Petrographic Characteristics of Coal Gasification and Combustion By
Total Page:16
File Type:pdf, Size:1020Kb
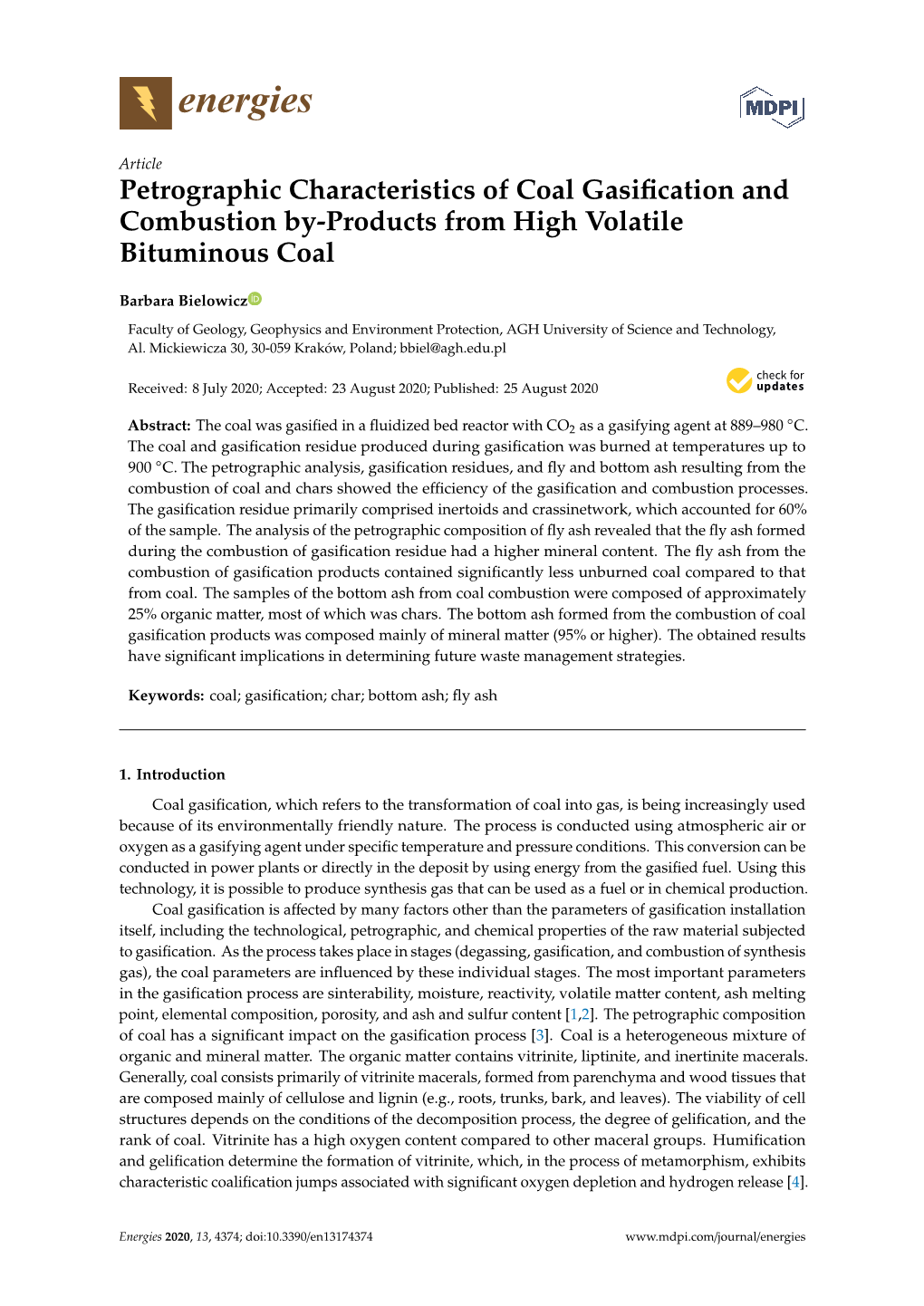
Load more
Recommended publications
-
Petrographic and Vitrinite Reflectance Analyses of a Suite of High Volatile Bituminous Coal Samples from the United States and Venezuela
Petrographic and vitrinite reflectance analyses of a suite of high volatile bituminous coal samples from the United States and Venezuela Open-File Report 2008-1230 U.S. Department of the Interior U.S. Geological Survey U.S. Department of the Interior Dirk A. Kempthorne, Secretary U.S. Geological Survey Mark D. Myers, Director U.S. Geological Survey, Reston, Virginia 2008 For product and ordering information: World Wide Web: http://www.usgs.gov/pubprod Telephone: 1-888-ASK-USGS For more information on the USGS—the Federal source for science about the Earth, its natural and living resources, natural hazards, and the environment: World Wide Web: http://www.usgs.gov Telephone: 1-888-ASK-USGS Suggested citation: Hackley, P.C., Kolak, J.J., 2008, Petrographic and vitrinite reflectance analyses of a suite of high volatile bituminous coal samples from the United States and Venezuela: U.S. Geological Survey Open-File Report 2008-1230, 36 p., http://pubs.usgs.gov/of/2008/1230. Any use of trade, product, or firm names is for descriptive purposes only and does not imply endorsement by the U.S. Government. Although this report is in the public domain, permission must be secured from the individual copyright owners to reproduce any copyrighted material contained within this report. ii Contents Introduction ........................................................................................................................................................................1 Methods ..............................................................................................................................................................................1 -
Middle School - Round 14A
MIDDLE SCHOOL - ROUND 14A TOSS-UP 1) Earth and Space – Short Answer What is the term for sediment with a particle size less than 2 microns? ANSWER: CLAY BONUS 1) Earth and Space – Multiple Choice Which of the following correctly describes the typical progression from dead organic matter to coal? W) Peat, lignite, bituminous [bih-TOOM-in-us], anthracite [AN-thrah-site] X) Lignite, peat, bituminous, anthracite Y) Lignite, bituminous, peat, anthracite Z) Peat, bituminous, anthracite, lignite ANSWER: W) PEAT, LIGNITE, BITUMINOUS, AND ANTHRACITE ~~~~~~~~~~~~~~~~~~~~~~~~~~~~~~~~~~~~~~~~ TOSS-UP 2) Physical Science – Short Answer Chlorine has an atomic mass of 35.45. Given that chlorine has two naturally-occurring isotopes, chlorine-35 and chlorine-37, then, to the nearest whole number, what percentage of chlorine atoms have a mass number of 35.45? ANSWER: ZERO BONUS 2) Physical Science – Short Answer To the nearest gram, what is the mass of two moles of carbon dioxide? ANSWER: 88 Middle School - Round 14A Page 1 TOSS-UP 3) Math – Short Answer What is the slope of a line perpendicular to the line with equation 7x – 4y = –28? ANSWER: –4/7 BONUS 3) Math – Short Answer A fence is built along the perimeter of a 200-foot-by-300-foot rectangular field. Posts are placed at the four corners and every 5 feet thereafter. How many posts are required? ANSWER: 200 ~~~~~~~~~~~~~~~~~~~~~~~~~~~~~~~~~~~~~~~~ TOSS-UP 4) Life Science – Short Answer In eukaryotes [YOO-care-ee-oats], DNA and histones are organized into what structures? ANSWER: CHROMOSOMES BONUS 4) Life Science – Short Answer What type of microscopy [my-CRAW-scah-pee] involves the use of a laser, photomultiplier detector, and a pinhole that ensures elimination of out-of-plane light emitted by the sample? ANSWER: CONFOCAL Middle School - Round 14A Page 2 TOSS-UP 5) Energy – Short Answer Researchers at the Joint BioEnergy Institute are studying ionic liquids as a solvent to break down cellulose before biofuel production. -
