The Quantitative Assessment of Retained Austenite in Induction Hardened Ductile Iron
Total Page:16
File Type:pdf, Size:1020Kb
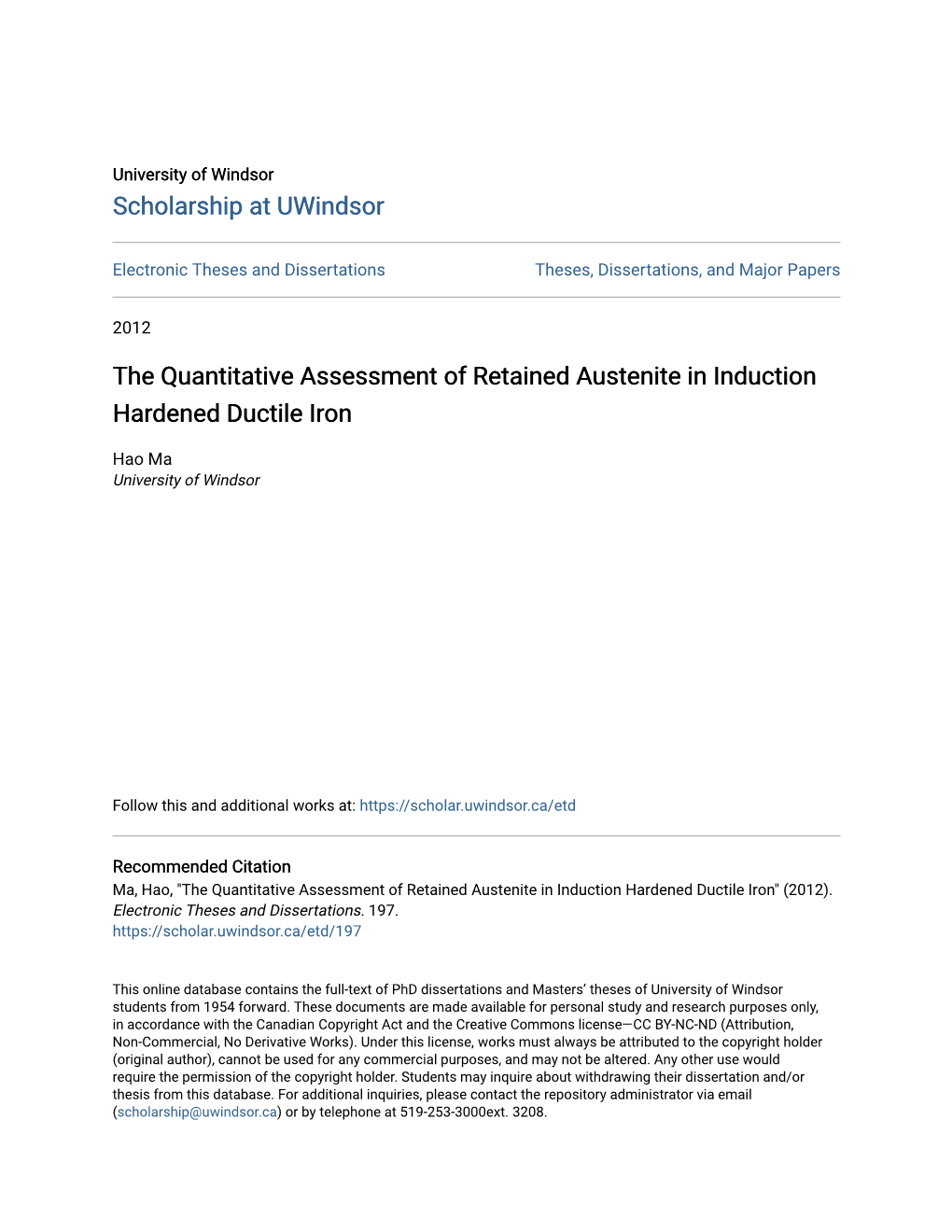
Load more
Recommended publications
-
Wear Behavior of Austempered and Quenched and Tempered Gray Cast Irons Under Similar Hardness
metals Article Wear Behavior of Austempered and Quenched and Tempered Gray Cast Irons under Similar Hardness 1,2 2 2 2, , Bingxu Wang , Xue Han , Gary C. Barber and Yuming Pan * y 1 Faculty of Mechanical Engineering and Automation, Zhejiang Sci-Tech University, Hangzhou 310018, China; [email protected] 2 Automotive Tribology Center, Department of Mechanical Engineering, School of Engineering and Computer Science, Oakland University, Rochester, MI 48309, USA; [email protected] (X.H.); [email protected] (G.C.B.) * Correspondence: [email protected] Current address: 201 N. Squirrel Rd Apt 1204, Auburn Hills, MI 48326, USA. y Received: 14 November 2019; Accepted: 4 December 2019; Published: 8 December 2019 Abstract: In this research, an austempering heat treatment was applied on gray cast iron using various austempering temperatures ranging from 232 ◦C to 371 ◦C and holding times ranging from 1 min to 120 min. The microstructure and hardness were examined using optical microscopy and a Rockwell hardness tester. Rotational ball-on-disk sliding wear tests were carried out to investigate the wear behavior of austempered gray cast iron samples and to compare with conventional quenched and tempered gray cast iron samples under equivalent hardness. For the austempered samples, it was found that acicular ferrite and carbon saturated austenite were formed in the matrix. The ferritic platelets became coarse when increasing the austempering temperature or extending the holding time. Hardness decreased due to a decreasing amount of martensite in the matrix. In wear tests, austempered gray cast iron samples showed slightly higher wear resistance than quenched and tempered samples under similar hardness while using the austempering temperatures of 232 ◦C, 260 ◦C, 288 ◦C, and 316 ◦C and distinctly better wear resistance while using the austempering temperatures of 343 ◦C and 371 ◦C. -
Ferritic Nitrocarburizing Gears to Increase Wear Resisitance And
Ferritic Nitrocarburizing Gears tOI Increase Wear Resistance and Reduce Distortion Loren ,JI, Epler uaHtygear manufacturing depends on controlled toler- asa gaseous territic nitrocarl:mrizillg process and patented by ances and geometry. As a re ult, ferritic nillocarburizing Lucas Industries in 1961. Lucas demonstrated that they could ha become the heat treat process of choice for many produce surface layers identical to those produced in salt bath gear manufacturers. The primary reason for this are: processes using an endothermic, ammonia-based atmosphere. The process is performed at low temperatures, i.e. less than The process was classified as a "thermochemical susfece critical treatment" that involved !he diffusion of both nitrogenand car- 2. The quench methods increase fatigue strength by up to, L25% bon into the surface of a metal at a temperature below the au tell- without distorting. Ferritlc nitrocarboriziag is used in place ite transforrnation temperature. The process would yield .3 single of carburizing and hardening, carbonitriding, nltriding or in phase epsilon layer with an atomic weight of Fep3' The ingle conjunction wi.th conventional and induction hardening. phase layer makes !:heproduct much more wear resistant than gas 3. h establishes gradient base haronesses, i.e, eliminates egg- or ionnitriding, according to Dawc and Trantner 0). shell effect on TiN, TiAlN,. ere. etc. [II 1982, lronbeund HeatTreat developed Ni.tmwear® using In addition, the process can also be applied to hobs, broaches, similar atmo pheres in a fluidized bed medium. Subsequently. drills and other cutting tools. Jack Ross, owner and founder of lronbound,. patented and HisUJry, Fenitic nitrocarburizing was first established in licensed the process to Dynamic Metal Treating. -
