For the Classification and Construction of Sea-Going
Total Page:16
File Type:pdf, Size:1020Kb
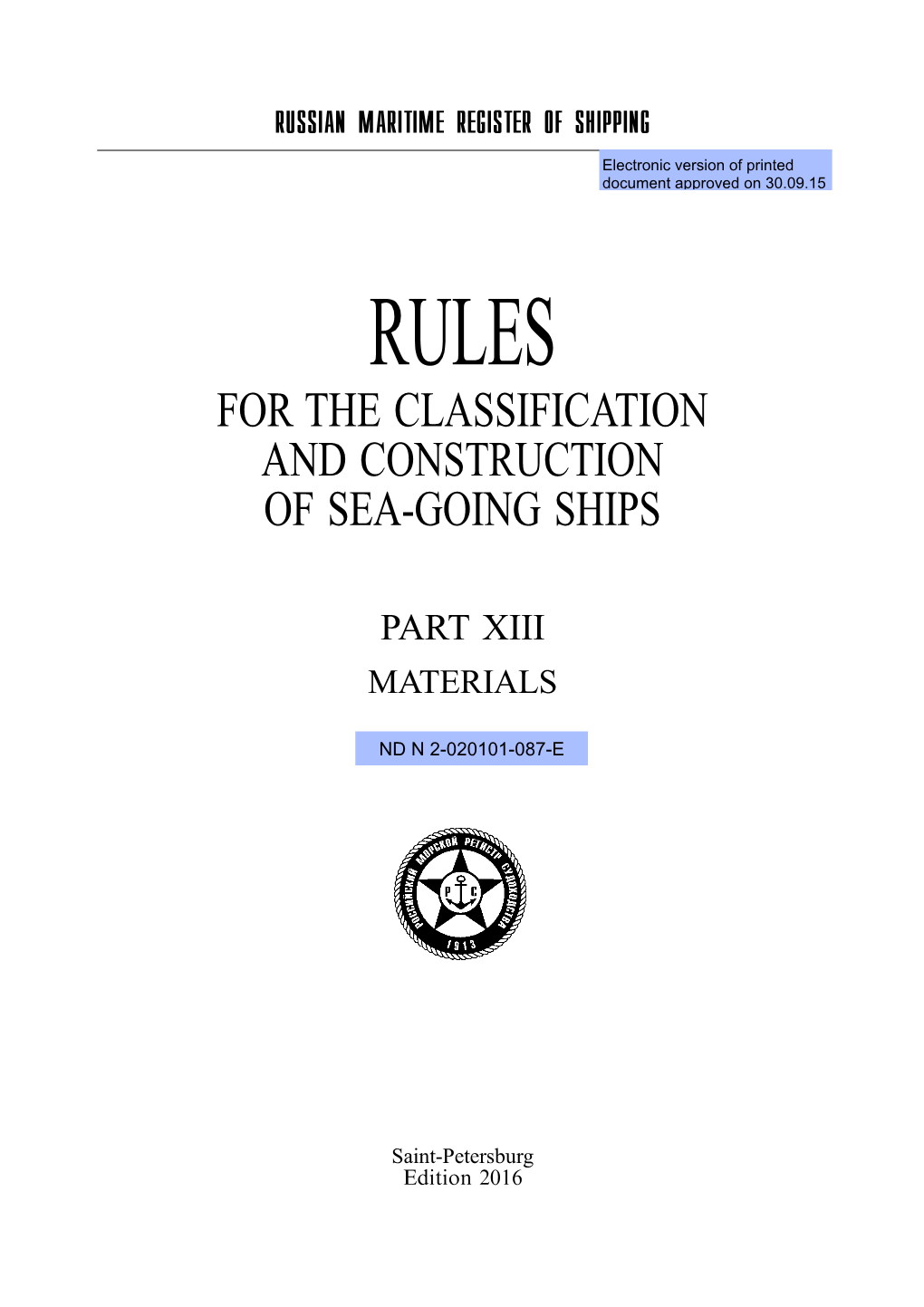
Load more
Recommended publications
-
View/Download PDF of This Issue, the File Size
E.O. Paton Electric Welding Institute of the National Academy of Sciences of Ukraine International Scientific-Technical and Production Journal Issue 06 2019 Published Monthly Since 2000 English translation of the monthly «Avtomaticheskaya Svarka» (Automatic Welding) journal published in Russian since 1948 EDITORIAL BOARD CONTENTS Editor-in-Chief B.E. Paton Plenary Papers for International Conference Scientists of PWI, Kyiv S.I. Kuchuk-Yatsenko (vice-chief ed.), «Consumables for Welding, Surfacing V.N. Lipodaev (vice-chief ed.), and Coating Deposition and 3D Technologies», Yu.S. Borisov, G.M. Grigorenko, A.T. Zelnichenko, V.V. Knysh, Kyiv, PWI, 4–5 June 2019 I.V. Krivtsun, Yu.N. Lankin, L.M. Lobanov, V.D. Poznyakov, Bonnel J.-M., Maurer M. and Rosert R. Submerged arc surfacing of high-alloy I.A. Ryabtsev, K.A. Yushchenko steels by flux-cored wires .................................................................................. 3 Scientists of Ukrainian Universities Golovko V.V., Stepanyuk S.N. and Ermolenko D.Yu. Dispersion modification V.V. Dmitrik, NTU «KhPI», Kharkov V.V. Kvasnitsky, NTUU «KPl», Kyiv of dendrite structure of weld metal .................................................................... 13 E.P. Chvertko, NTUU «KPl», Kyiv Yushchenko K.A., Gakh I.S., Zadery B.A., Zvyagintseva A.V. and Foreign Scientists Karasevskaya O.P. Repair surfacing of gas turbine engine blades from N.P. Alyoshin high-temperature nickel alloys with surface defects and damage ..................... 19 N.E. Bauman MSTU, Moscow, Russia Guan Qiao Goncharov I.O., Sudavtsova V.S., Mishchenko D.D., Duchenko A.M. and Beijing Aeronautical Institute, China M. Zinigrad Sokolsky V.E. Influence of refractory dispersed phases on physical-chemical Ariel University, Israel properties of slag metls of MgO–Al2O3–SiO2–CaF2 system .............................. -
The Effects of Heat Treatment on the Microstructure and Microhardness of Explosive Welding
Scientific Research and Essays Vol. 6(19), pp. 4141-4151, 8 September, 2011 Available online at http://www.academicjournals.org/SRE DOI: 10.5897/SRE11.1018 ISSN 1992-2248 ©2011 Academic Journals Full Length Research Paper The effects of heat treatment on the microstructure and microhardness of explosive welding 1,2 1 1 Fehim Findik *, Ramazan Yilmaz and Tolga somyurek 1Technical Education Faculty, Sakarya University, 54090 Esentepe Adapazari, Turkey. 2Faculty of Engineering and Natural Sciences, International University of Sarajevo, Hrasnicka Cesta 15, 71000 Sarajevo, Bosnia-Herzegovina. Accepted 28 July, 2011 An AISI 304 type of austenitic stainless steel and low carbon steel were cladded by explosive welding in this study. Four explosive loading rates were used with the range of 1 and 2.0. Stand-of distance (s=t) was also used as a welding parameter. Cladded materials have been subjected to heat treatment at 250°C for times of ranging from 1 to 4 h. Effect of heat treatment on the microstructure and mechanical properties has been evaluated using optical and scanning electron microscopy, EDS analysis technique and hardness tests, respectively. The results indicate that straight and wavy structures of bonding at the interface were obtained according to the loading of explosive rate. The grain size of the cladded materials near the interface were increased with the duration of heat treatment. Hardness values at the interface of the cladded materials were decreased with the increment of heat treatment period. Key word: Explosive welding, hardness, microstructure, stainless steel, low carbon steel. INTRODUCTION Explosion welding is one of the joining methods steel has low corrosion resistance therefore, it may be consisting of a solid state welding process in which cladded with the materials such as aluminium, titanium controlled explosive donation on the surface of a metal. -