Final Report Coal Project
2011 Coal Electrolysis for the Production of Hydrogen and Liquid Fuels Dr. Gerardine Botte OHIO UNIVERSITY Center for Electrochemical Engineering Research CEER-Ohio University Final Executive Summary Report Clean technologies for the production of high value chemicals, such as hydrogen, liquid fuels, and refined organic and inorganic compounds, with significant impact in the different business spheres (e.g., petrochemical, polymers, and plastics) are very important for national security purposes and for preservation of the environment. Power is traditionally generated from coal by the complete combustion (oxidation) of coal. When hydrogen is desired as a product, coal gasification (partial oxidation) is employed. Most overall coal gasification schemes use a series of reactions ranging from combustion (for heat generation) to partial oxidation (for hydrogen generation), to the water-gas shift reaction and others to produce a fuel gas product stream. In order to produce a hydrogen (H2) product from this fuel gas stream, the hydrogen must be removed from a mixture that includes carbon monoxide (CO), carbon dioxide (CO2), hydrogen sulfide (H2S), particulates, and other gases (perhaps including nitrogen, if an oxygen plant is not used). In addition, CO2 needs to be captured and sequestered from the stream to reduce the emissions of this gas to the environment. These separations become an extremely complex and costly consideration. In order for CO2 to be captured, it either must be separated from other gases in a mixture (say, CO2 from N2), or O2 must be separated from air in order to be used as combustion feed to create “pure” CO2 product. In either case, significant capital and operating expenses, as well as significant power consumption, are incurred for either kind of separation. -
Chemical and Physical Structural Studies on Two Inertinite-Rich Lump
CHEMICAL AND PHYSICAL STRUCTURAL STUDIES ON TWO INERTINITE-RICH LUMP COALS. Nandi Malumbazo A thesis submitted in fulfilment of the requirements for the degree of Doctor of Philoso- phy in the School of Chemical and Metallurgical Engineering at the University of the Witwatersrand. Johannesburg, 2011 DECLARATION I, Nandi Malumbazo, declare that the thesis entitled: “CHEMICAL AND PHYSICAL STRUCTURAL STUDIES ON TWO INER- TINITE-RICH LUMP COALS” is my own work and that all sources I have used or quoted have been indicated and ac- knowledged by means of references. Signature: ……………………………………………………………….. Date:………………………………………………………………………… Page i ABSTRACT ABSTRACT Two Highveld inertinite-rich lump coals were utilized as feed coal samples in order to study their physical, chemical structural and petrographic variations during heat treat- ment in a packed-bed reactor unit combustor. The two feed lump coals were selected as it is claimed that Coal B converts at a slower rate in a commercial coal conversion process when compared to Coal A. The reason for this requires detailed investigation. Chemical structural variations were determined by proximate and coal char CO2 reactiv- ity analysis. Physical structural variations were determined by FTIR, BET adsorption methods, XRD and 13C Solid state NMR analysis. Carbon particle type analysis was con- ducted to determine the petrographic constituents of the reactor generated samples, their maceral associations (microlithotype), and char morphology. This analysis was undertaken with the intention of tracking the carbon conversion and char formation and consumption behaviour of the two coal samples within the reactor. Proximate analysis revealed that Coal A released 10 % more of its volatile matter through the reactor compared to Coal B. -