Role of Austenitization Temperature on Structure Homogeneity and Transformation Kinetics in Austempered Ductile Iron
Metals and Materials International https://doi.org/10.1007/s12540-019-00245-y Role of Austenitization Temperature on Structure Homogeneity and Transformation Kinetics in Austempered Ductile Iron M. Górny1 · G. Angella2 · E. Tyrała1 · M. Kawalec1 · S. Paź1 · A. Kmita3 Received: 17 December 2018 / Accepted: 14 January 2019 © The Author(s) 2019 Abstract This paper considers the important factors of the production of high-strength ADI (Austempered Ductile Iron); namely, the austenitization stage during heat treatment. The two series of ADI with diferent initial microstructures were taken into consideration in this work. Experiments were carried out for castings with a 25-mm-walled thickness. Variable techniques (OM, SEM, dilatometry, DSC, Variable Magnetic Field, hardness, and impact strength measurements) were used for investi- gations of the infuence of austenitization time on austempering transformation kinetics and structure in austempered ductile iron. The outcome of this work indicates that the austenitizing temperature has a very signifcant impact on structure homo- geneity and the resultant mechanical properties. It has been shown that the homogeneity of the metallic matrix of the ADI microstructure strongly depends on the austenitizing temperature and the initial microstructure of the spheroidal cast irons (mainly through the number of graphite nodules). In addition, this work shows the role of the austenitization temperature on the formation of Mg–Cu precipitations in ADI. Keywords Metals · Casting · ADI · Heat treatment · Mg2Cu particles 1 Introduction light/heavy trucks, construction and mining equipment, railroad, agricultural, gears and crankshafts, and brackets, Austempered ductile iron (ADI) belongs to the spheroidal among others [5–7]. In the literature, numerous papers have graphite cast iron (SGI) family, which is subjected to heat been published on ADI: particularly, on the numerical sim- treatment; i.e., austenitization and austempering. -
Induction Hardening on Drive Axle Shaft and It's
www.ierjournal.org International Engineering Research Journal (IERJ) Special Issue Page 1197-1201, June 2016, ISSN 2395-1621 Induction Hardening on Drive axle shaft and it’s FEA #1Aniket A. Deshmukh, #2Prof. D.H. Burande 1 PG student, Automotive Engineering, Mechanical Engineering Department, Savitribai Phule Pune University, Pune, Maharashtra, India. 2Associate professor, Mechanical Engineering Department, Savitribai Phule Pune University, Pune, Maharashtra, India. Abstract: This work deals with increasing strength of steel drive axle shafts by placing an extra bush support. It includes the modeling of shaft in CATIA. Drive shaft made up of MS material will be analyzed first. Stress and deformation will be the output of analysis. The meshing and boundary condition application will be carried using Hypermesh; Structural analysis of shaft will be carried out using ANSYS. Re-designing the shaft placing a bush for additional support in the length of shaft, and applying induction hardening process at the place of bush support for increasing the strength and reducing the deflection of the shaft. The design optimization also improves the performance of drive shaft. Keywords: Finite Element Analysis, Drive axle shaft, Induction hardening, Bush support. 1. INTRODUCTION Power is transmitted from engine to differential through propeller shaft, Axle shaft is connected between Hardening process is used for parts that wears while differential and wheel. It takes torque from engine. In this operating. During hardening core of the part does not get paper, drive axle shaft of Bolero automobile is thought of affected. Hardening increases wear resistance of a for the study. This axle shaft is semi-floating kind. -