VOLUME 1 Welding Metallurgy Carbon and Alloy Steels
VOLUME 1 Welding Metallurgy Carbon and Alloy Steels Volume I Fundamentals George E. Linnert GML Publications Hilton Head Island, South Carolina, USA Fourth Edition Published by the American Welding Society Miami, Florida, USA Contents Contents Chapter One: Background to Welding Metallurgy 1 MILESTONES IN WELDING HISTORY 1 THE FUTURE OF WELDING 4 WHAT IS WELDING METALLURGY? 6 PUTTING WELDING METALLURGY TO USE 12 WELDING TECHNOLOGY RESOURCES 12 SUGGESTED READING 15 Chapter Two: The Structure of Metals 18 ATOMS 18 Elementary Particles 20 Electrons 22 Positrons 26 Atomic Nuclei 26 Protons 27 Neutrons 28 Atom Construction 32 Isotopes of Elements 33 Isobars 34 Atomic Weight 34 Atomic Mass 34 Atom Valency 35 lonization 36 Radioactivity 37 Atom Size or Diameter 38 THE ELEMENTS 39 AGGREGATES OF ATOMS 41 The Solid State 45 The Crystalline Solids 45 Amorphous Solids 47 The Liquid State 48 The Gaseous State 49 FUNDAMENTALS OF CRYSTALS 50 Identification of Planes and Directions in Crystals 56 Basic Types of Crystals 56 vi Welding Metallurgy Inert Gas Crystals 58 Ionic Crystals 58 Covalent Crystals 59 Metallic Crystals 59 THE CRYSTALLINE STRUCTURE OF METALS 61 How Does a Crystal Grow from the Melt? 64 The Formation of Dendrites 66 The Formation of Grains 68 The Shape of Grains 71 The Size of Grains 72 Undercooling 72 THE IMPORTANCE OF A CRYSTALLINE STRUCTURE 74 Allotropic Transformation 75 Solubility in the Solid State 76 Plasticity in Metallic Crystals 77 Slip in Crystalline Structures 77 Slip and Lattice Orientation 78 Slip in Polycrystalline Metals -
Explosive Welding of Metals in a Vacuum Environment
WELDING Explosive welding of metals in a vacuum environment Over the years, several articles have already been written on the phenomenon of explosive metal working. This is then usually taken to mean the explosive welding and cladding of metals, although explosives can also be used to shape, cut and harden the surfaces of metals. Various sources of literature provide the essentials on this subject and regular articles can be found on the development of various theories regarding the binding mechanism. It would therefore be a good idea to once again think about this remarkable welding process that also lends itself well, these days, to being performed in a vacuum environment. This last mentioned fact is particularly noteworthy as this process is normally carried out in the open air (Fig. 1). The main reason for this is that oxygen is needed to facilitate the explosion and because the explosive forces would destroy buildings. The main purpose of the article below is to describe the process of explosive welding and the cladding of metals. By N.W. Buijs - Metallurgist at Innomet b.v. vacuum. The solution is then to use a relatively cheap base material to which a relatively thin layer of expensive metal is bonded by means of explosive welding. This base material is often unalloyed or low alloy carbon steel. Examples are sheets used for shells and bases in the construction of reactor vessels, boilers, clad tube sheets for heat exchangers, nozzles etc. A few examples can be seen in Fig. 2. In addition, explosive welding can be used to produce metal combinations that are impossible to achieve with a thermal welding process. -
Solid State Welding and Application in Aeronautical Industry