Structural Transformation of Nascent Char During the Fast Pyrolysis Of
Structural transformation of nascent char during the fast pyrolysis of mallee wood and low-rank coals 5 Lei Zhang1, Tingting Li1, Dimple Quyn1, Li Dong1, Penghua Qiu1,2, Chun-Zhu Li1,* 1Fuels and Energy Technology Institute, Curtin University of Technology, GPO Box U1987, Perth, WA 6845, Australia 10 2School of Energy Science and Engineering, Harbin Institute of Technology, 92 West Dazhi Street, Harbin, Heilongjiang 150001, People’s Republic of China 15 * Corresponding author: E-mail address: [email protected] (Chun-Zhu Li) Phone: +61 8 9266 1131 Fax: +61 8 9266 1138 20 February 2015 1 25 Abstract The changes in char structure during the fast pyrolysis of three different feedstocks from 600 °C to 1200 °C were investigated. Western Australian Collie sub-bituminous coal, Victorian Loy Yang brown coal and Australian mallee wood were pyrolysed in a wire-mesh 30 reactor at a heating rate of 1000 K s-1 with holding time ranging from 0 s to 50 s. FT- Raman/IR spectroscopy was used to characterise the structural features of the chars obtained at different temperatures. The combined use of a wire-mesh reactor and a FT-Raman/IR spectrometer has provided significant insights into the rapid changes in the chemical structure of nascent char during fast pyrolysis. Our results indicate that the three fuels began 35 significant ring condensation at different temperatures. Mallee wood showed significant growth of large rings within 1 s holding at 600 °C; however Loy Yang and Collie coals showed significant ring condensation at 800 °C and 900 °C respectively. -
Anthracite Coal 13
Rock and Mineral 10-Specimen Kit Companion Book Presented by This mineral kit was also made possible through the generosity of the mining companies who supplied the minerals. If you have any questions or comments about this kit please contact the SME Pittsburgh Section Chair at www.smepittsburgh.org. For more information about mining, visit the following web site: www.smepittsburgh.org BSA’s www.scouting.org - search “Mining in Society” SME’s www.mineralseducationcoalition.org/ Updated July 2016 © SME Pittsburgh Section The SME Pittsburgh Section thanks the companies, mines, and individuals who provided mineral samples and donated time or services that made these mineral kits possible. Alpha Natural Resources, Inc. CONSOL Energy, Inc. Coolspring Stone Supply John T. Boyd Company Morton Salt Murray Energy Corporation Newmont Mining Corporation Reed Gold Mine (State of North Carolina) Steelhead Specialty Minerals United States Gypsum Company US Steel Corporation United Taconite (Cliffs Natural Resources, Inc.) CONTENTS INTRODUCTION 3 MINERAL IDENTIFICATION 5 FUELS 10 Bituminous Coal 12 Anthracite Coal 13 BASE METAL ORES 14 Iron Ore 15 Copper Ore 16 PRECIOUS METALS 17 Gold Ore 18 ROCKS AND INDUSTRIAL MINERALS 19 Gypsum 21 Limestone 22 Marble 23 Salt 24 Zeolite 25 Note: many of the images reproduced here are from Wikipedia which allows non commercial use or from the Minerals Education Coalition web site http://www.mineralseducationcoalition.org/minerals. INTRODUCTION The effect rocks and minerals have on our daily lives is not always obvious, but this book will help explain how essential they really are. If you don’t think you come in contact with minerals every day, think about these facts below and see if you change your mind. -
