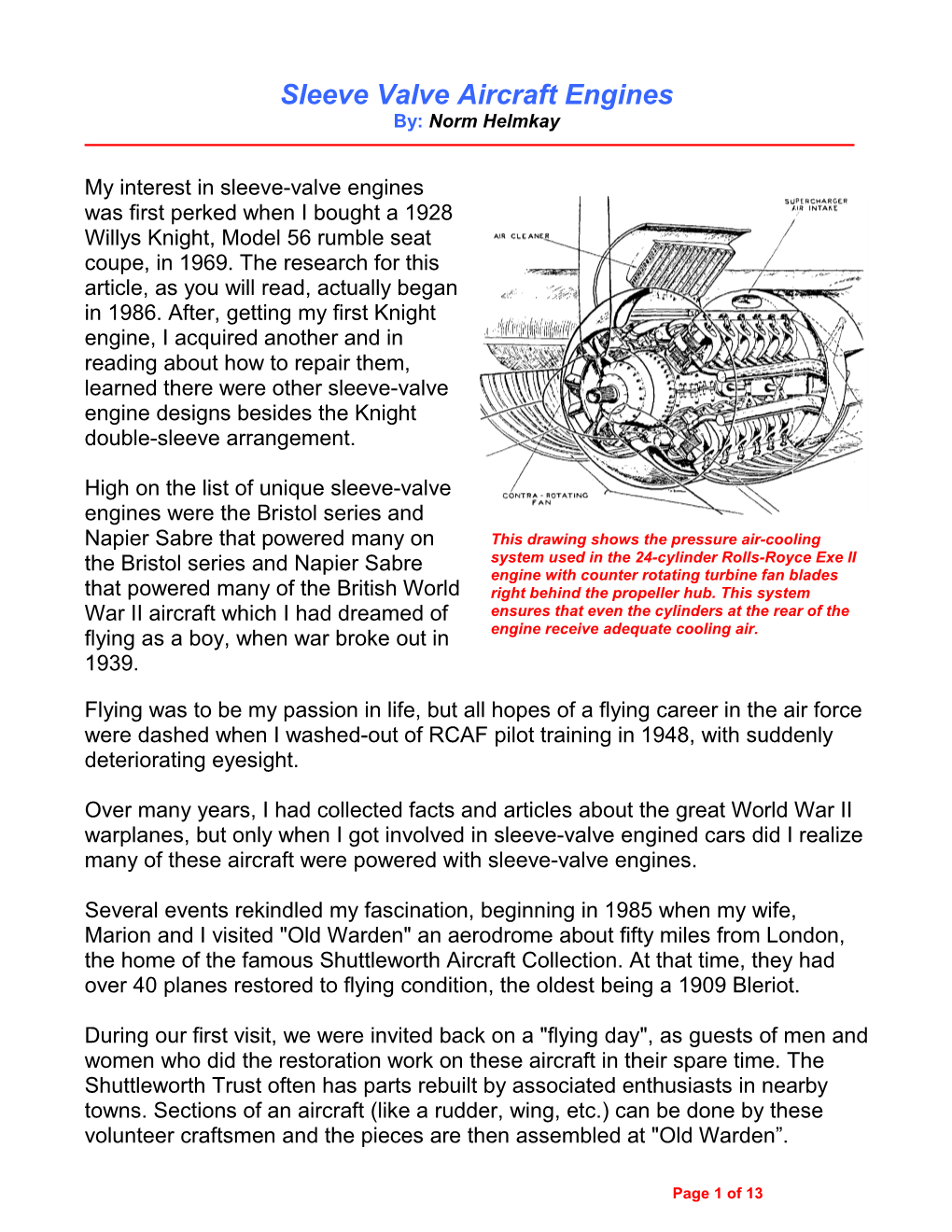
Load more
Recommended publications
-
Locomotive Dedication Ceremony
The American Society of Mechanical Engineers REGIONAL MECHANICAL ENGINEERING HERITAGE COLLECTION LOCOMOTIVE DEDICATION CEREMONY Kenefick Park • Omaha, Nebraska June 7, 1994 Locomotives 4023 and 6900 are examples of the world’s largest motive power in the steam and diesel eras. These locomotives are on permanent display at Kenefick Park, which was established in 1989 in honor of noted former Union Pacific chairman, John C. Kenefick. The 4023 was one of twenty-five famous “Big Boy” type simple articulated locomotives Locomotive 4023 was a feature display lauded in the industry and press as the highest horsepower, heaviest and longest steam at the Omaha Shops locomotives ever built, developing seven thousand horsepower at their seventy miles until being moved to per hour design speed. Kenefick Park. 2 World’s largest The Big Boy type was designed at the Omaha headquarters of Union Pacific under the single unit diesel personal direction of the road’s noted mechanical head, Otto Jabelmann. The original locomotives required four axle trucks to distribute twenty locomotives of this type were built by American Locomotive Company in their heavy weight and Schenectady, New York, in the fall of 1941. They were built in preparation for the nation’s keep within track probable entry into World War II because no proven diesel freight locomotive was yet loading limits. in production. These 4-8-8-4 type locomotives were specifically designed to haul fast, heavy eastbound freight trains between Ogden, Utah, and Green River, Wyoming, over the 1.14 percent eastbound grade. The 4023 was one of five additional units built in 1944 under govern- ment authority in preparation for a twenty-five percent increase in traffic due to the shift from European to Pacific war operations. -
How Did You Sleep Last Night?????
Official Bulletin of the VALIANT AIR COMMAND, INC. (a 501(c)(3) Non-profit Organization Space Coast Regional Airport, Titusville, FL 32780-8009 Volume 25, Issue 5 May 2003 HOW DID YOU SLEEP LAST NIGHT????? Bed a little lumpy? Toss and turn any? Wish the heat was higher? Maybe the A/C wasn't on.....Had to go to the john? Need a drink of water???????? THINK OF THEM PROTECTING YOUR FREEDOM!!! 1 CALENDAR OF EVENTS 6600 Tico Road, Titusville, FL 32780-8009 BOARD OF D IRECTORS MEETINGS Tel (321) 268-1941 FAX (321) 268-5969 MAY 13, 2003 EXECUTIVE STAFF 12:00 NOON VAC MUSEUM BOARD ROOM COMMANDER Lloyd Morris (386) 423-9304 JUNE 10, 2003 EXECUTIVE OFFICER Harold Larkin 12:00 NOON (321) 453-4072 VAC MUSEUM BOARD ROOM AIRSHOW DEBRIEF/MEMBERSHIP MEETING OPERATIONS OFFICER Mike McCann Email: [email protected] (321) 259-0587 MAY 17, 2003 12:00 NOON MAINTENANCE OFFICER Bob James VAC HANGAR (POTLUCK--PLEASE BRING YOU FAVORITE DISH. (321) 453-6995 VAC WILL PROVIDE ENTREE. CALL 268-1941 TO LET US KNOW YOU WILL ATTEND.) FINANCE OFFICER Pieter Lenie (321) 727-3944 PROCUREMENT - Bob Frazier PERSONNEL OFFICER Alice Iacuzzo (321) 799-4040 Things have been busy this month with meetings and the Easter holidays. However, the T-2C Buckeye arrived by truck on April TRANSP/FACILITY OFFICER Bob Kison 17. It was immediately unloaded by the in-resident crew and (321) 269-6282 attempts to reattach the wings were initiated. The crew will be identified and thanked next month following completion of these PROCUREMENT OFFICER Bob Frazier efforts. -