Optimal Design of High-Frequency Induction Heating Apparatus for Wafer Cleaning Equipment Using Superheated Steam
energies Article Optimal Design of High-Frequency Induction Heating Apparatus for Wafer Cleaning Equipment Using Superheated Steam Sang Min Park 1 , Eunsu Jang 2, Joon Sung Park 1 , Jin-Hong Kim 1, Jun-Hyuk Choi 1 and Byoung Kuk Lee 2,* 1 Intelligent Mechatronics Research Center, Korea Electronics Technology Institute (KETI), Bucheon 14502, Korea; [email protected] (S.M.P.); [email protected] (J.S.P.); [email protected] (J.-H.K.); [email protected] (J.-H.C.) 2 Department of Electrical and Computer Engineering, Sungkyunkwan University (SKKU), Suwon 16419, Korea; [email protected] * Correspondence: [email protected]; Tel.: +82-31-299-4581 Received: 19 October 2020; Accepted: 22 November 2020; Published: 25 November 2020 Abstract: In this study, wafer cleaning equipment was designed and fabricated using the induction heating (IH) method and a short-time superheated steam (SHS) generation process. To prevent problems arising from the presence of particulate matter in the fluid flow region, pure grade 2 titanium (Ti) R50400 was used in the wafer cleaning equipment for heating objects via induction. The Ti load was designed and manufactured with a specific shape, along with the resonant network, to efficiently generate high-temperature steam by increasing the residence time of the fluid in the heating object. The IH performance of various shapes of heating objects made of Ti was analyzed and the results were compared. In addition, the heat capacity required to generate SHS was mathematically calculated and analyzed. The SHS heating performance was verified by conducting experiments using the designed 2.2 kW wafer cleaning equipment. -
Structure/Property Relationships in Irons and Steels Bruce L
Copyright © 1998 ASM International® Metals Handbook Desk Edition, Second Edition All rights reserved. J.R. Davis, Editor, p 153-173 www.asminternational.org Structure/Property Relationships in Irons and Steels Bruce L. Bramfitt, Homer Research Laboratories, Bethlehem Steel Corporation Basis of Material Selection ............................................... 153 Role of Microstructure .................................................. 155 Ferrite ............................................................. 156 Pearlite ............................................................ 158 Ferrite-Pearl ite ....................................................... 160 Bainite ............................................................ 162 Martensite .................................... ...................... 164 Austenite ........................................................... 169 Ferrite-Cementite ..................................................... 170 Ferrite-Martensite .................................................... 171 Ferrite-Austenite ..................................................... 171 Graphite ........................................................... 172 Cementite .......................................................... 172 This Section was adapted from Materials 5election and Design, Volume 20, ASM Handbook, 1997, pages 357-382. Additional information can also be found in the Sections on cast irons and steels which immediately follow in this Handbook and by consulting the index. THE PROPERTIES of irons and steels -