Vitrinite Recycling: Diagnostic Criteria and Reflectance Changes During Weathering and Reburial
Vitrinite recycling: diagnostic criteria and reflectance changes during weathering and reburial. Pierre Nzoussi - Mbassani, Yoann Copard, Jean-Robert Disnar To cite this version: Pierre Nzoussi - Mbassani, Yoann Copard, Jean-Robert Disnar. Vitrinite recycling: diagnostic criteria and reflectance changes during weathering and reburial.. International Journal of Coal Geology, Elsevier, 2005, 61, pp.223-239. 10.1016/j.coal.2004.08.002. hal-00023485 HAL Id: hal-00023485 https://hal-insu.archives-ouvertes.fr/hal-00023485 Submitted on 23 May 2006 HAL is a multi-disciplinary open access L’archive ouverte pluridisciplinaire HAL, est archive for the deposit and dissemination of sci- destinée au dépôt et à la diffusion de documents entific research documents, whether they are pub- scientifiques de niveau recherche, publiés ou non, lished or not. The documents may come from émanant des établissements d’enseignement et de teaching and research institutions in France or recherche français ou étrangers, des laboratoires abroad, or from public or private research centers. publics ou privés. Vitrinite recycling: diagnostic criteria and reflectance changes during weathering and reburial P. Nzoussi-Mbassani, Y. Copard and J.R. Disnar Institut des Sciences de la Terre d'Orléans (ISTO- UMR 6113 du CNRS, Université d'Orléans, Bâtiment de Géosciences, 45067 Orléans cedex 2, France Keywords: Recycled vitrinite; Autochthonous vitrinite; Vitrinite reflectance; Senegalese basin; Ardèche margin; Weathering Abstract The aim of this study was first to review or even identify reliable diagnostic criteria to distinguish recycled and autochthonous vitrinite particles and, second, to examine and try to explain the impact of weathering and reburial on optical changes (reflectance) of recycled material. -
Coal Characteristics
CCTR Indiana Center for Coal Technology Research COAL CHARACTERISTICS CCTR Basic Facts File # 8 Brian H. Bowen, Marty W. Irwin The Energy Center at Discovery Park Purdue University CCTR, Potter Center, 500 Central Drive West Lafayette, IN 47907-2022 http://www.purdue.edu/dp/energy/CCTR/ Email: [email protected] October 2008 1 Indiana Center for Coal Technology Research CCTR COAL FORMATION As geological processes apply pressure to peat over time, it is transformed successively into different types of coal Source: Kentucky Geological Survey http://images.google.com/imgres?imgurl=http://www.uky.edu/KGS/coal/images/peatcoal.gif&imgrefurl=http://www.uky.edu/KGS/coal/coalform.htm&h=354&w=579&sz= 20&hl=en&start=5&um=1&tbnid=NavOy9_5HD07pM:&tbnh=82&tbnw=134&prev=/images%3Fq%3Dcoal%2Bphotos%26svnum%3D10%26um%3D1%26hl%3Den%26sa%3DX 2 Indiana Center for Coal Technology Research CCTR COAL ANALYSIS Elemental analysis of coal gives empirical formulas such as: C137H97O9NS for Bituminous Coal C240H90O4NS for high-grade Anthracite Coal is divided into 4 ranks: (1) Anthracite (2) Bituminous (3) Sub-bituminous (4) Lignite Source: http://cc.msnscache.com/cache.aspx?q=4929705428518&lang=en-US&mkt=en-US&FORM=CVRE8 3 Indiana Center for Coal Technology Research CCTR BITUMINOUS COAL Bituminous Coal: Great pressure results in the creation of bituminous, or “soft” coal. This is the type most commonly used for electric power generation in the U.S. It has a higher heating value than either lignite or sub-bituminous, but less than that of anthracite. Bituminous coal -
And Pb-Enriched Coals from Jungar Coalfield, Northwestern China