Aviation Classics Magazine
Avro Vulcan B2 XH558 taxies towards the camera in impressive style with a haze of hot exhaust fumes trailing behind it. Luigino Caliaro Contents 6 Delta delight! 8 Vulcan – the Roman god of fire and destruction! 10 Delta Design 12 Delta Aerodynamics 20 Virtues of the Avro Vulcan 62 Virtues of the Avro Vulcan No.6 Nos.1 and 2 64 RAF Scampton – The Vulcan Years 22 The ‘Baby Vulcans’ 70 Delta over the Ocean 26 The True Delta Ladies 72 Rolling! 32 Fifty years of ’558 74 Inside the Vulcan 40 Virtues of the Avro Vulcan No.3 78 XM594 delivery diary 42 Vulcan display 86 National Cold War Exhibition 49 Virtues of the Avro Vulcan No.4 88 Virtues of the Avro Vulcan No.7 52 Virtues of the Avro Vulcan No.5 90 The Council Skip! 53 Skybolt 94 Vulcan Furnace 54 From wood and fabric to the V-bomber 98 Virtues of the Avro Vulcan No.8 4 aviationclassics.co.uk Left: Avro Vulcan B2 XH558 caught in some atmospheric lighting. Cover: XH558 banked to starboard above the clouds. Both John M Dibbs/Plane Picture Company Editor: Jarrod Cotter [email protected] Publisher: Dan Savage Contributors: Gary R Brown, Rick Coney, Luigino Caliaro, Martyn Chorlton, Juanita Franzi, Howard Heeley, Robert Owen, François Prins, JA ‘Robby’ Robinson, Clive Rowley. Designers: Charlotte Pearson, Justin Blackamore Reprographics: Michael Baumber Production manager: Craig Lamb [email protected] Divisional advertising manager: Tracey Glover-Brown [email protected] Advertising sales executive: Jamie Moulson [email protected] 01507 529465 Magazine sales manager: -
Pertonix Catalog
Quality Products for Over 40 Years 2015 We are excited to present our 2015 catalog with many new applications and updates. The development of a smaller form factor Ignitor III has allowed us to add many new applications in all our served markets. We’ve expanded our “Stock Look” Cast Distributors offering to include many new popular engine families. Get the original look plus improved performance levels without the hassle of points. Don’t forget to check out our new coils for GM LS engines, custom fit Flame-Thrower 8mm wire sets for late model applications and HEI III 4-pin ignition module. Our customers are our biggest asset and we would like to thank you for your continued support of the PerTronix Performance Brands! The Pertronix Performance Brands sponsored Hairston Motorsports and Racing Pro-Mod GTO is the Quickest quarter mile Small Block door car in history running 5.91 seconds and the Fastest Small Block in drag racing history Period 252.38 MPH! TABLE OF CONTENTS ELECTRONIC IGNITION CONVERSIONS IGNitor / IGNitor II / IGNitor III FEATURES ................................................ 2-3 AUtomotiVE IGNitor ELECtroNIC IGNITION ........................................... 4-18 ELECtroNIC IGNITION SERVICE PARTS ....................................................... 18 IGNITION ACCESSORIES .................................................................................. 19 MARINE IGNitor ELECtroNIC IGNITION ..................................................... 20-22 INDUSTRIAL IGNitor ELECtroNIC IGNITION ............................................ -
Military Aircraft Crash Sites in South-West Wales