Comparison of Wear Performance of Austempered and Quench-Tempered Gray Cast Irons Enhanced by Laser Hardening Treatment
applied sciences Article Comparison of Wear Performance of Austempered and Quench-Tempered Gray Cast Irons Enhanced by Laser Hardening Treatment Bingxu Wang 1,2,*, Gary C. Barber 2, Rui Wang 2,3 and Yuming Pan 2 1 Faculty of Mechanical Engineering and Automation, Zhejiang Sci-Tech University, #928 No.2 Street, High Education Zone, Hangzhou 310018, China 2 Department of Mechanical Engineering, School of Engineering and Computer Science, Oakland University, Rochester, MI 48309, USA; [email protected] (G.C.B.); [email protected] (R.W.); [email protected] (Y.P.) 3 College of Modern Science and Technology, China Jiliang University, Hangzhou 310018, China * Correspondence: [email protected] Received: 30 March 2020; Accepted: 26 April 2020; Published: 27 April 2020 Abstract: The current research studied the effects of laser surface hardening treatment on the phase transformation and wear properties of gray cast irons heat treated by austempering or quench-tempering, respectively. Three austempering temperatures of 232 ◦C, 288 ◦C, and 343 ◦C with a constant holding duration of 120 min and three tempering temperatures of 316 ◦C, 399 ◦C, and 482 ◦C with a constant holding duration of 60 min were utilized to prepare austempered and quench-tempered gray cast iron specimens with equivalent macro-hardness values. A ball-on-flat reciprocating wear test configuration was used to investigate the wear resistance of austempered and quench-tempered gray cast iron specimens before and after applying laser surface-hardening treatment. The phase transformation, hardness, mass loss, and worn surfaces were evaluated. There were four zones in the matrix of the laser-hardened austempered gray cast iron. -
Cast Irons$ KB Rundman, Michigan Technological University, Houghton, MI, USA F Iacoviello, Università Di Cassino E Del Lazio Meridionale, DICEM, Cassino (FR), Italy
Cast Irons$ KB Rundman, Michigan Technological University, Houghton, MI, USA F Iacoviello, Università di Cassino e del Lazio Meridionale, DICEM, Cassino (FR), Italy r 2016 Elsevier Inc. All rights reserved. 1 Metallurgy of Cast Iron 1 2 Solidification of a Hypoeutectic Gray Iron Alloy With CE¼4.0 3 3 Matrix Microstructures in Graphitic Cast Irons – Cooling Below the Eutectic 3 4 Microstructure and Mechanical Properties of Gray Cast Iron 4 5 Effect of Carbon Equivalent 5 6 Effect of Matrix Microstructure 5 7 Effect of Alloying Elements 5 8 Classes of Gray Cast Irons and Brinell Hardness 5 9 Ductile Cast Iron 5 10 Production of Ductile Iron 6 11 Solidification and Microstructures of Hypereutectic Ductile Cast Irons 6 12 Mechanical Properties of Ductile Cast Iron 7 13 As-cast and Quenched and Tempered Grades of Ductile Iron 8 14 Malleable Cast Iron, Processing, Microstructure, and Mechanical Properties 8 15 Compacted Graphite Iron 9 16 Austempered Ductile Cast Iron 9 17 The Metastable Phase Diagram and Stabilized Austenite 9 18 Control of Mechanical Properties of ADI 10 19 Conclusion 10 References 11 Further Reading 11 Cast irons have played an important role in the development of the human species. They have been produced in various compositions for thousands of years. Most often they have been used in the as-cast form to satisfy structural and shape requirements. The mechanical and physical properties of cast irons have been enhanced through understanding of the funda- mental relationships between microstructure (phases, microconstituents, and the distribution of those constituents) and the process variables of iron composition, heat treatment, and the introduction of significant additives in molten metal processing. -