minerals Article The Petrography, Mineralogy and Geochemistry of Some Cu- and Pb-Enriched Coals from Jungar Coalfield, Northwestern China Dongna Liu 1,3 ID , Anchao Zhou 1, Fangui Zeng 1,3, Fenghua Zhao 2,3,* and Yu Zou 2 1 College of Minging Engineering, Taiyuan University of Technology, Taiyuan 030024, China; [email protected] (D.L.); [email protected] (A.Z.); [email protected] (F.Z.) 2 College of Geoscience and Surveying Engineering, China University of Mining and Technology, Beijing 100083, China; [email protected] 3 Key Laboratory of Coal and Coal Gas Geology of Shanxi Province, Taiyuan 030024, China * Correspondence: [email protected]; Tel.: +86-010-62331878 Received: 24 September 2017; Accepted: 21 December 2017; Published: 27 December 2017 Abstract: The petrological, geochemical, and mineralogical composition of the Carboniferous-Permian coal deposit in the Jungar coalfield of inner Mongolia, Northwestern China, were investigated using optical microscopy and field emission scanning electron microscopy in conjunction with an energy-dispersive X-ray spectrometer (SEM-EDX), as well as X-ray powder diffraction, X-ray fluorescence, and inductively coupled plasma mass spectrometry. The Jungar coal is of high volatile C/B bituminous quality with 0.58% vitrinite reflectance and has a low sulfur content of 0.70% on average. Inertinite (mineral-free basis) generally dominates in coal from the lower part of the Shanxi formation, and vitrinite is the major maceral assemblage in the coal from the Taiyuan formation, which exhibits forms suggesting variation in the sedimentary environment. The Jungar coal is characterized by higher concentrations of copper (Cu) in No. -
Characteristics of Early Cretaceous Wildfires in Peat-Forming Environment, NE China Shuai Wang, Long-Yi Shao*, Zhi-Ming Yan, Ming-Jian Shi and Yun-He Zhang
Wang et al. Journal of Palaeogeography (2019) 8:17 https://doi.org/10.1186/s42501-019-0035-5 Journal of Palaeogeography ORIGINAL ARTICLE Open Access Characteristics of Early Cretaceous wildfires in peat-forming environment, NE China Shuai Wang, Long-Yi Shao*, Zhi-Ming Yan, Ming-Jian Shi and Yun-He Zhang Abstract Inertinite maceral compositions in coals from the Early Cretaceous Erlian, Hailar, and Sanjiang Basins in NE China are analyzed in order to reveal palaeowildfire events and palaeoclimate variations. Although huminite is the dominant maceral group in the studied basins, the inertinite group, as a byproduct of palaeowildfires, makes up a considerable proportion. Occurrence of inertinite macerals indicates that wildfires were widespread and frequent, and supports the opinion that the Early Cretaceous was a “high-fire” interval. Inertinite contents vary from 0.2% to 85.0%, mostly within the range of 10%–45%, and a model-based calculation suggests that the atmospheric oxygen levels during the Aptian and Albian (Early Cretaceous) were around 24.7% and 25.3% respectively. Frequent fire activity during Early Cretaceous has been previously related to higher atmospheric oxygen concentrations. The inertinite reflectance, ranging from 0.58%Ro to 2.00%Ro, indicates that the palaeowildfire in the Early Cretaceous was dominated by ground fires, partially reaching-surface fires. These results further support that the Cretaceous earliest angiosperms from NE China were growing in elevated O2 conditions compared to the present day. Keywords: Inertinite, Coal, Wildfire, Palaeo-atmospheric oxygen level, Angiosperm, Early Cretaceous, NE China 1 Introduction 2004;Bowmanetal.2009). The minimum oxygen content As a byproduct of peatland evolution under the common that can support combustion in nature is 15% (Belcher influence of geological conditions including palaeoclimate, and McElwain 2008). -