MILITARY AIRCRAFT CRASH SITES IN SOUTH-WEST WALES Aircraft crashed on Borth beach, shown on RAF aerial photograph 1940 Prepared by Dyfed Archaeological Trust For Cadw DYFED ARCHAEOLOGICAL TRUST RHIF YR ADRODDIAD / REPORT NO. 2012/5 RHIF Y PROSIECT / PROJECT RECORD NO. 105344 DAT 115C Mawrth 2013 March 2013 MILITARY AIRCRAFT CRASH SITES IN SOUTH- WEST WALES Gan / By Felicity Sage, Marion Page & Alice Pyper Paratowyd yr adroddiad yma at ddefnydd y cwsmer yn unig. Ni dderbynnir cyfrifoldeb gan Ymddiriedolaeth Archaeolegol Dyfed Cyf am ei ddefnyddio gan unrhyw berson na phersonau eraill a fydd yn ei ddarllen neu ddibynnu ar y gwybodaeth y mae’n ei gynnwys The report has been prepared for the specific use of the client. Dyfed Archaeological Trust Limited can accept no responsibility for its use by any other person or persons who may read it or rely on the information it contains. Ymddiriedolaeth Archaeolegol Dyfed Cyf Dyfed Archaeological Trust Limited Neuadd y Sir, Stryd Caerfyrddin, Llandeilo, Sir The Shire Hall, Carmarthen Street, Llandeilo, Gaerfyrddin SA19 6AF Carmarthenshire SA19 6AF Ffon: Ymholiadau Cyffredinol 01558 823121 Tel: General Enquiries 01558 823121 Adran Rheoli Treftadaeth 01558 823131 Heritage Management Section 01558 823131 Ffacs: 01558 823133 Fax: 01558 823133 Ebost: [email protected] Email: [email protected] Gwefan: www.archaeolegdyfed.org.uk Website: www.dyfedarchaeology.org.uk Cwmni cyfyngedig (1198990) ynghyd ag elusen gofrestredig (504616) yw’r Ymddiriedolaeth. The Trust is both a Limited Company (No. 1198990) and a Registered Charity (No. 504616) CADEIRYDD CHAIRMAN: Prof. B C Burnham. CYFARWYDDWR DIRECTOR: K MURPHY BA MIFA SUMMARY Discussions amongst the 20th century military structures working group identified a lack of information on military aircraft crash sites in Wales, and various threats had been identified to what is a vulnerable and significant body of evidence which affect all parts of Wales. -
Engineering Info
Engineering Info To Find Given Formula 1. Basic Geometry Circumference of a circle Diameter Circumference = 3.1416 x diameter Diameter of a circle Circumference Diameter = Circumference / 3.1416 2. Motion Ratio High Speed & Low Speed Ratio = RPM High RPM Low RPM Feet per Minute of Belt RPM = FPM and Pulley Diameter .262 x diameter in inches Belt Speed Feet per Minute RPM & Pulley Diameter FPM = .262 x RPM x diameter in inches Ratio Teeth of Pinion & Teeth of Gear Ratio = Teeth of Gear Teeth of Pinion Ratio Two Sprockets or Pulley Diameters Ratio = Diameter Driven Diameter Driver 3. Force - Work - Torque Force (F) Torque & Diameter F = Torque x 2 Diameter Torque (T) Force & Diameter T = ( F x Diameter) / 2 Diameter (Dia.) Torque & Force Diameter = (2 x T) / F Work Force & Distance Work = Force x Distance Chain Pull Torque & Diameter Pull = (T x 2) / Diameter 4. Power Chain Pull Horsepower & Speed (FPM) Pull = (33,000 x HP)/ Speed Horsepower Force & Speed (FPM) HP = (Force x Speed) / 33,000 Horsepower RPM & Torque (#in.) HP = (Torque x RPM) / 63025 Horsepower RPM & Torque (#ft.) HP = (Torque x RPM) / 5250 Torque HP & RPM T #in. = (63025 x HP) / RPM Torque HP & RPM T #ft. = (5250 x HP) / RPM 5. Inertia Accelerating Torque (#ft.) WK2, RMP, Time T = WK2 x RPM 308 x Time Accelerating Time (Sec.) Torque, WK2, RPM t = WK2 x RPM 308 x Torque WK2 at motor WK2 at Load, Ratio WK2 Motor = WK2 Ratio2 6. Gearing Gearset Centers Pd Gear & Pd Pinion Centers = ( PdG + PdP ) / 2 Pitch Diameter No. of Teeth & Diametral Pitch Pd = Teeth / DP Pitch Diameter No. -