ISSN 2303-4521 PERIODICALS OF ENGINEERING AND NATURAL SCIENCES Vol. 4 No. 1 (2016) Available online at: http://pen.ius.edu.ba Solid State Welding and Application in Aeronautical Industry Enes Akca*, Ali Gursel International University of Sarajevo Faculty of Engineering and Natural Sciences Sarajevo, Bosnia and Herzegovina [email protected], [email protected] Abstract In this study solid state welding andapplication in aeronautic industryhave been researched. The solid state welding technicisused in the industrial production fields such as aircraft, nucleer, space industry, aeronautic industry, ect., actually solid state welding is a process by which similar and dissmilar metals can be bonded together. Hence a material can be created as not heavy but strong strength. Beside, advantages and disasvantages of solid state welding have been discussed. Also the diffusion welding and friction welding which belong to the solid state welding is obsevered in aeronautic industry. Keywords: solid state welding, aeronautic industry,diffusion welding, dissimilar materials 1 Introduction Welding is a metal joining process which produces Disadvantages of Solid State Welding: coalescence of metals by heating them to suitable Internal stresses, distortions and changes of micro- temperatures with or without the application of pressure structure in the weld region, or by the application of pressure alone, and with or Harmful effects: light, ultra violate radiation, fumes, without the use of filler material. Basically, welding is high temperature, used for making permanent joints. It is used in the manufacture of automobile bodies, aircraft frames, Also there are many kinds of welding processes; railway wagons, machine frames, structural works, tanks, Arc welding; furniture, boilers, general repair work and ship building. -
High-Velocity Impact Welding Process: a Review
metals Review High-Velocity Impact Welding Process: A Review Huimin Wang 1 and Yuliang Wang 2,3,* 1 National Center for Materials Service Safety, University of Science and Technology Beijing, Beijing 100083, China; [email protected] 2 School of Mechanical Engineering and Automation, Beihang University, Beijing 100191, China 3 Beijing Advanced Innovation Center for Biomedical Engineering, Beihang University, Beijing 100191, China * Correspondence: [email protected]; Tel.: +86-1861-252-5756 Received: 26 December 2018; Accepted: 27 January 2019; Published: 28 January 2019 Abstract: High-velocity impact welding is a kind of solid-state welding process that is one of the solutions for the joining of dissimilar materials that avoids intermetallics. Five main methods have been developed to date. These are gas gun welding (GGW), explosive welding (EXW), magnetic pulse welding (MPW), vaporizing foil actuator welding (VFAW), and laser impact welding (LIW). They all share a similar welding mechanism, but they also have different energy sources and different applications. This review mainly focuses on research related to the experimental setups of various welding methods, jet phenomenon, welding interface characteristics, and welding parameters. The introduction states the importance of high-velocity impact welding in the joining of dissimilar materials. The review of experimental setups provides the current situation and limitations of various welding processes. Jet phenomenon, welding interface characteristics, and welding parameters are all related to the welding mechanism. The conclusion and future work are summarized. Keywords: impact welding; impact velocity; impact angle; welding interface 1. Introduction Welding technique has wide applications in the areas of aerospace, automobiles, shipbuilding, pressure vessels, and bridges. -