Lecture 32: Coke Production
NPTEL – Chemical – Chemical Technology II Lecture 32: Coke production 32.1 Introduction Coal is used as fuel for electric power generation, industrial heating and steam generation, domestic heating, rail roads and for coal processing. Coal composition is denoted by rank. Rank increases with the carbon content and decreases with increasing oxygen content. Many of the products made by hydrogenation, oxidation, hydrolysis or fluorination are important for industrial use. Stable, low cost, petroleum and natural gas supplies has arose interest in some of the coal products as upgraded fuels to reduce air pollution as well as to take advantage of greater ease of handling of the liquid or gaseous material and to utilize existing facilities such as pipelines and furnaces. 32.2 Coking of coal Raw material is Bituminous coal. It appears to have specific internal surfaces in the range of 30 to 100m2/g. Generally one ton of bituminous coal produces 1400 lb of coke. 10 gallons of tar. Chemical reaction:- 4(C3H4)n nC6H6 + 5nC + 3nH2 + nCH4 Coal Benzene Coke Lighter hydrocarbon Joint initiative of IITs and IISc – Funded by MHRD Page 1 of 9 NPTEL – Chemical – Chemical Technology II Process flow sheet: Illustrated in Figure. Figure 32.1 Flow sheet of coking of coal 32.3 Functional role of each unit (Figure 32.1): (a) Coal crusher and screening: At first Bituminous coal is crushed and screened to a certain size. Preheating of coal (at 150-250˚C) is done to reduce coking time without loss of coal quality. Briquetting increases strength of coke produced and to make non - coking or poorly coking coals to be used as metallurgical coke. -
On the Fundamental Difference Between Coal Rank and Coal Type
International Journal of Coal Geology 118 (2013) 58–87 Contents lists available at ScienceDirect International Journal of Coal Geology journal homepage: www.elsevier.com/locate/ijcoalgeo Review article On the fundamental difference between coal rank and coal type Jennifer M.K. O'Keefe a,⁎, Achim Bechtel b,KimonChristanisc, Shifeng Dai d, William A. DiMichele e, Cortland F. Eble f,JoanS.Esterleg, Maria Mastalerz h,AnneL.Raymondi, Bruno V. Valentim j,NicolaJ.Wagnerk, Colin R. Ward l, James C. Hower m a Department of Earth and Space Sciences, Morehead State University, Morehead, KY 40351, USA b Department of Applied Geosciences and Geophysics, Montan Universität, Leoben, Austria c Department of Geology, University of Patras, 265.04 Rio-Patras, Greece d State Key Laboratory of Coal Resources and Safe Mining, China University of Mining and Technology, Beijing 100083, China e Department of Paleobiology, Smithsonian Institution, Washington, DC 20013-7012, USA f Kentucky Geological Survey, University of Kentucky, Lexington, KY 40506, USA g School of Earth Sciences, The University of Queensland, QLD 4072, Australia h Indiana Geological Survey, Indiana University, 611 North Walnut Grove, Bloomington, IN 47405-2208, USA i Department of Geology and Geophysics, College Station, TX 77843, USA j Department of Geosciences, Environment and Spatial Planning, Faculty of Sciences, University of Porto and Geology Centre of the University of Porto, Rua Campo Alegre 687, 4169-007 Porto, Portugal k School Chemical & Metallurgical Engineering, University of Witwatersrand, 2050, WITS, South Africa l School of Biological, Earth and Environmental Sciences, University of New South Wales, Sydney, Australia m University of Kentucky, Center for Applied Energy Research, 2540 Research Park Drive, Lexington, KY 40511, USA article info abstract Article history: This article addresses the fundamental difference between coal rank and coal type.