Arctic Discovery Seasoned Pilot Shares Tips on Flying the Canadian North
A MAGAZINE FOR THE OWNER/PILOT OF KING AIR AIRCRAFT SEPTEMBER 2019 • VOLUME 13, NUMBER 9 • $6.50 Arctic Discovery Seasoned pilot shares tips on flying the Canadian North A MAGAZINE FOR THE OWNER/PILOT OF KING AIR AIRCRAFT King September 2019 VolumeAir 13 / Number 9 2 12 30 36 EDITOR Kim Blonigen EDITORIAL OFFICE 2779 Aero Park Dr., Contents Traverse City MI 49686 Phone: (316) 652-9495 2 30 E-mail: [email protected] PUBLISHERS Pilot Notes – Wichita’s Greatest Dave Moore Flying in the Gamble – Part Two Village Publications Canadian Arctic by Edward H. Phillips GRAPHIC DESIGN Rachel Wood by Robert S. Grant PRODUCTION MANAGER Mike Revard 36 PUBLICATIONS DIRECTOR Jason Smith 12 Value Added ADVERTISING DIRECTOR Bucket Lists, Part 1 – John Shoemaker King Air Magazine Be a Box Checker! 2779 Aero Park Drive by Matthew McDaniel Traverse City, MI 49686 37 Phone: 1-800-773-7798 Fax: (231) 946-9588 Technically ... E-mail: [email protected] ADVERTISING ADMINISTRATIVE COORDINATOR AND REPRINT SALES 22 Betsy Beaudoin Aviation Issues – 40 Phone: 1-800-773-7798 E-mail: [email protected] New FAA Admin, Advertiser Index ADVERTISING ADMINISTRATIVE ASSISTANT PLANE Act Support and Erika Shenk International Flight Plan Phone: 1-800-773-7798 E-mail: [email protected] Format Adopted SUBSCRIBER SERVICES by Kim Blonigen Rhonda Kelly, Mgr. Kelly Adamson Jessica Meek Jamie Wilson P.O. Box 1810 24 Traverse City, MI 49685 1-800-447-7367 Ask The Expert – ONLINE ADDRESS Flap Stories www.kingairmagazine.com by Tom Clements SUBSCRIPTIONS King Air is distributed at no charge to all registered owners of King Air aircraft. -
Harry Ricardo – a Passion for Efficiency
The Piston Engine Revolution Harry Ricardo – A Passion for Efficiency David Morrison Harry Ricardo, born in 1885, was a true pioneer of internal combustion engine research and development, designing and building his first practical engine from the age of 16. His early life, especially at Trinity College, Cambridge, coincided with some key embryonic developments in internal combustion engines, which had a strong influence on his research, especially the work of Bertram Hopkinson and Sir Dugald Clerk. He was passionate about energy efficiency in both his business and private life. This paper covers Harry Ricardo’s early work, experimenting with stratified charge concepts as early as 1903, leading to his work in the early decades of the twentieth century which generated internationally-renowned designs in both diesel and gasoline road vehicle combustion systems. Of these, perhaps the Comet indirect injection system for diesel engines was the most prolific and persisted in various forms well into the 1980s. A very important opportunity for the company was the early work with Shell to study the influence of fuel properties, using a Ricardo variable compression ratio engine. During his time, he had none of the powerful simulation and visualisation tools we take for granted today. He had to use his vivid imagination by trying to visualise what the airflow and fuel mixing must be like inside a combustion chamber. Significant engines up to 1950 included the Dolphin two-stroke, the Comet IDI diesel engine for the world’s first production diesel car – the Citroen Rosalie, the Rolls-Royce diesel conversion for the Flying Spray land speed record car and many developments of spark-ignition combustion systems, including the Turbulent Head. -