Material Characterization of Explosion Welded Clad Plate of Carbon Steel and Alloy 825
International Journal of Scientific Research and Review ISSN NO: 2279-543X MATERIAL CHARACTERIZATION OF EXPLOSION WELDED CLAD PLATE OF CARBON STEEL AND ALLOY 825 Kamal Kishore Research Scholar, Department of Mechanical Engineering, O.P.J.S. University, Churu, Rajasthan, India, E-mail: [email protected] Dr. Mohammad Israr Professor, Department of Mechanical Engineering, Sur University College, Sur, Sultanate of Oman E-mail: [email protected] Dr. Jai Dev Chandel Senior Vice President – Operations, Jindal Saw Ltd, Samaghogha, Gujarat, India E-mail: [email protected] Abstract The petrochemical, oil and gas industries are always looking for the economic and best suitable material for the critical operating atmosphere. The project and operational cost can be reduced by selecting the suitable material by considering corrosion and temperature of the service. Suitable alloy system can be used for the operating service. The usage of clad plates is one of the better solutions for the above statement. In clad plates, two different materials are metallurgically bonded where one material take care of structural strength whereas other corrosion. In this work the carbon steel and UNS N08825 (alloy 825) clad plate was investigated for its structural, corrosion and metallurgical properties. The plate was metallurgically bonded by explosion bonding (welding) process and a comprehensive testing program is used for characterization of the explosion bonded clad plate. The plate was investigated for mechanical tests like tensile, impact test, shear bond test and micro hardness test. The structural steel material grade was API 5L X60M and the grade of CRA was UNS N08825 (alloy 825). The interface was evaluated by optical microscope and SEM (Scanning electron microscope). -
World Market for Clad Plate Stainless Steel – Nickel Alloy – Titanium
The World Market for Clad Plate Stainless Steel – Nickel Alloy – Titanium July 2016 © SMI GmbH 2016 - This report may not be copied, published or disclosed to third parties without the permission of SMI GmbH. TABLE OF CONTENTS DISCLAIMER AND COPYRIGHT .............................................................................. 7 Disclaimer ............................................................................................................. 7 Copyright Protection ............................................................................................ 7 1 Introduction ....................................................................................................... 8 1.1 Clad Plates ...................................................................................................... 8 1.1.1 Rolled Clad Plates ...................................................................................... 9 1.1.2 Explosion Clad Plates ............................................................................... 16 1.1.3 Weld Overlay ............................................................................................ 22 1.1.4 Size Range Comparisons ......................................................................... 23 1.2 Clad Pipes ..................................................................................................... 25 1.2.1 Metallurgically Bonded Clad Pipes ............................................................ 26 1.2.2 Mechanically Bonded Clad Pipes ............................................................. -
Signature Redacted