Hardening of Small Gears in Well Under a Second
Hardening of small gears PUTTING THE SMARTER HEAT TO SMARTER USE A guide to the benefits of induction heating FD - 2011236 02/16 ENG How to reduce distortion and costs when hardening small gears Induction is the cost-cutting alternative to furnace Induction can heat precisely localized zones in gears. case hardening of small- and medium-sized Achieving the same degree of localized hardening gears. Key features of induction hardening are with carburizing can be a time- and labor-intensive fast heating cycles, accurate heating patterns and procedure. When carburizing specific zones such as cores that remain relatively cold and stable. Such the teeth areas, it is usually necessary to mask the characteristics minimize distortion and make it more rest of the gear with ‘stop off’ coatings. These masks repetitive, reducing post-heat processing such as must be applied to each and every workpiece, and grinding. This is especially true when comparing removed following the hardening process. No such induction to case carburizing. masking is necessary with induction hardening. Induction hardening also reduces pre-processing, as Induction hardening is ideal for integrating into the geometry changes are less than those caused by production lines. Such integrated hardening is carburizing. Such minimal changes mean distortion more productive than thermochemical processes. does not need to be accounted for when making Moreover, integrated hardening minimizes costs, as the gear. With gears destined for gas carburizing, the gears do not have to be removed for separate however, ‘offsets’ that represent distortion are often heat treatment. In fact, induction heating makes introduced at the design stage. -
Design of a Wireless Power Transfer System Using Inductive Coupling and MATLAB Programming Apoorva.P1 Deeksha.K.S2 Pavithra.N3 Student, Dept
International Journal on Recent and Innovation Trends in Computing and Communication ISSN: 2321-8169 Volume: 3 Issue: 6 3817 - 3825 _______________________________________________________________________________________________ Design of a Wireless Power Transfer System using Inductive Coupling and MATLAB programming Apoorva.P1 Deeksha.K.S2 Pavithra.N3 Student, Dept. Of EEE, Student, Dept. Of EEE Student, Dept. Of EEE, Dr. T. Thimmaiah Institute of Dr. T. Thimmaiah Institute of Dr. T. Thimmaiah Institute of Technology Technology Technology K.G.F,India K.G.F, India K.G.F, India [email protected] [email protected] [email protected] Vijayalakshmi.M.N4 Somashekar.B5 David Livingston.D6 Student, Dept. Of EEE Asst Professor Dept. Of EEE, Asst Professor Dept. Of EEE, Dr. T. Thimmaiah Institute of Dr. T. Thimmaiah Institute of Dr. T. Thimmaiah Institute of Technology Technology Technology K.G.F, India K.G.F, India K.G.F, India [email protected] [email protected] [email protected] Abstract—Wireless power transfer (WPT) is the propagation of electrical energy from a power source to an electrical load without the use of interconnecting wires. It is becoming very popular in recent applications. Wireless transmission is useful in cases where interconnecting wires are difficult, hazardous, or non-existent. Wireless power transfer is becoming popular for induction heating, charging of consumer electronics (electric toothbrush, charger), biomedical implants, radio frequency identification (RFID), contact-less smart cards, and even for transmission of electrical energy from space to earth. In the design of the coils, the parameters of coils are obtained by using the basic calculations and measurements. -
Induction Heating Principles PRESENTATION