History of a Forgotten Engine Alex Cannella, News Editor
POWER PLAY History of a Forgotten Engine Alex Cannella, News Editor In 2017, there’s more variety to be found un- der the hood of a car than ever. Electric, hybrid and internal combustion engines all sit next to a range of trans- mission types, creating an ever-increasingly complex evolu- tionary web of technology choices for what we put into our automobiles. But every evolutionary tree has a few dead end branches that ended up never going anywhere. One such branch has an interesting and somewhat storied history, but it’s a history that’s been largely forgotten outside of columns describing quirky engineering marvels like this one. The sleeve-valve engine was an invention that came at the turn of the 20th century and saw scattered use between its inception and World War II. But afterwards, it fell into obscurity, outpaced (By Andy Dingley (scanner) - Scan from The Autocar (Ninth edition, circa 1919) Autocar Handbook, London: Iliffe & Sons., pp. p. 38,fig. 21, Public Domain, by the poppet valves we use in engines today that, ironically, https://commons.wikimedia.org/w/index.php?curid=8771152) it was initially developed to replace. Back when the sleeve-valve engine was first developed, through the economic downturn, and by the time the econ- the poppet valves in internal combustion engines were ex- omy was looking up again, poppet valve engines had caught tremely noisy contraptions, a concern that likely sounds fa- up to the sleeve-valve and were quickly becoming just as miliar to anyone in the automotive industry today. Charles quiet and efficient. -
Blue Badge January 2014
Volume 18 Issue 1 Dedicated to all Combat Infantrymen January 2014 In This Issue You’ll Find: Jodrey To Lead CIA A Short Bio of new National Cdr as the Cover Story The annual listing of CIA Offi- cers and CIA unit locations. A preview of the 2014 convention site and member survey Convention photos and highlights Commander’s Column and Our View How to recommend a future con- vention site Blue Badge’s newest feature Looking Back Division’s Doings, activities that member divisions are engaged in Taps Welcome Mat The readers write, letters to the editor Association information Brother’s –in-arms New membership applications Jerry Jodrey of Sunbury, OH will lead the Combat Infantrymen’s Association for the next two years. He is a retired US Army Master Sergeant earning his CIB in Vietnam. In addition to his CIB other personal and campaign medals (Continued on page 2) Page 2 Blue Badge/Admin “Stuff” January 2014 STATEMENT OF ADMINISTRATIVE PUBLICATION GUIDELINES The Blue Badge is the official publication of the One of the delays that causes some confusion and ag- Combat Infantrymen’s Association. It is published two gravation among members is sometimes perceived as a times a year. Issue 1 covers Jan-June and will be lack of response to the member needs. The staff works published in July; issue 2 covers July-Dec and will be hard to answer your questions, act on your requests, and in published in January. All official information pertaining general be responsive to your needs. One of the problems to the Association will be found here. -