JUL 2NS 94 JUlL 2 1945') PROPAGATION OF ELECTROMAGNETIC PULSES IN THE IONOSPHERE by Pauline Morrow Austin B.A., Wilson College 1938 M.A., Smith College 1939 SUBMITTED IN PARTIAL FULFILLMENT OF THE REQUIRElI&ETS FCR THE DEGRETh OF DOCTOR OF PHILOSOPHY at the MASSACHUSETTS INSTITUTE O TECHNOLOGY 1942 Signature Redacted Signature of Author ............. ........ Department of Physics, October 7, 1942 Signature Redacted Certified by: ... b71 Thsis Iiperyisor Signature Redacted Chairman!, Department Committee on Graduate Students MANAGEMENT GUIDELINES FOR THE EVALUATION AND SELECTION OF THE WELDING TECHNOLOGIES FOR USE IN OUTER SPACE by Ravikumar Ramiah Nagabushanam Submitted to the department of OCEAN ENGINEERING in partial fulfillment of the requirements for the degree of Master of Science in Ocean Systems Management ABSTRACT Future construction of space structures and inter planetary vehicles will be carried out in space. Also due to the increased service life of the space structures there is an increased need of repair and maintenance work to be carried out in space. NASA has plans for using welding for this purposes. By using welding reliable repair, maintenance and construction of space, structures can be achieved. However, at present research on space welding is at its infancy and not many experiments have been conducted so far. This is mainly due to the resource constraint faced by NASA. This thesis explains the need for using proper evaluation and selection methods for choosing R&D projects. It also examines the drawbacks involved in using conventional financial techniques and suggests the use of option valuation techniques and decision tree analysis to overcome those drawbacks. -
Welding Aluminum—Questions and Answers
Welding Aluminum— Questions and Answers A Practical Guide for Troubleshooting Aluminum Welding-Related Problems by Tony Anderson, CEng, CWEng Welding Aluminum— Questions and Answers A Practical Guide for Troubleshooting Aluminum Welding-Related Problems by Tony Anderson, CEng, CWEng Reviewed by the AWS Product Development Committee This publication is designed to provide information in regard to the subject matter covered. It is made available with the understanding that the publisher is not engaged in the rendering of professional advice. Reliance upon the information contained in this document should not be undertaken without an independent verification of its application for a particular use. The publisher is not responsible for loss or damage resulting from use of this publication. This document is not a consensus standard. Users should refer to the applicable standards for their particular application. 550 N.W. LeJeune Road, Miami, FL 33126 WELDING ALUMINUM—QUESTIONS AND ANSWERS Preface This book is largely comprised of individual Aluminum Questions and Answers that were originally published over a number of years in the American Welding Society (AWS) Welding Journal. The majority of the questions addressed herein originate from inquiries to me, primarily from individuals within the welding fabrication indus- try. Also included in this collection of material are some feature articles that I have had published previously in the Welding Journal. The welding processes section con- tains some information and parameters graciously provided by The Aluminum Associ- ation and reproduced from their outstanding publication “Welding Aluminum Theory and Practice.” Many of the graphics and charts within this book have been reproduced with permission from ESAB Welding and Cutting Products and were taken from material that is used by AlcoTec Wire Corporation and ESAB Welding and Cutting Products for their aluminum welding technology training programs. -
SRI Hermetics Capabilities