Induction Heating Principles PRESENTATION www.ceia-power.com This document is property of CEIA which reserves all rights. Total or partial copying, modification and translation is forbidden FC040K0068V1000UK Main Applications of Induction Heating ¾ Hard (Silver) Brazing ¾ Tin Soldering ¾ Heat Treatment (Hardening, Annealing, Tempering, …) ¾ Melting Applications (ferrous and non ferrous metal) ¾ Forging This document is property of CEIA which reserves all rights. Total or partial copying, modification and translation is forbidden FC040K0068V1000UK Examples of induction heating applications This document is property of CEIA which reserves all rights. Total or partial copying, modification and translation is forbidden FC040K0068V1000UK Advantages of Induction Reduced Heating Time Localized Heating Efficient Energy Consumption Heating Process Controllable and Repeatable Improved Product Quality Safety for User Improving of the working condition This document is property of CEIA which reserves all rights. Total or partial copying, modification and translation is forbidden FC040K0068V1000UK Basics of Induction INDUCTIVE HEATING is based on the supply of energy by means of electromagnetic induction. A coil, suitably dimensioned, placed close to the metal parts to be heated, conducting high or medium frequency alternated current, induces on the work piece currents (eddy currents) whose intensity can be controlled and modulated. This document is property of CEIA which reserves all rights. Total or partial copying, modification and translation is forbidden FC040K0068V1000UK Basics of induction The heating occurs without physical contact, it involves only the metal parts to be treated and it is characterized by a high efficiency transfer without loss of heat. The depth of penetration of the generated currents is directly correlated to the working frequency of the generator used; higher it is, much more the induced currents concentrate on the surface. -
Magnetic Flux Controllers in Induction Heating and Melting
ASM Handbook, Volume 4C, Induction Heating and Heat Treatment Copyright # 2014 ASM InternationalW V. Rudnev and G.E. Totten, editors All rights reserved www.asminternational.org Magnetic Flux Controllers in Induction Heating and Melting Robert Goldstein, Fluxtrol, Inc. MAGNETIC FLUX CONTROLLERS are workpiece. For both cases, there are three closed is applied, it strongly reduces the reluctance of materials other than the copper coil that are used loops: flow of current in the coil, flow of mag- the back path for the magnetic flux (Ref 3). All in induction systems to alter the flow of the mag- netic flux, and flow of current in the workpiece. induction heating systems can be described in netic field. Magnetic flux controllers used in In most cases, the difference between induc- this way. power supplying components are not considered tion heating applications and transformers is that The benefits of a magnetic flux concentrator in this article. the magnetic circuit is open. The magnetic field on the electrical parameters for a given applica- Magnetic flux controllers have been in exis- path includes not only the area with the control- tion depends on the ratio of the reluctance of tence since the development of the induction ler, but also the workpiece surface layer and the the back path for magnetic flux to the overall technique. Michael Faraday used two coils of air between the surface and controller, which reluctance in the system. It is also possible to wire wrapped around an iron core in his experi- cannot be changed. Therefore, the reluctance of break down basic system components into sub- ments that led to Faraday’s law of electromagnetic the magnetic path only partially depends on the components to determine the most economical induction, which states that the electromotive magnetic permeability of the controller (Ref 3).