Dive Bombing
FLIGHT, Jti'y 10th, 11741. a The Brewster Bermuda two-seater dive-bomber now in production m America for the R.A.F. and F.A.A. DIVE BOMBING Factors Affecting Pilot and Machine IVE bombing may be defined as is aimed at the target and descends for an effect of " 5g " while holding the release of bombs when com- rapidly towards it. For maximum the same speed of 340 m.p.h. right D ing out of a dive at a target. accuracy, the bomb should not be re round the curve. That is to say, the There is only one exact position for leased in the straight dive, but its pilot's effective weight on the seat at release of the bomb because, unless instant of release should be timed to the bottom of the pull-out curve is the dive is at 90 deg. to the ground, occur just after the start of the pull- five times what it is in straight and the bomb does not travel in a straight out, so that the curvature of the unaccelerated flight. For such a path after it leaves the aeroplane. bomb's path will bring it right on to factor, the descent is 1,300ft after Although, as is obvious, different air the target. starting the pull-out. Of course, if craft will dive at different speeds, it During the pull-out the aeroplane the diving speed is lower, the loss of is generally assumed that the addi- travels round the arc of a circle until height in recovery from the dive is tional velocity imparted to the bomb it is again climbing, and after that very much reduced, and a Ju 87 is equal to dropping the same bomb makes good its escape. -
The “Michell” Crankless Engine – Why Was It Not a Commercial Success?
The Piston Engine Revolution The “Michell” Crankless Engine – Why was it not a commercial success? John A. Anning At the beginning of the twentieth century, when the internal combustion engine was being developed for automobiles and aircraft, some designers arranged for the cylinders to be parallel to the output shaft. These became known as axial or barrel engines. They utilised either the swash plate or wobbleplate principles. The most promising was the Michell Crankless Engine, which was patented in 1917. AGM Michell FRS (1870-1959) was an Australian engineer best known for the design of the “Michell” tilting pad thrust bearing, patented in the UK and Australia in 1905. By the end of WWI Michell was a wealthy man from royalties and applied the tilting pad principle to an axial engine. The principle was first applied to compressors and by 1920 the first IC engine was made. An advantage is that perfect primary and secondary balance can be achieved at all rotational speeds. Michell formed Crankless Engines (Australia) Pty Ltd. A number of engines were built and installed in existing production vehicles. He realised that for the future commercialisation an overseas involvement was essential so offices were opened in London and New York. The Michell crankless principle still remains the most efficient method of converting linear into rotary motion. By the late 1920s with the world depression the Australian company was forced into receivership. A business analysis is given as to the possible reasons for its failure to achieve commercial success. It deserves its place in the panoply of IC engine history.