Technology and Process Capability FoundAtion SRI Hermetics is a design and manufacturing company Metal-to-Metal Joining SRI Hermetics was founded on the principle of using The ability to join dissimilar metals through the use that specializes in the science of hermetic sealing. • Explosion Welding advanced engineering and material science to create of advanced processes such as explosion welding, We structured our business with a complement of • Laser Welding the world’s leading hermetic electrical connectors and vacuum brazing, diffusion bonding and laser welding equipment, processing, technology and expertise to • Vacuum Brazing/Soldering electronic packaging solutions. Since our inception, we is another core technology area that SRI Hermetics has provide our customers with turn-key solutions for their • Diffusion Bonding have developed and introduced many new technologies developed for the manufacturing of high performance mission critical electronic packaging. to the industry, setting new performance standards and hermetic assemblies. Many of our exclusive joining • Furnace H2 Brazing/Soldering displacing the traditional methods of glass to ferrous processes strengthen weak points within an assembly Ceramax Seals Metal-to-Ceramic Joining • Copper Alloy Contacts alloy sealing. by eliminating solder joints while providing the ability • Active Brazing to customize physical properties such as thermal • Nickel Alloy Contacts Our exclusive ceramic dielectric material, Ceramax, Precision Machining conductivity, weight, stiffness or expansion rate. • Titanium Alloy Contacts is one of the core technologies used to produce • Milling • Aluminum Alloy Contacts our advanced connector line. Ceramax is a multi- These advanced joining technologies, coupled with • Turning Engineering phase devitrifi ed ceramic compound used as a direct our use of Ceramax dielectric compounds, allow • 3D Design Wire Assembly replacement for glass. -
Electrode Manufacturing at PPWE of the E.O. Paton Electric Welding Back Issues Available
E.O. Paton Electric Welding Institute of the National Academy of Sciences of Ukraine International Scientific-Technical and Production Journal Issue 06 2019 Published Monthly Since 2000 English translation of the monthly «Avtomaticheskaya Svarka» (Automatic Welding) journal published in Russian since 1948 EDITORIAL BOARD CONTENTS Editor-in-Chief B.E. Paton Plenary Papers for International Conference Scientists of PWI, Kyiv S.I. Kuchuk-Yatsenko (vice-chief ed.), «Consumables for Welding, Surfacing V.N. Lipodaev (vice-chief ed.), and Coating Deposition and 3D Technologies», Yu.S. Borisov, G.M. Grigorenko, A.T. Zelnichenko, V.V. Knysh, Kyiv, PWI, 4–5 June 2019 I.V. Krivtsun, Yu.N. Lankin, L.M. Lobanov, V.D. Poznyakov, Bonnel J.-M., Maurer M. and Rosert R. Submerged arc surfacing of high-alloy I.A. Ryabtsev, K.A. Yushchenko steels by flux-cored wires .................................................................................. 3 Scientists of Ukrainian Universities Golovko V.V., Stepanyuk S.N. and Ermolenko D.Yu. Dispersion modification V.V. Dmitrik, NTU «KhPI», Kharkov V.V. Kvasnitsky, NTUU «KPl», Kyiv of dendrite structure of weld metal .................................................................... 13 E.P. Chvertko, NTUU «KPl», Kyiv Yushchenko K.A., Gakh I.S., Zadery B.A., Zvyagintseva A.V. and Foreign Scientists Karasevskaya O.P. Repair surfacing of gas turbine engine blades from N.P. Alyoshin high-temperature nickel alloys with surface defects and damage ..................... 19 N.E. Bauman MSTU, Moscow, Russia Guan Qiao Goncharov I.O., Sudavtsova V.S., Mishchenko D.D., Duchenko A.M. and Beijing Aeronautical Institute, China M. Zinigrad Sokolsky V.E. Influence of refractory dispersed phases on physical-chemical Ariel University, Israel properties of slag metls of MgO–Al2O3–SiO2–CaF2 system ..............................